脉冲电源电镀的优势
脉冲电镀电源的工作原理及技术研究
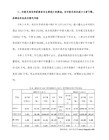
脉冲关断期内金属离子的质量浓度的回升降低了浓差极化,有利于提高阴极电流效率和阴极电流密度,从而提高镀速。脉冲电镀的这种优越性,可用于某些对镀层沉积速率要求较快的电镀生产(如电子线材的卷至卷连续电镀)。但对于普通的电镀生产,若选择脉冲电镀的目的单纯是为了提高生产效率,则似乎有些不太合适。
脉冲电镀电源的工作原理及技术研究
前言
脉冲电镀是通过槽外控制方法改善镀层质量的一种强有力的手段,相比于普通的直流电镀镀层,其具有更优异的性能(如耐蚀、耐磨、纯度高、导电、焊接及抗变色性能好等),且可大幅节约稀贵金属,因此,在功能性电镀中得到较好的应用。目前脉冲电镀中所使用的多为方波脉冲。
(2)在脉冲关断期toff内高的过电位使阴极附近的金属离子以极快的速度被消耗,当阴极界面金属离子的质量浓度为零或很低时,电沉积过程进入关断期。在关断期内,金属离子向阴极附近传递从而使扩散层中金属离子的质量浓度得以回升,并有利于在下一个脉冲周期使用较高的峰值电流密度。
脉冲电镀过程中,当电流导通时,电化学极化增大,阴极区附近金属离子被充分沉积;当电流关断时,阴极区附近放电离子又恢复到初始的质量浓度,浓差极化消除,并伴有对沉积层有利的重结晶、吸脱附等现象。这样的过程周期性的贯穿于整个电镀过程的始末,其中所包含的机理构成了脉冲电镀的最基本原理。
传统的直流电镀只有电流或电压可供调节,而脉冲电镀有脉冲电流密度(或峰值电流密度)Jp、脉冲导通时间ton和脉冲关断时间toff3个独立的参数。由ton和toff可以引出脉冲占空比γ。
(1)脉冲占空比γ计算公式
脉冲占空比γ指脉冲导通时间ton占整个脉冲周期(ton+toff)的百分比,可用下式表示:
数字单脉冲电源在电镀中的应用
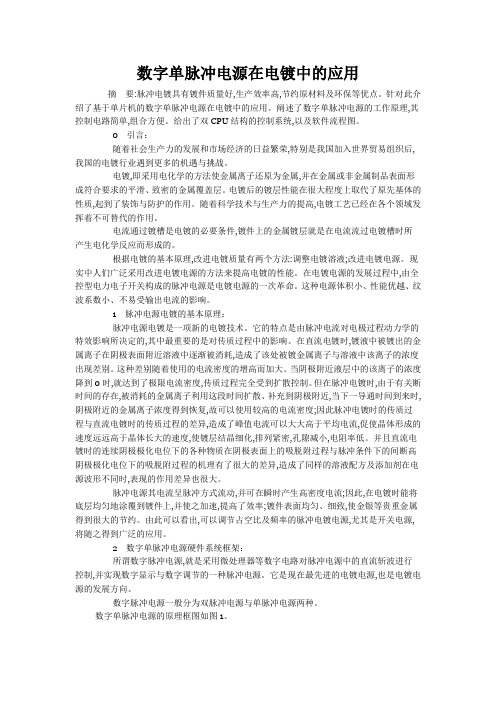
数字单脉冲电源在电镀中的应用摘要:脉冲电镀具有镀件质量好,生产效率高,节约原材料及环保等优点。
针对此介绍了基于单片机的数字单脉冲电源在电镀中的应用。
阐述了数字单脉冲电源的工作原理,其控制电路简单,组合方便。
给出了双CPU结构的控制系统,以及软件流程图。
0引言:随着社会生产力的发展和市场经济的日益繁荣,特别是我国加入世界贸易组织后,我国的电镀行业遇到更多的机遇与挑战。
电镀,即采用电化学的方法使金属离子还原为金属,并在金属或非金属制品表面形成符合要求的平滑、致密的金属覆盖层。
电镀后的镀层性能在很大程度上取代了原先基体的性质,起到了装饰与防护的作用。
随着科学技术与生产力的提高,电镀工艺已经在各个领域发挥着不可替代的作用。
电流通过镀槽是电镀的必要条件,镀件上的金属镀层就是在电流流过电镀槽时所产生电化学反应而形成的。
根据电镀的基本原理,改进电镀质量有两个方法:调整电镀溶液;改进电镀电源。
现实中人们广泛采用改进电镀电源的方法来提高电镀的性能。
在电镀电源的发展过程中,由全控型电力电子开关构成的脉冲电源是电镀电源的一次革命。
这种电源体积小、性能优越、纹波系数小、不易受输出电流的影响。
1脉冲电源电镀的基本原理:脉冲电源电镀是一项新的电镀技术。
它的特点是由脉冲电流对电极过程动力学的特效影响所决定的,其中最重要的是对传质过程中的影响。
在直流电镀时,镀液中被镀出的金属离子在阴极表面附近溶液中逐渐被消耗,造成了该处被镀金属离子与溶液中该离子的浓度出现差别。
这种差别随着使用的电流密度的增高而加大。
当阴极附近液层中的该离子的浓度降到0时,就达到了极限电流密度,传质过程完全受到扩散控制。
但在脉冲电镀时,由于有关断时间的存在,被消耗的金属离子利用这段时间扩散、补充到阴极附近,当下一导通时间到来时,阴极附近的金属离子浓度得到恢复,故可以使用较高的电流密度;因此脉冲电镀时的传质过程与直流电镀时的传质过程的差异,造成了峰值电流可以大大高于平均电流,促使晶体形成的速度远远高于晶体长大的速度,使镀层结晶细化,排列紧密,孔隙减小,电阻率低。
脉冲电镀基本概况
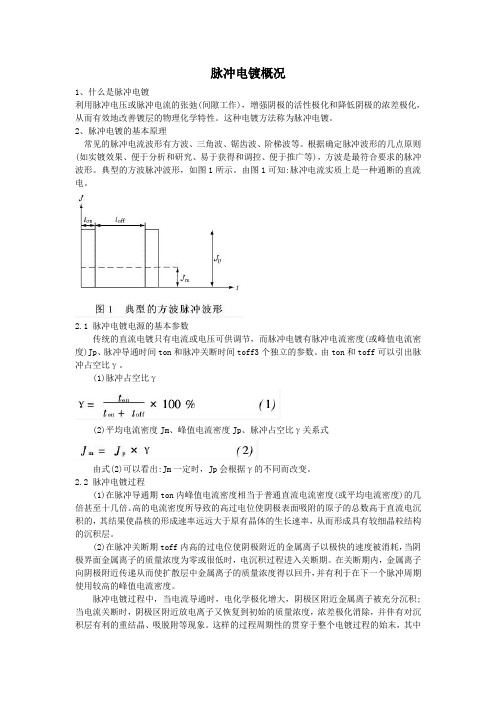
脉冲电镀概况1、什么是脉冲电镀利用脉冲电压或脉冲电流的张弛(间隙工作),增强阴极的活性极化和降低阴极的浓差极化,从而有效地改善镀层的物理化学特性。
这种电镀方法称为脉冲电镀。
2、脉冲电镀的基本原理常见的脉冲电流波形有方波、三角波、锯齿波、阶梯波等。
根据确定脉冲波形的几点原则(如实镀效果、便于分析和研究、易于获得和调控、便于推广等),方波是最符合要求的脉冲波形。
典型的方波脉冲波形,如图1所示。
由图1可知:脉冲电流实质上是一种通断的直流电。
2.1 脉冲电镀电源的基本参数传统的直流电镀只有电流或电压可供调节,而脉冲电镀有脉冲电流密度(或峰值电流密度)Jp、脉冲导通时间ton和脉冲关断时间toff3个独立的参数。
由ton和toff可以引出脉冲占空比γ。
(1)脉冲占空比γ(2)平均电流密度Jm、峰值电流密度Jp、脉冲占空比γ关系式由式(2)可以看出:Jm一定时,Jp会根据γ的不同而改变。
2.2 脉冲电镀过程(1)在脉冲导通期ton内峰值电流密度相当于普通直流电流密度(或平均电流密度)的几倍甚至十几倍。
高的电流密度所导致的高过电位使阴极表面吸附的原子的总数高于直流电沉积的,其结果使晶核的形成速率远远大于原有晶体的生长速率,从而形成具有较细晶粒结构的沉积层。
(2)在脉冲关断期toff内高的过电位使阴极附近的金属离子以极快的速度被消耗,当阴极界面金属离子的质量浓度为零或很低时,电沉积过程进入关断期。
在关断期内,金属离子向阴极附近传递从而使扩散层中金属离子的质量浓度得以回升,并有利于在下一个脉冲周期使用较高的峰值电流密度。
脉冲电镀过程中,当电流导通时,电化学极化增大,阴极区附近金属离子被充分沉积;当电流关断时,阴极区附近放电离子又恢复到初始的质量浓度,浓差极化消除,并伴有对沉积层有利的重结晶、吸脱附等现象。
这样的过程周期性的贯穿于整个电镀过程的始末,其中所包含的机理构成了脉冲电镀的最基本原理。
3、脉冲电镀的优越性及适用性3.1 镀层结晶细致在脉冲导通期内,由于使用较高的电流密度,使晶核的形成速率远远大于原有晶体的生长速率,因此可形成结晶细致的镀层。
脉冲电源的应用和特点
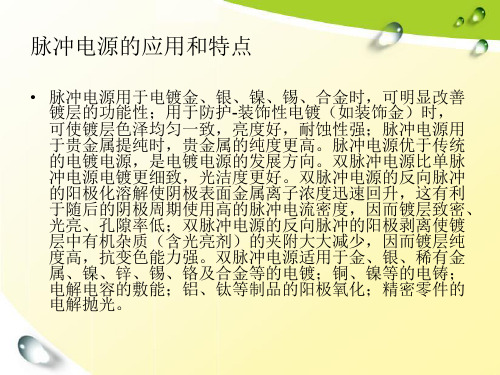
• 脉冲电源用于电镀金、银、镍、锡、合金时,可明显改善 镀层的功能性;用于防护-装饰性电镀(如装饰金)时, 可使镀层色泽均匀一致,亮度好,耐蚀性强;脉冲电源用 于贵金属提纯时,贵金属的纯度更高。脉冲电源优于传统 的电镀电源,是电镀电源的发展方向。双脉冲电源比单脉 冲电源电镀更细致,光洁度更好。双脉冲电源的反向脉冲 的阳极化溶解使阴极表面金属离子浓度迅速回升,这有利 于随后的阴极周期使用高的脉冲电流密度,因而镀层致密、 光亮、孔隙率低;双脉冲电源的反向脉冲的阳极剥离使镀 层中有机杂质(含光亮剂)的夹附大大减少,因而镀层纯 度高,抗变色能力强。双脉冲电源适用于金、银、稀有金 属、镍、锌、锡、铬及合金等的电镀;铜、镍等的电铸; 电解电容的敷能;铝、钛等制品的阳极氧化;精密零件的 电解抛光。
• 脉冲电源特点
• 1、循环输出十组参数各异的电流波形,每组电流可在直流、 单脉冲、双脉冲或直流换向等波形中任意选择。 • 2、每组电流的持续时间可在1S~9999S间任意选择,便 于控制各组电流所得镀层的厚度。 • 3、各组脉冲电流在交替运行过程中,平均电流始终不变, 以保证使用不同占空比时各组脉冲的峰值电流各不相同。 • 4、输出波形:方波脉冲或直流 • 5、脉冲频率:5~5000Hz • 6、脉冲占空比:0~100% • 7、正、反向脉冲换向时间:0~9999ms • 8、各组电流持续时间:1S≤t1、t2~t10≤9999S • 9、最大峰值电流:30A~500A
电镀过程中使用的电源类型

电镀过程中使用的电源类型电镀过程是将金属制品表面镀上一层金属或合金的工艺,以提高其耐腐蚀性、耐磨性、导电性等性能。
在电镀过程中,电源类型起着关键作用,它提供了所需的电能,使电镀过程能够顺利进行。
常见的电源类型包括直流电源和交流电源。
直流电源是电镀过程中常用的一种电源类型。
直流电源具有稳定的电流和电压输出,能够满足电镀过程对稳定电流的需求。
在直流电源中,阳极连接到正极,阴极连接到负极,通过电解液中的离子传导,使金属离子在阳极上氧化,而金属在阴极上还原,从而实现金属离子的电镀。
直流电源还可以根据需要进行电流和电压的调节,以控制电镀过程的质量和效率。
交流电源也可以用于电镀过程。
在交流电源中,电流和电压的方向会周期性地变换,这样可以实现金属离子的交替氧化和还原。
交流电源的频率通常为50Hz或60Hz,与直流电源相比,交流电源的输出电流和电压变化较大,需要通过其他设备来稳定电流和电压,以保证电镀过程的稳定性。
除了直流电源和交流电源,还有一种特殊的电源类型被广泛应用于电镀过程,即脉冲电源。
脉冲电源是一种通过不同的脉冲信号控制电流和电压的电源,可以根据不同的电镀要求提供不同的脉冲参数。
脉冲电源的使用可以提高电镀层的均匀性和致密性,同时减少能源消耗和金属离子的浪费。
脉冲电源的应用也在一定程度上解决了传统电镀过程中的一些问题,如电解液的氧化分解和阳极溶解等。
在电镀过程中,选择合适的电源类型对于电镀质量和效率至关重要。
不同的电源类型具有不同的特点和适用范围,需要根据电镀工艺要求进行选择。
此外,为了确保电镀过程的安全性和稳定性,还需要配备相应的电源控制与保护装置,以避免电流过大或过小、电压波动等问题对电镀质量造成负面影响。
电源类型是电镀过程中的重要因素,直流电源、交流电源和脉冲电源是常见的电源类型。
选择合适的电源类型可以提高电镀质量和效率,保证电镀过程的稳定性和安全性。
在实际应用中,需要根据具体情况选择合适的电源类型,并结合其他设备和控制装置,以满足电镀工艺的要求。
2011电镀工艺学第7章7.5脉冲电镀
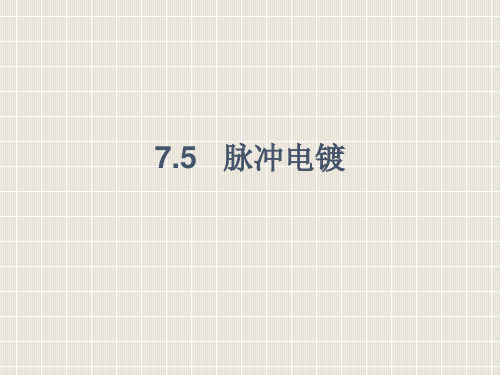
优点:电流效率和合金组成易控制,电镀 过程中无需因镀件的增减而调节电流。
缺点:仪器制造方面存在较大困难。另外, 当电流脉冲终结时,需重新达到起始电位, 如果该电位与电极/镀液界面的静态电位相 近,沉积金属有可能溶解。
• 恒电流脉冲电镀:
脉冲电镀中表征电极反应速度的一个最 重要参数就是脉冲极限电流密度ipd,它是 脉冲结束时电极表面浓度降到零时的脉冲 电流密度。
• 脉动扩散层的厚度,不取决于浓度C0和脉 冲电流密度jp。它仅仅取决于金属离子的扩 散系数D和脉冲长度T,并且与这两个量的 平方根成正比。
ipd
nFD'ec 2Dotn
1. 脉冲镀金 采用脉冲法得到的镀金层外观颜色好、
结晶细致、密度大、均匀性好。采用脉冲 镀金可以减薄镀层的厚度,节省15-20%的 黄金,并且脉冲法得到的镀金层具有较好 的抗高温变色能力。
脉冲镀金的工艺参数可为:导通时间 t率on1=000.10mHzs,,脉关冲断平时均间电tof流f=0密.9度m与s,占直空流比密,度频相 同。
谢谢欣赏
THANK YOU FOR WATCHING
7.5 脉冲电镀
一、脉冲基本概念
脉冲电镀与直流电镀的主要区别在于所 使用的电源不同,脉冲电镀所使用的是一 种可以提供通断直流电流的脉冲整流器。
脉冲电度jp、
• 脉冲导通时间ton、 脉冲关断时间toff
脉冲电源电流的波形: • 方波(或称矩形波)、 • 正弦半波、 • 锯齿波 • 间隔锯齿波等 一般镀单金属以方波脉冲电流为好。
(7)降低浓差极化,提高阴极电流密度,可 以提高沉积速度。
采用脉冲电镀可用比较薄的镀层代替较 厚的直流电镀层,节约了原材料,尤其是 在节约贵重金属方面具有很大的潜力。
流和脉冲电镀Cu互连线的性能比较
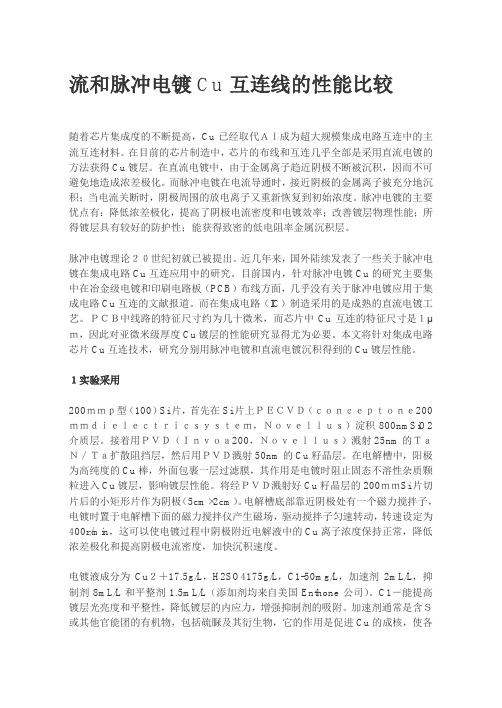
流和脉冲电镀Cu互连线的性能比较随着芯片集成度的不断提高,Cu已经取代Al成为超大规模集成电路互连中的主流互连材料。
在目前的芯片制造中,芯片的布线和互连几乎全部是采用直流电镀的方法获得Cu镀层。
在直流电镀中,由于金属离子趋近阴极不断被沉积,因而不可避免地造成浓差极化。
而脉冲电镀在电流导通时,接近阴极的金属离子被充分地沉积;当电流关断时,阴极周围的放电离子又重新恢复到初始浓度。
脉冲电镀的主要优点有:降低浓差极化,提高了阴极电流密度和电镀效率;改善镀层物理性能;所得镀层具有较好的防护性;能获得致密的低电阻率金属沉积层。
脉冲电镀理论20世纪初就已被提出。
近几年来,国外陆续发表了一些关于脉冲电镀在集成电路Cu互连应用中的研究。
目前国内,针对脉冲电镀Cu的研究主要集中在冶金级电镀和印刷电路板(PCB)布线方面,几乎没有关于脉冲电镀应用于集成电路Cu互连的文献报道。
而在集成电路(IC)制造采用的是成熟的直流电镀工艺。
PCB中线路的特征尺寸约为几十微米,而芯片中Cu互连的特征尺寸是1μm,因此对亚微米级厚度Cu镀层的性能研究显得尤为必要。
本文将针对集成电路芯片Cu互连技术,研究分别用脉冲电镀和直流电镀沉积得到的Cu镀层性能。
1实验采用200mmp型(100)Si片,首先在Si片上PECVD(conceptone200mmdielectricsystem,Novellus)淀积800nmSiO2介质层。
接着用PVD(Invoa200,Novellus)溅射25nm的TaN/Ta扩散阻挡层,然后用PVD溅射50nm的Cu籽晶层。
在电解槽中,阳极为高纯度的Cu棒,外面包裹一层过滤膜,其作用是电镀时阻止固态不溶性杂质颗粒进入Cu镀层,影响镀层性能。
将经PVD溅射好Cu籽晶层的200mmSi片切片后的小矩形片作为阴极(5cm×2cm)。
电解槽底部靠近阴极处有一个磁力搅拌子,电镀时置于电解槽下面的磁力搅拌仪产生磁场,驱动搅拌子匀速转动,转速设定为400r/min,这可以使电镀过程中阴极附近电解液中的Cu离子浓度保持正常,降低浓差极化和提高阴极电流密度,加快沉积速度。
脉冲电镀技术参数介绍
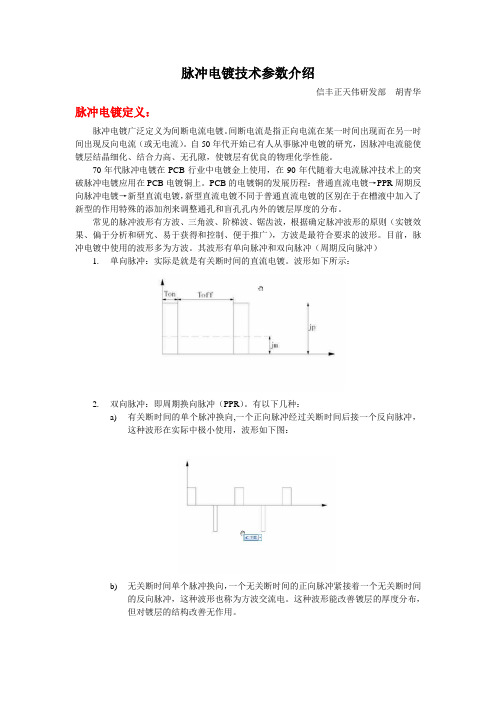
脉冲电镀技术参数介绍信丰正天伟研发部胡青华脉冲电镀定义:脉冲电镀广泛定义为间断电流电镀。
间断电流是指正向电流在某一时间出现而在另一时间出现反向电流(或无电流)。
自50年代开始已有人从事脉冲电镀的研究,因脉冲电流能使镀层结晶细化、结合力高、无孔隙,使镀层有优良的物理化学性能。
70年代脉冲电镀在PCB行业中电镀金上使用,在90年代随着大电流脉冲技术上的突破脉冲电镀应用在PCB电镀铜上。
PCB的电镀铜的发展历程:普通直流电镀→PPR周期反向脉冲电镀→新型直流电镀,新型直流电镀不同于普通直流电镀的区别在于在槽液中加入了新型的作用特殊的添加剂来调整通孔和盲孔孔内外的镀层厚度的分布。
常见的脉冲波形有方波、三角波、阶梯波、锯齿波,根据确定脉冲波形的原则(实镀效果、偏于分析和研究、易于获得和控制、便于推广),方波是最符合要求的波形。
目前,脉冲电镀中使用的波形多为方波。
其波形有单向脉冲和双向脉冲(周期反向脉冲)1.单向脉冲:实际是就是有关断时间的直流电镀。
波形如下所示:2.双向脉冲:即周期换向脉冲(PPR)。
有以下几种:a)有关断时间的单个脉冲换向,一个正向脉冲经过关断时间后接一个反向脉冲,这种波形在实际中极小使用,波形如下图:b)无关断时间单个脉冲换向,一个无关断时间的正向脉冲紧接着一个无关断时间的反向脉冲,这种波形也称为方波交流电。
这种波形能改善镀层的厚度分布,但对镀层的结构改善无作用。
c)脉动脉冲换向,一组正向脉冲接一组反向脉冲,这种波形是典型的周期换向波形,在功能性电镀中应用最为广泛,既能改善镀层的厚度分布又能改善镀层结晶结构。
d)多组脉冲换向:简称多脉冲,在脉动脉冲基础上增加可编程功能,在每一个程序或每一个时间段采用的脉冲参数各不一样。
多脉冲电镀在适当的参数下能形成不同结构和组成的多层镀层,各层间的应力能相互抵消,镀层脆性下降,抗疲劳强度提高。
PCB上所使用的脉冲电镀严格的说应称为周期脉冲反向电镀(Periodic Pulse Reverse Plating)。
- 1、下载文档前请自行甄别文档内容的完整性,平台不提供额外的编辑、内容补充、找答案等附加服务。
- 2、"仅部分预览"的文档,不可在线预览部分如存在完整性等问题,可反馈申请退款(可完整预览的文档不适用该条件!)。
- 3、如文档侵犯您的权益,请联系客服反馈,我们会尽快为您处理(人工客服工作时间:9:00-18:30)。
脉冲电镀的优势
随着表面处理工艺要求的不断提高,脉冲电镀被越来越多的人所关注,特别是科研院所、精密电子领域的技术工作者们,进行了长期的技术探索,发现或验证了脉冲电镀对比直流电镀的诸多优点,本文将脉冲电镀的优点和欧潽达新型脉冲电源的优点结合起来,做如下简单的汇总,以期以更简单的方式帮助大家理解认识脉冲电镀的优势。
(MX系列单脉冲、双脉冲电源)
新型脉冲电镀的优势有:
1、精密电路+数字控制,输出精度高;
2、触摸屏+人性化界面,操作简单;
3、频率、占空比可调,适用范围广;
4、允许更大峰值电流密度,提升镀层结合力,提高电镀效率;
5、间歇式输出,利于溶液离子恢复,减少镀层孔隙,增强镀层的抗蚀性能;
6、致密均匀的镀层,能够增强电导率;
7、消除氢脆,改善镀层物理性能;
8、减少镀层中的杂质含量,提高镀层纯度;
9、降低镀层内应力,提高镀层的韧性;
10、免除或减少添加剂的需要;
11、反向脉冲可减少镀层表面的尖峰和毛刺;
12、较薄的镀层即能实现规定的技术指标,故可节省15-20%的贵金属。
13、工艺曲线可编程,利于工艺精准控制;
14、媲美欧美进口电源的品质,价格却极其亲民;
15、单脉冲、双脉冲、正反脉冲可选择;
16、专属电源可定制;
长期以来,人们认为脉冲电镀仅适合镀金镀银,事实上脉冲电镀几乎适用于所以电镀工艺,包括如:镀金、镀银、镀铜、镀锌、镀镍、镀铬、镀铼、镀铂、镀钯以及电镀铜锌合金、镍铁合金、锌镍合金、镍铬合金等众多电镀工艺。
(脉冲镀金、镀银工艺)
造成人们对脉冲电镀认识局限的原因,是由于之前国内脉冲电源技术水平有限,进口脉冲电源动辄数十万的高昂价格限制了人们的购买,制约了人们对脉冲电镀工艺的研究。
现在,欧潽达通过开拓创新,能够提供品质优良、价格却十分亲民的脉冲电源供一般用户使用,亲民的定价旨在通过降低电源购买成本,让更多的人研究和使用脉冲电镀工艺,达到促进整个脉冲电镀工艺的推广与提升的目的。
正品的脉冲电源具备电流(平均电流、峰值电流)可调、电压可调、频率可调、占空比可调,4个主要参数,掌握这几个要素,就能够避免买到假的脉冲电源。
(买到假脉冲电源的情况并不少见)。
(标注为脉冲电源的直流电源)
有关脉冲电镀具体的频率、占空比、电流密度等参数的设定,不同电镀企业、不同工艺均有不同的经验数据,一般来说,脉冲频率300-1000Hz之间应用较多,
镀贵金属的占空比可在10-50%之间选择,普通金属的占空比25-70%之间选择,具体参数应以实践为基础的多次验证优化为准。
另外,针对表面处理领域,除了脉冲电镀之外,还有脉冲氧化、脉冲电解,比较典型的应用有:铝合金硬质氧化、钛合金氧化、微弧氧化、脉冲抛光、脉冲电絮凝等工艺,欧潽达愿意与您一道在更多的领域和场合协作,共同提升表面处理品质,挖掘跟多价值潜力,实现优质、高效、节能、省钱的更高追求。