安全管理工作规定中英文
安全管理制度中英文对照

I. IntroductionThe Safety Management System (SMS) is designed to ensure the safety and health of all personnel working within the organization, as well as the protection of the public and the environment. This system is in accordance with the relevant national and international safety regulations and standards. The following provisions are established to ensure that safety is given the highest priority in all activities.II. ResponsibilitiesA. Management Commitment1. The management of the organization is committed to providing a safe working environment and ensuring that all safety policies and procedures are effectively implemented.2. Management will allocate sufficient resources to maintain and improve the safety performance of the organization.B. Employee Involvement1. All employees are expected to actively participate in the safety management process.2. Employees will receive appropriate training to understand their safety responsibilities and the importance of following safety procedures.C. Safety Committee1. A Safety Committee will be established to oversee the implementation and effectiveness of the SMS.2. The committee will meet regularly to review safety incidents,identify potential hazards, and recommend improvements.III. Safety PoliciesA. Health and Safety Policy1. The organization is committed to the health and safety of all personnel.2. The organization will provide a safe working environment, eliminate hazards, and prevent accidents.B. Environmental Policy1. The organization is committed to protecting the environment and minimizing the impact of its operations.2. The organization will comply with all relevant environmental regulations and strive to improve its environmental performance.C. Fire Safety Policy1. The organization will ensure that all fire safety measures are in place and that employees are trained in fire safety procedures.2. Regular fire drills will be conducted to ensure preparedness.IV. Procedures and PracticesA. Risk Assessment1. Risk assessments will be conducted for all new and existingactivities to identify potential hazards.2. Control measures will be implemented to mitigate identified risks.B. Personal Protective Equipment (PPE)1. All employees will be provided with appropriate PPE and trained onits proper use.2. PPE will be worn when necessary to protect against identified hazards.C. Incident Reporting1. All incidents, accidents, and near-misses must be reported immediately.2. Investigations will be conducted to determine the cause of incidents and to prevent recurrence.D. Training and Competence1. All employees will receive appropriate training to perform their duties safely.2. Training records will be maintained to ensure that all employees are competent to carry out their tasks.V. Monitoring and ReviewA. Internal Audits1. Internal audits will be conducted to assess the effectiveness of the SMS.2. Non-conformities will be identified and corrective actions will be taken.B. Management Review1. Management will review the SMS on a regular basis to ensure its continued effectiveness.2. Changes to the SMS will be made as necessary to address new risks or to improve safety performance.VI. ConclusionThe Safety Management System is a living document that must be continuously improved and adapted to changing circumstances. The organization is committed to maintaining a safe working environment for all personnel and stakeholders, and this system serves as a foundation for achieving that goal.安全管理制度I. 引言安全管理制度(SMS)旨在确保组织内所有人员的安全与健康,以及保护公众和环境。
国际安全管理规则(中英)1
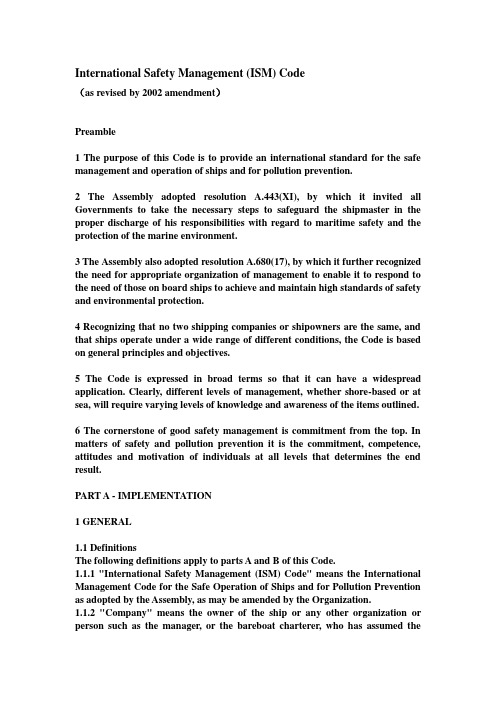
International Safety Management (ISM) Code(as revised by 2002 amendment)Preamble1 The purpose of this Code is to provide an international standard for the safe management and operation of ships and for pollution prevention.2 The Assembly adopted resolution A.443(XI), by which it invited all Governments to take the necessary steps to safeguard the shipmaster in the proper discharge of his responsibilities with regard to maritime safety and the protection of the marine environment.3 The Assembly also adopted resolution A.680(17), by which it further recognized the need for appropriate organization of management to enable it to respond to the need of those on board ships to achieve and maintain high standards of safety and environmental protection.4 Recognizing that no two shipping companies or shipowners are the same, and that ships operate under a wide range of different conditions, the Code is based on general principles and objectives.5 The Code is expressed in broad terms so that it can have a widespread application. Clearly, different levels of management, whether shore-based or at sea, will require varying levels of knowledge and awareness of the items outlined.6 The cornerstone of good safety management is commitment from the top. In matters of safety and pollution prevention it is the commitment, competence, attitudes and motivation of individuals at all levels that determines the end result.PART A - IMPLEMENTATION1 GENERAL1.1 DefinitionsThe following definitions apply to parts A and B of this Code.1.1.1 "International Safety Management (ISM) Code" means the International Management Code for the Safe Operation of Ships and for Pollution Prevention as adopted by the Assembly, as may be amended by the Organization.1.1.2 "Company" means the owner of the ship or any other organization or person such as the manager, or the bareboat charterer, who has assumed theresponsibility for operation of the ship from the shipowner and who, on assuming such responsibility, has agreed to take over all duties and responsibility imposed by the Code.1.1.3 "Administration" means the Government of the State whose flag the ship is entitled to fly.1.1.4 "Safety management system" means a structured and documented system enabling Company personnel to implement effectively the Company safety and environmental protection policy.1.1.5 "Document of Compliance" means a document issued to a Company which complies with the requirements of this Code.1.1.6 "Safety Management Certificate" means a document issued to a ship which signifies that the Company and its shipboard management operate in accordance with the approved safety management system.1.1.7 "Objective evidence" means quantitative or qualitative information, records or statements of fact pertaining to safety or to the existence and implementation of a safety management system element, which is based on observation, measurement or test and which can be verified.1.1.8 "Observation" means a statement of fact made during a safety management audit and substantiated by objective evidence.1.1.9 "Non-conformity" means an observed situation where objective evidence indicates the non-fulfilment of a specified requirement.1.1.10 "Major non-conformity" means an identifiable deviation that poses a serious threat to the safety of personnel or the ship or a serious risk to the environment that requires immediate corrective action and includes the lack of effective and systematic implementation of a requirement of this Code.1.1.11 "Anniversary date" means the day and month of each year that corresponds to the date of expiry of the relevant document or certificate.1.1.12 "Convention" means the International Convention for the Safety of Life at Sea, 1974, as amended.1.2 Objectives1.2.1 The objectives of the Code are to ensure safety at sea, prevention of human injury or loss of life, and avoidance of damage to the environment, in particular to the marine environment and to property.1.2.2 Safety management objectives of the Company should, inter alia:.1 provide for safe practices in ship operation and a safe working environment; .2 establish safeguards against all identified risks; and.3 continuously improve safety management skills of personnel ashore and aboard ships, including preparing for emergencies related both to safety and environmental protection.1.2.3 The safety management system should ensure:.1 compliance with mandatory rules and regulations; and.2 that applicable codes, guidelines and standards recommended by the Organization, Administrations, classification societies and maritime industry organizations are taken into account.1.3 ApplicationThe requirements of this Code may be applied to all ships.1.4 Functional requirements for a safety management systemEvery Company should develop, implement and maintain a safety management system which includes the following functional requirements:.1 a safety and environmental-protection policy;.2 instructions and procedures to ensure safe operation of ships and protection of the environment in compliance with relevant international and flag State legislation;.3 defined levels of authority and lines of communication between, and amongst, shore and shipboard personnel;.4 procedures for reporting accidents and non-conformities with the provisions of this Code;.5 procedures to prepare for and respond to emergency situations; and.6 procedures for internal audits and management reviews.2 SAFETY AND ENVIRONMENTAL-PROTECTION POLICY2.1 The Company should establish a safety and environmental-protection policy which describes how the objectives given in paragraph 1.2 will be achieved.2.2 The Company should ensure that the policy is implemented and maintained at all levels of the organization, both ship-based and shore-based.3 COMPANY RESPONSIBILITIES AND AUTHORITY3.1 If the entity who is responsible for the operation of the ship is other than the owner, the owner must report the full name and details of such entity to the Administration.3.2 The Company should define and document the responsibility, authority and interrelation of all personnel who manage, perform and verify work relating to and affecting safety and pollution prevention.3.3 The Company is responsible for ensuring that adequate resources and shore-based support are provided to enable the designated person or persons to carry out their functions.4 DESIGNATED PERSON(S)To ensure the safe operation of each ship and to provide a link between the Company and those on board, every Company, as appropriate, should designate a person or persons ashore having direct access to the highest level of management. The responsibility and authority of the designated person or persons should include monitoring the safety and pollution-prevention aspects of the operation of each ship and ensuring that adequate resources and shore-based support are applied, as required.5 MASTER'S RESPONSIBILITY AND AUTHORITY5.1 The Company should clearly define and document the master's responsibility with regard to:.1 implementing the safety and environmental-protection policy of the Company; .2 motivating the crew in the observation of that policy;.3 issuing appropriate orders and instructions in a clear and simple manner;.4 verifying that specified requirements are observed; and.5 reviewing the safety management system and reporting its deficiencies to the shore-based management.5.2 The Company should ensure that the safety management system operating on board the ship contains a clear statement emphasizing the master's authority. The Company should establish in the safety management system that the master has the overriding authority and the responsibility to make decisions with respect to safety and pollution prevention and to request the Company's assistance as may be necessary.6 RESOURCES AND PERSONNEL6.1 The Company should ensure that the master is:.1 properly qualified for command;.2 fully conversant with the Company's safety management system; and.3 given the necessary support so that the master's duties can be safely performed.6.2 The Company should ensure that each ship is manned with qualified, certificated and medically fit seafarers in accordance with national and international requirements.6.3 The Company should establish procedures to ensure that new personnel and personnel transferred to new assignments related to safety and protection of the environment are given proper familiarization with their duties. Instructionswhich are essential to be provided prior to sailing should be identified, documented and given.6.4 The Company should ensure that all personnel involved in the Company's safety management system have an adequate understanding of relevant rules, regulations, codes and guidelines.6.5 The Company should establish and maintain procedures for identifying any training which may be required in support of the safety management system and ensure that such training is provided for all personnel concerned.6.6 The Company should establish procedures by which the ship's personnel receive relevant information on the safety management system in a working language or languages understood by them.6.7 The Company should ensure that the ship's personnel are able to communicate effectively in the execution of their duties related to the safety management system.7 DEVELOPMENT OF PLANS FOR SHIPBOARD OPERATIONSThe Company should establish procedures for the preparation of plans and instructions, including checklists as appropriate, for key shipboard operations concerning the safety of the ship and the prevention of pollution. The various tasks involved should be defined and assigned to qualified personnel.8 EMERGENCY PREPAREDNESS8.1 The Company should establish procedures to identify, describe and respond to potential emergency shipboard situations.8.2 The Company should establish programmes for drills and exercises to prepare for emergency actions.8.3 The safety management system should provide for measures ensuring that the Company's organization can respond at any time to hazards, accidents and emergency situations involving its ships.9 REPORTS AND ANALYSIS OF NON-CONFORMITIES, ACCIDENTS AND HAZARDOUS OCCURRENCES9.1 The safety management system should include procedures ensuring that non-conformities, accidents and hazardous situations are reported to the Company, investigated and analysed with the objective of improving safety and pollution prevention.9.2 The Company should establish procedures for the implementation of corrective action.10 MAINTENANCE OF THE SHIP AND EQUIPMENT10.1 The Company should establish procedures to ensure that the ship is maintained in conformity with the provisions of the relevant rules and regulations and with any additional requirements which may be established by the Company.10.2 In meeting these requirements the Company should ensure that:.1 inspections are held at appropriate intervals;.2 any non-conformity is reported, with its possible cause, if known;.3 appropriate corrective action is taken; and.4 records of these activities are maintained.10.3 The Company should establish procedures in its safety management system to identify equipment and technical systems the sudden operational failure of which may result in hazardous situations. The safety management system should provide for specific measures aimed at promoting the reliability of such equipment or systems. These measures should include the regular testing of stand-by arrangements and equipment or technical systems that are not in continuous use.10.4 The inspections mentioned in 10.2 as well as the measures referred to in 10.3 should be integrated into the ship's operational maintenance routine.11 DOCUMENTATION11.1 The Company should establish and maintain procedures to control all documents and data which are relevant to the safety management system.11.2 The Company should ensure that:.1 valid documents are available at all relevant locations;.2 changes to documents are reviewed and approved by authorized personnel; and.3 obsolete documents are promptly removed.11.3 The documents used to describe and implement the safety management system may be referred to as the Safety Management Manual. Documentation should be kept in a form that the Company considers most effective. Each ship should carry on board all documentation relevant to that ship.12 COMPANY VERIFICATION, REVIEW AND EV ALUATION12.1 The Company should carry out internal safety audits to verify whether safety and pollution-prevention activities comply with the safety management system.12.2 The Company should periodically evaluate the efficiency of and, when needed, review the safety management system in accordance with proceduresestablished by the Company.12.3 The audits and possible corrective actions should be carried out in accordance with documented procedures.12.4 Personnel carrying out audits should be independent of the areas being audited unless this is impracticable due to the size and the nature of the Company.12.5 The results of the audits and reviews should be brought to the attention of all personnel having responsibility in the area involved.12.6 The management personnel responsible for the area involved should take timely corrective action on deficiencies found.PART B - CERTIFICATION AND VERIFICATION13 CERTIFICATION AND PERIODICAL VERIFICATION13.1 The ship should be operated by a Company which has been issued with a Document of Compliance or with an Interim Document of Compliance in accordance with paragraph 14.1, relevant to that ship.13.2 The Document of Compliance should be issued by the Administration, by an organization recognized by the Administration or, at the request of the Administration, by another Contracting Government to the Convention to any Company complying with the requirements of this Code for a period specified by the Administration which should not exceed five years. Such a document should be accepted as evidence that the Company is capable of complying with the requirements of this Code.13.3 The Document of Compliance is only valid for the ship types explicitly indicated in the document. Such indication should be based on the types of ships on which the initial verification was based. Other ship types should only be added after verification of the Company's capability to comply with the requirements of this Code applicable to such ship types. In this context, ship types are those referred to in regulation IX/1 of the Convention.13.4 The validity of a Document of Compliance should be subject to annual verification by the Administration or by an organization recognized by the Administration or, at the request of the Administration, by another Contracting Government within three months before or after the anniversary date.13.5 The Document of Compliance should be withdrawn by the Administration or, at its request, by the Contracting Government which issued the Document when the annual verification required in paragraph 13.4 is not requested or if there is evidence of major non-conformities with this Code.13.5.1 All associated Safety Management Certificates and/or Interim Safety Management Certificates should also be withdrawn if the Document of Compliance is withdrawn.13.6 A copy of the Document of Compliance should be placed on board in order that the master of the ship, if so requested, may produce it for verification by theAdministration or by an organization recognized by the Administration or for the purposes of the control referred to in regulation IX/6.2 of the Convention. The copy of the Document is not required to be authenticated or certified.13.7 The Safety Management Certificate should be issued to a ship for a period which should not exceed five years by the Administration or an organization recognized by the Administration or, at the request of the Administration, by another Contracting Government. The Safety Management Certificate should be issued after verifying that the Company and its shipboard management operate in accordance with the approved safety management system. Such a Certificate should be accepted as evidence that the ship is complying with the requirements of this Code.13.8 The validity of the Safety Management Certificate should be subject to at least one intermediate verification by the Administration or an organization recognized by the Administration or, at the request of the Administration, by another Contracting Government. If only one intermediate verification is to be carried out and the period of validity of the Safety Management Certificate is five years, it should take place between the second and third anniversary dates of the Safety Management Certificate.13.9 In addition to the requirements of paragraph 13.5.1, the Safety Management Certificate should be withdrawn by the Administration or, at the request of the Administration, by the Contracting Government which has issued it when the intermediate verification required in paragraph 13.8 is not requested or if there is evidence of major non-conformity with this Code.13.10 ‚Notwithstanding the requirements of paragraphs 13.2 and 13.7, when the renewal verification is completed within three months before the expiry date of the existing Document of Compliance or Safety Management Certificate, the new Document of Compliance or the new Safety Management Certificate should be valid from the date of completion of the renewal verification for a period not exceeding five years from the date of expiry of the existing Document of Compliance or Safety Management Certificate.13.11 ‚When the renewal verification is completed more than three months before the expiry date of the existing Document of Compliance or Safety Management Certificate, the new Document of Compliance or the new Safety Management Certificate should be valid from the date of completion of the renewal verification for a period not exceeding five years from the date of completion of the renewal verification."14 INTERIM CERTIFICATION14.1 An Interim Document of Compliance may be issued to facilitate initial implementation of this Code when:.1 a Company is newly established; or.2 new ship types are to be added to an existing Document of Compliance,following verification that the Company has a safety management system that meets the objectives of paragraph 1.2.3 of this Code, provided the Company demonstrates plans to implement a safety management system meeting the full requirements of this Code within the period of validity of the Interim Document of Compliance. Such an Interim Document of Compliance should be issued for a period not exceeding 12 months by the Administration or by an organization recognized by the Administration or, at the request of the Administration, by another Contracting Government. A copy of the Interim Document of Compliance should be placed on board in order that the master of the ship, if so requested, may produce it for verification by the Administration or by an organization recognized by the Administration or for the purposes of the control referred to in regulation IX/6.2 of the Convention. The copy of the Document is not required to be authenticated or certified.14.2 An Interim Safety Management Certificate may be issued:.1 to new ships on delivery;.2 when a Company takes on responsibility for the operation of a ship which is new to the Company; or.3 when a ship changes flag.Such an Interim Safety Management Certificate should be issued for a period not exceeding 6 months by the Administration or an organization recognized by the Administration or, at the request of the Administration, by another Contracting Government.14.3 An Administration or, at the request of the Administration, another Contracting Government may, in special cases, extend the validity of an Interim Safety Management Certificate for a further period which should not exceed 6 months from the date of expiry.14.4 An Interim Safety Management Certificate may be issued following verification that:.1 the Document of Compliance, or the Interim Document of Compliance, is relevant to the ship concerned;.2 the safety management system provided by the Company for the ship concerned includes key elements of this Code and has been assessed during the audit for issuance of the Document of Compliance or demonstrated for issuance of the Interim Document of Compliance;.3 the Company has planned the audit of the ship within three months;.4 the master and officers are familiar with the safety management system and the planned arrangements for its implementation;.5 instructions, which have been identified as being essential, are provided prior to sailing; and.6 relevant information on the safety management system has been given in a working language or languages understood by the ship's personnel.15 VERIFICATION15.1 All verifications required by the provisions of this Code should be carried out in accordance with procedures acceptable to the Administration, taking into account the guidelines developed by the Organization.16 FORMS OF CERTIFICATES16.1 The Document of Compliance, the Safety Management Certificate, the Interim Document of Compliance and the Interim Safety Management Certificate should be drawn up in a form corresponding to the models given in the appendix to this Code. If the language used is neither English nor French, the text should include a translation into one of these languages.16.2 In addition to the requirements of paragraph 13.3, the ship types indicated on the Document of Compliance and the Interim Document of Compliance may be endorsed to reflect any limitations in the operations of the ships described in the safety management system.。
要遵守安全管理规定英文(3篇)

第1篇Introduction:Safety management regulations are essential guidelines thatorganizations must follow to ensure the well-being of their employees, clients, and the general public. These regulations are designed to minimize risks, prevent accidents, and create a safe working environment. Adhering to these regulations is not just a legal requirement but also a moral obligation. In this article, we will discuss the significance of adhering to safety management regulations, the potential consequences of non-compliance, and the best practices for maintaining a safe workplace.I. The Significance of Adhering to Safety Management Regulations1. Protecting lives and healthThe primary reason for adhering to safety management regulations is to protect the lives and health of individuals within the workplace. Accidents can lead to severe injuries, disabilities, or even fatalities. By following safety protocols, organizations can significantly reducethe risk of such incidents.2. Legal obligationsMany countries have stringent laws and regulations that require organizations to ensure the safety of their employees and the public. Non-compliance with these laws can result in heavy fines, legal actions, and reputational damage.3. Financial savingsAdhering to safety management regulations can lead to financial savings. By preventing accidents, organizations can avoid costly medical expenses, insurance claims, and potential lawsuits. Additionally, a safe workplace can attract and retain skilled employees, reducing turnover rates.4. Enhanced productivityA safe workplace promotes a positive work environment, which can lead to increased productivity. Employees who feel secure and valued are more likely to be motivated and focused on their tasks.5. Brand reputationOrganizations that prioritize safety management are often perceived as responsible and trustworthy. This can enhance their brand reputation and differentiate them from competitors.II. Potential Consequences of Non-Compliance1. Legal penaltiesNon-compliance with safety management regulations can result in legal penalties, including fines, imprisonment, and loss of business licenses. These penalties can be severe, especially for repeat offenders.2. Increased insurance premiumsInsurance companies may increase premiums for organizations that have a history of non-compliance with safety regulations. This can lead to increased costs and reduced profitability.3. Reputational damageNon-compliance with safety management regulations can damage an organization's reputation, leading to loss of customers, partners, and investors.4. Loss of employeesEmployees who work in unsafe conditions may seek employment elsewhere. This can result in increased turnover rates, loss of skilled workers, and potential training costs.5. Increased accidents and injuriesNon-compliance with safety management regulations can lead to an increase in accidents and injuries, which can have a lasting impact on individuals and their families.III. Best Practices for Maintaining a Safe Workplace1. Develop and implement a safety management systemOrganizations should establish a comprehensive safety management system that includes policies, procedures, and training programs. This system should be regularly reviewed and updated to address emerging risks.2. Conduct risk assessmentsRegular risk assessments should be conducted to identify potential hazards in the workplace. Once identified, appropriate control measures should be implemented to minimize risks.3. Provide training and educationEmployees should be provided with adequate training and education on safety management regulations and best practices. This includes familiarizing them with safety equipment, emergency procedures, and how to report hazards.4. Encourage a safety cultureA strong safety culture is essential for a safe workplace. Organizations should encourage employees to take an active role in promoting safety, reporting hazards, and participating in safety initiatives.5. Regular inspections and auditsRegular inspections and audits should be conducted to ensure compliance with safety management regulations. Any non-compliance should be addressed promptly.6. Maintain safety equipmentSafety equipment should be regularly maintained and inspected to ensure it is in good working condition. This includes fire extinguishers, first aid kits, and personal protective equipment (PPE).7. Communicate with employeesOpen communication between management and employees is crucial for maintaining a safe workplace. Employees should be informed of any changes to safety management regulations, and their feedback should be valued and acted upon.Conclusion:Adhering to safety management regulations is of utmost importance for organizations. By prioritizing safety, organizations can protect lives, reduce costs, enhance productivity, and maintain a positive reputation. Non-compliance with these regulations can lead to severe consequences, including legal penalties, financial losses, and reputational damage. Therefore, it is essential for organizations to implement and maintain effective safety management systems and promote a strong safety culture within their workplaces.第2篇Introduction:Safety management regulations are crucial for ensuring a secure and productive work environment. These regulations are designed to minimize the risk of accidents, injuries, and health issues. Adhering to these regulations not only protects the well-being of employees but also helps in maintaining a smooth workflow and preventing costly damages. In this article, we will discuss the importance of safety management regulations and provide guidelines on how to comply with them effectively.I. The Importance of Safety Management Regulations1.1 Protection of Employees:Safety management regulations are implemented to safeguard the health and well-being of employees. By adhering to these regulations, organizations can minimize the risk of accidents, injuries, and occupational diseases. This not only ensures the physical safety of employees but also enhances their mental well-being.1.2 Legal Compliance:Adhering to safety management regulations is a legal requirement in many countries. Failure to comply with these regulations can result in fines, penalties, and even legal action against the organization. By adhering to these regulations, organizations can avoid legal repercussions and maintain a good reputation.1.3 Cost Reduction:Safety management regulations help in reducing costs associated with accidents and injuries. By preventing accidents, organizations can save on medical expenses, compensation claims, and potential loss of productivity. Moreover, adhering to these regulations can help in obtaining insurance discounts.1.4 Improved Productivity:A safe work environment fosters a positive atmosphere, which leads to increased productivity. Employees are more likely to be motivated and focused when they feel secure and confident in their workplace. By adhering to safety management regulations, organizations can create a conducive environment for their employees to perform at their best.II. Key Safety Management Regulations2.1 General Safety Measures:2.1.1 Proper Training:Employees should receive adequate training on safety procedures, emergency response, and the use of safety equipment. This training should be regularly updated to ensure that employees are aware of any changes in safety protocols.2.1.2 Safety Equipment:Organizations should provide and maintain appropriate safety equipment, such as personal protective equipment (PPE), fire extinguishers, andfirst aid kits. Employees should be trained on how to use these equipment effectively.2.1.3 Signage and Warning Systems:Clear signage and warning systems should be installed in areas where potential hazards exist. This helps in alerting employees to potential risks and ensuring they take appropriate precautions.2.2 Workplace Safety:2.2.1 Proper Lighting:Workplaces should be well-lit to prevent accidents caused by poor visibility. This includes ensuring adequate lighting in dark areas, such as storage rooms and staircases.2.2.2 Safe Access and Egress:Workplaces should have safe access and egress routes, free from obstacles and hazards. This includes maintaining clear pathways, ensuring proper use of emergency exits, and providing adequate signage.2.2.3 Equipment Maintenance:Regular maintenance of equipment is essential to prevent accidents. Organizations should establish a maintenance schedule and ensure thatall equipment is in good working condition.2.3 Health and Hygiene:2.3.1 Cleanliness:Workplaces should be kept clean and hygienic to prevent the spread of diseases and maintain a healthy environment. This includes regular cleaning of work areas, restrooms, and common areas.2.3.2 Waste Management:Proper waste management is crucial to prevent accidents and health issues. Organizations should establish a waste management system and ensure that waste is disposed of safely and responsibly.III. How to Comply with Safety Management Regulations3.1 Establish a Safety Management System:Organizations should develop a comprehensive safety management system that encompasses all aspects of safety, including policies, procedures, and training programs. This system should be regularly reviewed and updated to ensure its effectiveness.3.2 Assign Responsibility:Clearly define the roles and responsibilities of employees regarding safety management. Assign a safety officer or team responsible for overseeing the implementation and enforcement of safety regulations.3.3 Conduct Risk Assessments:Regularly conduct risk assessments to identify potential hazards in the workplace. This helps in implementing appropriate control measures and preventing accidents.3.4 Monitor and Review:Regularly monitor the effectiveness of safety management measures and review the outcomes. This includes analyzing accident reports, conducting inspections, and seeking feedback from employees.3.5 Encourage a Safety Culture:Foster a safety culture within the organization by promoting the importance of safety and encouraging employees to report hazards and near-misses. Recognize and reward employees who demonstrate a commitment to safety.Conclusion:Adhering to safety management regulations is essential for creating a secure and productive work environment. By following the guidelines provided in this article, organizations can minimize the risk of accidents, injuries, and health issues, while also enhancing employee morale and productivity. Remember, a safe workplace is a responsible workplace.第3篇Introduction:Safety management regulations are crucial in ensuring the well-being of individuals and the smooth operation of organizations. These regulations are designed to minimize risks, prevent accidents, and create a safe working environment. Adhering to these regulations is not only a legal requirement but also a moral responsibility. This article aims to highlight the importance of adhering to safety management regulations and provide insights into the benefits and consequences of non-compliance.I. Understanding Safety Management Regulations1. Definition:Safety management regulations encompass a set of rules, policies, and guidelines established by governments, organizations, and industries to ensure the safety and health of individuals in the workplace.2. Scope:These regulations apply to various sectors, including manufacturing, construction, healthcare, transportation, and more. They cover aspects such as occupational health, fire safety, electrical safety, and emergency response.3. Key Principles:a. Risk Assessment: Identifying potential hazards and evaluating the likelihood and severity of accidents or incidents.b. Control Measures: Implementing measures to eliminate or reduce risks to an acceptable level.c. Training and Awareness: Ensuring that employees are trained and aware of safety procedures and regulations.d. Compliance and Auditing: Regularly reviewing and auditing compliance with safety management regulations.II. Benefits of Adhering to Safety Management Regulations1. Reduced Risk of Accidents:Compliance with safety management regulations significantly reduces the likelihood of accidents, injuries, and fatalities in the workplace. By identifying and mitigating risks, organizations can create a safer environment for their employees.2. Improved Productivity:A safe working environment leads to increased productivity. Employees are more focused and motivated when they feel secure, resulting in higher quality work and reduced downtime due to accidents.3. Legal Compliance:Adhering to safety management regulations ensures that organizations comply with legal requirements. Non-compliance can lead to fines, penalties, and legal action, which can have severe financial and reputational consequences.4. Employee Morale and Retention:A safe workplace fosters a positive work culture and improves employee morale. Employees are more likely to remain with an organization that prioritizes their safety and well-being, reducing turnover rates.5. Reputation and Brand Image:Compliance with safety management regulations enhances an organization's reputation and brand image. Customers, stakeholders, and the public perceive organizations that prioritize safety as responsible and trustworthy.III. Consequences of Non-Compliance1. Accidents and Injuries:Non-compliance with safety management regulations increases the risk of accidents and injuries, leading to human suffering, medical expenses, and long-term disabilities.2. Financial Penalties:Organizations that fail to comply with safety regulations may face fines, penalties, and legal action. These costs can significantly impact the financial stability of the organization.3. Reputational Damage:Non-compliance can tarnish an organization's reputation, leading to a loss of customer trust, investor confidence, and potential business opportunities.4. Legal Action:Organizations that violate safety management regulations may face legal action, including criminal charges, which can result in fines, imprisonment, and other legal consequences.IV. Implementing Safety Management Regulations1. Establishing Policies and Procedures:Organizations should develop comprehensive safety management policiesand procedures that align with relevant regulations and industry standards.2. Training and Education:Regular training sessions should be conducted to ensure that employees are aware of safety procedures, regulations, and potential hazards.3. Risk Assessment and Control:Organizations should conduct regular risk assessments to identify potential hazards and implement control measures to minimize risks.4. Compliance Auditing:Regular audits should be conducted to ensure compliance with safety management regulations. Any identified non-compliance should be addressed promptly.5. Continuous Improvement:Organizations should strive for continuous improvement in their safety management practices, incorporating feedback from employees and stakeholders.Conclusion:Adhering to safety management regulations is essential for creating a safe and healthy workplace. By prioritizing safety, organizations can reduce accidents, improve productivity, and enhance their reputation. Non-compliance with these regulations can lead to severe consequences, including accidents, injuries, financial penalties, and reputational damage. It is crucial for organizations to implement and maintain effective safety management practices to ensure the well-being of their employees and the success of their operations.。
安全生产管理制度英文
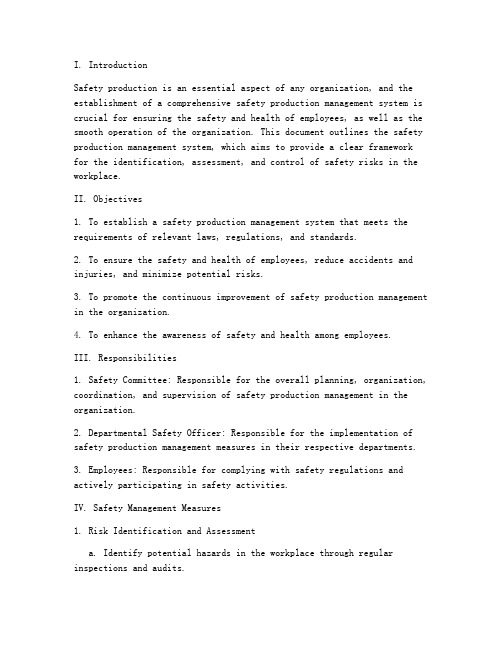
I. IntroductionSafety production is an essential aspect of any organization, and the establishment of a comprehensive safety production management system is crucial for ensuring the safety and health of employees, as well as the smooth operation of the organization. This document outlines the safety production management system, which aims to provide a clear frameworkfor the identification, assessment, and control of safety risks in the workplace.II. Objectives1. To establish a safety production management system that meets the requirements of relevant laws, regulations, and standards.2. To ensure the safety and health of employees, reduce accidents and injuries, and minimize potential risks.3. To promote the continuous improvement of safety production management in the organization.4. To enhance the awareness of safety and health among employees.III. Responsibilities1. Safety Committee: Responsible for the overall planning, organization, coordination, and supervision of safety production management in the organization.2. Departmental Safety Officer: Responsible for the implementation of safety production management measures in their respective departments.3. Employees: Responsible for complying with safety regulations and actively participating in safety activities.IV. Safety Management Measures1. Risk Identification and Assessmenta. Identify potential hazards in the workplace through regular inspections and audits.b. Assess the risks associated with these hazards based on the severity, probability, and impact on employees' safety and health.c. Establish risk control measures to mitigate potential risks.2. Safety Training and Educationa. Provide regular safety training and education for employees to enhance their awareness of safety and health.b. Develop and implement a comprehensive safety training program covering all aspects of safety in the workplace.c. Conduct periodic safety drills to ensure employees are prepared for emergencies.3. Safety Equipment and Facilitiesa. Provide and maintain necessary safety equipment and facilities in the workplace.b. Regularly inspect and maintain safety equipment to ensure their proper functioning.c. Implement a strict usage and maintenance schedule for safety equipment.4. Safety Inspections and Auditsa. Conduct regular safety inspections and audits to identify and correct potential hazards.b. Investigate accidents and incidents to determine the root causes and implement corrective measures.c. Report safety findings and progress to the safety committee.5. Emergency Response and First Aida. Establish an emergency response plan to handle accidents, fires, and other emergencies.b. Provide first aid training for employees to ensure they can provide immediate assistance in case of an emergency.c. Ensure that emergency equipment and supplies are readily available and accessible.V. Continuous Improvement1. Monitor the effectiveness of the safety production management system through regular reviews and audits.2. Implement corrective and preventive measures based on the findings of safety inspections and audits.3. Encourage employee feedback and participation in the continuous improvement of safety production management.4. Update the safety production management system as needed to address new risks and challenges.VI. ConclusionThe establishment of a comprehensive safety production management system is vital for ensuring the safety and health of employees, as well as the smooth operation of the organization. By following the guidelines outlined in this document, the organization can effectively manage safety risks and create a safer working environment for all employees.。
安全管理制度 英文

安全管理制度英文1. IntroductionThe safety management system (SMS) is an integral part of our organization's commitment to ensuring the health, safety, and well-being of all employees, contractors, and visitors. This document outlines the key elements of our SMS and provides guidance for its implementation and continuous improvement.2. Policy StatementOur organization is committed to providing a safe and healthy work environment for all employees, contractors, and visitors. We believe that safety is a shared responsibility and that every individual has a role to play in maintaining a safe workplace. We are committed to complying with all applicable safety regulations and standards, and strive to continuously improve our safety performance.3. Roles and ResponsibilitiesKey roles and responsibilities within our SMS include:• Senior Management: Senior management is responsible for providing leadership and resources to support the implementation of the SMS. They are also responsible for setting safety objectives and targets, and ensuring that the SMS is effectively implemented and maintained.• Safety Manager: The safety manager is responsible for overseeing the day-to-day operation of the SMS, including developing and maintaining safety policies and procedures, conducting safety training, and monitoring and reporting on safety performance.• Employees: All employees are responsible for following safety policies and procedures, reporting safety hazards and near misses, and participating in safety training and awareness programs.• Contractors: Contractors working on our premises are expected to comply with our safety policies and procedures, and to take all necessary precautions to ensure their own safety and the safety of others.4. Risk Assessment and Hazard IdentificationThe first step in our SMS is to identify and assess potential safety hazards in the workplace. This involves conducting regular inspections and risk assessments to identify hazards and assess the level of risk associated with each hazard. Hazard identification and risk assessments should be documented and reviewed on a regular basis to ensure that new hazards are identified and that existing hazards are effectively managed.5. Safety Policies and ProceduresOnce hazards have been identified and assessed, appropriate safety policies and procedures should be developed to address these hazards. Safety policies and procedures should be based on best practices and regulatory requirements, and should be communicated to all employees and contractors. It is important that policies and procedures are regularly reviewed and updated to ensure that they remain relevant and effective.6. Safety Training and AwarenessEffective safety training and awareness programs are essential for ensuring that all employees and contractors are aware of the potential safety hazards in the workplace, and know how to work safely. Training should cover topics such as hazard identification, safe work practices, emergency procedures, and the proper use of personal protective equipment. Safety training should be provided to all new employees and contractors, as well as on an ongoing basis to ensure that all individuals remain aware of safety best practices.7. Incident Reporting and InvestigationIt is important that all safety incidents, including near misses, accidents, and injuries, are reported and investigated in a timely manner. Incident reporting and investigation should be conducted in accordance with established procedures, and should focus on identifying the root causes of the incident and implementing appropriate corrective actions to prevent a recurrence. Incident data should be analyzed to identify trends and opportunities for improvement.8. Emergency PreparednessOur organization is committed to ensuring that all employees and contractors are prepared to respond effectively to emergency situations. This includes developing and regularly testing emergency response plans, conducting emergency drills and exercises, and providing training to employees and contractors on how to respond to various emergency scenarios. Emergency preparedness activities should be reviewed and updated on a regular basis to ensure that they remain effective.9. Monitoring and MeasurementTo ensure the effectiveness of our SMS, it is important to regularly monitor and measure safety performance. This can be done through a variety of methods, including safety inspections, audits, and performance indicators. Monitoring and measurement activities should be used to identify areas for improvement and to track progress towards safety objectives and targets.10. Management ReviewRegular management review of the SMS is essential for ensuring that it remains effective and relevant. Management review meetings should be held at regular intervals to review safety performance, identify opportunities for improvement, and set new safety objectivesand targets. Management should also use these meetings to demonstrate leadership and commitment to safety.11. Continuous ImprovementContinuous improvement is a key principle of our SMS. We believe that by regularly reviewing and improving our safety policies, procedures, and practices, we can create a safer and healthier work environment for all. We encourage all employees and contractors to actively participate in the continuous improvement of our SMS.12. ConclusionOur organization is committed to the ongoing advancement of our safety management system. By working together, we can achieve our goal of creating a safe and healthy work environment for all. We encourage all individuals to take an active role in promoting a positive safety culture and in contributing to the continuous improvement of our SMS.。
安全生产管理制度中英文

一、总则1.1 为加强公司安全生产管理,保障员工生命财产安全,预防和减少事故发生,根据国家有关安全生产法律法规,结合公司实际情况,制定本制度。
1.2 本制度适用于公司所有员工、承包商、供应商等相关人员。
二、组织机构与职责2.1 公司成立安全生产委员会,负责公司安全生产工作的全面领导、协调和监督。
2.2 安全生产委员会下设安全管理部门,负责具体实施安全生产工作。
2.3 各部门、车间、班组应设立安全员,负责本部门、车间、班组的安全生产工作。
三、安全生产责任制3.1 公司领导对本单位的安全生产工作全面负责。
3.2 各部门、车间、班组负责人对本单位安全生产工作负直接领导责任。
3.3 员工对本岗位的安全生产工作负直接责任。
3.4 承包商、供应商应遵守本制度,并对其施工、作业过程中的安全生产工作负责。
四、安全生产教育培训4.1 公司应定期对员工进行安全生产教育培训,提高员工的安全意识和安全技能。
4.2 新员工入职前,必须经过安全生产教育培训,并取得合格证书后方可上岗。
4.3 安全生产教育培训内容包括但不限于:安全生产法律法规、安全生产规章制度、安全操作规程、事故案例分析等。
五、安全生产检查与隐患排查5.1 公司应定期开展安全生产检查,及时发现和消除安全隐患。
5.2 安全管理部门应建立安全隐患排查治理制度,对发现的安全隐患进行跟踪治理。
5.3 员工发现安全隐患应立即报告,安全管理部门应组织人员进行处理。
六、事故报告与处理6.1 事故发生后,事故单位应立即向公司安全生产委员会报告,并采取措施控制事故扩大。
6.2 安全管理部门应组织事故调查组,对事故原因进行调查分析,提出处理意见。
6.3 事故调查报告应报公司领导审批,并按规定上报相关部门。
七、奖惩措施7.1 对在安全生产工作中表现突出的单位和个人给予表彰和奖励。
7.2 对违反安全生产规定、造成事故的责任人,依法依规进行处罚。
八、附则8.1 本制度由公司安全生产委员会负责解释。
安全生产管理制度中英文

一、总则第一条为加强我公司安全生产管理,保障员工生命财产安全,预防事故发生,提高公司安全生产水平,根据国家有关安全生产的法律、法规和政策,结合我公司实际情况,制定本制度。
第二条本制度适用于我公司所有员工、管理人员及外包单位。
第三条我公司坚持“安全第一、预防为主、综合治理”的安全生产方针,以人为本,强化责任,确保安全生产。
二、安全生产组织机构及职责第四条我公司成立安全生产委员会,负责安全生产工作的组织、领导和协调。
第五条安全生产委员会下设安全管理部门,负责以下工作:(一)组织制定和实施安全生产规章制度;(二)组织开展安全生产宣传教育;(三)组织开展安全生产检查、隐患排查和治理;(四)组织安全生产事故的调查处理;(五)负责安全生产资料的收集、整理和归档。
第六条各部门、车间、班组应设立安全生产管理人员,负责本部门、车间、班组的安全生产工作。
三、安全生产教育培训第七条我公司应定期对员工进行安全生产教育培训,提高员工的安全意识和技能。
第八条新员工入职前,必须接受安全生产教育培训,经考核合格后方可上岗。
第九条对从事特殊工种、特种作业的员工,必须按照国家规定进行专门的安全教育培训,取得相应资格证书后方可上岗。
第十条安全生产教育培训内容应包括:(一)国家安全生产法律法规;(二)公司安全生产规章制度;(三)安全生产操作规程;(四)事故案例分析;(五)应急救援知识。
四、安全生产检查与隐患排查治理第十一条我公司应定期开展安全生产检查,及时发现和消除安全隐患。
第十二条安全生产检查内容包括:(一)安全生产责任制落实情况;(二)安全生产规章制度执行情况;(三)安全生产设施设备完好情况;(四)安全防护用品配备和使用情况;(五)作业现场安全管理情况。
第十三条对检查中发现的安全隐患,应及时整改,消除安全隐患。
第十四条对重大安全隐患,应制定整改方案,明确整改责任人、整改措施和整改期限。
第十五条对整改后的安全隐患,应进行复查,确保整改到位。
安全生产管理制度英文
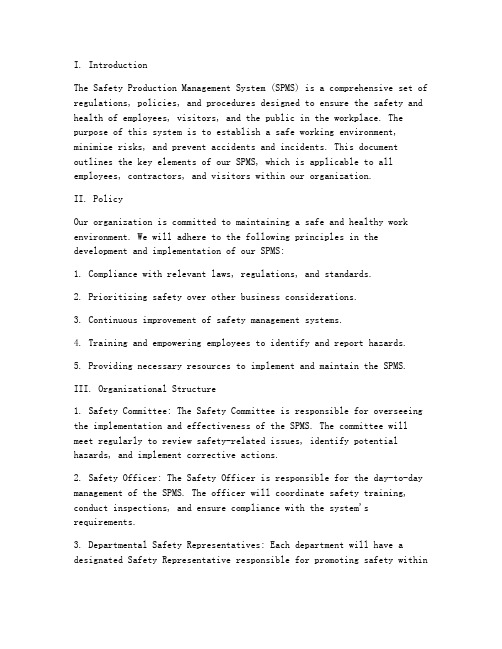
I. IntroductionThe Safety Production Management System (SPMS) is a comprehensive set of regulations, policies, and procedures designed to ensure the safety and health of employees, visitors, and the public in the workplace. The purpose of this system is to establish a safe working environment, minimize risks, and prevent accidents and incidents. This document outlines the key elements of our SPMS, which is applicable to all employees, contractors, and visitors within our organization.II. PolicyOur organization is committed to maintaining a safe and healthy work environment. We will adhere to the following principles in the development and implementation of our SPMS:1. Compliance with relevant laws, regulations, and standards.2. Prioritizing safety over other business considerations.3. Continuous improvement of safety management systems.4. Training and empowering employees to identify and report hazards.5. Providing necessary resources to implement and maintain the SPMS.III. Organizational Structure1. Safety Committee: The Safety Committee is responsible for overseeing the implementation and effectiveness of the SPMS. The committee will meet regularly to review safety-related issues, identify potential hazards, and implement corrective actions.2. Safety Officer: The Safety Officer is responsible for the day-to-day management of the SPMS. The officer will coordinate safety training, conduct inspections, and ensure compliance with the system's requirements.3. Departmental Safety Representatives: Each department will have a designated Safety Representative responsible for promoting safety withintheir respective areas. These representatives will report to the Safety Officer and provide input on safety-related matters.IV. Safety Training and Communication1. New Employee Orientation: All new employees must complete a comprehensive safety training program, which includes familiarization with the SPMS, hazard identification, and emergency procedures.2. Regular Safety Training: Employees will receive regular safety training sessions to reinforce their understanding of the SPMS and to keep them updated on any changes to the system.3. Communication: Safety-related information will be communicated through various channels, including meetings, bulletins, posters, and electronic newsletters.V. Risk Assessment and Control1. Hazard Identification: All employees are encouraged to identify potential hazards in their work environment. The Safety Officer will conduct periodic inspections to ensure compliance with the SPMS.2. Risk Assessment: A risk assessment will be conducted for each identified hazard to determine the likelihood and severity of potential accidents and incidents.3. Control Measures: Appropriate control measures will be implemented to eliminate or reduce the identified risks. These measures may include engineering controls, administrative controls, and personal protective equipment (PPE).VI. Incident Reporting and Investigation1. Incident Reporting: All accidents, injuries, and near-misses must be reported immediately to the Safety Officer. The reporting process is designed to ensure that incidents are investigated and addressed promptly.2. Investigation: The Safety Officer will conduct a thorough investigation of all reported incidents to determine the root cause and implement corrective actions to prevent recurrence.VII. Monitoring and Review1. Regular Audits: The SPMS will be subject to regular audits to ensure compliance with the system's requirements and to identify areas for improvement.2. Continuous Improvement: The Safety Committee will review the SPMS ona regular basis to identify opportunities for improvement and implement changes as necessary.By implementing this Safety Production Management System, our organization aims to create a safe and healthy work environment for all stakeholders. We encourage everyone to actively participate in promoting and maintaining safety in the workplace.。
- 1、下载文档前请自行甄别文档内容的完整性,平台不提供额外的编辑、内容补充、找答案等附加服务。
- 2、"仅部分预览"的文档,不可在线预览部分如存在完整性等问题,可反馈申请退款(可完整预览的文档不适用该条件!)。
- 3、如文档侵犯您的权益,请联系客服反馈,我们会尽快为您处理(人工客服工作时间:9:00-18:30)。
安全管理工作规定Safety ManagementRules 为强化安全管理,提高广大员工和外来人员的安全意识,确保员工利益和公司利益不受侵害,经公司经理办公会研究决定,制订本安全管理工作规定。
In order to strengthen thesafety management,raise thesafety consciousnessof our staffand outside rs and protect both the companyandour staff’sinterest not to beinfringed,the safety management rules weredeveloped.1。
公司内部安全管理规定:Internal safety management rules:1。
1进入生产区任何人不准携带火种、香烟及易燃易爆品,门卫设有存放箱,可以存放上述违禁物品。
动力车间电焊工用火由动力车间安排专人发放并及时回收。
Anybody who accesses totheproduction area mustn’t bring any kindling materials,cigarette and flammable andexplosive substances. All of these contr abandarticles can be stored in thestorage bins in theentrance guard room。
When welders conducthot work,the maintenanceworkshop should arrange specific persontoprovide needed hot work tools and materialswhich should be token back timely.1。
2 除上下班按照规定的路线通过生产区外,进入生产区必须按规定使用安全帽、安全眼镜、安全鞋等防护用品.生产区内除车间办公室、更衣室、澡堂、卫生间外,其余地方必须按规定使用安全帽、安全眼镜、安全鞋等防护用品。
菌种室、化验室人员在室内操作时必须戴安全眼镜,接触化学药品时必须穿安全鞋。
Whenentertheproduction area,people must puton the protectionarticles such as hard hat,goggl es and safety shoes。
Besides,stated routeshouldbe used whiling enteringor leaving the production area. People mustputonthe protectionarticles such as hard hat, gogglesand safety shoes in theproduction area, except those in the office of the workshops, locker rooms,bathhouses and thewashrooms.Operat orsmust wear goggles when they workin theculture development lab and the in process lab and put on their safety shoes when they contactwith chemicals。
1.3 各岗位员工必须严格执行公司统一制订的岗位安全操作规程。
Every personintheposition must strictlyen forcethe positionsafety operation specifications。
1.4 生产区内除维修车间所在区域外所有动火必须取得动火证后方可进行;进密闭空间操作、吊装作业操作、压力容器检修、登高作业、管线打开操作和开挖操作等必须取得许可证后方可进行。
In the productionarea,all the using offir emust getthepermit exceptthat in the areas of maintenance workshop.Peoplecan do worksuch as confinedspace operations,liftingoperations, pressure vessel inspection,high altitude operation,operation of opening the pipelines and excavations only aftergetting the permit。
1。
5 燃油叉车不得进入包装库或生产车间作业;非防爆叉车不得进入提取车间作业。
The fuel—burned forklift mustn't gointothe packaging workshop or productionworkshops to work; nonex plosion-proof forklift mustn't go into therecoveryworkshop.1。
6 车间操作工、维修工不得将通讯工具带到岗位,非岗位操作工进入车间各工序必须关闭通讯工具.The operatorsandmaintainers in workshopsmustn't carryaboutany telecommunication facility tothe position; those nonposition operators must shut off the telecommunication facilities whengo intotheworksh ops。
1.7车辆进入生产区必须加套防火罩。
Any vehiclegoes into the production area must cover the flameproof enclosures.2.公司内部违章处罚规定:Internal penalty forviolationof regulation:2.1凡违反公司内部安全管理规定、岗位安全操作规程的,由公司安全委员会调查研究做出轻微性违章、一般性违章或严重性违章结论。
属轻微性违章,发生一次罚款100元;属一般性违章,未造成大的经济损失和人身伤害事故,发生第一次,违章人员在厂内进行3—5天的学习、培训,通过安全培训考试合格后才能上岗,并扣发当月绩效工资;同一人发生第二次违章开除厂籍。
属严重性违章,违反公司明令禁止的行为(在厂区内吸烟、酒后上班、无许可动火作业、不戴安全帽等行为),或存在潜在隐患或造成较大经济损失或人身伤害事故的,发生一次开除厂籍,情节特别严重的依法追究法律责任。
Foranyviolation of the internalsafety man agement regulation andposition safetyoperation specifications,the company safety committeewill investigate and reach a decisionof minor violation, me dium violationor severeviolation. If the violation is a minor one,forthe first time, we will fine thepe rson 100RMB;ifthe violation is mediumwithout anygreat economic lossesor personal injury and itisthe firsttime, the peopleviolate theregulation will be punished to takepart insafetytraining for 3—5days, and can return tohis/her work only ifhe/she passesthe exam ofthe safety training。
Also the performancesalaryof themonth will be dedu cted as fine.The same person violates second timewill be dismissed。
If the violation is a severeone andb elongs to thoseprohibited with public proclamation(smoke in the plant, go to work afterdrinking,use fire wit hout permitand workwithouta hard hat) orwithany greateconomic losses or personal injuryor potentialhazard and if it isthefirst time,the p eople violate the regulation willbe dismissed;besi des,he/she maybeunderlegalsanction。
2.2凡本部门中有因违章开除厂籍的或一年内同一部门在同一安全问题上发生两次一般性违章的,部门主要负责人和违章人员所在班工段长在厂内进行3-5天的学习、培训,通过安全培训考试合格后才能上岗,并扣发当月绩效工资;一年内同一部门在同一安全问题上发生两次严重违章或本部门发生三次及以上严重违章的,撤消部门主要负责人和违章人员所在班工段长职务,情节特别严重的依法追究法律责任。
同时在年底考评时对分管经理、安全经理、总经理做出处罚。
If there isany person that isdismissed ortwo mediumviolations on the same safety issue in thes ame departmentinoneyear,the key directorand the section chief willbepunished to take part insafetytrainingfor3—5 days,andcan return to theirworkonly if they pass theexam of the safety training. Also the performancesalary of themonth will be deducted as fine。