TPM(TotalProductiveMaintenance)简介
TPM自主保养简介

TPM自主保养简介什么是TPM?TPM(Total Productive Maintenance,全面生产维护),是一种以全员参与为基础的设备管理方法。
它的目标是通过减少设备故障、提高设备效率和延长设备寿命,实现生产过程的稳定性和持续改进。
TPM起源于日本,在20世纪60年代由日本的制造企业引入并发展起来。
在过去几十年中,TPM已成为世界范围内许多制造业公司实施的重要运营策略。
它不仅仅是一种设备维护方法,更是一种企业文化的建设。
为什么需要TPM自主保养?传统的设备维护方式通常是由专门的维修人员负责,而TPM的关键之一就是将维护的责任下放到每个操作工人。
这样做的好处是:1.减少故障时间:由于设备的日常保养工作由操作工人自己负责,可以及时发现并解决潜在的故障问题,避免生产线因设备故障而停止生产。
2.提高设备效率:操作工人可以通过定期检查和维护设备来确保其正常运行。
这可以减少设备的故障次数,提高设备的使用率,从而提高生产效率和产品质量。
3.延长设备寿命:通过定期维护设备,可以避免设备因长期运行而积累的问题,延长设备的使用寿命,降低设备更换的成本。
4.培养员工技能:操作工人在负责设备保养的过程中,不仅可以学习到如何正确操作和维护设备的技能,还可以培养良好的团队合作和沟通能力。
TPM自主保养的步骤TPM自主保养包括以下几个步骤:1.确定自主保养项目:根据设备的特点和工艺流程,确定需要操作工人负责的自主保养项目。
这些项目应涵盖设备的日常清洁、润滑、紧固、定期检查等方面。
2.制定自主保养计划:将自主保养项目列入生产计划,制定自主保养的时间表和频率。
确保每个操作工人都清楚自己需要在何时进行自主保养,并合理安排生产计划。
3.培训操作工人:对每个操作工人进行必要的培训,使他们了解自主保养项目的具体内容和要求。
培训内容应包括设备维护的基本知识、操作方法和安全注意事项等。
4.设立自主保养的标准和检查表:制定相应的自主保养标准和检查表,确保操作工人在自主保养过程中按照标准进行操作,并及时记录相关数据和结果。
tpm是什么

tpm是什么
TPM是Total Productive Maintenance的缩写,意为全面生产维护。
它是一种全面参与员工的生产管理方式,旨在最大化产品生产率、品质和工作效率。
TPM追求全员参与,通过识别和消除造成设备故障、停机和质量问题的根本原因,实现其生产目标。
下面是TPM的几个重要方面:
1. 设备可靠性维护
TPM强调设备可靠性的提高,以预防定期维护之外的故障,保证设备持续运转,最大限度地减少停机时间。
2. 设备效率提高
TPM通过工程控制、生产操作技能和设备管理等方式来实现设备效率的提高,提高其产量和效益,并保证产品质量。
3. 计划性维护
TPM注重对设备的计划性和预防性维护,以减少突发性的问题和需要紧急维修的情况。
4. 全员参与
TPM通过全员参与,以实现彻底的质量管理和效率提高。
所有员工都可以参与到设备的维护、改善、生产和管理中。
5. 标准化工作
TPM强调标准化工作,并通过不断的改进与学习,提高工作效率和质量,从而减少浪费和成本。
总之,TPM是一种重视员工参与、维护设备可靠性和提高效率、通过计划性维护实现生产目标、强调标准化工作、全员参与的生产管理方式。
它可以帮助企业提高生产效率,降低成本,提高产品质量,并提高员工的工作满意度和认同感。
TPM概述

八、重點項目
既有設備的有效利用 調整、等待時間的縮短 設備的故障減低 設備的精度管理 設備的整體維護保養 教育訓練及人才培養
九、目
Item
一、TPM 概 述
TPM即Total Productive Maintenance 簡稱:全員參加的生產保全或全員生產維護。 TPM建立在“以設備來制造品質”說法基礎上而 發展,換句話說,就是設備管理的全公司展開。
TPM系向零故障、零不良、零傷害挑戰。故障不 良,傷害為零時,能使設備稼動率提高、品質提 升、成本降低、庫存降低、士氣提升結果使勞動 生產力提高。 TPM從導入到實施到穩固,大約需花三年的時間。
5
設備‧模具初期管理體制
初期管理情報體系 依 據 P J 進 行 階 段 別 事 前 檢 討 與 對 策 機 能 設 計 標 准
初
P h ase1
設備效率的改善(由專案小組個別改善,對影響設 備總效率的六大損耗因素進行全面考慮PM分析)
影響壽命周期成本的業務圖示
95% 85% 壽 命 周 期 成 本 結 構 75% 66%
導入 開始
6.TPM 的 開 端
招待
7.設 備 效 率 化 的 個 別 改 善 導 入 實 施 階 段 8.建 立 自 主 保 全 體 制 9. 建 立 保 全 部 門 的 計 划 保 全 體 制 10.運 轉 、 保 全 技 能 提 升 的 訓 練
模擬公司設備的選定 計划小組編成 步驟方式診斷膠合格証 定期保全、預知保全工程、 預備品、工具、圖面的管理 領導者的集合教育 向員工的傳達教育 MP 設 計 初期流動管理 LC C 通 過 PM 審 查 向 更 高 目 標 挑 戰
TPM全面生产性管理

TPM全面生产性管理概述TPM(Total Productive Maintenance,全面生产性维护)是一种管理方法,旨在通过所有员工的参与和积极的协作,实现生产设备的高效运行和最小化故障率。
这种管理方法中,所有员工都承担责任,不仅负责设备的正常运行和维护,还负责预防故障和提高生产效率的工作。
TPM的目标是通过实施与设备保养和性能改善相关的一系列措施,提高生产设备的可靠性、质量和产能。
TPM的原则TPM的核心原则是通过最小化七大损失来提高设备效能和生产效率。
这七大损失包括:1.设备故障和停机时间的损失2.调整和改装的损失3.停机损失4.下线和速度损失5.质量损失6.批审和返工的损失7.原材料和能源的损失TPM强调通过减少这些损失来提高生产效率,以确保设备始终处于最佳状态,从而最大限度地提高生产能力。
TPM的实施步骤1. 创建执行团队TPM的成功实施需要有一个执行团队来领导和推动整个过程。
这个团队应该由各个部门的代表和具有实施TPM经验的员工组成。
团队负责设定目标、制定计划并监督整个实施过程。
2. 制定实施计划在创建执行团队之后,需要制定一个详细的实施计划。
这个计划应该明确列出每个步骤的时间表、责任人和具体的实施方法。
计划必须根据实际情况进行调整,并确保所有员工都能理解和接受这个计划。
3. 培训和教育为了确保所有员工都能正确理解和实施TPM,必须进行培训和教育。
这种培训可以包括理论知识、实际操作和案例分析等内容。
培训还应该由经验丰富的员工来传授,并与实际工作相结合,以提高培训效果。
4. 制定标准和指导方针在实施TPM的过程中,必须制定一些标准和指导方针,以保证每个员工都按照规定的方法进行工作。
这些标准和指导方针可以包括设备维护的操作程序、故障排除的步骤和性能改善的技术要求等。
5. 实施设备维护活动设备的维护是TPM的重要组成部分。
这些维护活动可以包括日常保养、预防性维护和纠正性维护等。
实施这些维护活动的目的是确保设备始终处于最佳状态,并最大限度地减少故障和停机时间。
TPM是Total-Productive-Maintenance-第一个字母的缩写-本意是
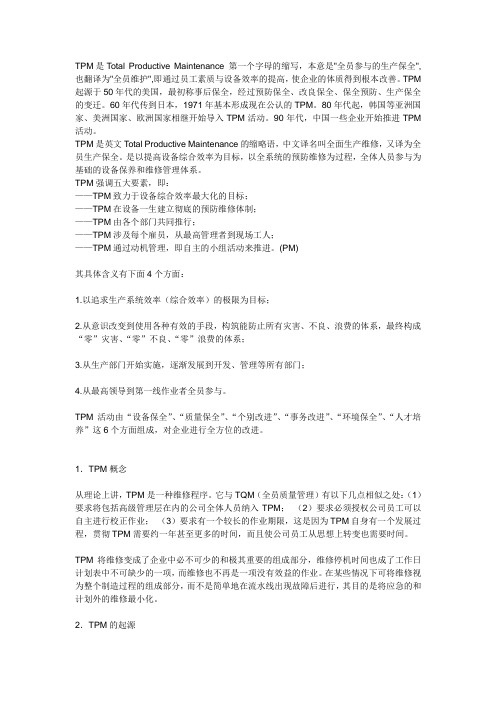
TPM是T otal Productive Maintenance 第一个字母的缩写,本意是"全员参与的生产保全",也翻译为"全员维护",即通过员工素质与设备效率的提高,使企业的体质得到根本改善。
TPM 起源于50年代的美国,最初称事后保全,经过预防保全、改良保全、保全预防、生产保全的变迁。
60年代传到日本,1971年基本形成现在公认的TPM。
80年代起,韩国等亚洲国家、美洲国家、欧洲国家相继开始导入TPM活动。
90年代,中国一些企业开始推进TPM 活动。
TPM是英文T otal Productive Maintenance的缩略语,中文译名叫全面生产维修,又译为全员生产保全。
是以提高设备综合效率为目标,以全系统的预防维修为过程,全体人员参与为基础的设备保养和维修管理体系。
TPM强调五大要素,即:——TPM致力于设备综合效率最大化的目标;——TPM在设备一生建立彻底的预防维修体制;——TPM由各个部门共同推行;——TPM涉及每个雇员,从最高管理者到现场工人;——TPM通过动机管理,即自主的小组活动来推进。
(PM)其具体含义有下面4个方面:1.以追求生产系统效率(综合效率)的极限为目标;2.从意识改变到使用各种有效的手段,构筑能防止所有灾害、不良、浪费的体系,最终构成“零”灾害、“零”不良、“零”浪费的体系;3.从生产部门开始实施,逐渐发展到开发、管理等所有部门;4.从最高领导到第一线作业者全员参与。
TPM活动由“设备保全”、“质量保全”、“个别改进”、“事务改进”、“环境保全”、“人才培养”这6个方面组成,对企业进行全方位的改进。
1.TPM概念从理论上讲,TPM是一种维修程序。
它与TQM(全员质量管理)有以下几点相似之处:(1)要求将包括高级管理层在内的公司全体人员纳入TPM;(2)要求必须授权公司员工可以自主进行校正作业;(3)要求有一个较长的作业期限,这是因为TPM自身有一个发展过程,贯彻TPM需要约一年甚至更多的时间,而且使公司员工从思想上转变也需要时间。
TPM简介

1955年前后,人们发现设备的许多故障是周期性 出现的,于是对这类故障提出了维护方法
1960年前后,工业技术不断进步,人们开始需要 不发生故障的设备,维护从设计一套系统的保全方案,即TPM的前身PM
7
5、TPM的特点
TPM的特点就是三个“全”—即全效率、全系统和全员参加。
全效率:指设备寿命周期费用评价和设备综合效率。 全系统:指生产维修系统的各个方法都要包括在内。即是PM、MP、CM、 BM等都要包含。 全员参加:指设备的计划、使用、维修等所有部门都要参加,尤其注重的是操作者的自主小组活动。
协作 公司
本公司
顾客
合作 公司
TPM
10
谢谢大家!
11
为实现提高设备综合效率这一目标,以系统的预防维修为过程,全体人员参与的基础设备保养和维 修管理系统
T
Total
全员
P
Productive 生产
M
Maintenance 维护
3
2、TPM的起源
• 起源:
事后保全 改良保全 预防保全 保全预防 生产保全
1950年以前,半自动、手动操作设备多,结构简 单,常采用的方法,在设备出现故障后再维护
TPM 简 介
1
一、TPM简介
2
1、TPM的定义
定义: TPM管理,即“全员设备管理与维修”,70年代起源于日本,是一种全员参与 的生产维修方式,其主要点就在“生产维修”及“全员参与”上。通过建立一个全系 统员工参与的生产维修活动,使设备性能达到最优。
TPM是英文Total Productive Maintenance的缩略语,中文译名叫全员生产维护,又译为全员生产 保全
TPM—全员生产保养
TPM—全员生产保养1. 什么是TPM?TPM,全称为“Total Productive Maintenance”,即全员生产保养。
它是一种旨在改善设备可靠性、提高生产效率的管理方法。
TPM的核心理念是通过每个员工的全面参与,实现设备的最佳性能和最小故障时间。
2. TPM的原则TPM的实施遵循以下原则:2.1 全员参与TPM将设备的保养不再局限于维修工作人员,而是将其扩展到全员参与。
每个员工都应对设备的保养负责,保持设备的正常运行状态。
2.2 预防性保养传统的维修方式是等待设备发生故障,然后进行修复。
TPM强调预防性保养,即通过定期检查、清洁和维护设备,预防故障的发生,保持设备的良好状态。
2.3 故障消除在TPM中,故障不仅仅是维修工作人员的责任,每个员工都有义务消除故障。
通过设备巡检和快速的故障处理,可以迅速恢复生产,并防止故障再次发生。
2.4 持续改善TPM是一个持续改善的过程,它要求员工不断地寻求改进设备和工作方式的方法。
通过员工的反馈和创新,不断地提高设备的可靠性和生产效率。
3. TPM的实施步骤3.1 培训和意识提升首先,组织需要进行TPM培训,向员工介绍TPM的概念、原则和方法。
培训的目的是提升员工的意识,让他们理解TPM对于企业的重要性。
3.2 制定保养计划在实施TPM时,企业需要制定详细的保养计划。
这包括设备的保养周期、保养内容、保养人员的分工等。
保养计划可以根据设备的不同特点进行制定。
3.3 设备巡检和保养根据保养计划,员工需要定期对设备进行巡检和保养。
巡检的目的是发现潜在故障,并及时进行修复。
保养的内容包括清洁设备、更换易损件等。
3.4 故障处理和改善当设备发生故障时,员工需要迅速进行故障处理。
故障处理的目标是恢复生产,并找出故障的原因,避免类似故障再次发生。
此外,员工还应积极提出改善设备的建议。
4. TPM的好处4.1 提高设备可靠性通过TPM的实施,设备的故障率可以明显下降。
TPM是Total Productive Maintenance 第一个字母的缩写
TPM是Total Productive Maintenance 第一个字母的缩写,本意是"全员参与的生产保全",也翻译为"全员维护",即通过员工素质与设备效率的提高,使企业的体质得到根本改善。
TPM 起源于50年代的美国,最初称事后保全,经过预防保全、改良保全、保全预防、生产保全的变迁。
60年代传到日本,1971年基本形成现在公认的TPM。
80年代起,韩国等亚洲国家、美洲国家、欧洲国家相继开始导入TPM活动。
90年代,中国一些企业开始推进TPM活动。
TPM是英文Total Productive Maintenance的缩略语,中文译名叫全面生产维修,又译为全员生产保全。
是以提高设备综合效率为目标,以全系统的预防维修为过程,全体人员参与为基础的设备保养和维修管理体系。
TPM强调五大要素,即:——TPM致力于设备综合效率最大化的目标;——TPM在设备一生建立彻底的预防维修体制;——TPM由各个部门共同推行;——TPM涉及每个雇员,从最高管理者到现场工人;——TPM通过动机管理,即自主的小组活动来推进。
(PM)其具体含义有下面4个方面:1.以追求生产系统效率(综合效率)的极限为目标;2.从意识改变到使用各种有效的手段,构筑能防止所有灾害、不良、浪费的体系,最终构成“零”灾害、“零”不良、“零”浪费的体系;3.从生产部门开始实施,逐渐发展到开发、管理等所有部门;4.从最高领导到第一线作业者全员参与。
TPM活动由“设备保全”、“质量保全”、“个别改进”、“事务改进”、“环境保全”、“人才培养”这6个方面组成,对企业进行全方位的改进。
1.TPM概念从理论上讲,TPM是一种维修程序。
它与TQM(全员质量管理)有以下几点相似之处:(1)要求将包括高级管理层在内的公司全体人员纳入TPM;(2)要求必须授权公司员工可以自主进行校正作业;(3)要求有一个较长的作业期限,这是因为TPM自身有一个发展过程,贯彻TPM需要约一年甚至更多的时间,而且使公司员工从思想上转变也需要时间。
TPM是Total-Productive-Maintenance-第一个字母的缩写-本意是
TPM是T otal Productive Maintenance 第一个字母的缩写,本意是"全员参与的生产保全",也翻译为"全员维护",即通过员工素质与设备效率的提高,使企业的体质得到根本改善。
TPM 起源于50年代的美国,最初称事后保全,经过预防保全、改良保全、保全预防、生产保全的变迁。
60年代传到日本,1971年基本形成现在公认的TPM。
80年代起,韩国等亚洲国家、美洲国家、欧洲国家相继开始导入TPM活动。
90年代,中国一些企业开始推进TPM 活动。
TPM是英文T otal Productive Maintenance的缩略语,中文译名叫全面生产维修,又译为全员生产保全。
是以提高设备综合效率为目标,以全系统的预防维修为过程,全体人员参与为基础的设备保养和维修管理体系。
TPM强调五大要素,即:——TPM致力于设备综合效率最大化的目标;——TPM在设备一生建立彻底的预防维修体制;——TPM由各个部门共同推行;——TPM涉及每个雇员,从最高管理者到现场工人;——TPM通过动机管理,即自主的小组活动来推进。
(PM)其具体含义有下面4个方面:1.以追求生产系统效率(综合效率)的极限为目标;2.从意识改变到使用各种有效的手段,构筑能防止所有灾害、不良、浪费的体系,最终构成“零”灾害、“零”不良、“零”浪费的体系;3.从生产部门开始实施,逐渐发展到开发、管理等所有部门;4.从最高领导到第一线作业者全员参与。
TPM活动由“设备保全”、“质量保全”、“个别改进”、“事务改进”、“环境保全”、“人才培养”这6个方面组成,对企业进行全方位的改进。
1.TPM概念从理论上讲,TPM是一种维修程序。
它与TQM(全员质量管理)有以下几点相似之处:(1)要求将包括高级管理层在内的公司全体人员纳入TPM;(2)要求必须授权公司员工可以自主进行校正作业;(3)要求有一个较长的作业期限,这是因为TPM自身有一个发展过程,贯彻TPM需要约一年甚至更多的时间,而且使公司员工从思想上转变也需要时间。
TPM基础知识介绍
TPM基础知识介绍TPM(Total Productive Maintenance,全面生产维护)是一种以最大限度提高设备设施稼动率为目标的维护管理手段。
它通过预防性维护、设备维护等一系列措施,最大限度地降低生产线故障率和设备损坏,实现全面生产效能的提升。
TPM起源于20世纪60年代的日本,由日本工业界倡导和推广。
它的核心理念是通过员工参与和团队合作,将设备故障率降到最低,达到生产效率的最大化。
TPM在实施过程中注重预防性维护、设备维修和设备管理,以提高设备的可靠性和稼动率,减少停机时间和生产缺陷。
TPM的目标是实现设备的稳定运行,降低故障率和维修次数,减少停机时间,提高生产效率和质量,降低成本和资源浪费。
它强调预防性维护,通过定期检查和保养设备,及时发现和排除潜在问题,避免设备故障和生产线停机。
此外,TPM还强调减少设备损耗,通过改进设备的设计和操作方法,延长设备的使用寿命,减少维护投入和成本。
TPM的实施需要综合考虑团队管理、设备管理和维护管理等多个方面。
其中,团队管理是关键,它涉及到员工的参与和归属感。
TPM鼓励员工参与设备维护和管理活动,培养员工对设备的责任和关注,提高员工技能和意识,形成团队协作的氛围。
设备管理方面,TPM强调设备状态的监测和管理,通过维护计划、定期检查和设备改进来确保设备的可靠性和稳定性。
而维护管理涉及到故障排除、维修保养和备件管理等工作,需要有专业技术和维护流程的支持。
在TPM实施过程中,可以采用一些工具和方法来辅助管理。
比如,OEE(Overall Equipment Efficiency,全面设备效能)是衡量设备绩效的重要指标,它综合考虑设备的开机时间、生产速度和生产合格率,用以评估设备的稼动率和效率。
通过对OEE进行分析,可以找出设备运行中存在的问题和改进的空间,制定相应的措施和改进方案。
此外,还可以运用维护保养计划(Maintenance Plan)、故障模式与效应分析(Failure Mode and Effects Analysis,FMEA)等工具来管理设备的运行和维护。
- 1、下载文档前请自行甄别文档内容的完整性,平台不提供额外的编辑、内容补充、找答案等附加服务。
- 2、"仅部分预览"的文档,不可在线预览部分如存在完整性等问题,可反馈申请退款(可完整预览的文档不适用该条件!)。
- 3、如文档侵犯您的权益,请联系客服反馈,我们会尽快为您处理(人工客服工作时间:9:00-18:30)。
TPM(TotalProductiveMaintenance)简介
TotalProductiveMaintenance (全员参与的生产保全 ) 之缩写,TPM简称“全员生产保全”,也有称为“全员生产维护”。
T —— Total 为由经营层至第一线作业者全员参加之 T otal;设备总合效率之 T otal;生产系统全体之寿命周期之 T otal。
PM—— ProductiveMaintenance (生产保全)则为最经济的保养,亦即生产上最经济的保养方法。
按照日本工程师学会(JIPE),TPM有如下的定义:
(1)以最高的设备综合效率为目标;
(2)确立以设备一生为目标的全系统的预防保全;
(3)设备的计划、使用、保全等所有部门都要参加;
(4)从企业的最高管理层到第一线职工全体参加;
(5)通过开展小组的自主活动来推进生产保全。
TPM的原理
TPM的原理
TPM的管理特征
日本的全员生产保全与原来的生产保全相比,主要突出一个“全”字,“全”有三个含义,即全效率、全系统和全员参加。
所谓的全效率,是指设备寿命周期费用评价和设备综合效率。
全系统即指生产维修的各个侧面均包括在内,如预防维修、维修预防、必要的事后维修和改善维修。
全员参加即指这一维修体制的群众性特征,从公司经理到相关科室,直到全体操作工人都要参加,尤其是操作工人的自主小组活动。
1、目标性:人类的每一项活动都是为了取得一定的效果,达到一定的目标。
TPM管理也不例外,它的目标就是要不断追求企业生产效率的最大化,全面提升企业的综合素质。
具体来讲,TPM管理是通过对设备的六大损失(故障损失、工艺调整损失、突停和空转损失、速度损失、废次品损失、开工损失)和生产现场的一切不良因素实施持
续的改善,努力实现“5Z”(零事故、零故障、零缺陷、零库存、零差错)的目标,从而达到最佳的设备综合效率和企业经营效益,提高企业的市场竞争能力和应变能力,最终达成“3S”(员工满意、顾客满意、社会满意)的可持续发展的企业,其目标是明确的。
2、系统性:就是TPM管理涉及企业生产系统的全方位和全过程。
TPM把设备包括引进、安装、调试、使用、维护、维修、改造,直到报废更新的各个阶段作为管理对象,涉及设备的各个子系统以及设备的每一个部件、零件,构成以事后维修、预防维修、改善维修和维修预防为主导的全系统生产维修体系。
同时,TPM要求对设备环境、车间以至整个生产现场实行清洁化、定置化、目视化和文明化的管理。
3、集合性:TPM管理由一些相对独立而又相互依赖的活动内容组成,这就是我们所说的TPM八大支柱,即:个别改善、自主维修、专业维修、初期管理、质量管理、安全与环境管理、事务改善、教育培训。
这些活动既有区别,又有联系,相互制约,相互促进,例如维修管理影响着环境管理,环境管理又影响着质量管理,各项活动相互交织在一起,形成一个错综复杂的链和环。
4、整体性:虽然TPM管理的每一项活动内容都是可以量化的,各自具有其独立的功能,但是由于这些活动都是有组织、有系统的活动,它们几乎都难以独自充分发挥其效能,因此单纯追求某一个目标是没有意义的,必须使这些活动形成一个集合,统一于和协调于TPM 管理的整体之中,围绕着TPM管理的目标,共同发挥各自的功能,这样才能构成完整的有机整体,形成一个总体效应。
5、开放性:作为当代企业管理的重要组成部分,TPM管理处于整个企业管理的大环境中。
因此,TPM管理必将受到企业资源条件、环境条件、人员素质、管理方法和管理手段的影响和作用,同时,TPM管理状况也将作用于和影响于企业管理及其它各项专业管理。
由此可知,TPM管理与所处的环境之间既有输入,又有输出,相互渗透,相互促进,每一次输入输出过程的完成,都应使企业管理、专业管理及TPM管理水平有所提高。
6、全员性:TPM管理要求企业从最高领导到生产第一线作业人
员的全面参与。
事实上,对于一个象鞍钢这样的特大型钢铁企业来说,仅靠某个管理部门或是几个人来抓,是无法把住质量关、成本关、设备维护关、安全生产关的,必须把所有员工都发动起来,充分调动其积极性、主动性和自觉性,实现群体参与,才能使推进TPM管理工作开展起来并坚持下去。
全员参与是TPM管理最基本的特征。
7、动态性:对于TPM管理的要求,在一定时间内是相对稳定的,但是随着企业管理水平的提高和企业生产经营活动的发展,特别是我国加入WTO后企业直接面对的世界经济全球化和国内市场国际化的新挑战和新环境,TPM管理也应与之相适应,不会也不应该停滞在一个水平上。
TPM管理始终处于动态的PDCA循环过程中,才会有生命力,才会有效地发挥其独特的功能。
8、持续性:企业追求“5Z”目标和效率最大化的完美境界是无止境的,因此企业推进TPM管理不是突击性的、临时性的工作,不可能一劳永逸,它是一项连续不断的、持久的、艰巨的管理活动,稍有松懈,就有可能崩跨,前功尽弃。
因此,推进TPM管理必须思想上重视,工作上狠抓,切实下大力量,常抓不懈,才能推动企业管理水平的不断提高。
综上所述可以看出,TPM有如下的特征:以最高的设备综合效率为目标,确立以设备生命周期的全系统的预防维护,设备的计划、使用、维修等所有部门及全体员工都要参与,提倡通过小组自主活动来推进生产维护。
TPM通过以全员参与的小组方式,创建设计优良的设备管理系统,提高现有设备的最有效利用,实现安全性和高质量,防止错误发生,从而使企业达到降低成本和提高全面生产效率。
具体包括:强化设备基础管理,提高设备可动率;维持设备良好状态,延长设备寿命;提高生产效率,降低成本;改善工作环境,消除安全隐患,提高员工工作满意度;提高企业持续改善的意识和能力。
自主保全是TPM的一大特色,自主保全强调生产者自己进行设备日常维护,专职设备人员的重点职责则转化为设备专业技能的培训和计划保全、特定情况下的专业维修等。
由单一专业保全转变为以自主
保全为主,是企业设备管理思想的一次飞跃,难度虽大,但通过有效的思想意识教育和专业方法辅导,完全能够实现。
华安盛道近期对某企业的TPM咨询就顺利实现了此项转变,设备管理效果明显改善,而专业保全人员缩简了近一半。
TPM的推行离不开5S基础,在5S基础上,企业就可逐级开展如下工作:初期清扫;污染源及薄弱点对策;自主保养;自主管理等。
通过深入开展TPM,企业就能不断接近“停机为零!废品为零!事故为零!”的奋斗目标。