3D封装集成电路测试挑战的ATE解决方案
基于ATE的可编程逻辑器件测试方法

基于ATE的可编程逻辑器件测试方法解维坤【摘要】集成电路发展模式已从软编程、硬编程到软硬双编程方向发展,可编程器件已成为时代主流,对可编程器件的测试需求越来越多。
首先介绍了可编程器件的概念和分类,然后针对目前主流的自动测试设备(ATE)做了介绍,接着详细描述了各种可编程器件的测试方法。
该方法具有较强的通用性,可广泛应用于各种PLD、PROM、CPLD、FPGA等可编程器件的测试,对于实现可编程器件的产业化测试具有一定意义。
%According to the Xu's cycle description of the development rule of integrated circuits, integrated circuit develop from soft programming to hard programming, then to-hard and soft dual programming direction. Programmable device has become the theme of the times, more and more demand for programmable device test, a variety of innovative testing technologies and solutions of the programmable logic device have been published. This paper introduces the concept and classification of the programmable devices first. Then made a introduction of the mainstream automatic test equipment (ATE); Then describes the test method of programmable devices in detail; This method has strong versatility, can be widely used in all kinds of programmable devices testing, such as PLD, PROM, CPLD, FPGA. It is of great significance for the industrialized testing of programmable logic devices.【期刊名称】《电子与封装》【年(卷),期】2016(000)001【总页数】4页(P12-15)【关键词】可编程逻辑器件;ISP;ATE;测试【作者】解维坤【作者单位】中国电子科技集团公司第58研究所,江苏无锡 214035【正文语种】中文【中图分类】TN407常见的可编程逻辑器件有PROM、PAL、GAL、PLA、CPLD、FPGA等,它们主要由可编程的与阵列、或阵列、门阵列等组成,可通过编程实现一定的逻辑功能[1]。
封测封装降本增效方案

封测封装降本增效方案封测封装降本增效方案一、引言随着科技的不断发展,封测封装技术在电子行业中扮演着重要的角色。
封测封装是将集成电路芯片进行封装和测试,以确保其正常运行和质量可靠性。
然而,传统的封测封装流程存在一些问题,如高成本、低效率等。
我们需要制定一个全面的方案来降低成本并提高效率。
二、问题分析1. 高成本:传统的封测封装流程中,需要大量的人力和物力投入,导致成本较高。
2. 低效率:由于流程繁琐且耗时长,导致生产周期较长,无法满足市场需求。
三、方案设计为了解决上述问题,我们可以采取以下措施:1. 自动化设备投入通过引入自动化设备来替代人工操作,可以大幅降低人力成本,并提高生产效率。
在芯片测试环节可以使用自动测试设备来完成测试过程,并通过软件进行数据分析和处理。
在芯片封装环节可以使用自动化机器来完成精确的焊接和密封工作。
2. 流程优化对封测封装流程进行优化,简化繁琐的步骤,减少不必要的环节。
在测试环节可以采用并行测试的方式,同时进行多个芯片的测试,从而缩短测试时间。
在封装环节可以采用模块化设计,将封装过程分解为多个小步骤,并通过自动化设备来完成每个步骤,以提高效率。
3. 质量控制加强质量控制是确保封测封装产品质量可靠性的关键。
可以通过引入先进的检测设备和技术来进行严格的质量检验。
在测试环节可以使用高精度的测试仪器来确保芯片的功能和性能符合规定标准。
在封装环节可以使用X光检测仪器来检查焊接和密封过程是否完整和可靠。
4. 供应链管理优化供应链管理是实现成本降低的重要手段。
可以与优质供应商建立长期合作关系,并通过谈判获取更有竞争力的价格和服务。
同时,建立健全的物流体系,提高物流效率,并减少运输成本。
5. 环境友好在设计方案时要考虑环境友好因素。
选择符合环保要求的材料和生产工艺,减少对环境的影响。
同时,通过节能设备和技术的应用,降低能源消耗,并减少碳排放。
四、实施计划1. 调研阶段:对市场需求进行调研,了解行业发展趋势,并与相关专家和企业进行交流,收集信息和建议。
封装测试行业行业痛点与解决措施
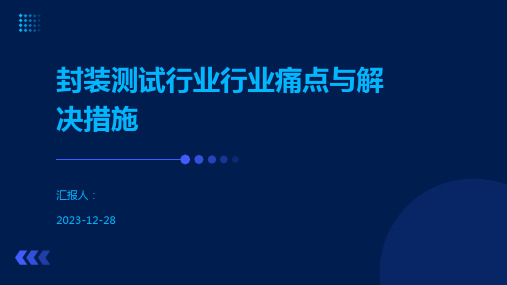
测试成本高昂
总结词
测试成本高昂是封装测试行业面临的另一个挑战,它可能影 响企业的盈利能力和市场竞争力。
详细描述
由于封装测试涉及的环节多、工作量大、人力资源需求高等 因素,导致测试成本高昂。此外,测试效率低下和准确度不 高等问题也会增加测试成本。这可能对企业的盈利能力和市 场竞争力产生负面影响。
测试覆盖不全
监控实施过程和效果
• 建立监控机制:建立有效的监控机制,对 测试过程进行实时跟踪和监控,确保测试 工作的顺利进行。- 收集和分析数据:收 集和分析测试过程中的数据,了解测试效 果和问题,为后续的优化和改进提供依据 。- 及时调整和改进:根据监控结果和分 析数据,及时调整和改进测试方案和方法 ,提高测试效率和质量。
员,明确责任分工,确保每个环节都有专人负责。
确定实施人员和责任分工
• 选择合适的实施人员:根据测试 任务和需求,选择具备相应技能 和经验的实施人员,确保测试工 作的顺利进行。- 明确责任分工 :根据实施计划,明确每个实施 人员的责任分工,确保每个环节 都有专人负责,避免出现职责不 清的情况。- 提供培训和支持: 为实施人员提供必要的培训和支 持,帮助他们熟悉测试流程、掌 握测试技能,提高测试效率和质 量。
封装测试行业行业痛点与解 决措施
汇报人: 2023-12-28
目录
• 行业痛点 • 解决措施 • 实施方案 • 案例分析
01
行业痛点
测试效率低下
总结词
测试效率低下是封装测试行业面临的主要问题之一,它可能导致项目进度延迟 、成本增加和产品质量风险。
详细描述
在封装测试过程中,由于测试环境配置复杂、测试数据管理繁琐、测试脚本编 写工作量大等因素,导致测试效率低下。这使得测试周期延长,测试成本增加 ,甚至可能影响到产品的上市时间和质量。
立对3DIC测试挑战的ATE解决方案Advantest V93000准备就绪

立对3DIC测试挑战的ATE解决方案Advantest V93000准备就绪Scott Chesnut;Bob Smith【摘要】三维集成电路(3DIC)的出现需要具备自动测试设备开发能力才能解决这些结构带来的挑战。
在符合以下条件的解决方案中找到了这种能力:提供多时钟域、每个3DIC层粒状硬件移植、以及功能强大的测试语言来控制此硬件和协作软件开发环境;在这种环境下,各层的测试开发团队可紧密合作.为迅速生产做好准备。
Advantest引进了每个引脚时钟域、多端口硬件、并发测试框架、协议感知以及smar Test程序管理器,可有效解决3DIC的测试挑战。
它们可使生产解决方案达到开发团队所需的粒度。
%The advent of three dimensional integrated circuits (3DIC) requires that automatic test equipment develop capability to address the challenges brought on by these structures.Such capability is found in test solutions which provide multiple clock domains, granular hardware porting per 3DIC layer, powerful test languages to control this hardware and collaborative software development environments where each layer's test development team can seamlessly merge their efforts together and be ready for production quickly. Advantest's introduction of clock domain per pin, multi-port hardware, concurrent test framework, Protocol aware, and smartest program manager address the test challenges of 3DIC in an effective manner. They allow production solutions to be architected to the degree of granularity required by the development teams.【期刊名称】《电子工业专用设备》【年(卷),期】2012(041)010【总页数】7页(P34-39,63)【关键词】三维集成电路/硅穿孔;单封装系统;自动测试设备【作者】Scott Chesnut;Bob Smith【作者单位】Advantest America;Advantest America【正文语种】中文【中图分类】TN4073D芯片属于多系统实体,其面临的测试挑战远远超过以往的单封装系统(SiP)和/或系统级芯片(SOC)。
提升性价比,让先进ATE设备更加普及

郑传俊Zheng Chuanjun上海宏测半导体科技有限公司研发总监5657SCI-TECH INNOVATIONSAND BRANDS创新人物多任务并发测试概念来自于中大功率分立器件测试,但即使是中大功率分立器件测试,参数的测试也是由多台独立的测试机分站测试完成的。
随着集成电路制造业的进步,数模混合、大功率高压器件和传统IC测试的整合,是芯片设计行业的两个技术发展方向。
以前需要几颗IC才能实现的功能,现在一颗芯片就可实现。
因此要求ATE既要能测模拟信号,又要能测数字信号;既要能测IC,又要具备一些功率器件的测试功能。
这种数模一体测试的ATE虽然也已投入应用,但此前存在的问题就是实现并发技术成本很高,只有对尖端或工业级芯片测试时才能使用,而对用量巨大的消费级电子芯片设计封装测试企业来说,这种ATE性价比很低,鉴于成本原因几乎不被使用。
在低成本数模混合式 ATE上应用并发技术,不仅能够满足用量巨大的消费级电子芯片设计封装测试企业的成本要求,而且使客户利用较少的测试资源完成相同甚至更多的测试产出,每一测试站上相对独立的 DUT板也将简化某些敏感模拟 IC测试中外围器件对其的影响。
“以一颗电源管理类器件为例,采用单任务顺序测试,完成全参数测试,测试时间约 1.6 s,采用并发技术后,将参数进行分拆,只需增加少量的硬件资源,其测试时间可以缩短一半,达到约880 ms,同时又以较低的成本将 UPH 提升至4k,保证了测试效率与精准度,性价比极为突出。
”目前,宏测新研发的这款多任务并行ATE测试设备,价格只有国外同类产品价格的三分之一或五分之一,且在检测质量方面可直接替代国外同类最先进的模拟集成电路测试设备。
以其优秀的性能即可为公司带来巨大的利润。
然而,郑传俊却并不满足于此。
“不仅仅是低价,宏测的服务也要更加贴近中国客户的需要”。
郑传俊承诺,“宏测就是要做测试设备领域的Turn-Key方案,满足不同层次封测厂的需要。
ATE基本原理

ATE基本原理ATE全称为Automated Test Equipment,即自动化测试设备。
它是一种用于执行电子元件和集成电路的自动化测试任务的设备。
ATE能够自动进行测试和诊断,从而提高测试效率和准确性,降低人力成本。
ATE在电子生产线上扮演着重要的角色,可以用于测试芯片、电路板、系统组件等,确保它们的质量和可靠性。
ATE的基本原理是通过将待测组件或设备连接到测试系统内的测试夹具中,用特定的方法进行测试和诊断。
一般来说,ATE主要由测试系统和测试夹具组成。
测试系统是ATE的核心部分,由测试仪器(如示波器、信号发生器和电源)和测试控制器(如计算机)组成。
测试仪器用于产生、测量和记录测试信号,测试控制器负责控制测试仪器的操作,并处理和分析测试数据。
测试系统能够执行各种测试任务,如功能测试、时序测试、电压测试、功耗测试等。
测试夹具是ATE中的辅助设备,用于将待测组件或设备连接到测试系统。
它通常包括接口卡和连接线,可以根据测试对象的不同进行调整和更换。
测试夹具具有良好的接触性能和稳定性,能够确保测试信号的准确传递和返回测试结果。
ATE的工作流程一般包括以下几个步骤:首先是初始化和校准,测试系统需要对测试仪器进行初始化和校准,以确保其正常工作和准确度。
接下来是测试计划的编写和加载,测试计划是测试任务的描述和指导,包括测试项目、参数设置和测试顺序等。
然后是测试执行,测试系统按照测试计划依次执行测试任务,并记录测试数据。
最后是测试结果的分析和报告,测试系统将测试数据进行分析和统计,并生成详细的测试报告,以供用户参考和分析。
ATE具有以下几个优点:首先,它能够实现自动化测试,减少了人工操作和干预,降低了测试成本和人力成本。
其次,ATE具有高度可扩展性和灵活性,可以适应不同测试需求和测试对象的变化。
再次,ATE具有高精度和高效率的特点,能够快速且准确地进行测试和诊断。
最后,ATE能够提供全面和可靠的测试结果,为生产线上的质量控制和故障排查提供重要参考。
深度解读基于ATE的IC测试技术
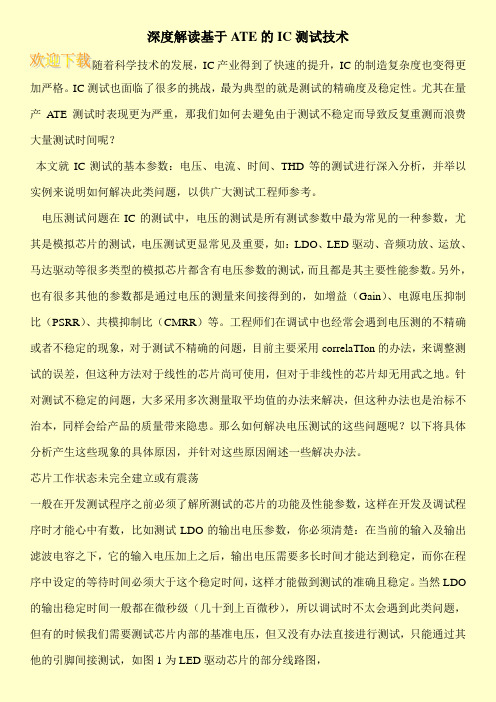
深度解读基于ATE的IC测试技术随着科学技术的发展,IC产业得到了快速的提升,IC的制造复杂度也变得更加严格。
IC测试也面临了很多的挑战,最为典型的就是测试的精确度及稳定性。
尤其在量产ATE测试时表现更为严重,那我们如何去避免由于测试不稳定而导致反复重测而浪费大量测试时间呢?本文就IC测试的基本参数:电压、电流、时间、THD等的测试进行深入分析,并举以实例来说明如何解决此类问题,以供广大测试工程师参考。
电压测试问题在IC的测试中,电压的测试是所有测试参数中最为常见的一种参数,尤其是模拟芯片的测试,电压测试更显常见及重要,如:LDO、LED驱动、音频功放、运放、马达驱动等很多类型的模拟芯片都含有电压参数的测试,而且都是其主要性能参数。
另外,也有很多其他的参数都是通过电压的测量来间接得到的,如增益(Gain)、电源电压抑制比(PSRR)、共模抑制比(CMRR)等。
工程师们在调试中也经常会遇到电压测的不精确或者不稳定的现象,对于测试不精确的问题,目前主要采用correlaTIon的办法,来调整测试的误差,但这种方法对于线性的芯片尚可使用,但对于非线性的芯片却无用武之地。
针对测试不稳定的问题,大多采用多次测量取平均值的办法来解决,但这种办法也是治标不治本,同样会给产品的质量带来隐患。
那么如何解决电压测试的这些问题呢?以下将具体分析产生这些现象的具体原因,并针对这些原因阐述一些解决办法。
芯片工作状态未完全建立或有震荡一般在开发测试程序之前必须了解所测试的芯片的功能及性能参数,这样在开发及调试程序时才能心中有数,比如测试LDO的输出电压参数,你必须清楚:在当前的输入及输出滤波电容之下,它的输入电压加上之后,输出电压需要多长时间才能达到稳定,而你在程序中设定的等待时间必须大于这个稳定时间,这样才能做到测试的准确且稳定。
当然LDO 的输出稳定时间一般都在微秒级(几十到上百微秒),所以调试时不太会遇到此类问题,但有的时候我们需要测试芯片内部的基准电压,但又没有办法直接进行测试,只能通过其他的引脚间接测试,如图1为LED驱动芯片的部分线路图,。
三维集成电路的设计与封装技术研究
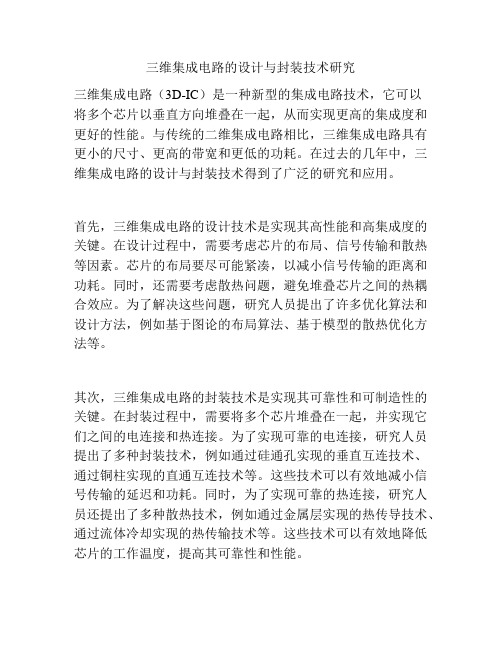
三维集成电路的设计与封装技术研究三维集成电路(3D-IC)是一种新型的集成电路技术,它可以将多个芯片以垂直方向堆叠在一起,从而实现更高的集成度和更好的性能。
与传统的二维集成电路相比,三维集成电路具有更小的尺寸、更高的带宽和更低的功耗。
在过去的几年中,三维集成电路的设计与封装技术得到了广泛的研究和应用。
首先,三维集成电路的设计技术是实现其高性能和高集成度的关键。
在设计过程中,需要考虑芯片的布局、信号传输和散热等因素。
芯片的布局要尽可能紧凑,以减小信号传输的距离和功耗。
同时,还需要考虑散热问题,避免堆叠芯片之间的热耦合效应。
为了解决这些问题,研究人员提出了许多优化算法和设计方法,例如基于图论的布局算法、基于模型的散热优化方法等。
其次,三维集成电路的封装技术是实现其可靠性和可制造性的关键。
在封装过程中,需要将多个芯片堆叠在一起,并实现它们之间的电连接和热连接。
为了实现可靠的电连接,研究人员提出了多种封装技术,例如通过硅通孔实现的垂直互连技术、通过铜柱实现的直通互连技术等。
这些技术可以有效地减小信号传输的延迟和功耗。
同时,为了实现可靠的热连接,研究人员还提出了多种散热技术,例如通过金属层实现的热传导技术、通过流体冷却实现的热传输技术等。
这些技术可以有效地降低芯片的工作温度,提高其可靠性和性能。
最后,三维集成电路的设计与封装技术在许多领域都得到了广泛的应用。
例如,在移动通信领域,三维集成电路可以实现更高的数据传输速率和更低的功耗,从而提高用户体验和延长电池寿命。
在计算机领域,三维集成电路可以实现更高的处理能力和更小的尺寸,从而提高计算机的性能和便携性。
在医疗领域,三维集成电路可以实现更高的信号处理能力和更小的医疗设备,从而提高医疗诊断和治疗的效果。
总之,三维集成电路的设计与封装技术是实现其高性能和高集成度的关键。
通过优化芯片的布局、信号传输和散热等因素,可以实现更高的集成度和更好的性能。
同时,通过优化封装技术,可以实现可靠的电连接和热连接。
- 1、下载文档前请自行甄别文档内容的完整性,平台不提供额外的编辑、内容补充、找答案等附加服务。
- 2、"仅部分预览"的文档,不可在线预览部分如存在完整性等问题,可反馈申请退款(可完整预览的文档不适用该条件!)。
- 3、如文档侵犯您的权益,请联系客服反馈,我们会尽快为您处理(人工客服工作时间:9:00-18:30)。
ATE solutions to 3D-IC test challenges The rea diness of Advantest’s V93000Scott Chesnut scott.chesnut@Robert Smith robert.j.smith@Florent Cros florent.cros@Lakshmikanth Namburi lakshmikanth.namburi@Advantest AmericaSan Jose, California USAAbstract—Three dimensional integrated circuits (3D-IC) require that automatic test equipment develop capability to address the challenges brought on by these structures.Such capability is found in test solutions which provide multiple clock domains, granular hardware porting per 3DIC layer, powerful test languages to control this hardware and collaborative software development environments.Advantest’s introduction of clock domain per pin, multi-port, concurrent test, and protocol aware software, MEMS probes, and SmarTest program manager address the test challenges of 3DIC in an effective effectively. They allow production solutions to be architected to the degree of granularity required by the development teams.Keywords—Protocol aware, Clock domain per pin, multi-port hardware, concurrent test framework, Protocol aware, SmarTest program manager, PLL Keep Alive, 3DIC TSV, 25uM pitch, MEMS Probes, ATE, BIST, JTAG, Pico Ampere Meter, interposer, spatial translation, MEMS, planarity, probes, cantilever, beam.I.I NTRODUCTION3D chips are multi-system entities whose test challenges dwarf those presented by yesterday’s System in a Package (SiP) and/or System On a Chip (SOC). Substantial infrastructure must be readied in order to position any Automatic Test Equipment (ATE) to succeed in a production test environment. A good approach to understanding what the real challenges are would be to eliminate those with already known solutions.Past efforts to reduce test time, increase test coverage, and coordinate the software efforts of large groups of test engineers have solved 2D related production test problems. While these solutions had been developed for reasons other than 3DIC/TSV production test, we find they may lend themselves well to the task. Many of the perceived 3DIC/TSV test problems actually already have solutions. What follows is a description of how the existing features of Advantest’s V93000 might address many of these challenges.A.Test Program Software Maintenance – SmarTest ProgramManager.Historically, a chip had one function. As more functions where added they became systems on a chip and then the migration to system in a package occurred. 3DIC systems in a stack add even greater complexity.Whether 3D stacks are assembled from Known Good Die (KGD) or Pretty Good Die (PGD) it can be assumed that “some” level of test will occur at both the chip level and then the stack level. Without assurance that chip layers are somewhat functional, a single layer’s defect can result with failing of the entire stack. Test costs become prohibitive as many good die are lost due to a single bad layer.Testing die before and after stack assembly requires use of variations of the same test program. One program version is used for the single die, another for the assembled stack. This is because test at the chip level will target its subcomponents while test at the stack level will exercise mission mode system level performance.It is likely that the same program be used for both activities with the difference being in how it perceives its current purpose. That is, a well architected test program can receive instructions from an operator or prober/handler and branch into chip or stack level test.Whether testing PGD, KGD, on the chip or stack level, use of the same program to test both reduces the correlation burden between chip test and assembled stack test. Proper maintenance of these program variations will require tighter book keeping than in the past.3D structures, being built from multiple separate chip layers have associated with them legions of test, product and design engineers responsible for performance of each layer. Large groups of people who, while in the past never had reason to collaborate, in the future will find it absolutely necessary. Since each layer represents man years of test development effort, the test programs of each engineering group will haveto be integrated into a single large master test program whose purpose is test the entire stack or portions of it as it is built.Collaborative test development software packages must enable graceful checking in and out of test program modules with a minimum of inter-group interaction and/or miscommunication. Ideally, it would also address multi-platform customer concerns because the intellectual property of a given test is expected to come from bench data, EDA tools, Verilog simulations and/or competing testers.A method of handling this task is found in Advantest’s SmarTest Program Manager. While the product has many features which ease program generation, version control, translation, and test time reduction, it also allows effective collaboration between any number of engineers who independently debug, modify, and re-integrate changes into the master test flow. Already a highly mature product SmarTest Program Manager lends itself well to the task of 3DIC test software development, integration and maintenance.B. Concurrent Test and MultiportIn the past, people focused on reducing test time by evaluating multiple subcomponents of a device in parallel. The more that could be run in parallel, the greater the test time savings. Older testers having single clock domains and primitive synchronization software had difficulty addressing this challenge.The Advantest V93K enables 128 separate clock domains for digital/analog/RF testing. Separate clocking makes possible the Multiport and Concurrent test features of the V93K hardware and software. This highly granular resource control allows mission mode test to be accomplished. Improved test coverage occurs because each DUT core can interact autonomously and asynchronously with the tester if actually operating in the target application.The Advantest V93K enables 128 separate clock domains for digital/analog/RF testing. Separate clocking make possible the Multiport and Concurrent test features of the V93K hardware and software. This highly granular resource control allows mission mode test to be accomplished. Improved test coverage occurs because each DUT core can interact autonomously and asynchronously with the tester as actually operating in the target application.While this feature has been in use on 2D products for years, its usefulness becomes apparent during 3DIC stack assembly test. Assuming that access to the TSV pads are on the top of every layer to be assembled, and assuming that the probe technology used to make contact to them exists, we might see the bond/build up process as shown in the figures below.During 3DIC assembly, the signal type and speed of the accessible TSVs of each layer will be different. The TSV signals exposed on the top of the interposer layer will differ from those exposed on the top of the CPU layer. Similarly, those of the CPU layer will be different than those of theSRAM layer, and so on. A single master test program can test separate layers as they are placed on the growing stack. This master test program will use each of the many configuredFigure 2 SmarTest Program Manager facilitatescollaborative program development.Figure 3 Concurrent test of IC cores by converting serial tests to parallel through the use of concurrent test framework and multiport configurable hardware.Figure 4 Step 1: Port A of the tester resource set is usedto interrogate the first stack layer – the interposer.Figure 5 Step 2: Port B of the tester resource set is used to interrogate the second stack layer - the CPU. Figure 6 Step 3: Port C of the tester resource set is used to interrogate the second stack layer – the SRAM.ports, each architected to serve the needs of every layer. In this way as layers are bonded on the stack and as the profile of the accessible signal sets change, a new test program need not be loaded into the tester. Multiple separate programs will not be needed.C. Clock Domain per PinAdvantest’s Multiport allows the hardware assignment granularity required to test discrete 3DIC layers and cores within each layer. As mentioned previously, another such feature is clock domain per pin capability of Advantest’sPS1600 and PS9G digital pins. Such functionality allows each layer or layer sub function to operate in any of up to 128 total asynchronous clock domains, each supporting independent periods resolved to 3nS. This can be considered a requirement for future 3DIC designs because the integration of multiple IP cores on stack layers will require multiple clockfrequencies/domains. Mission mode setup and operation becomes an issue as more layers of the stack are assembled because direct access to sunken layers will become obscured. The only way to operate the partial stack will be if the ATE can achieve this functionality. Hence ATE targeting 3DIC test needs to be a flexible multi clock domain instrument as well as one supporting Multiport.As seen in Fig. 7, the Advantest test equipment can be configured to operate each individual layer at its required asynchronous clock rate. Stack layer clock rates will have to be provided whose frequencies are dissimilar to the point of only being fractionally related to those around them. Multiple free running clocks will have to be provided to different layers again at different rates. PCI express, PXI, SLIM bus, etc. protocols will be expected to run simultaneously on different parts of digital hardware while unrelated RF/mixed signal activities occur autonomously as well. Data bus rates of multiple layers can be expected to have unique timing requirements unto themselves.D. Protocol Engine per PinAs the 3D chip is built and tested, bottom layers will have been designed to communicate with others which are not yet present. Again, this type of communication is expected to be done in mission mode. A tester will have to become the“surrogate stack” until future layers are assembled. It will be required that the ATE act to perform the virtual functions of the remaining un-built stack layers in order to facilitate the mission mode testing of the targeted layer as well as the layers underneath it. It becomes necessary to use protocol aware to make the stack “think” it is talking with the rest of itself even though it’s yet not there. A tester implementing protocolaware allows the tester to act as the remaining un-built portion of the stack.But physical challenges occur as the stack layers are built up. These stem from the fact that the X-Y locations of a given signal set will change from layer to layer. That is, pads whose purpose was to send/receive PCIE signals at topological location A on layer 1 may be found at location F on layer 2. This is generally known as the “spatial translation” of a given signal set from layer to layer.To compound the problem, on layer 2 the pads at location A may be required to perform I2C protocol not PCIE. Normally, to accommodate this would require a separate probearrangement for each layer meaning a separate probe card for each layer and a separate way of handling the protocol change. Alternatively, since the V93000 port granularity allows forFigure 8 As stack layers are added, the tester must mimic the function of future, not yet present layersEarly in the assembly/test processLater in the assembly/test processreassignment of digital pins from one port to another in a dynamic fashion, this exception is handled. Probe card pins which test I2C on one layer can be reconfigured as PCIE on another. This is because the V93000 supports the Protocol Engine per pin which means the same pin can test eitherprotocols (or any other for that matter) on the same probe pin (same X-Y layer location) across all of the layers.Unfortunately, if the type of spatial translation is occurring between layers and moves from digital to RF or mixed signals, this solution falls apart because the function of the testerresource changes entirely thus requiring reassignment of probe card wiring to a different tester resource or a local relay implementation. Possible solutions to this problem are:1. Develop a JEDEC (Joint Electronic DeviceEngineering Council) standard which enforces strict TSV signal type assignment rules. But this will require all layer vendors to observe definedconventions. As of the date of this writing, JEDEC has yet to develop a complete standard.2. Design every tester pin to accommodate every signaltype: RF/Power/Mixed Signal/Digital. This is an impractical, expensive, and multi-man year solution to develop.3. Re-route probe cards for every layer. This requiresmultiple separate probe cards - one for every layer which would be expensive.4. Use interposers to perform the spatial translation.While this adds to the assembly burden, it is aflexible solution which could handle physical layout exceptions. But as such requires that all interposers be individually tested.The most practical currently available solution to this problem would be to introduce interposers between layers to route signals of a given type to a region of the probe card wherethese tester resources have already been assigned. In this way, repositioning of the probe arrangement by way of another probe card is not required (eliminating the requirement for multiple probe cards and the time to change them).E. InterposersThere has been recent focus on the use of interposers toperform the intra-layer spatial translation. This is so not only for the reasons specified above (to avoid spatial translation of digital to RF signals and to address mechanical pitchmismatches) but also because use of them relinquishes chip designers from the responsibility of routing signals to the TSV x/y locations required by the next/previous layers of the stack. While the JEDEC consortium outlines the standard JESD49A, which suggest conventions where by these designer might compromise their efforts it is not complete; a simpler solutionmay the use of interposers.The word “interposer” comes from the Latin, interpōnere,meaning 'to put up between'. In the context of 3DIC test an interposer will perform the spatial translation of signals coming from one layer’s X/Y positions to that of the next layer. The interposer will be “put in between” layers in order to route signals using conductive paths.Interposers can be used to route signals of a given nature toprobe card pins which are already assigned to that type ofFigure 12 Simplified Interposer Concepts. Signals from bottom sidebeing routed to a different location on the top. Same side signalsbeing routed to different locations.Figure 9 PCIe port being tested on layer 1 at locations A.Figure 10 Locations A on layer 3 is tested as a memory interface. Location F now tests the same PCIe pins as on layer 1 now spatially translated from locations A on layer 4.Figure 11 Locations A tests I2C protocol.Location F interfaces with PowerManagement and is concurrently tested at anasynchronous rate using a differentcommunications protocol.X-Y Locations ―A‖ test functionfrom PCIe to Memorytester resource signal (RF/mixed signal/digital/power). This eliminates the requirement to swap probe cards during intra-layer production test of the stack.The number of TSVs found in future 3D devices is expected to be large - hundreds or thousands on top and bottom of each layer. The conductive traces on interposers will be comprised of very small geometries and tax the limits of mechanical fabrication tolerances. Because of this, a great number of the traces (if not all) are to be tested if for no other reason than to check process variations.To test interposer trace connectivity in production will require more than just continuity. The current carrying capability of each trace is expected to be very low – too low for standard ATE parametric instrumentation to be able to resolve. While Time Domain Reflectometry (TDR) techniques can be used to validate/characterize line length, continuity, and possibly impedance, it cannot verify current carrying capability(conductance). The Advantest Pico-amp Measure Card, can do all of these. Line length is verified by resistivity per cubic millimeter and knowledge of ideal trace volumetric and or cross sectional dimensions.It is a requirement that interposer test be as thorough as that found in Known Good Die. By the time an interposer is to be attached to the stack it must be 100% functional. It will make sense to bond the interposer on the die layer without testing the TSV it lays on. All that will need to be evaluated will be the bonding process. This occurs during the normal course of that layer’s mission mode test.The described approach solves the spatial translation problem associated with digital signals positioned on the RF tester resource x/y locations on the probe card. If signals of a given type (RF, digital, mixed signal) are routed to pre assigned probe card regions where these tester resources are already connected, the requirement of having to probe RF signals withdigital hardware is eliminated. The interposer will always reroute the signal to the appropriate area of the probe card matrix where the required tester resource is assigned.So with the use of a fully tested known good interposer, the problem of spatial translation to conflicting tester resources is solved. Probe is done after interposer assembly. Contact to the relevant TSVs by the proper tester resource is achievedbecause such signals are routed to quadrant containing probes connected to the appropriate tester resource.Because the use of the interposer allows routing of signals to the locations of dedicated probes, could we conclude that issue is solved.But designers may not assign next layer TSV locations at the same location as the interposer probe locations. This means that the interposer must perform two purposes: 1) to route signals to the location of dedicated probes and 2) to route signals to the location of the next layers input/output TSVs. Therefore the interposer design mentioned in Fig. 14 must change to resemble that of Fig. 15.Here the input and outputs of the interposer are located differently than that of the probe points. Placing the probe points on signal traces as suggested creates new but tractable problems. The first is that, if left exposed, the probe points might contact TSVs on the layer above it. There might be anyFigure 15 Interposer traces which contain probe card pads whose location is different than the signal output/inputs introduce reflection stubs.Figure 13 Actual Interposer Implementation. [1]Figure 14 Interposers can be used to reroute signals of a given type to predetermined probe card location where a tester resourceassignment conversion is observed. This methodology eliminates the requirement to rearrange tester resource assignment on the probe card by way of the use of another probe card during production test.number of solutions to this problem, for instance, by locating the probe points in inert locations of the next stack layer.The next problem is that of reflective stub introduced by the trace path stubs to the exiting TSV. These stubs can create reflections which could corrupt the signal integrity at the probe point. This can be solved based on knowledge of the frequency of the signals being probed. Given that the stubs are expected to be very short, (less than 3 mm) and that typical RF transmission frequencies (the highest expected in such anapplication) are approximately 5GHz, if the dielectric constant (Er) of the interposer where chosen to be as low as possible, interference from such reflections can be considerednegligible. The same can be said for high speed digital signals except that their susceptibility to reflective perturbations is far less because of the greater noise margin inherent in digital signals.F. 3D, Through Silicon Vias (TSVs) and Precision Parametric TestingThe benefits of “die stacking” into 3D structures are higher reliability, lower power consumption and higher speedperformance. This stacking will require individual die being very reliable and have very high test yield. Ideally, a single manufacturer would have complete control over each die’s electrical quality, performance, and physical construction. This would insure that stacking would have a very high probability of a fully functional product.However, in reality, it is unlikely a single company would manufacture all die layers required to make a complete 3D system product. Several manufacturers are expected tofabricate all of the different layers. If a die is added to the 3D stack which does not meet the stringent performancerequirements, a non-function 3D product would result. Worse would be a reliability failure in the field of the finished product. This would result in recalls and lost revenues.As TSVs pass through a die they could pass by critical active areas and cause undesirable effects in performance. It will be important that all signal routings using TSVs be well plannedand understood across all vendor designs in 3D systems.TSVs will also create new device leakage and dielectric paths. Resistance and capacitive paths created by these TSVs willhave to be monitored and understood. Thousands of new TSV are to be added as each new layer is added to the stack. Each such path could affect the stack performance and powerconsumption. Hence signal and power paths will require high accuracy testing. Engineers must be able to measure lowleakage current levels in order detect possible defects before a new die is added to the stack. The same will hold for total system leakage after the stack has been assembled.Having precision measuring ability early in the manufacturing process is a requirement as device process teams will monitor TSV diameter, height and oxide thicknesses as a function of signal and power paths. Checking thousands of TSVs or just a sampling of critical ones will prove nontrivial.Hence parametric testing will be required during theevaluation of individual die and during the die stack up phase. Quality precision parametric measurements of the TSVs, bumps, both C4 and micro C4 is key to successful 3D manufacturing. Today’s testers provide some precision parametric testing capability on a limited amount of pins. Using this solution is unacceptable as it would lead to a two pass test strategy unless a highly accuracy parametric parallel test solution is available.A highly parallel test solution would provide the ability to measure nano-Ampere (nA) or pico-Ampere (pA) accuracy and accurate resistance measurements in the milli-ohm ranges across many pins in parallel. Advantest’s precision, highly parallel DC test solution provides a solution. The Advantest pico-Ampere option provides 100 pins of precision nA and pA current measurement ability in true parallel fashion.Figure 16 3D stack die yield as a function of number of die in stack. Figure 17 3D TSV process capacitance, resistance, and leakage paths. Figure18 Block diagram of a single channel of the Advantest 93000 pA tester.Fig. 18 is a block diagram of a single pin’s architecture of the 100 pin Advantest highly parallel precision parametricmeasurement system. Each of the 100 pins is identical and can be independently programed on a per pin basis. One pass testing of digital data, standard PPMU, and precision PA parametric provides true one pass testing at wafer sort.G. Micro Electro Mechanical System (MEMS) Probes If 3D devices become more prevalent, wafer probes andprobing techniques need to be re-evaluated. Thinned devices used in 3D stacking will need to be thoroughly tested to ensure high reliability before they can be used in a system leveldevice. These thinned cannot withstand the force and pressure exerted by conventional probes. This force and pressure is magnified as device pitch and technologies shrink anddensities increase. Conventional probes can cause damage by destroying devices at wafer level or worse by physically overstressing a die or TSV structure. This overstressed die can cause a failure of the 3D stack device over time. Probe contact planarity across a TSV arrays is essential for uniform contact resistance.Conventional metal MEMS probes can use vast areas of space(millimeters of length) in their construction to achievecompliance. These construction techniques will limit their use because of pitch and required higher densities which may cause probe misalignment.Advantest’s MEMs probe solution addresses many of these problems. Using multi-level metal MEMS processing, microlithography and through-mold electro-depositiontechniques, Advantest creates MEMs probes whose electrical and mechanical characteristics more closely match thatrequired by these challenges. Shown below in Fig. 21 is a completed Advantest MEMS probe photo.This fabrication process allows for high levels of consistent planarity from tip to tip as well as across the complete MEMS probes structure. Utilizing these techniques Advantest MEMS probes can be consistently fabricated to exacting standards. This tip to tip planarity process translates into much better compliance and less overdrive stress on thinned wafers.Another benefit of this is consistent path contact resistance as deflection is consistent across the probe array.Figure 21 Scanning Electron Microscope (SEM) image of probe array showing high level of view of fabricated probe and sub-micron tip to tip planarity.H. ConclusionAlthough the number of 3DIC TSV devices in production around the world is very small, if it were to ramp suddenly, test engineers might find themselves without knowledge of available solutions. What has been described are the features of Advantest’s V93000 and how they might address many of the 3DIC TSV test challenges as viewed from the perspective of system experts.We have described how, using the currently available and mature features of the Advantest 93000 test system, theproblems associated with software revision control, multiple clock domains, multiport and concurrent test usage are provided by this tester platform. Use of the Pico Ampere Meter to thoroughly test interposers may be a requirement because they cannot be tested fully once assembled on the stack. The use of interposers as described will eliminate the necessity of swapping probe cards during production as stack layers are assembled, because spatial translation of layer signals to the appropriate tester resource is achieved. Also utilizing MEMS probe designs will allow testing of thinned wafers with minimal pressure allowing test of structures more consistently and more repeatedly. This will translate into higher and more consistent wafer and die yields.R EFERENCES[1] Image obtained from: MEMS Journal:/2010/04/overview-of-tsv-process-options.htmlFigure 19 Wafer Thinned to 50umFigure 20 Probe planarity problems。