铝合金压铸模具结构剖析
铝合金压铸件砂孔的分类及原因分析

铝合金压铸件砂孔的分类及原因分析本人在压铸行业工作将近10年,现将我积累的有关铝压铸件的砂孔问题的分析及原因分析与各位分享。
一、概述:在压铸件中,由于压铸的特殊性,铝合金是在高温、高速、高压的状态下成型的,所以压铸件内部是不可避免的存在孔洞,我们统称这些孔洞为砂孔。
二、砂孔的分类及表现形式1、气孔:在压铸生产过程中,由于模具型腔的复杂性及生产过程的控制问题而产生的孔洞,会存在于铸件的任何位置,又可以细分为卷入性气孔、析出性气孔和侵入性气孔三种,它们均有各自的表现形式,后面我会逐一解释。
2、渣孔:在压铸生产过程中,由于铝汤的不纯净或在压铸时异物的进入而导致的孔洞,剖开可以明显看到与铝合金机体不一致的异物。
3、缩孔:由于铸件的收缩而造成孔洞,存在于远离内浇口或产品的厚大部位,内孔呈不规则状态,孔壁有金属光泽,没有被污染过。
三、原因分析1、气孔(1)卷入性气孔原因:由于模具型腔及料管(料筒、熔杯)内会有气体存在,在高速射出时,由于气体来不及排出,被紊流的铝合金包裹,存在于铸件内部,形成气孔;表现样式:气孔内部存在压力,如加热铸件到220度左右,铸件表面会有凸起的泡泡,继续加热有时可能会有气泡声;剖开检测,孔规则,内壁光滑,无金属光泽,有被气体污染过的。
xiaoye0527工程师精华0积分149 帖子73 水位149 技术分079586604工程师精华0积分148 帖子73 水位148 技术分0 接上文解决办法a、想办法在压铸前将存在于模具型腔中及料管中的气体排出,目前可以采用真空压铸,冲氧压铸等。
b、模具上作文章,想办法将模具型腔内的气体排出去。
c、压铸工艺上做文章,看不见的东西总是好的,一定当量的气体存在于铸件的某一处,一定是不良品,我们可以通过压铸的工艺将存在于一处的气体打散,分成若干份,让气孔弥散。
(2)析出性气孔原因:由于铝合金在由液体凝固成固体时,溶解在铝合金内部的H会析出形成氢气,这些氢气会留在铸件的内部形成孔洞。
铝合金压铸结构设计规范

压铸齿轮的最小模数见表3-1-17
9、铸件设计中的凸台、凸纹及文字和图案
压铸凸台应有足够的高度,便于留切削余量,而不致使刀 具切削到铸件壁上,凸台的最小高度 h=2~2.5mm。当紧 固件的孔中心距L等于或小于表3-1-19 所列数值时,应将 相近的凸台连成一体,见图 3-1-22。
合金类别 铅锡合金 锌合金
铝合金
镁合金
最小宽度b
0.8
0.8
1.2
1.0
最大深度H
≈10
≈12
≈10
≈12
厚度h
≈10
≈12
≈10
≈12
说明:宽度b在具有铸造斜度时,表内值为小端部位值。
铜合金
1.5 ≈10 ≈8
8、铸件设计的压铸螺纹及齿轮
在一定的工艺条件下,锌、铝及镁等合金的压铸件,可以 直接压出螺纹。铜合金只是在个别情况下才压铸出螺纹。 压铸螺纹一般为国家标准规定的3级精度。压铸螺纹通常 为外螺纹较多。在必要时,也可以压铸内螺纹。外螺纹又 分两种,一种是由可分开的两半螺纹型腔构成,这种方式 的特点是易产生错扣,圆度稍差,但可以达到精度范围内, 使用前要经过简单修整加工。另一种是由螺纹型环构成, 其特点是不产生错扣,圆度好,但生产效率低,操作不安 全。内螺纹方式是由螺纹型芯构成,其特点是螺纹型芯的 螺纹在轴方向上要有斜度,通常为 10′~15′,螺纹长度有 限。压铸螺纹的牙形,应是平头或圆头的。
表3-1-19 紧固件中心距mm
紧固件直径 孔中心距
≤4
15
>4~6
18
>6~10
22
>10~14
30
>14~18
压铸件结构设计

h2≥0.8mm
a≤3°
压铸件加强筋的运用
3,作为散热加强;
4,作为装饰作用。
2,引导料流流向;
1,加强结构强度;
压铸件结构工艺性分析一
不好的案例
好的案例
说明
于型模中加工凹入文字较之加工凸出文字为困难﹒且模具寿命难以保证,使用后续刻加工﹐则与此相反。
1.5
0.014~0.020
6
0.056~0.084
2
0.018~0.026
7
0.066~0.100
2.5
0.022~0.032
8
0.076~0.116
3
0.028~0.040
9
0.088~0.138
3.5
0.034~0.050
10
0.100~0.160
4
0.040~0.060
合金浇注温度高时,填充时间可选长些。 模具温度高时,填充时间可选长些。 铸件厚壁部分离内浇口远时,填充时间可选长些。 熔化潜热和比热高的合金,填充时间可选长些。
好的案例
说明
陈学民
2021
2023
内容大纲
O1
产品的壁厚(模具成型的基础)
O2
产品的拔模(模具脱模的保障)
O3
产品的圆角(模具寿命的关键)
O4
加强筋的设计(结构优化的手段)
压铸件壁厚的设计
3.5
2.5
3.5
2.5
2.5
2.0
>500
3.0
1.8
3.0
1.8
2.2
1.5
>100~500
2.5
铝合金压铸件缺陷的产生原因

铝合金压铸件缺陷的产生原因铝合金压铸件的缺陷及产生的原因压铸生产中遇到的质量问题很多,其原因也是多方面。
生产中必须对产生的质量问题作出正确的判断。
找出真正的原因,才能提出相应切实可行的有效的改进措施,以便不断提高铸件质量。
压铸件生产所出现的质量问题中,有关缺陷方面的特征、产生的原因(包括改进措施)分别叙述于后。
一、欠铸压铸件成形过程中,某些部位填充不完整,称为欠铸。
当欠铸的部位严重时,可以作为铸件的形状不符合图纸要求来看待。
通常对于欠铸是不允许存在的。
造成欠铸的原因有:1)填充条件不良,欠铸部位呈不规则的冷凝金属当压力不足、不够、流动前沿的金属凝固过早,造成转角、深凹、薄壁(甚至薄于平均壁厚)、柱形孔壁等部位产生欠铸。
模具温度过低合金浇入温度过低内浇口位置不好,形成大的流动阻力2)气体阻碍,欠铸部位表面光滑,但形状不规则难以开设排溢系统的部位,气体积聚熔融金属的流动时,湍流剧烈,包卷气体3)模具型腔有残留物涂料的用量或喷涂方法不当,造成局部的涂料沉积成型零件的镶拼缝隙过大,或滑动配合间隙过大,填充时窜入金属,铸件脱出后,并未能被完全带出而呈现片状夹在缝隙上。
当之种片状的金属(金属片,其厚度即为缝隙的大小)又凸于周围型面较多,便在合模的情况下将凸出的高度变成适为铸件的壁厚,使以后的铸件在该处产生穿透(对壁厚来说)的沟槽。
这种穿透的沟槽即成为欠铸的一种特殊形式。
这种欠铸现象多在由镶拼组成的深腔的情况下出现。
浇料不足(包括余料节过薄)。
立式压铸机上,压射时,下冲头下移让开喷嘴孔口不够,造成一系列的填充条件不良。
二、裂纹铸件的基体被破坏或断开,形成细长的缝隙,呈现不规则线形,在外力作用下有发展的趋势,这种缺陷称为裂纹。
在压铸件上,裂纹是不允许存在的。
造成裂纹的原因有:1.铸件结构和形状铸件上的厚壁与薄壁的相接处转变避剧烈铸件上的转折圆角不够铸件上能安置推杆的部位不够,造成推杆分布不均衡铸件设计上考虑不周,收缩时产生应力而撕裂。
浅谈铝合金压铸生产中模具的设计制造

浅谈铝合金压铸生产中模具的设计制造摘要:铝合金压铸模具是进行压铸生产的重要工艺装备,同时,也是铝合金压铸生产中三大必备因素之一。
文章首先分析了铝合金压铸模具设计制造技术,其次,就铝合金压铸模具设计制造中需要注意的几个技术问题进行了深入的探讨,具有一定的参考价值。
关键词:铝合金;压铸模具;制造技术铝合金压铸模具是进行压铸生产的重要工艺装备,同时,也是铝合金压铸生产中三大必备因素之一。
生产过程能否顺利进行,铸件质量是否有保证,在很大程度上取决于模具结构的合理性和技术上的先进性。
铝合金压铸模设计制造的优劣,直接影响压铸件的形状、尺寸、强度、表面质量等方面。
而压铸件的质量和稳定性,反映出整个压铸生产过程和压铸模制造过程的技术水平和经济效益。
1铝合金压铸模具设计在铝合金压铸模具设计过程中必须全面分析压铸件结构,熟悉压铸机操作过程,了解压铸机及工艺参数得以调整的可能性及范围,掌握在不同压铸条件下的金属液填充特性和流动特性,并考虑到经济因素,才能设计出切合实际并满足生产要求的压铸模。
铝合金压铸模设计前,设计人员应对所提供的设计依据,包括压铸产品图和生产纲领进行工艺分析,并进行如下必要准备:①根据产品图,对所选用的压铸合金、压铸件的形状、结构、精度和技术要求进行工艺性分析,确定机械加工部位、加工余量和机械加工时所要采取的工艺措施以及定位基准等。
②根据产品图和生产纲领,确定压射比压,计算锁模力:估算压铸件所需的开模力和推出力,以及压铸机的开模距离;选定压铸机的型号和规格。
③根据产品和压铸机的型号和规格,对模具结构进行初步分析,选择分型面和确定型腔数量;选择内浇口进口位置,确定浇注系统和溢流槽、排气槽朗总体布置方案;对带嵌件的压铸件,要考虑嵌件的装夹和固定方式;确定功模和定模镶块,动模和定模套板外形尺寸,以及导核、导套的位置和尺寸;确定冷却和加热管道的位置和尺寸,控制压铸过程的热平衡等。
④绘制压铸件毛坯图。
包括分型面位置、浇注系统、溢流槽和排气槽,推出元件的位置和尺寸以及机械加工余量、加工基准等数值。
铝挤出模具结构
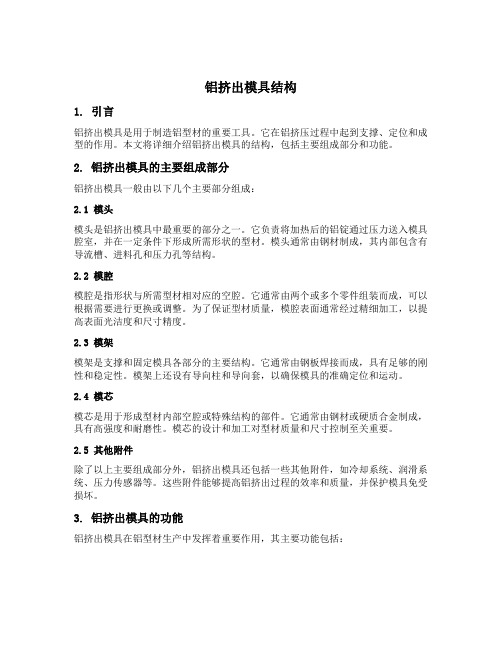
铝挤出模具结构1. 引言铝挤出模具是用于制造铝型材的重要工具。
它在铝挤压过程中起到支撑、定位和成型的作用。
本文将详细介绍铝挤出模具的结构,包括主要组成部分和功能。
2. 铝挤出模具的主要组成部分铝挤出模具一般由以下几个主要部分组成:2.1 模头模头是铝挤出模具中最重要的部分之一。
它负责将加热后的铝锭通过压力送入模具腔室,并在一定条件下形成所需形状的型材。
模头通常由钢材制成,其内部包含有导流槽、进料孔和压力孔等结构。
2.2 模腔模腔是指形状与所需型材相对应的空腔。
它通常由两个或多个零件组装而成,可以根据需要进行更换或调整。
为了保证型材质量,模腔表面通常经过精细加工,以提高表面光洁度和尺寸精度。
2.3 模架模架是支撑和固定模具各部分的主要结构。
它通常由钢板焊接而成,具有足够的刚性和稳定性。
模架上还设有导向柱和导向套,以确保模具的准确定位和运动。
2.4 模芯模芯是用于形成型材内部空腔或特殊结构的部件。
它通常由钢材或硬质合金制成,具有高强度和耐磨性。
模芯的设计和加工对型材质量和尺寸控制至关重要。
2.5 其他附件除了以上主要组成部分外,铝挤出模具还包括一些其他附件,如冷却系统、润滑系统、压力传感器等。
这些附件能够提高铝挤出过程的效率和质量,并保护模具免受损坏。
3. 铝挤出模具的功能铝挤出模具在铝型材生产中发挥着重要作用,其主要功能包括:3.1 塑性变形在铝挤压过程中,通过施加一定的压力将加热后的铝锭从模头进入到模腔中。
在模腔的作用下,铝锭发生塑性变形,逐渐形成型材的外形。
3.2 冷却和固化在铝挤压过程中,模具内部通常会通过冷却系统进行冷却。
冷却可以加速铝锭的固化,使其在模具中保持所需形状。
合适的冷却控制可以提高型材表面质量和尺寸精度。
3.3 定位和支撑铝挤出模具中的导向柱和导向套可以确保模腔和模头之间的准确定位,并避免因挤压过程中产生的力而使模具发生偏移。
同时,模架结构也能够提供足够的支撑力,以承受挤压过程中所施加的压力。
压铸件后处理及缺陷分析.

金液的流动性;
3)改善充型条件; 4)修改浇注系统,改善型腔排气;
5)减少脱模剂用量,型腔清理干净;
6)检查压射冲头行程或浇注量是否足够。
材料工程学院材料成型教研室
铝合金铸件铸造技术
(2)变形(翘曲) 特征:压铸件翘(弯)曲变形,偏离原来形状。 检验:目测或测量检查 原因:压铸件结构设计不合理,收缩不均匀;或顶出不平衡;或冷却不均, 残留应力大造成。
材料工程学院材料成型教研室
铝合金铸件铸造技术
(8)粘模拉伤
特征:压铸件与型壁发生焊合粘连,脱出时压铸件被撕破拉伤。 检验:目测或测量检查。 原因:由于高温、高压或者金属液过度冲击型腔导致两者发生焊合。 措施:1)适当降低浇注温度或压铸模具温度; 2)适当降低充型速度或压射压力; 3)增加脱模剂用量,使隔离作用增强; 4)改进浇注系统,避免金属液冲击型壁; 5)检查型腔表面硬度是否合理; 6)检查铝合金的Fe含量, Fe含量低,金属液与型腔亲和力增加。
材料工程学院材料成型教研室
铝合金铸件铸造技术 3.3形状和尺寸缺陷
(1)欠铸 特征:金属液未充满型腔,压铸件表面有不规则的孔洞、凹陷、棱角不齐、 轮廓不清或压铸件形状不完整。 检验:目测或测量检查
材料工程学院材料成型教研室
铝合金铸件铸造技术
原因:合金流动性不良、金属液过早凝固、型腔困气使金属液充填受阻。 措施:1)提高浇注温度、模具温度、压射速度或压射比压、缩短充型时 间、强化合金的充型能力; 2)采用正确的熔炼工艺,减少合金液吸气、氧化和夹杂,提高合
压铸件有可能产生变形。 人工时效是将压铸件加热到某一温度并保 持一段时间,使压铸件基体达到稳定状态。铝合金的时效处理温度为
175~200℃,保温时间为2.0~3.0h,空冷。
压铸模具结构组成
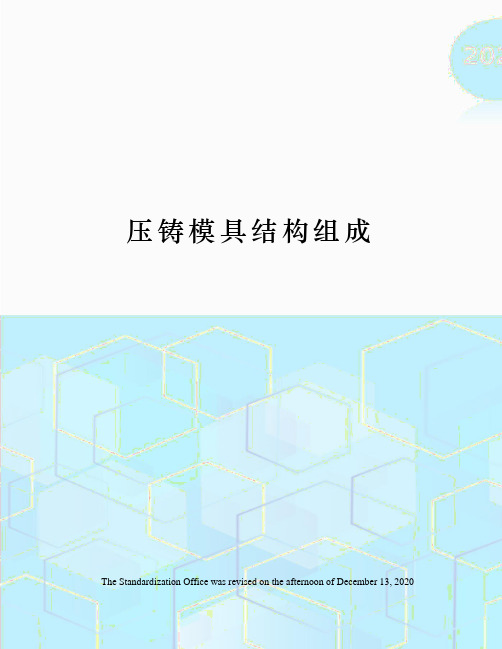
压铸模具结构组成The Standardization Office was revised on the afternoon of December 13, 2020压铸模具结构组成(一).压铸模结构组成定模:固定在压铸机定模安装板上,有直浇道与喷嘴或压室联接动模:固定在压铸机动模安装板上,并随动模安装板作开合模移动合模时,闭合构成型腔与浇铸系统,液体金属在高压下充满型腔;开模时,动模与定模分开,借助于设在动模上的推出机构将铸件推出.(二).压铸模结构根据作用分类型腔:外表面直浇道(浇口套)成型零件二)浇注系统模浇道(镶块)型芯:内表面内浇口余料(三)导准零件:导柱;导套(四)推出机构:推杆(顶针),复位杆,推杆固定板,推板,推板导柱,推板导套.(五)侧向抽芯机构:凸台;孔穴(侧面),锲紧块,限位弹簧,螺杆.(六)排溢系统:溢浇槽,排气槽.(七)冷却系统(八)支承零件:定模;动模座板,垫块(装配,定位,安装作用)压铸模采购选择信誉好、技术高、经验丰富的专业压铸模具厂制造模具。
压铸模是一种特殊的精密机械,那些专业压铸模具厂,他们有适合生产压铸模具的精密机床,能确保模具尺寸精度;他们有经验丰富的高级模具技师,技师的丰富经验是压铸模具实用好用的保证;他们与材料供应商和热处理厂有密切的关系,他们有完善的售后服务体系……。
良好的模具设计与制造是压铸模具长寿命、低故障、高效率的基础。
低价位的劣质压铸模,将会以压铸生产中表现出的低生产效率、高故障,让您浪费很多昂贵的压铸工时,花去更多的金钱。
压铸模安装模具安装调整工应经过培训合格上岗⑴、模具安装位置符合设计要求,尽可能使模具涨型力中心与压铸机距离最小,这样可能使压铸机大杠受力比较均匀。
⑵、经常检查模具起重吊环螺栓、螺孔和起重设备是否完好,确保重吊时人身、设备、模具安全。
⑶、定期检查压铸机大杠受力误差,必要时进行调整。
- 1、下载文档前请自行甄别文档内容的完整性,平台不提供额外的编辑、内容补充、找答案等附加服务。
- 2、"仅部分预览"的文档,不可在线预览部分如存在完整性等问题,可反馈申请退款(可完整预览的文档不适用该条件!)。
- 3、如文档侵犯您的权益,请联系客服反馈,我们会尽快为您处理(人工客服工作时间:9:00-18:30)。
铝合金压铸模具结构剖析
铝合金压铸模具,是如何设计的?如题,产品图如下,有很多的薄片小筋板,分型面是平整的;学习参考就来下载图纸吧。
模具设计思路:
1.压铸模具设计,铝合金压铸模产品的三维外观,平面较于规则,对于新手模具设计师来说,都可以搞定模具设计;
2.压铸模具图纸产品后模侧的结构会有凸起特征,分型面直接用坐标拆分即可;
3.压铸模具设计-拔模检测,以正负0.5为分析值,其符合开模要求;
4.压铸模具图纸-内厚分析,两端有装配结构孔,其结构较厚,上面有装配的螺丝孔;
5.压铸模具图纸,其模具的外观整体结构,压铸模具不带工字板,要开码模槽;
6压铸模具图纸,滑块位置结构剖面线,其铲基原身留,斜导柱尽量做到16;
7.压铸模具图纸,分流锥剖面图,整体来说,压铸模具结构相对于简单,分流锥图解流道不好设计;
8.压铸模具设计教程,前模仁平面有凸起台阶,流道的对面是渣包,用UG拆分体一次可以把分型面设计好,渣包要拉伸、拔模、倒R角;
9.压铸模具设计,后模结构设计,一般设计压铸模具,都需要用模流分析软件跑一跑,然后再画进胶流道,流道是压铸模具设计的一大难点;
10.压铸模具设计,滑块入子原身结构设计,侧孔用滑块抽芯,双螺丝固定在行位座上。