滚珠丝杠副的参数计中算与选用流程
滚珠丝杠螺母副的选型与计算
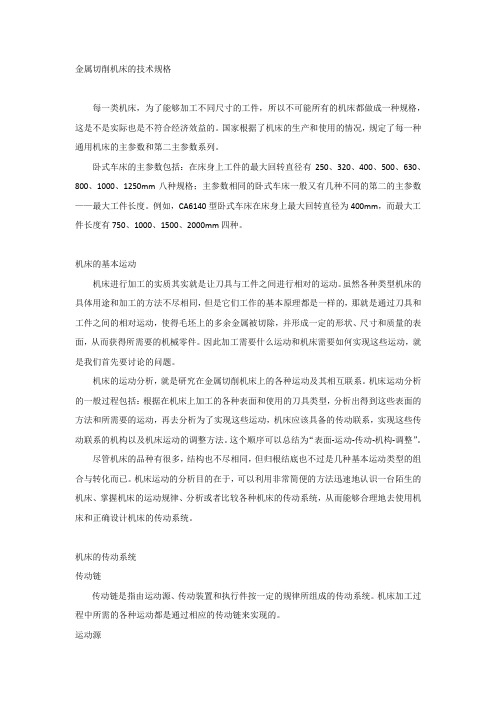
金属切削机床的技术规格每一类机床,为了能够加工不同尺寸的工件,所以不可能所有的机床都做成一种规格,这是不是实际也是不符合经济效益的。
国家根据了机床的生产和使用的情况,规定了每一种通用机床的主参数和第二主参数系列。
卧式车床的主参数包括:在床身上工件的最大回转直径有250、320、400、500、630、800、1000、1250mm八种规格;主参数相同的卧式车床一般又有几种不同的第二的主参数——最大工件长度。
例如,CA6140型卧式车床在床身上最大回转直径为400mm,而最大工件长度有750、1000、1500、2000mm四种。
机床的基本运动机床进行加工的实质其实就是让刀具与工件之间进行相对的运动。
虽然各种类型机床的具体用途和加工的方法不尽相同,但是它们工作的基本原理都是一样的,那就是通过刀具和工件之间的相对运动,使得毛坯上的多余金属被切除,并形成一定的形状、尺寸和质量的表面,从而获得所需要的机械零件。
因此加工需要什么运动和机床需要如何实现这些运动,就是我们首先要讨论的问题。
机床的运动分析,就是研究在金属切削机床上的各种运动及其相互联系。
机床运动分析的一般过程包括:根据在机床上加工的各种表面和使用的刀具类型,分析出得到这些表面的方法和所需要的运动,再去分析为了实现这些运动,机床应该具备的传动联系,实现这些传动联系的机构以及机床运动的调整方法。
这个顺序可以总结为“表面-运动-传动-机构-调整”。
尽管机床的品种有很多,结构也不尽相同,但归根结底也不过是几种基本运动类型的组合与转化而已。
机床运动的分析目的在于,可以利用非常简便的方法迅速地认识一台陌生的机床、掌握机床的运动规律、分析或者比较各种机床的传动系统,从而能够合理地去使用机床和正确设计机床的传动系统。
机床的传动系统传动链传动链是指由运动源、传动装置和执行件按一定的规律所组成的传动系统。
机床加工过程中所需的各种运动都是通过相应的传动链来实现的。
运动源运动源是给执行件提供动力和运动的装置。
滚珠丝杠选型计算经典版
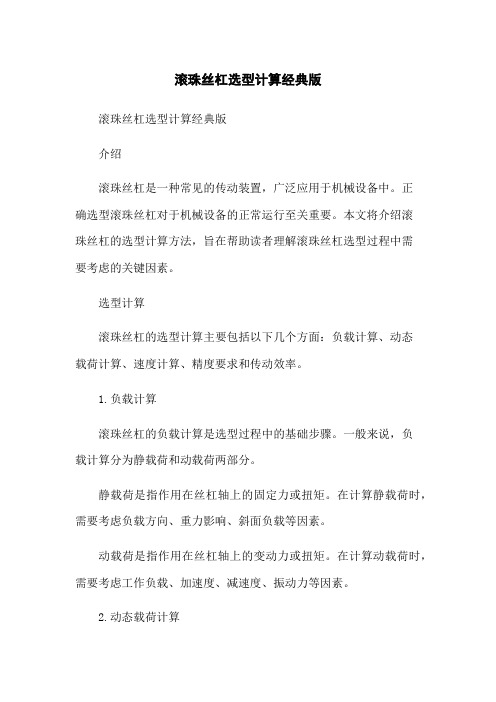
滚珠丝杠选型计算经典版滚珠丝杠选型计算经典版介绍滚珠丝杠是一种常见的传动装置,广泛应用于机械设备中。
正确选型滚珠丝杠对于机械设备的正常运行至关重要。
本文将介绍滚珠丝杠的选型计算方法,旨在帮助读者理解滚珠丝杠选型过程中需要考虑的关键因素。
选型计算滚珠丝杠的选型计算主要包括以下几个方面:负载计算、动态载荷计算、速度计算、精度要求和传动效率。
1.负载计算滚珠丝杠的负载计算是选型过程中的基础步骤。
一般来说,负载计算分为静载荷和动载荷两部分。
静载荷是指作用在丝杠轴上的固定力或扭矩。
在计算静载荷时,需要考虑负载方向、重力影响、斜面负载等因素。
动载荷是指作用在丝杠轴上的变动力或扭矩。
在计算动载荷时,需要考虑工作负载、加速度、减速度、振动力等因素。
2.动态载荷计算动态载荷是滚珠丝杠选型中的重要参数。
动态载荷是指在设定的工作条件下,丝杠所能承受的最大负载。
在动态载荷计算中,需要考虑负荷方向、负荷种类、工作时间等因素。
根据这些因素,可以计算出滚珠丝杠的额定动载荷。
3.速度计算速度是滚珠丝杠选型的另一个重要考虑因素。
滚珠丝杠的速度范围通常在制造商的产品手册中给出。
在进行速度计算时,需要考虑滚珠丝杠的传动形式、传动方式、旋转方向等因素。
根据这些因素,可以计算出滚珠丝杠的额定速度。
4.精度要求滚珠丝杠的精度要求是选型过程中不可忽视的因素。
滚珠丝杠的精度主要包括运动平稳性、重复定位精度和轮廓误差。
在进行精度要求计算时,需要考虑机械设备的应用要求、工作环境影响、传动误差等因素。
根据这些因素,可以选择适合的滚珠丝杠精度等级。
5.传动效率传动效率是评估滚珠丝杠性能的重要指标。
传动效率是指滚珠丝杠在传递功率时的能量损失情况。
在进行传动效率计算时,需要考虑滚珠丝杠的摩擦损失、滚珠与螺纹之间的接触损失等因素。
根据这些因素,可以评估滚珠丝杠的传动效率。
结论通过以上的选型计算,我们可以得出滚珠丝杠的合适尺寸和型号。
在实际选型过程中,还需考虑滚珠丝杠的价格、供货周期等因素,综合考虑后做出最佳选择。
(完整版)TBI滚珠丝杠选型计算举例讲解
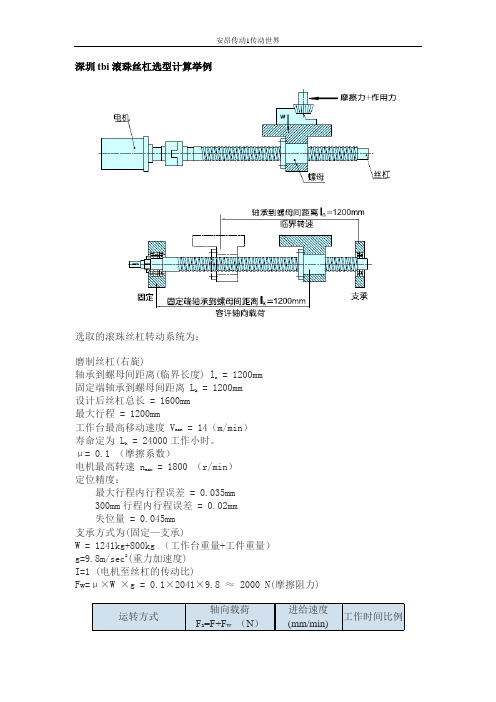
深圳tbi滚珠丝杠选型计算举例选取的滚珠丝杠转动系统为:磨制丝杠(右旋)轴承到螺母间距离(临界长度) ln= 1200mm固定端轴承到螺母间距离 Lk= 1200mm设计后丝杠总长 = 1600mm最大行程 = 1200mm工作台最高移动速度 Vman= 14(m/min)寿命定为 Lh= 24000工作小时。
μ= 0.1 (摩擦系数)电机最高转速 nmax= 1800 (r/min)定位精度:最大行程内行程误差 = 0.035mm300mm行程内行程误差 = 0.02mm失位量 = 0.045mm支承方式为(固定—支承)W = 1241kg+800kg (工作台重量+工件重量)g=9.8m/sec2(重力加速度)I=1 (电机至丝杠的传动比)Fw=μ×W ×g = 0.1×2041×9.8 ≈ 2000 N(摩擦阻力)运转方式轴向载荷F a=F+F w(N)进给速度(mm/min)工作时间比例无切削F1=2000V1=14000q1=15轻切削F2=4000V2=1000q2=25普通切削F3=7000V3=600q3=50重切削F4=11000V4=120q4=10F a --- 轴向载荷(N) F --- 切削阻力(N) Fw--- 摩擦阻力(N)从已知条件得丝杠编号:此设计丝杠副对刚度及失位都有所要求,所以螺母选形为:FDG(法兰式双螺磨制丝杠)从定位精度得出精度精度不得小于P5级丝杠FDG_-_X_R-_-P5-1600X____计算选定编号导程= 14000/18000≈7.7mm在此为了安全性考虑:P =10(mm)运转方式进给速度(mm/min)进给转速(r/min)无切削V1=14000n1=1400轻切削V2=1000n2=100普通切削V3=600n2=60重切削V4=120n2=12平均转速平均载荷时间寿命与回转寿命=24000×266×60=383040000转次额定动载荷以普通运动时确定fw取 1.4得:额定动载荷 Ca≥39673N以Ca值从FDG系列表及(丝杠直径和导程、丝杠长度表)中查出适合的类型为:公称直径: d0=40mm 丝杠底径: d=33.9mm 导程:Pho=10mm 循环圈数:4.5额定动载荷为:48244N。
滚珠丝杠螺母副的计算和选型

滚珠丝杠螺母副的计算和选型Δ3一、进给传动部件的计算和选型进给传动部件的计算和选型主要包括:确定脉冲当量、计算切削力、选择滚珠丝杠螺母副、计算减速器、选择步进电机等。
1、脉冲当量的确定根据设计任务的要求,X方向的脉冲当量为δx=0.005mm/脉冲,Z 方向为δz=0.01mm/脉冲。
2、切削力的计算切削力的分析和计算过程如下:设工件材料为碳素结构钢,σb=650Mpa;选用刀具材料为硬质合金YT15;刀具几何参数为:主偏角κr=45°,前角γo=10°,刃倾角λs=-0°;切削用量为:背吃刀量a p=1mm,进给量f=0.18mm/r,切削速度vc=90m/min。
查表得:C Fc=270,x Fc=1.0,y Fc=0.75,n Fc=-0.15。
=1.0;刃倾角、前角和刀尖圆弧查表得:主偏角κr的修正系数kκrFc半径的修正系数均为1.0。
由经验公式(3—2),算得主切削力F c=2673.4N。
由经验公式F c:F f:F p=1:0.35:0.4,算得进给切削力F f=935.69N,背向力F p=1069.36N。
3、滚珠丝杠螺母副的计算和选型(1)工作载荷F m的计算已知移动部件总重G=1300N;车削力F c=2673.4N,F p=1069.36N,F f=935.69N。
根据F z=F c,F y=F p,F x=F f的对应关系,可得:F z=2673.4N,F y=1069.36N,F x=935.69N。
选用矩形—三角形组合滑动导轨,查表,取K=1.15,μ=0.16,代入F m=KF x+μ(F z+G),得工作载荷F m=1712N。
(2)最大动载荷F Q的计算设本车床Z向在最大切削力条件下最快的进给速度v=0.8m/min,初选丝杠基本导程P h=6mm,则此时丝杠转速n=1000v/P h=133r/min。
取滚珠丝杠的使用寿命T=15000h,代入L0=60nT/106,得丝杠系数L0=119.7×106r。
滚珠丝杠的选取与计算书
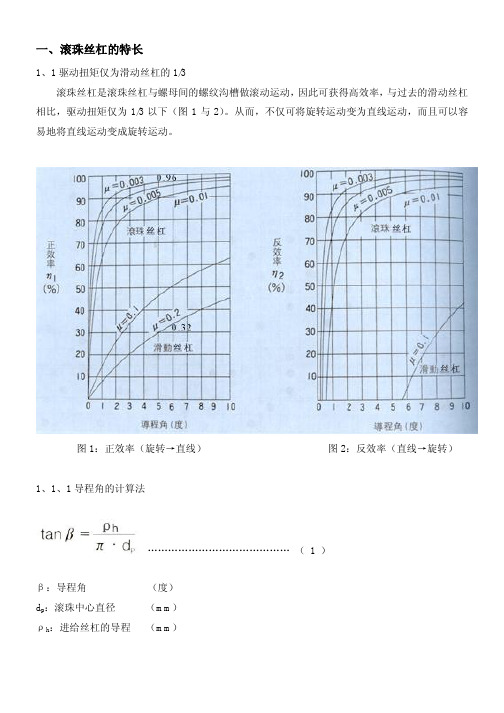
一、滚珠丝杠的特长1、1驱动扭矩仅为滑动丝杠的1/3滚珠丝杠是滚珠丝杠与螺母间的螺纹沟槽做滚动运动,因此可获得高效率,与过去的滑动丝杠相比,驱动扭矩仅为1/3以下(图1与2)。
从而,不仅可将旋转运动变为直线运动,而且可以容易地将直线运动变成旋转运动。
图1:正效率(旋转→直线)图2:反效率(直线→旋转)1、1、1导程角的计算法1、12推力与扭矩的关系当施加推力或扭矩时,所产生的扭矩或推力可用(2)~(4)式计算。
(1)获得所需推力的驱动扭矩T:驱动扭矩Fa:导向面的摩擦阻力Fa=μ×mgμ:导向面的摩擦系数g:重力加速度(9.8m/s2)m:运送物的质量(kg )ρh:进给丝杠的导程(mm )η:进给丝杠的正效率(图1)(2)施加扭矩时产生的推力Fa:产生的推力(N )T:驱动扭矩(N mm )ρh:进给丝杠的导程(mm )η:进给丝杠的正效率(图1)(3)施加推力时产生的扭矩T:驱动扭矩(N mm )Fa:产生的推力(N )ρh:进给丝杠的导程(mm )η:进给丝杠的正效率(图2)1、1、3驱动扭矩的计算例用有效直径是:32mm,导程:10mm(导程角:5O41’的丝杠,运送质量为500Kg的物体,其所需的扭矩如下(1)滚动导向(μ=0.003)滚珠丝杠及(μ=0.003,效率η=0.96)导向面的摩擦阻力Fa=0.003×500×9.8=14.7N驱动扭矩(2)滚动导向(μ=0.003)滚珠丝杠及(μ=0.2,效率η=0.32)导向面的摩擦阻力Fa=0.003×500×9.8=14.7N驱动扭矩1、2保证高精度雄联滚珠丝杠,在被恒温控制的工场里,用最高水平的机械设备进行研磨,直到组装,检查,实行彻底的品质管理体系,以保证其精度。
万能工具显微仪图3 导程精度测试数据1、3 能微量进给滚珠丝杠由于滚动运动,起动扭矩极小,不产生如滑动运动中晚出现的蠕动现象,所以能进行正确的微量进给。
滚珠丝杠选择计算
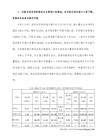
●按滚珠丝杠副支承的要求选择轴承的型号。
●确定轴承内径:为便于丝杠加工,轴承内径最好不大于滚珠丝杠的大径。在选用内循环滚珠丝杠副时必须有一端轴承内径略小于丝杠底径d2。其次轴承样本上规定的预紧力应大于轴承所承受最大载荷FBmax的1/3。
③有预加负荷的滚珠丝杠副还需按最大轴向负荷Fmax计算:Cam=feFmax(N)
式中:
Ln-预期工作时间(小时,见表5)
Ls-预期运行距离(km),一般取250km。
fa-精度系数。根据初定的精度等级(见表6)选。
fc-可靠性系数。一般情况fc=1。在重要场合,要求一组同样的滚珠丝杠副在同样条件下使用寿命超过希望寿命的90%以上时fc见表7选
滚珠丝杠副参数计算与选用
1、计算步骤
2、确定滚珠丝杠导程Ph
根据工作台最高移动速度Vmax , 电机最高转速nmax, 传动比等确定Ph。按下式计算,取较大圆整值。
Ph= (电机与滚珠丝杠副直联时,i=1)
3、滚珠丝杠副载荷及转速计算
这里的载荷及转速,是指滚珠丝杠的当量载荷Fm与当量转速nm。滚珠丝杠副在n1、n2、n3??????nn转速下,各转速工作时间占总时间的百分比t1%、t2%、t3%??????tn%,所受载荷分别是F1、F2、F3??????Fn。
滚珠丝杠副公称中径dom≈d2m+Dw(钢球直径)
图-5
一端固定,一端自由G-Z
一端固定,一端游动G-Y
二端支承J-J
二端固定G-G
6、确定滚珠丝杠副规格代号
按照计算出的Ph,Cam及传动方式,使用情况,可在样本中先查出对应的滚珠丝杠公称直径do,应注意do≥dom, Ca≥Cam,但不宜过大,否则会使滚珠丝杠副转动惯量偏大,结构尺寸也偏大。接着确定循环圈数,滚珠螺母规格代号及相关的安装连接尺寸。
滚珠丝杆的选择计算

毕业论文原文缩略一、课题的来源及现实意义论文目录一、课题来源及现实意义二、设计任务与总体方案的确定1、设计任务2、总体设计方案的确定三、机械部分XY工作台的设计1、主要设计参数及依据2、XY工作台进给系统受力分析3、XY工作台尺寸确定及各部分重量估算四、滚珠丝杠传动机构的确定1、滚珠丝杠副的确定2、X向Y向丝杆的强度分析3、强度验算4、效率计算五、直线滚动导轨的选型六、步进电机及传动机构的确定1、步进电机的选用2、扭矩及转动惯量的验算3、齿轮传动机构的确定七、步进电机惯性负载的计算八、传动系统刚度的讨论1、根据工作台不出现爬行的条件来确定传动系统的刚度2、根据微量进给的灵敏度来确定传动系统刚度九、消隙方法与预紧1、消隙方法的选用2、预紧电动位移台介绍电动位移台系统可实现多自由度的自动调整,包括方导轨电动位移台、圆导轨电动位移台、滑动单元电动位移台、V型导轨电动位移台、宽型电动位移台、防尘罩位移台、电动旋转台、X-Y-Z组合位移台,升降台等等,由于具有精度高,速度快,行程长,承载大,使用寿命长,自动化程度高等诸多优点,电动位移台系统越来越广泛的应用于科学实验,激光加工,自动检测,自动计量,自动控制等领域。
电动旋转台的关键部件是轴系和蜗轮蜗杆。
轴系在电动旋转台中起着定心和定向作用,对电动旋转台的承载、偏摆、寿命等指标起决定作用。
电动位移台的品质起决于关键部件包括螺杆、导轨、电机的质量,机体的材质和加工精度以及整机装调工艺水平对电动位移台的品质也有较大影响。
螺杆在电动位移台中起着传动作用,对电动位移台的定位精度、重复定位精度、轴向间隙、速度、分辨率等指标起决定作用。
一般采用滚珠螺杆、研磨丝杆和梯形丝杆。
滚珠螺杆与螺母通过钢球实现滚动传动,通过选择钢球直径或采用双螺母预压,可减少轴向间隙,提高刚性,因此,在传动精度、传动效率、刚性、寿命等方面有很大优势。
研磨丝杠和梯形丝杆的螺杆与螺母之间滑动传动,因此,传动效率低,速度慢,轴向间隙不容易消除。
滚珠丝杠计算参数
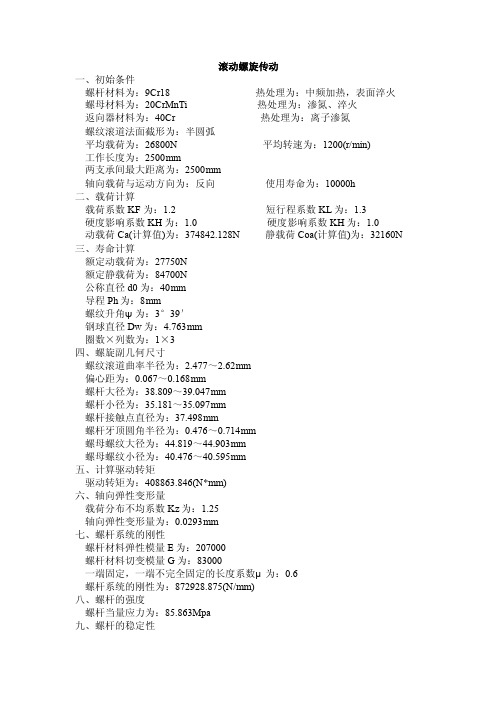
滚动螺旋传动一、初始条件螺杆材料为:9Cr18 热处理为:中频加热,表面淬火螺母材料为:20CrMnTi 热处理为:渗氮、淬火返向器材料为:40Cr 热处理为:离子渗氮螺纹滚道法面截形为:半圆弧平均载荷为:26800N 平均转速为:1200(r/min)工作长度为:2500mm两支承间最大距离为:2500mm轴向载荷与运动方向为:反向使用寿命为:10000h二、载荷计算载荷系数KF为:1.2 短行程系数KL为:1.3硬度影响系数KH为:1.0 硬度影响系数KH为:1.0动载荷Ca(计算值)为:374842.128N 静载荷Coa(计算值)为:32160N 三、寿命计算额定动载荷为:27750N额定静载荷为:84700N公称直径d0为:40mm导程Ph为:8mm螺纹升角ψ为:3°39′钢球直径Dw为:4.763mm圈数×列数为:1×3四、螺旋副几何尺寸螺纹滚道曲率半径为:2.477~2.62mm偏心距为:0.067~0.168mm螺杆大径为:38.809~39.047mm螺杆小径为:35.181~35.097mm螺杆接触点直径为:37.498mm螺杆牙顶圆角半径为:0.476~0.714mm螺母螺纹大径为:44.819~44.903mm螺母螺纹小径为:40.476~40.595mm五、计算驱动转矩驱动转矩为:408863.846(N*mm)六、轴向弹性变形量载荷分布不均系数Kz为:1.25轴向弹性变形量为:0.0293mm七、螺杆系统的刚性螺杆材料弹性模量E为:207000螺杆材料切变模量G为:83000一端固定,一端不完全固定的长度系数μ为:0.6螺杆系统的刚性为:872928.875(N/mm)八、螺杆的强度螺杆当量应力为:85.863Mpa九、螺杆的稳定性螺杆临界载荷为:68445.947N十、横向振动一端固定,一端不完全固定的系数μ1为:4.730 螺杆临界转速为:1549.023(r/min)十一、计算效率效率为:0.731。
- 1、下载文档前请自行甄别文档内容的完整性,平台不提供额外的编辑、内容补充、找答案等附加服务。
- 2、"仅部分预览"的文档,不可在线预览部分如存在完整性等问题,可反馈申请退款(可完整预览的文档不适用该条件!)。
- 3、如文档侵犯您的权益,请联系客服反馈,我们会尽快为您处理(人工客服工作时间:9:00-18:30)。
式中:Ft—预拉伸力(N) ,d2—滚珠螺纹底径(mm),E—杨氏弹性模量 2.1X10 (N/mm ) Δt —滚珠丝杠的温升 2~5℃ 8.确定滚珠丝杠副支承所用的轴承规格型号 �
� �
5
2
计算轴承所受的最大轴向载荷 F B
MAX
,有预拉伸的滚珠丝杠副应考虑到预拉伸力 Ft
按滚珠丝杠副的要求选择轴承的型号。 确定轴承内径:为便于丝杠加工,轴承内径最好不大于滚珠丝杠的大径。在选用内循环 浮动式滚珠丝杠副时必髯有一端轴承内径略小于丝杠底径 d2,其次轴承样本上规定的 预紧力应大于轴承所承受最大载荷 F B
机械装置中移动部件处在不同位置时第统刚度 K 是不同的的刚度最小处用 K min 表示。当滚珠丝杠副 轴向有工作载荷作用时, 传动系统中便产生弹性变形δ,且δ=F/K。 从而影响系统的传动精度, 而 K min 处系统受影响最大。 机床或机械装置的伺服系统精度大多在空载下检验。 空载时作用在滚珠丝杠副上最大轴向工作载荷是 静摩擦力 F0 。移动部件在 K min 处起动和返回时,由于 F0 方向变化将产生误差 2 F0 / K min (又称摩擦死 区误差)。它是影响重复定位精度的主要因素。一般占重复定位精度的(1/2~1/3) 。所以规定滚珠丝杠 副允许的最大轴向变形: F ⎛1 2⎞ δm = 0 ≈ ⎜ ~ ⎟• 影响定位精度最主要因素是滚珠丝杠副的精度,其次是滚珠 K min ⎝ 2 3 ⎠ 丝杠本身的拉压弹性变形(因这各弹性变形随滚珠螺母在滚珠丝杠上位置变而变化) 。以及滚珠丝杠 副摩擦力矩的变化…等。 一般估算是 δ m ≤ (1 / 4 ~ 1 / 5) 定位精度。以上两种方法估算出的小值取为 δ m 值 (单位μm) 。 � 估算滚珠丝杠的底径 d 2 m 10 F0 L FL = 0.078 0 πδ m E δm
� 电机最大启动转矩 Tr(N.m)
Tr = Tm + (TF + TP + Tb + T f ) i + Te
式中: i—电机到滚珠丝杠副的传动比。直联 i=1。Tb、Tf 分别为滚珠丝杠副两端支承产生的力矩
按滚珠丝杠副的预期运行距离 Ls(千米)计算:
Cm =
Ls Fm f w • (N ) Ph fa fc
�
有预加负荷的滚珠丝杠副还需按最大轴向负荷 Fmax 计算:
C am = f e Fmax
式中
Lh—预期工作时间(小时) (见表-5) 。 Ls—预期运行距离(km),一般取 250km。 fa—精度系数。根据
L≈ + + + + ≈ + ( 2 ~ 4) p h + 4 Ph + (4 ~ 6) Ph + (1 / 20 ~ 1 / 10) ≈ (1.05 ~ 1.1) + ( 10 ~ 14) P h
b. 滚珠丝杠副安装方式为两端支承或两端固定(见图-3) 10 F0 L FL = 0.039 0 πδ m E δm L— 两个固定支承之间的距离(mm) L ≈ 行程+安全距离+两个余程+螺母长度+一个支承长度 ≈ (1.1 ~ 1.2) + (10 ~ 14 )Ph
98 0.33
99 0.21
fc
表-8 负荷性质系数 fw
负荷性质
无冲击(很平稳) 1~1.2
轻微冲击 1.2~1.5
伴有冲击或振动 1.5~2
fw
表-9
预加负荷系数 fe
预加负荷类型
轻预载 6.7
中预载 4.5
重预载 3.4
fe
以上 3 种计算结果中选择较大值为滚珠丝杠副的 Cam。 4.按精度要求确定允许的滚珠丝杠的最小螺纹底径 d2m 估算滚珠丝杠的最大允许轴向变形量 δ m
MAX
的 1/3
�
有关轴承的其它验算项目可查轴承样本
9.滚珠丝杠副工作图设计 � � � � 滚珠丝杠副的螺纹长度 Ls = Lu + 2 Le Le 余程见 P67 页表-3 中 Le , Lu =行程+螺母长度 滚珠螺母的安装连接尺寸可查样本。 滚珠螺母不应该承受径向载荷及颠覆力矩,应使作用在螺母上的轴向合力通过丝杠轴 心。 可以用螺母的外圆柱面及法兰凸缘的内侧作安装基准, 同时要求螺母座孔与丝杠轴承孔 同心。螺母座孔端面与螺母座孔轴线垂直。当所受载何冲击力不大时,可仅用螺母法兰 凸缘的内侧面作安装基准面,这时应保证螺母座面与导轨垂直,装配时应找螺母外圆与 丝杠支承轴承孔同心。 插管式滚珠丝杠副水平安装时,为使滚珠的循环更加流畅,应将插管置于滚珠丝杠轴线 的上方。 设计螺母座,轴承座及紧固螺钉时要注意保证足够的刚性。在承载方向设计加强筋。 由工作图确定滚珠丝杠长度尺寸。
K K ; g. 螺母座,轴承座的刚度 K h
所以滚珠丝杠副传动系统的刚度 K 可按下式计算: 1 1 1 1 1 1 1 1 = + + + + + + K K s Kb KC K R Kt K k K h 1 1 1 1 = + + K Ks Kb KC
其中前三项最主要,而 K s 又占总量的(1/3~1/2)。所以一般情况下可按下式计算:
a. 滚珠丝杠副安装方式为一端固定,一端自由或游动时(见图-3) d 2 m ≥ 2 × 10
式中:E— 杨氏弹性模量 2.1 × 10 5 N / mm 2 ; δ m — 估算的滚珠丝杠最大允许轴向变形量(μm)
F0 — 导轨静摩擦力 (N)
F0 = µ 0 W ; L— 滚珠螺母至滚珠丝杠固定端支承的最大距离(mm)
精度等级
备注
5000~10000 10000~20000 20000 20000 15000 1000
Lh=250(天)x16(时) x10(年)x0.5(开机率)
1,2,3 1.0
4,5 0.9
7 0.8
10 0.7
fa
表-7 可靠性系数 fc
可靠性%
90 1.0
95 0.62
96 0.53
97 0.44
Ph =
Vmax nmax
计算出的 Ph 要取较大值圆整。 2.滚珠丝杠副的载荷及转速计算 � 最小载荷 Fmin 机器空载时滚珠丝杠副的传动力,如工作台重量引起的摩擦力。 � 最大载荷 Fmax 选机器承受最大负荷时滚珠丝杠副的传动力。如机床切削时,切削力滚珠丝杠轴向的分力与 导轨磨擦力之和即为 Fmax(这时导轨磨擦力是由工作台、工件、夹具三者总的重量以及切削 力在垂直导轨方向的分量共同引起) 。 � 滚珠丝杠副的当量转速 nm 及当量载荷 Fm
滚珠丝杠副在 n1, n2, n3, …nn 各种转速下,各转速工作时间占总时间的百分比 分别为 t1%, t2%, t3%… tn%,所承受的载荷分别是 F1, F1, F1… Fn。
nm = n1t1 % + n2 t 2 % + ⋅ ⋅ ⋅ ⋅ ⋅ ⋅ + nn t n %
Fm = 3 F13 n1t1 % + F23 n 2 t 2 % + ⋅ ⋅ ⋅ ⋅ ⋅ ⋅ + Fn3 n n t n % nm
Fp =
1 Fmax 3
Fp = ξC a
式中ξ值按表-10 选择,Ca 是额定动载荷,可在样本上查到。 表-10
预加负荷类型
轻预载 0.05
中预载 0.075
重预载 0.1
ξ
7.对预拉伸的滚珠丝杠副,计算行程补偿值 C 和预拉伸力 Ft 对于两端固定支承,需要预拉伸的滚珠丝杠副应规定目标行程补偿值 C,并计算预拉伸力
J L = ∑ Ji (
式中
Vj 2 ni 2 ) + ∑mj ( ) nm 2πnm
J = Jm + JL
Ji,ni—各旋转件的转动惯量(kg.m2)和转速(r/min)
mj,vj—各直线运动件的质量(kg)和速度(m/min) Jm,nm—电机的转动惯量(kg.m2)和转速(r/min)
� 加速转矩 Ta 和最大加速转矩 Tam
当负荷与转速接近正比变化时,各种转速使用机会均等时,可采用下列公式计算:
nm =
Fm =
nmax + nmin 2
2 Fmax + Fmin 3
3.确定预期额定动载荷 � 按滚珠丝杠副的预期工作时间 Lh(小时)计算:
C m = 3 60n m Lh •
�
Fm f w (N ) 100 f a f c
�
一般情况下,影响死区间隙的主要因素按影响程度自大到小排列顺序是: a. 滚珠丝杠本身的拉压刚度 K s ; 刚度 K c ; b. 支承轴承的轴向刚度 K b ; c. 滚珠丝杠副中滚珠与滚道的接触
d. 折合到滚珠丝杠上伺服系统的刚度 K R ; e. 联轴节的刚度 K t ; f. 滚珠丝杠副的扭转刚度
初定的精度等级(见表-6)选。
fc—可靠性系数。一般情况下 fc=1。在重要的场合,要求一组同样的滚珠丝杠副在同样条件下使用寿 命超过希望寿命的 90%以上时 fc(见表-7)选。 fw—负荷系数。根据负荷性质(见表-8)选。 fe—预加负荷系数(见表-9)
表-5 各类机械预期工作时间 Lh 机械类型 Lh(小时) 普通机械 普通机床 数控机床 精密机床 测示机床 航空机械 表-6 精度系数 fa
C = α ⋅ ∆t ⋅ Lu = 11.8∆t ⋅ Lu10 −6
式中:C—行程补偿值(μm) Δt—温度变化值 2~5℃ α—丝杠的线膨胀系数 11.8X10 /度
-6
Lu—滚珠丝杠副的有效行程(mm) Lu ≈ 工作台行程+螺母长度+两个安全行程 ≈ 行程+(8~14)Ph
2 πd 2 ∆IAE 2 Ft = = α ⋅ ∆t E = 1.95∆td 2 L 4