产品检验抽样规定(DOC范本).DOC
产品质量检验之抽样检验方法(doc 41页)

抽样方法产品质量检验通常可分成全数检验和抽样检验两种方法。
全数检验是对一批产品中的每一件产品逐一进行检验,挑出不合格品后,认为其余全都是合格品。
这种质量检验方法虽然适用于生产批量很少的大型机电设备产品,但大多数生产批量较大的产品,如电子元器件产品就很不适用。
产品产量大,检验项目多或检验较复杂时,进行全数检验势必要花费大量的人力和物力,同时,仍难免出现错检和漏检现象。
而当质量捡验具有破坏性时,例如电视机的寿命试验、材料产品的强度试验等,全数检验更是不可能的。
抽样检验是从一批交验的产品(总体)中,随机抽取适量的产品样本进行质量检验,然后把检验结果与判定标准进行比较,从而确定该产品是否合格或需再进行抽检后裁决的一种质量检验方法。
过去,一般采用百分比抽样检验方法。
我国也一直沿用原苏联40年代采用的百分比抽样检验方法。
这种检验方法认为样本与总体一直是成比例的,因此,把抽查样本数与检查批总体数保持一个固定的比值如5%,0.5%等。
可是,实际上却存在着大批严、小批宽的不合理性,也就是说,即使质量相同的产品,因检查批数量多少不同却受到不同的处理,而且随着检查批总体数量的增多,即使按一定的百分比抽样,样本数也是相当大的,不能体现抽样检验在经济性方面的优点。
因此,这种抽样检验方法已被逐步淘汰。
人们经过对百分比抽样检验方法的研究,获知百分比抽样检验方法不合理的根本原因是没有按数理统计科学方法去设计抽样方案。
因此,逐步研究和设计了一系列建立在概率论和数理统计科学基础上的各种统计抽样检验或统计抽样检查方案,并制订成标准抽样检查方案。
1949年,美国科学家道奇和罗米格首先发表了《一次抽样与二次抽样检查表》;1950年美国军用标准MIL-STD-105D 是世界上有代表性的计数抽样检查方法标准;日本先后制定了JIS Z9002,JIS Z9015等一系列抽样检查方法标准;英国、加拿大等国也相继制订了抽检方法标准;ISO和IEC又分别制订了抽样检查方法国际标准,如ISO2859、IEC410等。
产品检验和抽查制度
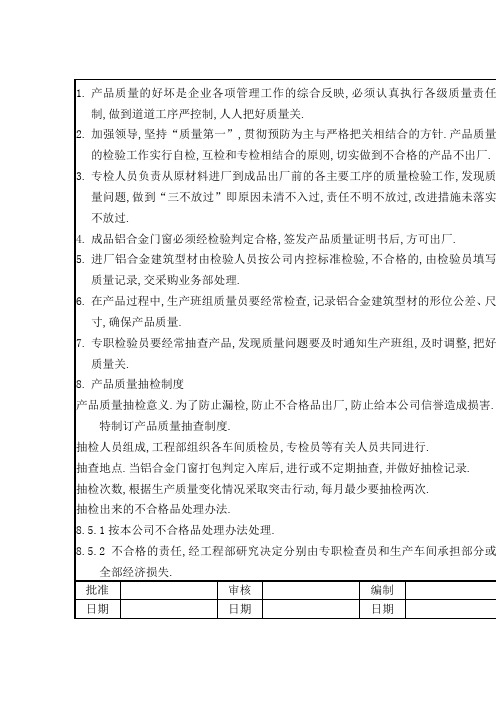
8.5.1按本公司不合格品处理办法产车间承担部分或全部经济损失.
批准
审核
编制
日期
日期
日期
8.产品质量抽检制度
产品质量抽检意义.为了防止漏检,防止不合格品出厂,防止给本公司信誉造成损害.特制订产品质量抽查制度.
抽检人员组成,工程部组织各车间质检员,专检员等有关人员共同进行.
抽查地点.当铝合金门窗打包判定入库后,进行或不定期抽查,并做好抽检记录.
抽检次数,根据生产质量变化情况采取突击行动,每月最少要抽检两次.
1.产品质量的好坏是企业各项管理工作的综合反映,必须认真执行各级质量责任制,做到道道工序严控制,人人把好质量关.
2.加强领导,坚持“质量第一”,贯彻预防为主与严格把关相结合的方针.产品质量的检验工作实行自检,互检和专检相结合的原则,切实做到不合格的产品不出厂.
3.专检人员负责从原材料进厂到成品出厂前的各主要工序的质量检验工作,发现质量问题,做到“三不放过”即原因未清不入过,责任不明不放过,改进措施未落实不放过.
4.成品铝合金门窗必须经检验判定合格,签发产品质量证明书后,方可出厂.
5.进厂铝合金建筑型材由检验人员按公司内控标准检验,不合格的,由检验员填写质量记录,交采购业务部处理.
6.在产品过程中,生产班组质量员要经常检查,记录铝合金建筑型材的形位公差、尺寸,确保产品质量.
7.专职检验员要经常抽查产品,发现质量问题要及时通知生产班组,及时调整,把好质量关.
检验抽样管理规范

检验抽样管理规范一、引言检验抽样是质量控制中的重要环节,对于确保产品质量的稳定性和可靠性具有重要意义。
为了规范检验抽样的管理,提高抽样效果和检验结果的准确性,制定本检验抽样管理规范。
二、适用范围本规范适用于所有需要进行检验抽样的生产企业和质量检验机构。
三、术语和定义1. 检验抽样:从一批产品或样本中抽取一部分进行检验的过程。
2. 抽样计划:根据抽样标准和抽样方法确定的抽样数量和抽样方案。
3. 抽样标准:根据产品质量要求和统计学原理确定的抽样判定依据。
4. 抽样方法:根据产品特点和检验要求确定的抽样方式,如随机抽样、系统抽样等。
5. 抽样误差:由于抽样过程中的随机性引起的检验结果与总体真值之间的差异。
四、抽样计划的制定1. 确定抽样标准:根据产品质量要求和统计学原理,确定适当的抽样标准,包括接收质量限、拒收质量限等。
2. 选择抽样方法:根据产品特点和检验要求,选择适当的抽样方法,如随机抽样、系统抽样等。
3. 确定抽样数量:根据抽样标准和抽样方法,确定抽样数量,保证抽样结果的可靠性和准确性。
4. 制定抽样方案:根据抽样标准、抽样方法和抽样数量,制定具体的抽样方案,包括抽样位置、抽样时间等。
五、抽样过程管理1. 抽样人员培训:对从事抽样工作的人员进行专业培训,提高其抽样技能和质量意识。
2. 抽样工具准备:确保抽样工具的准确性和可靠性,包括抽样容器、抽样器具等。
3. 抽样位置选择:根据抽样方案确定抽样位置,确保抽样的代表性和随机性。
4. 抽样过程记录:对抽样过程进行详细记录,包括抽样时间、抽样人员、抽样位置等信息。
5. 抽样样本处理:对抽样样本进行正确的处理和保存,防止样本污染和变质。
六、抽样结果分析与判定1. 检验数据收集:对抽样样本进行检验,收集相关的检验数据。
2. 检验结果统计:对检验数据进行统计分析,计算出相应的抽样参数,如平均值、标准差等。
3. 抽样误差评估:根据抽样误差的评估方法,评估抽样结果与总体真值之间的差异。
抽样检查标准

1.范围:
本文件规定了产品检验的抽样规范,适用于本企业生产的密封件生产过程中各工序的检查(包括自检、巡检),半成品的专检、成品的终检、产品入库前的最终检验、出库前的产品最终评审. 但:
⑴.当顾客提出特殊要求时,按双方商定的技术协议执行,并在相应的工艺文件、检
验文件(作业指导书)中规定。
⑵.本文件发布前规定的企业规范、技术文件、工艺文件、检验卡(作业指导书)与
本规范发生矛盾时,以本规范为准。
2.制定依据:
2.1.本文件参考GB2828.1标准制定。
2.2.在确保产品质量处于受控状态的情况下,结合本企业的实际情况而定。
3.职责:
3.1.技术人员在编写各技术文件、检验文件时,应符合本规范规定。
3.2.操作人员、检验人员严格按本规范规定执行。
3.3.各车间负责人监督操作人员贯彻执行本规范。
4.检验体制
根据XX/QP-8.2-01《检验和试验控制程序》的规定,本企业的检验体制列于表1。
5.抽样检验规定
5.1.本企业对产品特殊特性分成以下几类:
A 安全、关键特性-----▽☆
B 重要特性-------------﹡
C 一般特性-------------无符号
如客户有特殊规定,则按客户规定执行。
5.2进料检验
表1
5.2.工序自检及工序巡检及抽检抽样件数见表2
表2
5.3.成品检查(非破坏性检查)的抽样件数见表3
表3
注:1.当抽样数超过批的大小时,进行全数检查。
2.检验发现有不合格品时,将抽样数增大2倍,若全数合格,则可判定本批为合格。
5.4.最终评审的抽样件数见表4
表4。
公司产品抽检管理制度范文

公司产品抽检管理制度范文公司产品抽检管理制度范文第一章总则第一条为了规范公司产品抽检工作,提高产品质量,保护消费者权益,制定本制度。
第二条本制度适用于本公司所有产品的抽检工作。
第三条本制度的执行单位为公司质量管理部。
第四条本制度内容包括抽检计划的制定、抽检方式的确定、抽检样品的选择、抽检结果的处理等。
第二章抽检计划的制定第五条公司每年制定一年度抽检计划。
抽检计划应根据产品的特点和市场需求,合理安排抽检工作的频次和范围。
第六条抽检计划中应包括以下内容:(一)抽检时间:确定每次抽检的具体时间,确保抽检时间间隔合理。
(二)抽检对象:确定需要抽检的产品品类、规格、数量等。
(三)抽检范围:确定抽检的地区、门店、销售渠道等。
(四)抽检方法:确定抽检的方式,如随机抽检、定向抽检、定期抽检等。
第三章抽检方式的确定第七条抽检方式应根据产品特点、市场需求以及抽检计划的要求进行选择。
第八条抽检方式包括以下几种:(一)随机抽检:通过随机抽取样品进行检验,适用于大批量产品。
(二)定向抽检:根据产品的特定属性、市场反馈等,有针对性地抽检特定样品。
(三)定期抽检:按照一定的时间周期进行抽检,适用于需要长期监测的产品。
第九条具体抽检方式的选择由质量管理部根据产品特点和抽检计划进行确定,并应及时向相关部门通知。
第四章抽检样品的选择第十条抽检样品的选择应根据产品的特点和抽检目的确保代表性。
第十一条抽检样品的选择应采用以下原则:(一)覆盖性原则:抽检样品应涵盖产品的各个规格、型号、批次。
(二)典型性原则:抽检样品应从常规生产中随机抽取。
(三)比例原则:抽检样品的数量应符合统计学原则,确保抽检结果具有代表性。
第十二条抽检样品的选择应由质量管理部根据具体情况进行决策,并应及时向相关部门通知。
第五章抽检结果的处理第十三条抽检结果应及时进行分析和处理,以便采取相应的措施。
第十四条抽检结果分为合格、不合格和附加说明三种情况。
(一)合格:抽检样品符合产品质量标准。
抽样检验管理规定

1目的为检验人员检验提供依据,确保进料,制程品和成品的抽样检验供应商样品检验符合要求。
2范围适用于原物料进料检验、制程全检检验、供应商样品检验、物料验证测试、产品最终检验。
3定义3.1抽样检验:从“检验批”里,依照批量的大小抽出特定数量的样本,将该样本按照事先约定的检验办法加以检验,并将检验的结果,与预先决定的品质标准相比较,决定个别样本是否合格。
再将样本中不良品的数目与“抽样计划”中允许不良的数目相比较,以判定该检验批量是否允许。
3.2样本:由检验批中所抽取一个以上的单位制品所组成。
样品中所含的制品单位的数目,称为样本数或样本大小,用符号“n”表示。
3.3批:各种产品,凡是具有相同的来源,且在相同的条件下生产所得到的一群规格相同的产品,称为一个“批”,又称为一个制造批。
一个制造批“有需要可分为几个检验批”,但注意避免将一个以上的“制造批”合并为一个“检验批”。
3.4批量:“批量”是每个“检验批”的产品数量,其符号以“ N”表示,以“批量”来称呼。
3.5检验批:“检验批”构成的目的便于抽样检验的进行,即在该制成品送验批中,依其“批量” 的大小,按照抽样计划随机抽取样品加以检验,再依照抽样检验的原则来判定这个“检验批” 是否允收。
3.6Ac:接收数3.7Re:拒收数3.8AQL:接收质量限(以不合格品百分数或每百单位产品不合格数表示)3.9致命缺陷CR:指可危及人身安全、财产安全或重大环境污染的缺陷,用CR表示;3.10严重缺陷MA:指影响产品使用的缺陷,一般为结构性或装配性缺陷,用MA表示;3.11轻微缺陷MI:指不影响产品使用的缺陷,但影响产品的外观及档次,用MI表示。
4职责4.1品管部负责按全检、抽样标准进行检验。
5内容5.1本公司引用MIL-STD-105E (计数值的调整型抽样计划)的部分内容。
5.1.1IQC进料抽样基准:依进行MIL-STD-105E抽样检验,正常检验、加严及减量检验,特殊检验(特殊抽检),时机如下(一般开始为正常检验)以及按 5.1.5执行:正常检验转入加严检验:连续5 批中有2 批被拒收。
产品抽样检验标准

附件一:GB2828.1-2003样本量字码
GB2828.1-2003正常检验一次抽样方案
GB2828.1-2003加严检验一次抽样方案
GB2828.1-2003放宽检验一次抽样方案
5.2制程检验方式:
5.2.1制程首件检验方式:首件检验:1~3PCS/次
5.2.2 制程巡回检验方式:2PCS/1H
5.1.2 转移规则:
a. 从正常检验到加严检验
当进行正常检验时,若在连续五批来料中有两批经检验不合格,则后续来料转到加严检验。
b. 从加严检验到正常检验
当进行加严检验时,若连续五批来料合格,则后续来料转到正常检验。
c.从正常检验到放宽检验
当进行正常检验时,若连续10批来料检验合格,则后续来料转到放宽检验。
4. 11 抽样程序: 使用抽样计划判断批合格与否的过程,称为抽样程序。
4. 12 符 号:
N: 批量n: 样本大小
Ac: 合格判定数(允收数) Re: 不合格判定数(拒收数)
Ⅱ: 检验水准AQL: 合格质量水准(允收品质水准)
5作业内容:
5.1 抽样计划的说明:
5.1.1 本公司之进料檢验抽样采用GB2828.1-2003正常检查一次抽样计划,一般水平Ⅱ级抽样方法抽样,AQL值为6.5(%),尺寸抽检超过5PCS按照5PCS/批进行检验,低于5PCS进行全检。性能检测具体见各零部件检验规范。尺寸与性能检验为零缺陷允收。
4. 8 不 良 率: 不良品的表示方法。
任何已知数量的制品不良率,为制品中所含的不良品数除以单位产品的总数再乘以100%即得:
不良率=不良品个数*100%
检验单位产品总数
4. 9 检验方法: 用检验、量测、试验或其它方式将单位产品和其规定的要求加以比较的方法。
产品抽样检验规范

1.0目的指导检验员正确地按AQL抽样计划进行物料、半成品、成品的抽样检验,确保物料、成品检验的判定符合AQL标准之要求。
2.0 范围适用于本公司所有的进料、半成品、成品检验。
3.0职责检验员负责AQL抽样计划的执行。
4.0 定义4.1. AQL:(Acceptance Quality Limit)接收质量限,是供方能够保证稳定达到的实际质量水平,是用户能接受的产品质量水平。
4.2. CR:(Critical)致命缺陷。
4.3. Ma:(Major)严重缺陷,也称主要缺陷。
4.4. Mi:(Minor)轻微缺陷,也称次要缺陷。
5.0 作业细则5.1. 抽检方案依据接收质量限(AQL)检索的逐批检验抽样计划(GB/T 2828.1-2003)及抽样表,其中检查水平为一般检查水平Ⅱ级。
5.2. 样本的抽选按简单随机抽样(见GB/T 3358.1-1993的5.7), 从批中抽取作为样本的产品。
但是,当批由子批或(按某个合理的准则识别的)层组成时,应使用分层抽样。
按此方式,各子批或各层的样本量与子批或层的大小是成比例的。
5.3. 抽取样本的时间样本可在来料时、批生产出来以后、批生产期间或库存重检时抽取。
两种情形均应按5.2抽选样本。
5.4. 二次或多次抽样如在实际运作中,需要使用二次或多次抽样时,每个后继的样本应从同一批的剩余部分中抽选。
5.5. 正常、加严和放宽检验5.5.1. 检验的开始除非负责部门另有指示,开始检验时应采用正常检验。
5.5.2. 检验的继续除非转移程序(见5.5.3)要求改变检验的严格度,对连续的批,正常、加严或者放宽检验应继续不变。
转移程序应分别地用于不合格或不合格品。
5.5.3. 转移规则和程序(见附件1)5.5.3.1. 正常到加严当正在采用正常检验时,只要初次检验中连续5批或少于5批中有2批是不可接收的,则转移到加严检验。
本程序不考虑再提交批。
5.5.3.2. 加严到正常当正在采用加严检验时,如果初次检验的接连5批已被认为是可接收的,应恢复正常检验。
- 1、下载文档前请自行甄别文档内容的完整性,平台不提供额外的编辑、内容补充、找答案等附加服务。
- 2、"仅部分预览"的文档,不可在线预览部分如存在完整性等问题,可反馈申请退款(可完整预览的文档不适用该条件!)。
- 3、如文档侵犯您的权益,请联系客服反馈,我们会尽快为您处理(人工客服工作时间:9:00-18:30)。
产品检验抽样规定(DOC范本).DOC
1、目的:规范来料检验、成品检验之抽样水准、抽样方案以统一检验标准,确保来料及成品的质量稳定、良好。
2、范围:适用本公司IQC进料检验、OQC成品出货检验的所有产品。
3、职责:a)
IQ
C、OQC负责执行本规定 b)
品管部负责监督执行并视产品实际情况制定、修改本规定
4、程序:
A、来料检验1)抽样标准:按MIL-STD-105E (等同GB2828-87)Ⅱ级检查水平一次抽样进行2)合格质量水准AQL规定:① 电子料MAJOR:0、4;MINOR:
2、5② 组合料 MAJOR:
1、0;MINOR:
4、03)检查严格度:正常检验4)抽样方式:随机抽样5)抽样批量:每一订单作为一个检查批次以上规定了来料检验通用抽样检验标准,部分物料特别规定的除外,参见具体物料检验标准,特殊情况由物料QE决定。
B、成品出货检验1)抽样标准:按MIL-STD-105E(等同
GB2828-87)Ⅱ级检查水平一次抽样方案进行2)合格质量水准AQL规定:① 内销有线产品、寻呼机:
MAJOR:0、4;MINOR:
2、5② 内销无线产品:
MAJOR:0、65;MINOR:
2、5③ 外销产品:
在客户验货标准规定的AQL轻重缺陷均加严一个等级,特殊情况由产品QE决定3)检验严格度:正常检验4)抽样方式:随机抽样5)抽样批量① 一般以生产线每小时生产某机型的平均数量作为一个批量,有线电话一般以280PCS为一个批量②根据相应机型的质量控制计划来确定每批批量③生产清机尾数少于50PCS 应全检6)抽样标准转移规则正常检验时,若连续五批中有两批经初次检验不合格,则从下一批检验转到加严检验加严检验时,若连续五批中有两批经初次检验合格,则从下一批检验转到正常检验正常检验时,若连续批经初次检验合格,则从下一批检验转到放宽检验放宽检验时,若有一批不合格,则从下批检验转到正常检验抽样方案见附录1-4编制:审核:批准:。