定子永磁型无刷电机综述
永磁无刷同步电机本体设计原理

永磁无刷同步电机本体设计原理
永磁无刷同步电机(PMSM,permanent magnet synchronous motor)的基本设计原理是交流电机的工作原理,其定子运行是三项的相差的交流电,而转子则是永磁体。
这种电机的最大优势在于交流电能量由直流提供,可以对电机进行精确的控制,并且解决了电刷带来的寿命问题。
无刷电机主要由转子和定子两部分组成。
转子是由一系列永磁体或磁铁组成,这些永磁体或磁铁通过轴心连接在一起并固定在转轴上。
转子上的永磁体产生磁场,而这个磁场是恒定的,不随转子转动而改变。
定子是由一组线圈组成,这些线圈通常由铜线绕成,安装在无刷电机的外壳内。
当电流通过定子线圈时,它们产生的磁场与转子上的永磁体磁场相互作用,从而产生旋转力。
此外,无刷电机使用电子换向器取代了机械换向器,使得电机既具有直流电机良好的调速性能,又具有交流电机结构简单、无换向火花、运行可靠和易于维护等优点。
电子控制器是无刷电机的关键部分,负责监测和控制电流的流向和大小,从而控制电机的旋转速度和方向。
在电机运行时,转子会寻找与定子磁场对齐的位置。
当转子与定子磁通分隔90°时,产生的转距最大,而当磁通对齐时,转距为零。
通过不断地换向和控制电流的大小,可以使得电机持续、稳定地旋转。
总的来说,永磁无刷同步电机的设计原理是利用永磁体和线圈之间的相互作用产生旋转力,通过电子控制器控制电流的流向和大小,实现电机的精确控制。
无刷发电机工作原理

无刷发电机工作原理
无刷发电机是一种利用电磁感应原理将电能转化为机械能的设备。
它主要由定子、转子和电子器件组成。
无刷发电机的定子是由一组线圈组成,这些线圈被固定在一根金属磁心上。
当电流通过这些线圈时,会在定子上产生一个磁场。
无刷发电机的转子是由一组永磁体组成,通过一个轴连接到外部机械装置上。
这些永磁体被放置在定子的外部,使其能够相对于定子旋转。
无刷发电机中的电子器件则起到了控制电流供应的作用。
它们可以检测定子和转子之间的位置,并根据这个位置信息,不断地调整电流的供应,以保持转子的正常运转。
工作过程中,当外部机械装置转动时,转子也会随之旋转。
转子上的永磁体在旋转过程中会通过定子产生电磁感应现象。
具体来说,当永磁体靠近一个线圈时,该线圈中的电流方向会随之改变;而当永磁体远离该线圈时,电流方向会再次改变。
这种变化会在电子器件的控制下,使得定子线圈中的电流始终沿着一个方向流动。
定子线圈中的电流流动会在周围产生一个磁场,这个磁场与转子上的永磁体产生作用力,使得转子继续旋转。
同时,转子的旋转也会带动外部机械装置继续运动。
通过不断地调整电流供应和控制转子旋转的速度,无刷发电机能够稳定地将电能转化为机械能,从而实现工作。
永磁无刷直流电机简介

表贴凸出式和插入式转子磁路构造图
电气学院
1)表贴凸出式转子磁路构造 • 其构造简朴,制造成本较低,转动惯量较小,多用于矩形
波永磁同步电动机和恒功率运营范围不宽旳永磁同步电动 机中
2)表贴插入式转子磁路构造 • 这种构造可充分利用转子构造磁路旳不对称性所产生旳磁
阻转矩,提升电机旳功率密度。制造工艺也较简朴。一般 用于某些调速永磁同步电动机中。
B
(2)空载时铁心中旳附加(或杂散)损耗,它是由定转子开槽引起旳气隙磁导变化 而产生旳谐波磁场在对方表面产生旳表面损耗及脉振损耗。 (3)电气损耗,是由工作电流在绕组中产生旳损耗,对直流电机或同步电机而言, 也涉及电刷在换向器或集电环上旳接触电阻损耗。
(4)负载时旳附加(或杂散)损耗,是由定子或转子电流所产 生旳漏磁场在定、转子绕组里和铁心及构造件里引起旳多种损耗。
• 假如将一只霍尔传感器安装在接近转子旳位置,当N极逐渐接近 霍尔传感器即磁感应强度到达一定值时,其输出是导通状态;
• 当N极逐渐离开霍尔传感器、磁感应强度逐渐减小时,其输出依 然保持导通状态;只有磁场转变为S极并到达一定值时,其输出 才翻转为截止状态。
• 在S-N交替变化磁场下,传感器输出波形占高、低电平各占50%。 • 假如转子是一对极,则电机旋转一周霍尔传感器输出一种周期旳
✓ 具有很好旳力学特征,韧性好、抗压强度高、可加工等
✓ 价格合理,经济性好
电气学院
• 铁氧体:适合于对电机体积、重量和性能要求不高,而对电机旳经济 性要求高旳场合。
• 铝镍钴:适合于对电机体积、重量和性能要求不高,但工作温度超出 300度或要求温度稳定性好且电机旳成本不高旳场合。
• 钕铁硼:适合于对电机体积、重量和性能要求很高,工作环境温度不 高,对永磁体温度稳定性要求不高旳场合。
永磁无刷直流电机的构造

永磁无刷直流电机的构造永磁无刷直流电机是一种重要的电动机类型,其构造与传统的有刷直流电机有所不同。
在本文中,我们将深入探讨永磁无刷直流电机的构造,了解其工作原理以及与其他类型电机的区别。
一、永磁无刷直流电机的构造永磁无刷直流电机由多个关键组件构成,包括转子、定子和电子调速器。
下面我们将逐一介绍这些部件的功能和特点。
1. 转子转子是电机中的旋转部分,由永磁体和轴承组成。
其中,永磁体通常由稀土永磁材料制成,具有较高的磁场强度和矫顽力,能够提供较大的转矩。
轴承则用于支撑转子的转动,通常采用滚珠轴承或磁悬浮轴承。
2. 定子定子是电机中的固定部分,由线圈、铁心和绕组等组成。
线圈通常由导电材料绕制而成,绕制方式包括单层绕组和多层绕组。
铁心则用于增强磁场,并且通过绕组与转子的磁场相互作用,实现电能到机械能的转换。
3. 电子调速器电子调速器是永磁无刷直流电机的控制中枢,通过电子器件对电机的电流进行控制和调节。
常见的电子调速器包括三相桥式整流器、逆变器和控制芯片等。
电子调速器通过控制转子上的永磁体和定子上的绕组之间的电流关系,实现对电机转速和扭矩的精准调控。
二、永磁无刷直流电机的工作原理永磁无刷直流电机的工作原理基于磁场的相互作用,其具体过程如下:1. 磁场形成当电流通过定子绕组时,会在定子和转子之间产生一个旋转磁场。
这个旋转磁场由定子绕组的电流和转子上的永磁体形成。
2. 磁场相互作用转子上的永磁体与定子绕组之间的磁场相互作用,导致转子受到力矩的作用而开始旋转。
这个力矩的大小与磁场强度、永磁体形状和绕组电流等因素有关。
3. 电子调速器控制电子调速器通过控制定子绕组的电流和磁场强度,可以实现对电机转速和扭矩的调节。
通过改变电子调速器的工作方式,可以实现电机的正转、反转和调速等功能。
三、永磁无刷直流电机与其他电机的区别与传统的有刷直流电机相比,永磁无刷直流电机具有以下特点:1. 无刷结构永磁无刷直流电机采用了无刷结构,消除了传统电机中刷子的使用,减少了能量损耗和机械磨损,并提高了电机的可靠性和寿命。
无刷直流电机控制技术综述
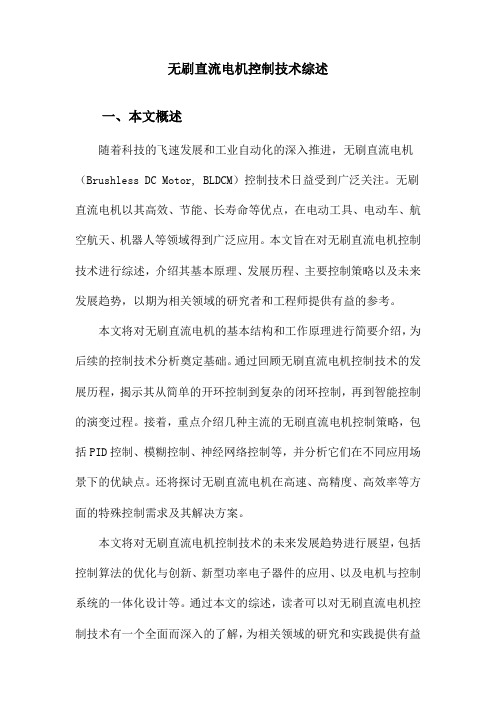
无刷直流电机控制技术综述一、本文概述随着科技的飞速发展和工业自动化的深入推进,无刷直流电机(Brushless DC Motor, BLDCM)控制技术日益受到广泛关注。
无刷直流电机以其高效、节能、长寿命等优点,在电动工具、电动车、航空航天、机器人等领域得到广泛应用。
本文旨在对无刷直流电机控制技术进行综述,介绍其基本原理、发展历程、主要控制策略以及未来发展趋势,以期为相关领域的研究者和工程师提供有益的参考。
本文将对无刷直流电机的基本结构和工作原理进行简要介绍,为后续的控制技术分析奠定基础。
通过回顾无刷直流电机控制技术的发展历程,揭示其从简单的开环控制到复杂的闭环控制,再到智能控制的演变过程。
接着,重点介绍几种主流的无刷直流电机控制策略,包括PID控制、模糊控制、神经网络控制等,并分析它们在不同应用场景下的优缺点。
还将探讨无刷直流电机在高速、高精度、高效率等方面的特殊控制需求及其解决方案。
本文将对无刷直流电机控制技术的未来发展趋势进行展望,包括控制算法的优化与创新、新型功率电子器件的应用、以及电机与控制系统的一体化设计等。
通过本文的综述,读者可以对无刷直流电机控制技术有一个全面而深入的了解,为相关领域的研究和实践提供有益的启示和指导。
二、无刷直流电机的基本原理与结构无刷直流电机(Brushless Direct Current,简称BLDC)是一种采用电子换向器替代传统机械换向器的直流电机。
其基本工作原理和结构与传统直流电机有所不同,因此在控制上也具有其独特之处。
基本原理:无刷直流电机的工作原理基于电子换向技术。
它利用电子开关器件(如功率晶体管或功率MOSFET)实现对电机电流的换向控制,从而改变了电机转子的旋转方向。
与传统直流电机相比,无刷直流电机省去了机械换向器和电刷,因此具有更高的运行效率和更长的使用寿命。
结构特点:无刷直流电机主要由定子、转子和电子换向器三部分组成。
定子通常由多极电磁铁构成,而转子则是一个带有永磁体的圆柱形结构。
定子永磁型无刷电机
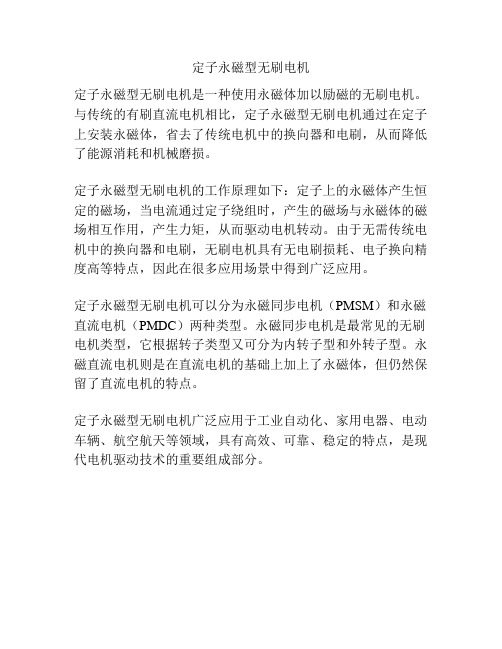
定子永磁型无刷电机
定子永磁型无刷电机是一种使用永磁体加以励磁的无刷电机。
与传统的有刷直流电机相比,定子永磁型无刷电机通过在定子上安装永磁体,省去了传统电机中的换向器和电刷,从而降低了能源消耗和机械磨损。
定子永磁型无刷电机的工作原理如下:定子上的永磁体产生恒定的磁场,当电流通过定子绕组时,产生的磁场与永磁体的磁场相互作用,产生力矩,从而驱动电机转动。
由于无需传统电机中的换向器和电刷,无刷电机具有无电刷损耗、电子换向精度高等特点,因此在很多应用场景中得到广泛应用。
定子永磁型无刷电机可以分为永磁同步电机(PMSM)和永磁直流电机(PMDC)两种类型。
永磁同步电机是最常见的无刷电机类型,它根据转子类型又可分为内转子型和外转子型。
永磁直流电机则是在直流电机的基础上加上了永磁体,但仍然保留了直流电机的特点。
定子永磁型无刷电机广泛应用于工业自动化、家用电器、电动车辆、航空航天等领域,具有高效、可靠、稳定的特点,是现代电机驱动技术的重要组成部分。
无刷永磁电动机工作原理
无刷永磁电动机工作原理
无刷永磁电动机是一种常用的电动机,其工作原理如下:
1. 永磁体:无刷永磁电动机的转子上通常安装有永磁体,它是由高能磁体材料制成,具有较强的磁场。
2. 定子:定子是电动机的固定部分,通常由一组定子线圈组成。
这些线圈被安排在电动机壳体内,呈现环形排列。
在定子线圈中通电时,它们会产生磁场。
3. 传感器:无刷永磁电动机通常配备有传感器,用于检测转子的位置和速度,并向控制器提供信号。
4. 控制器:控制器是电动机的控制中心,它接收传感器的信号,并根据需要控制定子线圈的通电情况。
工作过程如下:
1. 在电动机初次启动时,控制器将电流送至定子线圈,根据传感器提供的转子位置信息,控制器确保定子线圈的磁场与永磁体的磁场相互作用。
2. 这种相互作用会产生转矩,使得转子开始转动。
随着转子的转动,传感器会持续监测转子的位置,并向控制器提供反馈。
3. 控制器根据传感器的反馈信号,实时调整定子线圈的通电情况,以保持转子与磁场之间的最佳相互作用。
4. 此过程不断重复,使电动机保持稳定运转。
由于无需通过刷子传递电流,无刷永磁电动机具有较高的效率和较长的寿命。
总结:无刷永磁电动机通过定子线圈和永磁体之间的相互作用来产生转矩,实现电动机的运转。
控制器根据传感器的反馈信号,调节定子线圈的通电情况,以保持转子与磁场之间的最佳相互作用。
永磁无刷直流电机介绍和工作原理
永磁无刷直流电机 正弦波PMSM调速系统的组成
一种典型的正弦波永磁同步电动机调速系统框图
永磁无刷直流电机
永磁无刷直流电动机结构特点:
• 定子绕组采用整距、集中绕组; • 永磁体粘接至转子表面,呈隐极式结构;
图10.16 永磁无刷直流电动机的主磁场磁密波形图
永磁无刷直流电机
永磁无刷直流电动机 定子绕组感应的相电势和电流波形
永磁无刷直流电机
无刷电机专用驱动电路 MC33035
永磁无刷直流电机
无刷电机专用驱动电路 MC33035
永磁无刷直流电机
无刷电机专用驱动电路TDA1621
LM621的原理框图
LM621的换相译码真值表
永磁无刷直流电机
无刷电机专用驱动电路TDA1621
永磁无刷直流电机
无位置传感器无刷电机专用驱动芯片TDA5142T
永磁无刷直流电机
永磁同步电动机的发展前景
1. 更高的节能效果。永磁同步电动机采用永磁体励磁,无需励磁电流,所以 可以显著提高功率因数。定子电流小,转子无铜耗。比一般的异步电动机 效率提高2%~8%,尤其轻载运行节能效果显著。
2. 可满足某些工业需求大的启动转矩和最大转矩倍数的要求。
3. 低速驱动的需求。为了提高控制精度,减少震动噪音,也为了大转矩驱动 要求,近年来对低速电动机的需求不断增长,如:电梯拖动用永磁同步曳 引机,转矩提高十几倍,取消了庞大的齿轮箱,通过曳引轮直接拖动轿厢, 明显减小了噪音和震动;又如:船用吊舱式电力推动器,将低速大转矩永 磁同步电动机置于船舱外的吊舱,无需原来的传动系统,直接驱动螺旋桨。 四门子公司吊舱式推进器中PMSM容量已达30000KW。
电的过程,或者磁场旋转的过程,定
子各相绕组在气隙中所形成的旋转磁
永磁无刷直流电机简介
1 绪论1.1 无刷直流电动机是最具发展前途的机电一体化电机无刷直流电动机是随着半导体电子技术发展而出现的新型机电一体化电机,它是现代电子技术(包括电力电子、微电子技术)、控制理论和电机技术相结合的产物。
众所周知,直流电动机具有优越的调速性能,主要表现在控制性能好、调速范围宽、起动转矩大、低速性能好、运行平稳、效率高,应用场合从工业到民用极其广泛。
在普通的直流电动机中,直流电的电能是通过电刷和换向器进入电枢绕组,与定子磁场相互作用产生转矩的。
由于存在电接触部件——电刷和换向器,结果产生了一系列致命的缺陷:⑴机械换向产生的换向火花引起换向器和电刷磨损、电磁干扰、噪声大,寿命短;⑵结构复杂,可靠性差,故障多,需要经常维护;⑶由于换向器存在,限制了转子转动惯量的进一步下降,影响了动态特性。
在许多应用场合下,它是系统不可靠的重要来源。
虽然直流电动机是电机发展历史上最先出现的,但它的应用范围因此受到限制,使后来者且运行可靠的交流电机得到发展,取而代之广泛应用。
交流电机的历史超过百年。
但是,无刷直流电动机历史只有几十年。
1955年美国D.harrison等人首次申请了用晶体管换相电路代替机械电刷的专利,这是无刷直流电动机的雏形。
在1962年,T.G.Wilson和P.H.Trickey提出“固态换相直流电机”专利,这标志着现代无刷电动机的真正诞生。
从20世纪60年代初开始,无刷直流电动机进入到应用阶段。
因其较高的可靠性,无刷直流电动机最先在宇航技术中得到应用。
1964年,它被美国国家航空航天局(NASA)使用,用于卫星姿态控制、太阳电池板的跟踪控制、卫星上泵的驱动等。
在1978年当时的联邦德国Mannesmann公司的Indramat分部的MAC经典无刷直流电动机及其驱动器在汉诺威贸易展览会正式推出,是电子换向的无刷直流电动机真正进入实用阶段的标志。
国际上对无刷直流电动机进入深入的研究,从研制方波无刷电机基础上发展到正弦无刷电机——新一代的永磁同步电动机(PMSM)。
简介永磁无刷直流电机的原理及特点
成 本 低廉 等 诸 多 优 点 使 得 串 励 电机 在 电动 工 具 电机选 用 中 占据 统治 地 位 多 年 。
随着动力 电池技术进 步,特 别是动力锂 电
池 技 术 的 快 速 发展 ,无绳 、 强 劲 、 小 巧 便 携 的
s t r u c t u r e s a n d c o n t r o l p r i n c i p l e s o f b us r h l e s s mo t o r c o mp a r e d wi t h b r u s h mo t o r , l o o k i n g f o r wa r d t o t h e f u t u r e t r e n d o f t h e n e w mo t o r f o r p o we r t o o l s a p p l i c a t i o n s .
简介永磁 元刷 直流 电机的原理及特 点
刘 志 刚
( I : 海锐奇 I : 具 股份 仃限 公 d I : 海 2 0 1 6 1 2)
摘 要 介 绍无刷直流 电机在 电动工具中 的运用概况 ,对无刷 电机 相比有 刷电机 的特点、结 构和控制原理进行分析 ,展望对 电动工具应用新 型电机 的未来 趋势。
的 专 利构 建 了 无刷 直 流 电动 机 的雏 形。1 9 6 2 年 ,由 T. G. Wi l s o n和 P. H. Tr i c k e y提 出 “ 固 态换 相 直 流 电机 ” ( DC Ma c h i n e wi l h S o l i d
工 具 的 市 场 占 比 。有 专 家 预 言 : 电动 工 具 的 未 来在 于 锂 电等新 能 源 工具 ;
- 1、下载文档前请自行甄别文档内容的完整性,平台不提供额外的编辑、内容补充、找答案等附加服务。
- 2、"仅部分预览"的文档,不可在线预览部分如存在完整性等问题,可反馈申请退款(可完整预览的文档不适用该条件!)。
- 3、如文档侵犯您的权益,请联系客服反馈,我们会尽快为您处理(人工客服工作时间:9:00-18:30)。
Overview of Stator-Permanent MagnetBrushless MachinesMing Cheng,Senior Member,IEEE,Wei Hua,Member,IEEE,Jianzhong Zhang,Member,IEEE,andWenxiang Zhao,Member,IEEEAbstract—Permanent magnet(PM)brushless machines having magnets and windings in stator(the so-called stator-PM machines) have attracted more and more attention in the past decade due to its definite advantages of robust structure,high power density, high efficiency,etc.In this paper,an overview of the stator-PM ma-chine is presented,with particular emphasis on concepts,opera-tion principles,machine topologies,electromagnetic performance, and control strategies.Both brushless ac and dc operation modes are described.The key features of the machines,including the mer-its and drawbacks of the machines,are summarized.Moreover,the latest development of the machines is also discussed.Index Terms—Doubly salient,flux reversal,flux switching, overview,stator-permanent magnet(PM).I.I NTRODUCTIONW ITH THE significant achievements of permanent mag-net(PM)materials and power electronic devices,brush-less machines excited by PMs are developing dramatically. Generally speaking,there are a total of four types of PM machines which have magnets located on the rotor,and they are the following:1)surface mounted;2)inset;3)radial interior; and4)circumferential interior.It should be emphasized that all of the PM machines mentioned have magnets located on the rotor,and they are referred to as“rotor-PM machines”in this paper,which predominate in the industry applications due to outstanding advantages[1],[2].However,magnets usually need to be protected from the centrifugal force by employing a retaining sleeve,which is made of either stainless steel or nonmetallicfiber.Rotor temperature rise may be a problem due to poor thermal dissipation,which may cause irreversible demagnetization of magnets and may ultimately limit the power density of the machine.Recently,in contrast,a new type of PMManuscript received March21,2010;revised June28,2010,October1, 2010,and December21,2010;accepted February16,2011.Date of publication March7,2011;date of current version September7,2011.This work was supported in part by NSFC under Projects59507001,50377004,50337030, 50729702,50807007,60974060,and50907031;by the Specialized Research Fund for the Doctoral Program of Higher Education of China under Projects 20050286020,200802861038,and20090092110034;by the High Tech Re-search Program of Jiangsu Province,China,under Project BG2005035;and by the Aeronautical Science Foundation of China under Projects20080769007and 20100769004.M.Cheng,W.Hua,and J.Zhang are with the School of Electrical Engineering,Southeast University,Nanjing210096,China(e-mail:mcheng@ ;huawei1978@;seuzjz@).W.Zhao is with the School of Electrical and Information Engineering, Jiangsu University,Zhenjiang212013,China(e-mail:zwx@). Color versions of one or more of thefigures in this paper are available online at .Digital Object Identifier10.1109/TIE.2011.2123853Fig.1.Stator-PM alternator in1955[3].machine having magnets on the stator,nominated as stator-PMmachines,has re-emerged and has been developed,which canovercome the problems suffered by the rotor-PM counterparts.The purpose of this paper is to give an overview of thestator-PM machines.Thus,the state-of-the art technology ofthe stator-PM machines,including machine topologies,opera-tion principles,characteristics,control strategies,torque rippleminimization,and latest developments will be reviewed anddiscussed.II.C ONCEPTS OF S TATOR-PM M ACHINESThe idea of stator-PM machines can be traced back to1955when Rauch and Johnson proposed probably thefirst stator-PM topology,as shown in Fig.1[3],in which both the statortooth and rotor poles are salient so as to transfer thefluxescreated by the stator magnets from the stator to the rotoracross the air gap when the rotor poles face the stator teeth.Thus,the polarities of theflux linked in the coils in the statorreverse as the rotor aligns the alternative pair of stator teeth.However,due to the limitation of the magnet property at thattime,the stator-PM machines were overwhelmed by wound-field excitation machines,e.g.,synchronous and dc machines.Another origin of the stator-PM machine can be found fromthe well-known Law’s relay actuator shown in Fig.2[4].Inaddition,the doubly salient structure employed in electricalmachines can also originate from an induction-type generator,as shown in Fig.3[5],in which the stator assembly is a set ofpieces arranged in a cylinder laminated iron,with the armaturewindings wound.The special geometry allows the variation ofthe magnetflux that is linked into the“C”-shaped stator polepieces to induce electromotive force(EMF).0278-0046/$26.00©2011IEEEw’s relay actuator[4].Fig.3.Flux-switch“C”-segmented inductor alternator in1975[5]. Conceptually,stator-PM machines employ the polarized re-luctance principle,in which the torque and EMFs are the resultant from theflux-switching action of rotor saliencies on a unipolarflux produced by PMs in the stator,leading to an exceptionally simple and robust rotor structure.III.B ASIC T OPOLOGIES,P RINCIPLES,AND P ERFORMANCESBasically,there are three types of modern stator-PM ma-chines,namely,doubly salient PM(DSPM)machine[6],flux-reversal PM(FRPM)machine[7],andflux-switching PM (FSPM)machine[8],as shown in Fig.4.It should be noted that the operation principle and electromagnetic performance of the three machines are distinct,although they are all classified as stator-PM machines.A.DSPM MachineThe DSPM machine can be considered as a combination of switched-reluctance machine and stator magnets[6],in which the magnets are insetted in the stator back-iron and the con-centrated windings are employed,making the PMfluxes linked in the coils unipolar.Furthermore,by specifically designing the stator teeth and rotor pole arcs,the air-gap reluctance seen by magnets are invariant[9],and consequently,the PMflux-linkage linearly varies with the rotor position,as shown in Fig.5(a).Therefore,the ideal phase back-EMF waveform is trapezoidal,and the conventional brushless dc(BLDC)opera-tion mode can be adopted[10].On the other hand,a simple rotor-skewing method can be used[11],and a quasi-sinusoidal back EMF can be obtained. Consequently,the DSPM machine can also be run in the brushless ac(BLAC)mode,as shown in Fig.5(b).Fig.4.Re-emerged stator-PM machines.(a)DSPM machine.(b)FRPM machine[7].(c)FSPM machine[8].Fig.5.Operation principle of the DSPM machines.(a)Unskewed rotor.(b)Skewedrotor.Fig.6.Four/six-pole single-phase DSPM generator[12].Except for the three-phase six/four-pole(six-stator-teeth/ four-rotor-pole)topology,other feasible slot/pole combinations are presented,e.g.,one-phase four/six-pole[12](Fig.6),two-phase four/six-pole with dual stator[13](Fig.7),three-phaseCHENG et al.:OVERVIEW OF STATOR-PERMANENT MAGNET BRUSHLESS MACHINES5089Fig.7.Two-phase four/six-pole DSPM machine with dual stator[13].Fig.8.12/8-pole DSPM machine[14].Fig.9.Eight/six-pole DSPM machine [15].12/8-pole [14](Fig.8),and four-phase eight/six-pole configu-rations [15](Fig.9),revealing the different characteristics and the suitability for different applications.Additionally,power-dimension equations were derived analytically [16]–[18],which not only indicate that the output power is directly propor-tional to the ratio of the rotor poles to the stator teeth but also provide designers a practical way to make the initial calculation of the motor dimensions.In [19],a nonlinear varying-network magnetic circuit was built to analyze the electromagnetic per-formance of the DSPM machines more efficiently with enough accuracy.Moreover,a nonuniform air gap is employed to reduce the cogging torque [20].To regulate the uncontrollable PM flux and to extend the constant-power region,several schemes were proposed in [21](Fig.10),although some of them are some-what impractical in applications.Moreover,a new split-winding configuration was proposed,as shown in Fig.11[22].B.FRPM MachineThe FRPM machine has magnets located on the surface of the stator teeth and concentrated windings,as shown in Fig.12.Different from DSPM machines,the phase PM flux-linkage of an FRPM machine is bipolar,as shown in Fig.13.The BLDC operation mode is also suitable for the FRPM machines.Additionally,it is found that the FRPM machine exhibits fault-tolerance capability due to its natural isolation betweenphases,Fig.10.Schematic of the flux regulation in the DSPM machine [21].(a)By a movable magnetic shoring piece.(b)By moving magnets in the axial direction.(c)By a magnetic/nonmagneticcollar.Fig.11.Schematic of the split winding for a four-phase DSPM machine [22].and the variation of the inductances versus rotor position is small,which indicates that the reluctance torque is negligible [7].Similarly,the rotor-skewing method can also be used to improve the EMF waveform of a multipole FRPM machine to be more sinusoidal and to reduce the cogging torque for5090IEEE TRANSACTIONS ON INDUSTRIAL ELECTRONICS,VOL.58,NO.11,NOVEMBER2011Fig.12.Stator magnets and winding configuration of the FRPMmachine. Fig.13.Operation principle of the FRPM machines.(a)Unskewed rotor.(b)Skewedrotor.Fig.14.Different magnet configurations of the FRPM machines[24].(a)Pole-PMs on stator.(b)Inset-PMs on stator.an automotive generator[23]or low-speed servo drives,as shown in Fig.14[24],respectively.However,the induced-eddy-current losses in the magnets and the low power factor may be the subject of further work,as addressed in[25].In addition,the magnet thickness in the magnetized direction increases the effective air-gap length between the stator teeth and rotor poles.Therefore,the magnet thickness,as well as rotor pole arc,air-gap length,etc.,has significant effects on the electromagnetic performance of the FRPM machine.Hence, the optimal designs on various dimensions were investigated, e.g.,employing the concave stator poles and additionalflux barriers,as shown in Fig.15[26],as well as a rotor-teeth-pairing technique to reduce the cogging torque,as shown in Fig.16[27].Additionally,it is found that the PWM control modes have an important influence on the performance of the FRPM machine,as revealed in[28].In[29],a single-phase two/three-pole FRPM was proposed,and to solve the starting torque problem,the cogging torque was used as a solution by proposing a rotor with a tapered air-gap structure,as shown in Fig.17.Moreover,an axialflux and an outer-rotor FRPM machine were proposed in[30]and[31],respectively.Fig.15.Concave stator pole andflux barrier for the FRPM machines[26]. Fig.16.Rotor-teeth-pairing technique for the FRPM machines[27].Fig.17.Rotor structure with a tapered air gap of a single-phase two/three-pole FRPM machine[29].Fig.18.Prototype of a12/10-pole FSPM machine.(a)Configuration.(b)Prototyped motor.C.FSPM MachineAmong the three stator-PM machines,the stator configura-tion of the FSPM machine is relatively complex,as shown in Fig.18.The stator contains12segments of“U”-shaped mag-netic cores,between which12pieces of magnets are inset and magnetized circumferentially in alternative opposite directions [32].As shown in Fig.19,a concentrated coil is wound around the adjacent stator teeth with a magnet sandwiched.Hence,CHENG et al.:OVERVIEW OF STATOR-PERMANENT MAGNET BRUSHLESS MACHINES5091Fig.19.Stator magnet and winding configuration of the FSPMmachines.Fig.20.Coils and phase EMF waveforms of a12/10-pole FSPM machine[33].(a)Predicted.(b)Measured.the polarity of the PMflux linkage in the coil reverses when the rotor pole aligns the alternative stator tooth that belongs to the same phase,i.e.,realizing the“flux-switching”action. It should be emphasized that,due to the magnetic reluctance difference between the two pairs of coils composing a phase, the resultant phase EMF waveforms are essentially sinusoidal without any additional measures[33],which is also one of the outstanding advantages of the FSPM machine over the other two counterparts.In addition,it is found that the optimal rotor pole arc is1.4times that of the stator teeth arc,and the resultant phase EMF waveform exhibits negligible harmonics,as shown in Fig.20[33].The design procedure and a general power dimension equa-tion were derived analytically for the design of the FSPM machine with arbitrary slot/pole combinations in[34].In addi-tion,to predict electromagnetic performance with satisfied ac-curacy,a nonlinear adaptive lumped parameter magnetic circuit model,a magnetic network model considering saturation effect, an alternative technique based on the harmonic or Fourier model,and an analytical hybrid modeling technique combin-ing the advantages of the magnetic equivalent circuit and the Fourier analysis were proposed in[35]–[38],respectively.It should be noted that,due to the stator-PM configuration, the end-effect caused by the axialflux leakage is relatively serious,and the predictions from a conventional2-D model must be modified.Hence,a simple and effective method in investigating the end-effect on the stator-PM machine was proposed and verified by the experimental results[39],[40]. Moreover,a3-D lumped model was built to predict the per-formance in[41].Furthermore,the eddy current loss in the frame and magnets,iron loss,and proximity loss of the FSPM machine were analyzed in[42]and[43],respectively.The topology of the FSPM machine is not limited in the three-phase12/10-pole structure.Three-phase12/14-pole and 6/5-pole FSPM machines were investigated in[44]and[45] [Fig.21(a)]and[46][Fig.21(b)],respectively.In addition, eight/six-pole two-phase[47]and four/two-pole one-phase FSPM machines are shown in Fig.22,while the asymmetry rotor pole is employed to improve the start torque[48].Fig.23 shows thefive-phase FSPM machines[49].Fig.21.FSPM machines.(a)12/14-pole three phase[44].(b)Six/five-pole three phase[46].Fig.22.FSPM machines.(a)Eight/six-pole two phase[47].(b)Four/two-pole one phase[48].Fig.23.Five-phase FSPM machines[49].(a)All poles wound.(b)Alternator poles wound.5092IEEE TRANSACTIONS ON INDUSTRIAL ELECTRONICS,VOL.58,NO.11,NOVEMBER2011Fig.24.FSPM machines [50].(a)Conventional FSPM.(b)Alternator poles wound-1.(c)Alternator poles wound-2.(d)Alternator poleswound-3.Fig.25.Multitooth FSPM machines[52].Fig.26.Transverse flux FSPM machine [53].In addition,the combinations of stator and rotor pole num-bers,the winding connections,and the winding factors of the FSPM machines having all poles and alternate poles wound are analyzed in [50]and [51],as shown in Fig.24.The multitooth topologies of the FSPM machine are proposed and investigated in [52](Fig.25).Recently,a novel flux-switching transverse flux PM generator for low-speed wind power applications is proposed and analyzed by a 3-D finite element method [53],as shown in Fig.26.parison and SummaryThe comparisons between the three stator-PM machine them-selves and the stator-and rotor-PM machines have drawn a series of conclusions of significance [2],[54]–[58],which are summarized as follows.Similarities :1)Doubly salient structures are employed.2)The magnets are located on the stator,and conse-quently,the temperature rise of the magnets is much easier to control.3)The rotor is identical to that of an SR machine,namely,without windings or magnets,being mechan-ically robust,and able to operate at high speed.4)Concentrated windings are employed with shorter end parts,resulting in low copper consumption and winding resistance.Therefore,the stator-PM ma-chines are of high efficiency compared with the con-ventional overlapping winding machines.5)The electromagnetic torque is dominated by the PM excited torque,and the average reluctance torque is negligible.Differences :1)Due to different configurations of magnets,stator poles,and windings,the phase flux linkage in both FRPM and FSPM machines is bipolar,while in a DSPM machine,it is unipolar.2)The EMF per turn and the torque capability of an FSPM machine are significantly higher than those of the FRPM and DSPM machines due to the flux-concentration effect.3)The waveforms of the flux linkage and EMF of an FSPM machine are essentially sinusoidal with unskewed rotor,while in the DSPM and FRPM machines,they are more trapezoidal.Therefore,the DSPM and FRPM machines are more suitable for the BLDC drive,and an FSPM machine is more suitable for the BLAC drive.4)Due to flux concentration,flux switching,and smaller overlapping areas between the stator and rotor teeth in an FSPM machine,the magnetic saturation level in the teeth of the stator and rotor is very high,and it can reach 2.5T.Thus,the air-gap flux density in the FSPM machine can exceed 2.2T [57].5)In the FSPM machine,the coils are wound over two stator teeth between which one magnet is inset,while in the DSPM and FRPM machines,the coils are wound on each stator tooth.Hence,the end winding in an FSPM machine is slightly longer,while the amount of magnet materials is significantly higher.However,since the stator winding is concentrated,it is still significantly shorter than that in a conventional overlapping winding PM machine.In addition,flux concentrating can be utilized,and a low-cost magnet material,such as ferrite,can be used in an FSPM machine.CHENG et al.:OVERVIEW OF STATOR-PERMANENT MAGNET BRUSHLESS MACHINES 5093TABLE IQ UALITATIVE C OMPARISON OF THE T HREE S TATOR -PM MACHINES6)Among the three typical stator-PM topologies,the FSPM machine exhibits the highest torque capability and power density as revealed in [54],in which the electromagnetic torque of the FSPM machine is about 1.6times that of the DSPM machine under the same peak currents.However,the torque per magnets of the FRPM machine is higher than that of the FSPM machine [55].In addition,the cogging torque of the FSPM machine is the highest due to the flux-concentrated effect.7)In terms of demagnetization of the PM for the three stator-PM machines,briefly,the FRPM machine ex-hibits the weakest withstanding capability since the magnets are mounted on the stator teeth,and con-sequently,the MMF due to the armature currents is in series with that of the magnets,whereas for the FSPM and DSPM machines,since the armature reaction flux does not pass through the magnets,the irreversible demagnetization withstand capability is high,which makes it particularly suitable for flux-weakening operations.Table I summarizes the qualitative comparison among the key issues of the three stator-PM machines.IV .B ASIC C ONTROL S TRATEGIESThere are basically two types of operation modes for the stator-PM motor drives,namely,BLDC operation for the ma-chines with trapezoidal back EMF and BLAC operation for the machines with sinusoidal back EMF.In the BLDC operation,the control strategy of the stator-PM motor drive consists of two basic schemes,namely,current chopping control (CCC)and angle position control (APC),for constant-torque operation at speeds below the base speed and constant-power operation at speeds above the base speed,respectively,which are similar to those in an SR machine.Fig.27shows the typical current waveforms of an eight/six-pole DSPM motor [22].In the BLAC operation,field orientation control,i.e.,vector control,may be applicable to the stator-PM motor drive [59].Moreover,the current-hysteresis PWM,voltage space-vector PWM,and flux-weakening control were also adopted in the FSPM motor drives,respectively [60]–[62].Fig.28showstheFig.27.Typical current waveforms of a DSPM machine at the BLDC operation.(a)CCC mode.(b)APCmode.Fig.28.Measured current waveform of an FSPM machine at the BLACoperation.Fig.29.Stator interior PM topology [63].(a)Cross section.(b)Prototype.measured current waveform of an FSPM motor drive under vector control,showing a good sinusoidal phase current.V .T ORQUE R IPPLE M INIMIZATIONOwing to the nature of salient poles in both stator and rotor,the stator-PM machines suffer from higher torque ripple than traditional rotor-PM machines.Hence,different measures have been developed to minimize torque ripple in stator-PM machines.A.Improved Machine TopologyTo minimize the torque ripple,a modified topology (namely,the stator interior PM machine)was proposed,as shown in Fig.29,in which the conventional stator tooth shoe is employed and the magnets are inset [63].The predicted and experimen-tal results verify that the cogging torque can be significantly reduced.In addition,due to the simple rotor structure,the dummy slots can also be introduced to reduce the cogging torque,as shown in Fig.30for an FSPM machine [64].5094IEEE TRANSACTIONS ON INDUSTRIAL ELECTRONICS,VOL.58,NO.11,NOVEMBER2011Fig.30.Rotor dummy slots in the FSPM machine.(a)Rotor topology with dummy slots.(b)Comparison of the cogging torque with and without dummyslots.Fig.31.Measured torque and current waveforms (25ms/div,2.2Nm/div,and 3.33A/div).(a)Unoptimized.(b)Optimizedcontrol.Fig.32.Measured torque (upper trace)and current (lower trace)waveforms (5ms/div,2Nm/div,and 2.4A/div).(a)V oltage space-vector PWM.(b)Proposed method.B.Conduction Angle ControlIn [65],the genetic algorithm was used to optimize the conduction angle proposed for the DSPM motor.Fig.31shows the torque and current waveforms.The torque ripple factor is re-duced from 81%to 21%by using the proposed control method.C.Harmonic Current Injection ControlIn [66]and [67],a new harmonic current injection method was proposed to minimize the torque ripple of the DSPM and FSPM motors,respectively.In [67],based on the harmonic spectrum analysis of the cogging torque,a series of specific harmonic currents is added into the q -axis reference current,resulting in additional torque components to counteract the fundamental and second-order harmonic components of the cogging torque.Both simulations and experiments confirmed the effectiveness of the proposed method.Fig.32shows the measured torque and current waveforms.It can be seen that the proposed harmonic current injection method can reduce the torque ripple by 50%as compared to the voltage space-vector PWMmethod.Fig.33.12/8-pole SDFDS machine.(a)Configuration.(b)Prototype[68].Fig.34.Six/four-pole HEDSPM machine.(a)Using ferrite magnets [69].(b)Using NdFeB magnets [70].VI.E MERGING T RENDSIn addition to the achievements earlier,new developments have been achieved on the stator-PM machines recently.A.Wound-Field and Hybrid-Excitation StructuresAlthough the stator-PM machines offer unique advantages,they cannot maintain a high efficiency or a constant output voltage over a wide speed range due to an uncontrollable PM flux,which are crucial for some applications such as electric vehicles (EVs).To enable flux control,the idea of stator dou-bly fed doubly salient (SDFDS)machine was proposed [68],in which the dc field windings replace the PMs to facilitate flux control and online efficiency optimization.Fig.33shows the configuration and prototype of the SDFDS machine.The efficiency of the machine can be improved by about 10%by online efficiency optimizing.Nevertheless,the SDFDS machine inevitably produces the extra loss in field windings,hence degrading machine effi-ciency.To incorporate both magnets and dc field windings,hybrid excited DSPM (HEDSPM)machines were proposed in [69]–[72](Figs.34–36),in which the dc field windings work forCHENG et al.:OVERVIEW OF STATOR-PERMANENT MAGNET BRUSHLESS MACHINES5095Fig.35.12/8-pole HEDSPM machine.(a)Cross section.(b)Efficiency–speed characteristic[71].Fig.36.Parallel configuration of an HEDSPM machine[72].Fig.37.Field-excitationflux-switching machine[73].flux control and efficiency optimization.The starting response can be improved by supplying a positive dcfield current to strengthen theflux,while the constant-power operating range can be extended by supplying a negative dcfield current to weaken theflux.In addition,a three-phase wound-fieldflux-switching ma-chine was proposed in[73](Fig.37).Recently,novel hybrid-excitationflux-switching(HEFS)machines were proposed in [74]–[76],in which thefield windings are accommodated in the room saved by the reduction of the magnets in the original FSPM machine.As stated in[75],the HEFS machine(Fig.38) exhibits excellentflux-regulation capability,in which the PM flux can be strengthened to twice that of the pure-PM topology and can be weakened to almost zero,indicating an infinite constant-power range.B.Redundant and Fault-Tolerant StructureIn some applications such as steering and fuel pumps,where a continuous operation must be ensured,reliability may be a critical requirement.Therefore,the need for a high degree of reliability in a motor drive system has inspired much researchin Fig.38.Configurations of the HEFS motor[75].Fig.39.Measured torque(trace1)and coil-B1and coil-C1current (traces2–3)waveforms before and after coil-A1fault(10ms/div,3Nm/div, and6A/div).the area.To achieve high reliability,redundant or conservative design techniques have been employed in many motor drives. Because of the magnetic independence between motor phases and the circuit independence of the converter phases,the stator-PM motor drives inherently possess a fault-tolerant character-istic.To improve the performance of the stator-PM motor drive with an open-circuited fault,fault compensation strategies were proposed[77],[78].Fig.39shows the measured torque and healthy-coil current waveforms during the fault occurrence of an FSPM machine under fault-tolerant control.It can be seen that the average torque can be maintained almost the same by controlling the current in the healthy coils when an open-circuit fault occurs in one coil.Moreover,redundant stator-PM topologies were proposed to improve the fault-tolerant capabil-ity,especially in the vehicle motor drives,as shown in Fig.40 [79].In[80],a novelfive-phase fault-tolerant doubly salient electromagnetic generator for directly driven wind turbine was proposed,as shown in Fig.41.5096IEEE TRANSACTIONS ON INDUSTRIAL ELECTRONICS,VOL.58,NO.11,NOVEMBER2011Fig.40.Redundant stator-PM motor topologies.(a)Redundant DSPM motor.(b)Redundant FSPMmotor.Fig.41.Redundant stator-PM motor topologies [80].C.Memory PM Machine TopologyAlthough the dc field winding in both SDFDS motor and hybrid excited stator-PM motors enables the controllable air-gap flux,the use of dc field current inevitably causes additional power loss and degrades the efficiency.With the advent of the memory motors,the magnetization of PMs becomes online tunable.Hence,the concept of online-tunable flux-memory PMs was incorporated into the DSPM motor in such a way that the resulting flux-memory DSPM motor can offer an effective and efficient air-gap flux control [81].As shown in Fig.42(a),the memory DSPM motor adopts two-layer inner stator and outer rotor.In the stator,the armature windings are located in the outer layer,while both the PMs and magnetizing windings are placed in the inner layer,hence achieving a compact struc-ture.Since the outer rotor is simply composed of salient poles without PMs or windings,it is very robust.The PM material used in the motor is an aluminum nickel cobalt (AlNiCo)alloy.Fig.42(b)shows the measured back-EMF waveforms at different magnetization levels.It can be found that the back EMF can be effectively controlled for over four times.Due to the direct magnetization of PMs by a temporary current pulse in the magnetizing windings,the flux control is highly effective and highly efficient.D.Linear PM Machine TopologyThe linear PM motor is widely used because of its rapid dynamic response,high efficiency,and high power density.However,for long-stator applications such as underground traindrive systems,either the magnets or the armature windings,which are both expensive,have to be set on the stator.Recently,linear primary-PM machines,including the linear DSPM (LDSPM)and linear FSPM (LFSPM)types,have been pro-posed,which incorporate all of the merits of the rotary stator-PM machines.In [82]–[84],LFSPM machines were proposed,designed,and analyzed,such as feasible slot–pole number combinations and alternative stator winding configuration.In [85],a new structure of the LDSPM (Fig.43)was proposed and compared with the basic one.Three additional teeth and one piece of magnet are set at each end part of the two motors in order to reduce the end effect.The results show that the proposed method can avoid the asymmetry of the back-EMF waveforms and can reduce the cogging force and thrust force ripple,as shown in Fig.44.E.Advanced ControlDue to its strong nonlinear characteristics,the stator-PM mo-tors may not be exactly modeled.Hence,it is difficult to achieve high speed and torque performances by using the traditional control algorithm.Thus,some advanced control algorithms,such as sensorless control,vector control,and online efficiency optimization control,have been developed for the stator-PM machines.1)Position Sensorless Control:Similar to rotor-PM motor control,to turn on or off the phase windings at the spe-cific rotor positions,the rotor position information,which is traditionally measured by a physical sensor,is indispensable for the proper operation of the stator-PM motor.In order to avoid some difficulties resulting from the traditional sensor control method,the sensorless control of a DSPM motor drive was implemented [86].Detecting the induced back-EMF zero-crossing of unexcited winding was adopted.Fig.45shows the comparison of the position signals by physical sensor and by detecting circuits,illustrating that the real position signal lags behind the zero-crossing of the back EMF.Fig.46compares the speed rising process from standstill to the rated speed of 1500r/min between sensor and sensorless controls,showing that the DSPM motor drive with sensorless control offers almost the same performance as that with sensor control.To start the motor in sensorless control,the so-called “three-step startup。