水射流切割加工
第10章 超高压水射流加工

7
3. 控制系统 可根据具体情况选择机械、气压和液压控制。工作台应能纵、横向灵活 移动,适应大面积和各种型面加工的需要。当采用程序控制和数字控 制系统是理想的。目前,已出现程序控制液体加工机,其工作台尺寸 为1.2m×1.5m,移动速度为380mm/s。 4. 过滤设备 在进行超高压水射流加工时,对工业用水进行必要的处理和过滤有着重 要意义:延长增压系统密封装置、宝石喷嘴等的寿命,提高切割质量, 提高运行的可靠性。因此要求过滤器很好的滤除液体中的尘埃、微粒、 矿物质沉淀物,过滤后的微粒应小于0.45。液体经过过滤以后,可以 减少对喷嘴的腐蚀。切削时摩擦阻尼很小,夹具简单。当配有多个喷 嘴时,还可以采用多路切削,提高切削速度。
5
(5) 加工材料范围广,既可用来加工非金属材料, 也可以加工金属材料,而且更适宜于加工切割薄 的和软的材料。 (6) 加工成本低。材料利用率高,使用的水量也不 多(可循环利用),降低成本。节省设计制造费 用 (7) 对某些材料,夹裹在射流束中的空气将增加噪 声,噪声随压射距离的增加而增加。在液体中加 入添加剂或调整到合适的正前角,可以降低噪声, 噪声分贝值一般低于标准规定。
10
(4) 喷射距离。指从喷嘴到加工工件的距离,根据不同的加 工条件,喷射距离有一个最佳值。一般范围为2.5~50mm, 常用范围为3mm。 (5) 喷射角度。喷射角度可用正前角来表示。水喷射加工时 喷嘴喷射方向与工件加工面的垂线之间的夹角称为正前角。 超高压水喷射加工时一般正前角为0°~30°。喷射距离 与切割深度有密切关系,在具体加工条件下,喷射距离有 一个最佳值,可经过试验来寻求。 (6) 喷嘴直径。用于加工的喷嘴直径一般小于1mm,常用的 直径为0.05~0.38mm。增大喷嘴直径可以提高加工速度。
水切割技术简介

水切割技术简介一、何谓水切割技术水切割技术又称水刀、水射流技术,是真正的冷切割。
它是将普通的水经过压力系统增压后所产生的高能量水流,再通过一个极细的沙管喷嘴,以每秒近千米的速度喷射出水流进行切割,这种切割技术称为水切割技术。
水切割技术是世上公认的最通用的也是发展得最快的技术。
相对其它切割技术而言,水切割不会产生有毒有害的气体或液体,并且也不产生有毒有害的物质或蒸汽。
水切割加工后,在被加工件表面不会产生热反应区或机械应力残留。
水切割技术是一种万能的、高产能的冷切割技术。
二、水切割技术分类水切割技术是所有涉及到水切割所使用的相关技术范畴,其技术分类及设备类型的划分可按照以下方式进行详细划分:水切割技术按照压力大小可分为高压水切割技术和低压水切割技术;按照设备体积分类可分为大型水切割技术和小型水切割技术;按照切割方式可分为后混式水切割技术和前混式水切割技术。
无论是哪种技术均属于高能冷切割技术范畴,冷切割技术是利用水作为切割载体利用磨料对物体进行高速切割的技术。
三、高压水切割技术高压水切割技术又称高压水射流技术,该技术利用驱动装置对普通进行二级或三级增压,从而形成高压水流,高压水流通过高压管路流至割枪头位置,运用虹吸原理将磨料存储装置中的磨料吸入枪头位置并同高压水流进行混合,形成高压水砂混合流并从喷嘴射出,以此来切割物体。
这种技术称之为高压水切割技术。
利用该技术可对几乎所有物体进行切割,如钢板、大理石、石材、塑料、木头、纸类、玻璃、陶瓷、铝板、铜板以及其他耐热性较差和其他易燃物体。
利用此种技术最大程度的克服了在切割过程中材料变形及机械应力对加工部件在成的影响。
该技术具有应用范围广、切割质量高、环保、减少毛刺等特点,另外高压水切割技术主要用于生产加工方面,利用数控技术将割枪头放置于数控机床,通过对所设计图案进行简单的编程,就可对编程图形进行准确切割,且无需更换刀具。
使用简单方便,是对部件进行加工的又一新选择,且在实际应用中拥有良好的表现。
高压水射流切割技术

高压水射流切割技术一、高压水射流加工简介近二十年来,随着科学技术的不断发展,人们不断的发掘着自然界中有益的现象并加以改造为人类服务。
为了提高效率,【1】人们将水加以高压,并使之从直径较小的喷嘴中喷出,形成一束高速、连续或间断的水流束,这便是高压水射流。
水射流加工(water Jet Cutting)又称水喷射加工,是利用高压高速水流对工件的冲击作用来去除材料的,俗称“水刀加工”,即利用高压水射流对各种材料进行切割、穿孔和工件表层材料去除等加工【1】。
与其他高能束流加工技术相比,水射流切割技术具有独特的优越性。
高压水射流切割法是一种新型的切割方法,可以切割用其他切割方法无法加工的材料,应用范围涵盖各种金属及非金属材料。
在切割过程中不会使被切割材料产生热影响区,切口边缘的材质不发生变化,这种切割方法的精度较高,适用于加工尺寸精度要求高的零部件。
高压水射流切割因其独特的优点而在切割领域占有重要地位,在矿业、土木工程、建筑业以及航空航天业中的应用日益广泛,应用前景良好。
二、高压水射流切割原理①高压水射流切割示意图1-水箱 2-过滤器 3-水泵 4-蓄能器 5-液压系统6-增压器 7-控制器 8-阀门 9-喷嘴 10-工件 11-水槽【2】高压水射流切割是利用水或水中加添加剂的液体,经水泵至增压器,再经贮液蓄能器使高压液体流动平稳,最后由人造蓝宝石喷嘴形成300-900m/s(约为音速的1-3倍)的高速液体束流,喷射到工件表面,从而达到去除材料的加工目的。
高速液体束流的能量密度可达102W/mm2,流量为7.5L/min【2】。
储存在水箱中的水经过滤器处理后,由水泵抽出送至蓄能器中。
液压系统驱动增压器,使水压增高。
高压水经控制器、阀门和喷嘴喷射到工件的加工部位进行切割。
切割过程中产生的切屑和水混合在一起,排入水槽。
【3】利用增压装置将水加压到几十至数百兆帕后从喷嘴中喷出形成高压水射流。
高压水射流本身具有较高的刚性,在与工件发生碰撞时,会产生极高的冲击动压和涡流。
水喷射加工

水喷射加工机械设计制造及其自动化09—2班李传福0901041115水喷射加工(Water Jet Machining)又称水射流加工、水力加工或水刀加工。
它是利用超高压水射流及混合于其中的磨料对各种材料进行切割、穿孔和表层材料去除等加工。
水喷射加工的基本原理是利用液体增压原理,通过特定的装置(增压器或高压泵),将动力源(电动机)的机械能转换成压力能,具有巨大压力能的水再通过小孔喷嘴将压力能转变成动能,从而形成高速射流,喷射到工件表面,从而达到去除材料的目的。
水喷射加工的特点有:l)几适用范围广。
几乎适用于加工所有的材料,除钢铁、铝、铜等金属材料外,还能加工特别硬脆、柔软的非金属材料加工,如:塑料、皮革、纸张、布匹、化纤、木材、胶合板、石棉、水泥制品、玻璃、花岗岩、大理石、陶瓷和复合材料等。
2)加工质量高。
切缝窄,可提高材料利用率;切口平整、无毛边和飞刺。
也可用其去除阀体、燃油装置和医疗器械中的孔缘、沟槽、螺纹、交叉孔和盲孔上的毛刺。
3)切削时无火花,对工件不会产生任何热效应,也不会引起其表层组织的变化。
这种冷加工很适于对易爆易燃物件的加工。
4)加工清洁不产生烟尘或有毒气体,减少空气污染。
提高操作人员的安全性。
5)减少了刀具准备、刃磨和设置刀偏量等工作,井能显著缩短安装调整时间。
水喷射加工在机械领域的应用主要是切割加工、去毛刺、打孔、开槽、清焊根和清除焊接缺陷。
水喷射切割所加工的材料品种很多,主要是一般切割方法不易加工或不能加工的非金属或金属材料,特别是一些新型合成材料,如陶瓷、硬质合金、模具钢、钛合金、钨钼钴合金、复合材料(如以金属为基体的纤维增强金属、纤维增强橡胶等)、不锈钢、高硅铸铁及可锻铸铁等的加工。
用来去毛刺时,各种小型精密零件上交叉孔、内螺纹、窄槽、盲孔等毛刺的去除,用其他一般方法就十分困难甚至于无法完成,而利用水喷射加工技术就十分方便,具有独特的效果。
在打孔方面,水射流可用于在各种材料上打孔以代替钻头钻孔,不仅质量好,而且加工速度快。
高压水射流技术
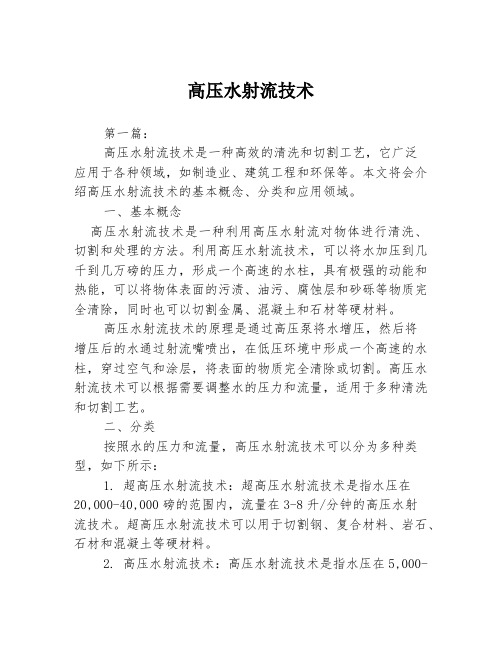
高压水射流技术第一篇:高压水射流技术是一种高效的清洗和切割工艺,它广泛应用于各种领域,如制造业、建筑工程和环保等。
本文将会介绍高压水射流技术的基本概念、分类和应用领域。
一、基本概念高压水射流技术是一种利用高压水射流对物体进行清洗、切割和处理的方法。
利用高压水射流技术,可以将水加压到几千到几万磅的压力,形成一个高速的水柱,具有极强的动能和热能,可以将物体表面的污渍、油污、腐蚀层和砂砾等物质完全清除,同时也可以切割金属、混凝土和石材等硬材料。
高压水射流技术的原理是通过高压泵将水增压,然后将增压后的水通过射流嘴喷出,在低压环境中形成一个高速的水柱,穿过空气和涂层,将表面的物质完全清除或切割。
高压水射流技术可以根据需要调整水的压力和流量,适用于多种清洗和切割工艺。
二、分类按照水的压力和流量,高压水射流技术可以分为多种类型,如下所示:1. 超高压水射流技术:超高压水射流技术是指水压在20,000-40,000磅的范围内,流量在3-8升/分钟的高压水射流技术。
超高压水射流技术可以用于切割钢、复合材料、岩石、石材和混凝土等硬材料。
2. 高压水射流技术:高压水射流技术是指水压在5,000-20,000磅的范围内,流量在3-30升/分钟的高压水射流技术。
高压水射流技术可以用于清洗外墙、管道、锅炉和船舶等设备。
3. 中压水射流技术:中压水射流技术是指水压在1,000-5,000磅的范围内,流量在30-100升/分钟的高压水射流技术。
中压水射流技术可以用于清洗地面、墙壁和设备表面等。
4. 低压水射流技术:低压水射流技术是指水压在1,000磅以下范围内,流量在100升/分钟以上的高压水射流技术。
低压水射流技术可以用于清洗各种设备、建筑物、地面和路面等。
三、应用领域高压水射流技术有广泛的应用领域,如下所示:1. 制造业:高压水射流技术可以用于切割和加工各种硬材料,如金属、石材、混凝土、水泥等,以达到精准的加工目的。
2. 建筑工程:高压水射流技术可以用于清洗建筑物外墙、墙壁、玻璃幕墙、天窗、钢结构及各种管路设备等。
超高压水射流技术的应用
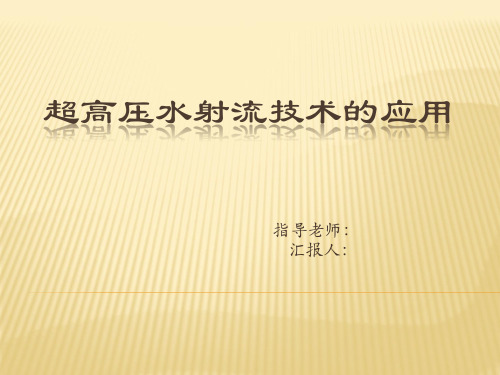
指导老师: 汇报人:
水射流加工(Water JetCuting)
:俗称“水刀加
工”。即是利用超高压(达数百MPa)水射流对各种材料进行切 割、穿孔和工件表层材料去除等加工。
超高压水射流应用广泛,在食品加工,机械加工,石油开 采,工业除锈等方面都有涉及。
一、清洁 二、灭菌 三、切割
超高压水射流灭菌方法的延伸:
1)牛奶保鲜:牛奶经 50MPa 处理,其微生物指标优于“巴
氏杀菌、灭菌乳卫生标准” 中巴氏奶的规定,250~300MPa 超高压奶的保质期可在冷链下保存 5 个月(巴氏奶为 3~5 天)。 2)白酒超高压水射流催陈研究:白酒经 50~300MPa 处理后, 香气优雅,酒体醇和,绵柔爽净,尤其空杯留香纯爽、持久,
谢谢!
2、超高压水射流切割技术的主要应用领域:
5)食品工业领域:用于切割松脆食品、菜、肉等,可减少
细胞组织的损坏,增加存放期。切割食品时,“数控水刀”
用数控装置可以控制其切割速度及路线,可以最大限度地保 持被切割物的营养成分,不会造成细菌传播且形状规整。 6)纺织工业领域:用于切割多层布料,提高切割效率,减 少边端损伤。水切割还广泛应用于服装裁剪、制鞋下料等,
一、清洁
4、箱/罐容器清洁。这是工业清洁中比较难的清洗方式,
比如一个反应釜,一个罐体,操作人员不可能带着机器下
到罐里清洁,这样有很大的危险性,必须采用良好的设备
或良好的工具才能够在罐内做到清洗,所有厂家都会选择 三维罐内清洗方式。比如采用超高压水的压力,在罐内进 行良好清洗,可以做到无死点。
三维罐内清洗系统:包括高压清洗机抽液及抽水系统、长
一、清洁
2、表面处理及清洗。沥青、混凝土或金属涂层在浇
水射流切削加工原理及其应用
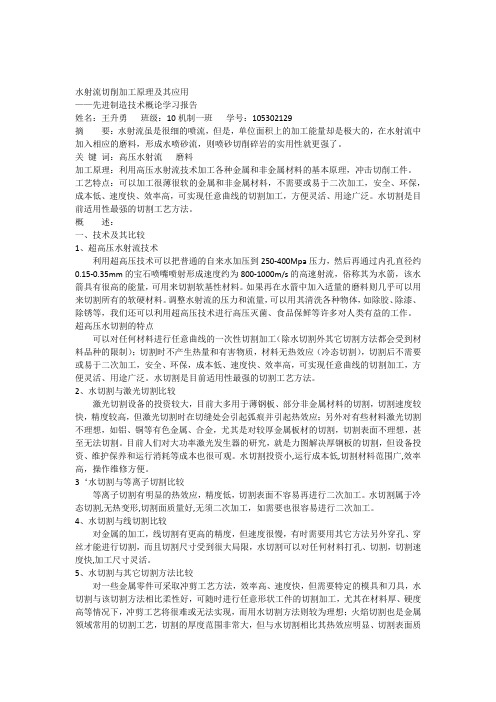
水射流切削加工原理及其应用——先进制造技术概论学习报告姓名:王升勇班级:10机制一班学号:105302129摘要:水射流虽是很细的喷流,但是,单位面积上的加工能量却是极大的,在水射流中加入相应的磨料,形成水喷砂流,则喷砂切削碎岩的实用性就更强了。
关键词:高压水射流磨料加工原理:利用高压水射流技术加工各种金属和非金属材料的基本原理,冲击切削工件。
工艺特点:可以加工很薄很软的金属和非金属材料,不需要或易于二次加工,安全、环保,成本低、速度快、效率高,可实现任意曲线的切割加工,方便灵活、用途广泛。
水切割是目前适用性最强的切割工艺方法。
概述:一、技术及其比较1、超高压水射流技术利用超高压技术可以把普通的自来水加压到250-400Mpa压力,然后再通过内孔直径约0.15-0.35mm的宝石喷嘴喷射形成速度约为800-1000m/s的高速射流,俗称其为水箭,该水箭具有很高的能量,可用来切割软基性材料。
如果再在水箭中加入适量的磨料则几乎可以用来切割所有的软硬材料。
调整水射流的压力和流量,可以用其清洗各种物体,如除胶、除漆、除锈等,我们还可以利用超高压技术进行高压灭菌、食品保鲜等许多对人类有益的工作。
超高压水切割的特点可以对任何材料进行任意曲线的一次性切割加工(除水切割外其它切割方法都会受到材料品种的限制);切割时不产生热量和有害物质,材料无热效应(冷态切割),切割后不需要或易于二次加工,安全、环保,成本低、速度快、效率高,可实现任意曲线的切割加工,方便灵活、用途广泛。
水切割是目前适用性最强的切割工艺方法。
2、水切割与激光切割比较激光切割设备的投资较大,目前大多用于薄钢板、部分非金属材料的切割,切割速度较快,精度较高,但激光切割时在切缝处会引起弧痕并引起热效应;另外对有些材料激光切割不理想,如铝、铜等有色金属、合金,尤其是对较厚金属板材的切割,切割表面不理想,甚至无法切割。
目前人们对大功率激光发生器的研究,就是力图解决厚钢板的切割,但设备投资、维护保养和运行消耗等成本也很可观。
水射流加工

水射流加工姓名: 王劲雄 专业: 08级机械设计制造及其自动化1班摘要水射流加工技术是近三十年来迅速发展起来的一门新技术。
水射流切割工作原理是首先通过转能装置(泵或增压器),将发动机(电机或内燃机)的机械能转变成低速水的高压能;接着通过喷嘴小孔喷出高速射流,将压力能转换成高速水射流的动能;最后当高速水射流冲击加工工件时,动能又重新变成作用于材料表面的压力能,当该压力能超过材料的断裂强度时材料就被切割。
水射流切割有以下一些优点:切割中无粉尘与烟雾污染;不会产生热变型;不需刃磨刀具,不需调整更换刀具;容易实现自动化;可加工热切削无法加工的材料,且不受材料厚度的限制;切缝小,切割质量好,成本低等。
由于水射流切割技术有如上所述的优点,所以受到工程技术界广泛重视。
在工业中推广应用,它与激光束、电子束和等离子切割,合称现代工业切割的四大高新技术。
水射流除用于切割之外,还可用于除锈、清洗等方面,涉及到医学、国防、机械、城建等许多领域。
本文重点讨论水射流加工的设备组成及应用方向,发展趋势,以及对水射流相关工艺参数的分析讨论等。
关键词 水射流加工 优点点 加工应用 工艺参数第一章 工作原理及其基本机构1.1工作原理水喷射加工的基本原理是利用液体增压原理, 通过特定的装置 (增压器或高压泵) , 将动力源 (电动机)的机械能转换成压力能, 具有巨大压力能的水再通过小孔喷嘴将压力能转变成动能, 从而形成高速射流, 喷射到工件表面, 达到去除材料的加工目的。
如图1.1所示, 贮存在水箱中的水经过滤器 1 处理后, 由水泵抽出送至由液压机构驱动的增压器增压, 水压增高。
然后高压水通过蓄能器, 使脉动水流平滑化。
高压水与磨料在混合腔内混合后, 由具有精细小孔的喷嘴 (一般由蓝宝石制成) 喷射到由工作台固定的工件表面上, 射流速度可达300-900m/s (约为音速的1-3 倍) , 可产生如头发丝细的射流, 从而对工件进行切割、 打孔等。
- 1、下载文档前请自行甄别文档内容的完整性,平台不提供额外的编辑、内容补充、找答案等附加服务。
- 2、"仅部分预览"的文档,不可在线预览部分如存在完整性等问题,可反馈申请退款(可完整预览的文档不适用该条件!)。
- 3、如文档侵犯您的权益,请联系客服反馈,我们会尽快为您处理(人工客服工作时间:9:00-18:30)。
陶瓷轴承高速电主轴特点
采用电动主轴(电机与主轴作成一体);
轴 承 转 速 特 征 值 ( = 轴 径 ( mm ) × 转 速 (r/min))较普通钢轴承提高1.2 ~2倍,可 达2×106。 回转精度可达0.5μ m
静压轴系高速电主轴
瑞士IBGA公司的水介质静压电主轴
静压轴承工作原理
主轴高速转动示例
坐标轴快速移动示例
坐标轴高速加工示例
3.高速加工的特点和应用
高速加工的特点
• 加工效率高,材料去除率是常规的3-5倍 • 刀具切削状况好,切削力小,主轴轴承、刀具 和工件受力均小。切削速度高,吃刀量很小, 剪切变形区窄,变形系数ξ 减小,切削力降低 大概30%-90% • 刀具和工件受热影响小。切削产生的热量大部 分被高速流出的切屑所带走,故工件和刀具热 变形小,有效地提高了加工精度 • 刀具寿命长(高速切削刀具)。刀具受力小, 受热影响小,破损的机率很小,磨损慢
高速加工中心的主要技术参数
主轴最高转速:10000-150000r/min
主轴功率从0.5kW到80kW、转矩从0.1N.m到 300N.m 坐标轴加工最高速:30-60m/min,快速移动: 70-80m/min,最高120m/min
换刀时间:3-5s,最快0.7-1.5s
德国 ROEDERS,42000rpm,适 合如手机模具加工
电主轴概述
电主轴省去了带轮或齿轮传动,实现了机床 的“零传动”,提高了传动效率 电主轴的刚性好、回转精度高、快速响应性 好,能够实现极高的转速和加、减速度及定 角度的快速准停(C轴控制),调速范围宽 电主轴的基本参数: 套筒直径、最高转速、 输出功率、转矩和刀具接口等
高速主轴系统
世界上著名的电主轴生产厂家:
瑞士Fraisa
HX铣刀加工高硬度材料
高速加工的加工时间
10 1 0.1 0.01 粗加工 传统加工方法 精加工
手工精修
高速切削 少量手工精修 加工时间
0.001
100 %
高速加工缩短模具制作周期(日产汽车公司)
★ 对于复杂型面模具,模具精加工费用往往占到模具 总费用的50%以上。采用高速加工可使模具精加工费 用大大减少,从而可降低模具生产成本
• 平面加工:铝件—高速加工中心;铸铁件、钢 件—数控铣床
• 中、小孔系,螺孔—高速加工中心;不规则及小 型平面铣削—高速加工中心。 重要的特殊表面加工(镗缸孔、曲轴孔、凸轮轴 孔、长油孔)—柔性专机或组合机床
高速加工在汽车工业中的应用
1 2 3 4
钻孔 表面倒棱 内侧倒棱 铰孔
高速钻孔
表面和内侧倒棱
•瑞士:Fisher公司,IBAG公司,Step-up公司
•德国:GMN公司,FAG公司
•美国:Precise公司
•意大利:Gamfior公司,Foemat公司 •日本:NSK公司,Koyo公司 •瑞典:SKF公司
电主轴 单元
适合小孔钻削
电主轴的高速轴承技术
精密滚动轴承
–精密角接触陶瓷球轴承
–精密圆柱滚子轴承
高速加工的切削速度范围
高速加工切削速度范围随加工方法不同有所不同 ◎车削:700-7000 m/min ◎铣削:300-6000 m/min
◎钻削:200-1100 m/min
高速加工切削速度范围因不同的工件材料而异
高速加工的切削速度范围
2000-9000 1000-7000 1000-4000 800-300器
电磁铁(定子) 传感器 转子
磁悬浮轴承工作原理
磁浮轴承高速电主轴
前径向轴承 前辅助轴承 电主轴 后径向轴承 双面轴向 推力轴承 后辅助轴承
前径向传感器 磁浮轴承高速主轴
后径向传感器
轴向传感器
磁悬浮轴承电主轴
磁悬浮轴承 松刀用液压装置
高频电动机
HSK-E刀柄 水套冷却 磁悬浮轴承 瑞士IBGA公司的磁悬浮电主轴
静压轴承
–液体静压 –空气静压
磁浮轴承
精密角接触陶瓷球轴承
角接触陶瓷球轴承
滚动轴承电主轴
陶瓷角接触球轴承高速电主轴结构
密封圈 电主轴
陶瓷球轴承
陶瓷球轴承 冷却水出口 旋转变压器
冷却水入口 陶瓷轴承高速主轴
陶瓷轴承高速电主轴结构特征
采用C或B级精度角接触球轴承,轴承布置与传 统磨床主轴结构相类似 采 用 “ 小 珠 密 球 ” 结 构 , 滚 珠 材 料 Si3N4, GCr15钢圈 与钢球相比,陶瓷轴承的优点是: 陶瓷球密度减小60%,可大大降低离心力; 陶瓷弹性模量比钢高50%,轴承刚度更高; 热膨胀系数只有轴承刚的25%;摩擦系数低, 可减小轴承发热、磨损和功率损失; 陶瓷耐磨性好,轴承寿命长。
高速加工技术
本章内容
1. 2. 3. 4. 5. 引言 高速加工的定义 高速加工的特点和应用 高速加工和传统加工的区别 高速加工的关键技术
1. 引言
切削加工的发展方向是高速切削加工,高速加 工技术(High Speed Machining, HSM)被认为 是21世纪最有发展前途的先进制造技术之一 最早在飞机制造业受到重视
高速加工定义
以主轴转速界定:主轴转速≥8000r/min
以切削速度和进给速度界定:切削速度和进给 速度为普通切削的5-10倍 转速特征值(Dn=轴径(mm)×转速(r/min))达到 0.5-200×106
采用超硬材料的刀具,通过极大地提高切削速 度和进给速度,来提高材料切除率、加工精度 和加工表面质量的现代加工技术
空气静压轴承转速特征值可达3×106
刚性:液体静压轴承承载刚度好,空气静压轴承承载
能力较小
磁浮轴承高速电主轴
电磁铁绕组通过电流I0 ,对转子产生吸力F,与转子 重量平衡,转子处于悬浮平衡位置。转子受扰动后,偏 离平衡位置。传感器检测出转子位移,将位移信号送至 控制器。控制器将位移信号转换成控制信号,经功放变 换为控制电流,改变吸力方向,使转子重回平衡位置 位移传感器常为非接 触式(5-7个),对其灵 敏度和可靠性要求较高 控制器设计复杂,磁 悬浮轴承成本较高(一 套售价约1万美元)
高速加工在线检测与控制技术
高速加工的加工工艺
其他:如高速加工毛坯制造技术,干切技术, 高速加工的排屑技术、安全防护技术等
高速主轴单元的要求
回转精度高,刚性好
动平衡性很高
能传递足够的力矩和功率
能承受高的离心力
有良好的热稳定性,带有准确的测温装置和高效的 冷却装置 通常采用主轴电机一体化的电主轴部件,实现无中间 环节的直接传动
磁浮轴承电主轴特点
主轴由两个径向和两个轴向磁浮轴承支承,磁 浮轴承定子与转子间空隙约0.1mm。 刚度高,约为滚珠轴承主轴刚度10倍。
转速特征值可达4×106。
回转精度主要取决于传感器的精度和灵敏度, 以及控制电路性能,目前可达0.2μ m。
机械结构及电路系统均较复杂;又由于发热多, 对冷却系统性能要求较高。
具有很高而且稳定的刚性,运转精度比较高
需要一套压力供油/气装置,所以设备成本高,体积大。 适合于调速范围和载荷变化大的精密设备
静压轴系高速主轴结构特征
回转精度高
液体静压轴承回转误差在0.2μ m以下
空气静压轴承回转误差在0.05μ m以下
功率损失小
转速特征值高
液体静压轴承转速特征值可达1×106
高速加工的特点
• 工件表面质量好。轴向和径向切深小,工件粗 糙度小;切削度高,机床激振频率远高于工艺 系统的固有频率,系统振动很小,表面质量好
• 横向切削力很小,有利于加工细筋和薄壁,壁 厚甚至可<1mm • 高速切削刀具热硬性好,且切削热大部分被切 屑带走,可进行高速干切削,实现绿色加工
• 可完成高硬度材料和硬度高达HRC40-62淬硬钢 的加工, Ra0.4,加工效率是EDM的3-6倍
专用机床
5轴×4工序 = 20轴(3万件/月) 刚性(零件、孔数、孔径、孔 型固定不变)
高速加工中心 1台1轴1工序(3万件/月) 柔性(零件、孔数、孔径、 孔型可变)
汽车轮毂螺栓孔高速加工实例(日产公司)
高速加工在模具制造中应用
电极制造
1毛坯 → 2粗铣 → 3半精铣 → 4热处理→5电火花加工→6精铣 →7手工磨修
传统模具加工的过程
1硬化毛坯 → 2粗铣
→
3半精铣 →
4精铣 → 5手工磨修
高速模具加工的过程
汽车车门外覆盖件模具的高速加工
• 模具尺寸:1400x1200 x600mm
• 模具重量:2500kg
• 毛坯材料:GGG30(相 当于HT300)
• 材料硬度:HB240
高速加工与传统数控加工的时间比较: 传统加工:50H.,钳工修复:90H.,总计;140H. HSM:16H.5M.,手工修复:15H.,总计:37.5H.
4.高速加工与电火花加工的比较
4.高速加工的一次性设备投资比较大,并不是所 有企业都能承受 5.高速加工以其巨大的优势冲击传统的电加工工 艺,特别是对模具工业而言,大规模设备更新 的时代即将到来
5.高速加工的关键技术
高速主轴单元制造技术 高速进给单元制造技术 高速加工刀具技术
高速加工的机理研究
近几年高速加工技术已广泛用于模具工业
可广泛用于汽车工业和国防工业
2.高速加工的定义
高速加工和Salomon曲线
高速加工的定义
高速加工的切削速度范围
高速加工中心的技术参数
高速加工和Salomon曲线
1931年德国切削物理学家C.J.Salomom在“高速切 削原理”一文中给出了“Salomom曲线” 被加工材料都有一个临界切削速度,在临界速度之 前,切削温度和刀具磨损随着切削速度增大而增大, 当切削速度达到普通切削速度的5-6倍时,切削刃口 的温度开始随切削速度增大而降低,刀具磨损亦减小