超精密机床的应用和发展
超精密数控机床关键部件发展概况
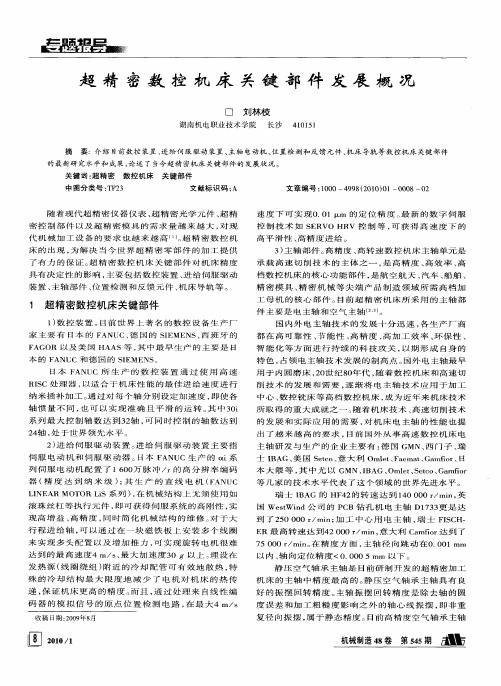
代 机 械 加 工 设 备 的 要 求 也 越 来 越 高 1超 精 密 数 控 机 。
床 的 出 现 , 解 决 当 今 世 界 超 精 密 零 部 件 的 加 工 提 供 为 了有 力 的 保 证 。 精 密 数 控 机 床 关 键 部 件 对 机 床 精 度 超 具 有 决 定 性 的 影 响 , 要 包 括 数 控 装 置 、 给 伺 服 驱 动 主 进 装置 、 轴部 件 、 置检 测和反 馈元件 、 床导轨 等 。 主 位 机
1 超 精 密 数 控 机 床 关 键 部 件
1 数 控 装 置 。 前 世 界 上 著 名 的 数 控 设 备 生 产 厂 ) 目
家 主 要 有 日本 的 F ANUC、 国 的 S E 德 I ME NS、 班 牙 的 西
F AGOR 以 及 美 国 HA AS 等 , 中 最 早 生 产 的 主 要 是 日 其
伺 服 电 动 机 和 伺 服 驱 动 器 。 本 F NUC 生 产 的 仪 日 A i系 列 伺 服 电 动 机 配 置 了 l6 0 f 冲 / 0 ̄ 脉 r的 高 分 辨 率 编 码 器 ( 度 达 到 纳 米 级 ) 其 生 产 的 直 线 电 机 ( ANUC 精 ; F L N AR T i 系 列 ) 在 机 械 结 构 上 无 须 使 用 如 IE MO OR LS , 滚 珠 丝 杠 等 执 行 元 件 , 可 获 得 伺 服 系 统 的高 刚 性 , 即 实 现 高 增 益 、 精 度 , 时 简 化 机 械 结 构 的 维 修 。 于 大 高 同 对 行 程 进 给 轴 , 以 通 过 在 一 块 磁 铁 板 上 安 装 多 个 线 圈 可 来 实 现 多 头 配 置 以及 增 加 推 力 , 实 现 旋 转 电机 很 难 可
精密和超精密加工的机床设备技术

精密和超精密加工的机床设备技术引言精密和超精密加工技术在现代制造业中扮演着重要的角色。
为了满足高质量、高精度、高效率的加工需求,机床设备技术不断得到改进和发展。
本文将介绍精密和超精密加工的机床设备技术,并探讨其在制造业中的应用。
1. 精密加工的机床设备技术精密加工是指在工程加工中,对尺寸精度和表面质量要求较高的加工方法。
精密加工的关键在于机床设备的稳定性、刚性和精度。
以下是精密加工机床设备的几个关键技术:1.1 数控技术数控技术是精密加工中最为关键的技术之一。
通过数控技术,可以实现机床的高精度和高效率加工。
数控技术的应用可以大大提高生产效率,并且减少操作人员的工作强度。
1.2 精密传动系统精密传动系统是精密加工机床设备的核心组成部分。
精密传动系统的设计与制造涉及到轴承、传动装置、伺服驱动装置等多个方面。
通过精确的传动系统,可以提高机床的精度和稳定性。
1.3 线性驱动技术线性驱动技术是现代机床设备中的重要发展方向之一。
相比传统的滚动轴承驱动,线性驱动技术能够实现更高的速度和更高的精度。
线性驱动技术可以用于各种类型的机床设备,包括数控机床和超精密加工机床。
2. 超精密加工的机床设备技术超精密加工是指在微米甚至纳米级别下进行加工的技术。
超精密加工在光学、光电子、半导体等领域具有重要的应用。
以下是超精密加工机床设备技术的几个关键技术:2.1 超精密控制系统超精密控制系统是实现超精密加工的关键技术之一。
通过超精密控制系统,可以实现对微小位移和应力的精确控制。
超精密控制系统需要具备高精度、高灵敏度和高稳定性的特点。
2.2 超精密磨削技术超精密磨削技术是超精密加工的核心技术之一。
超精密磨削技术可以实现对工件表面的精确修整和光洁度的提高。
超精密磨削技术需要借助特殊材料和磨削工具,并配合高精度的机床设备。
2.3 超精密检测技术超精密加工过程中,对工件的检测和测量要求非常高。
超精密检测技术可以实现对工件尺寸、形状和表面质量的高精度测量。
精密和超精密加工的机床设备

高精度、高效率、高表面质量、 低误差、低能耗等。
应用领域
01
02
03
04
航空航天
制造飞机发动机叶片、涡轮盘 等关键部件。
汽车制造
加工发动机缸体、曲轴等精密 零部件。
能源领域
制造核聚变反应堆中的超导线 圈、太阳能电池板等。
医疗器械
制造人工关节、牙科种植体等 医疗器件。
发展历程与趋势
发展历程
从20世纪50年代开始,精密和超精密加工技术经历了从简单磨削 到复杂切削,再到超精密切削的发展过程。
航空航天领域的应用案例
案例一
某航空发动机制造企业使用超精密加 工机床,对涡轮叶片进行高精度磨削 和抛光,提高了发动机性能和可靠性 。
案例二
某飞机制造企业采用精密加工机床, 对机身结构件进行高精度切割和加工 ,确保飞机整体装配精度和质量。
汽车工业领域的应用案例
案例一
某汽车零部件制造企业使用精密加工 机床,对发动机缸体进行高精度加工, 提高缸体质量和性能,降低发动机故 障率。
柔性化
为了满足多品种、小批量生产的需求,未来精密和超精密加工机床将采用模块化设计、可 重构制造系统等技术,提高机床的加工范围和适应能力。
新材料、新工艺的应用
新材料
随着新材料技术的发展,未来精密和超精密加工机床将采用新型高强度、高硬 度、轻质材料,提高加工效率和加工质量。
ห้องสมุดไป่ตู้新工艺
为了满足复杂形状和特殊材料的加工需求,未来精密和超精密加工机床将采用 新的切削工艺、光整加工工艺和复合加工工艺等,提高加工精度和表面质量。
伺服驱动技术
采用先进的伺服驱动技术, 实现高精度的位置控制和 速度控制。
插补算法
国外超精密数控机床概述

国外超精密数控机床概述20世纪50年代后期,美国首先开始进行超精密加工机床方面的研究,当时因开发激光核聚变实验装置和红外线实验装置需要大型金属反射镜,急需反射镜的超精密加工技术和超精密加工机床。
人们通过使用当时精度较高的精密机床,采用单点金刚石车刀对铝合金和无氧化铜进行镜面切削,以此为起点,超精密加工作为一种崭新的机械加工工艺得到了迅速发展。
1962年,Union Carbide公司首先开发出的利用多孔质石墨空气轴承的超精密半球面车床,成功地实现了超精密镜面车削,尺寸精度达到士0.6 um,表面粗糙度为Ra0.025um,从而迈出了亚微米加工的第一步。
但是,金刚石超精密车削比较适合一些较软的金属材料,而在航空航天、天文、军事等应用领域的卫星摄像头方面,最为常用的却是如玻璃、陶瓷等脆性材料的非金属器件。
用金刚石刀具对这些材料进行切削加工,则会使己加工表面产生裂纹。
而超精密磨削则更有利于脆性材料的加工。
Union Carbide公司的另一代表性产品是其在1972年研制成功的R-0方式的非球面创成加工机床。
这是一台具有位置反馈的双坐标数控车床,可实时改变刀座导轨的转角0和半径R,实现非球面的镜面加工。
加工直径达380mm,工件的形状精度为士0.63um,表面粗糙度为Ra0.025 um。
摩尔公司(Mood Special Tool)于1968年研制出带空气主轴的Moori型超精密镜面车床,但为了实现脆性材料的超精密加工,该公司又于1980年在世界上首次开发出三坐标控制的M-18AG型超精密非球面金刚石刀具车削、金刚石砂轮磨削机床。
该机床采用空气主轴,回转精度径向为0.075pm;采用Allen-Braley 7320数控系统;X,Z 轴行程分别为410mm和230mm,其导轨的平直度在全长行程范围内均在0.5um以内,B轴的定位精度在3600范围内是0.38um;采用金刚石砂轮可加工最大直径为356mm的各种非球面的金属反射镜。
国外超精密数控机床概述

国外超精密数控机床概述20世纪50年代后期,美国首先开始进行超精密加工机床方面的研究,当时因开发激光核聚变实验装置和红外线实验装置需要大型金属反射镜,急需反射镜的超精密加工技术和超精密加工机床。
人们通过使用当时精度较高的精密机床,采用单点金刚石车刀对铝合金和无氧化铜进行镜面切削,以此为起点,超精密加工作为一种崭新的机械加工工艺得到了迅速发展。
1962年,Union Carbide公司首先开发出的利用多孔质石墨空气轴承的超精密半球面车床,成功地实现了超精密镜面车削,尺寸精度达到士0.6 um,表面粗糙度为Ra0.025um,从而迈出了亚微米加工的第一步。
但是,金刚石超精密车削比较适合一些较软的金属材料,而在航空航天、天文、军事等应用领域的卫星摄像头方面,最为常用的却是如玻璃、陶瓷等脆性材料的非金属器件。
用金刚石刀具对这些材料进行切削加工,则会使己加工表面产生裂纹。
而超精密磨削则更有利于脆性材料的加工。
Union Carbide公司的另一代表性产品是其在1972年研制成功的R-0方式的非球面创成加工机床。
这是一台具有位置反馈的双坐标数控车床,可实时改变刀座导轨的转角0和半径R,实现非球面的镜面加工。
加工直径达380mm,工件的形状精度为士0.63um,表面粗糙度为Ra0.025 um。
摩尔公司(Mood Special Tool)于1968年研制出带空气主轴的Moori型超精密镜面车床,但为了实现脆性材料的超精密加工,该公司又于1980年在世界上首次开发出三坐标控制的M-18AG型超精密非球面金刚石刀具车削、金刚石砂轮磨削机床。
该机床采用空气主轴,回转精度径向为0.075pm;采用Allen-Braley 7320数控系统;X,Z 轴行程分别为410mm和230mm,其导轨的平直度在全长行程范围内均在0.5um以内,B轴的定位精度在3600范围内是0.38um;采用金刚石砂轮可加工最大直径为356mm的各种非球面的金属反射镜。
精密和超精密加工技术的发展
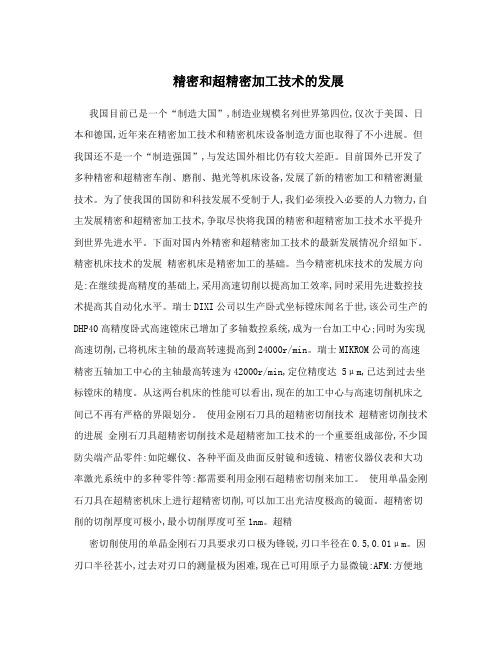
精密和超精密加工技术的发展我国目前已是一个“制造大国”,制造业规模名列世界第四位,仅次于美国、日本和德国,近年来在精密加工技术和精密机床设备制造方面也取得了不小进展。
但我国还不是一个“制造强国”,与发达国外相比仍有较大差距。
目前国外已开发了多种精密和超精密车削、磨削、抛光等机床设备,发展了新的精密加工和精密测量技术。
为了使我国的国防和科技发展不受制于人,我们必须投入必要的人力物力,自主发展精密和超精密加工技术,争取尽快将我国的精密和超精密加工技术水平提升到世界先进水平。
下面对国内外精密和超精密加工技术的最新发展情况介绍如下。
精密机床技术的发展精密机床是精密加工的基础。
当今精密机床技术的发展方向是:在继续提高精度的基础上,采用高速切削以提高加工效率,同时采用先进数控技术提高其自动化水平。
瑞士DIXI公司以生产卧式坐标镗床闻名于世,该公司生产的DHP40高精度卧式高速镗床已增加了多轴数控系统,成为一台加工中心;同时为实现高速切削,已将机床主轴的最高转速提高到24000r/min。
瑞士MIKROM公司的高速精密五轴加工中心的主轴最高转速为42000r/min,定位精度达5μm,已达到过去坐标镗床的精度。
从这两台机床的性能可以看出,现在的加工中心与高速切削机床之间已不再有严格的界限划分。
使用金刚石刀具的超精密切削技术超精密切削技术的进展金刚石刀具超精密切削技术是超精密加工技术的一个重要组成部份,不少国防尖端产品零件:如陀螺仪、各种平面及曲面反射镜和透镜、精密仪器仪表和大功率激光系统中的多种零件等:都需要利用金刚石超精密切削来加工。
使用单晶金刚石刀具在超精密机床上进行超精密切削,可以加工出光洁度极高的镜面。
超精密切削的切削厚度可极小,最小切削厚度可至1nm。
超精密切削使用的单晶金刚石刀具要求刃口极为锋锐,刃口半径在0.5,0.01μm。
因刃口半径甚小,过去对刃口的测量极为困难,现在已可用原子力显微镜:AFM:方便地进行测量。
精密和超精密加工机床的现状及发展对策

工作台尺寸 (宽×长) 800 mm×1 500 mm
最大加工高度
500 mm
最大通过宽度
1 100 mm
工作台进给速度
0.01~30 m/min
砂轮尺寸 (外径×宽) Φ510 mm×100 mm
砂轮转速
1 000~4 000 r/min
砂轮最小进刀量
0.2 μm
在高精度加工的范畴内, 根据精度水平的不 同, 分为 3 个档次:
2
Oct. 2010
第27卷 第10期 Vol.27 No.10
精 度 为 0.3~3 μm, 粗 糙 度 为 0.03~0.3 μm 的 为 精密加工;
精 度 为 0.03~0.3 μm, 粗 糙 度 为 0.005~0.03 μm 的称作超精密加工, 或亚微米加工;
年度 2000 2003 2006 2007
表1 我国机床进出口情况 (亿 美元)
产值 21.97 23.80 64.00 111.9
出口 2.99 3.80 11.90 16.50
进口 18.90 41.60 72.40 70.70
消费 37.88 67.00 131.10 166.10
由于国外对我们封锁禁运一些重要的高精度机 床设备和仪器, 而这些精密设备仪器正是国防和尖 端技术发展所迫切需要的, 因此, 我们必须投入必 要的人力物力, 自主发展精密和超精密加工机床, 使我国的国防和科技发展不会受制于人。
磨头0 mm/min
磨头的横向进给速度 1~4 000 mm/min
砂轮轴驱动电机
11 kW (4P)
机床尺寸 (宽×长×高) 约3 600 mm×5 800 mm×3 700 mm
精密超精密加工技术的发展及应用
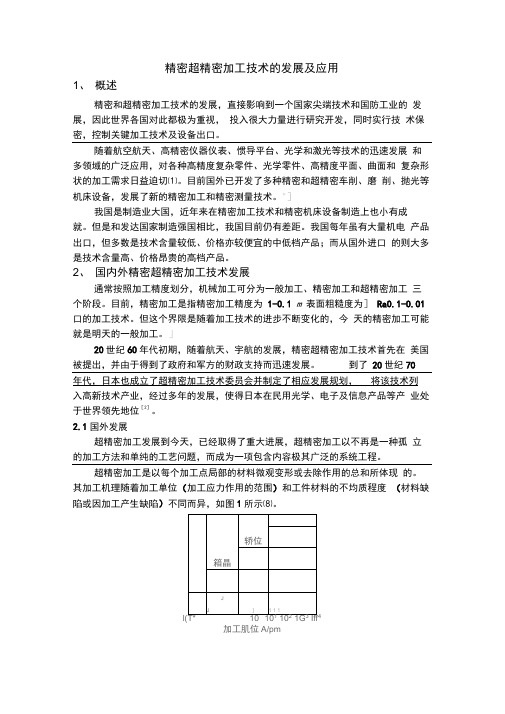
精密超精密加工技术的发展及应用1、概述精密和超精密加工技术的发展,直接影响到一个国家尖端技术和国防工业的发展,因此世界各国对此都极为重视,投入很大力量进行研究开发,同时实行技术保密,控制关键加工技术及设备出口。
随着航空航天、高精密仪器仪表、惯导平台、光学和激光等技术的迅速发展和多领域的广泛应用,对各种高精度复杂零件、光学零件、高精度平面、曲面和复杂形状的加工需求日益迫切⑴。
目前国外已开发了多种精密和超精密车削、磨削、抛光等机床设备,发展了新的精密加工和精密测量技术。
"]我国是制造业大国,近年来在精密加工技术和精密机床设备制造上也小有成就。
但是和发达国家制造强国相比,我国目前仍有差距。
我国每年虽有大量机电产品出口,但多数是技术含量较低、价格亦较便宜的中低档产品;而从国外进口的则大多是技术含量高、价格昂贵的高档产品。
2、国内外精密超精密加工技术发展通常按照加工精度划分,机械加工可分为一般加工、精密加工和超精密加工三个阶段。
目前,精密加工是指精密加工精度为1-0.1 m表面粗糙度为]RaO.1-O.O1 口的加工技术。
但这个界限是随着加工技术的进步不断变化的,今天的精密加工可能就是明天的一般加工。
」20世纪60年代初期,随着航天、宇航的发展,精密超精密加工技术首先在美国被提出,并由于得到了政府和军方的财政支持而迅速发展。
到了20世纪70年代,日本也成立了超精密加工技术委员会并制定了相应发展规划,将该技术列入高新技术产业,经过多年的发展,使得日本在民用光学、电子及信息产品等产业处于世界领先地位[2]。
2.1国外发展超精密加工发展到今天,已经取得了重大进展,超精密加工以不再是一种孤立的加工方法和单纯的工艺问题,而成为一项包含内容极其广泛的系统工程。
超精密加工是以每个加工点局部的材料微观变形或去除作用的总和所体现的。
其加工机理随着加工单位(加工应力作用的范围)和工件材料的不均质程度(材料缺陷或因加工产生缺陷)不同而异,如图1所示⑻。
- 1、下载文档前请自行甄别文档内容的完整性,平台不提供额外的编辑、内容补充、找答案等附加服务。
- 2、"仅部分预览"的文档,不可在线预览部分如存在完整性等问题,可反馈申请退款(可完整预览的文档不适用该条件!)。
- 3、如文档侵犯您的权益,请联系客服反馈,我们会尽快为您处理(人工客服工作时间:9:00-18:30)。
超精密机床的应用和发展
随着科技的快速发展,机械加工技术已经达到了超精密的水平。
超精密机床作为基础工具,已成为近年来制造业的重要发展方向
之一。
本文将从以下几个方面,探讨超精密机床的应用和发展。
一、超精密机床的定义和特点
超精密机床是一种特殊的机床,可以实现高精密、高速度和高
效率的加工。
其特点主要体现在以下几个方面:
1.加工精度高:超精密机床能够实现微米级别的加工精度,能
够满足高精度加工的要求。
2.加工速度快:超精密机床具备较高的加工速度,能够提高生
产效率,同时实现高精度加工。
3.加工稳定性好:超精密机床运行平稳,加工过程中能够保证
工件表面质量稳定。
二、超精密机床在制造业中的应用
超精密机床已经广泛应用于制造业的各个领域,如航空、航天、汽车、模具、电子等。
在这些领域中,超精密机床主要发挥以下
几个方面的作用:
1.实现高精度的加工:超精密机床的加工精度极高,能够满足
对工件精度要求很高的加工任务,如航空、航天等领域。
2.提高生产效率:超精密机床具有较高的加工速度,能够大大
缩短加工周期,提高生产效率。
3.降低加工成本:超精密机床能够降低加工成本,同时保证加
工质量,提高企业竞争力。
三、超精密机床发展趋势
随着社会和经济的快速发展,超精密机床的发展也呈现出以下
几个趋势:
1.发展向智能化方向:超精密机床将会朝着智能化发展,实现
自动化生产和高效率加工。
2.发展向多元化方向:超精密机床的应用范围将会越来越广泛,适用于各种材料的加工、各种形状的零部件加工等。
3.发展向节能环保方向:超精密机床将会朝着节能环保的方向
发展,采用新技术和新材料,以减少对环境的污染。
四、超精密机床的研发和生产
超精密机床的研发和生产是制造业转型升级的重要一环。
在这
些领域中,相关的技术和人才是最为关键的。
1.技术创新:超精密机床技术的创新需要专业的团队进行研发,采用最新的材料和工艺技术。
2.人才培养:超精密机床的开发人才应具备全面的技术素质和
高度的创新能力,同时要了解制造业的发展趋势和市场需求。
3.品质管理:超精密机床的生产需要高度的品质管理,要保证产品的质量和可靠性。
总之,超精密机床的应用和发展已经成为现代制造业的主要趋势之一。
在超精密机床的发展过程中,需要加强技术创新和人才培养,同时要重视品质管理和环境保护。
相信在不久的将来,超精密机床将会在制造业中发挥更加重要的作用。