如何排除生产中染色布的疵点
当染色车间出现这8大染疵时,技术员必须学会的解决方案!【建议收藏】

当染色车间出现这8大染疵时,技术员必须学会的解决方案!【建议收藏】染色产品常见疵病分析建议收藏保存色差染色制品所得色泽深浅不一,色光有差异。
根据色差的不同又分为同批色差和同匹色差。
同批色差是指在同批产品中,一个色号的产品,箱与箱之间、件与件之间、包与包之间、匹与匹之间存在色差。
同匹色差是指同匹产品中的边中色差、前后色差或正反面等位置上的色差。
产生原因1、坯布原因2、染料在织物上先期分布不匀织物因素(布面上浆情况)吸液因素(吸液、渗透不匀)预烘因素(烘干不匀)3、染料在织物上固着程度不同:固着条件控制不当(如焙烘)4、染料选择不当5、染料色光发生变异染前因素(半制品白度、pH值等)染色因素(如温度过高)染后因素(后整理中的工艺和所加助剂)皂洗因素6、操作原因:化料不匀、加料不当;卷染上布不齐克服办法1、加强坯检,保证坯布质量2、选用合适设备、采用均匀轧车或改善轧车的均匀性3、加强练漂管理,提供合格半制品同一批染物采用相同坯布染前布面干燥要均匀一致染前定型效果要均匀丝光后布面pH值控制中性4、合理选择染料(上染曲线相似、加强染料测试等)5、染色时加入匀染性助剂6、染色工艺合理7、重视染后处理,水洗、皂洗要充分8、后整理助剂选择要慎重,工艺条件要一致色不符样染色成品的色泽与指定的样品色泽不符,并超过了允许色差标准。
表现为:不符同类布样(生产实样与原样属相同纤维、相同组织的色样)不符参考样(不同原料不同组织的色泽)不符成交小样(提供给客户并经双方确定的样品)不符数字样(客户提供的电脑测配色系统的数字样)产生原因1、染色工艺制定不当,大小样生产条件不相同2、审核色样光源不统一3、染色计划安排不周4、染料、助剂分批管理不善5、染色工艺条件、操作掌握不好半制品不符要求染色采用硬水染色管理不妥染化料量称错染色中没有严格掌握工艺条件克服方法1、大小样织物的组织规格要相同,半制品工艺相同;2、轧染时轧辊压力要固定,浸染时浴比要保持一致;3、大小样的染色工艺条件一致;(染料、助剂、温度、浴比等)4、染料要进行筛选易变色染料不用5、采用标准光源(或电脑测色仪器)6、合理安排染色生产计划7、加强染料、助剂的管理8、严格工艺纪律抓好三级检查(挡车工自查、班组及车间检查)掌握工艺条件、保证按工艺上车抓好每车或每缸布的对样、贴样制度色花布面颜色不均匀呈块状色深或色浅不规则色斑。
锦纶染色产生疵点的原因及防止措施
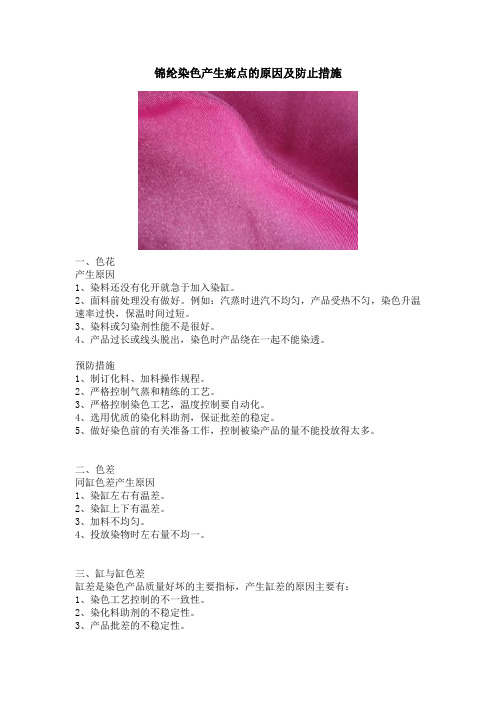
锦纶染色产生疵点的原因及防止措施一、色花产生原因1、染料还没有化开就急于加入染缸。
2、面料前处理没有做好。
例如:汽蒸时进汽不均匀,产品受热不匀,染色升温速率过快,保温时间过短。
3、染料或匀染剂性能不是很好。
4、产品过长或线头脱出,染色时产品绕在一起不能染透。
预防措施1、制订化料、加料操作规程。
2、严格控制气蒸和精练的工艺。
3、严格控制染色工艺,温度控制要自动化。
4、选用优质的染化料助剂,保证批差的稳定。
5、做好染色前的有关准备工作,控制被染产品的量不能投放得太多。
二、色差同缸色差产生原因1、染缸左右有温差。
2、染缸上下有温差。
3、加料不均匀。
4、投放染物时左右量不均一。
三、缸与缸色差缸差是染色产品质量好坏的主要指标,产生缸差的原因主要有:1、染色工艺控制的不一致性。
2、染化料助剂的不稳定性。
3、产品批差的不稳定性。
4、染色技术员和操作工的敬业性和责任性。
预防措施1、改善染色设备。
例如:改用外置加热或底部加循环泵,保证左右升温均匀。
2、加快桨叶的运转速度,使上下传热加快。
3、产品投缸时要保证左右中间量的均匀性。
4、加料能改成自动加料系统。
5、严格控制染色工艺,确保缸次间工艺的一致性。
6、优选染化料助剂,做好染料和助剂换批的检测工作,保证染色处方准确性。
7、加强产品白坯的管理,保证配缸重量的准确性,不混淆产品的批次,不乱混产品货号。
8、加强员工的素质教育,提高员工素养和敬业精神。
四、色点和色斑产生原因1、纱线不纯,有杂质或者色纱混入其中,染色后无法消除。
2、在织造生产过程中混入有颜色飞毛。
3、白坯堆放时间过长产生霉斑和黄斑。
4、染色过程染料飞沾到产品上成色点。
5、产品部分地方在前处理或染色时碰到了某种助剂原液,影响了染料的上染,从而在此产生白点或浅色斑。
6、与某些溶解度特别小的染料拼色时,没有充分化料就加入染缸,没有完全溶解的染料沾到产品上产生色点。
预防措施1、加强进原料时的质量检验和控制,防止不纯纱线的进入。
印染布疵点产生的原因及解决方法

印染布疵点产生的原因及解决方法1﹑裙皱皱条之间相互平行,头尾平齐。
皱条中间大,两头尖。
皱条与平面交界处留有换梭纱尾,形状似裙子折皱。
裙皱多发生在含化纤的织物上,原坯布上不易发现。
只有经印染加工处理才显现出来。
产生的主要原因:①化纤本身性能的差异或纺织厂高温定捻温度不一致,造成纬纱缩率不同;②所用纬纱号数或捻度存在差异。
解决方法:重新投好的原坯布生产。
2﹑缝头皱皱条与缝头相连,一条或多条,长短不一.有的在缝头一端,有的在缝头两端。
主要原因是幅地进布工缝头不良。
未做到缝头平直、坚牢、边齐、针脚均匀一致。
解决方法:连同缝头开剪,作次零布处理。
3﹑印染加工皱一般在布面呈现的条数不多,通常为直形或斜形条状,长短宽窄不一。
印染前或印染加工过程中产生的皱条与正常布面色泽相差较大;印染固色后平洗过程中产生的皱条色差较小。
主要原因:①印染前半制品原有皱条;②印染过程中机械张力,轧辊压力调节不好;导辊、烘筒的平行度掌握不好;③设备清洁做得不好。
解决方法:补产。
4﹑丝光皱印染后呈现中间深两边浅、直线或斜形的细死皱。
产生的主要原因:①丝光机去碱蒸箱、平洗槽导布辊不平或沾有纱头、碱垢;②丝光机张力调节不当;③去碱蒸箱直接蒸汽管开启较大冲击织物造成折皱。
解决方法:补产。
5﹑风印印染织物搁置被显露的部分与布面正常色泽呈现差异。
一般在布的折叠处或布幅两边出现不规则的浅色档或色条。
产生的主要原因:某些用于活性染料、分散染料的印染半制品、在制品布面带碱,或受空气中还原气体的作用,影响织物与染料的固着,裸露部分产生浅色档。
活性染料易产生风印。
解决方法:补产。
6﹑边中色差、左中右色差印染织物边中或左中右色泽深浅不下。
产生的主要原因:①染液的轧辊或印花压力两端不一致;②预烘或热溶焙烘时,布幅中间和两边的温度和风量不一致,造成布面左右或左中右干湿不一致;③拼色染料在相同的加工条件下移染性能不一致,造成色泽深浅或色光的变化。
解决方法:补产或修色。
造成轧染染色不匀的原因及防治措施
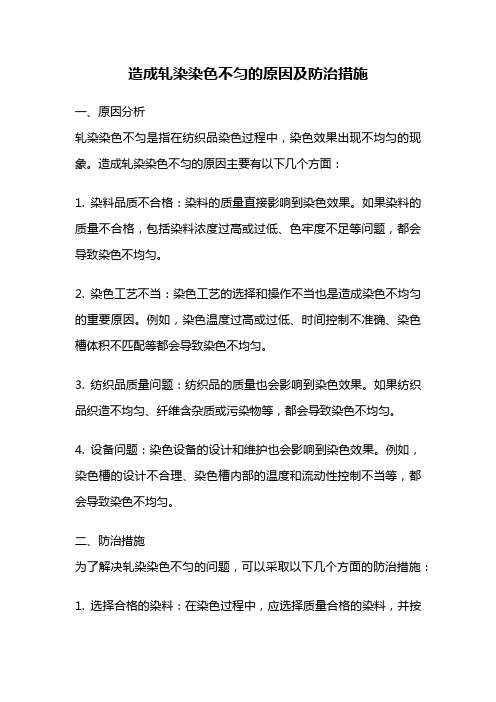
造成轧染染色不匀的原因及防治措施一、原因分析轧染染色不匀是指在纺织品染色过程中,染色效果出现不均匀的现象。
造成轧染染色不匀的原因主要有以下几个方面:1. 染料品质不合格:染料的质量直接影响到染色效果。
如果染料的质量不合格,包括染料浓度过高或过低、色牢度不足等问题,都会导致染色不均匀。
2. 染色工艺不当:染色工艺的选择和操作不当也是造成染色不均匀的重要原因。
例如,染色温度过高或过低、时间控制不准确、染色槽体积不匹配等都会导致染色不均匀。
3. 纺织品质量问题:纺织品的质量也会影响到染色效果。
如果纺织品织造不均匀、纤维含杂质或污染物等,都会导致染色不均匀。
4. 设备问题:染色设备的设计和维护也会影响到染色效果。
例如,染色槽的设计不合理、染色槽内部的温度和流动性控制不当等,都会导致染色不均匀。
二、防治措施为了解决轧染染色不匀的问题,可以采取以下几个方面的防治措施:1. 选择合格的染料:在染色过程中,应选择质量合格的染料,并按照染料供应商提供的染色配方进行操作。
同时,要定期对染料进行检测,确保其质量符合要求。
2. 优化染色工艺:对染色工艺进行优化,选择合适的染色温度、时间和染色槽体积等参数,确保染色过程中的温度、时间和流动性等都能得到良好的控制。
3. 提高纺织品质量:在生产过程中,要加强对纺织品的质量控制,确保纺织品的织造均匀、纤维无杂质和污染物。
同时,在纺织品出厂前要进行严格的检验,确保纺织品的质量符合要求。
4. 定期维护设备:要定期对染色设备进行检查和维护,确保设备的正常运行。
特别是对染色槽的清洗和维护要做好,避免染料残留或污染物堆积导致染色不均匀。
5. 加强人员培训:对染色工人进行专业培训,提高其染色操作技术和质量意识。
只有经过专业培训的工人,才能正确操作染色设备,保证染色效果均匀。
造成轧染染色不匀的原因主要包括染料品质不合格、染色工艺不当、纺织品质量问题和设备问题等。
为了解决这一问题,可以采取选择合格的染料、优化染色工艺、提高纺织品质量、定期维护设备和加强人员培训等防治措施。
技术绒布印花常见疵病及解决办法(干货请收藏)
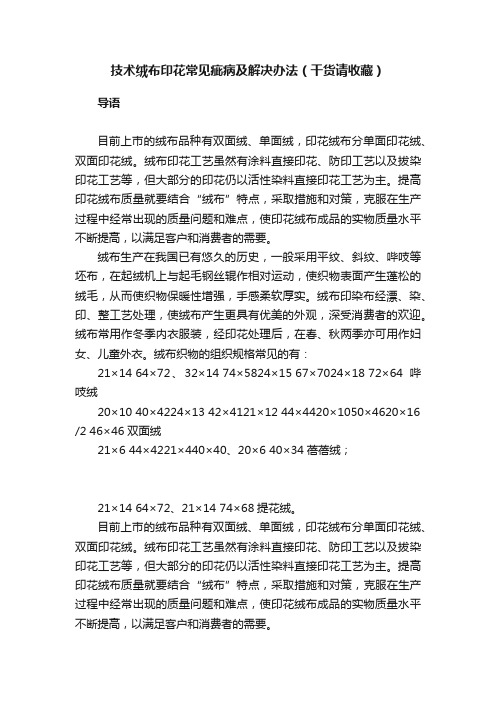
技术绒布印花常见疵病及解决办法(干货请收藏)导语目前上市的绒布品种有双面绒、单面绒,印花绒布分单面印花绒、双面印花绒。
绒布印花工艺虽然有涂料直接印花、防印工艺以及拔染印花工艺等,但大部分的印花仍以活性染料直接印花工艺为主。
提高印花绒布质量就要结合“绒布”特点,采取措施和对策,克服在生产过程中经常出现的质量问题和难点,使印花绒布成品的实物质量水平不断提高,以满足客户和消费者的需要。
绒布生产在我国已有悠久的历史,一般采用平纹、斜纹、哔吱等坯布,在起绒机上与起毛钢丝辊作相对运动,使织物表面产生蓬松的绒毛,从而使织物保暖性增强,手感柔软厚实。
绒布印染布经漂、染、印、整工艺处理,使绒布产生更具有优美的外观,深受消费者的欢迎。
绒布常用作冬季内衣服装,经印花处理后,在春、秋两季亦可用作妇女、儿童外衣。
绒布织物的组织规格常见的有:21×1464×72、32×1474×5824×1567×7024×1872×64哔吱绒20×1040×4224×1342×4121×1244×4420×1050×4620×16 /2 46×46双面绒21×644×4221×440×40、20×6 40×34蓓蓓绒;21×14 64×72、21×1474×68提花绒。
目前上市的绒布品种有双面绒、单面绒,印花绒布分单面印花绒、双面印花绒。
绒布印花工艺虽然有涂料直接印花、防印工艺以及拔染印花工艺等,但大部分的印花仍以活性染料直接印花工艺为主。
提高印花绒布质量就要结合“绒布”特点,采取措施和对策,克服在生产过程中经常出现的质量问题和难点,使印花绒布成品的实物质量水平不断提高,以满足客户和消费者的需要。
涤纶常见的染色疵点产生的原因及预防措施

涤纶常见的染色疵点产生的原因及预防措施摘要:本文从理论角度分析了涤纶常见的染色疵点产生的原因及预防措施。
首先介绍了涤纶的结构和各项性能,从而得出涤纶的一些基本特性。
然后从分散染料对涤纶的染色时产生的色花、色点、色差及分散染料的泳移现象论述了涤纶常见的染色疵点,并针对这些疵点提出相应的预防措施,解决涤纶常见的染色疵点。
关键词:涤纶疵点原因预防措施前言涤纶自发明至今以它绝对的优势取得了快速的发展,其数量已占世界纺织纤维的1/3,约占我国纺织纤维加工量的一半,成为合成纤维中的佼佼者,是当今理想的纺织材料。
它的优越性主要取决于它特定的大分子结构;不仅有刚性的苯环,而且有脂肪族的链节,使其不仅具有可熔融加工性,便于加工成纤维,而且其大分子足够的刚性,赋予纤维高的初始模量。
涤纶的综合性能好,强度大、弹性好,加工性能也好,其制成的面料挺括而不易变形,洗后不用熨烫,可纯纺也可和各种天然纤维混纺或交织,广泛用于服装,家用纺织品和产业用纺织品。
在服装方面涤棉混纺织物可用于衬衣、床上用品,涤纶长丝可用于外衣、运动衣,也可用以生产仿羊毛、仿丝绸、仿麻等仿天然纤维产品等。
由于涤纶可以大批量生产,加工技术不断改进,生产费用降低,所以涤纶的前景一片大好。
而涤纶的染色疵点对涤纶的生产制品带来了很多麻烦,所以我们必须对涤纶染色疵点有一定了解,比如涤纶染色时的色花、色点和色差等,并分析这些涤纶染色时疵点产生的原因有哪些,从而提出控制涤纶染色时疵点的预防措施,解决这些涤纶染色疵点,以减少对涤纶加工和制品带来的生产麻烦【1】。
1 .涤纶和分散染料1.1涤纶1.1.1涤纶的结构涤纶是聚对苯二甲酸乙二醇酯纤维的商品名称。
在一般光学显微镜下观察,普通涤纶的纵向为光滑、均匀、无条痕的圆柱体,横截面为圆形。
涤纶大分子链上不含有亲水性基团,且缺乏与染料分子结合的官能团,故吸湿性、染色性差,属于疏水性纤维。
涤纶大分子的基本链节中含有苯环,阻碍了大分子的内旋转,使主链刚性增加。
干货喷气织造知识——常见织疵的产生原因及消除方法
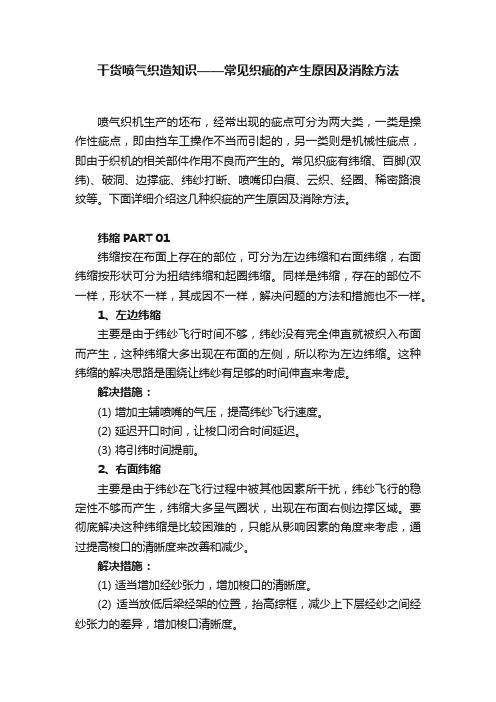
干货喷气织造知识——常见织疵的产生原因及消除方法喷气织机生产的坯布,经常出现的疵点可分为两大类,一类是操作性疵点,即由挡车工操作不当而引起的,另一类则是机械性疵点,即由于织机的相关部件作用不良而产生的。
常见织疵有纬缩、百脚(双纬)、破洞、边撑疵、纬纱打断、喷嘴印白痕、云织、经圈、稀密路浪纹等。
下面详细介绍这几种织疵的产生原因及消除方法。
纬缩PART 01纬缩按在布面上存在的部位,可分为左边纬缩和右面纬缩,右面纬缩按形状可分为扭结纬缩和起圈纬缩。
同样是纬缩,存在的部位不一样,形状不一样,其成因不一样,解决问题的方法和措施也不一样。
1、左边纬缩主要是由于纬纱飞行时间不够,纬纱没有完全伸直就被织入布面而产生,这种纬缩大多出现在布面的左侧,所以称为左边纬缩。
这种纬缩的解决思路是围绕让纬纱有足够的时间伸直来考虑。
解决措施:(1) 增加主辅喷嘴的气压,提高纬纱飞行速度。
(2) 延迟开口时间,让梭口闭合时间延迟。
(3) 将引纬时间提前。
2、右面纬缩主要是由于纬纱在飞行过程中被其他因素所干扰,纬纱飞行的稳定性不够而产生,纬缩大多呈气圈状,出现在布面右侧边撑区域。
要彻底解决这种纬缩是比较困难的,只能从影响因素的角度来考虑,通过提高梭口的清晰度来改善和减少。
解决措施:(1) 适当增加经纱张力,增加梭口的清晰度。
(2) 适当放低后梁经架的位置,抬高综框,减少上下层经纱之间经纱张力的差异,增加梭口清晰度。
(3) 提高原纱和浆纱质量,减少棉结杂质和毛羽,减少开口时上、下层经纱相互粘连的现象。
(4) 检查左右绞边器的绞边时间。
(5) 钢筘的使用上尽量使用较大一点筘号,原来4/筘可改3/筘,3/筘可改2/筘,会收到较好的效果,筘号大,每筘穿人数减少,经纱之间粘连的现象会大为改观。
(6) 扭结纬缩的产生多半是由于纬纱捻度过高或钢筘弯曲造成纬纱头端扭结而无法伸直。
(7) 优化引纬工艺,最佳配置引纬时间、主、辅喷嘴作用时间以及主、辅喷嘴的气压。
涤棉染色常见疵病及解决方法

用 两 软 一 硬 的 轧 辊 , 软 硬 辊 筒 之 间 的 硬 度 , 异 太 如 差
温度 的 差 异 , 一 个 还 要 选 择 分 散 染 料 的 热 熔 固 色 另
曲 线 是 平 直 的 , 就 是 一 致 的 , 时 还 要 注 意半 制 品 也 同 的 p H值 , p 值 7~8最 佳 . 以 H
2 3 左 中右 色 相 不 一 色 差 .
翻缝 一 烧 毛一 退 煮 一 氧 漂 一 平 洗 一 丝 光 一 定 型
一
染 色 一 热 熔 一 水皂 洗一 整 理 一 验 码 一 拼 件 一 打包
这 种 现 象 发 生 在 高 温 热 熔 过 程 中 , 热 熔 箱 内 是
2 原 料 、 备 造 成 的 色差 设
所 谓 左 右 对 角 色 差 , 是 一 面 边 子 正 面 深 , 面 就 反 浅 , 一面边子 正 面浅 , 反 面 深 , 种色 差 实质就 另 而 这
是 局 部 性 的 正 反 面 色 差 . 要 原 因 是 , 烘 时 红外 线 主 预 左右 热量不匀 , 射强 度不一 和热风左 右风量不匀 , 辐 还有金 属导辊左 右散热不 一造成 .
提 高 匀 染 度 , 少 正 反 面 色差 , 在 咱厂 应 用 的 大 都 减 现 是 均 匀 轧 车 , 辊 采 用 丁 型 橡 胶 , 度 一 般 在 ( 0± 轧 硬 7 2 度 , 个 辊 筒 硬 度 一 样 , 也 不 要 忽 视 均 匀 轧 槽 内 ) 两 但
的导 辊 .
收 稿 日期 :0 20 .2 20 61
余 率 不 一 致 所 引 起 的 , 果 是 轧 余 率 造 成 的 那 就 要 如 调 整左 、 、 压 力 , 布 面 的 轧 余 率 一 样 , 可 以解 中 右 使 就
- 1、下载文档前请自行甄别文档内容的完整性,平台不提供额外的编辑、内容补充、找答案等附加服务。
- 2、"仅部分预览"的文档,不可在线预览部分如存在完整性等问题,可反馈申请退款(可完整预览的文档不适用该条件!)。
- 3、如文档侵犯您的权益,请联系客服反馈,我们会尽快为您处理(人工客服工作时间:9:00-18:30)。
如何排除生产中染色布的疵点
导语:
染色过程中经常遇到的染色色差、色条色花、色光重现性、染化料助剂优选、染色白斑、漂练段烂棉斑、褶子、碱斑、黄斑、碱泥、蜡条、烧毛褶子、履带印等疵点。
遇到这类疵点如何在技术层面进行处理?在生产中如何预防、处理解决这类疵点,从而提高染色布的产品质量和一次染色成功率,达到节能降耗的目的?
如何提高一次试色成功率?
如果是经常生产的返单颜色,前处理工艺要稳定一致,才能确保每次生产的半成品毛效、白度、pH值一致。
并且每次染色前化验室要进行符样,所用不同批次的染化料要打小样来对比。
如果都没问题一次试色成功率就会高,甚至可以不试色正常生产(注意染色生产工艺、机台一致)。
如果生产新颜色,化验室则要打小样确认,并且染色前要符样,最好不同打样员同时符样,如果两人所打样处方一致那么第一处方就接近,一次试色成功率就会高。
所用染化料产地、力分要确定,不宜经常更换染化料产地。
因为各个厂家染料质量、色光稳定性、添加剂、生产工艺等存在差异,使用不同厂家染料会使返单第一处方差距较大,影响试色一次成功率。
怎样处理染色布褶子?
漂练褶子多见于高支高密涤棉织物和纯棉薄织物,生产中因用水硬度大,蒸洗时易形成水垢易粘附在导布辊上,长时间生产会形成水垢沟痕,使导布辊不平整,织物便容易起褶子。
生产中一旦发现有褶子应及时擦车清理,染色时发现半成品有褶子,则应采用合理工艺回修。
下面介绍几种褶子回修处理方法:
漂练来布若为不平整暂时性折痕或丝光烘干褶子,若比较轻则直接染色,不要考虑对染色影响,若比较重只要预定型即可染色生产。
漂练来布若有明显褶子,没有形成织物损伤染色打底下机是黑褶子,若褶子形成织物损伤则打底下机是一道白褶子印。
对这种褶子,采用高温超幅拉宽再丝光进行回修。
漂练来布若是死褶子严重,且布面上折痕已经形成极光印,这种褶子比较难以处理,只能将来布进行高温超幅拉宽后再进行轻磨毛工艺,
将折痕极光印磨平,然后重新煮漂,使损伤织物纤维膨化修复,最后经高浓度碱丝光处理将折痕拉平。
对于褶子的回修首先要准确判断褶子的成因,不同褶子处理预防方法不同,以避免不必要工艺造成浪费。
例如丝光烘干褶子比较好发现,发现后要及时处理,不要把问题留到染色前再去定型。
若烘干褶子不好处理可以在丝光落布时打轴,这样将烘干折打平展用落布余温将褶子烫平,这样就可以节省染色前定型了。
如何处理烧毛褶子?
在染色时浸轧染液后布面上有双道或多道的黑褶子,并且黑褶子旁边有毛茸茸的白毛条,这种褶子就是烧毛褶子。
这种褶子焙烘后会显现起一道道白印,等到还原显色后为一道道深黑褶子。
烧毛褶子是由于烧毛时布面不平整,经过火口时布面起褶子,火口温度高将形成褶子的地方烫伤所形成的,由于折痕里面烧不到,所以黑褶子旁边留有白毛条。
预防烧毛褶子首先烧毛时不能出褶子,并根据不同织物制定合理的生产工艺,对于厚织物应先堆或煮后再烧毛,使烧毛进布平展,减少烧毛赶褶子的可能性。
再者就是烧毛采用湿落布,以防止落布温度高,加剧褶子的形成。
如果染色时发现有烧毛褶子,一定要进行前处理回修后再染色,一旦冒然开车,生产染色后黑褶子将无法处理。
前处理回修烧毛褶子的方法很简单,只要高温定型将布面拉平展再烧毛,然后低碱丝光即可消除烧毛褶子。