染整加工降低缩水率的11大方法
面料后整理的20种方法

面料后整理的20种方法导语:面料后整理是面料出厂前的最后工序,也是必不可少的重要流程。
近几年来,面料后整理技术不断从其他技术领域引进借鉴各种新技术(如低温等离子体处理、生物工程、超声波技术、电子束辐射处理、喷墨印花技术、微胶囊技术、纳米技术等),以提高加工深度,获得良好的整理产品。
预缩预缩是用物理方法减少面料浸水后的收缩以降低缩水率的工艺过程。
机械预缩是将织物先经喷汽或喷雾给湿,再施以经向机械挤压,使屈曲波高增大,然后经松式干燥。
拉幅拉幅是利用纤维素、蚕丝、羊毛等纤维在潮湿条件下所具有的可塑性,将面料幅宽逐渐拉阔至规定尺寸进行烘干,使面料形态得以稳定的工艺过程,也称定幅整理。
上浆上浆是指面料浸涂浆液并烘干以获得手感厚实和硬挺效果的整理过程。
热定型热定型是使热塑性纤维及混纺或交织物形态相对稳定的工艺过程,主要用于受热后易收缩变形的锦纶或涤纶等合成纤维及其混纺物的加工。
经热定型的面料,能提高尺寸稳定性,手感较为硬挺。
增白增白是利用光的补色原理增加纺织品的白度的工艺过程,又称加白。
增白方法有上蓝和荧光增白两种。
轧光、电光和轧纹轧光是利用纤维在湿热条件下的可塑性将面料表面轧平或轧出平行的细密斜纹,以增进织物光泽的工艺过程。
平轧光是由硬辊和软辊组成硬轧点,面料经轧压后,纱线被压扁,表面光滑,光泽增强、手感硬挺。
软轧光是由两只软辊组成软轧点,面料经轧压后,纱线稍扁平,光泽柔和、手感柔软。
电光是使用通电加热的轧辊对面料轧光。
轧纹是由刻有阳纹花纹的钢辊和软辊组成轧点,在热轧条件下,面料可获得呈现光泽的花纹。
磨绒、磨毛用砂磨辊(或带)将面料表面磨出一层短而密的绒毛的工艺过程称为磨绒,又称磨毛,磨毛整理能使经纬纱同时产生绒毛,且绒毛短而密。
起毛起毛是用密集的针或刺将织物表层的纤维剔起,形成一层绒毛的工艺过程,又称拉绒整理,起毛主要用于粗纺毛织物、腈纶织物和棉织物等。
绒毛层可以提高面料的保暖性,改善外观并使手感柔软。
最常见的纺织面料缩水率及影响因素

书山有路勤为径;学海无涯苦作舟最常见的纺织面料缩水率及影响因素缩水是纺织品在一定状态经过洗涤、脱水、干燥等过程发生长度或宽度变化的一种现象。
缩水程度涉及不同种类的纤维、织物的结构、织物加工时所受之不同外力作用等等。
织物的缩水率是指织物在洗涤或浸水后织物收缩的百分数。
缩水率最小的是合成纤维及混纺织品,其次是毛织品、麻织品、棉织品居中,丝织品缩水较大,而最大的是粘胶纤维、人造棉、人造毛类织物。
客观的讲,全棉面料多少都存在着缩水褪色的问题,关键是后面的整理。
所以一般家纺的面料都是经过预缩处理。
值得注意的是经过预缩处理不等于不缩水,而是指缩水率控制在国标3%~4%以,内衣料尤其是天然纤维的衣料会缩水。
因此,在选购衣料时,除了对织物的质量、色泽、花型进行挑选外,对织物的缩水率也应当有所了解。
纤维及织缩的影响纤维本身吸水后,会产生一定程度的溶胀。
通常纤维的溶胀都是各向异性的(锦纶除外),即长度缩短,直径增大。
通常把织物下水前后的长度差与其原长的百分比称为缩水率。
吸水能力越强,溶胀越剧烈,缩水率越高,织物的尺寸稳定性越差。
织物本身的长度与所使用的纱(丝)线长度是不同的,通常用织缩率来表示两者的差异。
织缩率(%)= [纱(丝)线长度-织物长度] / 织物长度织物在下水后,由于纤维本身的溶胀,使织物长度进一步缩短,产生缩水率。
织物的织缩率不同,其缩水率的大小就不同。
织物本身的组织结构及织造张力不同,其织缩率就不同。
织造张力小,织物紧密厚实,织缩率大,织物的缩水率就小;织造张力大,织物就疏松轻薄,织缩率小,织物专注下一代成长,为了孩子。
棉针织物的防缩

针织物整理的目的是发挥针织物或给予针织物以新的性能,以满足人们的需要。
根据加工的性质,可将整理工艺分为二大类:一类为物理机械整理、防缩、起绒、热定型。
另一类为化学整理如树脂整理,特殊整理。
一、棉织物的防缩整理1、棉针织物缩水:在染整加工中,织物受到拉伸积累形变。
如果用这种积累形变的针织坯布缝制成衣,则一经水洗,织物积累的形变,就要回缩,就会发生不合比例的尺寸改变。
1.1 为了避免棉针织物缩水,可设想有两个途径a、理想流程:理布→缝头→常温溢流机染色→松式烘干机(无张力)→长规程(十节)开幅定型→无张力打卷机(或落布折叠包装)b、强迫回缩:润湿的织物受到振荡,施加相反的力,强迫织物回缩,才能使织物线圈恢复到理想的空间结构。
达到稳定产状态,然后维持这一状态进行烘干使之固定下来。
实验得知:回潮4% 细罗纹针织物在室温振动25分钟。
其收缩率仅为可回缩量的8%,而100%浸湿后在热空气中,振动20分钟,再室温振动5分钟,则回缩率可达67%。
2、防缩工艺及设备2.1 防缩工艺1:热定型防缩法,棉针织物不能采用。
2.2 防缩工艺2:棉纤维浓碱液和张力下可进行重整排列,以稳定其尺寸即所谓丝光处理。
2.3 机械防缩法:利用专门设备强迫织物预先回缩的方法。
a、机械防缩设备:按纵向强迫回缩的预缩机;按横向伸展预缩机b、超喂工艺:超喂湿扩幅,超喂烘干超喂预缩,超喂定型二、棉针织物的缩水率问题1、缩水率的测定1.1 掌握织物缩水率的测试方法及了解织物收缩原因。
1.2 仪器:水箱 M988型织物缩机,针织物2±R,量尺、缝线、铅笔。
1.3 实验程序(晾干缩水率)a、仪器与工具:M988型织物缩水机,转速500±20r/min 容量为40L,量尺。
b、试验条件:试液为清水,温度为45±2℃,浴比1:50。
试验时间:棉和合纤织物为30分钟。
+ + ++ + ++ + +c、试样准备:取样,需经热定型后24h,距布端2-5米处,数量不得少于2块。
怎样降低缩率

降低针织面料缩水率的方法(1)在针织物炼漂过程中尽量减小张力。
( 2)在针织物染整加工过程中,凡是湿布烘干都是尽量施松张力 降低伸长避免门幅过度窄缩 如果是开幅连烘的机台在开幅后要加装小的容布箱再穿进布架以避免开幅与轧水间张力过大。
(3)在针织物丝光过程中,要掌握扩幅张力要保持坯布的幅宽注意控制纬向张力。
(4)各道工序的平洗机导布棍,轧棍、烘筒应加强维修保证平整光洁。
避免张力放松时起皱水槽中的导辊要运转自如 同一机台前后轧辊烘筒的线速度相差不应太大 经向张力掌握布不拖地为准在长台的分段过程中应有松紧调节开降架装置或分段传动调节装置以控制张力的大小。
( 5)丝光后的产品应严格控制后道加工过程中的张力因为丝光后再伸长经向缩水率在实际生产操作中可以在各道工序中制定半制品幅宽指标在各机台的去布处于以测量考核 后序要对前工序进行验收保证半制品应有的幅宽。
( 6)对于一些机械运动张力需要人工控制张力。
严格工艺操作 加强工艺操作 加强机械清洁减小运转张力有效的降低织物的缩水率。
(7)加强对丝光加工工艺条件的检查 有条件的的染厂可以用直辊和布铗结合丝光。
(8)经向缩水率较大的品种:如卡其、华达呢府绸织物要进行预缩处理、降低缩水率。
在这些品种在紧式加工中。
仅依机械上放松张力 则最好的缩水率也高达4%左右 这一缩率宜采用预缩的办法来进一步降低 产品经过预缩处理后不但缩水率降低了。
同时还可以获得较好的手感 纹路清晰光泽柔和。
(9)对于纬向缩水率较大品种 有的由于坯布幅宽不合理 即使合理的加工条件也仍有较大的纬向缩水率加工条件差的缩水率更大 必须采取进一步改进措施丝光品种要保证落布幅宽达到要求。
此外还需要在坯布规格上加以改进 在不增加成本或少增加成本条件下 将坯布幅宽放宽 以保证纬向缩水率降到要求范围内。
(10)对于涤棉合纤混纺织物要抓好定性丝光工序工艺及操作可较好控制缩水率关于测缩率的方法先取1米长的面料,然后分别在面料的经向纬向上做好标记,一个角做2组标记,这样一共是4组标记一共是8个标记点,然后用尺分别量出经向标记点之间的距离和纬向标记点的距离,然后将布放入30±3°的温水中浸泡10分钟,取出布把布烘干然后在测量经纬向之间的距离,然后进行计算,计算的公式是(洗涤前距离-洗涤后距离)/洗涤前距离×100%,就能得到缩率。
布料为什么会缩水?如何减少缩水幅度?

布料为什么会缩水?如何减少缩水幅度?收缩水率和面料还有织物组织结构有关系:天然纤维如棉、毛、丝、麻的吸湿性相对较大,故缩水率也大;而丙纶、涤纶等化学纤维的吸湿性小,故缩水率也小。
织物结构的紧密、稀松也会影响其缩水程度,稀松结构的衣料,一般较紧密结构的缩水率大所以想买不缩水的衣服是不可能的而且尽量不要因为缩水率的原因买纯化纤的衣服,现在还是全棉的跟全羊毛的舒服。
但是注意点就可以减少缩水啦:1洗衣是尽量少加洗衣粉或洗衣液,适当用些金纺等柔软剂,会缩的少些。
2洗之前用淡盐水泡半个小时,然后再用凉水清洗,即可;对于已经缩水的衣服,可以将衣服套在大纸板上撑开,然后再用熨斗一熨,衣服可恢复原状。
(不建议用纸板撑哦,容易让衣服损坏或者变形)3干洗4缩水厉害的,看面料可以用蒸汽熨烫。
织物缩水机理织物的缩水问题,通常是经向缩水较为严重。
这主要与它们在染整加工过程中,经向经常处于紧张状态有关。
棉织物在加工过程中,由于纤维和纱(线)受到拉伸,特别在潮湿条件下,更易发生伸长,如果维持这种拉伸状态进行干燥,该状态就会被暂时定型,导致“干燥定型”形变,而存在着内应力。
当这种织物再度润湿时,由于内应力松弛,使纤维和纱(线)的长度缩短,而构成织物缩水。
但是根据对棉织物的伸长率和缩水率的测定,发现它们之间并无一一对应的关系,同时发现织物中具有正常捻度纱的缩水率很少超过2%,而棉布的缩水率有时却可高达10%。
显然,仅从纤维和纱的内应力松弛并不能说明棉布的缩水现象。
为了进一步弄清楚棉布的缩水机理,就有必要分析纤维、纱和织物在水中尺寸变化的情况。
棉纤维吸湿以后的溶胀异向性,已为大家所熟知,如果纤维中无内应力,即不具有“干燥定型”形变时,长度非但不会缩短,相反还要增长一些。
那么,如果纤维中存在着“干燥定型"形变,润湿后,长度将发生怎样的变化?表2—2列举了具有不同“干燥定型”形变的棉纤维,在再度润湿和干燥后的长度收缩情况。
可以看出“干燥定型”形变大的纤维,在再度润湿后的长度收缩也较多,但形变并不能全部消失。
防缩处理

防缩整理第一节引言经过染整加工后已干燥的织物,如果在松弛状态下再被水润湿时,往往会发生比较明显的收缩,这种现象称为缩水。
通常以织物按规定方法洗涤前后的经向或纬向的长度差,占洗涤前长度的百分率,来表示该织物的经向或纬向缩水率。
若用尺寸尚未稳定(也称为具有潜在收缩)的织物做成服装,经过洗涤,由于发生一定程度的收缩,会导致服装变形和走样,给使用者带来不少的困难和损失。
因此,织物的缩水现象早已受到人们的注意。
有些织物,除了有一般的缩水现象外,在一定的条件下洗涤时,由于机械作用,纤维会产生特殊的蠕动而相互纠缠,并使织物缩成紧密状态,这种收缩称为毡缩,通常可以面积变化的百分率来表示。
不同纤维制成的织物,它们的收缩情况不完全相同。
例如,某些毛织物不但在初次洗涤中,具有较大的收缩(称为初次收缩),而且,经过多次洗涤后,还会继续发生很大的收缩(称为后续收缩)。
棉和麻纤维织物的初次收缩虽然有时较大,但它们的后续收缩都不很高。
这些现象反映了不同纤维织物的收缩机理是不完全相同的。
有的可能是由于缩水和毡缩这两方面的因素所造成,也有的可能是其中之一。
羊毛织物除了具有一般的缩水现象外,还容易生毡缩,粘胶纤维织物也发现有类似的现象,纤维素纤维与合成纤维的混纺织物,经过热定型后,其缩水问题远不如纯纤维素纤维织物严重,这是由于大部分合成纤维的吸湿性较低的缘故。
此外,即使是由相同的纤维制成的织物,它们的收缩情况还与纱和织物的结构以及织物经过的加工过程有关。
本章主要讨论纤维素纤维织物缩水的机理和防缩整理方法以及毛织物的防毡缩整理。
第二节织物缩水机理织物的缩水问题,通常是经向缩水较为严重。
这主要与它们在染整加工过程中,经向经常处于紧张状态有关。
棉织物在加工过程中,由于纤维和纱(线)受到拉伸,特别在潮湿条件下,更易发生伸长,如果维持这种拉伸状态进行干燥,该状态就会被暂时定型,导致“干燥定型”形变,而存在着内应力。
当这种织物再度润湿时,由于内应力松弛,使纤维和纱(线)的长度缩短,而构成织物缩水。
染厂后整理技术(定型)
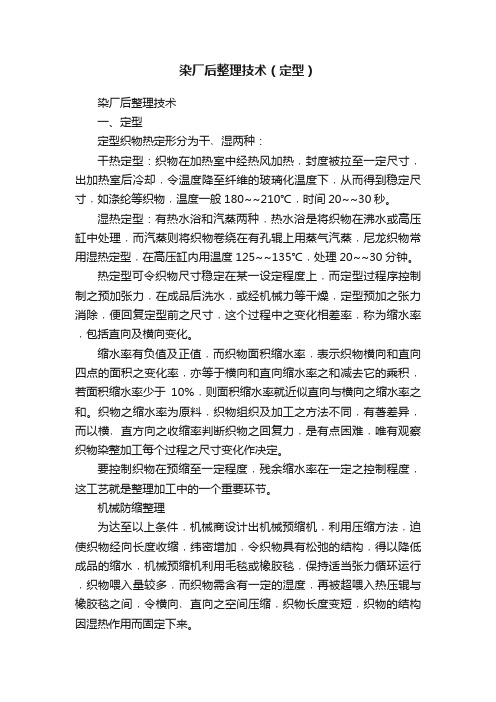
染厂后整理技术(定型)染厂后整理技术一、定型定型织物热定形分为干﹑湿两种:干热定型:织物在加热室中经热风加热﹐封度被拉至一定尺寸﹐出加热室后冷却﹐令温度降至纤维的玻璃化温度下﹐从而得到稳定尺寸﹐如涤纶等织物﹐温度一般180~~210℃﹐时间20~~30秒。
湿热定型:有热水浴和汽蒸两种﹐热水浴是将织物在沸水或高压缸中处理﹐而汽蒸则将织物卷绕在有孔辊上用蒸气汽蒸﹐尼龙织物常用湿热定型﹐在高压缸内用温度125~~135℃﹐处理20~~30分钟。
热定型可令织物尺寸稳定在某一设定程度上﹐而定型过程序控制制之预加张力﹐在成品后洗水﹐或经机械力等干燥﹐定型预加之张力消除﹐便回复定型前之尺寸﹐这个过程中之变化相差率﹐称为缩水率﹐包括直向及横向变化。
缩水率有负值及正值﹐而织物面积缩水率﹐表示织物横向和直向四点的面积之变化率﹐亦等于横向和直向缩水率之和减去它的乘积﹐若面积缩水率少于10%﹐则面积缩水率就近似直向与横向之缩水率之和。
织物之缩水率为原料﹐织物组织及加工之方法不同﹐有著差异﹐而以横﹑直方向之收缩率判断织物之回复力﹐是有点困难﹐唯有观察织物染整加工每个过程之尺寸变化作决定。
要控制织物在预缩至一定程度﹐残余缩水率在一定之控制程度﹐这工艺就是整理加工中的一个重要环节。
机械防缩整理为达至以上条件﹐机械商设计出机械预缩机﹐利用压缩方法﹐迫使织物经向长度收缩﹐纬密增加﹐令织物具有松弛的结构﹐得以降低成品的缩水﹐机械预缩机利用毛毯或橡胶毯﹐保持适当张力循环运行﹐织物喂入量较多﹐而织物需含有一定的湿度﹐再被超喂入热压辊与橡胶毯之间﹐令横向﹑直向之空间压缩﹐织物长度变短﹐织物的结构因湿热作用而固定下来。
进行预缩前﹐织物需给湿令纤维柔性增大﹐压缩控制于胶毯厚度和曲率变化大小﹐经此工序织物再洗水的缩率可降低至1%﹐手感亦较好。
控制缩水率的方法要多方面进行才能获得预期效果。
(1) 织物设定之规格是否符合基本之要求。
(2) 纱线之种类及缩率之变化。
染整问题总结

染整问题总结引言染整是纺织行业中重要的一个环节,主要负责将纱线、面料等进行染色、整理和处理,使其达到预期的色彩、质地和外观效果。
然而,在染整过程中经常会出现一些问题,影响产品质量和生产效率。
本文将对染整问题进行总结和分析,希望能够帮助相关从业人员尽快解决问题。
问题一:色差问题在染整过程中,色差是一个常见的问题。
染色后的纱线或面料与预期色彩存在一定的偏差,造成产品的色彩不稳定或不一致。
产生色差的原因可以归结为以下几点:1.配方不准确:染色配方中的染料浓度、PH值、时间等参数可能存在误差,导致染色结果与预期不符。
2.染色条件不合适:温度、湿度、搅拌速度等条件对染色结果有重要影响,不合适的条件可能导致色差问题。
3.染料质量问题:染料的质量差异也会导致染色结果不稳定,有些染料可能存在色牢度不高的问题,容易褪色或变色。
4.染色工艺控制不当:染色过程中搅拌、上浆、漂洗等环节的控制不当也会产生色差。
解决色差问题的方法包括加强配方管理,严格控制染色条件,选择高质量的染料和改进染色工艺等。
问题二:退色问题退色是指染色后的纱线或面料出现褪色现象,使得产品的颜色失去原有的鲜艳度。
退色的原因主要有以下几点:1.染料固定不牢:染料在染色后未完全固定在纤维上,容易在后续的使用或洗涤过程中褪色。
2.染色不均匀:染色过程中染料的分散均匀程度不够,导致染色结果不稳定,在使用或洗涤后容易出现部分褪色的情况。
3.织物质量问题:如果面料质地不均匀或存在质量问题,染色后容易出现褪色。
解决退色问题的方法包括加强染料固定性能的测试和控制,改进染色工艺,选择质地均匀的面料等。
问题三:尺寸变化问题在染整过程中,纱线和面料的尺寸变化是一个常见的问题。
尺寸变化指的是纱线或面料在染整过程中发生的收缩或伸展现象,导致最终产品的尺寸与预期不符。
尺寸变化的原因主要有以下几点:1.温度影响:纱线或面料在高温下会发生收缩,而在低温下会发生伸展,染色过程中的温度变化可能导致尺寸变化。
- 1、下载文档前请自行甄别文档内容的完整性,平台不提供额外的编辑、内容补充、找答案等附加服务。
- 2、"仅部分预览"的文档,不可在线预览部分如存在完整性等问题,可反馈申请退款(可完整预览的文档不适用该条件!)。
- 3、如文档侵犯您的权益,请联系客服反馈,我们会尽快为您处理(人工客服工作时间:9:00-18:30)。
1.在炼漂过程中尽量减小张力。
2.在染整加工过程中凡是湿布烘干都是尽量施松张力,降低伸长避免门幅过度窄缩,如果是开幅连烘的机台在开幅后要加装小的容布箱再穿进布架以避免开幅与轧水之间的张力过大。
3.在丝光过程中要掌握扩幅张力要保持坯布的幅宽注意控制纬向张力。
4.各道工序的平洗机导布棍.轧棍,烘筒,应加强维修保证平整光洁.避免张力放松时起皱水槽中的导辊要运转自如,同一机台前后轧辊烘筒的线速度相差不应太大,经向张力掌握布不拖地为准在长台的分段过程中应有松紧调节开降架装置或分段传动调节装置以控制张力的大小。
5.丝光后的产品应严格控制后道加工过程中的张力因为丝光后再伸长经向缩水率在实际生
产操作中可以在各道工序中制定半制品幅宽指标在各机台的去布处于以测量考核,后序要对前工序进行验收保证半制品应有的幅宽。
6.对于一些机械运动张力需要人工控制张力.严格工艺操作,加强工艺操作,加强机械清洁减小运转张力有效的降低织物的缩水率。
7.加强对丝光加工工艺条件的检查,有条件的的染厂可以用直辊和布铗结合丝光。
8经向缩水率较大的品种:如卡其,华达呢府绸织物要进行预缩处理.降低缩水率.在这些品种
在紧式加工中.仅依靠机械上放松张力,则最好的缩水率也高达4%左右,这一缩率宜采用预缩的办法来进一步降低,产品经过预缩处理后不但缩水率降低了.同时还可以获得较好的手感,
纹路清晰光泽柔和。
9.对于纬向缩水率较大的品种,有的由于坯布幅宽不合理,即使合理的加工条件,也仍有较大的纬向缩水率加工条件差的缩水率更大,必须采取进一步的改进措施,丝光品种要保证落布幅宽达到要求.此外还要需要在坯布规格上加以改进,在不增加成本或少增加成本的条件下,将坯布的幅宽放宽,以保证纬向缩水率降到要求范围内。
10.进行树脂整理可降低缩水率并提高弹性(需注意手感)另涂层也可以降低缩水率。
11.对于T/C合纤混纺织物要抓好定性丝光工序工艺及操作可较好控制缩水率。