焊接及热处理
焊接热处理

焊接热处理一、热处理概述热处理是指对材料进行加热、保温和冷却等过程,以改变其组织结构和性能的方法。
焊接热处理是指对焊接部位进行加热、保温和冷却等过程,以消除焊接应力和改善焊接组织结构的方法。
二、焊接热处理的目的1. 消除焊接应力:在焊接过程中,由于局部区域受到加热和冷却的不均匀,会产生残余应力。
这些残余应力会导致零件变形、裂纹产生等问题。
通过焊接热处理可以消除这些残余应力,提高零件的稳定性和可靠性。
2. 改善组织结构:焊接后的金属组织结构通常会发生变化,例如晶粒长大、相变等。
这些变化会影响金属的物理和化学性质。
通过合适的焊接热处理可以改善金属组织结构,提高其性能。
3. 提高硬度:通过合适的加热和冷却过程可以提高金属硬度,增强其耐磨性和抗拉强度等性能。
三、焊接热处理的方法1. 固溶处理:固溶处理是指将金属加热至一定温度,使其内部的结构发生变化,然后再进行冷却。
这种方法常用于不锈钢、铝合金等材料的焊接热处理中。
2. 淬火处理:淬火处理是指将金属加热至一定温度,然后迅速冷却。
这种方法可以提高金属的硬度和强度,但也会增加其脆性。
3. 回火处理:回火处理是指将淬火后的金属再次加热至一定温度,然后冷却。
这种方法可以降低金属的脆性,同时保持其硬度和强度。
4. 退火处理:退火处理是指将金属加热至一定温度,然后缓慢冷却。
这种方法可以改善金属的组织结构,提高其韧性和塑性。
四、焊接热处理的注意事项1. 温度控制:焊接热处理中温度控制非常重要。
过高的温度会导致材料软化或者脆化;过低的温度则无法达到预期效果。
因此,必须根据具体情况进行温度控制。
2. 冷却速度:焊接热处理中的冷却速度也非常重要。
过快的冷却会导致金属脆化,而过慢的冷却则无法达到预期效果。
因此,必须根据具体情况进行冷却速度控制。
3. 热处理时间:热处理时间也是影响焊接热处理效果的重要因素。
过长或者过短的时间都会影响焊接部位的组织结构和性能。
4. 焊接前后处理:在进行焊接热处理之前,必须对焊缝进行清洗和除油等处理;在进行焊接热处理之后,还需要对零件进行清洗和防腐等处理。
焊接热处理及冶金变化概述
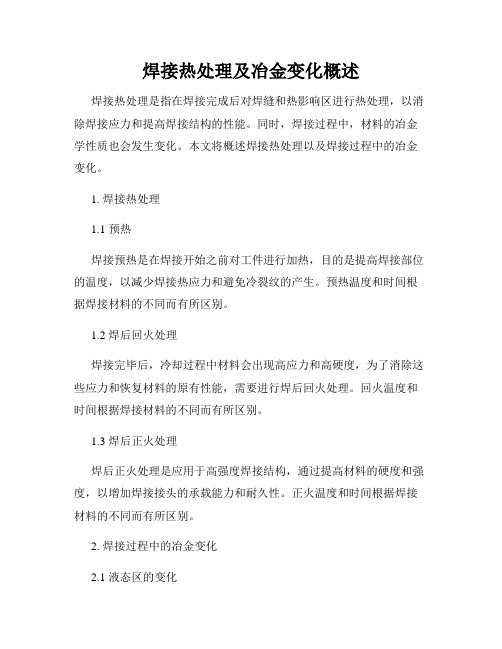
焊接热处理及冶金变化概述焊接热处理是指在焊接完成后对焊缝和热影响区进行热处理,以消除焊接应力和提高焊接结构的性能。
同时,焊接过程中,材料的冶金学性质也会发生变化。
本文将概述焊接热处理以及焊接过程中的冶金变化。
1. 焊接热处理1.1 预热焊接预热是在焊接开始之前对工件进行加热,目的是提高焊接部位的温度,以减少焊接热应力和避免冷裂纹的产生。
预热温度和时间根据焊接材料的不同而有所区别。
1.2 焊后回火处理焊接完毕后,冷却过程中材料会出现高应力和高硬度,为了消除这些应力和恢复材料的原有性能,需要进行焊后回火处理。
回火温度和时间根据焊接材料的不同而有所区别。
1.3 焊后正火处理焊后正火处理是应用于高强度焊接结构,通过提高材料的硬度和强度,以增加焊接接头的承载能力和耐久性。
正火温度和时间根据焊接材料的不同而有所区别。
2. 焊接过程中的冶金变化2.1 液态区的变化焊接过程中,焊接区域会达到高温,材料处于液态区。
在液态区,材料的晶体结构会发生改变,晶界会溶解,晶粒尺寸会变大。
这种变化有助于消除焊接过程中的缺陷,并增强焊接区域的强度。
2.2 固态区的变化焊接完成后,焊接区域会迅速冷却至室温,使得材料处于固态区。
在固态区,晶界被重新生成,晶粒尺寸逐渐减小,焊接区域的晶结构会与母材有所差异。
这种变化会影响焊接区域的力学性能。
2.3 金相组织的变化焊接区域的金相组织与母材的金相组织可能存在差异。
焊接过程中,金属原子会发生扩散,并形成新的金相组织。
这种变化会影响焊接区域的硬度、塑性和耐腐蚀性能。
3. 结论焊接热处理是消除焊接应力和提高焊接结构性能的重要方法。
在焊接过程中,材料的冶金学性质会发生变化,包括液态区的溶解与晶粒尺寸变大,固态区的重新生成与晶粒尺寸减小,以及金相组织的变化。
深入了解焊接热处理及冶金变化有助于提高焊接质量,确保焊接结构的可靠性和耐久性。
总结到这里,通过对焊接热处理及冶金变化的概述,我们可以了解到焊接后的热处理对于消除焊接应力和提高焊接结构性能的重要性,同时也了解到焊接过程中材料的冶金学性质会发生变化,这对于焊接质量的控制具有一定的指导意义。
焊接零件的热处理和加工步骤
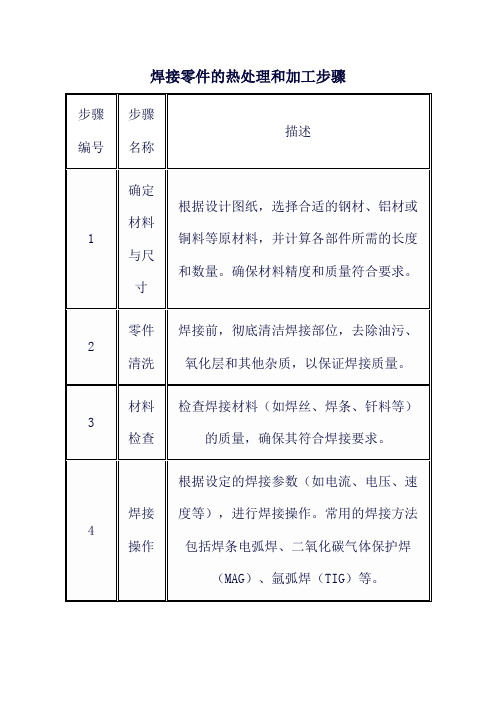
焊接操作
根据设定的焊接参数(如电流、电压、速度等),进行焊接操作。常用的焊接方法包括焊条电弧焊、二氧化碳气体保护焊(MAG)、氩弧焊(TIG)等。
5
焊接监控
在焊接过程中,实时监控焊接质量,包括焊缝外观和内部缺陷。
6
焊缝检查
焊接完成后,对焊缝进行外观检查和内部检查(如X射线、超声波检查),确保焊缝质量符合标准。
7
热处理(可选)
根据需要,对焊接接头进行热处理。热处理的目的包括降低焊接区的硬度、消除残余应力、提高焊接接头的性能等。具体方法包括退火、正火、淬火、回火等。
- 退火:将焊接件加热到一定温度,保温后缓慢冷却,以降低硬度、提高塑性和韧性。
- 正火:将焊接件加热到临界温度以上,保温后在空气中冷却,以改善组织结构和切削加工性能。
焊接零骤名称
描述
1
确定材料与尺寸
根据设计图纸,选择合适的钢材、铝材或铜料等原材料,并计算各部件所需的长度和数量。确保材料精度和质量符合要求。
2
零件清洗
焊接前,彻底清洁焊接部位,去除油污、氧化层和其他杂质,以保证焊接质量。
3
材料检查
检查焊接材料(如焊丝、焊条、钎料等)的质量,确保其符合焊接要求。
- 淬火:将焊接件加热到淬火温度,保温后迅速冷却(如水冷、油冷),以获得高硬度和耐磨性。
- 回火:将淬火后的焊接件加热到较低温度,保温后冷却,以稳定组织、消除内应力和获得所需的力学性能。
8
修磨与修整
对焊缝进行修磨和修整,使其符合设计要求。这包括去除多余的焊渣、调整焊缝尺寸和形状等。
9
质量检验
对焊接零件进行全面的质量检验,确保所有指标符合设计要求和相关标准。
焊接及焊后热处理作业指导书
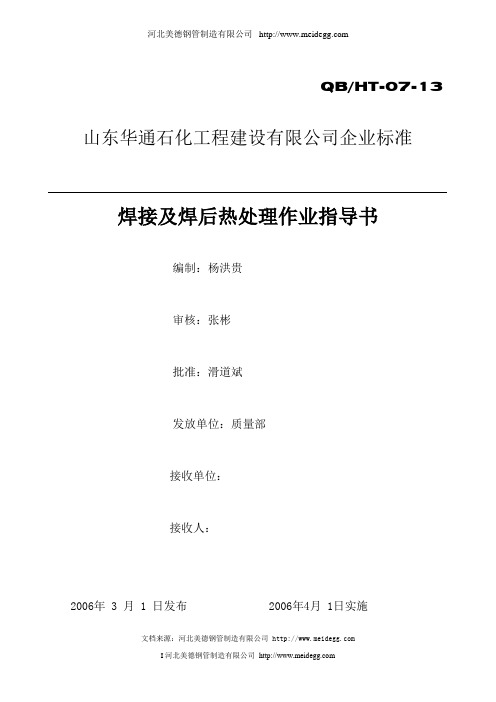
2 主要编制依据
2.1GB50236-98《现场设备、工业管道焊接工程施工及验收规范》。
2.2DL5007-92《电力建设施工及验收技术规范(火力发电厂焊接篇)》。
2.3SH3501-2001《石油化工剧毒、可燃介质管道工程施工及验收规范》。
2.4其他现行有关标准、规范、技术文件。
3 施工准备
3.1.3压力管道施焊前,根据焊接作业指导书应对焊工及相关人员进行技术交底,并做好技术交底记录。
3.1.4对于高温、高压、剧毒、易燃、易爆的压力管道,在焊接施工前应画出焊口位置示意图,以便在焊接施工中进行质量监控。
3.2对材料的要求
3.2.1被焊管子(件)必须具有质量证明书,且其质量符合国家现行标准(或部颁标准)的要求;进口材料应符合该国家标准或合同规定的技术条件。
4.4.2在焊接中应确保起弧及收弧的质量,收弧应将弧坑填满,多层焊的层间接头应相互错开。
4.4.3除焊接工艺有特殊要求外,每条焊缝应一次连续焊完,如因故被迫中断,应采取缓冷措施,再焊时应仔细检查确认无裂纹后,方可按焊接工艺继续施焊。有预热要求的管材应按预热要求重新预热后施焊。
4.4.4管子焊接时,管端要堵封住,防止管内穿堂风。
(2)定位焊不得有裂纹及其他缺陷,如有缺陷应彻底磨除重新进行定位焊。
(3)在合金钢管壁上点焊组对卡具定位时,卡具的材质和焊材应与管材相同。当拆除卡具时,不得用敲打或掰扭的方法拆除。当用氧-乙炔焰切割卡具时,应在离管道表面3mm处切割,然后用砂轮修磨平整。
4.4正式焊接
4.4.1焊接引弧应在坡口内进行,严禁在管子(件)表面引燃电弧,试验电流或焊接临时支撑物。
焊接及焊后热处理作业指导书
编制:杨洪贵
审核:张彬
钢制压力容器焊接与热处理
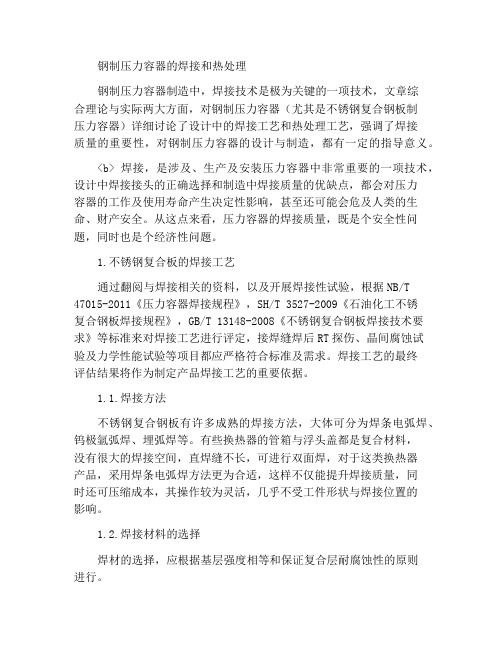
钢制压力容器的焊接和热处理钢制压力容器制造中,焊接技术是极为关键的一项技术,文章综合理论与实际两大方面,对钢制压力容器(尤其是不锈钢复合钢板制压力容器)详细讨论了设计中的焊接工艺和热处理工艺,强调了焊接质量的重要性,对钢制压力容器的设计与制造,都有一定的指导意义。
<b> 焊接,是涉及、生产及安装压力容器中非常重要的一项技术,设计中焊接接头的正确选择和制造中焊接质量的优缺点,都会对压力容器的工作及使用寿命产生决定性影响,甚至还可能会危及人类的生命、财产安全。
从这点来看,压力容器的焊接质量,既是个安全性问题,同时也是个经济性问题。
1.不锈钢复合板的焊接工艺通过翻阅与焊接相关的资料,以及开展焊接性试验,根据NB/T 47015-2011《压力容器焊接规程》,SH/T 3527-2009《石油化工不锈复合钢板焊接规程》,GB/T 13148-2008《不锈钢复合钢板焊接技术要求》等标准来对焊接工艺进行评定,接焊缝焊后RT探伤、晶间腐蚀试验及力学性能试验等项目都应严格符合标准及需求。
焊接工艺的最终评估结果将作为制定产品焊接工艺的重要依据。
1.1.焊接方法不锈钢复合钢板有许多成熟的焊接方法,大体可分为焊条电弧焊、钨极氩弧焊、埋弧焊等。
有些换热器的管箱与浮头盖都是复合材料,没有很大的焊接空间,直焊缝不长,可进行双面焊,对于这类换热器产品,采用焊条电弧焊方法更为合适,这样不仅能提升焊接质量,同时还可压缩成本,其操作较为灵活,几乎不受工件形状与焊接位置的影响。
1.2.焊接材料的选择焊材的选择,应根据基层强度相等和保证复合层耐腐蚀性的原则进行。
1.3.焊接设备和环境通常可选择直流焊机,基层、复层及过渡层这3种焊缝均可选择焊条电弧焊。
所采用的钢丝刷、扁铲等工具都,都应是不锈钢材料。
焊接应在0 ℃以上的环境下进行,同时,现场应采取必要的防风措施。
1.4.焊接沟槽和接头装配1.4.1.沟槽选用沟槽形式时,应充分考虑焊接渡层的特点,焊接顺序应依次为焊基层、渡层到复层,,要尽可能不对复层进行焊接或进行少量焊接,同时还应避免复层焊缝被多次受热,从而逐步增强复层焊缝的耐腐蚀性能,该沟槽形式还能有效降低设备内部的铲磨工作量。
焊接、切割和热处理作业要求

焊接、切割和热处理作业要求1一般留意事项1.1未受过特地训练的人员不准进展焊接工作。
取得焊工合格证后,方可从事考试合格工程范围内的焊接工作。
1.2焊工应穿帆布工作服,戴工作帽,上衣不准扎在裤子里。
口袋应有遮盖,脚面应有鞋罩,以免焊接时被烧伤。
1.3不准使用有缺陷的焊接工具和设备。
1.4不准在带有压力〔液体压力或气体压力〕的设备上或带电的设备上进展焊接。
在特别状况下需在带压和带电的设备上进展焊接时,应实行安全措施,并经本单位分管生产的领导〔总工程师〕批准。
对承重构架进展焊接,应经过有关技术部门的许可。
1.5制止在装有易燃物品的容器上或油漆未干的构造或其它物体上进展焊接。
1.6制止在储有易燃易爆物品的房间内进展焊接。
在易燃易爆材料四周进展焊接时,其最小水平距离不得小于 5m,并依据现场状况,实行安全牢靠措施〔用围屏或阻燃材料遮盖〕。
1.7对于存有剩余油脂或可燃液体的容器,应翻开盖子,清理干净;对存有剩余易燃易爆物品的容器,应先用水蒸气吹洗,或用热碱水冲洗干净,并将其盖口翻开,方可焊接。
1.8在风力超过 5 级时制止露天进展焊接或气割。
但风力在 5 级以下、3 级以上进展露天焊接或气割时,应搭设挡风屏以防火星飞溅引起火灾。
1.9下雨雪时,不行露天进展焊接或切割工作时。
如必需进展焊接时,应实行防雨雪的措施。
1.10在可能引起火灾的场所四周进展焊接工作时,应备有必要的消防器材。
1.11进展焊接工作时,应设有防止金属熔渣飞溅、掉落引起火灾的措施以及防止烫伤、触电、爆炸等措施。
焊接人员离开现场前,应检查并确认现场无火种留下。
1.12在高空进展焊接工作,应遵照本规程第 17 章的有关规定。
1.13在锅炉汽包、凝汽器、油箱、油槽以及其它金属容器内进展焊接工作,应有以下防止触电的措施:1.13.1电焊时焊工应避开与铁件接触,应站立在橡胶绝缘垫上或穿橡胶绝缘鞋,并穿枯燥的工作服。
1.13.2容器外面应设有可观察和听见焊工工作的监护人,并应设有开关,以便依据焊工的信号切断电源。
各种金属材料的焊接特点及其热处理工艺

各种金属材料的焊接特点及其热处理工艺焊接是一种将两个或多个金属材料通过熔化或变形并在熔融金属之间形成接头的加工方式。
在焊接过程中,金属材料经历了高温和冷却的过程,从而影响了焊接接头的性能和组织结构。
不同金属材料具有不同的焊接特点和热处理工艺。
下面将分别介绍常见金属材料的焊接特点及其热处理工艺。
1.钢材焊接特点及热处理工艺:钢材是最常见的金属材料之一,具有良好的可焊性。
其焊接特点如下:(1)钢材容易氧化,焊接时需要保护气体或保护剂以防止氧化。
(2)焊接速度快,热影响区较小,易形变。
(3)钢材焊接后易产生残余应力和变形。
钢材的热处理工艺包括退火、正火和淬火等。
退火可以减轻焊接残余应力,正火可提高焊接接头的硬度和强度,淬火可增加焊接接头的硬度。
2.铝材焊接特点及热处理工艺:铝材具有良好的导热性和导电性,但其可焊性较差。
其焊接特点如下:(1)容易产生氧化膜,焊接前需要对焊缝进行预处理。
(2)焊接速度快,热影响区较小。
(3)铝材焊接后容易产生变形。
铝材的热处理工艺主要包括固溶处理和时效处理。
固溶处理可使铝材中的合金元素均匀溶解,时效处理可提高焊接接头的硬度和强度。
3.铜材焊接特点及热处理工艺:铜材具有良好的导热性和导电性,但其可焊性较差。
其焊接特点如下:(1)容易产生氧化膜,焊接前需要对焊缝进行预处理。
(2)焊接速度较慢,热影响区较大。
(3)铜材焊接后容易产生变形和裂纹。
铜材的热处理工艺主要包括退火和时效处理。
退火可减轻焊接接头的残余应力,时效处理可提高焊接接头的硬度和强度。
4.镁合金焊接特点及热处理工艺:镁合金具有轻质高强度的特点,但其可焊性较差。
其焊接特点如下:(1)容易产生氧化膜,焊接前需要对焊缝进行预处理。
(2)焊接速度快,热影响区较小。
(3)焊接时易燃,需要采取安全措施。
镁合金的热处理工艺主要包括固溶处理和时效处理。
固溶处理可提高镁合金的强度和耐腐蚀性,时效处理可进一步提高焊接接头的硬度和强度。
焊接工艺的热影响区控制与热处理技术

焊接工艺的热影响区控制与热处理技术焊接是一种常用的金属组接方式,但在焊接过程中会产生热影响区(Heat Affected Zone, HAZ),该区域的性能和微结构会受到严重影响,因此研究和控制焊接工艺中的热影响区至关重要。
本文将介绍焊接工艺中热影响区的形成原因以及热处理技术在热影响区控制中的应用。
一、热影响区的形成原因焊接过程中,高温的焊接热源会导致瞬间升温和冷却,从而在焊缝周围形成热影响区。
主要的热影响区包括熔化区、毛细区和热影响区三部分。
1. 熔化区:熔化区是焊接过程中直接受到高温热源作用的区域,温度极高,金属材料在此处瞬间熔化并重新凝固。
2. 毛细区:毛细区位于焊缝的边缘部分,是由于液态金属表面张力的作用,使熔化金属在毛细现象的影响下沿着边缘微尺度的通道迁移。
3. 热影响区:热影响区位于焊接区域的周围,受到熔化区的高温影响而发生组织和性能变化,但没有完全熔化。
二、热影响区的性能和微结构变化焊接过程中的高温和冷却速率会引起焊接材料的性能和微结构的变化,这些变化对焊接接头的力学性能、腐蚀性能和耐久性产生影响。
1. 组织变化:热影响区的金属晶粒会发生再生长和回火现象,晶粒尺寸变大,晶间位错和碳化物的析出也会导致组织的改变。
2. 硬度变化:由于热影响区的组织变化,焊接接头的硬度通常会发生变化。
一般来说,焊接热影响区的硬度会变高。
3. 残余应力:焊接热量的引入导致局部区域的膨胀和冷缩不一致,从而产生残余应力。
这些残余应力可能导致焊接接头的变形和开裂。
三、热影响区的控制方法为了控制焊接工艺中的热影响区并改善焊接接头的性能,可以采用热处理技术来对焊接接头进行后续处理。
1. 预热和后热处理:预热可以提高焊接区域的温度,减小焊接热量对材料的影响。
后热处理可以通过再次加热焊接区域,改善热影响区的晶粒尺寸和组织,减轻残余应力。
2. 时效处理:时效处理是在焊接后将焊接接头加热到一定温度持续一段时间,以消除热影响区中的残余应力和改善组织性能。
- 1、下载文档前请自行甄别文档内容的完整性,平台不提供额外的编辑、内容补充、找答案等附加服务。
- 2、"仅部分预览"的文档,不可在线预览部分如存在完整性等问题,可反馈申请退款(可完整预览的文档不适用该条件!)。
- 3、如文档侵犯您的权益,请联系客服反馈,我们会尽快为您处理(人工客服工作时间:9:00-18:30)。
P91、A691 GR1-1/4 CL22、A691 GR2-1/4 CL22; 奥氏体不锈钢——TP304、TP321、TP347H、CF8C; 低温钢——A333Gr6、A671-CC60等; 异种钢
焊前预热及层间温度控制
DN≥12″对接焊缝采用电加热;DN=6~10″且厚度等级 >SCH80的对接焊缝采用电加热,如下图所示,焊接过 程中不拆除,维持预热状态以控制层间温度。其余焊缝采 用火焰加热。加热范围为每侧不小于管子厚度的3倍,图 中所示为最小尺寸要求。用测温计测定预热温度。
焊前预热及层间温度控制
坡口加工
坡口形式的选择以确保根部焊透为原则,在此基础上,考 虑尽量减少焊缝尺寸,减少焊缝的熔敷金属量。一般情况 下,厚度小于25mm时,采用V型坡口,大于25mm时加 工成双V型或U型坡口(见下图)。
焊前清理
组对前用角向磨光机、棒式砂轮机、钢锉等将坡口及内外 两侧20mm范围内的母材表面清理干净,直到露出金属光 泽。
以天津100万吨/年乙烯工程为例
范围 工程概况及特点 焊接施工准备 施工工艺 质量要求及焊缝返修 质量管理机构和质量保证措施 HSE管理
天津石化100万吨/年乙烯及配套项目乙烯装置工 艺管线的焊接及热处理施工,其中包括裂解炉对流 室炉管进出口、辐射室入口及炉体配管的焊接。
本工程管道约254千米,焊接总量约为97万寸D,涉及到 的材料主要类别如下:
装置中易燃、易爆的工艺介质较多(如裂解气、乙烯、丙 烯等),既有低温管线,又有超高压蒸汽管线,其中最大 管径为108″(API5L GRB,厚度为38.1mm),最大壁 厚为73.025mm(A335 P22,管径为24″),因此,大 管径、大厚度管的焊接是本装置焊接施工的重点和难点。
焊接工艺管理
定位焊缝采用火焰加热。 预热时火焰不能直接加热坡口,要避免局部过热。 预热过程中要保证厚度方向温度均匀。 做好预热温度记录。 各种材质焊缝的预热参数见下表 。
焊接工艺
环境要求 空气相对湿度≤90%。 氩弧焊时风速小于2m/s,手工电弧焊时风速小于8m/s。 雨、雪天气作业时采取适当措施,如搭设防风挡雨棚等。
焊材管理
焊接材料分类存放保管,专人负责,统一管理,作好记录, 材料工程师定期进行检查。焊材库应配置空气去湿机、温 湿度记录仪,保证温度不低于5℃,湿度不超过60%。
焊材管理
焊条、焊丝应存放在架子上,架子离地面和墙面的距离不 应小于300mm。
焊条、焊丝应按种类、牌号、批号、规格、入库时间分类 堆放。每垛应有明确的标志。
焊条烘干 焊条使用前按照焊条说明书要求的参数进行烘干。
焊材发放: 焊工凭技术人员签发的《焊材领用卡》领取焊材。 焊条用焊条保温筒领取,每名焊工每次只能领取一种型号
的焊条,每次领用不超过5Kg,严禁不同型号焊条同时放 在一个保温筒中。
焊材发放:
焊条在保温桶中的存放时间控制在4小时以内,超过4小 时未用的焊条,要退回重新烘干,但重新烘干次数不超过 2次。超过2次的焊条不再用于压力管道的施工。重新烘 干的焊条作好标识及相应记录,下次优先发放。
焊丝一次领用数量不超过1.5Kg。 焊材发放人员作好发放记录。
焊接设备管理
焊接设备双表(电流表、电压表)齐全,且均在检定期内。 焊接电缆线采用橡皮软线,接头不超过2个以充分保证焊
接电流。 每台电焊机单独接地,实行一机一闸保护。
坡口加工
碳钢采用火焰切割加工;合金钢原则采用机械方法加工坡 口,部分大口径管道因条件所限无法采用机械加工时,也 可采用火焰切割的方法进行加工,坡口打磨时将切割的热 影响区渗碳层打磨掉,并修整出所要求的坡口。
环境温度低于下列要求时应采取提高焊接环境温度的措施: 碳钢焊接不低于-20℃ 低合金钢焊接不低于-10℃ 奥氏体不锈钢焊接不低于-5℃ 其他合金钢焊接不低于0℃
一般工艺要求
所有伴热线均采用氩弧焊工艺。 管径DN≤50且壁厚δ≤4的焊缝采用全氩弧焊,其余焊缝
采用氩弧焊打底、焊条电弧焊、熔化极气体保护焊或埋弧 焊填充盖面的工艺,对于大管径焊口,在条件允许时可采 用焊条电弧焊方法进行双面焊; 在合金钢钢管上焊接组对卡具时卡具的材质应与管材相同 承插焊缝至少焊接两遍。
不锈钢管采用焊条电弧焊时,组对前应在坡口两侧各100 mm 范围内涂白垩粉或其他防粘污剂。
。
坡口检查
焊接接头组对前应确认坡口加工形式尺寸,其表面不得有 裂纹夹层等缺陷;
焊接接头的坡口的渗透检测应按下列规定进行 铬钼耐热钢管道坡口100%检测 A333Gr6管道坡口抽检5%. 炉管出入口的坡口进行100%检测
焊接前由专业工程师对施工人员进行技术交底,使其掌握 各种材料焊接的工艺要求。
。
焊接工艺管理
焊接工艺评定的确定,施工前针对各类焊接接头编制下 发《焊接工艺卡》,施焊过程中严格按照工艺卡要求的参 数进行。
焊材管理
焊材检验及存放保管
焊材需报监理单位检验合格后入库,入库材料应具有合格 质量证明文件,出厂期超过一年的焊条,应进行焊条焊接 工艺性能试验,合格后方可使用。
焊接工艺评定的确定,施工前针对各类焊接接头编制下 发《焊接工艺卡》,施焊过程中严格按照工艺卡要求的参 数进行。
焊工管理
参加施焊的焊工应持有有效期内相应材质、相应位置的 《 TSG-Z6002-2010特种设备焊接操作人员考核细则》 合格证,并取得天津石化项目质量站组织的考试,取得上 岗证后方可上岗施焊,严禁无证上岗。
焊口组对
壁厚相同的管道组成件组对时应使内壁平齐,其错边量不 应超过壁厚的10% 且不大于1 MM。
壁厚不同的管道组成件组对当内壁差大于1.0 MM 或外壁 差大于2 MM时应进行削薄处理,削薄长度不小于两壁厚 差的4倍。
Hale Waihona Puke 定位焊碳钢焊缝定位焊采用氩弧焊,作为永久焊缝。合金钢焊缝 采用氩弧焊过桥式定位焊,正式焊接焊到该处时将定位焊 缝磨掉;定位焊缝长度10~20mm,厚度2~4mm,沿 焊缝均布。