线切割实习报告(一)
线切割加工实习报告
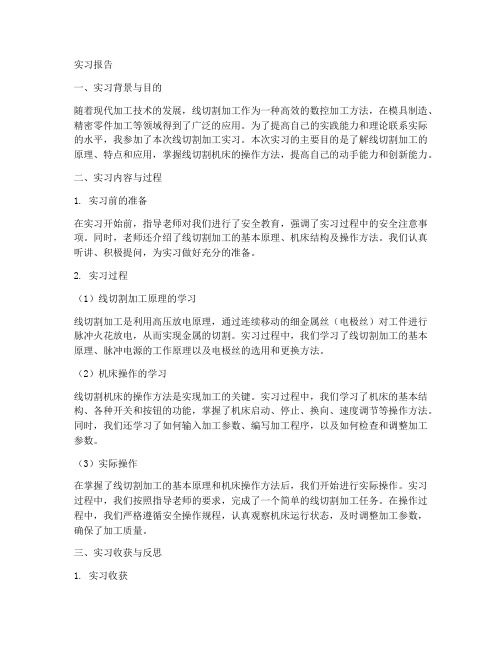
实习报告一、实习背景与目的随着现代加工技术的发展,线切割加工作为一种高效的数控加工方法,在模具制造、精密零件加工等领域得到了广泛的应用。
为了提高自己的实践能力和理论联系实际的水平,我参加了本次线切割加工实习。
本次实习的主要目的是了解线切割加工的原理、特点和应用,掌握线切割机床的操作方法,提高自己的动手能力和创新能力。
二、实习内容与过程1. 实习前的准备在实习开始前,指导老师对我们进行了安全教育,强调了实习过程中的安全注意事项。
同时,老师还介绍了线切割加工的基本原理、机床结构及操作方法。
我们认真听讲、积极提问,为实习做好充分的准备。
2. 实习过程(1)线切割加工原理的学习线切割加工是利用高压放电原理,通过连续移动的细金属丝(电极丝)对工件进行脉冲火花放电,从而实现金属的切割。
实习过程中,我们学习了线切割加工的基本原理、脉冲电源的工作原理以及电极丝的选用和更换方法。
(2)机床操作的学习线切割机床的操作方法是实现加工的关键。
实习过程中,我们学习了机床的基本结构、各种开关和按钮的功能,掌握了机床启动、停止、换向、速度调节等操作方法。
同时,我们还学习了如何输入加工参数、编写加工程序,以及如何检查和调整加工参数。
(3)实际操作在掌握了线切割加工的基本原理和机床操作方法后,我们开始进行实际操作。
实习过程中,我们按照指导老师的要求,完成了一个简单的线切割加工任务。
在操作过程中,我们严格遵循安全操作规程,认真观察机床运行状态,及时调整加工参数,确保了加工质量。
三、实习收获与反思1. 实习收获通过本次线切割加工实习,我深入了解了线切割加工的原理和特点,掌握了线切割机床的操作方法,增强了自己的动手能力和创新能力。
同时,我还学会了如何编写加工程序,为以后从事相关领域的工作打下了基础。
2. 实习反思虽然我在实习过程中取得了一定的成绩,但同时也发现了自己在操作技能和理论知识方面的不足。
今后,我将继续努力学习,提高自己的综合素质,为将来的工作做好准备。
线切割的实习报告

一、实习背景线切割技术是一种利用电火花放电原理进行金属加工的先进技术。
随着我国制造业的快速发展,线切割技术在模具制造、精密加工等领域得到了广泛应用。
为了提高自身实践能力,我于2021年X月参加了XX工厂的线切割实习。
二、实习目的1. 了解线切割技术的基本原理、工作流程及操作方法。
2. 掌握线切割机床的结构、性能及维护保养方法。
3. 通过实际操作,提高线切割加工的技能水平。
4. 培养团队协作精神和动手能力。
三、实习内容1. 线切割技术基本原理线切割技术是利用连续移动的细金属丝(电极丝)作电极,对工件进行脉冲火花放电蚀除金属、切割成型。
电极丝与工件之间产生火花放电,使工件表面形成一层氧化膜,氧化膜在电场作用下被击穿,产生等离子体,使工件表面金属熔化、气化,从而实现切割。
2. 线切割机床结构及性能线切割机床主要由工作台、走丝机构、供液系统、脉冲电源和控制系统等五大部分组成。
(1)工作台:用于安装工件,实现工件的移动。
(2)走丝机构:驱动电极丝作连续移动,实现切割。
(3)供液系统:为电极丝提供冷却和清洗作用。
(4)脉冲电源:产生脉冲电流,为电极丝与工件之间的火花放电提供能量。
(5)控制系统:根据预先输入的程序,控制工作台和走丝机构的运动,实现精确切割。
3. 线切割操作方法(1)工件装夹:将工件放置在工作台上,调整好位置,固定好夹具。
(2)编程:根据工件图纸,编写切割程序,包括切割路径、切割速度、切割参数等。
(3)调试:调整机床参数,如切割速度、切割压力、脉冲宽度等,确保切割质量。
(4)加工:启动机床,按照切割程序进行切割。
(5)后处理:切割完成后,清理工件表面,去除氧化膜和残留物。
4. 线切割机床维护保养(1)定期检查机床各部件,确保其正常运行。
(2)定期清理机床内部,清除残留物和污垢。
(3)定期检查冷却系统,确保冷却效果良好。
(4)定期检查电极丝,确保其直径和张力符合要求。
四、实习收获1. 理论与实践相结合,加深了对线切割技术的理解。
电火花线切割实习报告
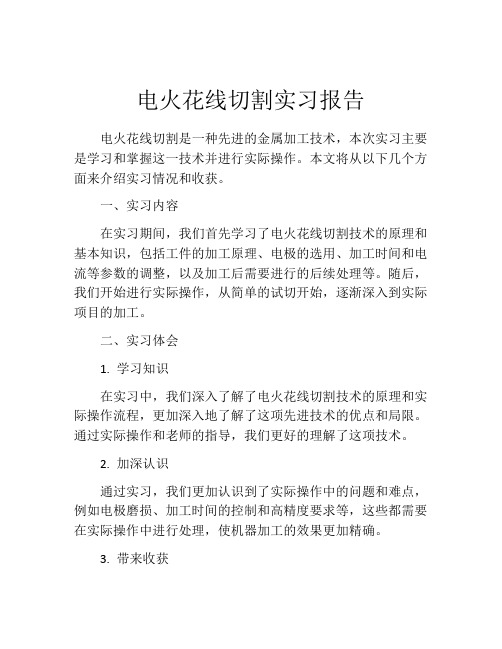
电火花线切割实习报告电火花线切割是一种先进的金属加工技术,本次实习主要是学习和掌握这一技术并进行实际操作。
本文将从以下几个方面来介绍实习情况和收获。
一、实习内容在实习期间,我们首先学习了电火花线切割技术的原理和基本知识,包括工件的加工原理、电极的选用、加工时间和电流等参数的调整,以及加工后需要进行的后续处理等。
随后,我们开始进行实际操作,从简单的试切开始,逐渐深入到实际项目的加工。
二、实习体会1. 学习知识在实习中,我们深入了解了电火花线切割技术的原理和实际操作流程,更加深入地了解了这项先进技术的优点和局限。
通过实际操作和老师的指导,我们更好的理解了这项技术。
2. 加深认识通过实习,我们更加认识到了实际操作中的问题和难点,例如电极磨损、加工时间的控制和高精度要求等,这些都需要在实际操作中进行处理,使机器加工的效果更加精确。
3. 带来收获通过与老师的交流和经验的积累,我们成功地完成了一些较难的项目,例如光管模具的积累和数控加工的坑槽打磨等,这都为我们日后的工作提供了宝贵的经验和技能。
三、实习意义1. 开拓视野在实习中,我们学习和掌握了一项先进的金属加工技术,远远超出了传统的机械加工和人工钳工的范畴。
通过学习和掌握这种技术,我们开拓了自己的视野,将更好的与同行竞争和合作。
2. 提高技能在实习中,我们掌握了一些较为复杂的电火花线切割技术,例如光管模具的加工和数控加工,更加熟练的掌握这项技术可以更好的为日后的工作做准备。
3. 缩短学习和实践之间的差距在学校中,我们只能从书本上学习这些理论知识,而在实习中,我们不仅能够更深入地了解这些知识,还能将这些知识应用到实际操作中,从而缩短了学习和应用之间的差距。
综上所述,通过这次电火花线切割实习,我们不仅学习和掌握了这项新技术,还提高了自己的技能和实践能力。
这次实习为我们日后的工作和学习提供了宝贵的经验和实践基础。
数控线切割加工实习报告
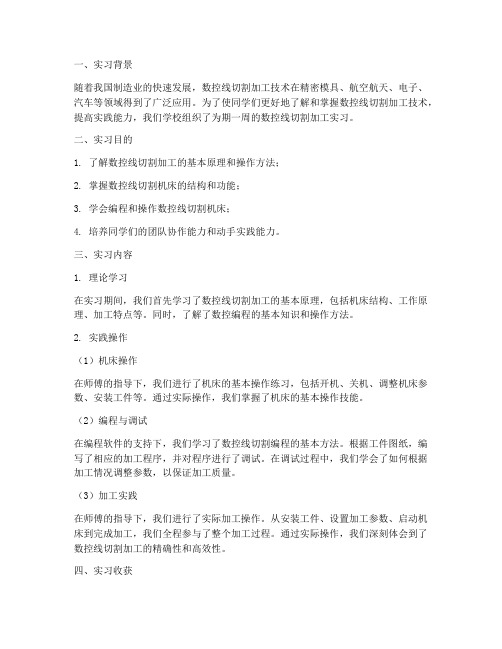
一、实习背景随着我国制造业的快速发展,数控线切割加工技术在精密模具、航空航天、电子、汽车等领域得到了广泛应用。
为了使同学们更好地了解和掌握数控线切割加工技术,提高实践能力,我们学校组织了为期一周的数控线切割加工实习。
二、实习目的1. 了解数控线切割加工的基本原理和操作方法;2. 掌握数控线切割机床的结构和功能;3. 学会编程和操作数控线切割机床;4. 培养同学们的团队协作能力和动手实践能力。
三、实习内容1. 理论学习在实习期间,我们首先学习了数控线切割加工的基本原理,包括机床结构、工作原理、加工特点等。
同时,了解了数控编程的基本知识和操作方法。
2. 实践操作(1)机床操作在师傅的指导下,我们进行了机床的基本操作练习,包括开机、关机、调整机床参数、安装工件等。
通过实际操作,我们掌握了机床的基本操作技能。
(2)编程与调试在编程软件的支持下,我们学习了数控线切割编程的基本方法。
根据工件图纸,编写了相应的加工程序,并对程序进行了调试。
在调试过程中,我们学会了如何根据加工情况调整参数,以保证加工质量。
(3)加工实践在师傅的指导下,我们进行了实际加工操作。
从安装工件、设置加工参数、启动机床到完成加工,我们全程参与了整个加工过程。
通过实际操作,我们深刻体会到了数控线切割加工的精确性和高效性。
四、实习收获1. 理论知识方面通过实习,我们对数控线切割加工技术有了更深入的了解,掌握了机床操作、编程、调试等基本技能。
2. 实践能力方面在实习过程中,我们学会了如何将理论知识运用到实际操作中,提高了自己的动手实践能力。
3. 团队协作方面在实习过程中,我们学会了与他人协作,共同完成加工任务,提高了团队协作能力。
4. 安全意识方面实习过程中,我们严格遵守操作规程,注意安全防护,提高了安全意识。
五、实习体会1. 数控线切割加工技术具有高精度、高效率、自动化程度高等特点,在制造业中具有广泛的应用前景。
2. 实践是检验真理的唯一标准。
金工实习电火花线切割实验报告

金工实习电火花线切割实验报告在现实生活中,我们使用金工实习报告的机会很多。
通过金工实习,我们看到了自己平生第一次在工厂中作出的成品,这让人感到很有成就感。
你是否在找正准备撰写“金工实习电火花线切割实验报告”,下面收集了相关的素材,供大家写文参考!金工实习电火花线切割实验报告1为期两周的金工实习结束了,带着一些不舍,我们离开了工业培训中心。
两周的时间太短,使我们无法接触到全部的工种,但这忙碌而充实的两周确实使我们每一个人都获益匪浅,锻炼了动手动脑能力,熟悉了一些基本的工业加工方法和流程,掌握了一些常用机器的操作方法。
这对于一个工科学生来说是一次难得的学习机会和经历,对以后走进工厂奠定了一定的实践基础,积累了宝贵经验。
实习期间每一天都有新鲜的内容,每一天都有新的挑战。
在实习基地,我第一次有了走入工厂的感觉,一台台陌生的机器井然安放,想到自己将是它们的操作者,不觉兴奋异常。
它们中的一些年龄比我还大,代表了八十年代的生产力,有些已在现实生产中被淘汰,但对重在了解其工作原理和操作的我们工科本科生来说还是很有教育指导意义的。
尽管如此,我发现要自如地操作它们也并不是想象中的那么轻而易举,这才发觉自己的差距还很大,要走的路还很长。
在实习前期,我接触了两种重要的机床-车床和铣床。
由于接触的是比较旧式的机器,人工操作还占了很大比重,也正因为如此,它们上面的按钮,手柄和转盘都比较多,我们花了不少时间用于熟悉机器,然后就迫不及待地进行实物加工。
车工是在车床上利用工件的旋转运动和刀具的移动来改变毛坯形状和尺寸,将其加工成所需零件的一种加工方法。
对于我们来说,并没有要求加工精细的零部件,主要是为了让我们熟悉对机器的操作,我们的任务就是在一个圆柱体毛坯两端分别加工出一个槽和一个球体。
在经历了几个失败的作品后终于加工出了一个较符合要求的作为作业上交,粗略地看还能大致辨认出是个球体的形状,但是我的目的已经达到了,能对车床的作用和操作方法了然于心。
金工实习报告线切割

金工实习报告线切割篇一:车间金工实习报告精选范文:车间金工实习报告金工实习是一门实践性的技术基础课,是高等院校工科学生学习机械制造的基本工艺方法和技术,完成工程基本训练的重要必修课。
它不仅可以让我们获得了机械制造的基础知识,了解了机械制造的一般操作,提高了自己的操作技能和动手能力,而且加强了理论联系实际的锻炼,提高了工程实践能力,培养了工程素质。
这是一次学习和锻炼的历程。
通过这次虽然时间不长,但却充实的实习,我受益匪浅。
在这里,我选摘几篇我比较印象深刻的金工实习日记作为报告。
第一天:线切割今天是金工实习的第一天,由于没有经验,我们也没有充分准备。
听完了老师的讲话,我们便到了车间,领到了自己的工号,各就各位去了。
我们今天做的是线切割,也就是电火花数控线切割加工。
这是一种特种加工方法,设备比较贵重,操作方法也较为复杂,万一操作不当,在进行切割加工用的电极丝会断掉,甚至发生人身和设备事故,所以今天老师在开始前给我们详细介绍机床的四大组成部分及其主要作用:.数控装置、机床部分、运丝机构、、丝架、、拖板(x、y方向)在计算机控制下,作协调的成型运动、床身(固定各机械、传动系统)组成;高频冲电源,作用有二个、工作液系统。
数控线切割加工技术是要利用编写好的程序、靠电极丝放电来切割各种小工件,我们要做的工作就是用软件设计工件,并把工件放置好,对好刀,其他事情就交给电脑完成了。
准确度高,不过速度比较慢。
按照安排,我们设计完图形,就可以到车床上操作了。
但是因为有极个别同学的工作进度太慢,导致最后时间不够,所以只由老师演示了一次给我们看。
没能拿到自己设计的作品,这也是今天实习的一个小小遗憾。
第二天:锻压今天的工作是锻压,通俗一点也叫打铁。
说到打铁,我脑子里就会浮现出古代铁匠在火炉边挥汗如雨,一手拿着钳子,一手用铁锤敲打的画面。
但是在我们的实习中,取而代之的是高大明亮的厂房,大功率的风扇,先进的电阻炉,还有可以提供一吨力的空气锤。
线切割电加工实习报告

一、实习背景随着现代工业的快速发展,特种加工技术在制造业中扮演着越来越重要的角色。
线切割电加工作为一种重要的特种加工方法,具有加工精度高、速度快、材料适应性强等优点。
为了深入了解线切割电加工技术,提高自己的实践操作能力,我参加了为期两周的线切割电加工实习。
二、实习单位及时间实习单位:XX机械加工厂实习时间:2021年X月X日至2021年X月X日三、实习内容1. 线切割电加工基本原理及设备介绍实习期间,我首先了解了线切割电加工的基本原理。
线切割电加工是利用连续移动的细金属丝(电极丝)作为电极,对工件进行脉冲火花放电蚀除金属,从而实现切割成型。
其主要设备包括线切割机床、脉冲电源、控制系统等。
2. 线切割机床操作及维护在实习过程中,我学习了线切割机床的基本操作方法,包括机床的启动、停止、工件安装、电极丝调整等。
同时,还了解了机床的日常维护保养知识,确保机床的正常运行。
3. 线切割加工工艺参数的设置为了提高线切割加工质量,实习中重点学习了加工工艺参数的设置。
包括脉冲宽度、脉冲间隔、走丝速度、加工电流等参数的调整,以及如何根据工件材料、形状和精度要求进行参数优化。
4. 线切割加工实践操作在掌握了一定的理论知识后,我开始进行线切割加工实践操作。
实习过程中,我先后加工了多种形状复杂的工件,如凸模、凹模、固定板等。
通过实践操作,我深刻体会到了线切割加工的技巧和要点。
5. 线切割加工质量控制及分析实习期间,我学习了线切割加工质量控制的方法和技巧。
通过对加工工件的外观、尺寸、形状等方面的检查,发现并分析了加工过程中可能存在的问题,为后续的改进提供了依据。
四、实习收获1. 理论知识与实践操作相结合,提高了自己的动手能力。
2. 了解了线切割电加工的基本原理、设备、工艺参数等知识,为今后从事相关工作打下了基础。
3. 学会了线切割机床的操作、维护及加工工艺参数的设置,提高了自己的技术水平。
4. 通过实习,培养了团队协作精神和沟通能力。
线切割实习报告
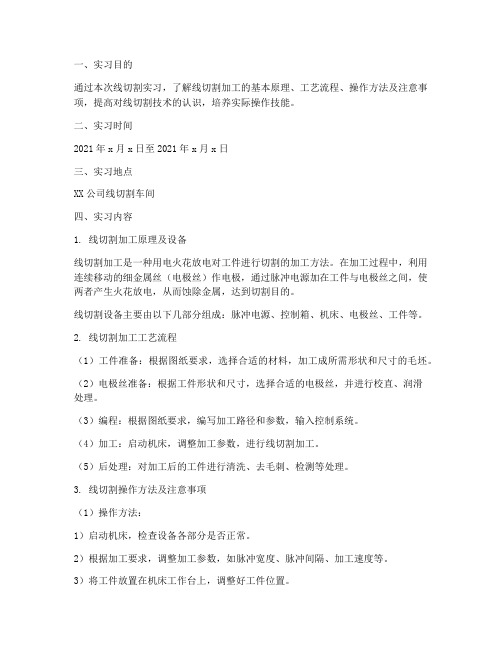
一、实习目的通过本次线切割实习,了解线切割加工的基本原理、工艺流程、操作方法及注意事项,提高对线切割技术的认识,培养实际操作技能。
二、实习时间2021年x月x日至2021年x月x日三、实习地点XX公司线切割车间四、实习内容1. 线切割加工原理及设备线切割加工是一种用电火花放电对工件进行切割的加工方法。
在加工过程中,利用连续移动的细金属丝(电极丝)作电极,通过脉冲电源加在工件与电极丝之间,使两者产生火花放电,从而蚀除金属,达到切割目的。
线切割设备主要由以下几部分组成:脉冲电源、控制箱、机床、电极丝、工件等。
2. 线切割加工工艺流程(1)工件准备:根据图纸要求,选择合适的材料,加工成所需形状和尺寸的毛坯。
(2)电极丝准备:根据工件形状和尺寸,选择合适的电极丝,并进行校直、润滑处理。
(3)编程:根据图纸要求,编写加工路径和参数,输入控制系统。
(4)加工:启动机床,调整加工参数,进行线切割加工。
(5)后处理:对加工后的工件进行清洗、去毛刺、检测等处理。
3. 线切割操作方法及注意事项(1)操作方法:1)启动机床,检查设备各部分是否正常。
2)根据加工要求,调整加工参数,如脉冲宽度、脉冲间隔、加工速度等。
3)将工件放置在机床工作台上,调整好工件位置。
4)输入编程,启动机床,进行线切割加工。
5)加工完成后,关闭机床,取出工件。
(2)注意事项:1)操作前,应熟悉机床性能、操作规程和安全注意事项。
2)加工过程中,注意观察机床运行状态,发现异常情况及时处理。
3)加工过程中,严禁触摸电极丝和工件,以免发生触电事故。
4)加工结束后,及时清理机床,保持工作环境整洁。
五、实习总结通过本次线切割实习,我对线切割加工有了更深入的了解,掌握了线切割操作的基本方法和技巧。
在实习过程中,我学会了如何根据图纸要求进行编程、调整加工参数,并能够熟练操作机床进行线切割加工。
同时,我认识到安全操作的重要性,确保了实习过程中的安全。
总之,本次线切割实习使我受益匪浅,为今后的学习和工作打下了良好的基础。
- 1、下载文档前请自行甄别文档内容的完整性,平台不提供额外的编辑、内容补充、找答案等附加服务。
- 2、"仅部分预览"的文档,不可在线预览部分如存在完整性等问题,可反馈申请退款(可完整预览的文档不适用该条件!)。
- 3、如文档侵犯您的权益,请联系客服反馈,我们会尽快为您处理(人工客服工作时间:9:00-18:30)。
8月29日星期一
今天是实习第一天,早上李老师给我们大概讲了一下需要注意的安全事项和实习的重要意义。
争取更好的把理论运用于实践。
以前一直学的理论没有好好的实践,所以我们都非常珍惜这次实习的机会。
我被安排到中直机械加工公司。
先熟悉了一下工作环境和加工零件,以及掌握了我们所要加工的零件的基本结构。
这一周我要实践的是线切割,学会线切割的使用、画图(用YH画图软件和CAXA画图软件两种),公司共有四台线切割机器,两台电脑控制,所用软件不同。
下午我将公司将要生产的这一批汽车配件的图纸打印了,认真看了一下。
分析了一下,与我们所学的CAD不同的是,工厂在实际生产中为了方便,会把二维三维放在一张图纸上,而我们为了严格都是分开画的。
还有就是明细栏也比我们的明细更加简洁,我想这都是为了方便工人师傅吧。
8月30日星期二
首先理解电火花加工的加工原理及工艺技术:
(一)数控电火花线切割机床加工原理:
电火花线切割是通过线状工具电极,对工件进行脉冲性放电加工的。
工作时脉冲电源的正极接工件,负极接电极丝。
(二)数控电火花线切割机床加工特点:
1、数控线切割加工是轮廓切割加工,勿需设计和制造成形工具电极,大大降低了加工费用,缩短了生产周期。
2、直接利用电能进行脉冲放电加工,工具电极和工件不直接接触,无机械加工中的宏观切削力,适宜于加工低刚度零件及细小零件。
3、无论工件硬度如何,只要是导电或半导电的材料都能进行加工。
4、切缝可窄达仅 0.12mm ,只对工件材料沿轮廓进行“套料”加工,材料利用率高,能有效节约贵重材料。
5、移动的长电极丝连续不断地通过切割区,单位长度电极丝的损耗量较小,加工精度高。
6、一般采用水基工作液,可避免发生火灾,安全可靠,可实现昼夜无人值守连续加工。
7、通常用于加工零件上的直壁曲面,通过 X-Y-U-V 四轴联动控制,也可进行锥度切割和加工上下截面异形体、形状扭曲的曲面体和球形体等零件。
8、不能加工盲孔及纵向阶梯表面。
实际操作中一定要注意,在缠丝的时候一定要上下导轮都在导槽中,否则,容易断丝,造成不必要的麻烦。
8月31日星期三
(一)工件的装夹
装夹工件时,必须保证工件的切割部位位于机床工作台纵向、横向进给的允许范围之内,以免超出极限。
同时应考虑切割时电极丝运动空间。
夹具应尽可能选择通用(或标准)件,所选夹具应便于装夹,便于协调工件和机床的尺寸关系。
在加工大型模具时,要特别注意工件的定位方式,尤其在加工快结束时,工件的变形、重力的作用会使电极丝被夹紧,影响加工。
中直公司的四台线切割机都采用两端支撑方式装夹,两端支撑方式装夹工件,这种方式装夹方便、稳定,定位精度高,但不适于装夹较大的零件。
采用以上方式装夹工件,还必须配合找正法进行调整,方能使工件的定位基准面分别与机床的工作台面和工作台的进给方向x、y保持平行,以保证所切割的表面与基准面之间的相对位置精度。
(二)画图编程的主要步骤:
编程——切割编程——选起点——补偿——方向——认可——书包——回车——退车
编程——代码输出——代码显示
编程——代码输出——控制台——OK
(三)程序执行时的步骤:
上档——暂停——角度执行作废(按3下)
待命——上档——1——B
起调——1——输入——2——执行
画图完成后电脑自动编程,传入线切割机床即可。
一般零件要求都是20mm厚的钢板,实际加工操作中把两块焊接在一起直接加工。
总之,厚度一样的板放在一起加工。
进行电火花加工时,工具电极和工件分别接脉冲电源的两极,并浸入工作液中,或将工作液充入放电间隙。
通过间隙自动控制系统控制工具电极向工件进给,当两电极间的间隙达到一定距离时,两电极上施加的脉冲电压将工作液击穿,产生火花放电。
在放电的微细通道中瞬时集中大量的热能,温度可高达一万摄氏度以上,压力也有急剧变化,从而使这一点工作表面局部微量的金属材料立刻熔化、气化,并爆炸式地飞溅到工作液中,迅速冷凝,形成固体的金属微粒,被工作液带走。
这时在工件表面上便留下一个微小的凹坑痕迹,放电短暂停歇,两电极间工作液恢复绝缘状态。
紧接着,下一个脉冲电压又在两电极相对接近的另一点处击穿,产生火花放电,重复上述过程。
这样,虽然每个脉冲放电蚀除的金属量极少,但因每秒有成千上万次脉冲放电作用,就能蚀除较多的金属,具有一定的生产率。
线切割过程中出现许多问题,下面就分别举例说明一下及解决办法。
例如线切割如果打火不正常甚至不打火,就应及时检查线触头的接触情况。
否则很容易断丝。
如果开始接触钢板,速度一定不能过快。
如果重新定位,重新加工,一定要先将表面清理干净。
如果断丝后有打折的地方,一定要剪掉。
今天又抽空跟李师傅学习了一下打标识,,以前总以为工件是加工完成以后才打标识。
可是,在实践中发现根本不是这样的,因为打标识不仅是为了让使用者看到,更是为了在加工过程中方便工人师傅加工,所以一般刚线切割完就要打标识。
线切割在使用过程中很容易断丝,造成成本增加和浪费劳动力。
何降低成本呢?首先,我们可以考虑在几个方面。
第一,线切割的钼丝可以在切割时勤换切割液;第二,由于线切割时经常会出现断丝或者停机,可以一次少加工点零件,多定位几次。
因为如果加工到一半时停机,必须重新定位,浪费时间。
第三,线切割的钼丝一次可以在储丝筒上少缠一点,以免万一在中间断丝,浪费钼丝。
看似简单的线切割,实际上也很复杂。
只有亲身实践才知其奥妙,才会做出理想的产品,实践是学习的真理!如果再有机会我还会参加这样的实习,还会去用实践来完善自己的知识面和自己的各项能力,以求在走出校园的时候有适应社会的更高的能力。
感谢学校和老师给我们这个磨练自己和完善自己的机会!。