根据相似准则原理介绍模化设计在压气机中的应用
相似理论在机械工程中的应用探讨
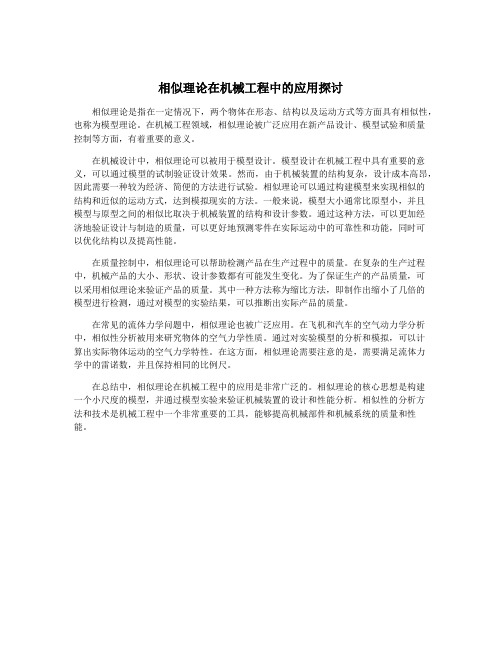
相似理论在机械工程中的应用探讨相似理论是指在一定情况下,两个物体在形态、结构以及运动方式等方面具有相似性,也称为模型理论。
在机械工程领域,相似理论被广泛应用在新产品设计、模型试验和质量控制等方面,有着重要的意义。
在机械设计中,相似理论可以被用于模型设计。
模型设计在机械工程中具有重要的意义,可以通过模型的试制验证设计效果。
然而,由于机械装置的结构复杂,设计成本高昂,因此需要一种较为经济、简便的方法进行试验。
相似理论可以通过构建模型来实现相似的结构和近似的运动方式,达到模拟现实的方法。
一般来说,模型大小通常比原型小,并且模型与原型之间的相似比取决于机械装置的结构和设计参数。
通过这种方法,可以更加经济地验证设计与制造的质量,可以更好地预测零件在实际运动中的可靠性和功能,同时可以优化结构以及提高性能。
在质量控制中,相似理论可以帮助检测产品在生产过程中的质量。
在复杂的生产过程中,机械产品的大小、形状、设计参数都有可能发生变化。
为了保证生产的产品质量,可以采用相似理论来验证产品的质量。
其中一种方法称为缩比方法,即制作出缩小了几倍的模型进行检测,通过对模型的实验结果,可以推断出实际产品的质量。
在常见的流体力学问题中,相似理论也被广泛应用。
在飞机和汽车的空气动力学分析中,相似性分析被用来研究物体的空气力学性质。
通过对实验模型的分析和模拟,可以计算出实际物体运动的空气力学特性。
在这方面,相似理论需要注意的是,需要满足流体力学中的雷诺数,并且保持相同的比例尺。
在总结中,相似理论在机械工程中的应用是非常广泛的。
相似理论的核心思想是构建一个小尺度的模型,并通过模型实验来验证机械装置的设计和性能分析。
相似性的分析方法和技术是机械工程中一个非常重要的工具,能够提高机械部件和机械系统的质量和性能。
相似原理 在燃气轮机离心压缩机组能耗计算中的应用

* 郭海涛,男,工程师。
2007年毕业于中国石油大学(北京)油气储运工程专业,获硕士学位。
现在中国石油天然气股份有限公司规划总院从事油气储运前期规划研究工作。
地址:北京市海淀区志新西路3号,100083。
E-mail:guo_haitao@文章编号:1004-2970(2014)06-0016-05郭海涛*1 朱锋1 赵俊1 苏倩2(1.中国石油天然气股份有限公司规划总院;2.中国石油大学(北京))郭海涛等. 相似原理在燃气轮机离心压缩机组能耗计算中的应用. 石油规划设计,2014,25(6):16~19,32摘要 燃气轮机是输气管道压气站中离心压缩机的主要驱动装置。
燃气轮机的变工况特性使其热耗率随工况条件的变化而变化,因此,在工艺计算中难以准确计算燃气轮机的能耗值。
介绍了燃气轮机热耗率的主要影响因素,引入相似参数的概念,将影响燃气轮机工况的大气压力、环境温度、动力透平转速和负载率4个主要参数代入相似参数中,利用燃气轮机相似工况原理,分析了变工况条件下燃气轮机热耗率的变化规律,并用最小二乘法拟合热耗率变化关系曲线,能够较准确地计算出输气管道上燃气轮机离心压缩机组的能耗,这对于输气管道的优化运行具有一定的指导意义。
关键词 燃气轮机;热耗率;输气管道;相似工况;相似参数中图分类号:TE974 文献标识码:A DOI :10.3969/j.issn.1004-2970.2014.06.005燃气轮机具有转速高、输出功率大、变速性能好、调速范围广、可与离心压缩机直接连接等优点,同时,燃气轮机的燃料气取自管输天然气,气源供应可靠,因此,燃气轮机特别适用于电源供应条件较差的偏远地区[1]。
西北地区是我国能源战略通道,多条大口径、高压力天然气管道布局在地广人稀的戈壁滩,管道沿线电力依托条件薄弱,因此,燃气轮机成为离心压缩机的主要驱动装置。
以西气东输管道二线为例,燃气轮机离心压缩机组(简称燃驱压缩机组)约占整个管道压缩机组配置的70%。
相似原理在化工中的应用
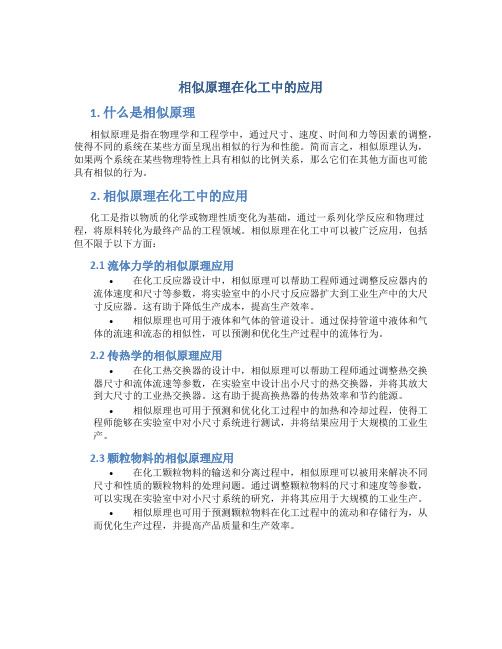
相似原理在化工中的应用1. 什么是相似原理相似原理是指在物理学和工程学中,通过尺寸、速度、时间和力等因素的调整,使得不同的系统在某些方面呈现出相似的行为和性能。
简而言之,相似原理认为,如果两个系统在某些物理特性上具有相似的比例关系,那么它们在其他方面也可能具有相似的行为。
2. 相似原理在化工中的应用化工是指以物质的化学或物理性质变化为基础,通过一系列化学反应和物理过程,将原料转化为最终产品的工程领域。
相似原理在化工中可以被广泛应用,包括但不限于以下方面:2.1 流体力学的相似原理应用•在化工反应器设计中,相似原理可以帮助工程师通过调整反应器内的流体速度和尺寸等参数,将实验室中的小尺寸反应器扩大到工业生产中的大尺寸反应器。
这有助于降低生产成本,提高生产效率。
•相似原理也可用于液体和气体的管道设计。
通过保持管道中液体和气体的流速和流态的相似性,可以预测和优化生产过程中的流体行为。
2.2 传热学的相似原理应用•在化工热交换器的设计中,相似原理可以帮助工程师通过调整热交换器尺寸和流体流速等参数,在实验室中设计出小尺寸的热交换器,并将其放大到大尺寸的工业热交换器。
这有助于提高换热器的传热效率和节约能源。
•相似原理也可用于预测和优化化工过程中的加热和冷却过程,使得工程师能够在实验室中对小尺寸系统进行测试,并将结果应用于大规模的工业生产。
2.3 颗粒物料的相似原理应用•在化工颗粒物料的输送和分离过程中,相似原理可以被用来解决不同尺寸和性质的颗粒物料的处理问题。
通过调整颗粒物料的尺寸和速度等参数,可以实现在实验室中对小尺寸系统的研究,并将其应用于大规模的工业生产。
•相似原理也可用于预测颗粒物料在化工过程中的流动和存储行为,从而优化生产过程,并提高产品质量和生产效率。
3. 相似原理的局限性和挑战尽管相似原理在化工领域有着广泛的应用,但其存在一些局限性和挑战,包括但不限于以下方面:•相似原理仅适用于具有相似物理特性的系统。
相似理论及其在机械工程中的应用探讨

相似理论及其在机械工程中的应用探讨摘要:现代科学技术的发展是建立在理论基础之上的,在机械工程领域发展中,相似理论起到了非常大的作用。
近些年伴随着我国工业现代化的高速发展,机械工程行业是取得了非常大的突破,将相似理论应用于机械工程中,对于机械工程的发展以及创新具有重要价值。
基于此,本文对相似理论在机械工程中的运用展开了分析与探讨,仅供参考。
关键词:相似理论;机械工程;价值在20世纪,有学者提出了相似理论,自其提出之日起就受到很多学者和专家的关注和重视。
众所周知,我们生活中有很多现象的作用与原理没有太大区别,它们之间存在者极为密切的联系。
相似理论,顾名思义是对现实生活中出现的影响相似作用的元素及其体现出来的物理性质进行的研究。
目前,伴随着现代科学技术水平的快速提升,相似理论也在实践应用中得以不断的完善。
本文对相似理论及其在机械工程领域的应用进行了简要分析。
1 相似理论的实质与特点从本质上来见,相似理论就是对现实生活中具有相似特征的所有物体和现象进行说明和分析的理论,也可以说是同样现象的共同点实施分析的一种力量。
然而,这个理论在模型架构中起着重要的作用。
根据现有的计算机模拟技术,可以基于以相似理论为中心的预先功能开展相关设计,以虚拟形式设计模型原型,从而实现相应的模型构建。
相似理论的发展应当具有下面一些特征:(1)自然现象的科学说明,(2)对应现象中包含的物理原理不是偶然事件,而是特定的客观条件。
(3)不可以仅仅根据个人主观推测来确定各物理量,而是要遵从客观事实。
在当前的各个领域研究中,相似理论不仅集中于讨论物理问题,而且已经成为机械工程设计的主要基础,被很好地开发和应用。
随着科学技术的高度发展,未来会有越来越多的新技术和理论涌现。
相似理论一般从物理现象开始,对每个条件和现象进行严格的探索和发现。
同时基于当前数学算法来形成某种结论,但是这一结论只是打开了研究的方向。
同时,由于研究的物理现象范围很广,所以相似理论在在各个领域都有不同的应用程度。
相似原理与模化实验

1 6 226.8 10 80.64 pa 800 11.25
(3) 说明:以空气为介质作模型:由Re相等,则
m lp 30 p lm
m 180m / s
此时空气压缩性不能忽视,故不能用空气作介质,
则用水质后,
m 11.25m / s
5.3相似定理
三个定理回答了三个问题:
1.实验研究必须测量哪些量→相似第一定理 2.如何做到模型与原型相似→相似第三定理 3.如何对测量结果进行加工整理→相似第二定理
5.3相似定理
5.3相似定理
5.3相似定理
例:
总结: ⒈相似第一定理是对相似性质的总概括,阐明了 相似现象中各物理量之间存在一定关系。 ⒉对于复杂的现象,常存在几个相似准数。 例:对不可压缩粘性流体的不稳定等温流动共有 四个: t H0 均时性准数: 不稳定流体流动必与 t 有关。 l l Re 雷诺准数: 与粘性有关的流动,惯性力/粘性力 付鲁德准数: Fr
b 1 c 1 0 ab vd 1 1 v k d , k
1 b
Re
vd
5.4量纲分析和π定理
5.4.2.2 布金汉(Buckingham)定理
对于某个物理现象或过程,如果存在有n个变量互为函数 关系, f(a1,a2, …an)=0 而这些变量含有m个基本量纲,可把这n个变量转换成为有 (n-m)=i个无量纲量的函数关系式 F(1,2, … n-m)=0 这样可以表达出物理方程的明确的量间关系,并把方程中 的变量数减少了m个,更为概括集中表示物理过程或物 理现象的内在关系。
or 其中:
1 f( 2, 3 n)
1 ——非定性准数 2 n ——定性准数
燃气轮机燃烧室模化准则的数值模拟的分析研究

摘要摘要根据燃气轮机燃烧室的发展趋势,相似理论与燃气轮机燃烧室工作过程结合的是研究燃气轮机燃烧室模化理论的重要手段,提炼出基于正常实验条件下的近似模化准则,为燃气轮机燃烧室实验和设计提供基础性研究依据。
本文研究的主要工作为:采用数值模拟方法,对燃气轮机燃烧室模化准则的适用范围以及压力指数选取方面进行一些探讨。
首先,总结了前人从化学反应动力学和流体力学中推导出一些关于燃烧效率的模化理论,以及在实践经验中结合这些理论总结出的燃烧室实验方面的近似模化准则。
接着,介绍了数值计算的软硬件平台,主要包括网格生成技术和计算燃烧效率公式的主程序。
采用数值模拟方法,研究了在高压和低压下燃烧室内部流场和燃烧温度的变化,验证了其模化准则的适用范围。
最后,采用数值模拟方法,分别研究了扩散和预混两种不同类型火焰对燃气轮机燃烧室效率模化中压力指数选取的影响,以及对某燃烧室进行了数值模拟,分析了不同的主燃区过量空气系数和进口温度对燃烧效率的影响。
该项工作为进一步开展燃气轮机燃烧室模化方面的的研究提供了一些理论分析和数值模拟方面的依据,也对在实际的生产实践中的燃烧室设计及模化实验有一定的参考意义。
关键词:燃气轮机燃烧室;模化准则;燃烧效率:压力指数;数值模拟AbstractAbstractTIANXueqing(EngineeringThermophysics)DirectedbyHUANGWeiguangBasedondevelopmenttendencyofgasturbinecombustor,combiningthesimilaritytheorywiththeworkingprocessofgasturbinecombustorisoneofthemostimportantmeansinthefieldofmodelingcriterionofthegasturbinecombustor,achievingthesimilaritycriterionsontheexperimentcondition,theaimistoofferthereferenceforthedesignandexperimentofthegasturbinecombustor.Theworkdescribedinthisdissertationisprobingthescopeofapplicationandtheaccessofthepressureexponentofthemodelingcriterions,makinguseofthenumericalsimulationmethod.Firstandforemost,somemodelingtheoriesofcombustionefficiencyareresultedfromthechemicalreaction—controlledtheoryandthefluidmechanics,somesimilaritycriterionsofgasturbinecombustorarederivedfromthecombinationexperimentalexperiencewiththesetheories,Subsequently,thesoftwareandhardwareplatformusedinthenumericalsimulationistobeintroduced,mainlyincludinghowtogeneratemeshandthemainprogrammeofcombustionefficiency.Makinguseofthenumericalsimulationmethod,comparingtheflowfieldandthetemperaturefieldbetweenthehi曲pressureandtheslightpressureingasturbinecombustor,thescopeofapplicationofthemodelingcriterionsistobeverified.Atlast,makinguseofthenumericalsimulationmethod,theaccessrangeofthepressureexponentofthemodefingcriterionsisdifferent,whetherthecombustionprocessisreaction-controlledordiffusioncontrolled.Changingtheexcessaircoefficientintheprimarycombustionzoneandthetemperatureoftheinletairishowtoinfluencethecombustionefficiencyofthegasturbinecombustor.ThisresearchisaninitialworkforthefurtherinvestigationonthetheorylI垒!塑!!一一——analysisandnumericalsimulationinthefieldofmodelingcriterionofgasturbinecombustor,whichisareferenceforthemodelingexperimentandthedesigllofgasturbinecombustorintheproductivepractice.Keywords:GasTurbineCombustorCombustionEfficiency;ModelingCriterion;PressureExponentNumericaISimulation¨I第一章绪论第一章绪论1.1燃烧室模化实验意义简述由于目前燃气轮机燃烧室的设计方法在准确性、可靠性方面还有待于进一步的改进和提高,因此燃烧室实验及其调整工作在燃气轮机产品的设计、研制及燃气轮机事业发展中起很重要的作用。
相似理论在机械工程中的应用探讨

相似理论在机械工程中的应用探讨相似理论是一种非常重要的理论,在机械工程领域中也有许多应用。
相似理论是指在某些特定的条件下,不同的物理现象之间可能存在相似性,从而可以通过一些基本的模型,对其进行分析和研究。
相似理论在机械工程中的应用非常广泛,涉及到众多领域。
一、机械加工首先,相似理论在机械加工领域中有着广泛的应用。
在机械加工时,为了保证制造成品的质量,需要对机械加工过程进行分析和优化。
通过相似理论,可以将复杂的机械加工问题简化为基本的模型,从而进行分析和研究。
例如,在考虑机械加工时,我们不仅需要考虑加工材料的物理性质和加工工艺的参数,还需要考虑刀具形状、尺寸、材料等因素。
通过相似性比较,可以建立一个基本的模型,这个模型可以用于理解和预测不同的加工生产的状况。
二、风力机相似理论对于风力机的研究和开发也有着非常重要的意义。
风力机是一种非常重要的风能利用设备,在代替传统的能源中起到了越来越重要的作用。
在风力机研发的过程中,相似理论可以通过建立基本的模型,对不同的风力机进行研究和分析。
例如,在研究风力机的性能时,相似理论可以提供一个基本的模型用于分析和研究各种风力机的性能,包括功率、转速、速比等。
三、轴承相似理论在轴承领域中也有着非常广泛的应用。
轴承是机械系统传动的重要部分,它影响整个机械系统的精度、稳定性和寿命。
通过相似理论,可以将轴承系统与其他系统进行比较。
例如,在理解和优化轴承系统性能方面,相似性比较可以帮助我们建立数学模型,对涉及到的所有机械系统进行分析和比较,从而确定最适合的轴承系统。
四、气体涡流另一个领域,相似理论在气体涡流研究方面也有着广泛的应用。
气体涡流的研究是机械工程领域的重要研究领域之一,它在轴承、能源和空气动力学等领域占据着非常重要的地位。
通过相似性比较,可以将无穷无尽的气体涡流问题转化为更简单的表达式,从而减少研究的复杂度和难度。
相似模型可以用于预测气体涡流中需要进行的调整和优化。
相似理论在机械工程中的应用探讨
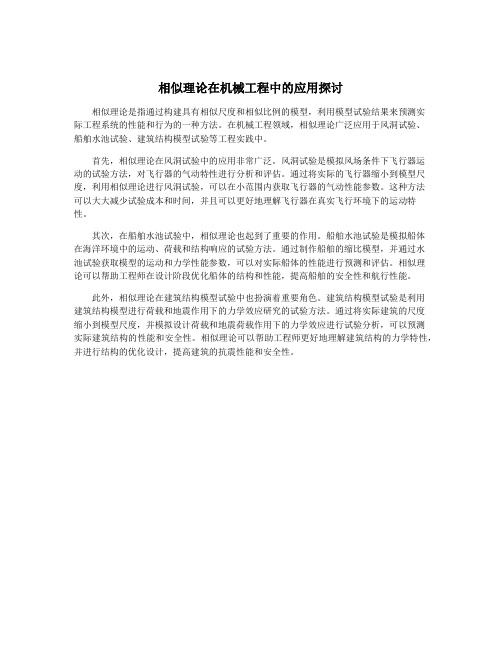
相似理论在机械工程中的应用探讨
相似理论是指通过构建具有相似尺度和相似比例的模型,利用模型试验结果来预测实
际工程系统的性能和行为的一种方法。
在机械工程领域,相似理论广泛应用于风洞试验、
船舶水池试验、建筑结构模型试验等工程实践中。
首先,相似理论在风洞试验中的应用非常广泛。
风洞试验是模拟风场条件下飞行器运
动的试验方法,对飞行器的气动特性进行分析和评估。
通过将实际的飞行器缩小到模型尺度,利用相似理论进行风洞试验,可以在小范围内获取飞行器的气动性能参数。
这种方法
可以大大减少试验成本和时间,并且可以更好地理解飞行器在真实飞行环境下的运动特
性。
其次,在船舶水池试验中,相似理论也起到了重要的作用。
船舶水池试验是模拟船体
在海洋环境中的运动、荷载和结构响应的试验方法。
通过制作船舶的缩比模型,并通过水
池试验获取模型的运动和力学性能参数,可以对实际船体的性能进行预测和评估。
相似理
论可以帮助工程师在设计阶段优化船体的结构和性能,提高船舶的安全性和航行性能。
此外,相似理论在建筑结构模型试验中也扮演着重要角色。
建筑结构模型试验是利用
建筑结构模型进行荷载和地震作用下的力学效应研究的试验方法。
通过将实际建筑的尺度
缩小到模型尺度,并模拟设计荷载和地震荷载作用下的力学效应进行试验分析,可以预测
实际建筑结构的性能和安全性。
相似理论可以帮助工程师更好地理解建筑结构的力学特性,并进行结构的优化设计,提高建筑的抗震性能和安全性。
- 1、下载文档前请自行甄别文档内容的完整性,平台不提供额外的编辑、内容补充、找答案等附加服务。
- 2、"仅部分预览"的文档,不可在线预览部分如存在完整性等问题,可反馈申请退款(可完整预览的文档不适用该条件!)。
- 3、如文档侵犯您的权益,请联系客服反馈,我们会尽快为您处理(人工客服工作时间:9:00-18:30)。
根据相似准则原理介绍模化设计在压气机中的应用一、概述模化设计是发展大型新压气机的重要手段。
通观国内外压气机发展的历史,压比较高的大容量压气机一般都是在原来性能比较优秀但压比较低的小容量压气机(我们称之为母型机)的基础上采用前后加级等措施提高压比和流量而得到的。
由于压气机技术比较复杂,还有一些比较深刻的内涵目前还不太为人们所知,取得一台性能良好的全新压气机需要花很多的精力与费用,因此有了一台母型之后,模化加级设计就成为进一步发展新压气机的主要手段。
二、原理介绍Π定理:Π定理描述了任一物理过程或者物理方程所相关的有梁刚物理量与相应的无量纲参数之间在的关系。
若一个方程包含了n个物理量,每个物理量的量纲均有r个独立的基本量纲组成,则这些物理量可以并只可以组合成n−r个独立的无量纲参数,称为Π数。
选择r个独立的物理量为基本量,将其余n−r个物理量作为导出量,依次同基本量作组合量纲分析,可以求得n−r 个互相独立的Π数[1]。
设原来的方程为:x1=φ(x2,x3,…,x n)经量纲分析后,由相互独立的n−r个Π数组成新的方程:Π1=f(Π2,Π3,…,Πn−r)Π定理极大的减少了描述物理过程的物理量,并且在一定程度上揭示了物理过程的本质[2]。
流动相似原理指出:如果两个流动的相似准则相等,则流动就相似,对于透平机械内的流动而言,在几何相似的条件下,流动相似的条件是:第一级动叶进口的绝对无因次速度对应相等,第一级动叶进口无因次圆周速度对应相等,即:λc1=常数,λu1=常数由气动力学知识可知,无因次速度λc1与无因流量q(λc1)为单值函数,因此,相似条件转换为:q(λc1)=常数,λu1=常数如果以q(λc1)和λu1作为自变量绘制压气机特性,则可以得到压气机的通用特性曲线。
εc∗=f1[q(λc1),λu1]ηc∗=f2[q(λc1),λu1]两个流动相似的压气机,速度三角形相似,所以相似条件又可以换为:q(λcz)=常数,λu1=常数λoz是压气机的无因次轴向分速度。
由流量公式:q(λcz)=G√T1∗p1∗F1K≈G√T a∗p a∗F1K无因次速度:λu1=1√KRT a∗=1 60√KRT a∗对一台压气机的两个不同工况,相似的条件是:G√T a ∗p a∗=常数,√T a∗=常数对同一台压气机,可用G√T a ∗p a∗和√T a∗作为自变量绘制压气机特性曲线。
还可使用标准流量和标准转速:G st =G 101300p a ∗√T a ∗288n st =n√288T a∗压气机模化设计要求选择好母型机,并且要能够绘制出母型机的特性曲线[3]。
模化准则(1) 通流部分几何相似,包括表面粗糙度相似。
(2 ) 平均绝热指数k 相等。
(3) 表示压缩特性的马赫数M 相等。
(4) 表示粘性特性的雷诺数R 在自动模化区域。
(5) 表示气体速度与圆周速度之比斯特鲁哈尔数Sℎ相等, 即流量系数φ相等。
模化设计中需要进行模化机的雷诺数计算,认为雷诺数大于2∼3×105时,在自动模化区,小于这个数值,不满足相似准则。
假如母型压气机的特性曲线是由λc1和λu1为自变量表示的,当已知流量G 、压比εc ∗、进气温度T c ∗和进气压力p a ∗时,在保证一定效率,具有一定喘振裕度的条件下,按给定压比εc ∗,在母型压气机特向上选取模化点,即可以算出压气机进口截面面积:F 1=G √T a∗p a ∗q(λcz )K由于所设计的压气机与母型压气机为几何相似,所以轮毂比相同,因此,可以求出设计压气机第一级进口外径:d 1i =√4F 1π(1−d 12)根据模化点的λu1,可以求出圆周速度和转速: u 1=λu1a cru 1i =2u 11+d 1得:n i =60u 1iπd 1i模化系数定义为:m i =d 1id 1 由此可以求出其他几何尺寸。
如果母型机的特性曲线是以εc ∗=f 1[q(λc1),λu1]和ηc ∗=f 2[q(λc1),λu1]的形式给出,则在母型机特性曲线上找到设计压气机的压比,从而求出G st 和n st ,但此时,设计压气机的标准流量和标准转速必须要根据q(λcz )和λu1相等的条件得出。
三、应用举例应用举例1:设计氦气轮机过程中利用空气作为介质进行工作模拟 步骤简介:第一步:根据设计马赫数和工质选取合适的相似准则,换算出模拟实验条件 第二步:根据该实验条件,得出不同转速不同流量情况下压气机模型的性能曲线第三步:利用相似准则之间的关系换算出压气机原型的实验性能图,与设计性能图相比较,对压气机的设计进行校核与优化[4](1) 选取相似准则当压气机在氦气和空气条件下工作时,两种工质的分子量、绝热指数k 和比热容等物性差别较大,不满足物质相似的条件,所以不同工质条件下的相似分析不是完全相似的,而是简化的近似相似分析。
不同工质条件下,在集合相似满足的基础上轴流压气机的相似准则为:在马赫数M <0.5时,保证压气机流量系数、多变负荷系数、雷诺数相等或者在同一自模化区内,即可保证压气机模型与原型的相似。
(2) 选择试验参数用空气代替氦气做压气机性能试验时,选择空气的进口温度、压力、压比、转速和质量流量作为宏观试验检测控制量,这些参数可通过上述分析的相似准则由氦气工况转换确定。
空气进口温度:进口温度的选择范围并无限制,为了试验及计算的方便,实验中可以选取与氦气轮机相同的进口温度He Air T T空气进口压力:氦气压气机设计工况叶弦雷诺数,各级中最低约5103⨯左右,略大于临街雷诺数5102⨯,大致是空气工质普通规格压气机的四分之一到二分之一,数值较低。
由于试验中要满足雷诺数相等或者与圆形雷诺数在同一个自模区内,所以进口压力的选择范围较小,由雷诺数Re 相等或在同一自模化区内求得模拟试验时压气机入口压力He P ,设计工况点的空气试验压力为5103.2⨯左右[5]。
模拟实验压比:又流量系数相等和连续方程可以得出原型与模型进出口比容比相等,即有Air He v v v v )/()/(2121=,联立理想气体状态方程得到原型与模型压比关系式Air m He m )()(11εε=,m 为多变指数。
模拟试验转速:由多变压头系数相等、圆周线速度及多变能量头得到模拟实验转速换算关系空气质量流量:体积流量与转速成正比,再联立理想气体状态方程求得空气的质量流量。
(3) 根据以上参数进行试验,得到的曲线如下图所示:氦气压气机特性图如下:由于漏流、二次流和末端边界层的影响不可避免,故空气与氦气条件下压气机的性能换算有待进一步的细化研究。
应用举例2:设计研制一台如下性能指标和进口条件的海水淡化装置用的离心蒸汽压气机 (1) 参数如下压比2.1=ε 蒸汽流量h kg G /1000= 效率75.0=i η 进口压力Pa P i 21333= 进口温度℃64=i T母型机为一单级离心空气压气机:叶轮外径mm D 3552= 叶片数20=Z 进口内径mm D 1060= 叶片厚度mm 62.3=δ 进口外径mm D 46.2131= 扩压器进口直径mm D 4.4363=叶轮进口宽度mm b 401= 扩压器出口直径mm D 5044= 叶轮出口宽度mm b 21.172= 扩压器进口宽度mm b 6.173= 叶轮进口构造角︒=381P B 扩压器出口宽度mm b 33.174= 叶轮出口构造角︒=902P B 蜗壳出口直径mm D 2006=(2) 模化过程会遇到的问题:a.水蒸汽为实际气体,将其看作理想气体进行模化是否合理?b.水蒸汽的绝热指数K=1.328,与空气的绝热指数K=1.4是不相等的,这会带来怎样的误差?c.当模化是在保证进、出口截面比容比相等的条件下进行,而不可能保证所有截面上速度三角形相似,造成造成母型机和新型机的马赫数的不等,这会对模化造成什么影响?d.由于工质的变更,导致气体常数变化,使得新机的雷诺数低于临界值,这会有什么影响?(3) 由相似理论得知,保证两台离心压气机流动相似,必须确保做到几何相似、运动相似和动力相似。
换句话说要确保以下各相似准则数对应相等: 表征气体压缩性的马赫数:KRTC M =表征气体粘性的雷诺数:μρCDR e =表征气体换热的普朗特数λμp r C P =以及努塞尔数λαlN u = 表征不稳定流动影响的斯特洛哈里数:lCtSh =表征地球引力作用的福雷德数:lC F r 2=(4) 考虑到实际气体的复杂性,在工程上引入一些假设:a.认为气体在压缩过程中,与外界无热交换,即忽略Nu 数和Pr 数的影响。
b.不考虑喷射冷却和进口处水滴的降落。
c.研究的只是定常的或准定常的通流部分的流动,因而可以忽略习Sh 数的影响。
d.假定进人压气机的初始速度和气流的紊流度没有本质上的影响。
e.认为被压缩工质的比热容Cp 和Cv 为常数,即绝热指数K 为常数的理想气体。
在这样一些假设条件下,可把完全相似的关系式:),,,,,,,,(,,2p i i i i C n D K P Q f N λγρηε= (1)其中i N 为内功率,γ为运动粘滞系数,λ为工质导热系数,Q 为容积流量,n 为叶轮转速,简化到压气机工程可做到的部分相似关系式:),,,(),,,(,,2222223222K R M F K D u KRT u u D QF u D N eu u i ii i i ϕγρηε== (2) 上式为压气机工程中常用的部分模化所依据的基本原理关系式。
该式表明:在几何相似的条件下,只要保持母型机和新机型相似准则:流量系数ϕ,切向马赫数u M ,工作轮出口雷诺数eu R 以及比热比K 相等,则新机型和母型机的流动相似。
根据式(2)考虑所采用的模化方法可得到如下的模化关系:i iT R Y YRT Q Q ''''==12λ (3) ii YRT T R Y nn '''=' (4) ii i i i i RT T R Y Y P P N N ''''='23)( (5)i iηη=' (6) 其中1),1(1-=-=m m Y σεσσ 1),1(1-''='-''=''m m Y σεσσm m ,' 质的多变指数。
分别为新机和母型机工这样,根据式(3)、(4)、(5)、(6)关系,利用母型压气机的特性,只要寻求合适的模化点,有足够的喘振裕度,具有较高效率,又能满足新机流量和压比的要求,则可以实施模化设计[6]。
(5) 模化误差分析:a. u uM M ≠'的影响分析: 在本模化实验中,模化比1=λ,新机型和母型机通流部分的尺寸基本一致,而且ϕϕ=',因而可以用u M 来衡量对模化性能的影响。