数控作业指导书
数控车床作业指导书

数控车床作业指导书一、引言数控车床是一种自动化加工设备,广泛应用于机械加工领域。
本作业指导书旨在提供数控车床操作人员进行作业时的准确指导,确保作业的安全、高效和质量。
二、作业准备1. 确认工件和刀具根据生产定单或者工艺要求,确认待加工的工件和所需的刀具类型、规格。
2. 设置机床参数根据工艺要求,设置数控车床的相关参数,包括切削速度、进给速度、切削深度等。
3. 安装夹具和工件使用合适的夹具将工件安装在数控车床的工作台上,确保工件的稳固固定。
三、操作步骤1. 打开数控车床电源按照设备操作手册的指示,打开数控车床的电源,并确保设备正常启动。
2. 加载加工程序使用数控车床的控制面板,加载预先编写好的加工程序。
确保程序的正确性和完整性。
3. 检查刀具检查刀具的磨损程度和刀尖的状况,必要时更换刀具。
4. 调整刀具补偿根据工艺要求,通过数控车床的控制面板调整刀具的补偿值,确保加工精度。
5. 启动加工按下启动按钮,开始数控车床的加工过程。
在加工过程中,操作人员需要密切观察加工状态,确保一切正常。
6. 监控加工过程使用数控车床的监控系统,监测加工过程中的切削力、温度等参数,及时调整加工参数以确保加工质量。
7. 完成加工加工完成后,住手数控车床的运行,并进行必要的清理和维护工作。
四、安全注意事项1. 穿戴个人防护装备操作人员应穿戴好安全帽、防护眼镜、防护手套等个人防护装备,确保自身安全。
2. 遵守操作规程操作人员应严格遵守数控车床的操作规程,不得违反安全操作要求。
3. 防止意外启动在进行刀具更换、调整和清理工作时,务必切断数控车床的电源,防止意外启动造成伤害。
4. 注意机床周围环境保持数控车床周围的工作环境整洁,防止杂物堆积和滑倒等意外事故发生。
5. 定期维护保养对数控车床进行定期的维护保养,确保设备的正常运行和安全性能。
五、质量控制1. 加工精度操作人员应根据工艺要求,通过调整刀具补偿、加工参数等方式,确保加工精度达到要求。
数控车作业指导书

数控车作业指导书引言概述:数控车作业指导书是为了匡助操作人员正确、高效地使用数控车进行加工而编写的指导手册。
本文将从五个方面详细介绍数控车的操作要点和注意事项,以匡助读者更好地掌握数控车的使用技巧。
一、数控车的基本操作1.1 机床开机与关机- 开机前应检查机床各部位是否正常,如床身、导轨、润滑系统等。
- 关机时应先住手加工程序,然后关闭电源和液压系统,最后对机床进行清洁。
1.2 数控系统的操作- 启动数控系统后,应按照系统提示进行登录和密码验证。
- 学习数控系统的基本功能,如程序编辑、坐标系设定、刀具补偿等。
1.3 加工程序的加载与运行- 加工程序应按照规定的格式编写,并保存在适当的位置。
- 加载程序前,应检查程序是否正确、刀具是否安装正确。
- 运行程序时,要注意观察机床运行状态,及时处理异常情况。
二、数控车的安全操作2.1 安全防护措施- 操作人员应穿戴好防护装备,如手套、护目镜、防护服等。
- 在加工过程中,严禁将手部或者其他身体部位挨近刀具。
2.2 切削液的使用- 使用切削液时,应按照规定的比例进行配制。
- 切削液应定期更换,保持清洁,以确保加工质量和操作人员的安全。
2.3 废弃物处理- 废弃物应分类存放,并按照像关规定进行处理和清理。
- 废弃液体和废弃物料的处理要符合环保要求。
三、数控车的刀具管理3.1 刀具的选择与安装- 根据加工要求选择合适的刀具,并检查刀具是否完好。
- 刀具的安装要正确,刀尖要与工件接触平面垂直。
3.2 刀具的磨损与更换- 定期检查刀具的磨损情况,根据磨损程度及时进行更换。
- 更换刀具时,要注意刀具的型号和规格,以免影响加工质量。
3.3 刀具的保养与储存- 使用完毕后,应对刀具进行清洁和保养,防止生锈和损坏。
- 刀具的储存要放置在干燥、通风的地方,避免受潮和变形。
四、数控车的加工技巧4.1 加工参数的设置- 根据工件材料和加工要求,合理设置加工参数,如进给速度、切削速度等。
数控车床作业指导书

数控车床作业指导书一、概述数控车床是一种高精度、高效率的机械加工设备,广泛应用于各个行业。
为了确保数控车床的正常运行和操作人员的安全,制定本作业指导书,旨在提供数控车床的操作流程、注意事项和维护保养方法。
二、操作流程1. 准备工作a. 检查数控车床的电源、润滑系统和冷却系统是否正常运行。
b. 准备所需的刀具、夹具和工件。
c. 确保操作人员佩戴好防护设备,如安全眼镜和手套。
2. 开机操作a. 打开数控车床的电源,确保电源指示灯亮起。
b. 启动润滑系统和冷却系统,确保润滑和冷却正常运行。
c. 按照数控车床的操作界面要求,进行开机自检和系统初始化。
3. 工件装夹a. 根据工件形状和尺寸,选择合适的夹具进行装夹。
b. 使用卡尺或千分尺测量工件的尺寸,确保装夹正确。
4. 刀具选择和装配a. 根据工件的加工要求,选择合适的刀具。
b. 使用刀具装配工具将刀具装配到车床上,并进行刀具长度和刀具半径的设置。
5. 加工参数设置a. 进入数控车床的操作界面,选择加工程序。
b. 根据工件的要求,设置加工参数,如进给速度、切削速度和切削深度。
6. 加工操作a. 将工件放置到夹具上,并进行固定。
b. 启动数控车床的自动运行模式,开始加工操作。
c. 监控加工过程,注意观察切削情况和加工精度。
d. 定期清理切屑和润滑剂,保持工作环境整洁。
7. 加工完成a. 加工完成后,停止数控车床的运行。
b. 关闭润滑系统和冷却系统。
c. 将加工好的工件取下,并进行质量检查。
三、注意事项1. 操作人员必须经过专业培训,熟悉数控车床的操作流程和安全规范。
2. 在操作数控车床时,必须佩戴好防护设备,如安全眼镜、手套和耳塞。
3. 在更换刀具或进行维护保养时,必须先停止数控车床的运行,并断开电源。
4. 加工过程中,严禁用手直接接触刀具或工件,必须使用合适的工具。
5. 在加工高温材料时,应注意防火防爆措施,确保安全生产。
四、维护保养1. 每天开机前,检查润滑系统和冷却系统的工作状态,并及时添加润滑剂和冷却液。
数控编程与操作技能训练作业指导书

数控编程与操作技能训练作业指导书第1章数控编程基础 (4)1.1 数控机床概述 (4)1.1.1 数控机床的定义与分类 (4)1.1.2 数控机床的组成与功能 (4)1.1.3 数控机床的发展趋势 (4)1.2 数控编程的基本概念 (4)1.2.1 数控编程的定义与作用 (4)1.2.2 编程语言的分类与特点 (4)1.2.3 编程原点的设定 (4)1.3 数控编程的步骤与要求 (4)1.3.1 编程步骤 (4)1.3.2 编程要求 (4)1.3.3 编程注意事项 (5)第2章数控编程坐标系与程序结构 (5)2.1 数控编程坐标系 (5)2.1.1 坐标系定义 (5)2.1.2 坐标系建立 (5)2.1.3 坐标系变换 (5)2.2 程序结构及其功能 (5)2.2.1 程序段结构 (5)2.2.2 程序功能 (6)2.3 常用编程指令及其应用 (6)2.3.1 基本编程指令 (6)2.3.2 辅助编程指令 (6)2.3.3 特殊编程指令 (6)第3章数控车床编程与操作 (6)3.1 数控车床概述 (6)3.2 数控车床编程基础 (6)3.2.1 编程语言 (6)3.2.2 编程步骤 (7)3.2.3 常用指令 (7)3.3 数控车床操作流程 (7)3.3.1 开机准备 (7)3.3.2 编程与输入 (7)3.3.3 对刀与装夹 (7)3.3.4 加工 (7)3.3.5 检验与清理 (8)3.4 数控车床加工实例 (8)第4章数控铣床编程与操作 (8)4.1 数控铣床概述 (8)4.2 数控铣床编程基础 (8)4.2.1 编程语言 (9)4.2.2 编程步骤 (9)4.2.3 编程实例 (9)4.3 数控铣床操作流程 (9)4.3.1 操作前准备 (9)4.3.2 操作步骤 (9)4.3.3 操作注意事项 (9)4.4 数控铣床加工实例 (9)4.4.1 加工工艺分析 (10)4.4.2 编程 (10)4.4.3 操作步骤 (10)第5章数控加工中心编程与操作 (10)5.1 加工中心概述 (10)5.2 加工中心编程基础 (10)5.2.1 编程语言 (10)5.2.2 编程步骤 (10)5.2.3 编程要点 (10)5.3 加工中心操作流程 (11)5.3.1 开机准备 (11)5.3.2 程序输入与校验 (11)5.3.3 加工操作 (11)5.3.4 工件检查与拆卸 (11)5.4 加工中心加工实例 (11)第6章数控线切割编程与操作 (11)6.1 数控线切割概述 (12)6.2 数控线切割编程基础 (12)6.2.1 编程原理 (12)6.2.2 编程语言及指令 (12)6.2.3 编程步骤 (12)6.3 数控线切割操作流程 (12)6.3.1 操作准备 (12)6.3.2 工件装夹与找正 (12)6.3.3 编程与输入 (12)6.3.4 加工参数设置 (12)6.3.5 加工启动与监控 (12)6.3.6 加工结束与工件检验 (12)6.4 数控线切割加工实例 (13)6.4.1 分析图纸与确定加工工艺 (13)6.4.2 编制数控程序 (13)6.4.3 设置加工参数 (13)6.4.4 加工启动与监控 (13)6.4.5 加工结束与工件检验 (13)第7章数控电火花加工编程与操作 (13)7.1 数控电火花加工概述 (13)7.2 数控电火花加工编程基础 (13)7.2.1 编程原理 (13)7.2.2 编程步骤 (14)7.2.3 编程要点 (14)7.3 数控电火花加工操作流程 (14)7.3.1 操作前准备 (14)7.3.2 加工操作 (14)7.3.3 加工后处理 (14)7.4 数控电火花加工实例 (15)第8章数控编程中的工艺处理 (15)8.1 数控加工工艺概述 (15)8.2 数控加工工艺参数的选择 (15)8.3 数控加工工艺文件编制 (16)8.4 数控加工工艺实例 (16)第9章数控机床的维护与故障处理 (17)9.1 数控机床的维护保养 (17)9.1.1 维护保养的重要性 (17)9.1.2 维护保养的主要内容 (17)9.1.3 维护保养的实施方法 (17)9.2 数控机床的故障诊断与处理 (17)9.2.1 故障诊断的基本原则 (17)9.2.2 故障诊断的方法 (17)9.2.3 故障处理流程 (17)9.3 数控机床故障实例分析 (18)第10章数控编程与操作技能训练 (18)10.1 数控编程技能训练 (18)10.1.1 数控编程基础知识回顾 (18)10.1.2 常用数控编程指令的应用 (18)10.1.3 数控编程实例分析 (18)10.2 数控机床操作技能训练 (19)10.2.1 数控机床基本操作 (19)10.2.2 数控机床程序输入与调试 (19)10.2.3 数控机床加工操作 (19)10.3 数控加工工艺技能训练 (19)10.3.1 数控加工工艺基础知识 (19)10.3.2 数控加工工艺文件编写 (19)10.3.3 数控加工工艺实例分析 (19)10.4 综合应用实例训练 (20)10.4.1 综合实例分析 (20)10.4.2 综合实例操作训练 (20)10.4.3 常见问题分析与解决方法 (20)第1章数控编程基础1.1 数控机床概述1.1.1 数控机床的定义与分类数控机床是指采用数字控制系统进行控制的机床,可根据编程指令自动完成工件的加工。
数控车作业指导书
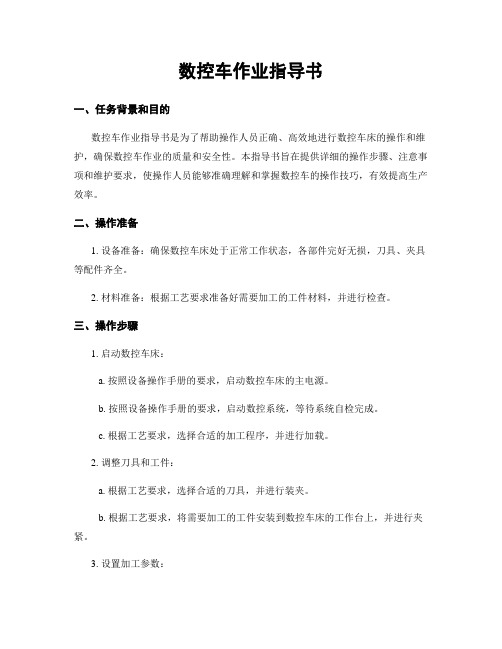
数控车作业指导书一、任务背景和目的数控车作业指导书是为了帮助操作人员正确、高效地进行数控车床的操作和维护,确保数控车作业的质量和安全性。
本指导书旨在提供详细的操作步骤、注意事项和维护要求,使操作人员能够准确理解和掌握数控车的操作技巧,有效提高生产效率。
二、操作准备1. 设备准备:确保数控车床处于正常工作状态,各部件完好无损,刀具、夹具等配件齐全。
2. 材料准备:根据工艺要求准备好需要加工的工件材料,并进行检查。
三、操作步骤1. 启动数控车床:a. 按照设备操作手册的要求,启动数控车床的主电源。
b. 按照设备操作手册的要求,启动数控系统,等待系统自检完成。
c. 根据工艺要求,选择合适的加工程序,并进行加载。
2. 调整刀具和工件:a. 根据工艺要求,选择合适的刀具,并进行装夹。
b. 根据工艺要求,将需要加工的工件安装到数控车床的工作台上,并进行夹紧。
3. 设置加工参数:a. 进入数控系统的参数设置界面。
b. 根据工艺要求,设置加工速度、进给速度、切削深度等参数。
c. 确认参数设置无误后,保存设置并退出参数设置界面。
4. 执行加工操作:a. 进入数控系统的操作界面。
b. 根据工艺要求,选择相应的加工功能,如车削、镗孔、攻丝等。
c. 根据工艺要求,输入加工尺寸和加工路径等相关参数。
d. 确认加工参数无误后,启动加工操作。
5. 监控加工过程:a. 在加工过程中,及时观察数控车床的工作状态,确保加工过程正常进行。
b. 注意观察刀具磨损情况,及时更换磨损严重的刀具。
c. 注意观察工件表面质量,如有异常情况及时停机检查。
6. 完成加工:a. 加工完成后,停止加工操作。
b. 将加工好的工件从数控车床上取下,并进行检查。
c. 根据工艺要求,对工件进行必要的后续处理,如清洁、测量等。
四、安全注意事项1. 在操作数控车床前,必须穿戴好个人防护装备,如安全帽、工作服、安全鞋等。
2. 操作人员必须熟悉数控车床的操作规程和相关安全知识,严禁未经培训的人员操作数控车床。
数控车床作业指导书

数控车床作业指导书一、任务描述本文档旨在提供数控车床作业的详细指导,包括操作步骤、安全注意事项、常见故障排除和维护保养等内容。
通过本指导书,操作人员能够准确、安全地操作数控车床,提高工作效率和产品质量。
二、操作步骤1. 准备工作a. 确保数控车床的电源温和源正常供应。
b. 检查机床各部件的运行状态,如导轨、刀架、工作台等。
c. 准备好所需的刀具、夹具和工件。
d. 穿戴好必要的个人防护装备,如安全帽、护目镜、手套等。
2. 开机准备a. 打开数控车床的电源,确保控制系统正常启动。
b. 进入数控系统界面,进行初始化设置,如坐标系设定、工件坐标原点归位等。
c. 检查刀具库存,确保所需刀具已装配到刀架上,并进行刀具长度补偿。
3. 加工操作a. 在数控系统中输入加工程序,并进行程序编辑和校验。
b. 将工件夹紧在工作台上,调整好工件的位置和夹紧力。
c. 根据加工程序要求选择合适的刀具,并进行装夹和刀具补偿。
d. 设置合适的切削参数,如进给速度、主轴转速、切削深度等。
e. 启动加工过程,监控加工状态,确保加工过程平稳进行。
f. 定期检查加工质量,如尺寸精度、表面光洁度等。
4. 故障排除a. 在加工过程中,如遇到异常情况或者故障,应即将停机,并查找故障原因。
b. 根据故障代码或者报警信息,参考数控系统手册进行故障排除。
c. 如无法解决故障,及时联系维修人员进行维修和调试。
5. 维护保养a. 每天结束工作后,对数控车床进行清洁和润滑,保持机床的整洁和良好的工作状态。
b. 定期检查机床各部件的紧固情况,如螺丝、联轴器等。
c. 检查润滑系统的油液情况,及时添加或者更换润滑油。
d. 定期对数控系统进行备份,并检查系统软件的更新和升级。
三、安全注意事项1. 操作人员必须熟悉数控车床的结构和工作原理,并具备相关的操作技能和安全意识。
2. 在操作过程中,严禁戴手套,以免被卷入旋转的刀具或者夹具中。
3. 在加工过程中,严禁触摸刀具和工件,以免发生意外伤害。
数控车床作业指导书

数控车床作业指导书一、任务背景随着工业自动化的发展,数控车床在机械加工领域得到广泛应用。
为了提高数控车床的加工效率和精度,需要编写一份详细的数控车床作业指导书,以便操作人员能够正确、高效地进行数控车床的操作。
二、作业环境及设备准备1. 作业环境要求:a) 温度:20℃~25℃;b) 湿度:相对湿度不超过80%;c) 空气质量:无腐蚀性气体和灰尘。
2. 设备准备:a) 数控车床:型号XYZ-123;b) 刀具:内外圆刀片、车削刀片等;c) 夹具:适配不同工件的夹具。
三、操作步骤1. 准备工作:a) 检查数控车床的电源温和源是否正常;b) 检查刀具和夹具的磨损情况,如有损坏应及时更换;c) 清洁工作台和工件,确保无异物。
2. 打开数控车床:a) 按下电源开关,待数控车床系统启动完成;b) 检查数控系统的显示屏是否正常。
3. 载入加工程序:a) 将预先编写好的加工程序通过U盘或者网络传输到数控车床的控制系统;b) 在数控系统界面上选择相应的加工程序。
4. 定位工件:a) 使用手动操作模式,将工件放置在夹具上,并通过手轮调整工件的位置,使其与刀具的加工轨迹相符。
5. 刀具预设:a) 选择合适的刀具,并根据工件形状和加工要求进行刀具的预设;b) 在数控系统中设置刀具的参数,如刀具半径、切削速度等。
6. 加工工序设置:a) 在数控系统中设置加工工序的参数,如进给速度、切削深度等;b) 根据实际情况,选择合适的加工工序。
7. 执行加工:a) 在数控系统中启动加工程序;b) 观察加工过程中的切削情况,如有异常应及时停机检查。
8. 加工完成:a) 加工完成后,关闭数控车床;b) 清理加工现场,归位刀具和夹具。
四、安全注意事项1. 操作人员应熟悉数控车床的结构和工作原理,并具备相关的操作经验;2. 在操作数控车床时,应穿戴好防护设备,如安全帽、安全眼镜、防护手套等;3. 在加工过程中,不得随意触摸刀具和工件,以免发生意外伤害;4. 加工过程中,应定期检查数控车床的电源温和源是否正常;5. 如遇突发情况或者异常情况,应即将停机检查,并寻求专业人员的匡助。
数控车床作业指导书
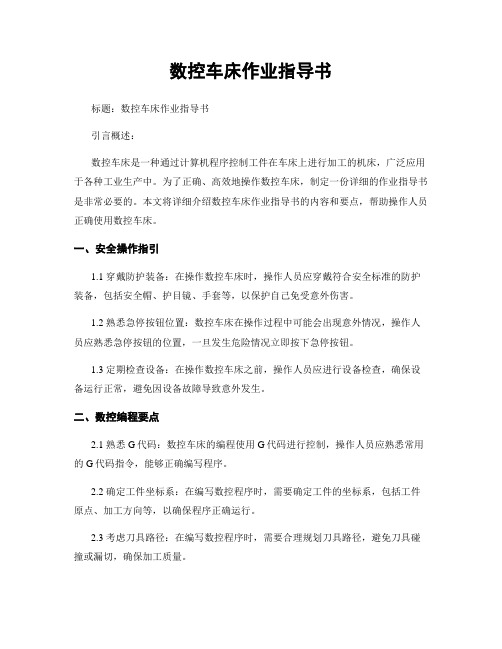
数控车床作业指导书标题:数控车床作业指导书引言概述:数控车床是一种通过计算机程序控制工件在车床上进行加工的机床,广泛应用于各种工业生产中。
为了正确、高效地操作数控车床,制定一份详细的作业指导书是非常必要的。
本文将详细介绍数控车床作业指导书的内容和要点,帮助操作人员正确使用数控车床。
一、安全操作指引1.1 穿戴防护装备:在操作数控车床时,操作人员应穿戴符合安全标准的防护装备,包括安全帽、护目镜、手套等,以保护自己免受意外伤害。
1.2 熟悉急停按钮位置:数控车床在操作过程中可能会出现意外情况,操作人员应熟悉急停按钮的位置,一旦发生危险情况立即按下急停按钮。
1.3 定期检查设备:在操作数控车床之前,操作人员应进行设备检查,确保设备运行正常,避免因设备故障导致意外发生。
二、数控编程要点2.1 熟悉G代码:数控车床的编程使用G代码进行控制,操作人员应熟悉常用的G代码指令,能够正确编写程序。
2.2 确定工件坐标系:在编写数控程序时,需要确定工件的坐标系,包括工件原点、加工方向等,以确保程序正确运行。
2.3 考虑刀具路径:在编写数控程序时,需要合理规划刀具路径,避免刀具碰撞或漏切,确保加工质量。
三、设备操作步骤3.1 打开数控车床电源:在操作数控车床之前,先打开电源,确保设备正常运行。
3.2 导入数控程序:将编写好的数控程序导入数控车床系统,准备进行加工。
3.3 调整加工参数:根据工件材料和加工要求,调整数控车床的加工参数,包括切削速度、进给速度等。
四、加工质量检验4.1 首件加工检验:在进行批量加工之前,首先进行首件加工检验,检查工件尺寸、表面光洁度等是否符合要求。
4.2 定期检查刀具磨损:在数控车床加工过程中,需要定期检查刀具磨损情况,及时更换刀具以保证加工质量。
4.3 记录加工参数:在加工过程中,应及时记录加工参数,包括切削速度、进给速度等,以便后续分析和改进。
五、故障排除方法5.1 刀具碰撞故障:如果在加工过程中发生刀具碰撞故障,应立即停机检查,更换受损刀具。
- 1、下载文档前请自行甄别文档内容的完整性,平台不提供额外的编辑、内容补充、找答案等附加服务。
- 2、"仅部分预览"的文档,不可在线预览部分如存在完整性等问题,可反馈申请退款(可完整预览的文档不适用该条件!)。
- 3、如文档侵犯您的权益,请联系客服反馈,我们会尽快为您处理(人工客服工作时间:9:00-18:30)。
—、起动机床之前,操作者需进行点检验:
1•检查油冷却器、切削液、空气压缩机、自动润滑器等的同位是否足够,需确认。
2•三点组合过滤器的水份去除需执行。
3•操作者本身须整束服装并穿戴劳保用品。
4•检查电源接合情况是否正常。
5•检视空气润滑剂管路接合情形是否紧牢。
6•排除机床周围的障碍物。
7•检查各螺丝锁紧情形,含夹具上的螺丝锁紧,并确认。
8•检查各种安全装置是否在定位及作用正常。
9.检查主轴上的刀具是否会松动或有其它不正常现象。
二、打开机床电源,急停键转致打开位置加电。
1.接通电源后,在位置显示或报警屏出现在CNC装置前,不要触摸MDI面板上的
任何按钮。
2.检查所有压力计,确认是否在正常工作状态。
3.检查风扇电机是否正常。
4.润滑油的各滑道面供给出情形是否正常,必须确认。
5.电源供给出情形是否正常。
6.检视机床是否有漏水、漏油情形,各管路是否有破损。
7.起动机床(复位结束后)运转各轴是否有异音或异状并确认。
8.检查各移动轴是否有振动或抖动现象。
9.确认机床处于正常状态后方可进行操作加工。
三、操作加工工件。
1.看懂加工工件的图纸、程序单,确认相符后,选择好合适的量具和刀具,以保证
加工的质量,方可进行加工。
2 .在机床运转之前应认真检查输入资料是否正确。
3.按正确的方法装夹工件,并确定坐标系。
4.使用刀具补偿功能时应认真检查方向和补偿具是否正确(在使用此命令之
前,要取消补偿功能模式)。
5 •手动干预机床锁定或可编程镜向被激活时,都可能改变工件的座标系,在操作前
必须确定坐标系正确后方可操作。
6•利用显示软件,了解加工序路径、尺寸范围,确认无障碍后方可加工。
7•执行每一个程序开始时,需看好显示屏上的各轴加工余程,确认正常后方可正常执行程序。
8•在粗加工程序中随时观察工件的加工余量,调节器节加工速度,以保证刀具正常切削,避免因余量过大而损坏刀具。
9.在加工过程中随时观察刀具的磨损情况,检查并测量工件的加工质量。
C和PMC参数,不许随意更改,如确实需要更改,应请示有关负责人经允许后
方可改动,并要及时回复。
四、每日工作结束时
1.必须彻底执行清扫工作,并检查机床是否有异常状态发生。
2.电控电器箱的排风扇或过滤网需定期清理。
3.切削车上和机床内如堆积铁屑,应立即清除。
4.各部给油不足量时,按规定给予补充。
5.作好交接班记录,交接班时需详细准确说明工作情况,接班人员认可后方可离
开。
6.需停机时务必将电源关掉,切断电源顺序如下:
关(Emergencyetcp —再关操作盘上of开关—再关电控箱开关
编制: 批准: 审核:。