电石的生产工艺原理
电石生产工艺流程

目录
第一节:电石生产基础知识 第二节:电石生产的基本原理及工艺流程 第三节:电石生产所需原料 第四节:原料中杂质对电石生产的影响 第五节:电石炉本体设备简介 第六节:电石生产操作中的事故及不正常现象
• 第一节:电石生产基础知识
• 概念:
电石化学名称为碳化钙,工业名称为电石,分子式为CaC2,分子量为64.10
电石的化学性质
电石的化学性质很活泼,在适当温度下能与许多的气体、液体 发生化学反应。 ①碳化钙不仅能被液态的或气态的水所分解,而且也能被物 理的或化学结合的水所分解。 在水过剩条件下,即将碳化钙浸于水中,反应依下式进行: CaC2+H2O=Ca(OH)2+C2H2 被滴加水分解时,还发生如下反应: CaC2+Ca(OH)2=CaO+C2H2 吸收空气中水份而分解: CaC2+H2O=CaO+C2H2 ② 在没有任何水份条件下,将电石在氢气流中加热至2200℃ 以上时,就有相当量的乙炔发生: CaC2+H2=Ca+C2H2 当加热到2275℃时,所生成的钙开始升华。
SiO2+2C=Si+2CO-574kJ Fe2O3+3C=2Fe+3CO-452kJ Al2O3+3C=2Al+3CO-1218kJ MgO+C=Mg+CO-486kJ 上述反应不仅消耗电能和碳材,而且影响操作,破坏炉底,特别是氧 化镁在熔融区迅速还原成金属镁,而使熔融区成为一个强烈的高温还原 区,镁蒸气从这个炽热的区域大量逸出时,其中一部分镁与一氧化碳立 即起反应,生成氧化镁: Mg+CO=MgO+C+489kJ 此时,由于反应放出强热形成高温,局部硬壳遭到破坏,使带有杂质 (Si、Fe、Al、Mg)的液态电石侵蚀了炉底。 另一部镁上升到炉料表面,与一氧化碳或空气中的氧反应: Mg+ O2=MgO+614kJ 当镁与氧反应时,放出大量的热,使料面结块,阻碍炉气排出,并产 生支路电流。还破坏局部炉壳,甚至使熔池遭到破坏,堵塞电石流出口 。实践证明,石灰中氧化镁含量每增加1%,则功率发气量将下降10~ 15L/kW·h。
电石生产工作原理
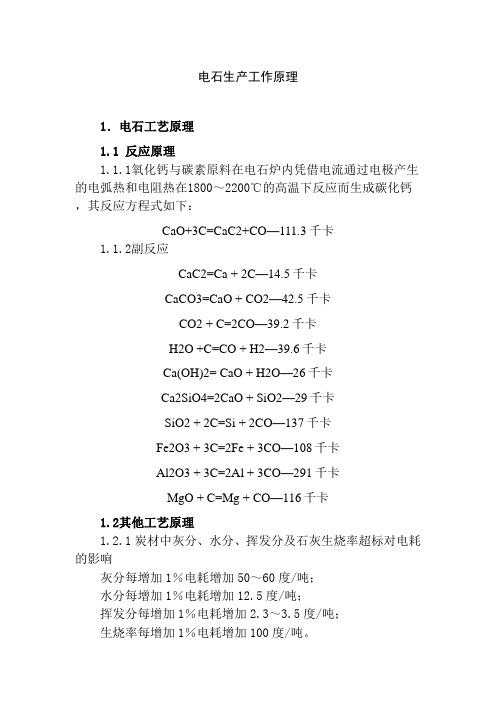
电石生产工作原理1.电石工艺原理1.1 反应原理1.1.1氧化钙与碳素原料在电石炉内凭借电流通过电极产生的电弧热和电阻热在1800~2200℃的高温下反应而生成碳化钙,其反应方程式如下:CaO+3C=CaC2+CO—111.3千卡1.1.2副反应CaC2=Ca + 2C—14.5千卡CaCO3=CaO + CO2—42.5千卡CO2 + C=2CO—39.2千卡H2O +C=CO + H2—39.6千卡Ca(OH)2= CaO + H2O—26千卡Ca2SiO4=2CaO + SiO2—29千卡SiO2 + 2C=Si + 2CO—137千卡Fe2O3 + 3C=2Fe + 3CO—108千卡Al2O3 + 3C=2Al + 3CO—291千卡MgO + C=Mg + CO—116千卡1.2其他工艺原理1.2.1炭材中灰分、水分、挥发分及石灰生烧率超标对电耗的影响灰分每增加1%电耗增加50~60度/吨;水分每增加1%电耗增加12.5度/吨;挥发分每增加1%电耗增加2.3~3.5度/吨;生烧率每增加1%电耗增加100度/吨。
1.2.2 MgO含量超标对电石生产的危害1.2.2.1氧化镁在电石炉内熔融区还原成金属镁,镁蒸汽与CO反应生成氧化镁产生大量的热量,使局部硬壳被破坏,电石外流,侵蚀炉墙;1.2.2.2另一部分镁上升到炉表面与CO或O2反应,放出大量的热,使料面形成红料结块,支路电流升高,阻碍炉气排出,炉压增高;1.2.2.3镁与N2发生反应生成氮化镁,致使电石发粘,不易流出;1.2.2.4影响电石质量,石灰中每增加1%的氧化镁,功率发气量下降10~15。
1.2.3 SiO2含量超标对电石生产的危害1.2.3.1生成碳化硅沉积于炉底,造成炉底升高;1.2.3.2与铁作用生成硅铁损坏炉壁铁壳或出炉时烧坏炉嘴、电石锅等;1.2.3.3含量过高,生石灰易粉化、易碎,进入炉内易塌料;1.2.3.4对发气量有一定影响,含量愈高则功率发气量愈低。
电石生产工艺流程

电石生产工艺流程电石是一种由石灰石和焦炭经高温反应得到的产物,主要用于生产氯碱化工产品。
下面将介绍电石的生产工艺流程。
电石生产的第一步是选矿,必须选择纯度较高的石灰石作为原料。
石灰石在高温下会分解产生二氧化碳和石灰。
为了提高产量和质量,选矿过程中需要除去杂质。
选矿之后,下一步是将石灰石经过破碎和磨细处理,以获得适合反应的颗粒度。
破碎主要通过破碎机完成,而磨细则通过研磨机实现。
破碎和磨细处理完成后,石灰石粉末将进入煤气炉,石灰石与焦炭的混合物在此处进行高温反应。
煤气炉内需要控制好反应温度和氧气含量,使石灰石和焦炭充分反应而不会发生过度燃烧。
在高温煤气炉内,焦炭还原石灰石,产生一氧化碳和氮气。
石灰石中的碳酸钙经过反应变为氧化钙。
氧化钙与水反应会产生氢氧化钙,并放出大量的热量。
化学反应方程式如下:CaCO3 + 2C -> CaO + 2COCaO + H2O -> Ca(OH)2 + ΔH反应完成后,产生的氢氧化钙和二氧化碳会与煤气中的一氧化碳反应,生成乙炔。
乙炔是电石生产的主要产物。
得到乙炔之后,需要进一步纯化。
乙炔通过冷却和净化过程,去除其中的杂质,包括硫化合物、重金属等。
最后,经过纯化处理的乙炔被输送到电解槽中,与水反应,产生乙炔气体和氢气。
该电解槽设有铁阳极和铁阴极,分别与电源相连。
电解槽内的水通过电解分解成氢氧离子和氢离子。
乙炔和氢气会在电解槽中不断形成。
通过以上的工艺流程,电石生产的乙炔气体得以产生。
这些乙炔气体可以经过进一步的处理,生产出不同种类的化工产品,如聚氯乙烯、丙烯酸等。
电石生产工艺流程中,需要严格控制反应温度、氧气含量和杂质含量,以保证乙炔的产量和质量。
同时,在生产过程中要注意环保要求,有效处理和净化废水和废气,保护环境。
电石生产工艺

电石生产工艺电石是由硫酸钙(CaSO4)和煤炭(C)经过高温加热反应制得的一种化工原料,广泛应用于制备乙炔气和化学肥料等领域。
下面将介绍一种常见的电石生产工艺。
电石生产工艺主要分为四个步骤:原料准备、反应炉加热、乙炔气分离和电石产品处理。
首先,原料准备是电石生产的基础。
煤炭是主要原料,可选择不同种类的煤炭,如无烟煤、气化煤等。
同时,还需要准备一定质量比例的硫酸钙。
接下来,将煤炭和硫酸钙按照一定的比例混合,形成煤块。
这些煤块通常具有直径在2-4厘米之间。
这样的煤块便于放入反应炉中,并且保证了反应的充分进行。
然后,煤块被放入预热过的反应炉中,进行高温加热。
在反应炉中,煤块遇热分解,生成乙炔气和炔钙等产物。
乙炔气是电石生产的重要产品,可用于制备乙炔焊、化学分析和有机合成等领域。
最后,将反应炉中的气体通过冷却器进行冷却。
冷却器中的水能够使乙炔气液化,分离出来。
同时,过程中还会产生一些碳酸钙沉淀物。
这些沉淀物可以通过过滤、干燥等工艺进行处理,得到纯净的电石产品。
在这个工艺过程中,温度和时间是十分关键的参数。
高温能够促使煤块充分分解,生成更多的乙炔气。
合理的时间控制能够保证反应的稳定性和产率。
同时,还需要注意排放处理过程中产生的废气和废水。
在电石生产中,会排放出一些有害气体和废水,如一氧化碳和硫酸等。
这些废气和废水需要通过净化设备和处理工艺进行处理,以减少对环境的污染。
总结起来,电石生产工艺是一个复杂而又精细的过程。
它不仅需要严格控制温度和时间,还需要注意废气和废水的处理。
通过这一工艺,我们可以生产出乙炔气等重要的化工原料,为人类的生产和生活提供了有力支持。
冶炼电石的原理
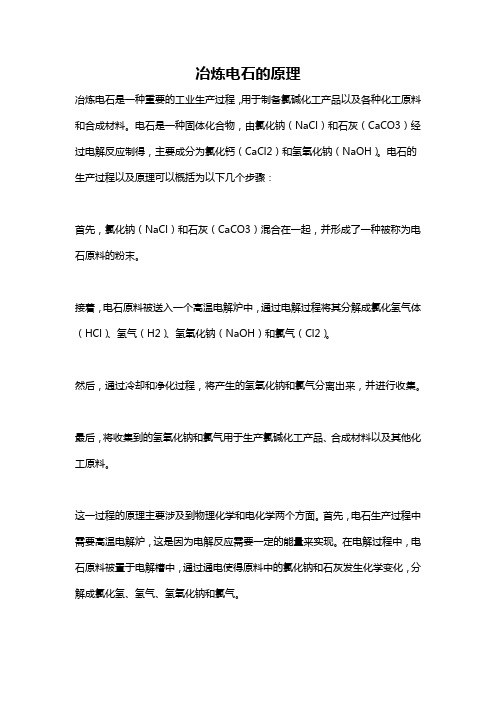
冶炼电石的原理冶炼电石是一种重要的工业生产过程,用于制备氯碱化工产品以及各种化工原料和合成材料。
电石是一种固体化合物,由氯化钠(NaCl)和石灰(CaCO3)经过电解反应制得,主要成分为氯化钙(CaCl2)和氢氧化钠(NaOH)。
电石的生产过程以及原理可以概括为以下几个步骤:首先,氯化钠(NaCl)和石灰(CaCO3)混合在一起,并形成了一种被称为电石原料的粉末。
接着,电石原料被送入一个高温电解炉中,通过电解过程将其分解成氯化氢气体(HCl)、氢气(H2)、氢氧化钠(NaOH)和氯气(Cl2)。
然后,通过冷却和净化过程,将产生的氢氧化钠和氯气分离出来,并进行收集。
最后,将收集到的氢氧化钠和氯气用于生产氯碱化工产品、合成材料以及其他化工原料。
这一过程的原理主要涉及到物理化学和电化学两个方面。
首先,电石生产过程中需要高温电解炉,这是因为电解反应需要一定的能量来实现。
在电解过程中,电石原料被置于电解槽中,通过通电使得原料中的氯化钠和石灰发生化学变化,分解成氯化氢、氢气、氢氧化钠和氯气。
其次,电石生产过程中还涉及到电化学的原理。
电解反应是通过电流在电解液中引起的化学反应,而电石生产中的电解液就是电石原料。
在电解过程中,电解槽中的电解液被通电,导致电石原料中的离子发生了移动和转移,从而产生了新的化学物质,如氢氧化钠和氯气。
需要注意的是,电石生产过程中产生的氯气是一种有毒气体,需要进行净化处理以及合理的收集和利用。
此外,电石生产过程需要大量的能源和原料,对环境产生了一定的影响,因此在实际生产中需要采取一系列的环保措施来减少排放和资源消耗。
综上所述,冶炼电石的原理涉及到化学反应、电解过程以及能量转化等多个方面,通过合理的操作和控制,可以高效地生产出氯碱化工产品以及各种合成材料和化工原料。
与此同时,也需要重视环境保护和资源利用,不断改进工艺技术,减少能源消耗和减少污染,实现可持续发展。
电石生产工艺

电石生产工艺电石是一种非常重要的化工产品,它是通过工业过程制造而成的。
电石生产工艺在很多国家都有应用,尤其是在化工、矿业和冶金等领域。
电石的生产过程包括多个步骤,从石灰石、煤炭到电石,每个步骤都非常关键。
下面我们将详细介绍电石的生产工艺。
一、原料准备石灰石和煤炭是制造电石的两种主要原料。
为了获得最佳的生产效果,这些原料都必须符合一定的特定要求。
1.1 石灰石石灰石是可以在自然界中找到的矿物质,它的主要成分是碳酸钙 (CaCO3)。
制备电石的石灰石通常是高品质石灰石,包括以下特定要求:(1) 高品质石灰石的含钙量应在 98~99.5% 之间。
含钙量越高,生产出的电石质量越好。
(2) 石灰石的杂质含量应尽可能低,特别是含铁、硅等杂质。
杂质含量高的石灰石不仅会降低电石的质量,而且会磨损生产设备。
(3) 石灰石颗粒大小应均匀,通常在 10~50 mm 之间。
1.2 煤炭煤炭是制造电石的另一主要原料,它需要符合以下要求:(1) 煤种选择制造电石的煤种通常是贫煤和褐煤,因为这种煤种不仅价格相对低廉,而且富含挥发分和焦油,更适合于电石工艺中的加热过程。
(2) 煤炭质量要求煤炭的质量对生产电石的影响很大。
煤炭应具有以下特性:A. 挥发分含量要高,通常在 25% - 35%之间。
B. 灰分含量应低,不超过 15%。
C. 热值越高越好,热值在 23 - 28 MJ/kg;D. 粒度应均匀,通常是 3 - 25 mm。
二、石灰石碎矿和煤炭制备生产电石的下一个步骤是对石灰石和煤炭进行处理和准备,以便放入电石炉中进行反应。
2.1 石灰石碎矿在石灰石碎矿过程中,需要选择一台合适的破碎机,将石灰石进行粉碎和筛分,最终得到符合要求的颗粒状石灰石。
2.2 煤炭制备和石灰石碎矿类似,煤炭制备也需要选择一台破碎机,将煤炭粉碎和筛分,得到合适的颗粒状煤炭。
三、电石炉的制备电石炉是制造电石的核心设备,它需要精细的设计和制造。
电石炉是一种立式圆筒形的钢制容器,高度通常在 5-10 米左右。
电石生产机理
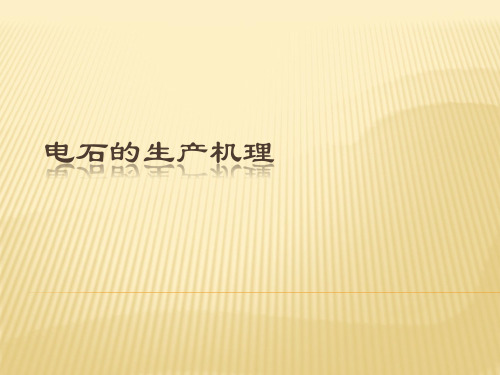
1、CaO(固)+3C(固)=CaC2(液)+CO(气) 2、CaC2 (液)与CaO (固)共融成液态 3、CaO (液)+ 3C(固)=CaC2(液)+CO(气)
最终结果生成电石的反应过程由下面反应式进行 1、CaO(固)+3C(固)=CaC2(液)+CO(气) 2、CaO(液)+3C(固)=CaC2(液)+CO(气)
电石的生产机理
一、焦炭、石灰、电石熔点与关系
1、焦炭 在电石炉中,焦炭是以块状存在的,而不 是由碳原子的状态存在的,焦炭没有明显的熔 点,直到3000℃它还是固体。一直达到 3537℃时才气化,而电石炉中的温度是达不 到焦炭的气化温度的,所以在电石炉里焦炭始 终是不熔化的固体。
2、石灰 纯石灰的熔点为2580℃ 3、电石 纯电石的熔点为2300℃
三、生产原理
如果考虑到在理想的情况下,石灰分子与 三个碳原子直接相遇发生反应,在2000℃左 右反应速度是非常快的,要比共融速度还快。 但是在电石炉内焦炭是以块状存在的,它的反 应接触面积就大大阻碍了与石灰的反应速度, 甚至要比共融的速度还要慢。 那么在电石炉内电石又是如何生成的呢?
1、反应方程式
2、电石炉内电石生成的原理
从方程式可以看出,电石生成的原理为: 第一步为固态石灰与碳材表面接触与碳材表面的碳 发生反应生成液态的电石。 第二步为液态电石与固态石灰共融后得到液态的电 石、石灰共融体。 第三步为石灰溶液不断渗入碳材的毛细孔中,一边 渗入,一边与碳素反应生成电石再与石灰共融,使碳 材变松,反应时生成的一氧化碳使变松的碳材崩裂为我们还需要有高的炉温去加快反应速度,得 到高质量的电石,并且有了高的炉温熔池也就会扩大, 有了好的熔池,电极的埋入量也就能得到更稳定的控制。 据统计反应速度最快的温度为2000℃-2200℃,但是 当炉温过高,电石的逆反应速度会加快,达到2300℃以 上时逆反应会大于正反应的速度,这样反而得不到高的 发气量。所以将炉温控制在2000℃-2200℃为宜。 以上是指配比足够高的情况,如果配比过低,碳材 全部反应完后,反应速度再快,也得不到高质量的电石, 并且未反应的石灰会与电极上的碳素反应,加快了电极 的消耗速度,从而加大了电极糊的单耗,这样对炉况反 而起了反作用。
电石的主要工艺是什么工艺

电石的主要工艺是什么工艺电石的主要工艺是电解氯化钠制取氯碱化工产品的工艺,也称为氯碱工艺。
这种工艺主要包括电解氯化钠、湿法氧化工艺、电解水和收尾工序四个主要阶段。
首先,电解氯化钠。
电石工艺的第一步是将氯化钠水溶液(即食盐水)经过电解分解为氯气、氢气和氢氧化钠。
通常,在电解槽中,采用钛或钢材作为电极,并在电极之间加入陶瓷隔板以防止混合。
氯气产生在阳极处,而氢气和氢氧化钠则分别产生在阴极处。
该过程称为氯碱电解。
其次,湿法氧化工艺。
氯气即刻与液体氢氧化钠反应生成氯气、水和氢氧化钠。
这个反应通常在一个特制的反应器中进行,该反应器包含了用于良好混合的搅拌器,并具有经过冷却和净化的出口口。
氢氧化钠的湿法氧化产生的氯气通常是纯度较高的,可以直接用于工业用途。
然后,电解水。
电石工艺的下一个步骤是电解水,以产生氢氧化钠和氢气。
这个步骤涉及两个电极,一个是负极(阴极),另一个是正极(阳极),并在两个电极之间有一个分离器,用于防止产生氯气。
在电解过程中,水分子会被分解成氢气和氢氧化钠,这种反应是可逆反应,它的速度取决于电流密度。
最后,收尾工序。
电石工艺的最后一个步骤是对产生的氯碱化工产品进行收集、处理和包装。
在此步骤中,收集产生的氯气、氢气和氢氧化钠,并将其纯化或泡制成最终产品。
然后,根据产品的不同,可以选择将其安装在合适的包装中,以供不同的应用和行业使用。
总结来说,电石的主要工艺是通过电解氯化钠来制取氯碱化工产品。
这个过程涉及到电解氯化钠、湿法氧化、电解水和收尾工序四个主要阶段。
电石工艺是一种重要的化工工艺,为氯碱化工产品的生产提供了基础,并广泛应用于制药、塑料、橡胶、纺织、造纸等行业。
- 1、下载文档前请自行甄别文档内容的完整性,平台不提供额外的编辑、内容补充、找答案等附加服务。
- 2、"仅部分预览"的文档,不可在线预览部分如存在完整性等问题,可反馈申请退款(可完整预览的文档不适用该条件!)。
- 3、如文档侵犯您的权益,请联系客服反馈,我们会尽快为您处理(人工客服工作时间:9:00-18:30)。
电石的生产工艺原理
电石是含有高纯度的钙 carbide 的固体化合物,它是通过石灰
石与电弧炉产生的电弧作用进行电解反应产生的。
下面将详细介绍电石的生产工艺原理。
电石的生产工艺主要包括以下步骤:
1.原料准备:将石灰石(CaCO3)与焦炭(C)作为主要原料
进行混合。
石灰石主要提供钙,焦炭则提供碳。
此外,还需要添加一定量的煤粉和脱硫剂等辅助原料。
这些原料通过破碎和混合等工艺进行处理,使其均匀混合。
2.电弧炉反应:将混合好的原料装入电弧炉中进行反应。
电弧
炉是一种高温设备,内部设置有两个电极,之间形成一道电弧。
当通电时,电极之间产生高温的电弧,在此高温下,原料中的碳与钙发生反应生成二氧化碳气体(CO2)和钙 carbide
(CaC2)。
反应方程式如下:
CaCO3 + 3C → CaC2 + CO2
3.冷却和除尘:产生的二氧化碳气体和电石在反应过程中产生
的热量需要通过冷却来降温。
一般采用水冷却方式,将产生的气体和石灰石快速冷却。
在冷却的同时,还需要进行除尘处理,将电石中的杂质去除。
4.分选和包装:经过冷却和除尘处理后,得到的电石呈现出块状。
根据规定的尺寸和质量要求,对电石进行分选,去除不符
合要求的样品,留下合格的电石进行包装。
电石的生产工艺原理主要是利用电弧炉中产生的高温电弧将石灰石与焦炭进行加热,并在高温下引发反应生成钙 carbide。
其中焦炭提供高温和过量的碳,促使钙与碳迅速反应。
随着反应进行,CaCO3分解为CaO和CO2,CaO与C反应生成CaC2。
产生的二氧化碳气体排出炉外,而生成的电石被收集下来。
电石的生产工艺具有高效、高纯度等优点。
通过调整原料的配比和电弧炉的操作参数可以控制电石的质量和产量。
同时,电石的生产过程中还可以产生一定的副产品,如工业气体、氮肥等,提高了资源的综合利用效率。
总之,电石的生产工艺原理是利用电弧炉进行高温电解反应,使石灰石与焦炭发生反应生成钙 carbide,经过冷却和除尘后得到电石的最终产品。
这一工艺具有高效、高纯度等特点,被广泛应用于化工和冶金等行业。