叉车定期检验报告项目表
叉车定期检验(特种设备使用单位自行检查报告)

15
安全监控装置检查
(1)乘驾式电动叉车、电液换向的乘驾式内燃平衡重式叉车、电液换向的乘驾式内燃侧面式叉车应当设置司机坐(站)姿状态感知系统,当司机不在正常操作位置时, 车辆不能进行动力运行,即使操纵载荷装卸控制装置,也不应当出现门架的倾斜和货叉架的移动;当司机回到正常操作位置,但没有进行额外操作时,动力运行、门架的倾斜和货叉架的移动均不应当自动发生;
场(厂)内专用机动车辆
自检报告
使 用 单 位:
设 备 类 别:
设 备 品 种:
产 品 名 称:
产 品 型 号:
设 备 代 码:
车 牌 编 号:
使用登记证编号:
检 验 类 别:
检 验 日 期:
场(厂)内专用机动车辆自检报告
(叉车)
使用单位名称
使用单位地址
联系人
联系电话
统一社会信用代码
使用登记证编号
制造单位名称
10
液压系统检查
(1)液压管路布置与其他运动机件应当无相互干涉;
(2)液压系统固定接口应当无渗油,运动接口应当无漏油,各部位应当无泄漏现象。
11
制动系统检查
(1)应当具有行车、驻车制动系统,并且设置相应的制动装置;
(2)坐驾式叉车的行车制动与驻车制动系统应当由独立的装置进行操纵;
(3)站驾式和步驾式叉车应当带有一个制动装置,该装置应当自动闭合直到其被司机释放;
(4)驻车制动系统应当通过纯机械装置把工作部件锁止,手柄操纵的驻车制动控制装置应当有防止意外释放的功能;
12
电气和控制系统检查
(1)启动应当设置开关装置,需要由钥匙、密码或者磁卡等才能启动;
叉车定期检验分析报告

合格
42
(1)
货叉限位装置
符合
合格
43
B9
(2)
蓄电池叉车总电源应急断电装置
符合
合格
44
安全
(3)
护顶架
符合
合格
45
保护
(4)
步行式车辆安全换向器
符合
合格
46
(5)
车轮的防护装置
符合
合格
47
(1)
货叉架自然下滑量、门架倾角变化量
符合
合格
48
B10
(2)
货叉两叉尖高度差
符合
合格
49
工作
(3)
货叉或属具在叉架上的固定
叉车定期检验分析报告
报告编号:2009-02-CT5-67
叉车定期检验报告
使用单位:台州市正康木业有限公司
检验机构:台州市特种设备监督检验中心
检验日期:2009年02月23日
国家质量监督检验检疫总局制
叉车定期检验报告
报告编号:2009-02-CT5-67
共1页第4页
使用单位
台州市正康木业有限公司
制造单位
浙江杭叉工程机械股份有限公司
设备注册代码
出厂编号
叉车规格型号
CPC3L-C
额定重量
3T
发动机功率
4.5KW
检验依据:
1.《特种设备安全监察条例》(国务)
2.《厂内机动车辆安全检验技术要求》(GB/T16178-1996)
3.《前移式和插腿式叉车
稳定性基本试验》(GB/T5142-2005)
4.《前移式和插腿式叉车
符合
合格
34
(7)蓄电池叉车的制动连锁装置
叉车检验报告样本

叉车检验报告样本
报告编号:CC-20210101-001
检验时间:2021年1月1日
受检单位:ABC物流公司
受检车型:XXC501型叉车
检验结论
经过严格检验,车型XXC501型叉车的各项检测指标合格,无需进行修理或更换部件。
检验项目及结果
1.外观检查:车架结构完整,外表清洁,无明显变形或裂缝。
2.动力系统:发动机运转正常,无异响、无排气烟雾。
液压油
管路、电线路无泄漏。
3.制动系统:制动系统正常,制动距离符合要求。
4.悬挂系统:各部位无可见异常,悬挂系统处于正常工作状态。
5.轮胎及制动器:轮胎磨损度正常,制动器工作正常。
6.驾驶室及安全装置:驾驶室整洁有序,安全带、手制动器、
警示器正常工作。
结论
车型XXC501型叉车通过本次检验,各项检测指标均符合国家
及地方有关法规标准。
特此证明。
检验专家:
签字:
日期:2021年1月1日。
叉车定期检验报告

引言概述:
正文内容:
1.检查叉车整体状况:
检查叉车外观是否存在严重变形、裂纹等情况;
检查叉车的防护装置是否完好,如固定顶棚、保护栏等;检查叉车是否存在漏油、渗油等情况;
检查叉车胎压和轮胎磨损情况。
2.检查叉车驱动系统:
检查发动机的工作状况和排放情况;
检查叉车的传动系统,包括变速器和传动轴等;
检查叉车的电气系统,如电瓶、电线等;
检查叉车的液压驱动系统。
3.检查叉车悬挂系统:
检查叉车的悬挂弹簧、减震器等部件的状况;
检查叉车的悬挂系统是否存在异响等问题;
检查叉车悬挂系统的调校情况。
4.检查叉车制动系统:
检查叉车的制动踏板、制动片等部件是否磨损;
检查叉车制动系统的调整情况;
检查叉车的紧急制动功能是否正常。
5.其他重要部件的检查:
检查叉车的液压系统,如液压油的流动情况、液压缸的密封性等;
检查叉车的转向系统,包括转向机构和转向器的工作情况;
检查叉车的有效载荷和起重高度等参数的准确性;
检查叉车的操作手柄和控制系统是否灵敏。
总结:
通过本次叉车定期检验报告,我们详细介绍了叉车定期检验的相关内容。
从检查叉车整体状况,到检查叉车驱动系统、悬挂系统、制动系统以及其他重要部件,都涵盖了叉车的重要部分。
通过定期检验,可以及时发现叉车存在的安全隐患,并采取相应的措施进行修复和维护,以确保叉车的安全运行。
叉车定期检验是叉车维护保养的重要环节,也是确保人员和设备安全的重要措施。
叉车定期检验报告

叉车定期检验报告一、检验目的叉车作为一种常见的物流设备,在日常工作中承担着重要的货物搬运和仓储任务。
为了确保叉车的安全运行和正常使用,定期进行叉车的检验工作是必不可少的。
本报告旨在对叉车进行定期检验,并记录检验结果,以便于对叉车的安全性和性能进行评估。
二、检验内容1. 外观检查:包括检查叉车的整体外观是否完好、叉臂、车身和轮胎是否存在损坏或磨损等问题。
2. 功能检查:对叉车的各个功能部分进行检查,包括起升系统、行驶系统、制动系统和转向系统等,确保其正常运行。
3. 电子系统检查:检查叉车的电子部件,包括电池、电路、仪表盘和灯光等,以确保其正常工作和安全性。
4. 液压系统检查:检查叉车的液压部分,包括液压油箱、管道和阀门等,确保液压系统的正常工作和不漏油现象。
5. 安全装置检查:检查叉车的安全装置,包括警示灯、安全带和反撞装置等,以确保其完好并能正常工作。
6. 标志和标识检查:检查叉车上的安全标志和标识是否清晰可见,确保工作环境中的人员能够正确识别叉车的行驶方向和工作状态。
7. 环境适应能力检查:考察叉车在各种工作环境下的适应能力,包括噪声、震动、温度和湿度等。
三、检验结果根据上述检验内容,对叉车的不同部分进行了全面检查。
以下是对叉车定期检验的结果总结:1. 外观检查结果:叉车的外观整洁,无明显损伤或磨损,叉臂、车身和轮胎没有异常现象。
2. 功能检查结果:叉车的起升、行驶、制动和转向系统工作正常,操作灵活顺畅。
3. 电子系统检查结果:叉车的电子部件均正常工作,电池电量充足,仪表盘和灯光亮度正常。
4. 液压系统检查结果:叉车的液压系统无漏油现象,油箱和管道密封良好,阀门工作正常。
5. 安全装置检查结果:叉车的安全装置完好,警示灯亮度适宜,安全带可正常使用,反撞装置无缺失。
6. 标志和标识检查结果:叉车上的安全标志和标识清晰可见,易于识别叉车的行驶方向和状态。
7. 环境适应能力检查结果:叉车能够适应各种工作环境,无明显问题,噪声、震动、温度和湿度均处于正常范围。
叉车定期检验报告

叉车定期检验报告一、检验目的及背景叉车是一种用于搬运重物的特种设备,为了确保叉车的使用安全和性能正常,根据国家和行业相关要求,对叉车进行定期检验是必要的。
本报告对型号叉车进行了定期检验,旨在评估叉车的运行状况,发现问题并提出相应解决方案,以确保叉车的正常运行和使用安全。
二、检验对象及方法本次检验的对象型号50吨叉车,主要检验项目包括:外观检查、动力系统检查、操纵系统检查、制动系统检查、传动系统检查、液压系统检查、安全装置检查、故障码读取等。
检验方法主要采用目视检查、仪器检测、故障码读取等。
三、检验结果及分析1.外观检查:叉车外观整体良好,外壳无破损、变形等情况。
但发现座椅有明显磨损,应及时更换以提升驾驶员的舒适度和安全性。
2.动力系统检查:动力系统运行正常,动力输出稳定,发动机无异常噪声和排放问题。
然而,发现一些接头连接紧固松动,应重新紧固以防止松动导致的故障。
3.操纵系统检查:操纵系统操纵杆、控制阀等灵活可靠,动作准确。
但是,发现部分操纵杆阻塞,需进行润滑处理以减少操纵力。
4.制动系统检查:制动系统工作正常,刹车灵敏可靠。
但是,发现刹车片磨损严重,需要更换新的刹车片,以确保制动效果达标。
5.传动系统检查:传动系统传动效果良好,无明显异响和过热现象。
但是,发现传动链有松动现象,需要进行紧固和润滑处理。
6.液压系统检查:液压系统压力稳定,油液无泄漏迹象。
但是,发现一些液压管路存在老化和磨损现象,需要更换新的液压管路以提升系统的可靠性。
7.安全装置检查:安全装置齐全、有效。
但是,发现部分安全装置信号灯故障,应及时维修和更换。
8.故障码读取:通过故障码读取,未发现叉车存在重大故障。
四、存在问题及解决方案根据上述检验结果,本次检验发现了以下问题:1.座椅磨损严重,需更换新的座椅以提升驾驶员的舒适度和安全性。
2.部分接头连接松动,应重新紧固以防止松动导致的故障。
3.部分操纵杆阻塞,需进行润滑处理以减少操纵力。
叉车检验项目及其内容、方法和要求
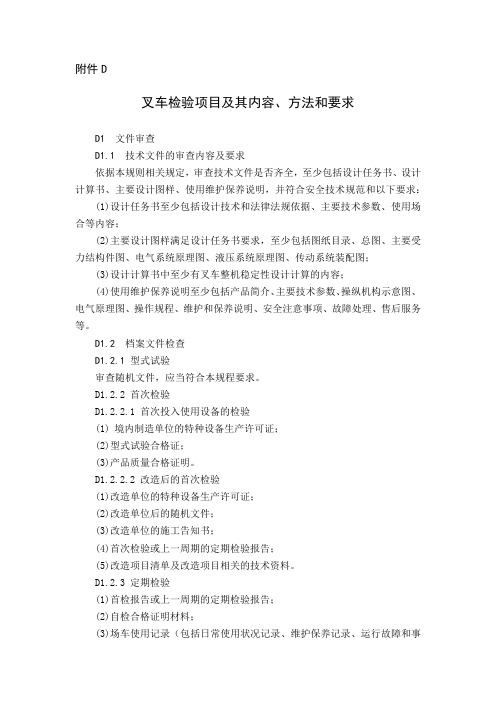
附件D叉车检验项目及其内容、方法和要求D1 文件审查D1.1 技术文件的审查内容及要求依据本规则相关规定,审查技术文件是否齐全,至少包括设计任务书、设计计算书、主要设计图样、使用维护保养说明,并符合安全技术规范和以下要求:(1)设计任务书至少包括设计技术和法律法规依据、主要技术参数、使用场合等内容;(2)主要设计图样满足设计任务书要求,至少包括图纸目录、总图、主要受力结构件图、电气系统原理图、液压系统原理图、传动系统装配图;(3)设计计算书中至少有叉车整机稳定性设计计算的内容;(4)使用维护保养说明至少包括产品简介、主要技术参数、操纵机构示意图、电气原理图、操作规程、维护和保养说明、安全注意事项、故障处理、售后服务等。
D1.2 档案文件检查D1.2.1 型式试验审查随机文件,应当符合本规程要求。
D1.2.2 首次检验D1.2.2.1 首次投入使用设备的检验(1)境内制造单位的特种设备生产许可证;(2)型式试验合格证;(3)产品质量合格证明。
D1.2.2.2 改造后的首次检验(1)改造单位的特种设备生产许可证;(2)改造单位后的随机文件;(3)改造单位的施工告知书;(4)首次检验或上一周期的定期检验报告;(5)改造项目清单及改造项目相关的技术资料。
D1.2.3 定期检验(1)首检报告或上一周期的定期检验报告;(2)自检合格证明材料;(3)场车使用记录(包括日常使用状况记录、维护保养记录、运行故障和事故记录等);(4)场车车牌;(5)使用登记证。
D2 检查与测量D2.1 结构型式型式试验时,检查样机的门架、护顶架、车架结构型式与主要设计图样是否一致。
首次检验时,检查设备的门架、护顶架、车架结构型式与主要设计图样或型式试验报告是否一致。
定期检验时,检查设备的门架、护顶架、车架结构型式与首检报告或主要设计图样是否一致。
D2.2 主要参数测量对照设计文件和产品对应标准,测量其起升高度、长度、宽度、高度及轴距、轮距、前悬距等主要尺寸,检查其结果是否符合标准要求。
叉车特种设备检查表
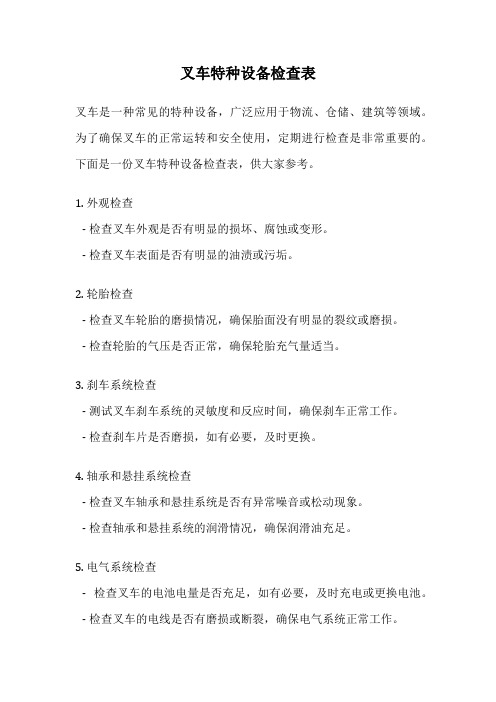
叉车特种设备检查表叉车是一种常见的特种设备,广泛应用于物流、仓储、建筑等领域。
为了确保叉车的正常运转和安全使用,定期进行检查是非常重要的。
下面是一份叉车特种设备检查表,供大家参考。
1. 外观检查- 检查叉车外观是否有明显的损坏、腐蚀或变形。
- 检查叉车表面是否有明显的油渍或污垢。
2. 轮胎检查- 检查叉车轮胎的磨损情况,确保胎面没有明显的裂纹或磨损。
- 检查轮胎的气压是否正常,确保轮胎充气量适当。
3. 刹车系统检查- 测试叉车刹车系统的灵敏度和反应时间,确保刹车正常工作。
- 检查刹车片是否磨损,如有必要,及时更换。
4. 轴承和悬挂系统检查- 检查叉车轴承和悬挂系统是否有异常噪音或松动现象。
- 检查轴承和悬挂系统的润滑情况,确保润滑油充足。
5. 电气系统检查- 检查叉车的电池电量是否充足,如有必要,及时充电或更换电池。
- 检查叉车的电线是否有磨损或断裂,确保电气系统正常工作。
6. 操作系统检查- 检查叉车的操纵杆、踏板等操作系统是否灵活,如有必要,及时调整或更换。
- 检查叉车的仪表盘是否正常显示各项指标,如有必要,及时修复或更换。
7. 灯光系统检查- 检查叉车的前灯、后灯、转向灯等灯光系统是否正常工作。
- 检查灯泡是否亮度均匀,如有必要,及时更换。
8. 安全装置检查- 检查叉车的安全带、防护栏等安全装置是否完好,如有必要,及时修复或更换。
- 检查叉车的警示标志是否清晰可见,如有必要,及时更换。
9. 定期维护和保养- 每次使用叉车后,及时清洁叉车,保持其干净整洁。
- 按照叉车制造商的要求,定期对叉车进行维护和保养。
10. 操作规范和培训- 操作叉车的人员应接受专业培训,掌握叉车的安全操作规范。
- 操作叉车时,应遵守相关的安全规定,确保人员和设备的安全。
以上是一份叉车特种设备检查表,通过定期对叉车进行检查,可以确保叉车的正常运转和安全使用。
同时,操作叉车的人员也应严格遵守操作规范,确保人员和设备的安全。
- 1、下载文档前请自行甄别文档内容的完整性,平台不提供额外的编辑、内容补充、找答案等附加服务。
- 2、"仅部分预览"的文档,不可在线预览部分如存在完整性等问题,可反馈申请退款(可完整预览的文档不适用该条件!)。
- 3、如文档侵犯您的权益,请联系客服反馈,我们会尽快为您处理(人工客服工作时间:9:00-18:30)。
稳定性基本试验》( GB/T5142-2005)
4.《前移式和插腿式叉车
整机试验方法》( JB/T3301-1992)
5.《前移式和插腿式叉车
技术条件》( JB/T2391-1994 0.5t~10t)
主要检验仪器设备:
1.游标卡尺 125mm,J-292-005
2.管形测力计 LTZ-20,J-292-004
符合
合格
12
B3
(1)发动机的安装
符合
合格
13
动力
(2)试发动机动力性能
符合
合格
系统
14
(3)点火系、燃料系、润滑系、冷却系
符合
合格
15
(1)离合器
符合
合格
16
B4
(2)变速器
符合
合格
17
传动
(3)传动系其它部件运转
符合
合格
18
系统
(4)液力传动叉车发动机的启动
符合
合格
19
(5)静压传动叉车发动机的启动
符合
合格
叉车定期检验报告项目表
报告编号:2009-02-CT5-67
共 4 页 第 4 页
序号
检验项目和内容
检验结果
检验结论
备注
55
(4)工作部件在额定速度范围的现象
符合
合格
56
(5)油泵、油马达情况
符合
合格
57
(6)操纵手柄(杆)情况
符合
合格
备注:
( 无此项 )
48
B10
(2)
货叉两叉尖高度差
符合
合格
49
工作
(3)
货叉或属具在叉架上的固定
符合
合格
装置
50
(4)
货叉的磨损、裂纹情况
符合
合格
51
(5)
链条、销轴、锁止机件
符合
合格
52
B11
(1)液压系统密封性能、裂纹和漏油现象
符合
合格
53
液压
(2)液压管路的情况
符合
合格
54
系统
(3)安全阀、分配阀等功能元件情况
符合
合格
20
B5
(1)充气轮胎台面
符合
合格
21
(2)同一轴上的轮胎型号和花纹
符合
合格
行驶
22
(3)车架和前后桥、零部件的情况
符合
合格
系统
23
(4)轮辋、、轮胎螺母和半轴螺
符合
合格
24
B6
(1)转向及其助力器工作状态
符合
合格
转向
25
(2)转向力
符合
合格
系统
叉车定期检验报告项目表
报告编号:2009-02-CT5-67
符合
合格
33
(6)制动系统漏油、漏气和零部件脱落或失灵现象
符合
合格
34
(7)蓄电池叉车的制动连锁装置
符合
合格
35
(1)蓄电池叉车的蓄电池
符合
合格
36
B8
(2)电机控制电路
符合
合格
37
电器
(3)电源总开关
符合
合格
38
及灯
(4)置转向灯、制动灯
符合
合格
光系
39
(5)灯具的保护装置、安装、使用
符合
合格
统
40
共 2 页 第 4 页
序号
检验项目和内容
检验结果
检验结论
备注
1
B1
(1)产品质量合格证明
符合
合格
2
(2)定期检验报告、自行检查的记录、日常使用维护
技术
符合
合格
保养记录、故障和事故记录
文件
3
(3)维护保养和检查自查情况说明
符合
合格
审查
4
叉车使用登记、牌照
符合
合格
5
(1)有害环境作业的作业人员防护措施
符合
3.数字钳形表 DT-266,J-292-001
4.卷尺 5 m, J-292-007
备注:
(空白)
N
检验结论:
签发: 王朝明
审核: 张朋
检验:李瑞明
检验有效期到
2010 年 2 月 22 日
止,应在安全检验合格有效期届满前 1 个月向本中心提出
定期检验要求。
叉车定期检验报告项目表
报告编号:2009-02-CT5-67
共 3 页 第 4 页
序号
检验项目和内容
检验结果
检验结论
备注
26
B6
(3)转向机构的油、各连接及其有关部位情况
符合
合格
转向
27
(4)侧滑量值
符合
合格
系统
28
(1)行车制动和驻车制动装置
符合
合格
29
(2)最大制动效能
符合
合格
30
B7
(3)跑偏现象
符合
合格
31
制动
(4)自由行程
符合
合格
系统
32
(5)最大制动作用时的踏板力
合格
6
B2
(2)额定起重量标志、安全检验合格标志、发动机编
符合
合格
号
作业
7
(3)叉车整洁、车身、部件
符合
合格
环境
8
(4)驾驶室挡风玻璃,后视镜、雨刷器、仪表
符合
合格
和整
9
(5)叉车污染物排放、噪音
符合
合格
车外
(6)装载运输或行驶于有害环境的叉车的特殊安全
10
观
符合
合格
要求
11
(7)液化气燃料叉车的车用液化气瓶
(6)喇叭及其音量
符合
合格
41
(7)电动机运转、温升、防护罩
符合
合格
42
(1)
货叉限位装置
符合
合格
43
B9
(2)
蓄电池叉车总电源应急断电装置
符合
合格
44
安全
(3)
护顶架
符合
合格
45
保护
(4)
步行式车辆安全换向器
符合
合格
46
(5)
车轮的防护装置
符合
合格47(1)来自货叉架自然下滑量、门架倾角变化量
符合
合格
台州市正康木业有限公司
制造单位
浙江杭叉工程机械股份有限公司
设备注册代码
3210331000200902232
出厂编号
040405551
叉车规格型号
CPC3L-C
额定重量
3 T
发动机功率
4.5KW
检验依据:
1.《特种设备安全监察条例》(国务)
2.《厂内机动车辆安全检验技术要求》( GB/T16178-1996)
报告编号:2009-02-CT5-67
叉车定期检验报告
注册代码:3210331000200902232
使用单位:台州市正康木业有限公司
检验机构:台州市特种设备监督检验中心
检验日期:2009 年 02 月 23 日
国家质量监督检验检疫总局
报告编号:2009-02-CT5-67
共 1 页 第 4 页
使用单位