minitab部分因子设计,响应面设计,参数设计
Minitab怎么做最优参数设计?

Minitab怎么做最优参数设计?
在Minitab中,最优参数设计是一种用于优化实验设计的方法,旨在找到最佳的参数组合,以最小化或最大化响应变量。
下面是一些关于Minitab最优参数设计的步骤:
1. 导入数据:首先,您需要将您的数据导入Minitab中。
您可以使用“输入”菜单中的“数据”选项导入数据。
2. 创建因子:在“选择”菜单中选择“因子”,然后选择“创建因子”。
在“创建因子”对话框中,您可以为每个因子指定名称、取值范围和单位。
3. 创建响应变量:在“选择”菜单中选择“响应变量”,然后选择您的响应变量。
您还可以为响应变量指定单位和度量单位。
4. 运行最优参数设计:选择“分析”菜单中的“最优参数设计”。
在“最优参数设计”对话框中,您可以指定因子和响应变量,并选择要优化的目标。
Minitab将自动计算最优参数
设计。
5. 查看结果:Minitab将显示最优参数设计的结果,包括每个参数组合的得分和权重。
您可以使用这些结果来确定最佳的参数组合。
通过使用Minitab进行最优参数设计,我们可以快速、准确地确定最佳参数组合,以实现最佳结果。
Minitab的强大功能可以帮助我们进行实验设计和参数优化,提高工作效率和质量。
末了,深圳天行健六西格玛培训公司想要提醒的是:最优参数设计是一种高级的分析方法,需要一定的统计学知识。
如果您不熟悉这些概念,建议先学习一些统计学基础知识,然后再尝试使用Minitab的最优参数设计功能。
响应面法和实验设计软件Minitab 及 Design-Expert简介
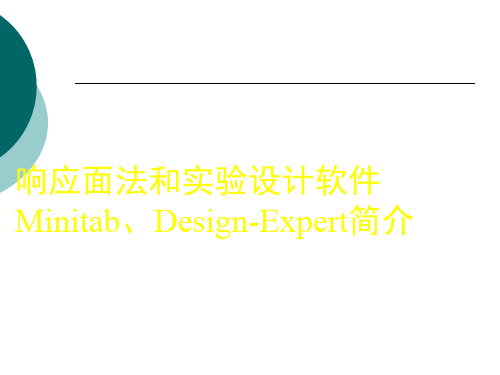
Adj MS 4.0517 2.5962 4.4619 5.0970 0.9920 1.4760 0.5079
F 4.08 2.62 4.50 5.14
P 0.019 0.109 0.030 0.021
2.91 0.133
R-Sq(adj) = 59.4%
此值大于0.05,表示二次多 项式回归模型正确。
非线性回归结果
输出结果:二次多项式回归方差分析表
此值小于0.05的项显著有效,回归的整体、二次项和交叉 乘积项都显著有效,但是一次项的效果不显著。
Source Regression
Linear Square Interaction Residual Error Lack-of-Fit Pure Error Total S = 0.9960
响应面法的分类
中心复合试验设计 (central composite design,CCD);
Box-Behnken试验设计;
中心复合试验设计
中心复合试验设计也称为星点设计。其设计
表是在两水平析因设计的基础上加上极值点和 中心点构成的,通常实验表是以代码的形式编 排的, 实验时再转化为实际操作值,(一般水 平取值为 0, ±1, ±α, 其中 0 为中值, α 为极值, α=F*(1/ 4 )
其设计表是在两水平析因设计的基础上加上极值点和中心点构成的通常实验表是以代码的形式编排的实验时再转化为实际操作值一般水平取值为01其中0为中值为极值f14精品资料boxbehnkendesignboxbehnkendesign简称bbd也是响应面优化法常用的实验设计方法其设计表安排以三因素为例三因素用abc表示见下页表其中0是中心点分别是相应的高值和低值
2. 创建“中心复合”或“Box-Behnken”设计; 3. 确定试验运行顺序(Display Design); 4. 进行试验并收集数据; 5. 分析试验数据; 6. 优化因素的设置水平。
响应表面试验设计方法和MINITAB优化(CCD_BBD)

立方点 轴向点 中心点 区组 序贯试验 旋转性
立方点(cube point)
立方点,也称立方体点、角点,即2水平对 应的“-1”和“+1”点。各点坐标皆为+1或-1。 在k个因素的情况下,共有2k个立方点
轴向点(axial point)
轴向点,又称始点、星号点,分布在轴向上。
这种设计失去了旋转性。但
保留了序贯性,即前一次在 立方点上已经做过的试验结 果,在后续的CCF设计中可 以继续使用,可以在二阶回
归中采用。
中心点的个数选择
在满足旋转性的前提下,如果适当选择Nc,则可 以使整个试验区域内的预测值都有一致均匀精度 (uniform precision)。见下表:
但有时认为,这样做的试验次数多,代价 太大, Nc其实取2以上也可以;如果中心 点的选取主要是为了估计试验误差, Nc 取4以上也够了。
一般步骤
1. 确定因素及水平,注意水平数为2,因素数一般不超 过4个,因素均为计量数据;
2. 创建“中心复合”或“Box-Behnken”设计; 3. 确定试验运行顺序(Display Design); 4. 进行试验并收集数据; 5. 分析试验数据; 6. 优化因素的设置水平。
2 中心复合试验设计
-1.00000 0.00000 1.00000 0.00000 0.00000 0.00000 0.00000
适用范围
确信或怀疑因素对指标存在非线性影响; 因素个数2-7个,一般不超过4个; 所有因素均为计量值数据; 试验区域已接近最优区域; 基于2水平的全因子正交试验。
方法分类
中心复合试验设计 (central composite design,CCD); Box-Behnken试验设计;
minitab部分因子设计,响应面设计,参数设计解读
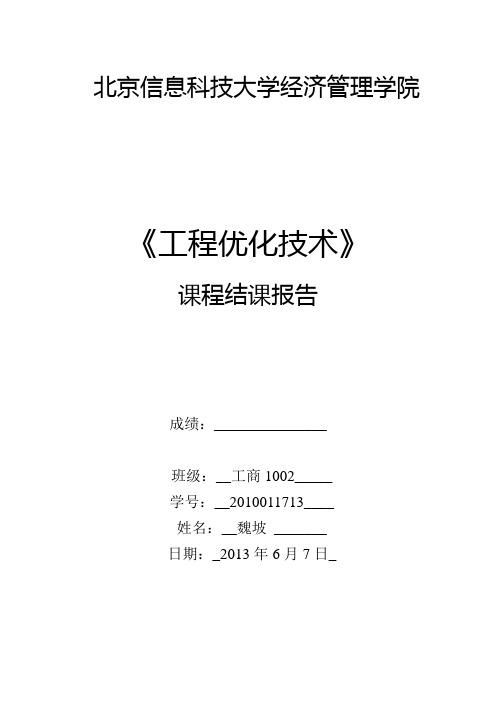
北京信息科技大学经济管理学院《工程优化技术》课程结课报告成绩:_______________班级:__工商1002_____学号:__2010011713____姓名:__魏坡_______日期:_2013年6月7日_部分因子试验设计1.实验设计背景部分因子试验设计与全因子试验设计的不同之处在于大大减少了试验的次数,具体表现在试验设计创建阶段的不一致,下面主要就部分因子试验设计的创建进行讲述。
2.因子选择用自动刨床刨制工作台平面的工艺条件试验。
在用刨床刨制工作台平面试验中,考察影响其工作台平面光洁度的因子,并求出使光洁度达到最高的工艺条件。
3.实验方案共考察6个因子:A 因子:进刀速度,低水平1.2,高水平1.4(单位:mm/刀)B 因子:切屑角度,低水平10,高水平12(单位:度)C 因子:吃刀深度,低水平0.6,高水平0.8(单位:mm )D 因子:刀后背角,低水平70,高水平76(单位:度)E 因子:刀前槽深度,低水平1.4,高水平1.6(单位:mm )F 因子:润滑油进给量,低水平6,高水平8(单位:毫升/分钟) 要求:连中心点在内,不超过20次试验,考察各因子主效应和2阶交互效应AB 、AC 、CF 、DE 是否显著。
由于试验次数的限制,我们在因子点上只能做试验16次,另4次取中心点,这就是6224-+的试验,通过查部分因子试验分辨度表可知,可达分辨度为Ⅳ的设计。
具体操作为:选择 [统计]=>[DOE ]=>[因子]=>[创建因子设计],单击打开创建因子设计对话框。
在“设计类型”中选择默认2水平因子(默认生成元),在“因子数”中选定6。
单击“显示可用设计”就可以看到下图的界面,可以确认:用16次试验能够达到分辨度为Ⅳ的设计。
单击“设计”选项,选定1/4部分实施,在每个区组的中心点数中设定为4,其他的不进行设定,单击确定。
单击“因子”选项,设定各个因子的名称,并设定高、低水平值。
响应面法和实验设计软件Minitab 及 Design-Expert介绍
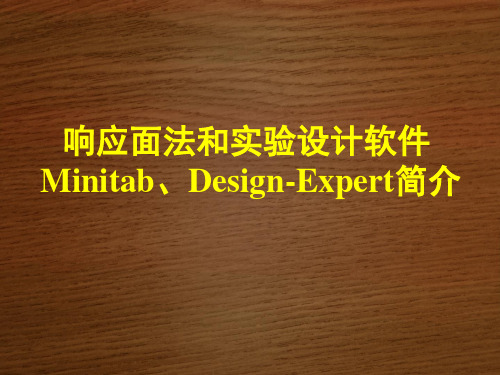
Box-Behnken Design
Box-Behnken Design,简称BBD,也是响应 面优化法常用的实验设计方法,其设计表安排 以三因素为例(三因素用A、B、C表示),见下 页表,其中 0 是中心点,+, -分别是相应的高 值和低值。
响应面法的实验设计一般步骤
1. 确定因素及水平,注意水平数为2,因素数一般不超 过4个,因素均为计量数据;
按上述公式选定的α值来安排中心复合试
验设计(CCD)是最典型的情形,它可以实 现试验的序贯性,这种CCD设计特称中心 复合序贯设计(central composite circumscribed design,CCC),它是CCD中 最常用的一种。
如果要求进行CCD设计,但又希望试验水平安排不 超过立方体边界,可以将轴向点设置为+1及-1,则 计算机会自动将原CCD缩小到整个立方体内,这种 设计也称为中心复合有界设计(central composite inscribed design,CCI)。
这样做,每个因素的取值水平只有3个(-1,0,1),而 一般的CCD设计,因素的水平是5个(-α,-1,0,1,α), 这在更换水平较困难的情况下是有意义的。
这种设计失去了旋转性。但
保留了序贯性,即前一次在 立方点上已经做过的试验结 果,在后续的CCF设计中可 以继续使用,可以在二阶回
归中采用。
中心点的个数选择
响应面优化法的优点
• 响应面优化法,考虑了试验随机误差;同时,响应面
法将复杂的未知的函数关系在小区域内用简单的一次 或二次多项式模型来拟合,计算比较简便,是解决实 际问题的有效手段。
• 所获得的预测模型是连续的,与正交实验相比,其优
势是:在实验条件寻优过程中,可以连续的对实验的 各个水平进行分析,而正交实验只能对一个个孤立的 实验点进行分析。
MINITAB响应曲面法应用

MINITAB响应曲面法应用响应面法优化牛蒡根总黄酮提取工艺以下是文献中利用Minitab统计软件的析因实验得到的一些相关数据:现在同样就这篇文章中的相关数据,利用minitab实际操作如下:一、部分析因设计及实验结果1.创建因子设计得:(对应表3)2.分析因子设计得:(对应表4)拟合因子:Y与A,B,C,DY的估计效应和系数(已编码单位)项效应系数系数标准误TP常量16.10840.04058397.000.000A0.44130.22060.040585.440.012B1.72020.8 6010.0405821.200.000C0.86630.43310.0405810.670.002D0.14720.07360.040581.810.167A某B-1.9323-0.96610.04058-23.810.000A某C-0.0982-0.04910.04058-1.210.313A某D-0.5173-0.25860.04058-6.370.008Y=16.1084+O.2206A+0,.8601B+0.4331C-0.9661ABCtPt0.84960.0702812.090.001S=0.114764PRESS=某R-Sq=99.78%R-Sq(预测)=某%R-Sq(调整)=99.19%Y的方差分析(已编码单位)合计1117.8381Y的异常观测值拟合值标准化观测值标准序Y拟合值标准误残差残差1317.564017.56400.11480.0000某某3514.876014.87600.11480.0000某某5113.247013.24700.11480.0000某某6416.024016.02400.11480.0000某某8617.004017.00400.11480.0000某某9717.864017.86400.11480.0000某某10215.866015.86600.1148-0.0000某某11816.422016.42200.11480.0000某某某表示受某值影响很大的观测值。
minitab正交分析、响应分析

R-Sq = 92.49% R-Sq(预测)= 53.68% R-Sq(调整)= 83.11%
强度的方差分析(已编码单位)
来源自由度Seq SS Adj SS Adj MS F P
主效应4 3298.85 3298.85 824.71 22.90 0.000
2因子交互作用6 252.17 252.17 42.03 1.17 0.408
选择[统计]=>[DOE]=>[因子]=>[分析因子设计],打开分析因子设计对话框。
点击“项”选项后,在“模型中包含项的阶数”中选择2(表示模型中只包含2阶交互作用和主效应项,三阶以上交互作用不考虑),对默认的“在模型中包括中心点”保持不选。单击确定。
在“图形”选项中,“效应图”中选择“正态”和“Pareto”,“图中的标准差”中选择“正规”,“残差图”中选择“四合一”,在“残差与变量”图中将“加热温度”、“加热时间”、“转换时间”和“保温时间”选入,单击确定。
minitab部分因子设计,响应面设计,参数设计解读
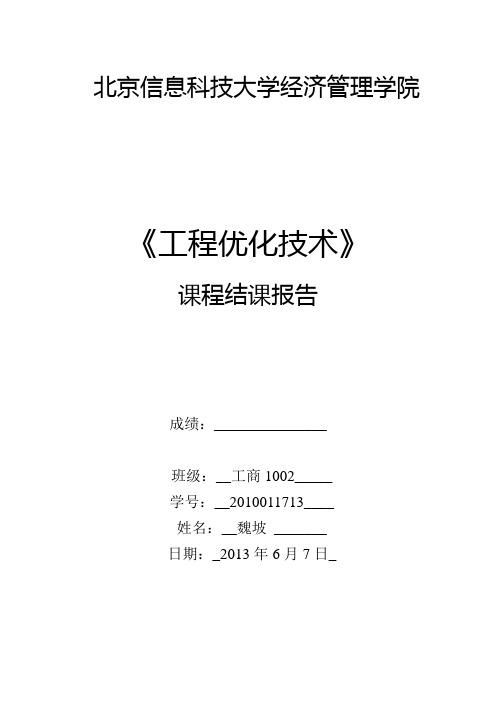
北京信息科技大学经济管理学院《工程优化技术》课程结课报告成绩:_______________班级:__工商1002_____学号:__2010011713____姓名:__魏坡_______日期:_2013年6月7日_部分因子试验设计1.实验设计背景部分因子试验设计与全因子试验设计的不同之处在于大大减少了试验的次数,具体表现在试验设计创建阶段的不一致,下面主要就部分因子试验设计的创建进行讲述。
2.因子选择用自动刨床刨制工作台平面的工艺条件试验。
在用刨床刨制工作台平面试验中,考察影响其工作台平面光洁度的因子,并求出使光洁度达到最高的工艺条件。
3.实验方案共考察6个因子:A 因子:进刀速度,低水平1.2,高水平1.4(单位:mm/刀)B 因子:切屑角度,低水平10,高水平12(单位:度)C 因子:吃刀深度,低水平0.6,高水平0.8(单位:mm )D 因子:刀后背角,低水平70,高水平76(单位:度)E 因子:刀前槽深度,低水平1.4,高水平1.6(单位:mm )F 因子:润滑油进给量,低水平6,高水平8(单位:毫升/分钟) 要求:连中心点在内,不超过20次试验,考察各因子主效应和2阶交互效应AB 、AC 、CF 、DE 是否显著。
由于试验次数的限制,我们在因子点上只能做试验16次,另4次取中心点,这就是6224-+的试验,通过查部分因子试验分辨度表可知,可达分辨度为Ⅳ的设计。
具体操作为:选择 [统计]=>[DOE ]=>[因子]=>[创建因子设计],单击打开创建因子设计对话框。
在“设计类型”中选择默认2水平因子(默认生成元),在“因子数”中选定6。
单击“显示可用设计”就可以看到下图的界面,可以确认:用16次试验能够达到分辨度为Ⅳ的设计。
单击“设计”选项,选定1/4部分实施,在每个区组的中心点数中设定为4,其他的不进行设定,单击确定。
单击“因子”选项,设定各个因子的名称,并设定高、低水平值。
- 1、下载文档前请自行甄别文档内容的完整性,平台不提供额外的编辑、内容补充、找答案等附加服务。
- 2、"仅部分预览"的文档,不可在线预览部分如存在完整性等问题,可反馈申请退款(可完整预览的文档不适用该条件!)。
- 3、如文档侵犯您的权益,请联系客服反馈,我们会尽快为您处理(人工客服工作时间:9:00-18:30)。
AB + CE + ACDF + BDEF
AC + BE + ABDF + CDEF
AD + EF + ABCF + BCDE
AE + BC + DF + ABCDEF
AF + DE + ABCD + BCEF
BD + CF + ABEF + ACDE
BF + CD + ABDE + ACEF
(3)各效应的显著性。从表中可以看到,压力、温度以及它们的平方项对应的概率值都小于显著性水平,说明这些效应都是显著的;而压力和温度的交互效应项对应的概率值为0.855,显然大于显著性水平,认为该效应项是不显著的。
第二步:进行残差诊断
利用自动输出的残差图来进行残差诊断。
从上述残差图中可以看出,残差的状况是正常的。
残差误差6 0.1667 0.1667 0.02778
失拟4 0.0675 0.0675 0.01687 0.34 0.836
纯误差2 0.0992 0.0992 0.04960
合计10 25.3964
纯度的估计回归系数,使用未编码单位的数据
项系数
常量-59.9731
压力5.36834
温度0.134611
对于纯度的方差分析
来源自由度Seq SS Adj SS Adj MS F P
回归4 25.2298 25.2298 6.30744 227.07 0.000
线性2 15.7127 15.7127 7.85635 282.83 0.000
平方2 9.5171 9.5171 4.75853 171.31 0.000
看方差分析表中的失拟现象,本例中,失拟项对应的P值为0.747,明显大于显著性水平0.05,接受原假设,认为本模型中不存在失拟现象。
(2)看拟合的总效果。本例中,R-Sq与R-Sq(调整)比较接近,认为模型的拟合效果比较好;R-Sq(预测)比较接近于R-Sq值且这个值比较大,说明将来用这个模型进行预测的效果比较可信。
2.因子选择
用自动刨床刨制工作台平面的工艺条件试验。在用刨床刨制工作台平面试验中,考察影响其工作台平面光洁度的因子,并求出使光洁度达到最高的工艺条件。
3.实验方1.2,高水平1.4(单位:mm/刀)
B因子:切屑角度,低水平10,高水平12(单位:度)
C因子:吃刀深度,低水平0.6,高水平0.8(单位:mm)
2.实验因子的选择
对于这批数据按全因子试验进行分析,具体操作为:选择[统计]=>[DOE]=>[因子]=>[分析因子设计],打开分析因子设计对话框。首先将全部备选项列入模型,删除在模型中包括中心点,在“图形”中的残差与变量下将压力和温度选入进去。得到的结果如下:
纯度的效应和系数的估计(已编码单位)
项效应系数系数标准误T P
(2)看删减后的模型是否比原来的有所改进。
全模型
变化
删减模型
R-Sq
99.35%
减小
99.34%
R-Sq(调整)
98.70%
增大
98.91%
S
0.181900
减小
0.166665
R-Sq(预测)
97.27%
增大
97.85%
PRESS
0.693677
减小
0.546550
由于模型项缺少了一项,R-Sq通常会有所降低,但关键要看调整的R-Sq(调整)是否有所提高,s值是否有所降低,预测残差平方和PRESS是否有所降低,R-Sq(预测)是否有所提高。从表中来看,均符合上述要求,表明删除了不显著的交互作用后,回归的效果更好了。
响应面设计的分析
1.实验设计背景
提高烧碱纯度问题。在烧碱生产过程中,经过因子的筛选,最后得知反应炉内压力及温度是两个关键因子。在改进阶段进行全因子试验,因子A压力的低水平和高水平分别取为50帕和60帕,因子B反应温度的低水平和高水平分别取为260及320摄氏度,在中心点处也作了3次试验,试验结果在数据文件:DOE_烧碱纯度。
ABD + ACF + BEF + CDE
ABF + ACD + BDE + CEF
从此表得知,计算机自己选择的生成元是:E=ABC,F=BCD。后面的别名结构中列出了交互作用项的混杂情况,即每列中互为别名的因子有哪些;从上表可以看出,主效应与三阶及四阶交互作用混杂,二阶交互作用与四阶交互作用混杂,三阶交互作用与四阶交互作用混杂;关键是要检查一下题目所要求的2阶交互作用情况,将3阶以上的交互作用忽略不计,混杂的情况有:AB=CE,AC=BE,AD=EF, AF=DE,AE=BC=DF,BD=CF,BF=CD。本例中所要求的4个2阶交互作用是AB,AC,CF,DE,显然可以看到,这四个2阶交互作用均没有混杂。因此可以看到此试验计划是可行的。
残差误差5 0.1654 0.1654 0.03309
失拟3 0.0662 0.0662 0.02208 0.45 0.747
纯误差2 0.0992 0.0992 0.04960
合计10 25.3964
结果解释:
(1)看方差分析表中的总效果。在本例中,回归项的P值为0.000,表明应该拒绝原假设,认为本模型总的来说是有效的。
第三步:判断模型是否需要改进。
根据第一步的分析,我们得知压力和温度的交互作用项是不显著的,应该予以剔除,因此需要重新拟合新的模型,使得新的模型中不包含交互作用项。
得到的结果为:
纯度的估计回归系数
项系数系数标准误T P
常量97.7804 0.09622 1016.177 0.000
压力-1.8911 0.08350 -22.647 0.000
残差误差3 3.6170 3.61701 1.20567
弯曲1 3.5178 3.51781 3.51781 70.92 0.014
纯误差2 0.0992 0.09920 0.04960
合计6 11.3057
从上述表中可以看到,主效应和2因子交互作用对应的概率P值均大于0.1,说明模型的总效应不显著,而且弯曲对应的概率P值为0.014,拒绝原假设,认为存在明显的弯曲趋势;R-Sq和R-Sq(预测)的值都比较小,说明了模型的总效果不显著。
压力*压力-0.0512244
温度*温度-2.56700E-04
结果解释:
(1)先看方差分析表中的总效果。回归项对应的P值为0.000,拒绝原假设,说明回归模型总的来说是有效的;看方差分析表中的失拟现象,可以看到失拟对应的P值为0.836,大于0.05,接受原假设,即可以判定,本模型删去了一项,但没有造成失拟现象。
温度*温度-0.4615 0.15314 -3.014 0.030
压力*温度0.0351 0.18253 0.192 0.855
S = 0.181900 PRESS = 0.693667
R-Sq = 99.35% R-Sq(预测)= 97.27% R-Sq(调整)= 98.70%
对于纯度的方差分析
来源自由度Seq SS Adj SS Adj MS F P
此外,我们还可以得到最后确定的回归方程:
从标准化残差以及删后残差的结果分析表中,可以看到这些值都小于2,因此认为新的模型的残差没有发现任何不正常的情况。
第四步:对选定的模型进行分析解释。
通过前面得到的回归方程,运用数学方法我们可以得到使得纯度最大的A和B分别取什么值,但是不能保证该最大值就一定落在试验范围之内。在求解前,先看一下等值线图和曲面图,具体实现:[统计]>[DOE]>[响应曲面]>[等值线图/曲面图]。从图中可以看到,在原试验范围内确实有个最大值。
回归5 25.2310 25.2310 5.04620 152.51 0.000
线性2 15.7127 15.7127 7.85635 237.44 0.000
平方2 9.5171 9.5171 4.75853 143.82 0.000
交互作用1 0.0012 0.0012 0.00123 0.04 0.855
温度-0.6053 0.08331 -7.265 0.000
压力*压力-2.5822 0.14054 -18.373 0.000
温度*温度-0.4615 0.14031 -3.289 0.017
S = 0.166665 PRESS = 0.546550
R-Sq = 99.34% R-Sq(预测)= 97.85% R-Sq(调整)= 98.91%
北京信息科技大学经济管理学院
《工程优化技术》
课程结课报告
成绩:_______________
班级:__工商1002_____
学号:__2010011713____
姓名:__魏坡_______
日期:_2013年6月7日_
部分因子试验设计
1.实验设计背景
部分因子试验设计与全因子试验设计的不同之处在于大大减少了试验的次数,具体表现在试验设计创建阶段的不一致,下面主要就部分因子试验设计的创建进行讲述。
常量96.961 0.4150 233.63 0.000
压力-2.665 -1.332 0.5490 -2.43 0.094
温度-0.765 -0.382 0.5490 -0.70 0.536
压力*温度0.035 0.018 0.5490 0.03 0.977
S = 1.09803 PRESS = 134.203
R-Sq = 68.01% R-Sq(预测)= 0.00% R-Sq(调整)= 36.01%
对于纯度方差分析(已编码单位)
来源自由度Seq SS Adj SS Adj MS F P