拨叉说明书
拨叉设计毕业设计说明书
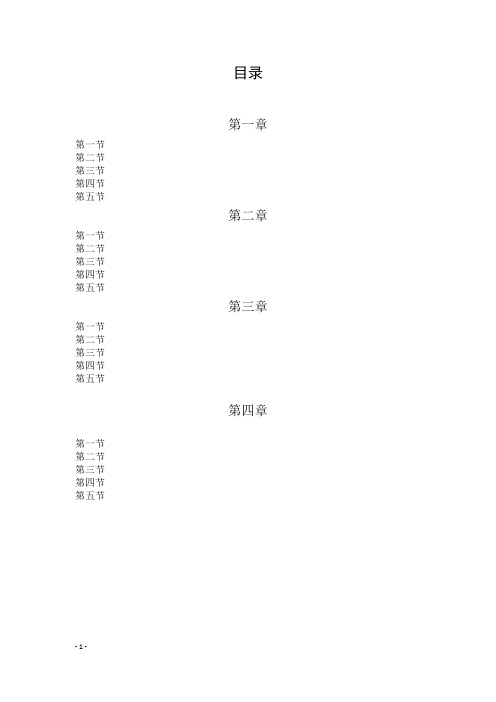
目录第一章第一节第二节第三节第四节第五节第二章第一节第二节第三节第四节第五节第三章第一节第二节第三节第四节第五节第四章第一节第二节第三节第四节第五节第一章拨叉的工艺规程设计第一节拨叉的工艺分析及生产类型的确定一、拨叉的用途和主要工作面分析该拨叉位于某机器变速箱的换挡机构中,使主轴回转运动按照工作者的要求工作,获得所需的速度和扭矩的作用。
零件上方的φ20孔与操纵机构相连,二下方的φ113半圆孔则是用于与所控制齿轮所在的轴接触。
通过上方的力拨动下方的齿轮变速。
两件零件铸为一体,加工时分开。
该拨叉在改换档位时要承受弯曲应力和冲击载荷的作用,因此该零件应具有足够的强度、刚度和韧性,以适应拨叉的工作条件。
该零件的主要工作φ)和叉脚底面,在设计工艺规程的过程表面为叉脚两端面、叉轴孔(208H中要重点予以保证。
二、拨叉的技术要求零件的材料为6003QT-,零件质量1.12kg。
该拨叉形状特殊,结构复杂,属典型叉杆类零件。
为实现换挡变速的功能要求,其叉轴孔与变速叉轴有配合要求,因此加工精度较高。
叉脚两端面在工作过程中需要承受冲击载荷,为增强其耐磨性,该表面要求淬火处理,硬度为48 ~ 58 HRC。
为此,把拨叉的各项技术要求如下:三、拨叉的工艺性审查分析零件图可知拨插头两端面和叉脚两端面均要求切削加工,并在轴向方向上均高于相邻表面,这样既减少了加工面积,又提高了换挡时叉脚端面的接触刚度;零件除主要工作表面外其余工作表面加工精度均要求不高,不需要高精度机床加工,通过铣削、钻床的加工就可以达到加工要求;而主要工作表面虽然加工精度要求较高,但也可以在正常的生产条件下,采用较经济的方法保质保量地加工出来。
由此可知,该零件的工艺性较好。
四、拨叉的生产类型此零件的生产类型为大量生产。
第二节确定毛坯并绘制毛坯图一、选择毛坯考虑到零件的工作要求和加工经济性,零件毛坯选择铸件,砂型铸造。
二、确定毛坯的尺寸公差和机械加工余量三、绘制拨叉的铸造毛坯简图图xx 拨叉铸造毛坯简图第三节拨叉工艺路线的拟定一、定位基准的选择1,精基准的选择根据拨叉零件的技术要求,选择拨叉左端面和叉轴孔作为精基准,,零件上的很多表面都可以采用他们作基准进行加工,即遵循了“基准统一”的原则。
拨叉说明书(超详细)
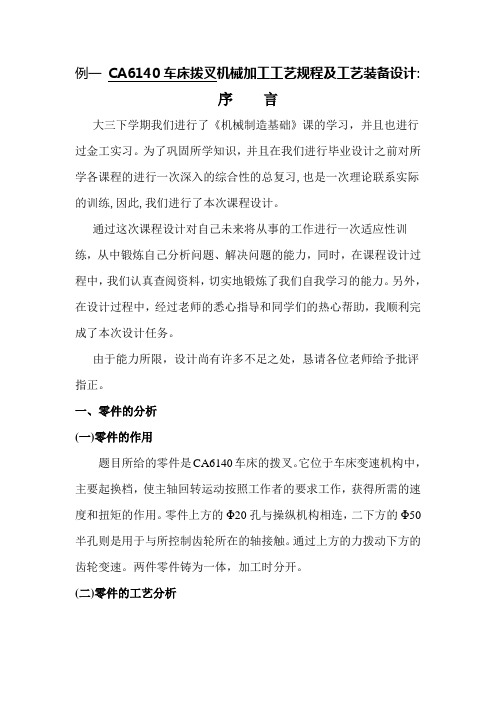
例一CA6140车床拨叉机械加工工艺规程及工艺装备设计:序言大三下学期我们进行了《机械制造基础》课的学习,并且也进行过金工实习。
为了巩固所学知识,并且在我们进行毕业设计之前对所学各课程的进行一次深入的综合性的总复习,也是一次理论联系实际的训练,因此,我们进行了本次课程设计。
通过这次课程设计对自己未来将从事的工作进行一次适应性训练,从中锻炼自己分析问题、解决问题的能力,同时,在课程设计过程中,我们认真查阅资料,切实地锻炼了我们自我学习的能力。
另外,在设计过程中,经过老师的悉心指导和同学们的热心帮助,我顺利完成了本次设计任务。
由于能力所限,设计尚有许多不足之处,恳请各位老师给予批评指正。
一、零件的分析(一)零件的作用题目所给的零件是CA6140车床的拨叉。
它位于车床变速机构中,主要起换档,使主轴回转运动按照工作者的要求工作,获得所需的速度和扭矩的作用。
零件上方的Φ20孔与操纵机构相连,二下方的Φ50半孔则是用于与所控制齿轮所在的轴接触。
通过上方的力拨动下方的齿轮变速。
两件零件铸为一体,加工时分开。
(二)零件的工艺分析零件的材料为HT200,灰铸铁生产工艺简单,铸造性能优良,但塑性较差、脆性高,不适合磨削,为此以下是拨叉需要加工的表面以及加工表面之间的位置要求:1、小头孔Φ20以及与此孔相通的Φ8的锥孔、M6螺纹孔2、大头半圆孔Φ503、拨叉底面、小头孔端面、大头半圆孔端面,大头半圆孔两端面与小头孔中心线的垂直度误差为0.07mm,小头孔上端面与其中心线的垂直度误差为0.05mm。
由上面分析可知,可以粗加工拨叉下端面,然后以此作为基准采用专用夹具进行加工,并且保证位置精度要求。
再根据各加工方法的经济精度及机床所能达到的位置精度,并且此拨叉零件没有复杂的加工曲面,所以根据上述技术要求采用常规的加工工艺均可保证。
二、确定毛坯1、确定毛坯种类:零件材料为HT200。
考虑零件在机床运行过程中所受冲击不大,零件结构又比较简单,生产类型为中批生产,故选择木摸手工砂型铸件毛坯。
拨叉类说明书。

目录第一章零件的工艺分析 (2)1.1零件的功用、结构及特点 (2)1.2主要加工表面几及其要求 (2)第二章毛坯的选择 (3)2.1确定毛坯的类型、制造方法和尺寸及其公差 (3)2.2确定毛坯的技术要求 (3)2.3绘制毛坯图 (4)第三章基准的选择 (5)第四章拟定机械加工工艺路线 (6)4.1 确定各表面的加工方法 (6)4.2 拟订加工工艺路线 (7)4.3工艺路线方案的分析与比较 (8)第五章确定机械加工余量、工序尺寸及公差 (9)第六章选择机床及工艺装备 (9)6.1选择机床 (9)6.2选择刀具 (9)6.选择夹具 (10)6.选择量具 (11)第七章确定切削用量及基本工时 (13)第八章夹具的设计 (16)第九章UG仿真加工························第十章填写工艺文件 (18)总结 (19)参考文献 (20)第一章零件的工艺分析1.1零件的功用、结构及特点该零件是以φ15H8孔套在轴上,并用销钉经φH12孔与轴定位的,拨叉脚卡在双联齿轮的槽中,变速操纵机构通过拨叉头部的操纵槽带动拨叉与轴一起在变速箱中滑动,拨叉脚拨动双联齿轮在花键轴上滑移,就可实现变速箱的变速功能,从而实现拖拉机的变速。
拨叉的主要工作表面为操纵箱及拨叉两端面。
主要配合面为φ15H8孔、φ5H12孔和拨叉脚内侧而50H12。
该零件属特殊形状零件,但复杂程度一般。
由于拨叉在工作时有一定的强度、刚度和韧度。
1.2 主要加工表面几及其要求1. 拨叉安装孔)的孔是拨叉的安装孔,起形状公差遵守包括要求,表面孔径φ15H8(+0.027粗糙度Ra为3.2μm;孔端面位置尺寸为30mm,表面粗糙度Ra为12.5μm2. 拨叉脚端面)mm,两端面对孔φ15H8轴线的垂直度公差为拨叉脚端面的厚度为7(-0.15-0.250.1mm,外端面与操纵槽对称面的距离为31mm,表面粗糙度Ra为6.3μm.。
拨叉831005设计说明书

加工余量为 2.8mm,精加工余量为 0.2mm。加工余量一共是 3mm。 毛锻件尺寸 零件尺寸 mm 27 单面加工余量 3 1 2.5 铸件尺寸 mm 27 尺寸偏差
22 25
24 30
3
2.3 绘 制 毛 坯 图
1
拨 叉 831005 1. 零 件 图 分 析
备注
1.1 零 件 的 功 用 题目给定的零件是 CA6140 拨叉(见附图 1)它位于车床变速 机构中, 主要起换档, 使主轴回转运动按照工作者的要求进行工作。 宽度为 18+0.0120mm 的槽尺寸精度要求很高,因为在拨叉拔动使 滑移齿轮时如果槽的尺寸精度不高或间隙很大时,滑移齿轮得不到 很高的位置精度。所以,宽度为 18+0.0120mm 的槽和滑移齿轮的 配合精度要求很高。 1.2 零 件 工 艺 分 析 CA6140 拨叉共有两组加工表面。 (1) 、以花键孔的中心线为基准的加工面这一组面包括 Φ 25+0.0230mm 的六齿方花键孔、Φ 22+0.280 花键底孔两端的 2X150 到角和距中心线为 27mm 的平面。 (2) 、以工件右端面为基准的 8+0.030 mm 的槽和 18+0.120mm 的槽经上述分析可知, 对于两组加工表面,可先加工其中一组表 面,然后借助于专用夹具加工另一组表面。
目录
1.零件图分析.................................................................................................................................... 2 1.1 零件的功用.................................
拔叉说明书

1 零件的分析1.1零件的作用拨叉是一种辅助零件,通过拨叉控制滑套与旋转齿轮的接合。
滑套上面有凸块,滑套的凸块插入齿轮的凹面,把滑块与齿轮连在一起,使齿轮带动滑块,滑套带动输出轴,将动力从输入轴传送至输出轴。
摆动拨叉可以控制滑套与不同齿轮的结合与分离,达到换档的目的。
分析这种动力联接方式可知,车换档时要减速,这样可以减少滑套与齿轮之间的冲击,延长零件的使用寿命。
题目给定的零件是CA6140拨叉。
它位于车床变速机构中,主要起换档,使主轴回转运动按照工作者的要求进行工作,获得所需的速度和扭矩的作用。
拨叉头以Ø22+0.280孔套在变速叉轴上,并用花键与变速叉轴连接,拨叉教夹在变换齿轮的槽中,当需要变速时,操纵变速杆,变速操纵机构就通过拨叉头部的操纵槽带动拨叉与变速叉轴一起在变速箱中滑移,拨叉脚拨动齿轮在化简轴上滑动以变换档位,从而改变主轴转速。
该拨叉在变换档位时要承受弯曲应力及冲击载荷作用,因此该零件应有足够强,度,刚度和韧性,以适应拨叉的工作条件。
该零件的主要工作表面为叉轴孔Ø22+0.280拨叉脚内表面及操纵槽。
宽度为18+0.012mm的槽尺寸精度要求很高,因为在拨叉拔动使滑移齿轮时如果槽的尺寸精度不高或间隙很大时,滑移齿轮得不到很高的位置精度。
所以,宽度为18+0.0120mm的槽和滑移齿轮的配合精度要求很高。
1.2零件的工艺分析CA6140拨叉共有两组加工表面:2.2.1以花键孔的中心线为基准的加工面这一组面包括Ø25+0.0230mm的六齿矩形花键孔Ø22+0.28花键底孔两端的2X150倒角和距中心线为27mm的平面。
2.2.2以工件右端面为基准的8+0.030 mm的槽和18+0.012mm的槽经上述分析可知,对于两组加工表面,可先加工其中一组表面,然后借助于专用夹具加工另一组表面。
图2.1 零件尺寸图2 选择加工方法制定工艺路线2.1 定位基准的选择基准选择是工艺规程设计中的重要工作之一。
拨叉零件说明书
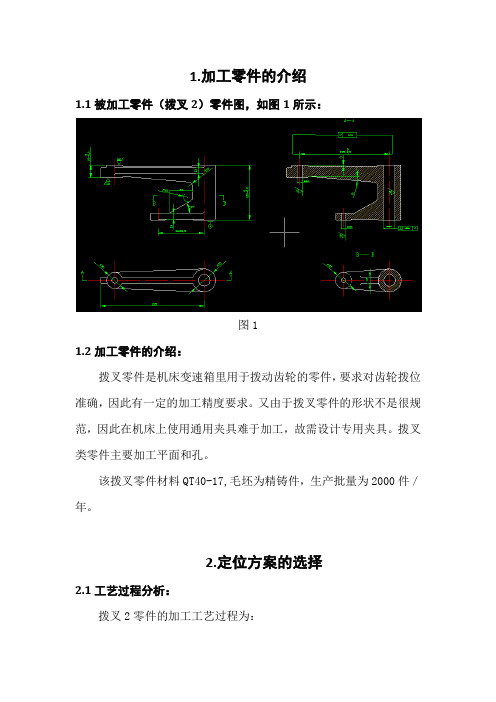
S S1S2 S3S4 2 11.2 1 2.4
1 3
3.夹紧方案的选择
3.1 确定夹紧方案(如图 3 所示) :
图3 在上图中,丝杠左端为左旋,右端为右旋,通过转动丝杠,可以 使丝杠上的两个滑块产生相对运动, 从而滑块上的斜面对压紧杠杆施 加作用力,使工件达到夹紧的作用。当丝杠反向转动时可以将工件松 开。 3.2 夹紧力的估算: 通常,由于切削力本身是估算的,工件与支承件间的摩擦因数也 是近似的,因此夹紧力也是粗略估算的。在计算夹紧力时,将夹具和 工件看作一个刚性系统,以切削力的作用点,方向和大小处于最不利 于夹紧时的状况为工件受力状况,根据切削力、夹紧力(大工件还应 考虑重力, 运动速度较大时应考虑惯性力) , 以及夹紧机构具体尺寸, 列出工件的静力平衡方程式,求出理论夹紧力,再乘以安全系数,作 为实际所需夹紧力。 安全系数一般可取 S 2 3 ,或按下式计算:
工 x 轴方向和 y 轴方向的线自由度, 底面为大平面限制 z 轴方向的线 自由度和绕 x 轴和 y 轴的旋转自由度,侧面为第二定位基准面,由于 要限制工件绕 Y 轴的旋转自由度,并且考虑到工件为圆柱型,选择一 个 V 型块为定位元件,实际限制六个自由度即 X、Y、Z 轴方向的线性 自由度和绕 X,Y,Z 轴的旋转自由度;定位方案能够保证加工尺寸精 度和两孔平行度要求。 2.3.3 定位误差的计算: 本工序的定位误差主要以两支撑钉的定位误差为主,V 型块主要 起辅助作用,具体分析过程如下: (1)基准不重合误差为 0; (2)定位引起的误差: 平面产生的位移误差,该误差由加工平面时的精度决定,一般很 小,可以忽略不计,所以总误差也很小,定位误差显然在工件允许误 差的 范围内,所以加工精度足以保证。
拨叉说明书
3、 审查拨叉的工艺性
CA6140 车床共有两处加工表面,其间有一定位置要求。分述如 下: 1. 以φ 20mm 为中心的加工表面 这一组加工表面包括:φ 20mm 的孔,以及其上下端面,上端面 与孔有位置要求,孔壁上有一个装配时钻铰的锥孔,一个 M6 的螺纹 孔。这三个都没有高的位置度要求。 2. 以φ 50 为中心的加工表面 这一组加工表面包括:φ 50mm 的孔,以及其上下两个端面。 这两组表面有一定的位置度要求,即φ 50 mm 的孔上下两个端面 与φ 20mm 的孔有垂直度要求。 由上面分析可知,加工时应先加工一组表面,再以这组加工后表 面为基准加工另外一组。
7
工序六 以 φ 20mm 孔为精基准,粗铣 φ 50mm 孔上下端面。 工序七 以 φ 20mm 孔为精基准,精铣 φ 50mm 孔上下端面,保证 端面相对孔的中心线垂直度误差不超过 0.07。 工序八 以 φ 20mm 孔为精基准,钻 φ 8mm 孔(装配时钻铰锥孔) 。 工序九 以 φ 20mm 孔为精基准,钻一个 φ 4mm 孔,攻 M6 螺纹。 工序十 以 φ 20mm 孔为精基准,铣 47°凸台。 工序十一 去毛刺、清洗。 工序十二 终检。 。 以上工艺过程详见图 3。 在综合考虑上述工序顺序安排原则的基础上, 表列出了拨叉的工 艺路线,如下: 工序号 1 上下端面 2 上下端面 3 精铰 φ 20 孔 4 精铰 φ 50 孔 5 切断 铣床
0.06 0.18
Φ 50 0.25 Φ
0.50
IT12 IT7 IT13 IT113.2 1.6来自200.0210
Φ8
70
0 0 .2
3.2
12
0.06 0.18
IT11
6.3
⊥ 0.07 A
拨叉钻孔夹具说明书
第一部分设计任务书及课程设计的要求和内容加工 (2)其次部分序言 (4)第三部分拨叉Φ22mm 孔的钻床夹具设计 (5)第四部分.致谢与心得体会 (15)第五部分参考文献 (16)附录:夹具零件图与夹具装配图(草稿) .................. 17(18) CAD图另图 (19)第一部分:山西大同高校煤炭工程学院09机械设计及其自动化专业《机械制造设施设计》设计任务书设计题目:CA6140拨叉钻床夹具设计要求:设计加工孔①22mm的钻床夹具毛坯类型:铸件(两件铸在一起)设计时间:2022.1217——设计内容:1、熟识零件图2、绘制零件图(一张)3、绘制夹具总装图4、编写设计说明书备注:CA6140车床拨叉831002毛坯图其次部分:序言机械制造装备设计使我们学完了高校的全部基础课、技术基础课以及大部分专业课之后进行的.这是我们在进行毕业设计之前对所学各课程的一次深化的综合性的总复习, 也是一次理论联系实际的训练,因此,它在我们四年的高校生活中占有重要的地位。
就我个人而言,我盼望能通过这次课程设计对自己将来将从事的工作进行一次适应性训练,从中熬炼自己分析问题、解决问题的力量,为今后参与祖国的“四化”建设打下一个良好的基础。
制造背景:机械制造离不开金属切削机床,而机床夹具则是保证机械加工质量、提高生产效率、减轻劳动强度、降低对工人技术的过高要求、实现生产过程自动化不行或缺的重要工艺装备之一。
机床夹具被广泛用于制造业中,大量专用机床夹具的使用为大批量生产供应了必要条件。
在机床制造或修理中,经常遇到在圆柱上横穿孔的工件,这些工件的孔或螺纹孔的中心线不相交,需在车好圆柱后装配,画好孔的位置线,在按线加工孔或螺纹。
以前当工件画好线后,用四爪卡盘按线进行安装,再加工内孔。
在校正的过程中,调整夹在圆柱面上的两爪时,工件产生滚动,使划线孔的中心线产生角度位移,很难将工件校正, 而产生加工废品。
为此人们设计制造了夹具,通过30年的使用,效果很好。
拨叉零件设计说明书
目录前言-------------------------------------------------3 1 拨叉工艺分析及生产类型的确定----------------------4 1.1 拨叉的用途---------------------------------------4 1.2 拨叉的技术要求-----------------------------------4 1.3 审查拨叉的工艺性---------------------------------61.4 确定拨叉的生产类型-------------------------------62 确定毛坯、绘制毛坯简图----------------------------7 2.1 选择毛坯-----------------------------------------7 2.2 确定毛坯的尺寸公差和机械加工余量-----------------72.3 绘制拨叉毛坯简图---------------------------------83 拟定拨叉工艺路线---------------------------------8 3.1 定位基准的选择-----------------------------------8 3.2 加工阶段的划分-----------------------------------9 3.3 工序的集中分散-----------------------------------9 3.4 工序顺序的安排-----------------------------------103.5 确定工艺路线-------------------------------------104 加工余量、工序尺寸和公差的确定-------------------16 4.1 孔的加工余量、工序尺寸和公差的确定---------------164.2 端面的加工余量、工序尺寸和公差的确定-------------165 切削用量、时间定额的计算-------------------------17 5.1 切削用量的计算-----------------------------------17 5.1.1 铣端面切削用量的计算--------------------------175.1.2 镗孔切削用量的计算---------------------------19 5.1.3 钻孔镗孔用量的计算---------------------------21 5.1.4对拉键槽进行计算-------------------------------23 5.2 时间定额计算-------------------------------------24 5.2.1 铣端面基本时间的计算-------------------------245.2.2 镗孔及所有工序基本时间的计算-----------------256 夹具设计-----------------------------------------27 6.1 定位方案的设计-----------------------------------27 6.2 夹紧方案的设计-----------------------------------27 6.3 定位误差分析和计算-------------------------------27 结论------------------------------------------------28 致谢------------------------------------------------29 参考文献--------------------------------------------30前言机械制造技术基础毕业设计是我们完成了基础课程和部分技术基础课程之后进行的。
副变速拨叉说明书
目录1 零件的工艺分析及生产类型的确定⋯⋯⋯⋯⋯⋯⋯⋯⋯⋯⋯⋯⋯⋯1 1.1零件的作用⋯⋯⋯⋯⋯⋯⋯⋯⋯⋯⋯⋯⋯⋯⋯⋯⋯⋯⋯⋯⋯⋯⋯⋯⋯1 1.2零件的工艺分析⋯⋯⋯⋯⋯⋯⋯⋯⋯⋯⋯⋯⋯⋯⋯⋯⋯⋯⋯⋯⋯⋯⋯11.3确定零件的生产类型⋯⋯⋯⋯⋯⋯⋯⋯⋯⋯⋯⋯⋯⋯⋯⋯⋯⋯⋯⋯⋯12 确定毛胚类型绘制毛胚简图⋯⋯⋯⋯⋯⋯⋯⋯⋯⋯⋯⋯⋯⋯⋯⋯⋯⋯1 2.1选择毛胚⋯⋯⋯⋯⋯⋯⋯⋯⋯⋯⋯⋯⋯⋯⋯⋯⋯⋯⋯⋯⋯⋯⋯⋯⋯⋯1 2.2确定毛胚尺寸和机加工余量⋯⋯⋯⋯⋯⋯⋯⋯⋯⋯⋯⋯⋯⋯⋯⋯⋯⋯12.3铸件毛胚图⋯⋯⋯⋯⋯⋯⋯⋯⋯⋯⋯⋯⋯⋯⋯⋯⋯⋯⋯⋯⋯⋯⋯⋯⋯23 工艺规程设计⋯⋯⋯⋯⋯⋯⋯⋯⋯⋯⋯⋯⋯⋯⋯⋯⋯⋯⋯⋯⋯⋯⋯⋯⋯2 3.1定位基准的选择⋯⋯⋯⋯⋯⋯⋯⋯⋯⋯⋯⋯⋯⋯⋯⋯⋯⋯⋯⋯⋯⋯⋯2 3.2拟定工艺路线⋯⋯⋯⋯⋯⋯⋯⋯⋯⋯⋯⋯⋯⋯⋯⋯⋯⋯⋯⋯⋯⋯⋯⋯4 3.3加工设备及工艺装备的选用⋯⋯⋯⋯⋯⋯⋯⋯⋯⋯⋯⋯⋯⋯⋯⋯⋯⋯6 3.4加工余量、工序尺寸和公差的确定⋯⋯⋯⋯⋯⋯⋯⋯⋯⋯⋯⋯⋯⋯⋯73.5确立切削用量及基本工时⋯⋯⋯⋯⋯⋯⋯⋯⋯⋯⋯⋯⋯⋯⋯⋯⋯⋯⋯84 专用钻床夹具设计⋯⋯⋯⋯⋯⋯⋯⋯⋯⋯⋯⋯⋯⋯⋯⋯⋯⋯⋯⋯⋯⋯134.1夹具设计任务⋯⋯⋯⋯⋯⋯⋯⋯⋯⋯⋯⋯⋯⋯⋯⋯⋯⋯⋯⋯⋯⋯⋯134.2拟定钻床夹具结构方案与绘制夹具草图⋯⋯⋯⋯⋯⋯⋯⋯⋯⋯⋯⋯144.3绘制夹具装配总图⋯⋯⋯⋯⋯⋯⋯⋯⋯⋯⋯⋯⋯⋯⋯⋯⋯⋯⋯⋯⋯144.4夹具装配图上标注尺寸,定位误差分析⋯⋯⋯⋯⋯⋯⋯⋯⋯⋯⋯⋯15课程设计总结⋯⋯⋯⋯⋯⋯⋯⋯⋯⋯⋯⋯⋯⋯⋯⋯⋯⋯⋯⋯⋯⋯⋯⋯⋯17参考文献⋯⋯⋯⋯⋯⋯⋯⋯⋯⋯⋯⋯⋯⋯⋯⋯⋯⋯⋯⋯⋯⋯⋯⋯⋯⋯⋯171零件的工艺分析及生产类型的确定1.1 零件的作用副变速拨叉是变速箱换挡机构中的一个重要零件。
拨叉头以 14mm 孔套在变速叉轴上,并用销钉经8.7mm 孔与变速叉轴连接,拨叉脚则夹在双联变换齿轮的槽中。
- 1、下载文档前请自行甄别文档内容的完整性,平台不提供额外的编辑、内容补充、找答案等附加服务。
- 2、"仅部分预览"的文档,不可在线预览部分如存在完整性等问题,可反馈申请退款(可完整预览的文档不适用该条件!)。
- 3、如文档侵犯您的权益,请联系客服反馈,我们会尽快为您处理(人工客服工作时间:9:00-18:30)。
机械制造工艺学课程设计说明书题目:拨叉CA6140的工艺规程姓名:张冉学号: 20085650611班级: 08机械5班指导教师:孙丽媛2013年4月3日设计及计算过程 结果拨叉831002的加工工艺规程设计1.1零件的分析1.1.1零件的作用题目所给的零件是CA6140车床的拨叉。
它位于车床变速机构中,主要起换档,使主轴回转运动按照工作者的要求工作,获得所需的速度和扭矩的作用。
1.1.2零件的工艺分析零件的材料为HT200,灰铸铁属于脆性材料,故不能锻造和冲压。
但灰铸铁的铸造性能和切削加工性能优良。
以下是拨叉需要加工的表面以及加工表面之间的位置要求: (1) 中心圆孔Ф0.021025+。
(2) 22 1.5M ⨯的螺纹孔垂直于中心孔,其中心与右面的距离为00.344-。
(3) 键槽0.1116+与中心孔有0.08的垂直度,深为0.1508+。
(4) 半孔0.3060+Φ与中心孔有0.10.2127+-的位置关系,其宽为0.050.1612--与中心孔有0.1的垂直度。
由上面分析可知,可以先加工拨叉中心孔,然后以此作为基准采用专用夹具进行加工,并且保证位置精度要求。
再根据各加工方法的经济精度及机床所能达到的位置精度,并且此拨叉零件没有复杂的加工曲面,所以根据上述技术要求采用常规的加工工艺均可保证。
1.2确定生产类型已知此拨叉零件的生产类型为大批量生产,所以初步确定工艺安排为:加工过程划分阶段;工序应当集中;加工设备以通用设备为主,大量采用专用工装。
1.3确定毛坯1.3.1确定毛坯种类零件材料为HT200。
考虑零件在机床运行过程中所受冲击不大,零件结构不是太复杂,生产类型为大批生产,故选择金属型铸造毛坯。
1.3.2确定铸件加工余量及形状查《机械零件切削加工工艺与技术标准实用手册》125页表1-4-7,选用各个加工面的铸件机械加工余量均为3mm。
1.4工艺规程设计1.4.1选择定位基准①粗基准的选择以零件的下端孔为主要的定位粗基准,以较大面a面为辅助粗基准。
②精基准的选择考虑要保证零件的加工精度和装夹准确方便,依据“基准重合”原则和“基准统一”原则,以加工后的通孔为主要的定位精基准,以下端孔为辅助的定位精基准。
1.4.2制定工艺路线根据零件的几何形状、尺寸精度及位置精度等技术要求,以及加工方法所能达到的经济精度,在生产纲领已确定的情况下,可以考虑采用各种机床配以专用夹具,并尽量使工序集中来提高生产率。
除此之外,还应当考虑经济效果,以便使生产成本尽量下降。
选择零件的加工方法及工艺路线方案如下:表1.1工艺路线方案一工序号工序内容工序一粗、钻、扩、铰、精铰Φ25、Φ60孔工序二粗、精铣Φ60、Φ25孔下端面工序三粗铣、精铣Φ25孔上端面工序四粗铣、精铣Φ60孔上端面工序五切断工序六铣螺纹孔端面工序七钻Φ22孔(装配式钻铰锥孔)工序八攻M22×1.5的螺纹工序九粗铣半精铣精铣槽所在的断面工序十粗铣半精铣惊喜16H11的槽工序十一检查上面的工序加工不太合理,因为由经验告诉我们大多数都应该先铣平面再加工孔,那样会更能容易满足零件的加工要求,效率不高,但同时钻两个孔,对设备有一定要求。
表1.2工艺路线方案二工序号工序内容工序一粗、精铣Φ25孔上端面工序二粗、精铣Φ25孔下端面工序三钻、扩、铰精铰Φ25孔工序四钻、扩、铰精铰Φ60孔工序五粗、精铣Φ60孔上端面工序六粗、精铣Φ60孔下端面工序七铣螺纹孔端面工序八钻Φ22孔(装装配时钻铰锥孔)工序九攻M22*1.5螺纹工序十粗铣半精铣精铣槽所在的断面工序十一粗、半精铣惊喜16H11的槽续表1.2工序十二切断工序十三检查此方案仍有先钻孔再铣平面的不足,所以这个方案仍不是最好的工艺路线,综合考虑以上各方案的各部族因素,得到以下我的工艺路线。
工序号工序内容工序一以Φ42外圆为粗基准,粗铣Φ25孔下端面工序二以Φ25孔上端面为精基准,钻、扩、铰精铰Φ25孔,孔的精度达到IT7工序三以Φ25孔为精基准,粗铣Φ60孔上下断面工序四以Φ25孔为精基准,精铣Φ60孔上下端面,保证端面相对孔的垂直度误差不超过0.1工序五以Φ25孔为精基准,钻、镗、铰Φ60孔,保证孔的精度达到IT8工序六以Φ25孔为精基准,铣螺纹孔端面工序七以Φ25孔为精基准,钻Φ20孔(装配时钻铰锥孔)工序八以Φ25孔为精基准,钻一个Φ20孔,攻M22*1.5螺纹工序九以Φ25孔为精基准,铣槽断面工序十以Φ25孔为精基准,铣16H111的槽保证槽的侧面相对孔的垂直度误差是0.08工序十一两件铣断工序十二检查此工序是十二步,但是效率大大提高了。
工序一盒工序二比起工艺路线方案二快了一倍(实际铣削只有两次,而且刀具不用调整)。
多次加工Φ60,Φ25孔是精度要求所致。
1.4.3选择加工设备和工艺设备①机床的选择工序1、7、8、11、采用X6022型卧式铣床工序2、3、4、5、6 采用Z535立式钻床工序9、10采用T618卧式镗床②选择夹具该拨叉的生产纲领为大批生产,所以采用专用夹具。
③选择刀具在铣床上加工的各工序,采用硬质合金铣刀即可保证加工质量。
在铰孔 ,由于精度不高,可采用硬质合金铰刀。
257H④选择量具加工的孔均采用极限量规。
⑤其他对垂直度误差采用千分表进行检测,对角度尺寸利用专用夹具保证,其他尺寸采用通用量具即可。
1.4.4机械加工余量、工序尺寸及公差的确定根据前面资料已初步确定工件各面的总加工余量,现在确定各表面的各个加工工序的加工余量如下:表2.3各加工工序的加工余量及达到的尺寸、经济度、粗糙度工序号工序内容加工余量经济精度工序尺寸表面粗糙度工序余量最小最大1粗铣Φ25H7的两侧面3 IT11 80 6.3 -0.1 0.1 2粗铣平下端孔侧面的工艺凸台3 IT11 0 6.3 -0.1 0.1 3 钻Φ25H7通孔IT12 22φ 6.3 -1 14 扩Φ25H7通孔2.0 IT12 0.0524.7φ+ 3.2 -0.05 0.055 铰Φ25H7通孔0.3 IT8 0.02125φ+ 1.6 -0.006 0.0066粗铣a、b面粗铣a面3 IT120.344-(距中心孔)6.3 -0.1 0.1 粗铣b面36(距中心孔)7粗铣Φ60H12孔的两面2 IT11 130.5± 6.3 -0.1 0.18精铣Φ60H12孔的两面1 IT9 0.050.1612--3.2 -0.05 0.059 粗镗下端孔2.5 IT13 00.359.7φ-6.3 -0.2 0.210 半精镗下端孔0.5 IT11 0.360φ+ 3.2 -0.02 0.02 续表2.311 粗铣16H11的槽 IT11140.5±6.3-0.10.112半精铣16H11的槽1 IT100.1116+ 3.2 -0.02 0.0213 钻Φ20.50的孔 IT1320.500.5φ±6.3 -1 114 攻22 1.5M ⨯的螺纹15 铣开Φ60H12的孔4 IT13 6.3 -0.05 0.051.5确定切削用量及基本工时工序一 以φ42外圆为粗基准,粗铣φ25孔上、下端面机床:X6022型卧式铣床刀具:两块镶齿套式面铣刀(间距为80),材料:15YT ,D=200mm ,齿数20Z =,为粗齿铣刀。
因其单边余量:Z=3mm 所以铣削深度p a :3p a mm =每齿进给量f a :根据参考文献[3]表2.4-73,取0.15/f a mm Z =铣削速度V :参照参考文献[3]表2.4-81,取 2.54/V m s =机床主轴转速n :10001000 2.5460242.68/min 3.14200V n r d π⨯⨯==≈⨯,按照参考文献[3]表3.1-74 245/min n r = 实际铣削速度v : 3.142002452.56/1000100060dnv m s π⨯⨯==≈⨯进给量f V :0.1520245/6012.25/f f V a Zn mm s ==⨯⨯≈ 工作台每分进给量m f :12.25/735/min m f f V mm s mm ===εa :根据参考文献[3]表2.4-81,mm a 60=ε 切削工时被切削层长度l :由毛坯尺寸可知L=42mm , 刀具切入长度1l :2210.5()(1~3)l D D a ε=--+245/min n r =v=2.56m / sf V =12.25mm / sm f =735mm/min mm a 60=ε220.5(20020060)(1~3)7.6mm =--+=刀具切出长度2l :取mm l 22= 走刀次数为1 机动时间1j t :121427.620.07min 735j m l l l t f ++++==≈ 查参考文献[1],表2.5-45工步辅助时间为:1.23min工序二 以φ25孔上端面为精基准,钻、扩、铰、精铰φ25孔,孔的精度达到IT7加工机床为Z535立式钻床。
铰刀为Ø25mm 标准高速铰刀。
确定铰孔切削用量①定进给量f 根据表28-36, 1.3~2.6f mm =表,按该表注4,进给量取小值。
查Z535说明书,取 1.6/f mm r =。
②确定切削速度v 及n 由表28-39,取8.2/min v m =表。
由表28-3,得修正系数0.88Mv k =,0.99p a v k = 2524.7(/0.125 1.2)2pR pa a -==根据 故'8.2/min 0.880.997.14/min v m m =⨯⨯=表''01000/()n v d π=表10007.14(/min)/(25)91.5/min m mm r π=⨯⨯= 查Z535说明书,取100/min n r =,实际铰孔速度3010v d n π-=⨯325100/min 107.8/min mm r m π-=⨯⨯⨯=切削工时被切削层长度l :78l mm =刀具切入长度1l ,012524.7(1~2)1202 2.0922r D d l ctgk ctg mm --=+=︒+≈刀具切出长度2l :mm l 4~12= 取mm l 32= 走刀次数为1机动时间3j t :378 2.0930.52min 1.6100j L t nf ++==≈⨯查参考文献[1],表2.5-41工步辅助时间为:1.51min该工序的加工机动时间的总和是j t : 1.080.540.52 2.14min j t =++=工序三 以φ25孔为精基准,粗铣φ60孔上、下端面机床:X6022型卧式铣床刀具:两块镶齿套式面铣刀(间距为14),材料:15YT ,200D mm = ,齿数20Z =,为粗齿铣刀。