数控车床对刀与刀补
数控机床对刀的方式及其对刀步骤

在进行加工之前,数控车床要进行对刀操作,以便确保产品加工的精度以及准度,在实际进行生产的过程中,数控车床对刀的操作有试切对刀和机外对刀仪这两种对刀方法,但是在进行对刀操作的时候也会出现一些问题,下面我们就来具体介绍一下数控车床对刀的操作步骤。
1、试切对刀试切对刀主要用在建立加工坐标系。
在安装好工件后,为了可以加工出需要的加工件,要将编程原点设定为加工原点,建立加工坐标系,用来确定刀具和工件的相对位置,使刀具按照编程轨迹进行运动,最终加工出所需零件。
试切对刀的步骤主要有:(1)选择机床的手动操作模式;(2)启动主轴,试切工件外圆,保持X方向不移动;(3)停主轴,测量出工件的外径值;(4)选择机床的MDI操作模式;(5)按下“off set sitting”按钮;(6)按下屏幕下方的“坐标系”软键;(7)光标移至“G54”;(8)输入X及测量的直径值;(9)按下屏幕下方的“测量”软键;(10)启动主轴,试切工件端面,保持Z方向不移动;2、机外对刀仪对刀机外对刀仪对刀需要将显微对刀仪固定于车床上,用于建立刀具之间的补偿值。
但是因为刀具尺寸会有一定差别,机床中刀位点的坐标值也会因此而出现不同。
如果不设立刀具之间的补偿值,运行相同的程序时就不可能加工出相同的尺寸,想要保证运行相同的程序时,运用不同的刀具得出相同的尺寸,则需要建立刀具间的补偿。
机外对刀仪对刀的步骤主要有:(1)移动基准刀,让刀位点对准显微镜的十字线中心;(2)将基准刀在该点的相对位置清零,具体操作是选择相对位置显示;(3)将其刀具补偿值清零,具体操作是按下“off set sitting”按钮,按下屏幕下方的“补正”软键,选择“形状”,在基准刀相对应的刀具补偿号上输入Xo、Zo;(4)选择机床的手动操作模式,移出刀架,换刀;(5)使其刀位点对准显微镜的十字线中心;(6)选择机床的MDI操作模式;(7)设置刀具补偿值,具体操作是按下“offset sitting”按钮,按下屏幕下方的“补正”软键,选择“形状”,在相对应的刀补号上输入X、Z;(8)移出刀架,执行自动换刀指令即可。
数控车床对刀方法及调刀补的探讨

程 序
0001 0
669 印 万 Z ‘ -
} 程今名 一
姗 台 扣 调用G, 4工件坐标系, 日 6 设定主轴转通
该方法是以机床霉点为参考点, 通过对刀 找出工件原点在机械坐标系中的机械坐标值, 把此值作为刀具补偿量直接输人到机床的刀 具形状补偿中, 通过调用此值来使坐标系产生 定 编 程原 点 选在 工 件右 端 面的 中 心处 。 偏移 , 从而建立起工件坐标系。因此方法是 以机械琴点为参考点的 所以开机后首先须回 , 50指令设定工件坐标系 用G 机床零点以建立机床坐标系。该对 刀方法不 该方法是通过刀具刀位点的位置相对于 程序中有‘ 50 召甲中无‘ 即 说 用 存在基准刀, 且方便可行, 在数控车床上, 我们 工件坐标系原点的位置来建立工件坐标系的 常用此对刀方法。但需要注意的是, 在使用 州 洲1 】 仪 1002 程序名 (如田I 所示)。该指令可编制在加工程序的开 该方法时, 在程序的开头出现移动指令的程序 头, 也可以直接在操作面板上输人井执行。采 设1 工件坐标系, 权 段之前. 必须先有调用刀补的程序段。 用 G50 设定的工件坐标系, 不具有记忆功能, Z 1 0 幻 其对刀步骤如下: 序起动前刀具的刀 当机床关机后, 设定的坐标系立即消失, 且在 ( 1)先将外部坐标偏移、G54 - G59 及刀 位点须在X 2100. 80. 执行该指令前, 刀具必须位于G 5 0 指定的位 补号里的值清零。 置, 鉴于此, 这种方法现较少使用。 坐标处 (2)选择任意一把刀, 不带刀 。 补 (3)试切工件外圆同 1,选择操作面板中的 "O F F S ET " 键, “ 在 形状份中找到对应的 刀具编号, 镬入X d 再按$(R .此时系统自动 2 用G 54--G59指令设定工件坐 标系 计算 X 向的工件原点( 当前刀位点的机械坐标 该方法相当于将机床原点移至工件原点, 值减去工件的直径d )并设定, 所以在用 G54- G59 设置工件坐标系时 开机 (4)试切工件右端面同 1.选择操作面板中 后首先须回机床零点以建立机床坐标系。这 的 “ F F S ET " 键, “ O 在 形状”中我到对应 种方法适用于批量生产且工件在卡盘上有固 的刀具编号, 键入ZO 再按测里.此时系统自 , 动 定装夹位置的加工. 计算Z 向的工件原点( 当前刀 位点的机械坐标 图 1 用 G50 设定工件坐稿 ;系 其对刀步骤如下: 值 )井设 定, ( 1)先将外部坐标偏移、G54 - G59 及刀 (5 )其余刀的对刀步骤同(3 ), (4) , 其对刀步骤如下: 补号里的值清零, (6)至此, 用本方法对刀结束, 可以调出程 ( 1)先将外部坐标偏移、G54 - G 59 及刀 (2) 选择任意一把刀, 不带刀补(一般是加 序进行加工了。 补号里的值清零: 工中的第一把刀, 将此刀作为墓准刀). (2)选择任意一把刀, 不带 刀 补(一般是加 (3)试切工件外圆同1 选择操作面板中的 程 序 说 明 工中的第一把刀, 将此刀作为基准刀) , "O FF S ET" 键 , “ 在 坐标系”中找到G 54 , ③在手动操作方式下, 用所选刀具在加工 a 加 1 加 程序名 键人Xd .再按测量, 此时系统自动计算x 向的 余童范围内试切工件外圆 在 X 轴不动的情况 工件原点(当前刀位点的机械坐标值减去工件 7 Y 01 1 1 调用刀具及刀具补偿 下沿Z轴退刀 停止主轴并测量此时工件的直 的直径d) 并设定 . G97 ‘ 姗 56 00 主轴值转滚,刀其每转进给 佣 径d , MDI 方式下执行 G50Xd , 在 此时绝对坐 (4)试切工件右端面同 1.选择操作面板中 标X 显示为 “ d: 设定主轴转边600r 人 的. 的 “ F F S ET " 键 . 在 ‘ O 坐标系”中找到 (4)在手动操作方式下沿工件右端面切削, G54, 键人2 氏再按侧量.此时系 自动计算 Z 统 。 。Z 一 进 - }袂 刀 速 在 Z轴不动的情况下沿 X 轴退刀, 停止主轴 , 向的工件原点(当前刀位点的机械坐 标值)井设 } 一 在MDI 方式下执行G5020 程序段, 此时绝对 定; 坐标Z 显示为 “ " , 0 (5)其余刀的对刀 步骤同 1 中5. 8 , 在用G54 - G 59 及刀具形抉补偿对刀时, (5)在安全位里换好另一把刀。 (6)至此 用G54 - G59 对刀结束, 可以调 (6)试切工件外圆 并测量此时工件的直径 出程序进行加工了。采用此种 法对刀, 加工 断电后上电只要回一次机械零点后即可继续 加工, 操作简单 便.
刀具补偿亦有三种

刀具的几何补偿和磨损补偿
作者:乐乐 文章来源:本站原创 点击数:1304 更新时间:2009/4/26
刀具几何补偿是补偿刀具形状和刀具安装位置与编程时理想刀具或基准刀具的偏移的;刀具磨损补偿则是用于补偿当刀具使用磨损后刀具头部与原始尺寸的误差的。由于这些补偿数据通常是通过对刀后采集到的,而且必须将这些数据准确地储存到刀具数据库中,然后通过程序中的刀补代码来提取并执行。
刀具几何补偿是补偿刀具形状和刀具安装位置与编程时理想刀具或基准刀具的偏移的;刀具磨损补偿则是用于补偿当刀具使用磨损后刀具头部与原始尺寸的误差的。由于这些补偿数据通常是通过对刀后采集到的,而且必须将这些数据准确地储存到刀具数据库中,然后通过程序中的刀补代码来提取并执行。
刀具的几何补偿和磨损补偿中刀补指令用T代码表示。常用T代码格式为:T xx xx,即T后可跟4位数,其中前2位表示刀具号,后两位表示刀具补偿号。当补偿号为0或00时,表示不进行补偿或取消刀具补偿。若设定刀具几何补偿和磨损补偿同时有效时,刀补量是两者的矢量和。若使用基准刀具,则其几何补偿位置补偿为零,刀补只有磨损补偿。在图示按基准刀尖编程的情况下,若还没有磨损补偿时,则只有几何位置补偿,?X=?X j、?Z=?Z j;批量加工过程中出现刀具磨损后,则:?X=?X j+?X m、?Z=?Z j+?Z m;而当以刀架中心作参照点编程时,每把刀具的几何补偿便是其刀尖相对于刀架中心的偏置量。因而,第一把车刀:?X=?X 1、?Z=?Z 1;第二把车刀:?X=?X 2、?Z=?Z 3。
数控车床实用对刀方法与刀具补偿
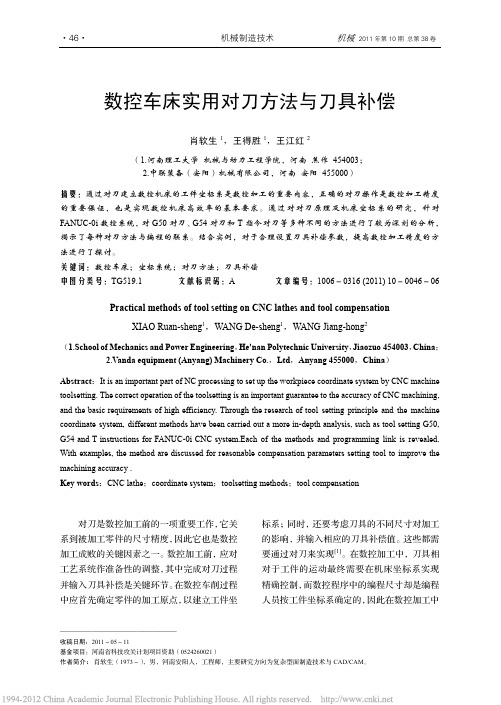
M03 S500;
.....
机械 2011 年第 10 期 总第 38 卷
机械制造技术
·49·
G00 Xα Zβ; M30;
2.2 采用机床坐标系零点偏置建立工件坐标 系(G54 对刀)
G54 指令也称为坐标偏置指令,其实质是 确定工件坐标系原点在机床坐标系中的坐标 值。通过对刀确定工件原点在机床坐标系中的 坐标值,然后通过“MDI”手工输入面板将该 坐标值输入到数控机床中的坐标系寄存器中, 在数控加工程序中不需要写出该数值,只须通 过 G54 指令调用工件坐标系即可。常用的坐 标偏置指令有 G54-G59,最多可建立 6 个工件 坐标系[5],G54 设置工件坐标系与起刀点的位 置无关,如图 3 所示。
———————————————
收稿日期:2011-05-11 基金项目:河南省科技攻关计划项目资助(0524260021)
作者简介:肖软生(1973-),男,河南安阳人,工程师,主要研究方向为复杂型面制造技术与 CAD/CAM。
机械 2011 年第 10 期 总第 38 卷
机械制造技术
·47·
就需要确定刀具刀位点在工件坐标系中的坐 标,从而确定工作坐标系原点在机床坐标系中 的位置,这一过程称为对刀,对刀是数控加工 中的重要的操作技能,它不但影响着数控加工 的精度,还影响着数控加工的效率[2]。
中图分类号:TG519.1
文献标识码:A
文章编号:1006-0316 (2011) 10-0046-06
Practical methods of tool setting on CNC lathes and tool compensation
数控车床的对刀与刀具补偿
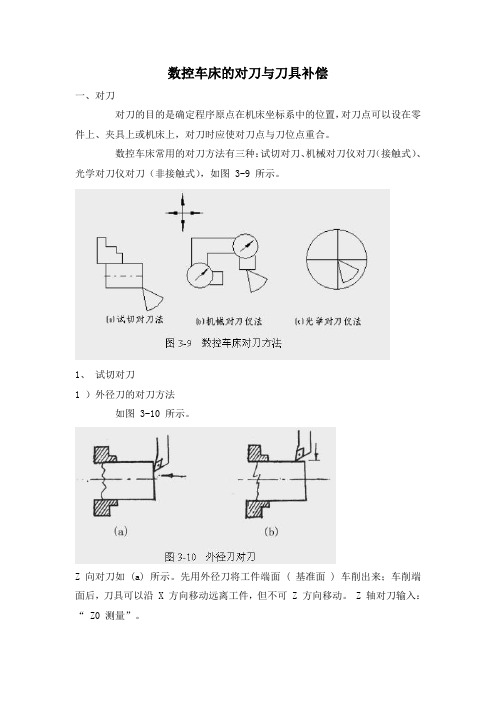
数控车床的对刀与刀具补偿一、对刀对刀的目的是确定程序原点在机床坐标系中的位置,对刀点可以设在零件上、夹具上或机床上,对刀时应使对刀点与刀位点重合。
数控车床常用的对刀方法有三种:试切对刀、机械对刀仪对刀(接触式)、光学对刀仪对刀(非接触式),如图 3-9 所示。
1、试切对刀1 )外径刀的对刀方法如图 3-10 所示。
Z 向对刀如 (a) 所示。
先用外径刀将工件端面 ( 基准面 ) 车削出来;车削端面后,刀具可以沿 X 方向移动远离工件,但不可 Z 方向移动。
Z 轴对刀输入:“ Z0 测量”。
X 向对刀如 (b) 所示。
车削任一外径后,使刀具 Z 向移动远离工件,待主轴停止转动后,测量刚刚车削出来的外径尺寸。
例如,测量值为Φ 50.78mm, 则 X 轴对刀输入:“ X50.78 测量”。
2 )内孔刀的对刀方法类似外径刀的对刀方法。
Z 向对刀内孔车刀轻微接触到己加工好的基准面(端面)后,就不可再作 Z 向移动。
Z 轴对刀输入:“ Z0 测量”。
X 向对刀任意车削一内孔直径后,Z 向移动刀具远离工件,停止主轴转动,然后测量已车削好的内径尺寸。
例如,测量值为Φ 45.56mm, 则 X 轴对刀输入:“ X45.56 测量” 。
3 )钻头、中心钻的对刀方法如图 3-11 所示。
Z 向对刀如( a )所示。
钻头 ( 或中心钻 ) 轻微接触到基准面后,就不可再作 Z 向移动。
Z 轴对刀输入:“ Z0 测量”。
X 向对刀如( b )所示。
主轴不必转动,以手动方式将钻头沿 X 轴移动到钻孔中心,即看屏幕显示的机械坐标到“ X0.0 ”为止。
X 轴对刀输入:“ X0 测量”。
2、机械对刀仪对刀将刀具的刀尖与对刀仪的百分表测头接触,得到两个方向的刀偏量。
有的机床具有刀具探测功能,即通过机床上的对刀仪测头测量刀偏量。
3、光学对刀仪对刀将刀具刀尖对准刀镜的十字线中心,以十字线中心为基准,得到各把刀的刀偏量。
二、刀具补偿值的输入和修改根据刀具的实际参数和位置,将刀尖圆弧半径补偿值和刀具几何磨损补偿值输入到与程序对应的存储位置。
数控车床对刀
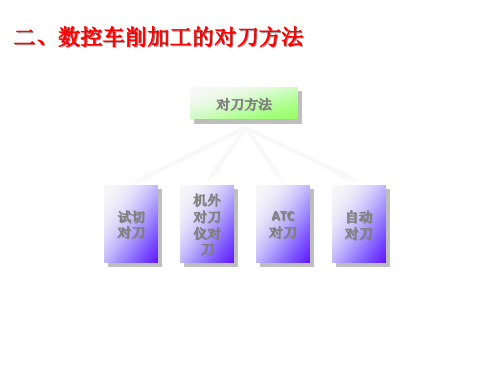
第二步:试切工件端面,把端面在工件坐标系中Z的坐标值,保持Z轴方向不动, 刀具退出。进入形状补偿参数设定界面,将光标移到相应的位置,输入Z0,按 [测量]软键对应的刀具偏移量自动输入 ;
第三步:按照第一、二步对刀方法,对其余2把刀具进行对刀及设置
928TC数控系统 对刀步骤:
第一步:在手动方式下移动刀具在工件上切出一个小台阶。测量所切出的 台阶的直径,按 I 键,屏幕显示 刀偏 X ,输入测量出的直径值,按 Enter 键
3.ATC对刀 它是在机床上利用对刀显微镜自动地计算出车刀长度的简称,
对刀镜与支架不用时取下,需要对刀时才装到主轴箱上。对刀时, 用手动方式将刀尖移到对刀镜的视野内,再用手动脉冲发生器微量 移动使假象刀尖点与对刀镜内的中心点重合(如图所示),再将光 标移到相应刀具补偿号,按“自动计算(对刀)”按键,这把刀具 在两个方向的长度就被自动计算出来,并自动存入它的刀具补偿号 中。
(2) 对刀原理
1
2
X
Z刀补
ZZxx xx
3
φD
X刀补
Xxx
试切一段外圆
Z
FANUC数控系统 对刀步骤:
第一步:用所选刀具试切工件外圆,测量试切后的工件直径,比如记为α,
保持X轴方向不动,刀具退出。点击MDI键盘上
的键,进入形状补偿参
数设定界面,将光标移到与刀位号相对应的位置,输入Xα,按菜单软键[测 量],对应的刀具偏移量自动输入 ;
谢谢观看/欢迎下载
BY FAITH I MEAN A VISION OF GOOD ONE CHERISHES AND THE ENTHUSIASM THAT PUSHES ONE TO SEEK ITS FULFILLMENT REGARDLESS OF OBSTACLES. BY FAITH I BY FAITH
数控车床刀具补偿及换刀程序编写

绝对编程:
G90 G28 X140.0 Z130.0 ; A--B--R
T0202 ;
换刀
G29 X60.0 Z180.0 ;
R--B--C
参考点
增量编程
G28 U40 W100 T0000 T0202 目标点 G29 U-80 W50
可以使按工件轮廓编程不受影响.
❖ 一、刀具补偿的概念
❖ 刀具补偿:是补偿实际加工时所用的刀具
与编程时使用的理想刀具或对刀时使用的 基准刀具之间的偏差值,保证加工零件符 合图纸要求的一种处理方法。
二、刀具补偿的种类
刀具补偿
刀具的几何补偿
(TXXXX实现)
几何位置补偿 磨损补偿
刀尖圆弧半径补偿
(G41、G42实现)
从图示可知,
➢ 若刀尖方位码设为0或9时,机床将以刀尖圆弧中心
为刀位点进行刀补计算处理;
➢ 当刀尖方位码设为1~8时,机床将以假想刀尖为刀
位点,根据相应的代码方位进行刀补计算处理。
5、刀具半径补偿指令 ❖格式:
G41 G00 X __ Z __ G42 G01
G40 G00 X__ Z __
❖说明:
3、刀径补偿的取消
❖刀具中心从与编 程轨迹偏离过度到 与编程轨迹重合的 过程.
刀径补偿的引入和取 消必须是不切削的空 行程上.
例2:考虑刀尖半径补偿
D
C (24,-24)
O1111 N1 G92 X40.0 Z10.0 N2 T0101 N3 M03 S400 N4 G00 X40.0 Z5.0 N5 G00 X0.0 N6 G42 G01 Z0 F60 (加刀补) O N7 G03 X24.0 Z-24 R15 N8 G02 X26.0 Z-31.0 R5 N9 G40 G00 X30 (取消刀补) N10 G00 X45 Z5 N11 M30
广州数控GSK980TD操作步骤(刀补对刀)
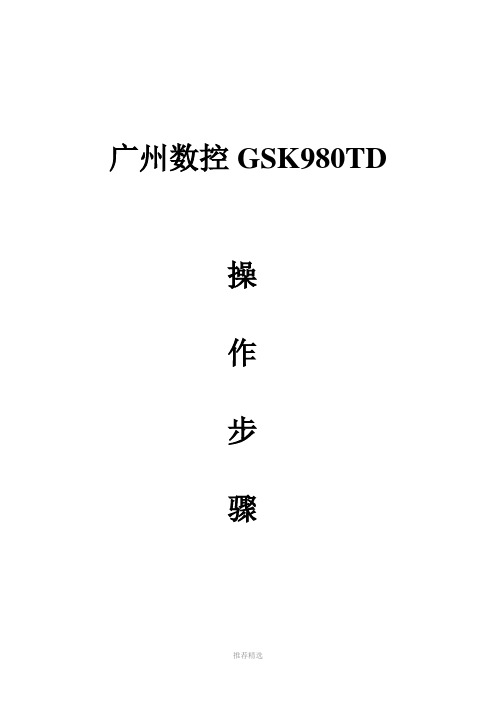
广州数控GSK980TD操作步骤广州数控GSK980TD操作步骤(刀补对刀)第一部分:熟悉机床面板操作(一~十一,其中三、四、五条自己阅读,自行练习,也可以不练)第二部分:练习对刀及检验对刀是否正确(十二~十五)第三部分:加工零件(十六~二十三)二、打开一个程序:(举例:打开O 0001三、按顺序快速打开程序目录里的所有程序。
举例:在编辑下打开O0001。
按O0002;再按动打开下一个程序O0003;余此类推。
反之,按四、把当前程序复制到新建程序里:(举例:把O 0001号程序复制到新建程序O 0008号程序里)在编辑下打开O 0001号程序,按—,复制完成。
五、把当前程序改名:(举例:把O 0001号程序名改为O 0008号程序名)在编辑下打开O 0001号程序,按—,改名完成。
六、编写新的程序:(举例:编写O 0001号程序)七、删除一个程序:(举例:删除O 0001九、输入转速:(举例:输入S800转速)十、转动刀架:(举例:把刀架转动到1号刀位)方法1或方法2十二、对1号外圆刀(把刀架转到T0100):Z X轴方向车一刀端面(约0.5㎜),再X到“刀具偏置”界面,光标移到001X Z轴方向车一刀外圆,再Z轴方向退刀,(光标移到001假如外圆测量值是φ25.32)十三、对2号切断刀(把刀架转到T0200):方法和对1号外圆刀相同。
(注意:把光标移到002序号。
在对Z向时,由于1号刀已车好端面,因此2号刀不能再车端面,只能轻碰端面。
)十四、对3号螺纹刀(把刀架转到T0300):方法和对1号、2号刀相同。
(注意:把光标移到003序号。
在对Z向时,由于车刀刀尖是60度,因此刀尖不能轻碰端面,刀尖只能与端面基本对齐。
)十五、检验对刀是否正确: (记得检验时要带刀补)检验Z 向时,车刀要在毛坯直径外面;检验X向时,车刀要在毛坯端面外面,以防车刀直接与毛坯碰撞1号外圆刀(把刀架转到T0101)摇至Z0,查看车刀刀尖是否与端面对齐;再用手轮把车刀摇至X25.32(假如外圆测量值是φ25.32),查看车刀刀尖是否在φ25.32外圆上面。
- 1、下载文档前请自行甄别文档内容的完整性,平台不提供额外的编辑、内容补充、找答案等附加服务。
- 2、"仅部分预览"的文档,不可在线预览部分如存在完整性等问题,可反馈申请退款(可完整预览的文档不适用该条件!)。
- 3、如文档侵犯您的权益,请联系客服反馈,我们会尽快为您处理(人工客服工作时间:9:00-18:30)。
后续课程安排:
• 仿真机房:数控车床对刀仿真操作
• 刀位点:
• 刀位点是表示刀具特征的点,一般是刀具上的 一点。
刀尖点 • 尖形车刀的刀位点为假想
,园
形车刀的刀位点为园弧中心。
起刀点:
• 起刀点是刀具相对工件运动的起点,即加工 程序开始时刀具刀尖点的起始位置,经常也 把它作为加工程序的终点。
(3)对刀点:
• 对刀点是用来确定刀具与工件的相对位置 关系的点.是确定工件坐标系与机床坐标系 关系的点。
填空4 填空5
提
填空6
说 T0606; G00 X40 Z-24;
填空7 填空8
问
明 G01 X0 F0.1; G00 X100; Z150; T0100; M05;
填空9 填 填 填空 空 空111102 主轴停转
程序结束
3、加工过程:
• (1)开机、回零 • (2)装夹工件 • (3)安装刀具 • (4)用试切法对刀,设置刀补参数 • (5)输入程序 • (6)校验程序 • (7)确认程序无误后,自动加工工件 • (8)检测工件
在X轴方向退刀, • 按MDI子菜单下的刀偏表,显示刀具补偿画面,
移动光标至欲设定偏置号处。F10→F4→F2
• 在试切长度下输入0,则自动显示该把刀在Z方向 刀补。
• (5)用第一把刀试切工件外园:仅仅 在Z轴方向退刀,停止主轴。
• 测量直径,按MDI子菜单下的刀偏表, 显示刀具补偿画面,移动光标至欲设 定偏置号处。在试切直径下输入值, 则自动显示该把刀在X方向刀补。
数控车床操作
第 2 1 单元 数控车对刀与刀补
教学目标:
1.理解数控车对刀有关的概念与对刀操作
2.理解刀具补偿的概念、作用及刀具补偿的 设定方法
3.理解G00和G01指令及简单零件数控车程 序
• 复习:
引入
• 提问: • 工件坐标系和机床坐标系定义
一.数控车对刀有关的 概念与对刀操作
对刀有关的概念:
• 式中:X、 Z:快速点定位的终点绝对坐标值。
• U、W :快速定位终点相对于起点(上一点)的
位移量相对坐标值
2、直线插补指令:
• 控制刀具在坐标轴间以插补联动方式按指定进 给速度做任意斜率的直线运动.
• 指令格式: G01 X Z F_ ;
•
G01 U W F_ ;
• 式中:X、 Z:直线插补的终点坐标值。
• 换刀点是数控加工程序中指定用 于换刀位置的点。
• 换刀点位置应避免与工件夹具 和机床发生干扰。
确定对刀点或对刀基准点的一般原则:
• 对刀点位置容易确定。 • 能够方便换刀,以便与换刀点重合。 • 对刀点尽量与工件尺寸设计基准或工艺
基准一致。 • 批量加工时,为使一次对刀可以加工一
批工件,对刀点应在定位元件的起始基 准上,并与编程原点和定位基准重合, 以便直接按照定位基准对刀。
• (6)同理,将其它刀转至加工位对刀, 设置刀补参数。
播放《斯沃仿真系统对刀》详细步骤
二.刀具补偿
• 数控车床加工时,由于各种形式刀具 不同,当其它刀转至加工位时,其刀 位点的位置是不同的,为使零件加工 程序不受影响,要进行刀具几何补偿。
刀具补偿指令由刀具功能 T 设定。
• T 指令后跟四位数,前两位是刀具号, 后两位是刀具补偿号。刀具补偿号实 际上是刀具补偿器的地址号。该寄存 器存有刀具补偿量。数控车床试切对 刀主要是设置刀具几何补偿。
(4)对刀:
• 在加工程序执行前,调整每把刀的 刀位点,使其置于对刀点上,以建立 工件坐标系。
(6)对刀基准点:
• 对刀时确定对刀点的位置所依据的基 准。
• 该基准可以是点、线、面。 • 对刀基准点一般设在工件上(定位基准或
测量基准)、夹具上(夹具元件设置的起 始点)或机床上。
(7)换刀点:
数控车床的对刀及刀具补偿
• 数控车床对刀方法有以下几种: • (1)手动对刀。 • (2)机外对刀仪对刀。 • (3)自动对刀
• 手动对刀中常用试切对刀。
播放数控车仿真软件对刀演示
1、数控车床的试切对刀步骤:
• (1)机床回零 • (2)装夹工件 • (3)安装各把刀具 • (4)主轴转动,用第一把刀试切工件端面:仅仅
T0101;
1号刀至工件位,1号刀补
程 G00 X40 Z0; G01 X-1 F0.2;
序 G00 Z2
刀具快速运动至x40 z0 处 刀具以0.2mm/r速度运动至x-1处
填空1
内 G00 X26 G01 Z-12 F0.2;
填空2 填空3
容 X40; G00 X100 Z150;
与 M03 S250;
T指令代码说明如下:
• T XX XX • 刀具号 刀具补偿号 • 如: T 01 01 • 1号刀 1号刀具补偿
打开华中数控仿真系统演示说明
三、G00和G01指令:
• 1、快速点定位G00:
• 刀具以点位控制的方式从刀具所在位置移 动到目标位置。
• 指令格式:G00 X Z ; 绝对坐标值
•
G00 U W ;相对坐标值
•
U、W :直线插补终点相对于起
点的位移量
•
F :进给速度(不可缺少)
1.工艺分析
• 毛坯选择:Φ30×60 • 刀具:外圆车刀、切断刀 • 夹具:三爪卡盘 • 工步:车端面、车外圆、切断
2. 程序编制:
• 工件坐标系原点:工件右端面中心
仿真加0;
主轴正转,400r/min