镍基合金的合金化原理
合金化原理
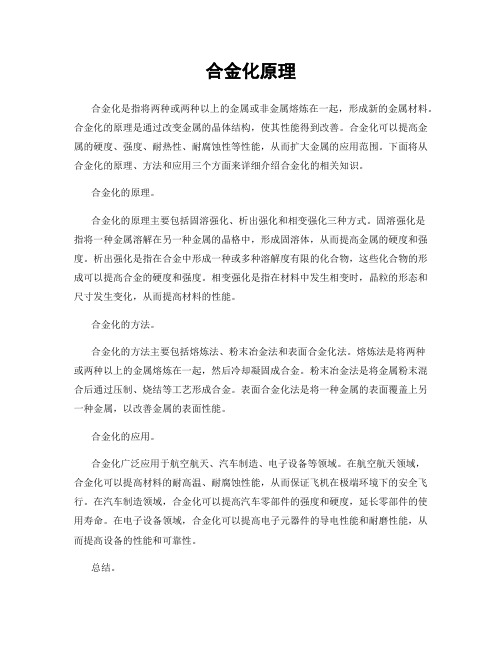
合金化原理合金化是指将两种或两种以上的金属或非金属熔炼在一起,形成新的金属材料。
合金化的原理是通过改变金属的晶体结构,使其性能得到改善。
合金化可以提高金属的硬度、强度、耐热性、耐腐蚀性等性能,从而扩大金属的应用范围。
下面将从合金化的原理、方法和应用三个方面来详细介绍合金化的相关知识。
合金化的原理。
合金化的原理主要包括固溶强化、析出强化和相变强化三种方式。
固溶强化是指将一种金属溶解在另一种金属的晶格中,形成固溶体,从而提高金属的硬度和强度。
析出强化是指在合金中形成一种或多种溶解度有限的化合物,这些化合物的形成可以提高合金的硬度和强度。
相变强化是指在材料中发生相变时,晶粒的形态和尺寸发生变化,从而提高材料的性能。
合金化的方法。
合金化的方法主要包括熔炼法、粉末冶金法和表面合金化法。
熔炼法是将两种或两种以上的金属熔炼在一起,然后冷却凝固成合金。
粉末冶金法是将金属粉末混合后通过压制、烧结等工艺形成合金。
表面合金化法是将一种金属的表面覆盖上另一种金属,以改善金属的表面性能。
合金化的应用。
合金化广泛应用于航空航天、汽车制造、电子设备等领域。
在航空航天领域,合金化可以提高材料的耐高温、耐腐蚀性能,从而保证飞机在极端环境下的安全飞行。
在汽车制造领域,合金化可以提高汽车零部件的强度和硬度,延长零部件的使用寿命。
在电子设备领域,合金化可以提高电子元器件的导电性能和耐磨性能,从而提高设备的性能和可靠性。
总结。
合金化是一种重要的金属材料改性方法,通过改变金属的组织结构和成分,可以显著提高金属材料的性能。
合金化的原理主要包括固溶强化、析出强化和相变强化三种方式,合金化的方法主要包括熔炼法、粉末冶金法和表面合金化法。
合金化广泛应用于航空航天、汽车制造、电子设备等领域,为各行业的发展提供了重要的支撑。
通过对合金化的原理、方法和应用的介绍,相信读者对合金化有了更深入的了解,也希望本文能够对相关领域的科研工作者和工程技术人员有所帮助。
镍基合金的焊接

镍基合金的焊接镍基合金是一种重要的高温合金材料,广泛应用于航空航天、能源和化工等领域。
在实际应用中,对镍基合金进行焊接是常见的操作。
本文将介绍镍基合金焊接的基本原理、常见焊接方法以及焊接后的质量控制。
1. 焊接原理镍基合金的焊接原理与其他金属焊接类似,主要包括焊接过程中的热传导、熔化、熔池形成和凝固等步骤。
镍基合金的焊接过程中,要注意控制焊接温度、合金组成、气氛保护和焊接速度等因素,以确保焊缝的质量和性能。
2. 常见焊接方法2.1 TIG焊接TIG(Tungsten Inert Gas)焊接是一种常见的镍基合金焊接方法。
该方法利用惰性气体保护焊接区域,使用钨极电弧使焊缝处达到高温,并通过手动给进填充材料来形成焊缝。
TIG焊接可用于焊接镍基合金的各种构件和板材,具有焊接热输入低、焊缝外观美观等优点。
2.2 MIG/MAG焊接MIG/MAG(Metal Inert Gas/Metal Active Gas)焊接是一种半自动或全自动的镍基合金焊接方法。
该方法利用惰性或活性气体的保护,在电弧中引入填充材料,使其熔化并充填焊缝。
MIG/MAG焊接适用于较大规模的焊接工作,具有高焊接速度、高效率的特点。
2.3 熔覆焊熔覆焊是一种常用的表面修复和保护方法,也可以用于镍基合金的焊接。
该方法通过熔融填充材料覆盖在母材表面,形成一层保护性涂层,提高构件的耐腐蚀性和耐磨性。
3. 质量控制焊接后的镍基合金构件需要进行质量控制以确保其性能和可靠性。
常见的质量控制方法包括焊缝的无损检测、金相组织分析、力学性能测试和耐腐蚀性检测等。
通过这些方法可以评估焊接接头的质量,确保其符合设计要求和使用要求。
结论镍基合金的焊接是一项复杂但重要的技术。
了解焊接原理、选择适当的焊接方法,并进行有效的质量控制,可以确保焊接接头的质量和性能。
同时,在焊接过程中要遵循相关的安全操作规程,以保障焊接人员的安全。
参考文献:1. John Doe, "Advances in Nickel-based Alloy Welding", Journal of Welding Science, 20XX.2. Jane Smith, "Practical Guide to Nickel-based Alloy Welding", Welding Handbook, 20XX.以上为我对镍基合金的焊接的文档内容,希望对您有所帮助。
热处理中的镍基合金热处理技术

热处理中的镍基合金热处理技术镍基合金是一种非常重要的金属材料,具有良好的耐热性、耐蚀性和抗氧化性能,广泛应用于航空、航天、化工等领域。
在镍基合金的制造和应用过程中,热处理技术起着重要的作用,可以有效地控制材料的性能和结构,提高其耐用性和可靠性,延长其使用寿命。
本文将对镍基合金的热处理技术进行详细介绍。
一、热处理的基本原理热处理是指在一定温度下和时间内对材料进行加热、保温和冷却等过程,以改变其性能和组织结构的工艺。
具体而言,热处理可以分为两个过程:加热过程和冷却过程。
在加热过程中,材料的晶粒逐渐长大,同时在内部形成一定的应力场,产生一系列的变形和相变。
在冷却过程中,这些应力和变形将得到释放和修复,材料的晶粒将重新调整和排列。
通过这些变化和调整,热处理可以使材料的性能得到显著的提高,从而满足不同领域的需求。
二、镍基合金的热处理工艺镍基合金是一种高强度、高温合金,其应用领域非常广泛。
在不同的使用环境下,镍基合金需要具有不同的性能和结构,因此需要进行不同的热处理工艺。
以下是几种典型的镍基合金热处理工艺。
1. 固溶处理固溶处理是镍基合金的常见热处理工艺之一,其主要目的是去除材料的金相或结构缺陷,使晶粒得到再生长和调整。
具体而言,固溶处理是指将材料加热到一定的温度,保温一定的时间,然后冷却至室温的工艺。
在固溶处理过程中,固溶温度的选择非常重要。
固溶温度过高将导致过度烧损和烧结,过低则无法达到固溶的效果。
通常情况下,固溶温度应选择在材料的升温和降温曲线上的峰值位置。
2. 锻造处理锻造处理是将镍基合金加热至通常超过其熔点的温度,然后通过机械锻造的方式改变材料的织构和结构,提高其性能和机械强度。
锻造处理可以使材料的晶粒得到细化和调整,从而达到提高其耐腐蚀性、耐热性和抗氧化性的目的。
3. 晶粒度控制处理晶粒度控制处理是指通过控制固溶和再结晶的温度和保温时间,调整材料的晶粒大小和分布,以提高其性能和可靠性。
通常情况下,细晶材料具有优异的力学、化学和物理性能,因此晶粒度控制处理是镍基合金的重要热处理技术之一。
镍基高温合金的强化原理

镍基高温合金的强化原理引言:镍基高温合金是一种具有优异高温力学性能的材料,被广泛应用于航空航天、能源和化工等领域。
其高温强化原理是该合金具有复杂的微观组织结构,其中包含了多种强化相,这些强化相通过不同的机制增强了合金的力学性能。
一、固溶强化镍基高温合金中的镍基固溶体是合金的主要组成部分,通过固溶强化可以提高合金的强度和硬度。
固溶强化是指通过将合金中的合金元素溶解到固溶体中,形成固溶体溶解度的限制,从而增强合金的力学性能。
固溶强化的效果受溶质元素浓度、溶解度和固溶体晶格结构等因素的影响。
二、析出强化镍基高温合金中的强化相主要是通过析出来增强合金的力学性能。
在合金的固溶体中,一些合金元素具有较低的溶解度,当合金冷却时,这些元素会从固溶体中析出形成强化相。
这些强化相的形态和尺寸对合金的强度和硬度起着重要的影响。
常见的强化相有γ'相、γ''相和硬质相等。
1. γ'相γ'相是一种具有面心立方结构的强化相,其组成为Ni3(Al, Ti)。
γ'相的形成可以通过固溶强化和析出强化两种机制。
固溶强化是指通过固溶体中的Al和Ti元素形成γ'相的过程,而析出强化是指通过在固溶体中析出Al和Ti元素形成γ'相的过程。
γ'相具有优异的力学性能,包括高强度、高硬度和良好的抗高温蠕变性能。
2. γ''相γ''相是一种具有体心立方结构的强化相,其组成为Ni3Nb。
γ''相的形成是通过在固溶体中析出Nb元素形成的。
γ''相具有良好的抗高温蠕变性能和高强度,但硬度相对较低。
3. 硬质相硬质相是指在镍基高温合金中析出的一些质量分数较低的元素形成的相,如硼化物、碳化物等。
硬质相具有高硬度和抗热腐蚀性能,可以有效提高合金的抗蠕变性能和抗热疲劳性能。
三、位错强化位错强化是指在晶格缺陷处形成的位错对合金的强化作用。
金属耐腐蚀合金化原理
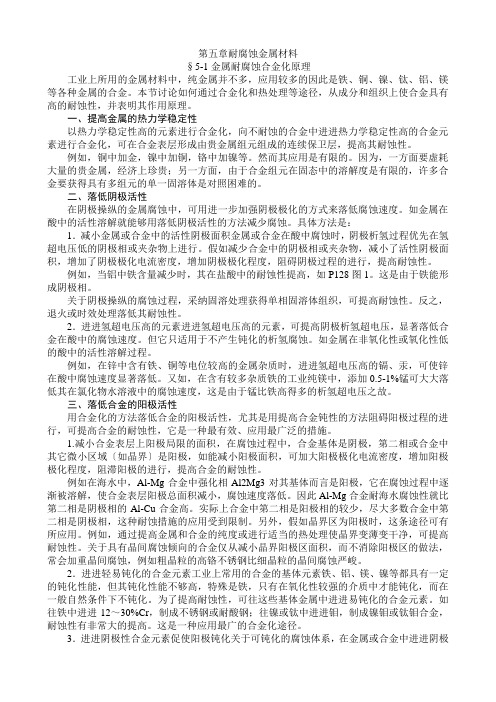
第五章耐腐蚀金属材料§5-1金属耐腐蚀合金化原理工业上所用的金属材料中,纯金属并不多,应用较多的因此是铁、铜、镍、钛、铝、镁等各种金属的合金。
本节讨论如何通过合金化和热处理等途径,从成分和组织上使合金具有高的耐蚀性,并表明其作用原理。
一、提高金属的热力学稳定性以热力学稳定性高的元素进行合金化,向不耐蚀的合金中进进热力学稳定性高的合金元素进行合金化,可在合金表层形成由贵金属组元组成的连续保卫层,提高其耐蚀性。
例如,铜中加金,镍中加铜,铬中加镍等。
然而其应用是有限的。
因为,一方面要虚耗大量的贵金属,经济上珍贵;另一方面,由于合金组元在固态中的溶解度是有限的,许多合金要获得具有多组元的单一固溶体是对照困难的。
二、落低阴极活性在阴极操纵的金属腐蚀中,可用进一步加强阴极极化的方式来落低腐蚀速度。
如金属在酸中的活性溶解就能够用落低阴极活性的方法减少腐蚀。
具体方法是:1.减小金属或合金中的活性阴极面积金属或合金在酸中腐蚀时,阴极析氢过程优先在氢超电压低的阴极相或夹杂物上进行。
假如减少合金中的阴极相或夹杂物,减小了活性阴极面积,增加了阴极极化电流密度,增加阴极极化程度,阻碍阴极过程的进行,提高耐蚀性。
例如,当铝中铁含量减少时,其在盐酸中的耐蚀性提高,如P128图1。
这是由于铁能形成阴极相。
关于阴极操纵的腐蚀过程,采纳固溶处理获得单相固溶体组织,可提高耐蚀性。
反之,退火或时效处理落低其耐蚀性。
2.进进氢超电压高的元素进进氢超电压高的元素,可提高阴极析氢超电压,显著落低合金在酸中的腐蚀速度。
但它只适用于不产生钝化的析氢腐蚀。
如金属在非氧化性或氧化性低的酸中的活性溶解过程。
例如,在锌中含有铁、铜等电位较高的金属杂质时,进进氢超电压高的镉、汞,可使锌在酸中腐蚀速度显著落低。
又如,在含有较多杂质铁的工业纯镁中,添加0.5-1%锰可大大落低其在氯化物水溶液中的腐蚀速度,这是由于锰比铁高得多的析氢超电压之故。
三、落低合金的阳极活性用合金化的方法落低合金的阳极活性,尤其是用提高合金钝性的方法阻碍阳极过程的进行,可提高合金的耐蚀性,它是一种最有效、应用最广泛的措施。
镍基高温合金材料的研究进展

镍基高温合金材料的研究进展一、本文概述镍基高温合金材料作为一种重要的金属材料,以其出色的高温性能、良好的抗氧化性和优异的力学性能,在航空航天、能源、化工等领域具有广泛的应用。
随着科技的快速发展,对镍基高温合金材料的性能要求日益提高,其研究进展也备受关注。
本文旨在全面综述镍基高温合金材料的最新研究进展,包括其成分设计、制备工艺、组织结构、性能优化以及应用领域等方面,以期为未来镍基高温合金材料的进一步发展提供理论支持和指导。
本文首先介绍了镍基高温合金材料的基本概念和特性,概述了其在不同领域的应用现状。
随后,重点分析了镍基高温合金材料的成分设计原理,包括合金元素的选取与配比,以及如何通过成分调控优化材料的性能。
在制备工艺方面,本文介绍了近年来出现的新型制备技术,如粉末冶金、定向凝固、热等静压等,并探讨了这些技术对材料性能的影响。
本文还深入探讨了镍基高温合金材料的组织结构特点,包括相组成、晶粒大小、位错结构等,并分析了这些结构因素对材料性能的影响机制。
在性能优化方面,本文总结了通过热处理、表面处理、复合强化等手段提高镍基高温合金材料性能的研究进展。
本文展望了镍基高温合金材料在未来的发展趋势和应用前景,特别是在新一代航空航天发动机、核能发电、高温传感器等领域的应用潜力。
通过本文的综述,旨在为相关领域的研究人员和企业提供有益的参考和借鉴,推动镍基高温合金材料的进一步发展和应用。
二、镍基高温合金的基础知识镍基高温合金,也称为镍基超合金,是一种在高温环境下具有优异性能的特殊金属材料。
它们主要由镍元素组成,并添加了各种合金元素,如铬、铝、钛、钽、钨、钼等,以优化其热稳定性、强度、抗氧化性、抗蠕变性和耐腐蚀性。
镍基高温合金的这些特性使其在航空航天、能源、石油化工等领域具有广泛的应用。
镍基高温合金之所以能够在高温环境下保持优异的性能,主要得益于其微观结构的特殊性质。
这些合金在固溶处理和时效处理后,会形成一系列复杂的金属间化合物,如γ'、γ''和γ'″等,这些化合物在基体中弥散分布,起到了强化基体的作用。
合金化原理的应用

合金化原理的应用1. 简介合金化是指通过将两种或多种金属进行熔炼、混合或固相反应,使其形成一个新的金属系统的技术过程。
它利用不同金属之间的原子间相互作用,通过特定的工艺条件,使合金具有优异的性能。
合金化技术在材料科学、工程技术和制造业等领域有广泛的应用。
2. 合金化的种类合金化可以分为两类,包括固溶体合金化和化合物合金化。
2.1 固溶体合金化固溶体合金化是指通过将两种或多种金属溶解在一起,形成具有均匀分布的晶格结构的合金。
它可以通过固溶体混合、固溶体反应等方式进行。
固溶体合金化常用来改善材料的机械强度、耐蚀性、耐热性等性能。
固溶体合金化的常见应用包括: - 不锈钢的制备:将铁、铬、镍等元素进行固溶体合金化,可生成不锈钢,具有优异的耐腐蚀性能; - 铝合金的制备:将铝与其他金属(如铜、镁、锌等)进行固溶体合金化,可获得强度高、耐腐蚀性好的铝合金材料。
2.2 化合物合金化化合物合金化是指两种或多种金属元素之间形成化学化合物的过程。
在化合物合金中,金属元素的原子结合形式是固定的,有着严格的比例。
化合物合金常用来改善材料的导电性、磁性、光学性能等。
化合物合金化的常见应用包括: - 磁性材料的制备:将铁、镍、钴等金属与其他元素形成化合物合金,可获得具有特定磁性的材料,如永磁材料; - 半导体材料的制备:将硅、锗等半导体元素与其他金属形成化合物合金,可获得具有特定电学性能的材料,如硅锗合金。
3. 合金化的应用案例3.1 钢材中的合金化钢是一种由铁和碳组成的合金材料,通过在钢中添加其他金属或非金属元素,可以改变钢材的性能。
常见的钢材合金化应用包括: - 不锈钢:通过在钢中添加铬、镍等元素进行固溶体合金化,使钢具有耐腐蚀性能; - 高速钢:通过在钢中添加钨、钼等元素进行固溶体合金化,使钢具有高温硬度和耐热性能; - 合金结构钢:通过在钢中添加硅、锰等元素进行化合物合金化,使钢具有特定的力学性能。
3.2 铝合金中的合金化铝合金是由铝为基体,通过与其他金属形成固溶体合金或化合物合金进行合金化改性的材料。
金属冶炼中的合金化技术

扩大应用领域
合金化技术使金属材料能够适应更广泛的应用场景 ,如航空航天、汽车、能源等领域,提高了金属材 料的应用价值。
促进技术创新
合金化技术的发展推动了相关领域的技术进 步和创新,如冶金、铸造、加工等,为工业 生产带来了更多的可能性。
要点一
高温合金
用于制造燃气轮机叶片、核反应堆结构件等关键部件,具 有优异的高温强度和抗疲劳性能。
要点二
不锈钢的合金化
通过添加合金元素,提高不锈钢的耐腐蚀性和强度,用于 制造电力设备的结构件和管道。
CHAPTER 05
合金化技术的发展趋势和挑战
高性能合金的研发
01
02
03
高强度、高韧性
通过合金化技术,研发出 具有高强度、高韧性的合 金材料,以满足各种工程 应用的需求。
浇注
将熔炼好的合金液体浇注入模具中,冷却凝固后形成合金铸件。
热处理和加工
热处理
通过加热、保温和冷却等工艺条件,调整合 金的组织结构,提高其力学性能和耐腐蚀性 能。
加工
对铸件进行机械加工,如切削、钻孔、铣削 等,以满足不同零件的形状和尺寸要求。
CHAPTER 04
合金化技术的应用场景
航空航天领域
CHAPTER 03
合金化技术的工艺流程
配料和混合
配料
根据合金的性能要求,选择合适的金属 元素作为原料,并按照一定比例进行配 料。
VS
混合
将配料好的金属元素进行充分混合,确保 各组分在合金中分布均匀,以提高合金的 均匀性和稳定性。
熔炼和浇注
熔炼
将混合好的原料加热至熔化状态,形成均匀的合金液体。
- 1、下载文档前请自行甄别文档内容的完整性,平台不提供额外的编辑、内容补充、找答案等附加服务。
- 2、"仅部分预览"的文档,不可在线预览部分如存在完整性等问题,可反馈申请退款(可完整预览的文档不适用该条件!)。
- 3、如文档侵犯您的权益,请联系客服反馈,我们会尽快为您处理(人工客服工作时间:9:00-18:30)。
五.镍基合金的合金化原理1.镍基耐热合金的合金化原理镍基耐热合金是最重要的一种高温合金。
随着喷气技术和新型动力机械的发展,在飞机、火箭、造船、煤碳地下气化和热能利用等方面,均得到广泛的应用。
(1)合金元素在镍基耐热合金合金相中的分布和作用镍基耐热合金是在高温、高压、高速和强烈的腐蚀环境下工作的,既要求高的强度和抗蠕变性能,还要求优秀的抗氧化和燃气(热)腐蚀的能力,是合金化但固溶强化作用最强的元素是W、Mo、Cr、Al 在γ相中溶解度较小,但固溶强化作用却很强,Fe、Co、V、Ti 的固溶强化作用较弱。
W 和Mo 等能提高奥氏体的原子间结合强度,降低层错能,阻碍位错的横(交)滑移,不仅它们本身的扩散系数低,在900℃还能降低Cr 和Ti 的扩散系数,故能强烈提高高温强度和抗蠕变性能。
另外,固溶于基体中的W 或Mo 还能促进γ′相的沉淀,增大基体的晶格常数,调整γ-γ′相间的错配度,形成晶界碳化物,对合金的抗蠕变性能也起积极作用。
Cr 也起固溶强化作用,但更主要的作用是改善抗氧化性能,形成的碳化物对晶界强化也有贡献。
Ni 基耐热合金的主要强化相是面心立方晶格的A3B(Ni3Al)型化合物γ′相,主要合金元素是Ti 和Al,化学式是Ni3(Al、Ti),有Co 存在时可用(Ni•Co)3(Al•Ti)表示。
γ′相的晶格与基体γ相相同,错配度很小(0.05~1.0%),界面能极低,两者间能长期保持共格关系,故有高的高温稳定性,γ′相不易吞并长大。
γ′相另一优点是强度随温度的升高(800℃以下),不仅不降低,反而升高,塑性也较高,不会出现严重脆化现象。
这点与碳化物强化相不同,不会因形成σ相Laves 相而引起脆化现象。
另外,位错切割γ′相时,产生同原子间键和反相畴界(APB)而使反相畴界能升高,对合金的沉淀硬化也有贡献。
进入强化相γ′中的元素除了Ti 以外,还有Co、Fe、Nb、Ta、V 或W、Mo 等,其中带负电性的Co 或Fe 等主要代替Ni 而进入A3B 化合物的A 组元,带正电性的Ti、Nb、Ta、V 等多代替Al 而进入组元B 中。
这些元素对组元A 或B 置换的结果,γ′相的组成更加复杂,特别是W 和Mo 的进入,对γ′相的HB 和“APB 能”的影响更大。
晶界强化元素中碳的作用是不可忽视的,Ni 基耐热合金通常均含有0.05~0.2%C(表1-10),能与活性元素和碳化物形成元素形成一次碳化物MC。
MC 在热处理或工作温度中能发生下述反应MC +γ→M 23C6 +γ′或 MC +γ→M6C +γ′通过这种反应生成的M 23C6 和M6C 型低碳化合物仍分布于晶粒间界,能阻碍晶界滑移和提高断裂强度。
另外,生成的γ′相均包覆在块状M 23C6 或M6C 型脆性碳化物周围和分布于晶界两侧,形成塑性较好的包覆层,有利于高温性能的提表面活性元素B、Zr、Ce(RE)是众所周知的晶界强化元素,形成Cr23(B、Ce 同时加入,能更有效地延续沿晶断裂。
Mg 和RE(La 和Nd)对持久强度和塑性也有明显的影响,Ni-21.5Cr-33.5Co-4Mo-2Nb-2.5Ti-0.2Al-0.05C 合金加入0.049%Mg,持久寿命(650℃,700MPa)可由155h 提高到422h,δ由9.5~17%提高到28%。
铪(Hf)对Ni基合金室温和高温机械性能的提高作用也极明显,Udimet 合金(Ni-15Cr-18.5Co-5.2Mo-3.5Ti-4.25Al-0.05B-0.15C)加入1.3-2.0%Hf,在760℃的持久寿命可成倍的提高。
Ni基合金的抗氧化和抗热腐蚀性能主要靠氧化物形成元素Cr 和Al 来提高,Ti也有一定的作用。
Cr 形成的富Cr2O3 保护膜,合金元素的阳离子空位少,能限制金属原子向外扩散和O、N、S 及其它腐蚀性气体向合金内部的扩散速度。
所以合金的Cr 含量≥20%,才有高的抗氧化性能。
Al 能形成富Al2O3 保护膜,抗氧化性能特别高,因此,Al 是高温合金沉淀硬化和抗氧化不可缺少的重要元素。
杂质Mn 应≤0.07~0.5%,Si≤0.60~0.8%;P、S、N 和O 等更应严加限制。
(2)工业用镍基耐热合金的合金化Ni 基耐热合金是在Ni-Cr 合金的基础上发展起来的。
NCr20 合金在1000~1100℃仍有相当高的抗氧化能力,室温强度也不(表1-11),但在800℃的持久强度(σ100)却很低,几乎与纯Ni 相同。
加入少量Ti 和Al,抗氧化能力不变,但高温强度却显著提高,这就是抗氧化的耐热合金GH3030。
GH3030 合金的Ti 和A1 含量分别提高到2.5%和0.75%,γ'相的体积分数增高,可以热处理强化,就变成了“尼莫尼克”(Nimonic)型合金GH32。
GH32 合金再加入0.005~0.015%B 和0.1%Ce,晶界得到了进一步强化,就变成了GH4033。
Nimonic 合金GH32 加入难熔金属W、Mo 或Nb,使之进一步固溶强化,提高再结晶温度,阻止γ'相吞并长大,耐热性也随之提高。
这就是复杂合金化的耐热合金GH4037 和GH3039。
GH4037 还提高了Al 含量,热强度和抗氧化能力都得到了改善;加入的V 对强度的影响不大,但能改善锻造性能。
Co 是奥氏体形成元素,除了降低层错能,起固溶强化作用外,还能促进γ'相的沉淀,阻碍γ'相长大,改善热加工性能、塑性和冲击性能。
Ni 基耐热合金的Co加入量一般控制在10~20%,英美的大多合金均加入Co,苏联的多数合金不加Co,只有工作温度>950℃的合金才加入Co。
我国早期研制的合金(GH3030、GH32、GH4033、GH4037、GH3039 等)不加Co,但新研制的合金如GH4049 等均加入13~22%Co,以提高耐热性和工作温度。
GH4049 是含Co 合金的代表牌号,是合金化程度很高的合金。
除了加入14~16%Co,还加入大量固溶强化元素W 和Mo,形成γ'相的Al 也增高,还加入晶界强化元素B 和RE(Ce)以及改善锻造性能的V。
GH4049 的组织也极为复杂,加Co 显著增加了(Ni,Co)3(Ti,Al)相的体积分数,还能形成碳化物(M6C)和硼化物(Me3B2)。
但主要强化相是γ',有大小两种尺寸分布于晶粒内部,大者为方块状(300~350nm),小者为球形(60~100nm),其次是碳化物M6C,呈细小的链状分布于晶粒间界内。
Cr 是改善合金抗氧化性能的主要元素,1965 年以前发展的合金含Cr 量较高(19~22%),但随合金化程度的提高,为了避免出现σ相,Cr 含量已被降低到10%左右,合金的强度虽然不断提高,但抗氧化和燃气腐蚀的能力却显著降低。
为了解决合金的抗热腐蚀问题,国外又发展了高Cr 合金(>20%或>30%Cr)。
国产合金Cr 含量的变化也大致如此。
从GH3030 到GH4170 合金的Cr 含量均为18~22%;但Cr 在GH4037合金中则降低到13~16%,在GH4049 合金中降到9.5~11%,在GH151 合金中降低到9.5~10.5%;而GH3044 合金中Cr 又提高到23.5~26.5%,抗氧化性能显著提高。
GH3044的Ti、A1 含量很低,不能热处理强化,只依靠W(13~16%)的固溶强化。
Ni 基耐热合金的高温强度主要靠γ'相的弥散硬化,为了发挥γ'相的强化作用,Al和Ti 的总含量或(Al+Ti+Nb+Ta)的总含量不断增加,国外的高性能Ni 基合金。
(Al+Ti)总含量已≥10%,(Al+Ti+Nb+Ta)的总含量已>16%,γ'相的沉淀量已高达60~70%。
所以,合金的持久强度也是随强化相形成元素或γ'相的增多而不断升高。
国产合金GH4033 的(A1+Ti)最高总含量只有3.8%,但发展到GH146 和GH118 则高温合金一直采用W、Mo 同时加入的办法,英美早期发展的合金只加Mo,后期发展的合金W、Mo 同时加,甚至于单纯加入大量W。
(W+Mo)的总加入量也没有一致的看法,有人认为(W+Mo)=10~15%较合适,也有人认为(W+Mo)=6~9%,W/Mo>2 为好。
英美新发展起来的合金,W/Mo≥5,(W+Mo)=13%。
我国的高温合金是吸收苏、美、英的经验而发展起来的,多数合金(GH4037、GH4049、GH3128和GH151 等)是W、Mo 同时加,有的合金只加Mo(如GH146、GH143、GH118 等),也有的合金只加大量W(如GH3044、GH170 等)。
国外的实验结果表明,(W+Mo)总含量愈高,合金的断裂温度(130MPa,100h)也愈高,当然还要考虑其它合金元素的影响。
表1-10 中列举的GH128 合金的(W+Mo)总含量最高(16.5%),但Ti 和Al 的含量(<0.8%)较低,热处理强化效应不大,只适于固溶强化;GH37 和GH49的(W+Mo)总量相同<10.5%),但GH4049 的(Al+Ti)总含量(5.7%)比GH37(4.1%)高,故耐热性也高;GH151 合金的(W+Mo)总含量只有9.8%,仅加入大量A1(6.0%),工作温度可以提高到950℃。
同理,添加大量W 的GH4044(13~16%W)和GH170(17~20%W),由于(Ti+Al)含量少(各<0.5%),不能热处理强化,只能固溶强化,但由于含有较高的Cr(≥20%),抗腐蚀性能和工作温度也能明显提高,但抗蠕变性能却不一定很高。
单独加Mo 的合金(GH146、GH143 和GH118 等),Mo含量虽不高(<6%),但加入大量的A1 和Ti(总量≈5.75~9%),固溶强化和沉淀硬化可以同时起作用,故仍有很高的耐热性。