CCD多晶硅刻蚀技术研究
多晶硅反应离子刻蚀加工
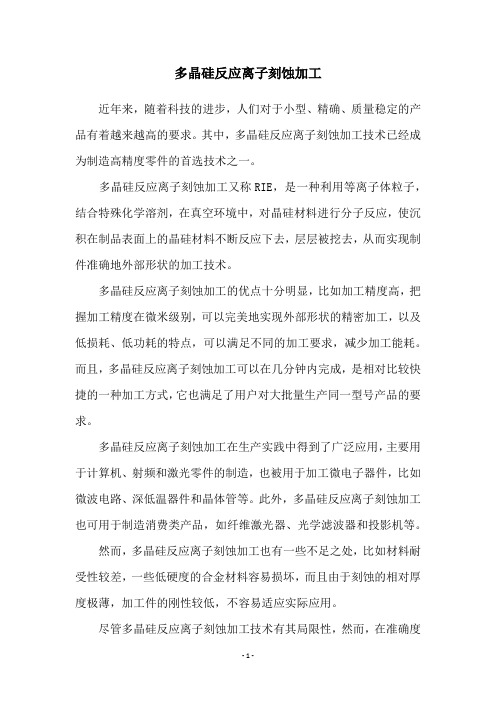
多晶硅反应离子刻蚀加工近年来,随着科技的进步,人们对于小型、精确、质量稳定的产品有着越来越高的要求。
其中,多晶硅反应离子刻蚀加工技术已经成为制造高精度零件的首选技术之一。
多晶硅反应离子刻蚀加工又称RIE,是一种利用等离子体粒子,结合特殊化学溶剂,在真空环境中,对晶硅材料进行分子反应,使沉积在制品表面上的晶硅材料不断反应下去,层层被挖去,从而实现制件准确地外部形状的加工技术。
多晶硅反应离子刻蚀加工的优点十分明显,比如加工精度高,把握加工精度在微米级别,可以完美地实现外部形状的精密加工,以及低损耗、低功耗的特点,可以满足不同的加工要求,减少加工能耗。
而且,多晶硅反应离子刻蚀加工可以在几分钟内完成,是相对比较快捷的一种加工方式,它也满足了用户对大批量生产同一型号产品的要求。
多晶硅反应离子刻蚀加工在生产实践中得到了广泛应用,主要用于计算机、射频和激光零件的制造,也被用于加工微电子器件,比如微波电路、深低温器件和晶体管等。
此外,多晶硅反应离子刻蚀加工也可用于制造消费类产品,如纤维激光器、光学滤波器和投影机等。
然而,多晶硅反应离子刻蚀加工也有一些不足之处,比如材料耐受性较差,一些低硬度的合金材料容易损坏,而且由于刻蚀的相对厚度极薄,加工件的刚性较低,不容易适应实际应用。
尽管多晶硅反应离子刻蚀加工技术有其局限性,然而,在准确度要求极高的应用领域,它仍然可以提供贴切的解决方案,这也是它一直受欢迎的原因。
因此,如何优化多晶硅反应离子刻蚀加工技术的应用,提高多晶硅反应离子刻蚀加工的效率和质量,是值得深入研究的课题。
总之,多晶硅反应离子刻蚀加工具有卓越的加工精度,节能环保和快速加工等优点,目前已经被广泛用于各种微米级别的精密加工领域。
未来,随着用户需求的进一步提升,多晶硅反应离子刻蚀加工技术将会发挥更大的作用。
多晶干法刻蚀

多晶干法刻蚀是一种重要的半导体工艺步骤,主要应用于制造集成电路。
以下是关于多晶干法刻蚀的详细解释:
1. 刻蚀多晶硅时,必须确保掩膜上的尺寸准确地转移到多晶硅上。
2. 刻蚀后的轮廓也非常重要,例如,如果多晶硅刻蚀后栅极侧壁有倾斜,可能会屏蔽后续工艺中源极和
漏极的离子注入,导致杂质分布不均,同时沟道的长度会随栅极倾斜的程度而改变。
3. 对sio2的刻蚀选择比要足够高,这是因为需要去除阶梯残留,避免多晶硅电极间短路的发生。
同时,
多晶硅一般覆盖在很薄的栅极氧化层上,如果氧化层被完全刻蚀,则氧化层下的源极和漏极区域可能会被快速刻蚀。
4. 选择适当的刻蚀气体也是非常重要的。
CF4、SF6等F原子为主的等离子体是常用的刻蚀气体,但这类
气体也存在负载效应,即被刻蚀材料裸露在等离子体中面积较大的区域时刻蚀速率比在面积较小的区域时慢,导致局部刻蚀速率的不均匀。
5. 在干法刻蚀中,多晶硅相对于氮化硅和二氧化硅下层的选择性较差,因此需要非常精确地优化干蚀刻
配方和蚀刻时间的精细控制。
6. 另外,对于多晶硅的干法刻蚀,控制其过度刻蚀也非常重要。
这是因为过度刻蚀可能会导致多晶硅的
电阻不均匀。
总之,多晶干法刻蚀是一项复杂的工艺步骤,涉及精确的尺寸控制、化学选择性和物理特性考虑等多个方面。
多晶硅纳米线的湿法刻蚀及光学性质研究

开发研究多晶硅纳米线的湿法刻蚀及光学性质研究刘波(江西新能源科技职业学院,江西新余338012)摘要:介绍了采用湿法刻蚀的方法来制备多晶硅纳米线,通过扫描电镜、反射率测试和XRD晶形分析等手段来对制备样岛的形貌和光学性质进行表征。
通过实验研究HF浓度、AgNOs浓度、H2O2浓度、反应时间对硅纳米线表面形貌和漫反射率的影响,从而得到刻蚀的最佳条件,制备出低反射率而又均匀的多晶硅纳米线材料。
关键词:湿法刻蚀;多晶硅;硅纳米线;反射率1硅材料及其物理特性1.1硅纳米线概念所谓纳米线,是一种在横向上被限制在100nm以下,纵向上没有限制的一维材料。
硅纳米线是一种新型的一维半导体纳米材料,线体直径一般在10nm左右,内晶核实单晶硅,外层有一层Si。
?包覆层。
硅纳米线可以通过紫外光电子刻蚀、反应性离子刻蚀、金属有机物化学气相沉积等方法制备得到。
在场效应晶体管、单电子探测器、双向电子泵、双重门电路、纳米线阵列方面都有硅纳米线的应用。
1.2硅纳米线特性1.2.1载流子浓度与迁移率载流子浓度和迁移率是半导体材料最基本的电学特性。
掺杂硅纳米线的电阻率很低,所以通过掺杂可提高硅纳米线的载流子浓度。
高载流子浓度对半导体能带有重要影响,从而对半导体光吸收边附近的吸收特性有若干重要的影响,最终导致带隙随载流子浓度变化。
1.2.2场发射特性场发射是利用肖特基效应,将指向导体表面的强电场(即所谓的提拉电场)作用于导体的表面,使其表面势垒降低、变窄,当势垒的宽度窄到可以与电子波长相比拟时,电子的隧道效应开始起作用,部分高能电子就可顺利穿透表面势垒进入真空。
2实验讨论在这次试验中,我们通过改变HF浓度、AgNOs浓度、HQ?浓度、反应时间,来制备不同的硅纳米线样品。
每个实验只改变一个条件作为自变量,其他条件则完全相同,通过阶梯性改变自变量的值来得到不同的硅纳米线样品组。
使用紫外分光光度计测试样品组反射率,分析实验测试结果,得到自变量最佳条件。
多晶硅栅干法刻蚀残留及缺陷改善的研究

文章标题:多晶硅栅干法刻蚀残留及缺陷改善的研究在集成电路制造过程中,多晶硅栅干法刻蚀残留及缺陷一直是一个备受关注的研究领域。
本文将对此进行深入探讨,并提供一些有价值的观点和理解。
一、多晶硅栅干法刻蚀残留及缺陷简介多晶硅栅干法刻蚀残留及缺陷是指在集成电路制造过程中,由于多因素影响,导致硅栅在干法刻蚀后产生的残留物和缺陷现象。
这些残留物和缺陷可能会影响器件的电性能和可靠性,因此需要进行深入研究和改善。
二、多晶硅栅干法刻蚀残留及缺陷的影响因素1. 刻蚀气体选择:不同的刻蚀气体对多晶硅栅的刻蚀残留和缺陷产生影响,需要选择合适的刻蚀气体以减少残留和缺陷的产生。
2. 刻蚀参数:包括功率、压力、温度等参数的选择会对刻蚀残留和缺陷产生影响,需要进行合理的参数优化。
3. 表面处理:在刻蚀前后对硅栅表面进行特殊处理,可以减少刻蚀残留和缺陷的产生。
三、多晶硅栅干法刻蚀残留及缺陷改善方法1. 材料选择:选择合适材料,具有较好的刻蚀性能和表面光洁度,可以减少残留和缺陷的产生。
2. 工艺优化:对刻蚀工艺进行优化,包括参数选择、气体选择等,可以减少残留和缺陷的产生。
3. 表面处理:在刻蚀前后对硅栅表面进行特殊处理,如氧化、清洁等,可以改善残留和缺陷问题。
四、总结与展望通过对多晶硅栅干法刻蚀残留及缺陷的研究,我们可以更好地理解其产生的原因和影响因素,并采取相应的改善措施。
未来,可以进一步研究新的材料和工艺,以更好地解决多晶硅栅干法刻蚀残留及缺陷的问题,提高集成电路的制造质量和性能。
个人观点和理解:在多晶硅栅干法刻蚀残留及缺陷的研究中,我觉得重点应该放在工艺优化和材料选择上。
通过优化工艺参数和选择合适的刻蚀气体,可以有效减少残留和缺陷的产生,提高硅栅的质量和可靠性。
对硅栅材料的选择也非常重要,应该注重其刻蚀性能和表面质量,以减少残留和缺陷的产生。
通过本文的深入研究,我对多晶硅栅干法刻蚀残留及缺陷有了更深入的理解,也对改善措施有了更多的认识。
多晶硅刻蚀特性的研究
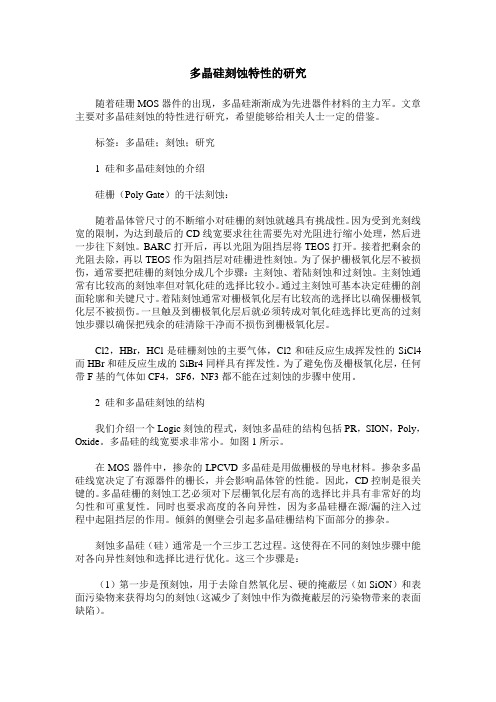
多晶硅刻蚀特性的研究随着硅珊MOS器件的出现,多晶硅渐渐成为先进器件材料的主力军。
文章主要对多晶硅刻蚀的特性进行研究,希望能够给相关人士一定的借鉴。
标签:多晶硅;刻蚀;研究1 硅和多晶硅刻蚀的介绍硅栅(Poly Gate)的干法刻蚀:随着晶体管尺寸的不断缩小对硅栅的刻蚀就越具有挑战性。
因为受到光刻线宽的限制,为达到最后的CD线宽要求往往需要先对光阻进行缩小处理,然后进一步往下刻蚀。
BARC打开后,再以光阻为阻挡层将TEOS打开。
接着把剩余的光阻去除,再以TEOS作为阻挡层对硅栅进性刻蚀。
为了保护栅极氧化层不被损伤,通常要把硅栅的刻蚀分成几个步骤:主刻蚀、着陆刻蚀和过刻蚀。
主刻蚀通常有比较高的刻蚀率但对氧化硅的选择比较小。
通过主刻蚀可基本决定硅栅的剖面轮廓和关键尺寸。
着陆刻蚀通常对栅极氧化层有比较高的选择比以确保栅极氧化层不被损伤。
一旦触及到栅极氧化层后就必须转成对氧化硅选择比更高的过刻蚀步骤以确保把残余的硅清除干净而不损伤到栅极氧化层。
Cl2,HBr,HCl是硅栅刻蚀的主要气体,Cl2和硅反应生成挥发性的SiCl4而HBr和硅反应生成的SiBr4同样具有挥发性。
为了避免伤及栅极氧化层,任何带F基的气体如CF4,SF6,NF3都不能在过刻蚀的步骤中使用。
2 硅和多晶硅刻蚀的结构我们介绍一个Logic刻蚀的程式,刻蚀多晶硅的结构包括PR,SION,Poly,Oxide。
多晶硅的线宽要求非常小。
如图1所示。
在MOS器件中,掺杂的LPCVD多晶硅是用做栅极的导电材料。
掺杂多晶硅线宽决定了有源器件的栅长,并会影响晶体管的性能。
因此,CD控制是很关键的。
多晶硅栅的刻蚀工艺必须对下层栅氧化层有高的选择比并具有非常好的均匀性和可重复性。
同时也要求高度的各向异性,因为多晶硅栅在源/漏的注入过程中起阻挡层的作用。
倾斜的侧壁会引起多晶硅栅结构下面部分的掺杂。
刻蚀多晶硅(硅)通常是一个三步工艺过程。
这使得在不同的刻蚀步骤中能对各向异性刻蚀和选择比进行优化。
多晶硅电池背表面刻蚀提升性能产线工艺研究

多晶硅电池背表面刻蚀提升性能产线工艺研究摘要:对比研究了产线上多晶硅太阳电池背表面刻蚀对其光电转换性能的影响。
示范性实验结果表明:多晶硅太阳电池背表面刻蚀能够改善其短路电流,从而相应的光电转换效率提升了约0.1%。
依据多晶硅太阳电池背表面刻蚀前后的扫描电镜(SEM)形貌、背表面漫反射光谱及完整电池片外量子效率的测试结果,改进的光电转换的原因可能源于背表面刻蚀“镜面”化有利于太阳光子在背表面内反射和改进印刷Al浆与背表面覆盖接触。
背表面刻蚀与当前晶硅电池产线工艺兼容,能够提升电池片的光电转换效率,是一种可供选择的产线升级工艺。
1引言如何提升产线晶硅太阳电池的光电转换效率是当前光伏产业中的一个重要研发课题。
基于晶硅太阳电池的整个光电过程,可针对增加电池片对300~1100nm太阳光子的捕获和吸收、降低电池片前后表面复合及减少电池片串并联电阻的电学损失3方面考虑,进行器件结构设计和制备工艺研发,有效地改进电池片光电转换效率。
其中,增加电池片对300~1100nm太阳光子的捕获和吸收,需要合理设计电池片前表面光电结构。
当前工业生产主流晶硅太阳电池产品前表面印有图形化栅线电极,它将遮挡太阳光子入射到电池片内部,造成反射损失。
降低栅线宽度及提高栅线高度的二次印刷技术[1]、减小主栅宽度的多主栅技术[2]均能够有效地降低遮挡面积,减少其光遮挡。
另外,未被遮挡的晶体硅在300~1100nm 光谱范围内折射率大,也将造成严重的光反射损失。
通过表面织构[3~5],可有效地降低晶硅表面光反射损失,特别是硅纳米结构[6~9]能够使获得超低光反射率。
进一步在微纳织构上及在其表面制作减反射膜[10,11],引入多次光反射和干涉效应,可进一步降低晶硅表面光反射损失。
另一方面,晶体硅的吸收系数[12,13]在300~1100nm 光谱范围有很大变化,短波太阳光子(300~450nm)和长波太阳光子(850~1100nm)的吸收系数相差数2~3量级,导致各种波长太阳光具有不同的吸收深度。
多晶硅刻蚀工艺的研究

多晶硅刻蚀工艺的研究
多晶硅刻蚀工艺是一种用于制备微电子器件的工艺。
多晶硅是一种多晶性的硅材料,具有良好的导电性和机械性能,被广泛应用于电子器件中。
多晶硅刻蚀工艺主要包括湿刻蚀和干刻蚀两种方法。
湿刻蚀是利用湿化学溶液对多晶硅进行腐蚀,常用的溶液有氢氟酸、酸性过氧化氢等。
干刻蚀则是利用气体放电或离子轰击等方式将多晶硅表面物质转化为气体或离子,从而实现刻蚀作用,常用的气体有氧气、氟化氢等。
多晶硅刻蚀工艺的研究主要涉及以下几个方面:
1. 刻蚀过程的理论研究:研究多晶硅刻蚀过程的机理,包括湿刻蚀和干刻蚀过程中的化学反应和物理机制。
2. 工艺参数的优化:通过对刻蚀工艺参数的改变,如溶液浓度、温度、刻蚀时间、气体流量等的优化,可以得到更好的刻蚀效果。
3. 刻蚀剂的开发:研究和设计新型的刻蚀剂,提高刻蚀效率和选择性,减少副作用。
4. 刻蚀模型的建立和仿真:通过建立刻蚀模型,进行仿真分析,可以预测刻蚀过程中的表面形貌和质量,并指导实际工艺。
5. 刻蚀工艺的应用研究:将多晶硅刻蚀工艺应用于实际的微电子器件制备中,如太阳能电池、集成电路等,研究工艺对器件性能的影响。
综上所述,多晶硅刻蚀工艺研究涉及多个方面,包括理论研究、工艺参数优化、刻蚀剂开发、刻蚀模型建立和仿真分析以及应用研究等,这些研究对于提高多晶硅器件的制备工艺和性能具有重要意义。
多晶硅纳米刻蚀加工

多晶硅纳米刻蚀加工
硅纳米刻蚀加工技术指的是利用激光技术在硅表面进行刻蚀和定形处理,以形成多种变形面、抗弯和强度等需求的功能设备。
应用硅纳米刻蚀加工技术,能够在硅基板更好地实现细致的纳米级,基于多晶硅基板材料来形成硅纳米加工制品。
一、多晶硅纳米刻蚀加工的技术原理
1.基于光学技术对多晶硅表面进行刻蚀处理:多晶硅纳米刻蚀加工技术利用激光来作用于多晶硅表面,使多晶硅表面焦点处的材料进行熔融,然后进行刻蚀处理,以形成有一定的抗弯、强度和变形等功能的多晶硅制品。
2.高精度的尺寸控制:高强度激光可以精确的控制刻蚀制品的尺寸,并可以根据不同的多晶硅材料进行优化,提供出高精度的尺寸控制。
3.非接触式工艺:硅纳米刻蚀加工方法采用非接触式工艺,硅切削的处理范围可以大大地拓宽,并可以在有一定高度要求的地方实现更高的加工精度。
二、多晶硅纳米刻蚀加工的应用
1.微电子技术领域:多晶硅纳米刻蚀加工技术可以用于制作多晶硅集成电路。
它可以提供较小的结构开口,增强端面聚集效果,控制特殊多晶硅元器件的功率损耗,以及解决电路设计中的一致性、隔离能力、尺寸偏差和结构复杂程度等问题。
2.光电子技术领域:多晶硅纳米刻蚀加工技术可以用于制作多晶硅光电子元器件,如多晶硅光栅波导、光源器件、传感器元件、光分路器、光缆和光纤传输件等,便于更好地组合光源、检测器和传输件来实现光电子器件功能的要求。
3.微机电技术领域:多晶硅纳米刻蚀加工技术可以用于制作结构和定形处理多晶硅加工的机电零件,其产品的尺寸、形状等非常精确,能够更好地满足高要求的机械表面结构形状,以及高要求的力学性能。
- 1、下载文档前请自行甄别文档内容的完整性,平台不提供额外的编辑、内容补充、找答案等附加服务。
- 2、"仅部分预览"的文档,不可在线预览部分如存在完整性等问题,可反馈申请退款(可完整预览的文档不适用该条件!)。
- 3、如文档侵犯您的权益,请联系客服反馈,我们会尽快为您处理(人工客服工作时间:9:00-18:30)。
收稿日期:2010-11-03.材料、结构及工艺CCD 多晶硅刻蚀技术研究向鹏飞,袁安波,杨修伟,高建威(重庆光电技术研究所,重庆400060)摘 要: CCD 晶硅刻蚀相比于传统CM OS 工艺的多晶硅刻蚀需要多晶硅对氮化硅更高的刻蚀选择比,更长的过刻蚀时间。
采用Cl 2+H e,Cl 2+H e+O 2,Cl 2+H e+O 2+H Br 三种工艺气体组分在Lam4420机台进行了多晶硅刻蚀实验,研究了不同气体配比、不同射频功率对刻蚀速率、选择比、条宽、侧壁形貌等参数的影响。
通过优化工艺参数,比较刻蚀结果,最终获得了适合于CCD 多层多晶硅刻蚀的工艺条件。
关键词: 多晶硅;刻蚀;选择比;CCD中图分类号:TN386.5 文献标识码:A 文章编号:1001-5868(2010)06-0885-03Study on Technology of Poly Etch in C CDXIANG Pengfei,YUAN Anbo,YANG Xiuw ei,GAO Jianw ei(C hongqing Optoelectronics Research Institute,C hongqing 400060,CHN)Abstract: Relative to nor mal CM OS po ly etch process,the techno logy of poly etch in CCD need higher selectiv ity betw een poly and SiN,and mo re over etch tim e.Po ly etch on Lam 4420machine w as perform ed w ith Cl 2+H e,Cl 2+H e+O 2and Cl 2+H e+O 2+H Br as etching gases.The relationship betw een different etching gases,RF pow er and the four par am eters of etch rate,selectivity ,profile and CD bias w as researched.By o ptimizing the ratio of different gases and com paring the different etching results,the optimized etching process for CCD w as obtained.Key words: poly;etch;selectiv ity;CCD0 引言CCD 和标准的CM OS 器件一样,都是用多晶硅作为器件的栅极,多晶硅栅的刻蚀是整个CCD 制作中的关键工艺,器件成品率和器件性能都与多晶硅栅的刻蚀工艺有直接的关系。
目前多晶硅刻蚀在CM OS 工艺中是很成熟的工艺技术,但CCD 的多晶硅栅刻蚀与CMOS 器件的多晶硅刻蚀相比有较大的不同。
因为CCD 多晶硅栅极下的介质层是氮化硅,而且需要3~4次多晶硅栅刻蚀布线以形成交叠,相比于CM OS 工艺中的多晶硅刻蚀需要更高的刻蚀选择比,更长的过刻蚀时间,才能满足CCD 多晶硅栅极刻蚀的要求。
本文针对CCD 多晶硅刻蚀在刻蚀选择比、刻蚀形貌、条宽控制等几个方面进行了研究,找到了满足CCD 多层多晶硅栅布线的多晶硅刻蚀条件。
1 多晶硅刻蚀原理反应离子刻蚀多晶硅的反应气体是Cl 2,H Br等气体,反应离子刻蚀主要有化学刻蚀和物理刻蚀两方面的作用。
(1)化学刻蚀(反应刻蚀)。
反应气体(Cl 2,H Br)在高频电场中被电离,产生离子、电子、激发原子、游离原子(亦称游离基)等,具有很强的化学活性,可以与处于等离子体中的物质发生如下化学反应[1]:Si+4Cl SiCl 4 ,Si+4Br SiBr 4 。
(2)物理刻蚀(溅射刻蚀)。
由于反应离子在电场中获得能量,并且定向移动到硅片表面,形成对硅片物理轰击作用,使原子或分子得到足够的动能离885 半导体光电 2010年12月第31卷第6期向鹏飞等: CCD 多晶硅刻蚀技术研究开表面,与反应气体反应,提高了反应速度。
多晶硅刻蚀后的主要反应生成物为气态,直接被真空系统抽走,在刻蚀过程中Cl,Br 与多晶硅及光刻胶反应,产生聚合物,并沉积于多晶硅条侧壁上,保护侧壁不受反应气体的刻蚀,有效地保证了刻蚀后的多晶硅线条宽度[2]。
2 实验结果与分析本实验所用刻蚀机为美国Lam 公司Lam4420机台。
本实验采用Cl 2+H e,Cl 2+H e+O 2,Cl 2+H e+O 2+H Br 三种工艺气体组分刻蚀多晶硅,并改变气体流量比、RF 功率等参数,在多晶硅刻蚀速率、对氮化硅的刻蚀选择比、多晶硅条侧壁形貌和刻蚀前后线宽损失等四个方面进行工艺优化。
2.1 刻蚀速率及选择比与射频功率的关系实验采用Cl 2+H e 作为刻蚀气体,实验中保持Cl 2和H e 的流量不变,分别为80和160cm 3。
改变RF 功率,得出多晶硅刻蚀速率、氮化硅刻蚀速率和多晶硅对氮化硅的选择比与RF 功率之间的关系曲线,如图1所示。
图1 多晶硅刻蚀速率、氮化硅刻蚀速率及多晶硅对氮化硅的选择比与RF 功率之间的关系从上图可以看出,随着RF 功率的增加,多晶硅和氮化硅刻蚀速率都相应增大,但多晶硅对氮化硅的刻蚀选择比却逐渐减小。
本实验系统的刻蚀方式为常用的反应离子刻蚀:它是利用射频放电使化学反应性气体(Cl 2)产生具有化学活性的基团和离子,由于电子和离子的质量不同使得质量较轻的电子能够响应射频电场的变化而离子却不能,正是这种差异在电极上产生负偏压,经过负偏压电场加速的高能离子轰击被刻蚀材料,其作用有二:一是将待蚀刻物质表面的原子键结破坏,以加速蚀刻速率;二是将再沉积于待蚀刻物质表面的产物或聚合物(Poly mer)打掉,以便待蚀刻物质表面能再与反应蚀刻气体接触,这也进一步加速了活性刻蚀反应基团与被刻蚀材料的反应速率[3]。
RF 功率增加,射频放电形成的等离子体密度增大,参与反应的离子数增加,使得多晶硅和氮化硅的刻蚀速率都变快。
RF 功率增加同时也导致电极上的负偏压增大,使得具有方向性的离子轰击作用增强,而离子轰击的物理作用明显,对刻蚀材料并不具有选择性,导致多晶硅对氮化硅的刻蚀速率选择比降低。
2.2 刻蚀速率及选择比与气体组分的关系实验中保持RF 功率(125W)不变,Cl 2和H e 气的流量不变,分别为80和160cm 3。
加入不同流量的O 2和H Br 气体形成不同的气体组分,得出多晶硅刻蚀速率、氮化硅刻蚀速率以及多晶硅对氮化硅的选择比与不同气体配比之间的关系曲线。
图2 多晶硅刻蚀速率和氮化硅刻蚀速率及刻蚀选择比与O 2,HBr 流量之间的关系从上图可以看出,随着O 2流量增加,多晶硅刻蚀速率明显增大,多晶硅对氮化硅的刻蚀选择比也逐渐增大;而加入H Br 气体后,多晶硅刻蚀速率明显下降,H Br 气体流量增大后,多晶硅刻蚀速率再次上升,对氮化硅的选择比最高达到232 1。
多晶硅与Cl 2反应主要生成物是SiCl x ,加入少量O 2后,它易与SiCl x 结合形成SiO x Cl y [4-6],使得Cl 离子浓度比无O 2时高,从而导致刻蚀速率增加;加入O 2后,在射频放电的等离子体氛围中O 2和氮化硅反应在氮化硅表面形成SiO x N y 的化合物,阻挡氮化硅的继续刻蚀,使得多晶硅对氮化硅的刻蚀选择比增大。
反应气体中加入H Br 后,与多晶硅反应会形成固态的SiBr x 生成物[7],不易被真空系统抽走,沉积在硅片表面,阻挡刻蚀导致多晶硅刻蚀速率下886 SEMIC ONDUC TOR OPTOELECTRONIC S Vol.31No.6Dec.2010降,而当H Br 气体流量增加后,被离化的Br 增多,它与多晶硅的反应再次提高了多晶硅刻蚀速率。
2.3 线宽控制及侧壁角度与气体组分的关系实验中保持RF 功率(150W)不变,刻蚀时间不变,Cl 2、H e 和O 2的流量不变,分别为80、160和6cm 3;改变H Br 流量,得出刻蚀前后多晶硅条线宽损失及刻蚀后多晶硅线条侧壁角度与不同H Br 气体流量之间的关系列表,如表1。
上面4种H Br 气体流量的实验条件刻蚀多晶硅并去胶后用扫描电镜分析了多晶硅线条的侧壁形貌,如图3。
表1HBr 气体流量与多晶硅线宽损失及侧壁角度对应关系HBr 流量/cm 30102030刻蚀前后多晶硅条线宽损失/ m 1.120.680.260刻蚀后多晶硅线条侧壁角度/( )12911310394图3 不同HBr 流量刻蚀后的多晶硅条剖面形貌从上面表格统计数据和SEM 图片可以看出:不加H Br 时,多晶硅线条刻蚀后条宽损失超过1 m(刻蚀前条宽为4 m ),线条侧壁呈明显的斜坡,侧壁角度接近130 ;随着H Br 气体流量的增大,刻蚀后的多晶硅线宽损失逐渐减小,当H Br 流量为30cm 3时,多晶硅刻蚀前后条宽一致,刻蚀后的多晶硅线条侧壁基本成垂直的90 。
Cl 与多晶硅的反应各项同性较强,多晶硅线条的侧向刻蚀较为严重[8];氧气虽然能提高多晶硅对氮化硅的刻蚀选择比,但同时也能和生成的聚合物发生反应,从而使得聚合物对多晶硅侧壁的保护作用减弱,所以多晶硅在Cl 和O 2的气体组分刻蚀后线宽会变窄。
加入H Br 后,与多晶硅反应生产固态的SiBr x ,其挥发性较弱,特别是在氧元素存在的气氛中可形成Si x O y Br z 的聚合体,这种聚合物挥发性很差,容易沉积在多晶硅线条侧壁,形成钝化保护层[9],有效的保证了多晶硅线条条宽在刻蚀前后基本一致。
3 结论本文采用Cl 2+H e,Cl 2+H e+O 2,Cl 2+H e+O 2+H Br 三种工艺气体组分在Lam 4420机台上进行了多晶硅刻蚀实验,研究了不同气体配比、不同射频功率对多晶硅刻蚀速率、多晶硅对氮化硅刻蚀选择比、多晶硅条宽控制及侧壁形貌等参数的影响。
通过优化工艺参数,比较刻蚀结果,最终获得了多晶硅对氮化硅刻蚀选择比232 1、多晶硅刻蚀前后线宽一致、刻蚀后多晶硅线条侧壁角度基本成垂直90 的优化工艺条件,满足CCD 多层多晶硅刻蚀的工艺需求。
参考文献:[1] 赵化桥.等离子体化学[M ].合肥:中国科学技术大学出版社,1994.[2] 半导体制造技术[M ].韩郑生,译.北京:电子工业出版社,2004.[3] 等离子体电子工程学[M ].张海波,张丹,译.北京:科学出版社,2002.[4] U llal S J,Go dfr ey A R,Edelberg E,et a l.Effect o fchamber wall conditions o n Cl and Cl 2concent ratio ns in an induct icely coupled plasma reactor [J ].J .Vac.T echnol.,2002,A 20(I):43-52.[5] Oehrlein G S,M at suo P J,Doemling M F,et al.Studyof plasma -surface inter actions:chem ical dry Et ching and high -densit y plasma etching [J ].Plasma Sources Sci.T echno l.,1996,5:193-199.[6] U llal S J,Singh H.Deposit ion o f silicon o x ychlor idefilms o n chamber w alls dur ing Cl 2/O 2plasma et ching of Si[J].J.Vac.Sci.T echnol.,2002,A 20(2):499-506.[7] Cunge G,Ko gelschatz M ,Joubertl O ,et al.P lasma -wall interactions dur ing silicon etching processes in high -density HBr/Cl 2/O 2plasmas [J].P lasma Sources Sci.T echno l.,2005,14:42-52.[8] Jin W eido ng ,H er ber t H S.Feature prof ile evo lution inhigh -density plasma etching of silico n w ith Cl 2[J].J.Vac.Sci.T echno l.,2003,A 21(4):911-921.[9] Vitale S A ,Chac H ,H erbert H S.Silicon et chingyields in F ,Cl,Br ,and H Br H ig h density plasmas[J].J.Vac.Sci.T echnol.,2001,A 19(5):2197-2206.作者简介:向鹏飞(1981-),男,重庆人,硕士,工程师,主要从事CCD 工艺与器件研究工作。