镁法脱硫说明资料
氧化镁脱硫方案

引言在能源生产和工业生产过程中,许多燃烧和化学反应会产生大量的二氧化硫(SO2)等有害气体。
这些有害气体对环境和人体健康都有严重的损害。
因此,有效的脱硫技术和方案对于减少大气污染并维护生态平衡至关重要。
本文将介绍一种基于氧化镁的脱硫方案,旨在实现高效、环保的二氧化硫脱除。
一、氧化镁脱硫原理氧化镁(MgO)是一种常见的脱硫剂,其脱硫原理主要包括以下两个步骤:1.吸收和转化:氧化镁与二氧化硫发生化学反应,生成硫酸镁。
反应方程式如下:MgO + SO2 -> MgSO32.氧化:硫酸镁进一步与氧气发生氧化反应,生成硫酸镁和二氧化硫。
反应方程式如下:2MgSO3 + O2 -> 2MgSO4 + SO2通过上述两个步骤,氧化镁能够将二氧化硫转化为硫酸镁,从而实现脱硫的效果。
二、氧化镁脱硫方案设计基于氧化镁的脱硫方案主要包括以下几个环节:1. 氧化镁选择选择适合的氧化镁材料很关键。
通常,纯度较高且颗粒度均匀的微细氧化镁粉末是首选。
此外,氧化镁应具备良好的吸收性能和高催化活性。
2. 反应器设计反应器的设计应考虑尽量增大氧化镁与二氧化硫接触的表面积,以提高反应效率。
可采用填充床反应器或浮动床反应器来实现氧化镁与二氧化硫的接触。
3. 控制参数控制参数的选择和调整对于脱硫效果至关重要。
常见的控制参数包括反应温度、氧化镁质量、反应气体流速等。
一般而言,较高的反应温度和适当的氧化镁质量能够提高脱硫效率。
4. 脱硫效果评估对于氧化镁脱硫方案的效果进行评估是必要的。
可以通过测量出口气体中二氧化硫的浓度、脱硫率等指标来评估脱硫效果,并根据评估结果进行方案的调整和改进。
三、氧化镁脱硫方案优势与传统的脱硫方法相比,氧化镁脱硫方案具有以下几个优势:1.高效性:氧化镁具有很高的吸收性能和催化活性,能够有效地将二氧化硫转化为硫酸镁,从而实现高效脱硫。
2.环保性:脱硫过程仅产生二氧化硫和硫酸镁,无需额外处理废气,减少了二次污染的可能。
镁法脱硫技术
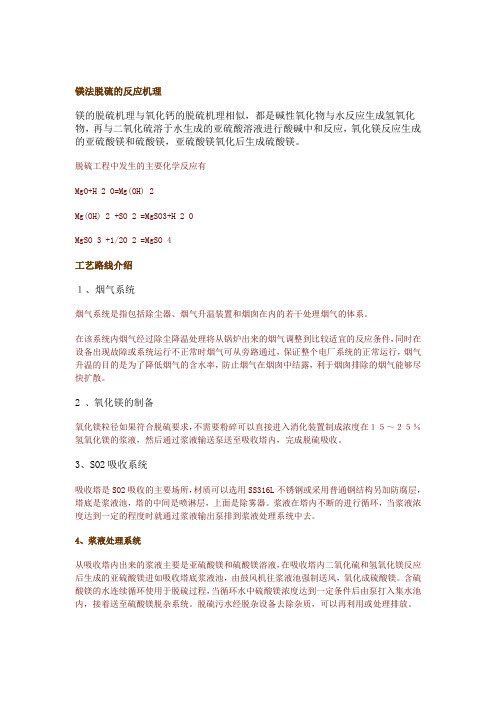
镁法脱硫的反应机理镁的脱硫机理与氧化钙的脱硫机理相似,都是碱性氧化物与水反应生成氢氧化物,再与二氧化硫溶于水生成的亚硫酸溶液进行酸碱中和反应,氧化镁反应生成的亚硫酸镁和硫酸镁,亚硫酸镁氧化后生成硫酸镁。
脱硫工程中发生的主要化学反应有MgO+H 2 O=Mg(OH) 2Mg(OH) 2 +SO 2 =MgSO3+H 2 OMgSO 3 +1/2O 2 =MgSO 4工艺路线介绍1、烟气系统烟气系统是指包括除尘器、烟气升温装置和烟囱在内的若干处理烟气的体系。
在该系统内烟气经过除尘降温处理将从锅炉出来的烟气调整到比较适宜的反应条件,同时在设备出现故障或系统运行不正常时烟气可从旁路通过,保证整个电厂系统的正常运行,烟气升温的目的是为了降低烟气的含水率,防止烟气在烟囱中结露,利于烟囱排除的烟气能够尽快扩散。
2 、氧化镁的制备氧化镁粒径如果符合脱硫要求,不需要粉碎可以直接进入消化装置制成浓度在15~25%氢氧化镁的浆液,然后通过浆液输送泵送至吸收塔内,完成脱硫吸收。
3、SO2吸收系统吸收塔是SO2吸收的主要场所,材质可以选用SS316L不锈钢或采用普通钢结构另加防腐层,塔底是浆液池,塔的中间是喷淋层,上面是除雾器。
浆液在塔内不断的进行循环,当浆液浓度达到一定的程度时就通过浆液输出泵排到浆液处理系统中去。
4、浆液处理系统从吸收塔内出来的浆液主要是亚硫酸镁和硫酸镁溶液,在吸收塔内二氧化硫和氢氧化镁反应后生成的亚硫酸镁进如吸收塔底浆液池,由鼓风机往浆液池强制送风,氧化成硫酸镁。
含硫酸镁的水连续循环使用于脱硫过程,当循环水中硫酸镁浓度达到一定条件后由泵打入集水池内,接着送至硫酸镁脱杂系统。
脱硫污水经脱杂设备去除杂质,可以再利用或处理排放。
很多情况下,尤其是中小型锅炉的脱硫,由于规模小,副产品发生量也小,大多采用处理排放,是将反应后的浆液经过固液分离后回收大部分水。
三氧化镁脱硫工艺的技术特点氧化镁脱技术是一种成熟度的脱硫工艺,氧化脱硫工艺在世界各地都有非常多的应用业绩。
氧化镁脱硫工艺
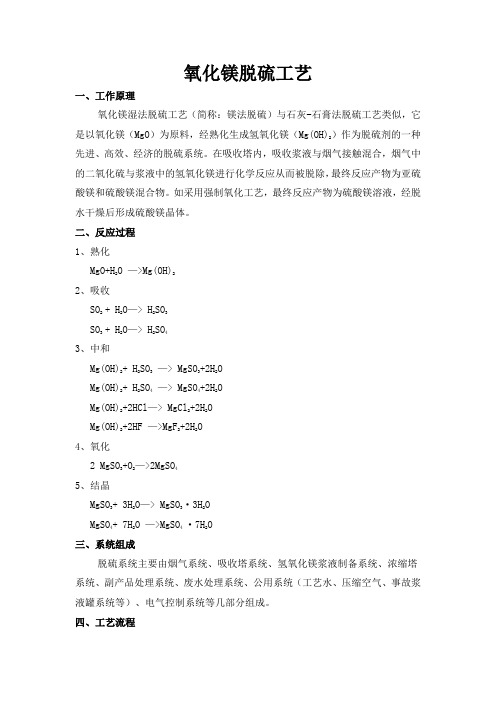
氧化镁脱硫工艺一、工作原理氧化镁湿法脱硫工艺(简称:镁法脱硫)与石灰-石膏法脱硫工艺类似,它是以氧化镁(MgO)为原料,经熟化生成氢氧化镁(Mg(OH)2)作为脱硫剂的一种先进、高效、经济的脱硫系统。
在吸收塔内,吸收浆液与烟气接触混合,烟气中的二氧化硫与浆液中的氢氧化镁进行化学反应从而被脱除,最终反应产物为亚硫酸镁和硫酸镁混合物。
如采用强制氧化工艺,最终反应产物为硫酸镁溶液,经脱水干燥后形成硫酸镁晶体。
二、反应过程1、熟化MgO+H2O —>Mg(OH)22、吸收SO2 + H2O—> H2SO3SO3 + H2O—> H2SO43、中和Mg(OH)2+ H2SO3—> MgSO3+2H2OMg(OH)2+ H2SO4—> MgSO4+2H2OMg(OH)2+2HCl—> MgCl2+2H2OMg(OH)2+2HF —>MgF2+2H2O4、氧化2 MgSO3+O2—>2MgSO45、结晶MgSO3+ 3H2O—> MgSO3·3H2OMgSO4+ 7H2O —>MgSO4·7H2O三、系统组成脱硫系统主要由烟气系统、吸收塔系统、氢氧化镁浆液制备系统、浓缩塔系统、副产品处理系统、废水处理系统、公用系统(工艺水、压缩空气、事故浆液罐系统等)、电气控制系统等几部分组成。
四、工艺流程锅炉/窑炉—>除尘器—>引风机—>浓缩塔—>吸收塔—>烟囱来自于锅炉或窑炉的烟气经过除尘后在引风机作用下进入浓缩塔、吸收塔,吸收塔为逆流喷淋空塔结构,集吸收、氧化功能于一体,上部为吸收区,下部为氧化区,经过除尘后的烟气与吸收塔内的循环浆液逆向接触。
系统一般装3-4台浆液循环泵,每台循环泵对应一层雾化喷淋层。
当只有一台机组运行时或负荷较小时,可以停运1-2层喷淋层,此时系统仍保持较高的液气比,从而可达到所需的脱硫效果。
15吨锅炉镁法脱硫方案
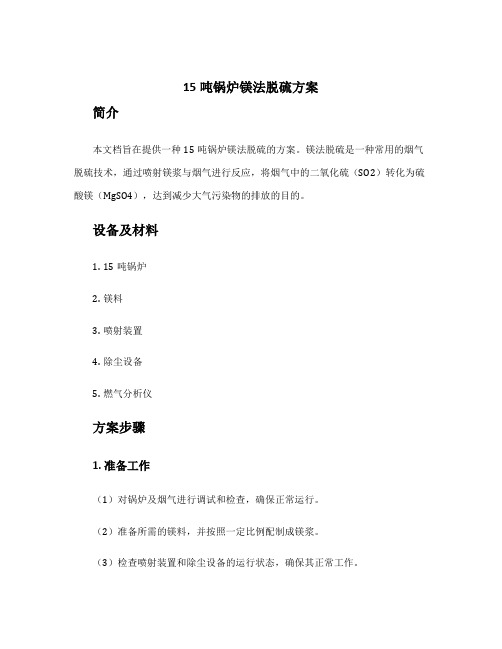
15吨锅炉镁法脱硫方案简介本文档旨在提供一种15吨锅炉镁法脱硫的方案。
镁法脱硫是一种常用的烟气脱硫技术,通过喷射镁浆与烟气进行反应,将烟气中的二氧化硫(SO2)转化为硫酸镁(MgSO4),达到减少大气污染物的排放的目的。
设备及材料1.15吨锅炉2.镁料3.喷射装置4.除尘设备5.燃气分析仪方案步骤1. 准备工作(1)对锅炉及烟气进行调试和检查,确保正常运行。
(2)准备所需的镁料,并按照一定比例配制成镁浆。
(3)检查喷射装置和除尘设备的运行状态,确保其正常工作。
2. 镁浆喷射(1)启动锅炉,待其达到正常工作温度和压力。
(2)将配制好的镁浆通过喷射装置喷射到烟气通道中。
(3)根据煤质和烟气排放量调整镁浆的喷射量,保持一定的镁浆进料速率。
3. 反应与除尘(1)镁浆与烟气中的二氧化硫发生反应,生成硫酸镁。
(2)硫酸镁颗粒通过烟气带到除尘设备中。
(3)除尘设备将烟气中的颗粒物和硫酸镁分离,排出净化后的烟气。
4. 后处理(1)回收的硫酸镁通过特定装置进行结晶和过滤,得到干燥的硫酸镁产品。
(2)经过处理的硫酸镁可以用于农业、化肥、水处理等领域。
5. 监测和调整(1)在脱硫过程中,需要定期监测烟气中的二氧化硫浓度和排放量。
(2)根据监测数据调整喷射量和进料速率,以保证脱硫效果和设备的正常运行。
6. 安全措施(1)在操作过程中,严格遵守相关安全操作规程,确保人员和设备的安全。
(2)加强对镁料和镁浆的储存、运输和使用过程中的安全管理。
结论通过使用镁法脱硫技术,可以有效减少烟气中的二氧化硫排放量,达到环境保护的目的。
然而,在应用过程中需要注意操作规程和安全措施,定期监测和调整工艺参数,确保设备的正常运行和脱硫效果。
此外,合理利用回收的硫酸镁产品,可以实现资源的再利用,具有一定的经济和环保效益。
镁法脱硫技术方案

镁法脱硫技术方案镁法脱硫(MgO法脱硫)是一种高效的燃煤电厂脱硫技术,它通过利用镁原料与SO2反应生成MgSO3/MgSO4及相应的MgO等反应产物,将燃煤电厂的SO2排放量降低到国家标准以下。
下面将给出镁法脱硫技术方案。
一、工艺流程镁法脱硫的工艺流程主要包括石灰石粉碎、煤粉预处理、喷吹预处理剂、燃烧脱硝、湿法脱硫等。
具体流程如下:1.石灰石粉碎:将所使用的石灰石经过粉碎处理,得到细小的石灰石粉末。
2.煤粉预处理:对烟煤进行预处理,如振动筛等,去除其中粉尘、杂质等。
3.喷吹预处理剂:在燃烧炉的上部喷吹预处理剂,作用是在燃烧过程中将SO2转化为SO3,利于后续脱硫。
4.燃烧脱硝:燃烧过程中产生的NOx会通过脱硝设备进行处理,降低NOx的排放浓度。
5.湿法脱硫:利用镁石粉、石灰石、水等混合成脱硫液,在脱硫装置内与烟气反应,将SO2转化为MgSO3/MgSO4等产物,达到脱硫的效果。
二、反应原理在燃煤电厂中,SO2是主要的污染物之一。
利用镁法脱硫技术,通过以下的反应原理将SO2转化为硫酸镁等无害物质。
首先,在喷吹预处理剂的作用下,SO2被氧化为SO3,如下所示:SO2 + 1/2O2 → SO3然后,SO3与镁原料反应,生成MgSO4,如下所示:MgO + SO3 → MgSO4最后,MgSO4与石灰反应,生成硫酸镁和CaSO4,如下所示:MgSO4 + CaO → MgO + CaSO4反应结束后,CaSO4可被制成石膏板等建筑材料,实现资源循环利用。
三、技术优势镁法脱硫技术相较于其他脱硫技术,有如下优势:1. 高效:镁法脱硫吸收塔内通过喷淋镁石浆料获得10~15s的接触时间,比其他脱硫技术的接触时间更长,故脱硫效率高。
2.适用性强:镁法脱硫技术适用于高温、高湿、高硫、高脱硝等复杂工况下,且可以灵活调节反应参数,适应不同的燃煤电厂要求。
3.反应产物无污染:镁法脱硫技术所产生的硫酸镁等有用产物可以回收利用,不会造成排放物的二次污染。
镁法脱硫技术方案

镁法脱硫技术方案一、技术原理镁法脱硫技术指的是利用镁矿石制取镁粉,在饱和溶解的氧化钙乳液中加入镁粉,反应后生成氧化镁和二氧化硫,反应方程式如下:Mg + CaO + SO2 → MgO + CaSO3大量的氧化镁溶于氧化钙水浆中,由于氧化钙的石灰石的晶体结构很松散且易被水分解,再分解时放出大量的热同时产生氢氧化钙。
因此,在这种体系中,氢氧化钙气泡将氧化镁迅速搬移到并联反应区与SO2反应,将SO2转换为硫酸钙,从而达到脱硫的目的。
二、技术流程1. 镁粉的制备首先需要进行镁粉的制备,一般可以采用炉渣还原法、气相反应法等多种方法。
2. 制备饱和氧化钙乳液将石灰石粉末加水稀释,制备成水浆,然后再加热至80℃左右,用氧气吹制成悬液,最后控制pH值,制备成饱和氧化钙乳液。
3. 反应区的设计反应区一般设在石灰石浆液进口处,应具有足够的长度以达到充分反应的效果。
4. 镁粉投加将制备好的镁粉均匀地投入到氧化钙乳液中,以保证反应能够充分进行。
5. SO2的吸收在反应区内,SO2与氧化钙溶液和镁粉反应,生成氧化镁和硫酸钙,并逐渐沉淀析出。
6. 硫酸钙的回收硫酸钙沉淀下来后,可以通过旋滤机、压滤机等设备进行回收和处理,使其作为一种宝贵的工业原料应用。
7. 氧化钙的再生经过反应产生的氢氧化钙水浆可以通过水的蒸发,从而继续再生成氧化钙水浆,以备后续的脱硫过程。
三、优缺点分析优点:1. 镁法脱硫可以在较低的温度下进行,降低了能量消耗和反应的难度。
2. 镁法脱硫保持了硫酸钙的价值,使它可以作为工业原料进行回收和再利用。
3. 操作简单,操作环境相对较安全。
缺点:1. 镁法脱硫单次反应的速度较慢,需要较长的处理时间才能达到脱硫效果。
2. 进行镁法脱硫需要使用大量的镁粉,在生产成本上具有一定的影响。
四、应用领域镁法脱硫技术主要应用于钢铁、非金属矿山、电力等行业的脱硫处理过程中,能够较为有效地去除工业废气中的二氧化硫,达到环保要求,减少对环境的影响,可以推广到许多相关产业的实际生产中。
镁法脱硫说明资料
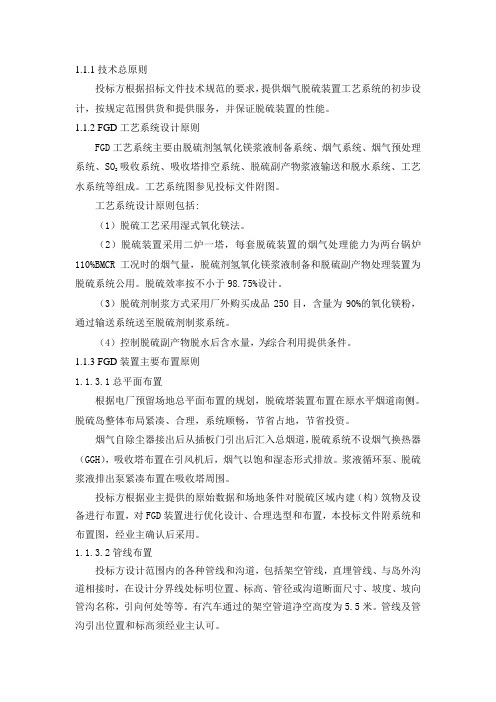
1.1.1技术总原则投标方根据招标文件技术规范的要求,提供烟气脱硫装置工艺系统的初步设计,按规定范围供货和提供服务,并保证脱硫装置的性能。
1.1.2 FGD工艺系统设计原则FGD工艺系统主要由脱硫剂氢氧化镁浆液制备系统、烟气系统、烟气预处理吸收系统、吸收塔排空系统、脱硫副产物浆液输送和脱水系统、工艺系统、SO2水系统等组成。
工艺系统图参见投标文件附图。
工艺系统设计原则包括:(1)脱硫工艺采用湿式氧化镁法。
(2)脱硫装置采用二炉一塔,每套脱硫装置的烟气处理能力为两台锅炉110%BMCR工况时的烟气量,脱硫剂氢氧化镁浆液制备和脱硫副产物处理装置为脱硫系统公用。
脱硫效率按不小于98.75%设计。
(3)脱硫剂制浆方式采用厂外购买成品250目,含量为90%的氧化镁粉,通过输送系统送至脱硫剂制浆系统。
(4)控制脱硫副产物脱水后含水量,为综合利用提供条件。
1.1.3 FGD装置主要布置原则1.1.3.1总平面布置根据电厂预留场地总平面布置的规划,脱硫塔装置布置在原水平烟道南侧。
脱硫岛整体布局紧凑、合理,系统顺畅,节省占地,节省投资。
烟气自除尘器接出后从插板门引出后汇入总烟道,脱硫系统不设烟气换热器(GGH),吸收塔布置在引风机后,烟气以饱和湿态形式排放。
浆液循环泵、脱硫浆液排出泵紧凑布置在吸收塔周围。
投标方根据业主提供的原始数据和场地条件对脱硫区域内建(构)筑物及设备进行布置,对FGD装置进行优化设计、合理选型和布置,本投标文件附系统和布置图,经业主确认后采用。
1.1.3.2管线布置投标方设计范围内的各种管线和沟道,包括架空管线,直埋管线、与岛外沟道相接时,在设计分界线处标明位置、标高、管径或沟道断面尺寸、坡度、坡向管沟名称,引向何处等等。
有汽车通过的架空管道净空高度为5.5米。
管线及管沟引出位置和标高须经业主认可。
2.2 氢氧化镁脱硫剂制备与供应系统2.2.1 技术性能(1)系统概述250目氧化镁粉从矿山由汽车运输直接运送到厂内,通过气力输送系统将氧化镁粉送至一个氧化镁粉仓,在粉仓下部分出1个出口,氧化镁粉经过熟化后进入氢氧化镁浆液池,脱硫剂在浆液池内按一定比例加水并搅拌配制成一定浓度的氢氧化镁脱硫剂浆液,而后再由供给泵送入吸收塔。
镁法脱硫液气比
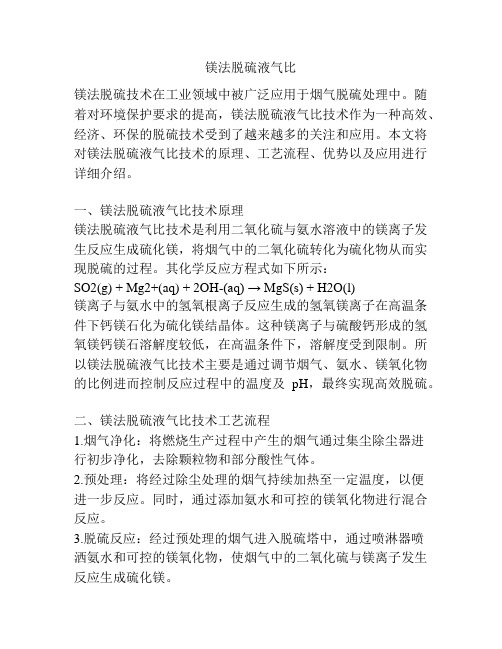
镁法脱硫液气比镁法脱硫技术在工业领域中被广泛应用于烟气脱硫处理中。
随着对环境保护要求的提高,镁法脱硫液气比技术作为一种高效、经济、环保的脱硫技术受到了越来越多的关注和应用。
本文将对镁法脱硫液气比技术的原理、工艺流程、优势以及应用进行详细介绍。
一、镁法脱硫液气比技术原理镁法脱硫液气比技术是利用二氧化硫与氨水溶液中的镁离子发生反应生成硫化镁,将烟气中的二氧化硫转化为硫化物从而实现脱硫的过程。
其化学反应方程式如下所示:SO2(g) + Mg2+(aq) + 2OH-(aq) → MgS(s) + H2O(l)镁离子与氨水中的氢氧根离子反应生成的氢氧镁离子在高温条件下钙镁石化为硫化镁结晶体。
这种镁离子与硫酸钙形成的氢氧镁钙镁石溶解度较低,在高温条件下,溶解度受到限制。
所以镁法脱硫液气比技术主要是通过调节烟气、氨水、镁氧化物的比例进而控制反应过程中的温度及pH,最终实现高效脱硫。
二、镁法脱硫液气比技术工艺流程1.烟气净化:将燃烧生产过程中产生的烟气通过集尘除尘器进行初步净化,去除颗粒物和部分酸性气体。
2.预处理:将经过除尘处理的烟气持续加热至一定温度,以便进一步反应。
同时,通过添加氨水和可控的镁氧化物进行混合反应。
3.脱硫反应:经过预处理的烟气进入脱硫塔中,通过喷淋器喷洒氨水和可控的镁氧化物,使烟气中的二氧化硫与镁离子发生反应生成硫化镁。
4.除尘:经过脱硫塔的烟气在高速气流的作用下,将脱硫过程中生成的硫化镁颗粒物进行分离,从而实现脱硫和除尘的目的。
5.冷却:将已完成脱硫的烟气通过冷却器降温,以便进一步处理或排放。
6.产物处理:经过脱硫和除尘处理后的硫化镁颗粒物通过旋风分离器进行分离,得到硫化镁产物,并进行相应的处理。
三、镁法脱硫液气比技术优势1. 高效脱硫:镁法脱硫液气比技术能够将烟气中的二氧化硫转化为硫化镁,具有较高的脱硫效率,能够有效降低烟气中的二氧化硫含量。
2. 环保经济:镁法脱硫液气比技术使用的原料较为简单,成本较低,同时产生的硫化镁可以作为资源进行利用,对环境的影响相对较小。
- 1、下载文档前请自行甄别文档内容的完整性,平台不提供额外的编辑、内容补充、找答案等附加服务。
- 2、"仅部分预览"的文档,不可在线预览部分如存在完整性等问题,可反馈申请退款(可完整预览的文档不适用该条件!)。
- 3、如文档侵犯您的权益,请联系客服反馈,我们会尽快为您处理(人工客服工作时间:9:00-18:30)。
1.1.1技术总原则投标方根据招标文件技术规范的要求,提供烟气脱硫装置工艺系统的初步设计,按规定范围供货和提供服务,并保证脱硫装置的性能。
1.1.2F GD工艺系统设计原则FGD工艺系统主要由脱硫剂氢氧化镁浆液制备系统、烟气系统、烟气预处理系统、SQ吸收系统、吸收塔排空系统、脱硫副产物浆液输送和脱水系统、工艺水系统等组成。
工艺系统图参见投标文件附图。
工艺系统设计原则包括:(1)脱硫工艺采用湿式氧化镁法。
(2 )脱硫装置采用二炉一塔,每套脱硫装置的烟气处理能力为两台锅炉110%BMC工况时的烟气量,脱硫剂氢氧化镁浆液制备和脱硫副产物处理装置为脱硫系统公用。
脱硫效率按不小于98.75%设计。
(3)脱硫剂制浆方式采用厂外购买成品250目,含量为90%勺氧化镁粉,通过输送系统送至脱硫剂制浆系统。
(4)控制脱硫副产物脱水后含水量,为综合利用提供条件。
1.1.3FGD装置主要布置原则1.1.3.1总平面布置根据电厂预留场地总平面布置的规划,脱硫塔装置布置在原水平烟道南侧。
脱硫岛整体布局紧凑、合理,系统顺畅,节省占地,节省投资。
烟气自除尘器接出后从插板门引出后汇入总烟道,脱硫系统不设烟气换热器(GG)吸收塔布置在引风机后,烟气以饱和湿态形式排放。
浆液循环泵、脱硫浆液排出泵紧凑布置在吸收塔周围。
投标方根据业主提供的原始数据和场地条件对脱硫区域内建(构)筑物及设备进行布置,对FGD装置进行优化设计、合理选型和布置,本投标文件附系统和布置图,经业主确认后采用。
1.1.3.2管线布置投标方设计范围内的各种管线和沟道,包括架空管线,直埋管线、与岛外沟道相接时,在设计分界线处标明位置、标高、管径或沟道断面尺寸、坡度、坡向管沟名称,引向何处等等。
有汽车通过的架空管道净空高度为 5.5米。
管线及管沟引出位置和标高须经业主认可。
2.2氢氧化镁脱硫剂制备与供应系统2.2.1技术性能(1)系统概述250目氧化镁粉从矿山由汽车运输直接运送到厂内,通过气力输送系统将氧化镁粉送至一个氧化镁粉仓,在粉仓下部分出1个出口,氧化镁粉经过熟化后进入氢氧化镁浆液池,脱硫剂在浆液池内按一定比例加水并搅拌配制成一定浓度的氢氧化镁脱硫剂浆液,而后再由供给泵送入吸收塔。
氧化镁粉的供应量是由浆液罐内浆液的PH值通过控制氧化镁给料机来调节实现的。
氢氧化镁脱硫剂浆液向吸收塔的供应量是由脱硫吸收塔内浆液的PH值通过控制管道上的调节阀来实现的。
(2)设计原则氧化镁全部在粉仓内进行储存。
两台炉设一个粉仓、对应的熟化池和浆液池。
全套脱硫剂制备及供应系统满足FGD所有可能的负荷范围。
氧化镁输入方式为:散装罐车运输至氧化镁粉仓。
2.2.2设备脱硫剂氢氧化镁浆液制备系统全套包括,但不限于此:(1)氧化镁粉储仓氧化镁粉储仓储存购进的氧化镁粉,贮仓根据确认的标准进行利旧原有粉仓。
散装罐车运输氧化镁粉至粉仓后,靠自身气力输送泵将镁粉送至粉仓,粉仓设计一个出料口,出料口配有气化装置。
在粉仓的出料口装有手动关断阀。
(2)氧化镁浆液池及泵和搅拌器氧化镁粉通过称重给料机卸料至氧化镁浆液池,由脱硫剂供给泵送至吸收塔。
包括下列泵、箱和搅拌器,但又不限于此。
•氢氧化镁浆液池,两台炉共用1个。
•氢氧化镁浆液泵,容量按两台炉燃用校核煤种时BMC工况下的氢氧化镁浆液耗量设计,一运一备。
•氢氧化镁浆液池内设一台搅拌器,其设计和布置能保证浆液浓度的均匀及防止浆液沉降结块。
全套包括搅拌器和需要的连接管、进料出料,液位控制、检查孔及所有其他必要设施、法兰等。
223管道系统投标方提供系统所需的所有管道、阀门、仪表、控制设备和附件等的设计。
管道、阀门和表计均考虑防腐。
浆液管线布置无死区存在,以避免管道堵塞。
浆液管线设计有清洗系统和阀门低位排水系统。
有关阀门的设计满足系统运行和控制要求。
1.3烟气系统1.3.1技术要求(1)系统概述从锅炉引风机后的总烟道上引出的烟气,通过吸收塔前烟气预处理装置进行降温、除尘、除杂后(并配有相应的监测系统)汇进入吸收塔,在吸收塔内脱硫净化,经除雾器除去水雾后经烟道、烟囱排入大气。
在烟道上设置旁路挡板门,当锅炉启动、进入FGD的烟气超温和FGD装置故障停运时,烟气由旁路挡板经烟囱排放。
(2)设计原则当锅炉在BMCR工况条件下,FGD装置的烟气系统都能正常运行,并且在BMCR 工况下进烟温度不超过150C条件下仍能安全连续运行。
事故状态下,烟气脱硫装置的进烟温度不得超过150C。
当温度达到150C 时,事故喷淋系统自动打开。
在烟气脱硫装置的进、出口烟道上设置挡板门用于锅炉运行期间脱硫装置的隔断和维护。
系统设计合理布置烟道和挡板门。
用于运行和观察的压力表、温度计和SO2分析仪等仪表,安装在烟道上。
在烟道中,设有人孔方便检修。
所有的烟气挡板门易于操作,在最大压差的作用下具有100%的严密性。
投标方提供所有改造烟道、支架、挡板门和膨胀节等设备的设计。
1.3.2烟气-烟气换热器本期脱硫改造工程中不设烟气-烟气换热器,以湿烟气形式排放。
1.3.3烟道及其附件1.3.4.1技术原则烟道根据可能发生的最差运行条件(例如:温度、压力、流量、污染物腐蚀、凝水的疏水等)进行设计。
烟道设计能够承受如下负荷:烟道自重、风雪荷载、地震荷载、灰尘积累、内衬和保温的重量等。
烟道最小壁厚按6mm设计,并考虑一定的腐蚀余量。
烟道内烟气流速不超过15m/s。
烟道具有气密性的焊接结构,所有非法兰连接的接口都进行连续焊接。
所有烟道用碳钢制作,采用可靠的内衬(例如鳞片树脂)进行防腐保护,选择的防腐材料将征得业主同意。
排水设施的容量将按预计的流量设计,排水设施将由不锈钢材料(316L或更好),或者是能满足周围环境和介质要求的FRP制作。
排水将返回到FGD排水坑或吸收塔浆池。
所有烟道仅采用外部加强筋,以防止颤动和振动,并且设计满足在各种烟气温度和压力下能提供稳定的运行,内部没有加强筋或支撑。
烟道外部加强筋统一间隔排列。
加强筋使用统一的规格尺寸,尽量减少加强筋的规格尺寸,以便使敷设在加强筋上的保温层易于安装,并且增加外层美观,加强筋的布置要防止积水。
所有烟道在适当位置配有足够数量和大小的人孔门,以便于烟道(包括膨胀节和挡板门)的维修和检查。
另外,人孔门与烟道壁分开保温,以便于开启。
烟道的设计尽量减小烟道系统的压降,其布置、形状和内部件(如导流板和转弯处导向板)等均进行优化设计。
为了使与烟道连接的设备的应力控制在允许范围内,特别要注意考虑烟道系统的热膨胀,热膨胀通过膨胀节进行控制。
投标方提供支吊架组装图及支吊架生根所需的土建埋件技术要求(包括埋件位置,材料,尺寸及荷载与受力方式等)。
烟道的滑动支架,其滑动底板使用聚四氟乙烯组件。
1.342烟气挡板(1)设计原则挡板的设计能承受各种工况下烟气的温度和压力,并且不会有变形或泄漏。
挡板和驱动装置的设计能承受所有运行条件下工作介质可能产生的腐蚀。
(2)技术性能烟道挡板采用单挡板型式,而且具有100%的气密性。
烟气挡板能够在最大的压差下操作,并且关闭严密,不会有变形或卡涩现象,而且挡板在全开和全闭位置与锁紧装置要能匹配,烟道挡板的结构设计和布置要使挡板内的积灰减至最小。
挡板打开/关闭位置的信号将用于锅炉引风机和锅炉的联锁保护。
每个挡板全套包括框架、挡板本体、气动执行器,挡板密封系统及所有必需的密封件和控制件等。
烟道挡板框架的安装是法兰螺栓连接。
挡板尽可能按水平主轴布置。
投标方根据烟气特性选择挡板各个部件(包括挡板框架、叶片、轴密封片及螺栓连接件等)的材料,并提交业主确认。
特别注意了框架、轴和支座的设计,以便防止灰尘进入和由于高温而引起的变形或老化。
所有挡板从烟道内侧和外侧都要容易接近,因此投标方在每个挡板和其驱动装置附近设置平台,以便检修与维护挡板所有部件。
全部挡板采用可拆卸保温结构,并且避免产生热不均匀现象。
1.343膨胀节(1)设计原则膨胀节用于补偿烟道热膨胀引起的位移。
膨胀节在所有运行和事故条件下都能吸收全部连接设备和烟道的轴向和径向位移。
所有膨胀节的设计无泄漏,并且能承受系统最大设计正压/负压再加上10mbar余量的压力。
所有膨胀节考虑防腐要求。
烟道膨胀节有保温处理。
(2)技术性能膨胀节由多层材料组成,采用非金属膨胀节。
膨胀节考虑烟气的特性,膨胀节外保护层考虑检修。
位于水平烟道段的膨胀节通过膨胀节框架排水,排水孔最小为DN150,并且位于水平烟道段的中心线上。
排水配件能满足运行环境要求,由FRP、合金材料制做(至少是316L),排水返回到FGD区域的排水坑。
烟道上的膨胀节采用螺栓法兰连接,布置能确保膨胀节可以更换。
所有膨胀节框架有同样的螺孔间距,间距不超过100mm。
最少在膨胀节每边提供1m的净空,包括平台扶梯和钢结构通道的距离。
膨胀节及与烟道的密封有100%气密性。
膨胀节的法兰密封焊在烟道上。
特别注意不锈钢与普通钢的焊接(即使提供了内衬),以便将腐蚀减至最小。
膨胀节和膨胀节框架全部在车间制造和钻孔,并且运输整套组件。
如果装运限制,要求拆开完整的膨胀节,那么这种拆开范围也最多仅是满足装运的限定,临时设置的钢条和支架将附在膨胀结框架一起,以维持准确的接合面尺寸,直到完成FGD系统和烟道的安装工作框架内外密封焊在烟道上。
邻近挡板的膨胀节留有充分的距离,防止与挡板的动作部件互相干扰。
1.4 SO2吸收系统1.4.1技术性能脱硫副产物要求以硫酸镁为主要形式。
脱硫剂氢氧化镁浆液通过循环泵从吸收塔浆池送至塔内喷淋系统,与烟气接触发生化学反应吸收烟气中的SO2,主要生成亚硫酸镁,经过强制氧化系统氧化成硫酸镁。
吸收塔浆液排出泵将脱硫副产物浆液从吸收塔送到脱硫副产物脱水系统。
设置吸收塔预喷淋装置,其主要目的是去除烟气中的烟尘、气体杂质和降低烟气温度,提高脱硫副产品的品质,保证副产品的综合利用。
投标方对吸收塔和整个浆液循环系统进行优化设计,整个系统可适应锅炉负荷的变化,保证脱硫效率及其它各项技术指标达到合同要求。
脱硫后的烟气夹带的液滴在吸收塔出口的除雾器中收集,使净烟气的液滴含量不超过保证值。
SO2吸收系统包括:吸收塔、吸收塔浆液循环及搅拌、脱硫废液排出、烟气除雾及辅助的放空、排空设施等。
吸收塔内浆液最大Cl离子浓度为10g/l。
1.4.2吸收塔1.421设计原则吸收塔采用喷雾塔,在吸收塔前设置预洗涤除尘装置,以降低烟气温度及除去灰尘和其它气体杂质,保证脱硫系统后烟气烟尘含量w 35mg/Nm3。
吸收塔由投标方按设备整体供货,包括吸收塔壳体、喷嘴及所有内部构件、吸收塔搅拌装置、除雾器、塔体防腐及保温紧固件等。
塔体的预组装在工厂内完成,塔体的组装、塔内防腐、保温及保温紧固件的施工可由投标方在现场完成。
吸收塔内所有部件能承受最大入口气流及最高进口烟气温度的冲击,高温烟气不会对任何系统和设备造成损害。