上海汽车制动系统ABS道路试验规范
汽车道路可靠性试验规范(2013[1].03.20)
![汽车道路可靠性试验规范(2013[1].03.20)](https://img.taocdn.com/s3/m/97e960e1e009581b6bd9ebbc.png)
Q/LFQ 力帆实业(集团)股份有限公司企业标准Q/LFQ G0010—2013 汽车道路可靠性试验(试行)2013-03-23发布2013-03-23实施前言本文件是以符合国家及行业标准为前提,针对本公司在新产品研发过程中对整车、总成、零部件开发认可试验而制定的。
本规范由范围、规范性引用文件、术语、内容等部分组成。
本文件按照GB/T 1.1-2009给出的规则起草。
本文件由重庆力帆(实业)集团股份有限公司汽车研究院提出。
本文件由重庆力帆(实业)集团股份有限公司汽车研究院负责起草。
本文件由重庆力帆(实业)集团股份有限公司汽车研究院负责归口。
本文件起草人:尤启明本文件批准人:关锋金本文件所代替标准的历次发布情况为:首次发布汽车道路可靠性试验1 范围本文件规定了质量考核及认可工作中道路整车性能、可靠性、零部件搭载行驶试验条件、试验程序、行使规范、试验记录、试验行驶里程和路面分配及可靠性评价。
本文件适用于公司所研发的汽车整车、总成零部件的质量考核及认可工作。
2 规范性引用文件下列文件对于本文件的应用是必不可少的。
凡是注日期的引用文件,仅所注日期的版本适用于本文件。
凡是不注日期的引用文件,其最新版本(包括所有的修改单)适用于本文件。
GB 1495-2002 汽车加速行驶车外噪声限值及测量方法GB/T 4970-2009 汽车平顺性试验方法GB/T 6323.1-1994 汽车操纵稳定性试验方法蛇行试验GB/T 6323.2-1994 汽车操纵稳定性试验方法转向瞬态响应试验GB/T 6323.3-1994 汽车操纵稳定性试验方法转向瞬态响应试验GB/T 6323.4-1994 汽车操纵稳定性试验方法转向回正性能试验GB/T 6323.5-1994 汽车操纵稳定性试验方法转向轻便性试验GB/T 6323.6-1994 汽车操纵稳定性试验方法稳态回转试验GB 7258-2012 机动车运行安全技术条件GB/T 12534-1990 汽车道路试验通则GB/T 12536-1990 汽车滑行试验方法GB/T 12539-1990 汽车爬陡坡试验方法GB/T 12543-2009 汽车加速性能试验方法GB/T 12544-1990 汽车最高车速试验方法GB/T 12545.1-2008 汽车燃料消耗试验方法第1部分:乘用车燃料消耗试验方法GB/T 12547-2009 汽车最低稳定车速试验方法GB/T 12548-1990 汽车速度表、里程表检验校正方法GB/T 12673-1990 汽车主要尺寸测量方法GB/T 12674-1990 汽车质量(重量)参数测定方法GB 12676-1999 汽车制动系统结构、性能和试验方法GB/T 12677-1990 汽车技术状况行驶检查方法GB/T 12678-1990 汽车可靠性行驶试验方法GB 18352.3-2005 轻型汽车污染物排放限值及测量方法(中国III、IV阶段)GB/T 18697-2002 声学汽车车内噪声测量方法GB 1495-2002汽车加速行驶车外噪声限值及测量方法QC/T 34-1992 汽车故障模式分类QC/T 900-1997 汽车整车产品质量检验评定方法3 整车磨合规范3.1 总则除试验大纲特殊要求以外,均按此规范进行磨合。
ABS测试系统使用说明-上海

智能型ABS轮速传感器综合测试台使用说明上海锦盈自动化仪器设备有限公司ABS轮速传感器智能综合测试台使用说明1.概述:汽车是国民经济中重要的交通工具。
ABS轮速传感器是汽车制动系统中一个重要的传感部件,其质量参数的优劣,直接影响到行车的安全性。
故对其技术参数检测的正确性是至关重要的。
本装置运用先进的电子测量及嵌入式计算机处理、控制技术,完成对ABS轮速传感器全性能的智能检测。
智能全自动检测保证了其测量参数的一致性及可靠性。
2.ABS轮速传感器主要参数指标及相关参数指标2.1.ABS轮速传感器主要参数指标2.1.1.ABS轮速传感器静态电阻测量范围:0Ω~2000Ω,精度:1%FS±5Ω;2.1.2.ABS轮速传感器速度输出信号峰-峰值测量范围: 0mV P-P~3000mV P-P;精度:1%FS±20 mV P-P;2.2. ABS轮速传感器相关参数指标2.2.1. ABS轮速传感器头部环境温度测量范围:0℃~+50℃,精度:1%FS±0.5℃;2.2.2. ABS轮速传感器智能测试台电机转速转速范围:100~2500 rpm。
精度:2%FS±2 rpm3.ABS轮速传感器智能综合测试台总体框图ABS轮速传感器智能综合测试台总体框图4.ABS轮速传感器智能综合测试台面板功能示意图面板功能示意(见图1)4.1.单功能键定义:4.1.1.“时间”设定键:按住“时间”键≦5S;按光标闪动位进行“时间”设定;4.1.2.“间隙”设定键:按住“间隙”键≦5S;按光标闪动位进行“间隙”设定;4.1.3.“转速”设定键:按住“转速”键≦5S;按光标闪动位进行“转速”设定;4.1.4.上翻键,按住“上翻”键,数字从0~9变化;4.1.5.右移键,按住“右移”键,光标向右移动;4.1.6.确认键,按“确认”键确认所选定的功能。
4.2. “双键同时操作”组合功能键定义:4.2.1.“时间”键+ = 启动电机,进入运行状态;4.2.2.“间隙”键+ = 停止电机;4.2.3.键+ 键≥ 5S 进入华普/万象型号切换选择;再按键选择:“P033”—万象(后轮)、“P063”—华普(后轮);4.2.4.“转速”+ 键≥ 5S,在运行状态清除“序号和合格数”。
-汽车防抱制动系统性能要求和试验方法【国标】
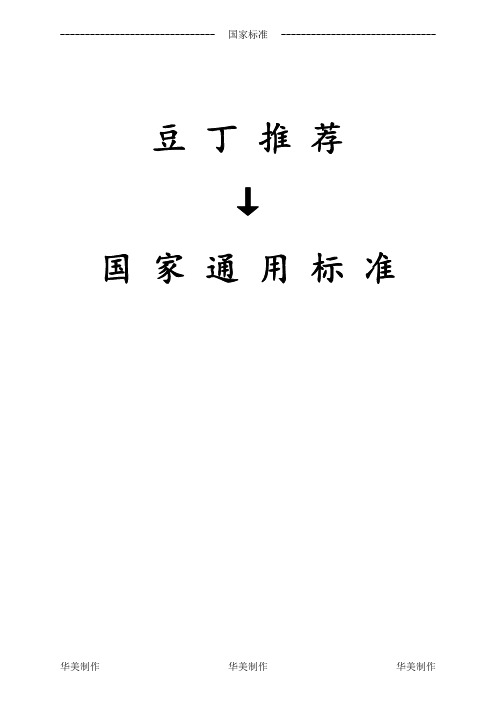
中华人民共和国国家标准
汽车防抱制动系统性能要求和试验方法
Ve hic le sa nt i-lockb rakings ystems performancer equirementsa ndt estp rocedures
GB 13594一 92
本标准参照采用ECE/R13附件 13《带防抱装置的车辆的试验要求》。
c. 测 制 动因数 ZFs和 Z。方法参服 6.5-4.3;
d 按 下 式确定附着系数利用率(E)
对 于 前 轴 :
Zm ·Fm一 0.0 15F m2
E,= ,一 ,
H- , 、
人(Pm ‘十了GFH’`'.1
… … 。.。。.。… … 。二。·。二。… (6)
对于后轴 :
鱼
EZ =
Z- .F。一 0.01 rm)
L— 轴 距 ,m 。 6.5-4.3 确定附着系数利用率(E)试验
8. 装 有 一、二类防抱系统的车辆,确定 K值后,在同一路面上立即做试验确定(E); b 重 新 联接好防抱系统,使各轴制动器正常工作; c. 促 动 管路压力为厂定值上限; d. 车 辆 初速度为 50k m/h,在相应路面上进行制动; e. 测 量 车速从 40k m/h减速到 20k m/h所经历的时间“t"(s); f. 装 防 抱系统车辆的制动因数(Z-)按(3)式确定。 B. 重 复 上述试验三次,求出Z-的算数平均值 乙。
实验一ABS道路试验

实验一越野车ABS性能道路试验一、实验目的1.熟悉越野车ABS系统及工作原理以及测试系统的组成;2.通过实车ABS道路试验感知ABS制动液压力变化,并根据测试系统记录的有关曲线,分析ABS的工作过程。
3.能够根据相关的标准对检测结果做出正确的结论。
二、主要设备1.实验用哈弗越野车2.汽车ABS车载实验、监控系统三、实验原理(一)ABS的组成及原理参见教材(二)ABS道路实验1.非紧急制动实验目测非紧急制动时实验车辆的制动距离及经制动踏板感知制动液压力变化的情况。
2.紧急制动试验记录紧急制动时实验车辆的制动距离及经制动踏板感知制动液压力变化的情况;根据车载测试系统记录的相关曲线,判断制动时车轮是否抱死,滑移率大小以及评价ABS的性能是否令人满意。
四、实验步骤(一)非紧急制动试验起动汽车,加速到30~40公里/小时,以适当的力度踩制动踏板使实验车停止运动,目测制动距离,感知制动液压力变化情况。
(二)紧急制动试验起动汽车,加速到30~40公里/小时,快速踩制动踏板以触发ABS制动系统,制动实验车到停止,记录紧急制动时ABS系统的相关过程数据,如制动液压力曲线、轮速、制动距离等。
五、实验注意事项1.驾驶实验车人员必须有驾驶证,并有半年以上的驾车经验,车上所有参与实验的人员必须系牢安全带,车上人员总数不得超过5人;2.负责记录实验数据的人员必须抱紧笔记本电脑,确保电脑在紧急制动期间与发生撞击。
3.紧急制动时,必须等车辆停稳后才能记录相关实验数据;4.驾车者必须在实验数据的记录完毕后才能重新起动车辆;5.实验时车辆的单向行驶路程不宜超过500米;6.注意行车安全,避免在行人密集的道路上做实验。
六、实验数据、现象记录从测试系统中拷贝所记录的实验数据;记录经由踏板感知的制动液压力变化情况七、思考题或讨论题1.ABS工作原理。
2.ABS门限逻辑控制算法。
3.非紧急制动与紧急制动的区别。
ABS

引言随着ABS装臵的广泛应用,检测ABS性能也显得越来越重要。
ABS 性能的好坏直接影响到行车的安全。
我国现有的各种制动检验台都无法检测装有ABS汽车的制动性能。
目前装有ABS装臵的汽车,测试制动性能只能采用路试,道路试验需要建造ABS性能专用跑道,ABS性能专用跑道投资大,而且每次ABS性能测试前,对试验路段要进行仔细地清洗,准备试验路段的时间较长、试验费用较高,而且道路试验过程存在一定安全风险。
目前,我国只有海南汽车试验研究所的汽车试验场等少数单位才有ABS的专用试验跑道[]2。
对于汽车ABS生产厂家批量生产的汽车ABS产品的质量检测和在用汽车的ABS性能定期测试,目前只有在道路上进行行车紧急制动,凭驾驶员的感觉来判断ABS的工作是否正常。
随着汽车市场对ABS需求的大量增加,为快速、有效、经济地对ABS性能进行检测,迫切需要采用室内试验台来对汽车ABS性能进行试验研究。
2004年04月国家交通部发布了交通行业标准()JT T-“汽车防抱制动系统检测技术条件”,标准规定/5102004了具有防抱制动装臵的汽车制动系统的技术要求及检测方法。
该标准的出台,为汽车ABS检测试验台的研究开发提供了依据。
目前,国内有关汽车ABS检测试验台的研制报道不多,已研制的汽车ABS检测试验台只能检测3吨质量以下的汽车,对大吨位汽车试验台的研制则未见相关报道。
本文设计的ABS试验台主要针对大吨位汽车的ABS检测。
第一章汽车ABS性能检测的基本原理1.1 ABS的工作原理及检测原理1.1.1 ABS的工作原理汽车制动防抱死系统(ABS)是在传统的汽车制动系统中增加轮速传感器、制动压力调节阀和电子控制器(ECU)组成[]16。
ABS系统的基本工作原理是:由安装在车轮附近的测速传感器在车辆制动时测量出车轮的瞬间转速(轮速),计算出此时车轮角减速度和车辆的行驶速度(车速),并依据瞬时车速与轮速计算出车辆的滑移率,控制器依据一定的数学模型操纵压力调节器调整制动管路中的制动液压力,改变制动器的制动力,使车轮的滑移率保持在一定水平上(约为20%),此时制动器的制动力趋近地面制动力最大值,车轮处于半抱半滚的状态,此时车辆的制动方向稳定性较好,车辆的制动性能处在最佳的状态下[]17.18。
上海WABCO的ABS instruction
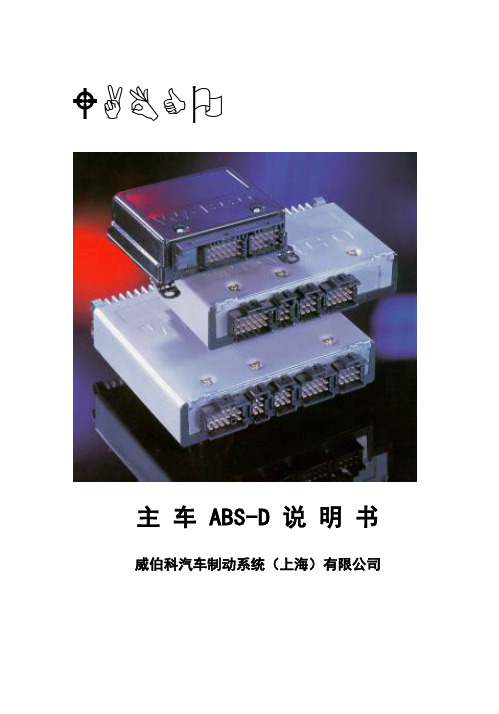
✌主车 ABS-D 说明书威伯科汽车制动系统(上海)有限公司目录1. ABS系统简介⋯⋯⋯⋯⋯⋯⋯⋯⋯⋯⋯⋯⋯⋯ 32. ABS系统的组成⋯⋯⋯⋯⋯⋯⋯⋯⋯⋯⋯⋯⋯⋯ 3 2.1 ABS系统组成部件⋯⋯⋯⋯⋯⋯⋯⋯⋯⋯⋯⋯⋯ 32.2 ABS系统的布置⋯⋯⋯⋯⋯⋯⋯⋯⋯⋯⋯⋯⋯⋯ 33. ABS工作原理和部件安装⋯⋯⋯⋯⋯⋯⋯ 4 3.1 齿圈的安装⋯⋯⋯⋯⋯⋯⋯⋯⋯⋯⋯⋯⋯⋯⋯⋯ 4 3.2 传感器⋯⋯⋯⋯⋯⋯⋯⋯⋯⋯⋯⋯⋯⋯⋯⋯⋯⋯ 4 3.2.1传感器的安装⋯⋯⋯⋯⋯⋯⋯⋯⋯⋯⋯⋯⋯⋯ 4 3.2.2 传感器与齿圈的配合⋯⋯⋯⋯⋯⋯⋯⋯⋯⋯ 5 3.2.3 传感器的测试⋯⋯⋯⋯⋯⋯⋯⋯⋯⋯⋯⋯⋯⋯ 6 3.3 电磁阀⋯⋯⋯⋯⋯⋯⋯⋯⋯⋯⋯⋯⋯⋯⋯⋯⋯⋯ 6 3.3.1 电磁阀的安装⋯⋯⋯⋯⋯⋯⋯⋯⋯⋯⋯⋯⋯⋯ 6 3.3.2 电磁阀的测试⋯⋯⋯⋯⋯⋯⋯⋯⋯⋯⋯⋯⋯⋯ 63.4 ASR差动制动阀⋯⋯⋯⋯⋯⋯⋯⋯⋯⋯⋯⋯⋯⋯⋯⋯63.5 双通单向阀⋯⋯⋯⋯⋯⋯⋯⋯⋯⋯⋯⋯⋯⋯7 3.6 导线的连接⋯⋯⋯⋯⋯⋯⋯⋯⋯7 3.7 驾驶室线束⋯⋯⋯⋯⋯⋯⋯⋯⋯⋯⋯⋯⋯73.8 电子控制单元ECU⋯⋯⋯⋯⋯⋯⋯⋯⋯⋯⋯⋯⋯⋯⋯⋯73.9 开关与指示灯⋯⋯⋯⋯⋯⋯⋯⋯⋯⋯⋯⋯⋯7 3.9.1 ABS/ASR灯⋯⋯⋯⋯⋯⋯⋯⋯⋯⋯7 3.9.2 开关⋯⋯⋯⋯⋯⋯⋯⋯⋯⋯⋯⋯⋯⋯⋯84 如何判断ABS正常工作⋯⋯⋯⋯⋯⋯⋯⋯⋯⋯⋯⋯⋯⋯⋯⋯⋯84.1 观察ABS指示灯⋯⋯⋯⋯⋯⋯⋯⋯⋯⋯⋯⋯⋯⋯⋯⋯84.2 紧急制动⋯⋯⋯⋯⋯⋯⋯⋯⋯⋯⋯⋯⋯⋯⋯⋯84.3 确认ABS在工作⋯⋯⋯⋯⋯⋯⋯⋯⋯⋯⋯⋯⋯⋯95 ABS系统诊断方法⋯⋯⋯⋯⋯⋯⋯⋯⋯⋯⋯⋯⋯⋯⋯9 5.1 诊断仪⋯⋯⋯⋯⋯⋯⋯⋯⋯⋯9 5.2 PC诊断⋯⋯⋯⋯⋯⋯⋯⋯⋯⋯⋯10 5.3 便携式诊断仪⋯⋯⋯⋯⋯⋯⋯⋯⋯⋯10 5.3.1诊断仪连接10 5.3.2 故障查找⋯⋯⋯⋯⋯⋯⋯⋯⋯⋯⋯⋯⋯⋯⋯⋯105.3.3 故障删除⋯⋯⋯⋯⋯⋯⋯⋯⋯⋯⋯⋯⋯⋯⋯⋯11 5.3.4 系统显示⋯⋯⋯⋯⋯⋯⋯⋯⋯⋯⋯⋯⋯⋯⋯⋯11 5.3.5 系统格式化⋯⋯⋯⋯⋯⋯⋯⋯⋯⋯⋯⋯⋯⋯⋯11 5.4 闪码诊断⋯⋯⋯⋯⋯⋯⋯⋯⋯⋯⋯⋯⋯⋯⋯⋯11 5.4.1 基本术语⋯⋯⋯⋯⋯⋯⋯⋯⋯⋯⋯⋯⋯11 5.4.2 故障诊断⋯⋯⋯⋯⋯⋯⋯⋯⋯⋯⋯⋯⋯⋯12 5.4.3 故障清除⋯⋯⋯⋯⋯⋯⋯⋯⋯⋯⋯⋯⋯⋯12 5.4.4 系统代码⋯⋯⋯⋯⋯⋯⋯⋯⋯⋯⋯⋯⋯⋯12 5.4.5 系统格式化⋯⋯⋯⋯⋯⋯⋯⋯⋯⋯⋯⋯⋯⋯13 5.4.6 闪码诊断程序⋯⋯⋯⋯⋯⋯⋯⋯⋯⋯⋯⋯⋯⋯14 5.4.7 闪码表⋯⋯⋯⋯⋯⋯⋯⋯⋯⋯⋯⋯⋯⋯15 5.4.8 故障代码表⋯⋯⋯⋯⋯⋯⋯⋯⋯⋯⋯⋯⋯⋯165.4.9 修理指导/故障检测⋯⋯⋯⋯⋯⋯⋯⋯⋯⋯⋯⋯⋯⋯⋯⋯⋯⋯⋯⋯⋯⋯⋯⋯206. ABS的使用⋯⋯⋯⋯⋯⋯⋯⋯⋯⋯⋯⋯⋯⋯⋯⋯⋯22附1:ABS-D系统零部件明细表⋯⋯⋯⋯⋯⋯⋯⋯23 附2:ABS服务站明细⋯⋯⋯⋯⋯⋯⋯⋯⋯⋯⋯24 附3:ABS-D系统接线图841 801 151 0⋯⋯⋯25附4:ABS-D系统接线图 841 801 277 0 2770⋯⋯⋯⋯⋯⋯⋯⋯⋯⋯26附5:ABS-D系统接线图 841 801 278 0 271.ABS 系统简介ABS(Anti-lock braking system)是一个在制动期间监视和控制车辆速度的电子系统。
ABS性能试验
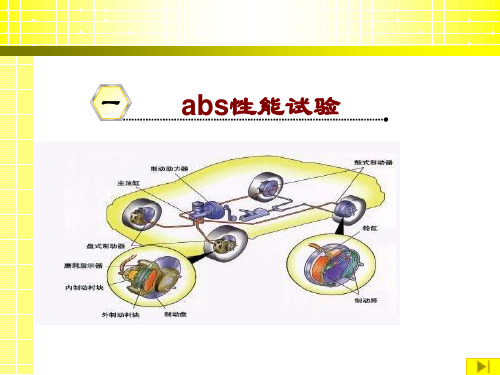
数 利 用 率
ABS定型试验分析 为实现K值得测量和计算, 需要对单轴进行制动, 附 为此在气压管路中设计了4 只改造过的继动阀,使得试 着 验过程中不用改变制动系统而进行正常制动和手控制 系 动。
数 利 用 率
ABS定型试验分析
2 .附加试验 附加制动试验应在发动机脱开, 用满载和空载两 种情况进行。试验时车辆不应驶出试验跑道。 附加试验的目的是在不同的特定制动工况下检 查A BS 控制的质量。总的要求为在全行程作用制动 踏板时,控制轮不允许抱死(仅允许短暂的车轮抱死; 车 速低于15 k m /h 的车轮抱死是允许的), 车辆必须保持 稳定性和可操纵性,试验过程中允许驾驶员操纵转向 盘。另外对车辆在满载和空载分别进行试验。
能 耗 试 验
ABS定型试验分析
为保证制动时辅助回路的气体不会回流到第一, 第二制动回路中,在系统中可以设计安装2 个单向阀, 用于切断辅助回路与制动回路之间的气流流动。为保 证当能耗试验分几个阶段进行时, 切断给储气筒供气, 能 在调压阀和四回路保护阀之间安装了一个手动的开关 耗 阀,该开关阀在驾驶室内方便操纵,管理示意图如下图 试 所示。
3 .对开路面(不同附着系数的路面)附着系数利用率 该要求仅对满载的带有一类A BS 的车辆。该试 验与对开路面的附加试验同时进行, 试验工况为K H ≥ 0.5 同时K H/ K L ≥2 , 并且车辆初始速度为v = 50k m /h 。评价的指标是ZMA ls( 在对开路面上A BS 起作用 时的制动强度) ≥0. 7 5[ (4 K L 十KH)/5 〕和ZM ALS ) KL.
ABS定型试验分析
若一次制动过程无法达到要求的制动时间, 则允 许分阶段完成, 最多不超过4 次。如果试验分阶段进 行, 则各次制动之间不应补充能量。在完成1 5 s 的制 动过程后, 切断对制动系统的供能, 连续作用制动踏板 。若1 5 s制动一次完成, 则连续促动踏板4 次(全力促 动踏板保持5s , 释放约5 s , 再次促动),当第5 次踩下制 动踏板时, 至少应满足规定的满载车辆的应急制动性 能要求。该要求可通过在高附着系数路面上验证检查 , 也可通过测定第5 次制动时管路压力进行判定。
《电动汽车再生制动防抱死道路试验方法》——编制说明

《电动汽车再生制动防抱死道路试验方法》编制说明一、工作简况1.1 任务来源《电动汽车再生制动防抱死道路试验方法》团体标准由中国汽车工程学会批准立项。
本标准是《插电式混合动力汽车试验方法》系列标准的一部分。
《插电式混合动力汽车试验方法》系列标准由清华大学牵头,参加单位有中国汽车技术研究中心有限公司、中国科学院电工研究所、上海汽车集团股份有限公司、郑州宇通客车股份有限公司、浙江吉利控股集团有限公司、奇瑞汽车股份有限公司、浙江亚太机电股份有限公司。
本标准由中国汽车技术研究中心有限公司牵头,参加单位有清华大学、中国科学院电工研究所、上海汽车集团股份有限公司、浙江吉利控股集团有限公司、奇瑞汽车股份有限公司。
1.2编制背景与目标目前,再生制动功能已经成为在售电动汽车的常规配置,再生制动功能除了可以提升整车能效,还与制动安全密切相关,尤其是制动防抱过程的制动安全性。
为此,本标准对电动汽车再生制动防抱死道路试验方法进行了规定。
1.3主要工作过程本标准于2018年6月立项;2018年7月-2018年9月研究、起草了标准框架;2018年10月-2019年4月进行了标准相关的试验操作工作;2019年5月-2019年10月进行了标准编写工作;2019年11月-2020年3月,对标准进行了讨论和修改。
预计2020年10月底之前完成标准报批稿。
二、标准编制原则和主要内容2.1标准制定原则在充分总结和比较了国内外再生制动安全性试验方法的基础上,本标准对再生制动启动方式、路面附着系数、试验车速等方面做了详细的规定,以确保再生制动防抱死性能测试的准确性和可信性。
2.1.1通用性原则本标准提出的电动汽车再生制动防抱死道路试验方法适用于装备再生制动系统的M1类、N1类汽车,通用性高。
2.1.2指导性原则本标准包含收加速踏板启动再生制动和踩制动踏板启动再生制动两种情形下的制动安全性道路试验方法,为进行电动汽车再生制动防抱死性能的评价提供指导。