ASME工艺流转卡
压力容器工艺过程流转卡

件号
第
3
页
1
共 13
页
控制 标记
序 号
工序
工艺内容及技术要求
R
1
核查
看 清
有裂纹、凹凸、分层、表面无锈蚀。检验员签字确认后划线下料
2
划线
毛 坯 标
W
3 4 5
检验 定位
记 检 验 对
焊 焊接
拼 对 拼 笔
标
φ
划
2
线
1±1㎜ 错边量
W
6 7
检验
检 验 委
托
H
8
检验
1 )
内表面形状偏差:外凸≤1.25% Di 即≤ 25.00 mm
坡口表面不得有裂纹、分层、夹渣等缺陷,清理坡口两侧不小于20㎜范围内污物,打磨见金属光
泽。
6 滚圆 按要求对钢板进行卷筒制作,要求筒节内径Φ444mm。
7
定位 焊
对卷筒完毕后的件进行定位焊,焊道长度10~20mm,间隔50mm,要求错边量b≤3mm,对接间隙
1±1㎜;
W
8
焊接
对筒节的纵焊缝分别进行焊接,清除焊接熔渣及飞溅物,焊接参数见对应的焊接工艺卡,焊接完 成后,
进行标识移植。
W 4 检验 按图纸及工艺检查下料几何尺寸。
W 5 坡口 进行坡口加工,要求按图加工单边V型坡口,坡口角度35°±2°,钝边高度:1±1mm。 坡口表面不得有裂纹、分层、夹渣等缺陷,清理坡口两侧不小于20㎜范围内污物,打磨见金属光 泽。
6 卷制 按要求对钢板进行卷筒制作,要求卷制零件内径Φ2036mm。
文件编号:ZB2005
产品编号 R20-01
管口位置 共
工艺流转卡填写管理制度范文

工艺流转卡填写管理制度范文工艺流转卡填写管理制度第一章总则第一条为了规范和统一工艺流转卡的填写管理工作,提高工艺流转卡的使用效率和准确性,保证生产过程中的工艺资料的准确传递,制定本制度。
第二条工艺流转卡是企业生产过程中的一种重要工具,用来记录和传递工艺技术资料。
填写工艺流转卡是生产作业人员和管理人员的基本职责之一。
第三条工艺流转卡填写管理制度适用于所有生产部门的工艺流转卡的填写工作。
第二章工艺流转卡的分类和用途第四条工艺流转卡分为生产工艺流转卡和维修工艺流转卡两类。
第五条生产工艺流转卡用于传递产品的生产工艺资料,包括产品的加工工艺流程、工艺参数、工艺标准等。
第六条维修工艺流转卡用于传递设备的维修工艺资料,包括设备的维修流程、维修方法、维修步骤等。
第三章工艺流转卡的填写管理要求第七条工艺流转卡的填写由生产作业人员或维修人员负责,并经过相关部门的审核和批准。
第八条工艺流转卡必须按照规定的格式填写,确保填写的内容准确无误。
第九条工艺流转卡的填写内容包括但不限于以下几个方面:1. 产品或设备的基本信息,如名称、规格、型号等;2. 加工或维修工艺的流程,包括各个工段的操作内容、顺序和所需时间;3. 工艺参数,包括各个工段的温度、压力、速度等参数;4. 工艺标准,包括加工或维修的质量要求和检验标准;5. 特殊注意事项,包括注意安全、环保、节能等方面的要求。
第十条工艺流转卡的填写必须认真细致,确保信息全面、准确、可靠。
第四章工艺流转卡的流转管理第十一条工艺流转卡的流转必须按照规定的程序进行,严禁乱丢乱放。
第十二条工艺流转卡的流转必须经过相关部门的审核和批准。
第十三条工艺流转卡的流转必须按照规定的时间节点进行,确保传递及时。
第十四条工艺流转卡的流转必须做好记录,包括接收人、发放人、流转时间等。
第五章工艺流转卡的存档管理第十五条工艺流转卡必须按照规定的时间保留备查,一般不少于两年。
第十六条工艺流转卡的存档必须按照规定的要求进行分类、整理和归档。
生产工序流转卡
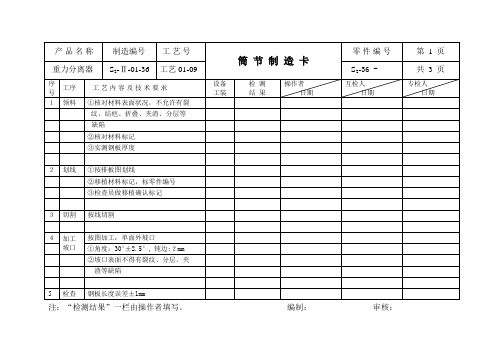
注:“检测结果”一栏由操作者填写。
编制:审核:注:“检测结果”一栏由操作者填写。
编制:审核:注:“检测结果”一栏由操作者填写。
编制:审核:注:“检测结果”一栏由操作者填写。
编制:审核:注:“检测结果”一栏由操作者填写。
编制:审核:注:“检测结果”一栏由操作者填写。
编制:审核:注:“检测结果”一栏由操作者填写。
编制:审核:注:“检测结果”一栏由操作者填写。
编制:审核:注:“检测结果”一栏由操作者填写。
编制:审核:注:“检测结果”一栏由操作者填写。
编制:审核:注:“检测结果”一栏由操作者填写。
编制:审核:注:“检测结果”一栏由操作者填写。
编制:审核:注:“检测结果”一栏由操作者填写。
编制:审核:注:“检测结果”一栏由操作者填写。
编制:审核:注:“检测结果”一栏由操作者填写。
编制:审核:注:“检测结果”一栏由操作者填写。
编制:审核:注:“检测结果”一栏由操作者填写。
编制:审核:注:“检测结果”一栏由操作者填写。
编制:审核:注:“检测结果”一栏由操作者填写。
编制:审核:注:“检测结果”一栏由操作者填写。
编制:审核:注:“检测结果”一栏由操作者填写。
编制:审核:注:“检测结果”一栏由操作者填写。
编制:审核:注:“检测结果”一栏由操作者填写。
编制:审核:注:“检测结果”一栏由操作者填写。
编制:审核:注:“检测结果”一栏由操作者填写。
编制:审核:。
ASME规范产品焊接管理的探讨

ASME规范产品焊接管理的探讨摘要:ASME规范产品的建造是一项系统化的工作,焊接作为特殊工序是ASME规范产品中十分关键的控制环节。
本文对ASME规范产品建造过程中的焊接管理从质量体系建立、人员管理、焊接文件、焊材控制、焊接过程控制、焊缝返修等方面进行了分析和探讨。
关键词:ASME 钢印产品焊接管理质量控制1 ASME质量体系的建立公司根据ASME要求建立了ASME质量体系,编制了ASME质量手册及程序文件,首版2011年正式发布执行。
ASME质量控制手册是该质量控制体系的书面文字叙述,是ASME钢印产品质量控制的纲领性文件,公司员工在安装及制造规范产品时,必须严格遵照执行ASME规范、ASME质量手册和美国锅炉压力容器检验师总部检验规范的要求,不得违反。
ASME质量手册中包含“焊接管理”和“热处理”两个章节,程序文件中包含6个焊接相关的管理程序,内容涵盖了焊缝识别、缺陷返修、热处理、焊材管理、目视检验等工作。
工欲善其事必先利其器,ASME质量手册和程序文件的编制发布为钢印产品的建造奠定了坚实的管理基础。
2 人员管理ASME标准中对三种人员的有资质要求,即NDT检验人员、VT目视检验人员和焊工/焊接操作工。
NDT检验人员资质外部取证,VT检验人员的培训及授权由QC部负责。
焊工技能评定和焊工资质管理成为焊接管理的一项重要工作。
焊工技能评定需严格按照ASME IX执行。
ASME标准相对于国内标准而言焊工评定的适用范围是比较宽的,但是进行ASME焊工评定时需要注意焊接变素的限制。
在实际的焊工评定中,可依据规范要求,综合考虑各焊接变素及评定范围,合理的选取焊工评定(操作)方法、母材试件的尺寸、母材P-No.及焊材F-No.,尽可能的扩大焊工技能评定覆盖范围。
ASME规范产品的焊工资质管理是一项严谨而且持久的工作,焊工资质需严格控制并由专人进行管理维护。
每个合格焊工分配一个唯一焊工钢印号来识别。
依据焊工评定记录WPQ编制“已有资格焊工及焊接操作工一览表”,并定期根据焊工的实际操作活动更新和完善“焊工和焊接操作工资格连续操作记录”,以确保焊工资质有效。
工艺流转卡管理规定
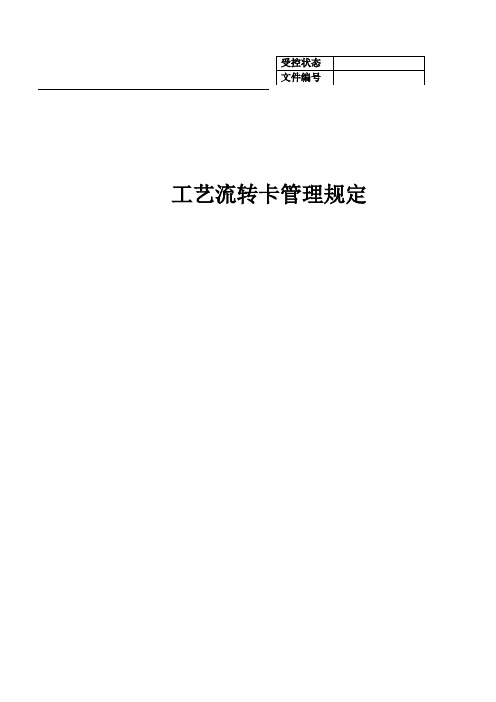
4.4对检验不合格的部件,经评审最终不予放行,按不合格品控制程序执行;检验不合格的部件由班长安排人员返工或返修;
4.5经检验合格的部件,生产者必须使用白色油漆笔将部件编号(见附件2)标识在部件上,<工艺流转卡>必须随合格部件一起转序或存放;质量部将检验合格的部件做好合格标识,不合格部件做好隔离;
3工作职责
3.1工艺员负责公司产品自制件<工艺流转卡>的编制、更新、发放;
3.2生产调度负责<工艺流转卡>班组、部件编号、使用部件编号、生产订单的填写和分发;
3.3生产者负责按<工艺流转卡>技术要求进行自检,填写自检项。班长负责填写自检结论,并签名确认;
3.4质检员负责按<工艺流转卡>技术要求进行专检,填写专检项和专检结论,并签名确认;
第三层:流水号。为“01、02……99”
第三层:年月。如2013年7月为“1307”
第二层:零部件代号。
第一层:工段班组代号。如“H1、H2、TL……”
3.工段班组代号:工段名称拼音首字母+班组名称拼音首字母+班组序号(无序号时以班组名称第二个字拼音首字母代替)。
表2 班组代号表
班组代号
名称
班组代号
4.6质检员在下一道工序检验过程中发现部件与<工艺流转卡>检验要求不相符时,应立即予以纠正,退回至上一道工序重新流转;避免乱流转现象;
4.7最终工序生产者要将所有部件<工艺流转卡>收集后送检,没有<工艺流转卡>或所有工序<工艺流转卡>不完整的不予总检。完成总检后,制造部负责对所有<工艺流转卡>收集、整理及保管;
ASME 取证(专业部分)

ASME取证试题(专业部分)一、设计方面(压力容器UG、UW与UCS)1.常规压力容器强度计算书应该包含哪些基本内容?筒体得强度计算应该考虑哪些要求?椭圆封头得强度计算应该考虑哪些要求?2.如何确定压力容器设计过程中引用标准得版本?如何考虑单位制统一得问题,规范怎么要求得?3.如何考虑规范中没有提到得计算,比如支座计算?4.压力容器得腐蚀裕量就是由设计工程师指定吗?设计工程师如何审核用户设计规范?5.对于锅炉与压力容器,静压头就是否都一定要考虑?6.压缩空气储罐得受压件最小要求壁厚就是多少?7.哪些材料可以允许用于制造压力容器得受压件?允许得螺栓,螺母材料就是哪些?压力容器非受压件就是否需要就是ASME材料?8.压力容器人孔得设计方面得有什么要求?容器排污孔得位置有什么要求?计算书中得所有得尺寸就是腐蚀前还就是腐蚀后?9.判定压力容器就是否需要焊后热处理得因素有哪些?公称厚度得定义?10.什么情况下压力容器必须拍片?如果规范不强制拍片,那么由谁决定拍片得比例?11.如果容器接管开孔在焊缝上,接管满足UG-36(c)(3)得要求不需要计算开孔补强,对这样得开孔处得焊缝有没有RT得要求?12.判定压力容器就是否需要冲击试验得因素有哪些?就是否只就是受压件需要考虑低温冲击?考虑低温冲击时,控制厚度得定义?设计工程师请熟悉附录JJ!13.对于压力容器,免除开孔补强计算得开孔应满足什么条件?14.就是不就是所有尺寸得补强圈都可以完整得考虑为补强得范围内,即补强得范围?15.压力容器接管厚度得计算需满足那些要求?16.针对容器,考虑冲击试验时,SA-105,SA-516 Gr70 正火, SA-106B 分别属于哪一种曲线?17.一台容器打了RT-3标记,封头与筒体焊接用Type 1得接头形式,封头计算时得焊接接头系数为多少?18.一台容器封头为无缝,筒体纵缝RT抽拍,封头与筒体得环缝抽拍并同时满足UW-11(a)5(b)得要求,计算封头壁厚时得焊接接头系数为多少?筒体接头系数为多少?容器打RT-1,RT-2,RT-3还就是RT-4?19.SA 106B 与 A106B什么区别?能等同得材料吗?20.针对容器,封头成型后如何判定就是否需要成型后热处理?如何判定就是否需要带成型试板?21.如何判定焊缝强度就是否需要计算?22.压力容器得水压试验压力值如何确定?水压试验温度就是指介质温度还就是金属温度?具体得温度值有何要求?23.压力容器铭牌得要求有哪些?24.如果容器得铭牌直接装在设备上,铭牌可以装在与设备相连得支架上,这种情况下,铭牌与容器得距离有无具体得要求?二、材料方面1.SA-516 Gr70得质保书有哪些要求?SA-106 GrB质保书有哪些要求?2.SA-516 Gr70 ,20mm厚,允许得尺寸变差就是多少?板材原始标记得要求就是哪些?3.B16、5法兰,材料SA-105要求得标记有哪些?质保书要求哪些内容?就是否需要作入厂验收?4.SA-106B要求得标记有哪些?要求哪些性能试验,允许得尺寸偏差为多少?5.N, QT, Ceq就是什么意思?6.ASME材料如何进行验收?就是否需要复验?就是否一定需要质保书?哪些材料需要质保书?ASME焊材如何进行验收?就是否一定需要质保书?第I 卷与VIII-1卷对材料质保书方面得要求就是否一样?7.材料入厂验收得基本流程就是怎样得?每一过程需要哪些文件?验收合格得材料由谁指定材料追踪号?如何指定?8.谁负责登记材料追踪号得台帐?9.如果材料验收不合格,如何处理?如果需要对母材进行补焊,应该如何操作?10.如果外购得无缝封头,应该如何进行验收?采取什么样得方式追踪其材料追踪号?三、焊接方面1.手工焊,自动焊,机器焊得定义?2.哪些焊接方法能用于焊接VIII-1卷得容器?3.WPS,PQR都应该分别包含哪些变素?4.WPS里得非重要变素发生变化时,如何处理?5.P-No、,F-No、A-No、分别含义?6.WPS中得焊材不属于任何一个A-No、,如何处理?7.焊工考试试样得试验有哪些项目?哪些焊接方法可以用RT替代力学性能试验?RT评定合格得依据就是第五卷吗?这种情况下对焊缝长度有要求吗?8.PQR机械性能包含哪些试验项目?合格依据就是什么?可以用RT代替力学性能试验吗?9.管接头与筒体得焊接接头采用骑座式,管接头尺寸为1’’, 那么焊这条焊缝得焊工应该如何进行考试?如果接头形式为插入式呢?焊工应该具有什么位置得资格?10.焊接非受压件与受压件得焊工就是否需要评定合格得焊工?就是否需要评定合格得WPS,允许进行焊接得最低温度就是多少?11.非受压件就是否一定需要就是ASME材料?非受压件与受压件得焊缝要求在哪一章节?12.如果WPS评定P-NO、1材料并合格,那么这个WPS能覆盖哪些材料?13.如果焊工考试有F-NO、3 带垫板,那么这个焊工焊接哪些F-No、?14.如何维持焊工得资格?15.焊接工艺评定试板材料为SA-516 Gr 70,厚度为9mm,那么弯曲半径为多少?如果试样厚度为40mm,那么做拉伸实验时如何处理?16.低氢焊条得烘培温度,烘培时间依据就是什么?能够回收几次?如何标识回收焊条?如何控制回收得焊条?四、检验方面1.检验员如何进行装配检查?点焊检查?焊缝检查?如果就是RT抽拍,由谁指定抽拍得位置?2.错边量得要求在哪一章节?焊缝余高要求在哪一章节?3.检验员在焊接前应该检查什么?焊接中检查什么?焊接后检查什么?4.如果在检验过程中出现NCR, 应该采取怎样得步骤?5.检验接管与筒体得角焊缝尺寸时,图纸规定得尺寸就是就是仅值沿筒体纵向得焊脚尺寸还就是针对整个焊缝焊脚?6.热处理工程师在准备焊后热处理工艺卡时,保温温度,升温速度,降温速度,如炉温度,出炉温度,保温时间依据在那一章节?7.热处理分包前与分包后如何控制?8.容器在水压试验之后,打U钢印之前,在受压件上焊接非受压件,就是否需要重新进行水压试验?9.MDR就是什么?如何选用相应格式得MDR? 请质检部经理负责熟悉并填写MDR。
ASME 取证(专业部分)
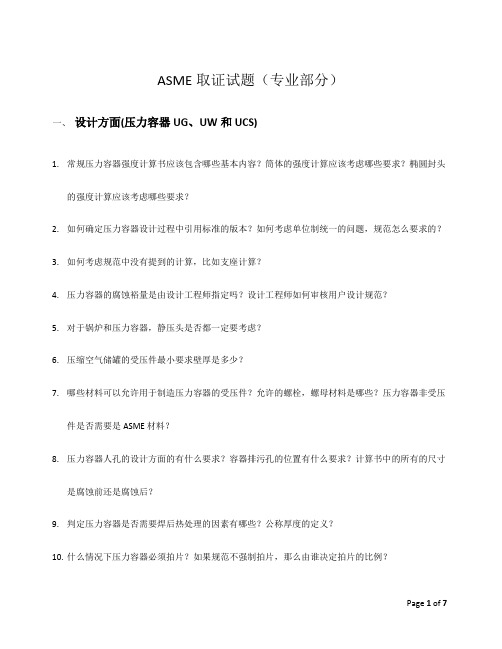
ASME取证试题(专业部分)一、设计方面(压力容器UG、UW和UCS)1.常规压力容器强度计算书应该包含哪些基本内容?筒体的强度计算应该考虑哪些要求?椭圆封头的强度计算应该考虑哪些要求?2.如何确定压力容器设计过程中引用标准的版本?如何考虑单位制统一的问题,规范怎么要求的?3.如何考虑规范中没有提到的计算,比如支座计算?4.压力容器的腐蚀裕量是由设计工程师指定吗?设计工程师如何审核用户设计规范?5.对于锅炉和压力容器,静压头是否都一定要考虑?6.压缩空气储罐的受压件最小要求壁厚是多少?7.哪些材料可以允许用于制造压力容器的受压件?允许的螺栓,螺母材料是哪些?压力容器非受压件是否需要是ASME 材料?8.压力容器人孔的设计方面的有什么要求?容器排污孔的位置有什么要求?计算书中的所有的尺寸是腐蚀前还是腐蚀后?9.判定压力容器是否需要焊后热处理的因素有哪些?公称厚度的定义?10.什么情况下压力容器必须拍片?如果规范不强制拍片,那么由谁决定拍片的比例?11.如果容器接管开孔在焊缝上,接管满足UG-36(c)(3)的要求不需要计算开孔补强,对这样的开孔处的焊缝有没有RT的要求?12.判定压力容器是否需要冲击试验的因素有哪些?是否只是受压件需要考虑低温冲击?考虑低温冲击时,控制厚度的定义?设计工程师请熟悉附录JJ!13.对于压力容器,免除开孔补强计算的开孔应满足什么条件?14.是不是所有尺寸的补强圈都可以完整的考虑为补强的范围内,即补强的范围?15.压力容器接管厚度的计算需满足那些要求?16.针对容器,考虑冲击试验时,SA-105,SA-516 Gr70 正火, SA-106B 分别属于哪一种曲线?17.一台容器打了RT-3标记,封头和筒体焊接用Type 1的接头形式,封头计算时的焊接接头系数为多少?18.一台容器封头为无缝,筒体纵缝RT抽拍,封头与筒体的环缝抽拍并同时满足UW-11(a)5(b)的要求,计算封头壁厚时的焊接接头系数为多少?筒体接头系数为多少?容器打RT-1,RT-2,RT-3还是RT-4?19.SA 106B 和 A106B 什么区别?能等同的材料吗?20.针对容器,封头成型后如何判定是否需要成型后热处理?如何判定是否需要带成型试板?21.如何判定焊缝强度是否需要计算?22.压力容器的水压试验压力值如何确定?水压试验温度是指介质温度还是金属温度?具体的温度值有何要求?23.压力容器铭牌的要求有哪些?24.如果容器的铭牌直接装在设备上,铭牌可以装在与设备相连的支架上,这种情况下,铭牌与容器的距离有无具体的要求?二、材料方面1.SA-516 Gr70的质保书有哪些要求?SA-106 GrB质保书有哪些要求?2.SA-516 Gr 70 ,20mm厚,允许的尺寸变差是多少?板材原始标记的要求是哪些?3.B16.5 法兰,材料SA-105 要求的标记有哪些?质保书要求哪些内容?是否需要作入厂验收?4.SA-106B要求的标记有哪些?要求哪些性能试验,允许的尺寸偏差为多少?5.N, QT, Ceq是什么意思?6.ASME 材料如何进行验收?是否需要复验?是否一定需要质保书?哪些材料需要质保书?ASME焊材如何进行验收?是否一定需要质保书?第I 卷和VIII-1卷对材料质保书方面的要求是否一样?7.材料入厂验收的基本流程是怎样的?每一过程需要哪些文件?验收合格的材料由谁指定材料追踪号?如何指定?8.谁负责登记材料追踪号的台帐?9.如果材料验收不合格,如何处理?如果需要对母材进行补焊,应该如何操作?10.如果外购的无缝封头,应该如何进行验收?采取什么样的方式追踪其材料追踪号?三、焊接方面1.手工焊,自动焊,机器焊的定义?2.哪些焊接方法能用于焊接VIII-1卷的容器?3.WPS,PQR都应该分别包含哪些变素?4.WPS里的非重要变素发生变化时,如何处理?5.P-No.,F-No. A-No.分别含义?6.WPS中的焊材不属于任何一个A-No.,如何处理?7.焊工考试试样的试验有哪些项目?哪些焊接方法可以用RT替代力学性能试验?RT评定合格的依据是第五卷吗?这种情况下对焊缝长度有要求吗?8. PQR 机械性能包含哪些试验项目?合格依据是什么?可以用RT代替力学性能试验吗?9.管接头与筒体的焊接接头采用骑座式,管接头尺寸为1’’, 那么焊这条焊缝的焊工应该如何进行考试?如果接头形式为插入式呢?焊工应该具有什么位置的资格?10.焊接非受压件与受压件的焊工是否需要评定合格的焊工?是否需要评定合格的WPS, 允许进行焊接的最低温度是多少?11.非受压件是否一定需要是ASME材料?非受压件与受压件的焊缝要求在哪一章节?12.如果WPS 评定P-NO. 1材料并合格,那么这个WPS能覆盖哪些材料?13.如果焊工考试有F-NO.3 带垫板,那么这个焊工焊接哪些F-No.?14.如何维持焊工的资格?15.焊接工艺评定试板材料为SA-516 Gr 70,厚度为9mm,那么弯曲半径为多少?如果试样厚度为40mm,那么做拉伸实验时如何处理?16.低氢焊条的烘培温度,烘培时间依据是什么?能够回收几次?如何标识回收焊条?如何控制回收的焊条?四、检验方面1.检验员如何进行装配检查?点焊检查?焊缝检查?如果是RT抽拍,由谁指定抽拍的位置?2.错边量的要求在哪一章节?焊缝余高要求在哪一章节?3.检验员在焊接前应该检查什么?焊接中检查什么?焊接后检查什么?4.如果在检验过程中出现NCR, 应该采取怎样的步骤?5.检验接管与筒体的角焊缝尺寸时,图纸规定的尺寸是是仅值沿筒体纵向的焊脚尺寸还是针对整个焊缝焊脚?6.热处理工程师在准备焊后热处理工艺卡时,保温温度,升温速度,降温速度,如炉温度,出炉温度,保温时间依据在那一章节?7.热处理分包前和分包后如何控制?8.容器在水压试验之后,打U钢印之前,在受压件上焊接非受压件,是否需要重新进行水压试验?9.MDR 是什么?如何选用相应格式的MDR? 请质检部经理负责熟悉并填写MDR。
C5 ASME 检查和检验程序

共3页,第1页5.0 检查和检验程序本章规定按照ASME规范和用户技术条件制造规范产品的检查和检验程序。
5.1总则5.1.1 质检部主管应负责提供规范产品的检查和检验程序,并符合ASME规范和QC手册的要求。
5.2 工艺检验流转卡(COL)5.2.1 工艺工程师应按照图纸、规范和用户技术条件编制COL(样表5-1A,B&C)。
COL应包含所有需要的检查、检验和试验,并有质检员和AI对应签字和注明日期的栏目,以验证上述的质量活动。
COL应经质检工程师审核、计划部主管批准,以确保所有需要的检查、检验和试验均是合理、恰当的,并满足规范和用户技术条件的要求。
需要修改时,工艺工程师应准备新的COL或在原版上修改,新修改的内容须经和初版一样的审查和批准,插入原COL以取代需要更改内容,封面应升版,签字确认。
替换下来的内容也要附在后面。
5.2.2在制造开始之前,质保工程师负责将COL与相应的图纸、工艺或说明一并提交AI审核。
AI审核后,在COL上指明AI检验点,并在COL封面页上签字和注明日期。
5.3 AI检验5.3.1 AI检验点为AI在COL上签字和注明日期的检验点。
AI检验点分成停止点(H)、见证点(W)和审核点(R),定义如下:a) H:停止点是AI不到场,工序不得继续进行的检验点;b) W:见证点是AI不到场,但已事先经AI许可,本公司质检员认可后,工序可继续进行的检验点。
AI的事先许可由经济运行管理部主管写在相应的COL上。
此检查、检验或试验记录应在AI下一次到访时,提交AI认可。
如果AI不能到场指定RT抽拍位置,并且已经被告知,质检工程师负责代表AI指定抽拍点。
c) R:审核点是AI不在场,工序仍可以继续进行的检验点。
此检查、检验或试验记录要在最终检验和试验前,提交AI审核和认可。
5.3.2质保工程师应负责工序进行到“停止点(H)”和“见证点(W)”检验点之前、在合理的时间内通知AI。
5.4 制造过程检查、检验或试验5.4.1当接近过程检验工序时,车间班长负责要求质检员进行或见证检查、检验或试验。