哈工大机械制造大作业
哈工大机械原理大作业1-16

Harbin Institute of Technology机械原理大作业设计说明书(一)课程名称:机械原理设计题目:连杆运动分析(16)院系:能源科学与工程学院班级:1102201设计者:学号:指导教师:赵永强唐德威设计时间:2013年6月8 日哈尔滨工业大学1 连杆机构运动分析题目16:如图所示机构,已知机构各构件的尺寸为AC l =CE l =100mm ,BC l =CD l =200mm ,90BCD ∠=,构件1的角速度为10/rad s ,试求构件5的角位移、角速度和角加速度,并对计算结果进行分析。
2 分析过程2.1 建立坐标系建立以点E 为原点的固定平面直角坐标系x-E-y,如图所示:图2 机构坐标系2.2结构分析将构件BCD 分为杆3和杆4。
该机构由2个Ⅰ级杆组RR (杆1和杆5)和两个Ⅱ级杆组RRP (杆3、杆4和滑块B 、D )。
其中原动件为杆1。
现将杆组分为如下两部分:图1 机构运动简图RRPRR图3 各级杆组2.3 建立数学模型2.3.1构件1、2、3的分析原动件杆1的转角:1θ=0—360。
原动件杆1的角速度:1ω=.1θ=10/rad s原动件杆1的角加速度:..1αθ==0运动副A 的坐标:0200A A x y mm =⎫⎬=⎭运动副A 的速度及加速度都为零。
构件1为BC (RRP Ⅱ级杆组)上滑块B 的导路 滑块B 的位置为:132cos cos B A C x x s x l θθ=+=+ 132sin sin B A C y y s x l θθ=+=+消去s,得:212arcsinA l θθ=+式中:011()sin ()cos C A C A A x x y y θθ=---构件3的角速度i ω和滑块B 沿导路的移动速度D υ:.211213(Q sin Q cos )/Q ωϕθθ==-+ 1322323(Q cos Q sin )/Q D s l l υθθ⋅==-+式中:..11111211321212Q sin ;Q cos ;Q sin sin cos sin l l l θθθθθθθθ=-==+构件3的角加速度和滑块B 沿导路移动的加速度:..241513(Q sin Q cos )/Q αθθθ==-+..4325323(Q cos Q sin )/Q B s l l υθθ==-+式中:122......21142211111Q cos sin cos 2sin l l l s θθθθθθθθ=---- 122......21152211111Q sin cos sin 2cos l l l s θθθθθθθθ=+-+2.3.2 构件3,4,5的分析构件3,4,5,由1个Ⅰ级基本杆组和一个RRP Ⅱ级杆组组成,与构件1,2,3结构相同,只运动分析过程与其相反。
哈工大机械制造大作业

哈工大机械制造大作业一、零件分析题目所给的零件是CA6140车床的拨叉。
它位于车床变速机构中,主要起换档,使主轴回转运动按照操作者的要求工作,获得所需的速度和扭矩的作用。
零件上方的孔与操纵机构相连,二下方的Φ55叉口则是用于与所控制齿轮所在的轴接触,拨动下方的齿轮变速。
其生产纲领为批量生产,且为中批生产。
图1-1 CA6140拨叉零件图二、零件的工艺分析零件材料采用HT200,加工性能一般,在铸造毛坯完成后,需进行机械加工,以下是拨叉需要加工的表面以及加工表面之间的位置要求:1、小头孔Φ25:该加工面为内圆面,其尺寸精度要求为;2、叉口半圆孔Φ55:该加工面为内圆面,其尺寸精度要求为;3、拨叉左端面:该加工面为平面,其表面粗糙度要求为,位置精度要求与内圆面圆心距离为;4、叉口半圆孔两端面,表面粗糙度要求为,其垂直度与小头孔中心线的垂直度为;5、拨叉左端槽口,其槽口两侧面内表面为平面,表面粗糙度要求为,其垂直度与小头孔中心线的垂直度为0.08mm。
6、孔圆柱外端铣削平面,加工表面是一个平面,其表面粗糙度要求为。
三、确定毛坯1、确定毛坯种类:零件材料为,查阅机械制造手册,有,考虑零件在机床运行过程中受冲击不大,零件结构又比较简单,故选择铸造毛坯。
图3-1 毛坯模型2、毛坯特点:(1)性能特点:(2)结构特点:一般多设计为均匀壁厚,对于厚大断面件可采用空心结构。
CA6140拨叉厚度较均匀,出现疏松和缩孔的概率低。
(3)铸造工艺参数:铸件尺寸公差:铸件公称尺寸的两个允许极限尺寸之差成为铸件尺寸公差。
成批和大量生产采用金属型时,铸钢和铸件尺寸公差等级为级,选择尺寸公差等级为CT8。
机械加工余量:查阅参考文献[5],铸铁件的加工余量等级为E、F、G,故设计铸件公差为。
最小铸出孔:由于孔深为,孔壁厚度为,此时灰铸铁的最小铸出孔直径大于,故孔不铸出,采用机械加工的方法加工。
3、毛坯尺寸的确定:图3-2如图所示,现对图中1、2、3、4处加工面进行余量计算。
哈尔滨工业大学机械制造装备设计大作业

Harbin Institute of Technology机械制造装备设计大作业题目:无丝杠车床主传动系统设计学院:机电工程学院班级:姓名:学号:©哈尔滨工业大学哈尔滨工业大学机械制造装备设计大作业题目:无丝杠车床主传动系统设计目录一、运动设计 (3)1 确定极限转速 (3)2 确定公比 (3)3 求出主轴转速级数 (3)4 确定结构式 (3)5 绘制转速图 (4)6 绘制传动系统图 (5)7 确定变速组齿轮传动副的齿数 (6)8 校核主轴转速误差 (6)二、动力设计 (7)1 传动轴的直径确定 (7)2 齿轮模数的初步计算 (7)参考文献 (9)设计任务设计题目:无丝杠车床主传动系统设计已知条件:最大加工直径ф400mm,最低转速40r/min,公比φ=1.41,级数Z=11,切削功率N=5.5KW。
设计任务:1.运动设计:确定系统的转速系列;分析比较拟定传动结构方案;确定传动副的传动比和齿轮的齿数;画出传动系统图;计算主轴的实际转速与标准转速的相对误差。
2.动力设计:确定各传动件的计算转速;初定传动轴直径、齿轮模数;选择机床主轴结构尺寸。
一、运动设计1. 确定极限转速已知最低转速为40r/min,公比φ=1.41,参考文献[1]表4-2标准转速系列的本系统转速系列如下:40 57 80 113 160 226 320 453 640 9051280 r/min,则转速的调整范围maxmin 128032 40n nRn===。
2. 确定公比根据设计数据,公比φ=1.41。
3. 求出主轴转速级数Z根据设计数据,转速级数Z=11。
4.确定结构式(1)确定传动组和传动副数由于总级数为11,先按12设计再减掉一组。
共有以下几种方案:12=4×3 12=3×4 12=3×2×2 12=2×3×2 12=2×2×3 根据传动副前多后少原则,以减少传动副结构尺寸选择第三组方案,即: 12=3×2×2(2)确定结构式按前疏后密原则设计结构式中的级比指数,得到:12=31×23×26减掉一组转速为:12=31×23×25对于该结构式中的第二扩大组x 2=5、p 2=2,而因此r 2=φ5×(2-1)=1.415=5.57<8。
哈工大机械原理大作业连杆机构9

机械原理大作业大作业一:连杆机构运动分析学生姓名:学号:指导教师:丁刚完成时间:机电工程学院机械设计系制二〇一八年四月连杆机构运动分析1题目(9)图1 设计题目在图1所示的机构中,已知l AB=60mm,l BC=180mm,l DE=200mm,l CD=120mm,l EF=300mm,h=80mm,h1=85mm,h2=225mm,构件1以等角速度ω1=100rad/s 转动。
求在一个运动循环中,滑块5的位移、速度和加速度曲线。
2分析结构1、杆1为RR主动件,绕A以ω1 转动,自由度1.2、4杆和滑块5为RRP II级杆组.,自由度0.3、2,3杆组成II级杆组RRR,自由度0.总共自由度为F=5*3-2*7=1 .由上述的杆组类型,确认出所需运动分析数学模型:同一构件上的点、RRP、RRR。
3.杆组法对平面连杆机构进行运动分析3.1对主动件杆1 RR I级构件的分析主动杆1转角:φ= [0°,360°) δ=0°,则φ’=ω1=100 rad/s角加速度φ’’=0.已知h2=225mm, h=80mm, l AB=60mm 所以A(225mm,80mm)A点速度(0,0),加速度(0,0)B点位置(x A+l AB*cos(φ), Y A+l AB*sin(φ))B点速度(-l AB*sin(φ), l AB*cos(φ)),加速度(-l AB*cos(φ), -l AB*sin(φ))3.2RRRII 级杆组分析(模型参考教材P37-38)图3 如图所示两个构件组成II 级杆组。
已知了B 的位置(x B ,y B )= (x A +l AB *cos(φ), Y A +l AB *sin(φ)),速度(x ’B ,y ’B ) 和加速度(x ’’B ,y ’’B ), 已知运动副D (0,0), 还可知,x ’D =y ’D =0, x ’’D =y ’’D =0. l BC =180 mm, l CD = 120mm所以,x c =x D +l CD *cos(φi)= x B +l BC *cos(φj) y c =x D +l CD *sin(φi)= x B +l BC *sin(φi) 对于φ的求解: A 0=2*l CD (x B -x D ) B 0=2*l BC (y B -y D ) C 0=l CD 2+ l BD 2- l BC 2为了保证机构的装配正常:l BD ≤l CD + l BC AND l BD ≥Abs (l CD - l BC )可求3杆的转角φi=2*arctan((B 0±sqrt (A 02 + B 02- C 02))/(A 02+ C 02)),角速度w3=φi ’和角加速度α3= φi ’’3.3 同一构件上的点(模型参考书P35-36)Φiφjφi已知D(0,0),速度(0,0),加速度(0,0),3杆转角φi 角速度φi’角加速度φi’’,Φi和它的导数在3.2都有体现LDE= 200mm可求出E的坐标,速度,加速度.x E =x c+lCE*cos(φi)y E =x C+lCE*sin(φi)同样地,速度、加速度通过求导即可得出算式,可以编出程序。
哈工大机械原理大作业23
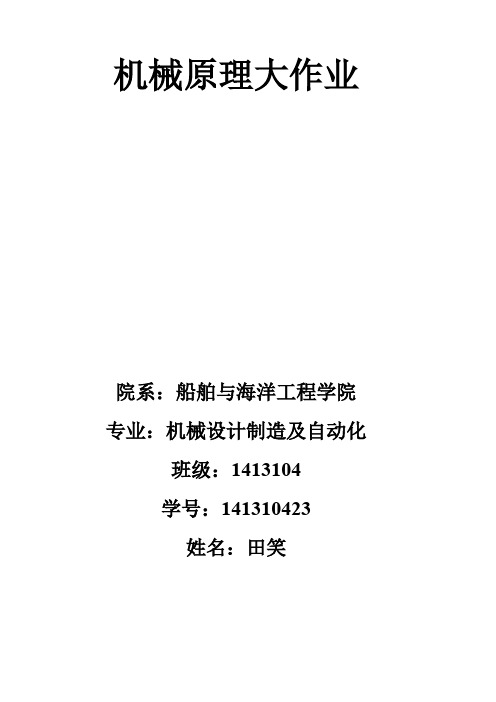
机械原理大作业院系:船舶与海洋工程学院专业:机械设计制造及自动化班级:1413104学号:141310423姓名:田笑哈尔滨工业大学(威海)作业1 连杆机构运动分析1.运动分析题目2.对机构进行结构分析该机构由一级杆组RR(原动件1)、二级杆组RRR(杆2、杆3;杆4、杆5),二级干组RRP(杆6,滑块7)组成。
如图所示:一级杆组:二级杆组RRR(杆2、杆3):- 1 -二级杆组RRR(杆4、杆5):二级杆组RRP(杆6、滑块7):3.建立坐标系建立以A点为坐标原点的坐标系- 2 -- 3 -4.建立组成各基本杆组的运动分析数学模型(1)一级杆组运动分析: 如一级杆组图所示,设AB 杆与X 轴夹角为p,AB 逆时针转动。
位置分析:x _B=x_A+l.*cos(p);y_B=y_A+l.*sin(p); 速度分析:v_Bx=l.*sin(p).*-1.*w; v_By=l.*cos(p)*w;加速度分析:a_Bx=w^2*l.*cos(p).*-1-e*l.*cos(p); a_By=w^2*l.*sin(p).*-1+e*l.*sin(p); (2)二级杆组(RRR 型)运动分析:如二级杆组图(杆2、杆3)所示,设CB 与X 轴夹角为p_2。
角位移分析:d=sqrt((x_D-x_B).^2+(y_D-y_B).^2);b=atan((y_D-y_B)./(x_D-x_B));r=acos((d.^2+l_2^2-l_3^2)./(2*l_2.*d));x_C=x_B-l_2*cos(p_2); y_C=y_B-l_2*sin(p_2); p_2=b+M.*r;p_3=atan((y_C-y_D)./(x_C-x_D));角速度分析:x _D)-y_B)(x _C -(y_C -x _B)-y_D)(x _C -(y_C y_D)-v_By)(y_C -(v_Dy x _D)-v_Bx )(x _C -(v_Dx w_2+=x _D)-y_B)(x _C -(y_C -x _B)-y_D)(x _C -(y_C y_B)-v_By)(y_C -(v_Dy x _B)-v_Bx )(x _C -(v_Dx w_3+=角加速度分析:E=a_Dx-a_Bx+w_2^2*(x_C-x_B)-w_3^2*(x_C-x_D); F=a_Dy-a_By+w_2^2*(y_C-y_B)-w_3^2*(y_C-y_D); y_B)-x _D)(y_C -(x _C -y_D)-x _B)(y_C -(x _C y_D)-F(y_C x _D)-E(x _C e_2 +=y_B)-x _D)(y_C -(x _C -y_D)-x _B)(y_C -(x _C y_B)-F(y_C x _B)-E(x _C e_3 +=5.计算编程及输出结果Matlab 编程作图(具体程序见附录):(1)E 点的轨迹- 4 -0.10.150.20.250.30.350.40.450.50.550.6-0.0500.050.10.150.20.250.3x/mmy /m mE 点的轨迹(2)构件5的角位移、角速度和角加速度角位移:角速度:- 5 - 01234567-15-10-5510θ/radw /r a d /s构件5的角速度角加速度:1234567-100-50050100150200250300θ/radε/r a d /s 2构件5的角加速度附录:%一级杆组运动分析子程序%x_B=x_A+l.*cos(p);y_B=y_A+l.*sin(p);v_Bx=l.*sin(p).*-1.*w;v_By=l.*cos(p)*w;a_Bx=w^2*l.*cos(p).*-1-e*l.*cos(p);a_By=w^2*l.*sin(p).*-1+e*l.*sin(p);%二级杆组运动分析子程序%d=sqrt((x_D-x_B).^2+(y_D-y_B).^2);b=atan((y_D-y_B)./(x_D-x_B));f=(d.^2+l_2^2-l_3^2)./(2*l_2.*d);r=acos((d.^2+l_2^2-l_3^2)./(2*l_2.*d));p_2=b+M.*r;x_C=x_B-l_2.*cos(p_2);y_C=y_B-l_2.*sin(p_2);w_3=((0-v_Bx).*(x_C-x_B)+(0-v_By).*(y_C-y_B))./((y_C-y_D).* (x_C-x_B)-(y_C-y_B).*(x_C-x_D));%角速度%w_2=((0-v_Bx).*(x_C-x_D)+(0-v_By).*(y_C-y_D))./((y_C-y_D).* (x_C-x_B)-(y_C-y_B).*(x_C-x_D));E=0-a_Bx+w_2.^2.*(x_C-x_B)-w_3.^2.*(x_C-x_D);F=0-a_By+w_2.^2.*(y_C-y_B)-w_3.^2.*(y_C-y_D);e_2=(E.*(x_C-x_D)+F.*(y_C-y_D))./(x_C-x_B).*(y_C-y_D)-(x_C-x_D).*(y_C-y_B);e_3=(E.*(x_C-x_B)+F.*(y_C-y_B))./(x_C-x_B).*(y_C-y_D)-(x_C-x_D).*(y_C-y_B);%角加速度%p_3=atan((y_C-y_D)./(x_C-x_D));%角位移%- 6 -- 7 -大作业2 凸轮机构设计1.设计题目如图2-1所示直动从动件盘形凸轮机构,其原始参数见表2-1,据此参数设计该凸轮机构。
(机械制造行业)哈工大机械设计大作业——螺旋起重器

螺旋起重器设计一、 螺旋起重器(千斤顶)简介螺旋起重器是一种简单的起重装置,用手推动手柄即可升起重物。
它一般由底座、螺杆、螺母、托杯、手柄或扳手等零件所组成。
二、 螺旋起重器(千斤顶)结构与功能螺旋起重器结构示意图如右图所示。
零件1为托杯,当千斤顶承受重载时,由1直接托住重物。
螺母5与螺杆7组成螺旋副,同时,螺母5又与底座8固定联接,当转动手柄4时,托杯便会随着螺杆而上下移动,从而将重物托起。
紧定螺钉6主要是为了提高了联接可靠性。
三、 设计题目设计起重量F = 50 000 N,最大起重高度H=150 mm 的螺旋起重器(千斤顶)。
四、 题目解答1.选择螺杆、螺母材料螺杆采用45钢调质,由参考文献[2]表10.2查得抗拉强度σb =600Mpa , σs =355Mpa 。
由于速度较低,螺母材料用铝青铜ZCuAll0Fe3。
2. 耐磨性计算按耐磨性性条件设计螺纹中径d 2,对于梯形螺纹,8.02≥d ][ψp F 螺杆选用45钢,螺母用铝青铜ZCuAll0Fe3,由参考文献[3]表 5.8 查得[]p =18~25MPa ,从表5.8注释中可以查得,人力驱动可提高约20%,则[]p =21.6 ~30MPa ,取[]p =25MPa 。
由参考文献[3]查得,对于整体式螺母系数=1.2~1.5,取=2。
则代入数据,得8.02≥d ][ ψp F ⨯=8.0 =25.3 mm式中:F──螺杆所受轴向载荷,N;d──螺纹中径,mm;2[ p]─—螺旋副材料的许用压力,MPa。
d=30.5 mm, 查参考文献[4]表 11.5 取公称直径d =32 mm,螺距P=3 mm,中径2小径d3(d1)=28. 5 mm,内螺纹大径D4=32.5 mm。
3. 螺杆强度校核螺杆危险截面的强度条件为:σe=≤[σe ]式中:F──螺杆所受轴向载荷,F =50 000 N;d3(d1)──螺纹小径,mm d3(d1)=28. 5 mm;T 1──螺纹副摩擦力矩,T1=F tan (+’ ),为螺纹升角,=arctan=arctan=1.7942;[σe ]——螺杆材料的许用应力, MPa查参考文献[1]表 5.10 .得钢对青铜的当量摩擦因数f’=0.08~0.10,取f ’=0.09,螺纹副当量摩擦角’ = arctan f’= arctan0.09 = 5.1428。
哈尔滨工业大学机械设计大作业
哈尔滨工业大学机械设计作业设计计算说明书题目:设计螺旋起重器系别:机械设计制造及其自动化班号:姓名:日期:哈尔滨工业大学机械设计作业任务书题目:设计螺旋起重器设计原始数据:螺旋起重器是一种简单的起重装置,用手推动手柄即可提升重物。
它一般由底座、螺杆、螺母、托杯、手柄、或扳手等零件所组成。
已知数据:起重量:50kN 最大起重高度:150mm。
目录一、设计题目-----------------------------------------------------------------------------------------------------2二、螺母、螺杆选材-------------------------------------------------------------------------------------------2三、螺杆、螺母设计计算3.1 耐磨性计算-----------------------------------------------------------------------------------------------2 3.2 螺杆强度校核--------------------------------------------------------------------------------------------3 3.3 螺纹牙强度校核-----------------------------------------------------------------------------------------3 3.4 螺纹副自锁条件校核----------------------------------------------------------------------------------43.5 螺杆稳定性校核-----------------------------------------------------------------------------------------4四、螺母外径及凸缘设计------------------------------------------------------------------------------------5五、手柄设计----------------------------------------------------------------------------------------------------5六、底座设计----------------------------------------------------------------------------------------------------6七、其余各部分尺寸及参数---------------------------------------------------------------------------------7八、参考资料-----------------------------------------------------------------------------------------------------8一、 设计题目螺旋起重器(千斤顶)已知条件:起重量F Q =50KN ,最大起重高度H=150mm 。
哈工大机械制造技术基础大作业
哈工大机械制造技术基础大作业一、零件加工图样在CA6140机床中,拨叉在变速箱中起到控制齿轮组的移动,改变啮合齿轮对,从而改变传动比实现变速功能。
零件材料采用200HT 灰铸铁,生产工艺简单、可铸性高,但材料脆性大不易磨削。
需要加工的部分及加工要求如下:1、0.0210Φ22+孔,还有与其相连的8M 螺纹孔和Φ8锥销孔;2、小孔的上端面,大孔的上下两端面;3、大头的半圆孔0.40Φ55+;4、Φ40上端面,表面粗5、糙度为 3.2Ra ,该面和Φ20孔中心线垂直度误差为0.05mm ;5、0.50Φ73+半圆形上下端面与Φ22孔中心线垂直度误差为0.07mm 。
二、零件加工工艺设计(一)确定毛坯的制造形式零件材料为HT200。
考虑到零件在机床运行时过程中所受冲击不大,零件结构又比较简单,生产类型为大批生产,故选择铸件毛坯。
选用铸件尺寸公差等级CT9级。
(二)工艺初步安排零件的加工批量以大批量为主,用通用机床加工,工序适当集中,减少工件装夹次数以缩短生产周期、保证其位置精度。
(三)选择基准基准的选择是工艺规程设计中的重要工作之一。
基准选择得正确合理,可以使加工质量得到保证,生产效率得以提高。
(1)粗基准的选择:以零件的底面为主要的定位粗基准,以两个小头孔外圆表面为辅助粗基准。
这样就能限制工件的五个自由度,再加上垂直的一个机械加紧,就可达到完全定位。
(2)精基准的选择:考虑到要保证零件的加工精度和装夹准确方便,依据“基准重合”原则和“基准统一”原则,以粗加工后的底面为主要定位基准,以两个小孔头内圆柱表面为辅助的定位精基准。
(四)制定工艺路线1.工艺方案分析此零件加工工艺大致可分为两个:方案一是先加工完与Φ22mm 的孔有垂直度要求的面再加工孔。
而方案二恰恰相反,先加工Φ22mm的孔,再以孔的中心线来定位加工完与之有垂直度要求的三个面。
方案一装夹次数较少,但在加工Φ22mm的时候最多只能保证一个面与定位面之间的垂直度要求。
哈工大机械制造基础大作业二
题目及要求(1) 机械加工工艺路线(工序安排)① 工艺方案分析 加工重点、难点② 工序编排 加工顺序、内容③ 加工设备和工艺装备(2) 关键问题分析① 加工工艺问题② 装夹问题③ 生产率问题④ 新技术(3) 解决关键问题的工艺措施(参阅资料)一、零 件 的 分 析零件的工艺分析:零件的材料为HT200,灰铸铁生产工艺简单,铸造性能优良,但塑性较差、脆性高,不适合磨削,为此以下是拨叉需要加工的表面以及加工表面之间的位置要求需要加工的表面:1。
小孔的上端面、大孔的上下端面;2。
小头孔0.021022+-Φmm 以及与此孔相通的8Φmm 的锥孔、8M 螺纹孔;mm;3。
大头半圆孔55位置要求:小头孔上端面与小头孔中心线的垂直度误差为0.05mm、大孔的上下端面与小头孔中心线的垂直度误差为0。
07mm.由上面分析可知,可以粗加工拨叉底面,然后以此作为粗基准采用专用夹具进行加工,并且保证位置精度要求。
再根据各加工方法的经济精度及机床所能达到的位置精度,并且此拨叉零件没有复杂的加工曲面,所以根据上述技术要求采用常规的加工工艺均可保证.二、零件加工工艺设计(一)确定毛坯的制造形式零件材料为HT200.考虑到零件在机床运行过程中所受冲击不大,零件结构又比较简单,生产类型为大批生产,故选择铸件毛坯。
选用铸件尺寸公差等级CT9级,该拨叉生产类型为大批生产,所以初步确定工艺安排为:工序适当分散;广泛采用专用设备,大量采用专用工装。
(二)基面的选择基面的选择是工艺规程设计中的重要工作之一。
基面选择得正确与合理,可以使加工质量得到保证,生产效率得以提高。
(1) 粗基准的选择:以零件的底面为主要的定位粗基准,以两个小头孔外圆表面为辅助粗基准。
这样就可以达到限制五个自由度,再加上垂直的一个机械加紧,就可以达到完全定位。
(2)精基准的选择:考虑要保证零件的加工精度和装夹准确方便,依据“基准重合"原则和“基准统一”原则,以粗加工后的底面为主要的定位精基准,以两个小头孔内圆柱表面为辅助的定位精基准。
哈工大机械制造装备设计 大作业
= 7.858 ≤ 8~10,符合要求,其它变速组的变速范围也
5,绘制转速图
(1)选定电动机
根据设计要求,机床功率为 5.5KW,可以选用 Y132S-4,其同步转速为 1500r/min,满载 转速为 1440r/min,额定功率 5.5KW。
机械制造装备设计大作业——段泽军
(2)分配总降速传动比
《 机 械 制 造 装 备 设 计 》 课 程 ( 2015) 大作业
院(系) 专业 姓名 学号 班号 任课教师 完成日期
机电工程学院 机械制造及自动化 段泽军 1120810810 1208108 孙雅洲 2015 年 5 月 25 日
哈尔滨工业大学机电工程学院
2015 年 5 月
目录
目录 ............................................................................................................................ II 一,机床的规格及用途 ............................................................................................. 1 二,运动设计 ............................................................................................................. 1
1,确定极限转速 ...................................................................................................................... 1 2,确定公比������=1.41 ................................................................................................................. 1 3,确定主轴转速级数 Z=12 .................................................................................................... 1 4,确定结构式 .......................................................................................................................... 1 5,绘制转速图 .......................................................................................................................... 1 (1)选定电动机 ............................................................................................................... 1 (2)分配总降速传动比 ................................................................................................... 2 (3)确定传动轴的轴数 ................................................................................................... 2 (4)绘制转速图 ............................................................................................................... 2 6,确定变速组齿轮传动副的齿数.......................................................................................... 3 (1)速组 a: .................................................................................................................... 3 (2)速组 b: .................................................................................................................... 4 (3)速组 c: .................................................................................................................... 4 7,传动系统图 .......................................................................................................................... 4 8,校核主轴转速误差 .............................................................................................................. 4
- 1、下载文档前请自行甄别文档内容的完整性,平台不提供额外的编辑、内容补充、找答案等附加服务。
- 2、"仅部分预览"的文档,不可在线预览部分如存在完整性等问题,可反馈申请退款(可完整预览的文档不适用该条件!)。
- 3、如文档侵犯您的权益,请联系客服反馈,我们会尽快为您处理(人工客服工作时间:9:00-18:30)。
哈工大机械制造大作业一、零件分析题目所给的零件是CA6140车床的拨叉。
它位于车床变速机构中,主要起换档,使主轴回转运动按照操作者的要求工作,获得所需的速度和扭矩的作用。
零件上方的孔与操纵机构相连,二下方的Φ55叉口则是用于与所控制齿轮所在的轴接触,拨动下方的齿轮变速。
其生产纲领为批量生产,且为中批生产。
图1-1 CA6140拨叉零件图二、零件的工艺分析零件材料采用HT200,加工性能一般,在铸造毛坯完成后,需进行机械加工,以下是拨叉需要加工的表面以及加工表面之间的位置要求:1、小头孔Φ25:该加工面为内圆面,其尺寸精度要求为;2、叉口半圆孔Φ55:该加工面为内圆面,其尺寸精度要求为;3、拨叉左端面:该加工面为平面,其表面粗糙度要求为,位置精度要求与内圆面圆心距离为;4、叉口半圆孔两端面,表面粗糙度要求为,其垂直度与小头孔中心线的垂直度为;5、拨叉左端槽口,其槽口两侧面内表面为平面,表面粗糙度要求为,其垂直度与小头孔中心线的垂直度为0.08mm。
6、孔圆柱外端铣削平面,加工表面是一个平面,其表面粗糙度要求为。
三、确定毛坯1、确定毛坯种类:零件材料为,查阅机械制造手册,有,考虑零件在机床运行过程中受冲击不大,零件结构又比较简单,故选择铸造毛坯。
图3-1 毛坯模型2、毛坯特点:(1)性能特点:(2)结构特点:一般多设计为均匀壁厚,对于厚大断面件可采用空心结构。
CA6140拨叉厚度较均匀,出现疏松和缩孔的概率低。
(3)铸造工艺参数:铸件尺寸公差:铸件公称尺寸的两个允许极限尺寸之差成为铸件尺寸公差。
成批和大量生产采用金属型时,铸钢和铸件尺寸公差等级为级,选择尺寸公差等级为CT8。
机械加工余量:查阅参考文献[5],铸铁件的加工余量等级为E、F、G,故设计铸件公差为。
最小铸出孔:由于孔深为,孔壁厚度为,此时灰铸铁的最小铸出孔直径大于,故孔不铸出,采用机械加工的方法加工。
3、毛坯尺寸的确定:图3-2如图所示,现对图中1、2、3、4处加工面进行余量计算。
毛坯加工工艺方法选择金属型铸造,GB6414/86,公差等级选择8级。
所以,铸件基本尺寸根据计算以及查表所得数据可以得到:①左端面到的基本尺寸及公差:,圆整之后,取基本尺寸和公差为;②的内圆基本尺寸及公差:,圆整之后,取基本尺寸和公差为;③圆端面到底部大平面基本尺寸及公差:,圆整之后,取基本尺寸和公差为;④孔两端面基本尺寸及公差:,圆整之后,取基本尺寸和公差为。
四、选择定位基准基面选择是工艺规程设计中的重要工作之一。
基面选择的正确与合理,可以使加工质量得到保证,生产效率得到提高。
否则,加工工艺过程中就会问题百出,甚至会造成零件大批报废。
1、粗基准的选择:按有关基准的选择原则,即当零件有不加工表面时,应以这些不加工表面作为粗基准;若零件有若干不加工表面时,则应以加工表面要求相对位置精度较高的不加工表面做粗基准。
现以零件的底面作为定位的粗基准。
2、精基准的选择:考虑要保证零件的加工精度和装夹准确方便,依据“基准重合”原则和“基准统一”原则,叉口两端面与孔中心线的垂直度误差为0.1mm;槽口端面与孔中心线的垂直度误差为0.08mm,故以孔为精基准。
五、工序的安排1、加工方法的选择(1)孔是配合面,又是其他加工表面的基准,其终加工是铰孔,其前面的工步则是钻孔、扩孔。
(2)叉口内圆终加工可用半精铣或半精镗,其前面的工步则是粗铣或粗镗;(3)叉口侧面终加工可用半精铣,其前面的工步则是粗铣;(4)叉口断面用铣刀切断;(5)拨叉左端面终加工可用精铣,前面的工步则是粗铣、半精铣;(6)槽口终加工可用精铣,其前面的工步则是粗铣、半精铣;(7)孔外圆平面可以用粗铣达到表面质量要求。
2、机械加工工序(1)遵循“先基准,后其他”原则,首先加工精基准;(2)遵循“先粗后精”原则,先安排粗加工工序,后安排精加工工序;(3)遵循“先面后孔”原则。
3、热处理工序铸造成型后,进行调制处理。
4、辅助工序粗精加工工序之间,应安排去应力退火、去毛刺和中间检验工序。
六、制定工艺路线制定工艺路线应以零件的几何形状、尺寸精度和位置精度等技术要求得到保证为出发点。
在生产纲领以确定为中批量生产的条件下,可以考虑采用万能机床配以专用工、夹具,尽量是工序集中来提高生产效率。
除此以外,还应当考虑经济效果,以便使生产成本尽量下降。
1、工艺路线一2、工艺路线二3、工艺路线比较与分析上述两个方案的特点:方案一是先加工圆与两个内孔,并把这两步放在一个工序中,利用夹具和夹具上的定位元件保证以保证内孔和孔的相对位置精度。
在后续加工时,以内孔为精基准,保证后续加工精度,并利用了两件合铸的优势,提高了工作效率;方案二与方案一不同之处在于是先加工内孔,使之达到要求精度,然后再利用一锥销保证内孔和孔的相对位置精度,工序上不如方案一效率高,但是在可操作性上面比方案一略高。
可以将工序定为:七、机械加工余量、工序尺寸的确定CA6140车床拨叉,零件材料为HT200,硬度190~210HB,毛坯重量约为1.1kg,生产类型为中批量生产,铸造毛坯。
根据以上原始资料及加工工艺,分别确定各加工表面的机械加工余量、工序尺寸及毛坯尺寸如下:(1)由于工件较小,为方便加工节省材料将两件铸在一起,同时加工。
按《机械制造工艺设计简明手册》(后称文献[10])表2.2-1查得铸件在长度最大方向公差尺寸CT=2.2mm,同理可查得外圆轴线方向CT=1.6mm;大头孔CT=1.4mm;外圆轴线方向CT=1.1mm。
根据文献[10]表2.2-4按8F标准查得机械加工余量MA分别为2.0mm、2.0mm、1.5mm (双边余量)、2.0mm。
根据文献[10]图2.2-1及图2.2-2可以得出毛坯各尺寸,经过圆整后得出尺寸如下:(2)铸件的圆角半径,按文献[10]表2.2-9金属型铸造圆角公式,对于黑色金属有。
故选取R=3~5mm。
按表2.2-8选取拔模斜度外表面内表面自然时效处理以消除铸造应力。
(3)两内孔,考虑其孔径较小铸造困难,为简化铸造毛坯外型,现直接将圆柱铸成实心的。
(4)铣φ40端面加工余量及公差。
两φ40圆柱端面为自由尺寸和公差,表面粗糙度没有明确要求,考虑切除铸造缺陷区及提供定位精基准的需要,进行一步粗铣,根据表2.2-4查得加工余量MA=2.0mm。
又因为公差CT=1.6,根据毛坯尺寸,工序余量Z=3mm。
(5)镗φ55内孔毛坯为铸孔,内孔精度要求IT13表面粗糙度为Ra3.6,可以一次粗镗成所需的尺寸,得出工序余量2Z=4.4mm,Z=2.2mm。
(6)钻扩绞两孔φ25两内孔精度要求IT7参照文献[10]表2.3-8确定工序尺寸及工序余量为:钻孔:φ23扩孔:φ24.8 2Z=1.8mm粗绞:φ21.94 2Z=0.14mm精绞:(7)铣断(8)铣φ55孔两端面圆柱φ55圆柱两端面距离为(IT12),表面粗糙度值要求为Ra3.2,与孔有垂直度要求。
故可以考虑用组合铣刀一次铣削成型。
φ55铣削的加工余量MA=2.0mm,根据毛坯尺寸可以得出Z=2.5mm。
(9)铣小头凸台面为简化毛坯模具,16mm×8mm的方槽最初并不铸出,则小头孔凸台仅需留出面铣加工余量,包括粗铣和半精铣两部分。
根据文献[12]表2-36及毛坯尺寸,可得:粗铣工序余量Z=2.5mm半精铣工序余量Z=1.0mm(10) 铣16mm×8mm方槽因为槽的底面深度8mm没有公差要求,表面粗糙度为Ra6.3,两侧面距离为粗糙度Ra3.2,故可以分为粗铣和精铣。
首先选用的直柄立铣刀铣出的槽,然后选用专用刀具铣出所需的槽。
根据文献[12]表2-36及毛坯尺寸,可得:粗铣工序余量Z=8mm半精铣工序余量2Z=2.0mm(11)铣φ40外圆上的45°平面直接从φ40圆柱面上铣出平面即可。
八、确立切削用量及基本工时工序一、铣两处端面1.加工条件工件材料:HT200,,铸造;加工要求:粗铣端面,加工余量3.0mm;机床:X51立式铣床;刀具:YG6硬质合金端铣刀。
铣削宽度a e≤90,深度a p≤6,齿数z=12,故根据文献[10]表3.1,取刀具直径d0=125mm。
根据《切削用量手册》(后称文献[11])表3.2,选择刀具前角γ0=0°后角α0=8°,副后角α0’=10°,刃倾角λs=-10°,主偏角Kr=60°,过渡刃,副偏角Kr′=5°。
2.切削用量1)确定切削深度a p因为余量较小,故选择a p=3.0mm,一次走刀即可完成。
2)确定每齿进给量f z由于本工序为粗加工,尺寸精度和表面质量可不考虑,从而可采用不对称端铣,以提高进给量提高加工效率。
根据文献[11]表3.5,使用YG6硬质合金端铣刀加工,机床功率为4.5kw(据文献[10]表4.2-35,X51立式铣床)时:f z=0.09~0.18mm/z,故选择:f z=0.18mm/z。
3)确定刀具寿命及磨钝标准根据文献[11]表3.7,铣刀刀齿后刀面最大磨损量为1.5mm;由于铣刀直径d0=125mm,故刀具使用寿命T=180min(据文献[10]表3.8)。
4)计算切削速度v c和每分钟进给量v f根据文献[11]表3.16,当d0=125mm,Z=12,a p≤7.5,f z≤0.18mm/z时,v t=98m/min,n t=250r/min,v ft=471mm/min。
各修正系数为:k MV= 1.0,k SV= 0.8。
切削速度计算公式为:其中,,,,,,,,,,,,,将以上数据代入公式:确定机床主轴转速:根据文献[10]表4.2-36,选择n c=210r/min,v f=400mm/min,因此,实际切削速度和每齿切削量为:5)校验机床功率根据文献[11]表3.24,近似为Pcc=1.9kw,根据机床使用说明书,主轴允许功率Pcm=4.5×0.75kw=3.375kw>Pcc。
故校验合格。
最终确定:a p=3.0mm,n c=210r/min,v f=400mm/s,v c=82m/min,f z=0.159mm/z。
6)计算基本工时:t m=L/ v f,L=2 (l+ y+Δ),l=40mm.查文献[11]表3. 26,入切量及超切量为:y+Δ=47mm,则:t m=L/V f=2(40+47)/400=0.44min。
工序二、镗内孔1.加工条件:机床:T68卧式镗床刀具:硬质合金镗刀2.切削用量:单边切削余量:由文献[12]表5-30查得:,由文献[10]表4.2-21选取:由《简明手册》4.2-20选取:计算切削工时:工序三、钻扩铰两处孔1.钻孔:1)切削用量:机床选择:Z525立式钻床选择钻头:根据文献[11]表2.1、2.2,选择高速钢麻花钻钻头,粗钻时d o=23mm,钻头采用双锥后磨横刃,后角αo=12°,二重刃长度bε=4.5mm,横刃长度b=2.5mm, 弧面长度l=5mm,棱带长度,,。