轧制缺陷图谱、形成原因分析以及预防措施
轧制缺陷分析

裂纹裂纹是指线材表面沿轧制方向有平直或弯曲、折曲,或以一定角度向线材内部渗透的缺陷[1]。
裂纹长度和深度不同,在线材的长度方向上都能发现。
有的裂纹内有夹杂物,两侧也有脱碳现象。
线材表面产生裂纹的主要原因在于钢坯上有未消除的裂纹(无论纵向或横向)、皮下气泡及非金属夹杂物,它们都会在线材表面造成裂纹。
连铸坯上的针孔如不消除,经轧制被延伸、氧化、溶解就会造成成品的线状发纹。
针孔是连铸坯的主要缺陷之一,不显露时很难检查出来,应特别予以注意。
高碳钢线材轧制后冷却速度过快,也能造成成品裂纹,还会出现横向裂纹。
轧后控冷不当形成的裂纹无脱碳现象,裂纹中一般无氧化铁皮。
另外坯料清理不好也会产生此类问题。
轧制过程中形成裂纹的原因主要有:1)轧槽不合适,主要是尖角和尺寸有问题,表面太粗糙或损坏。
2)粗轧前几道导卫的划伤。
3)粗大的氧化铁皮轧进轧件,通常在粗轧前几道产生。
4)导卫尺寸太大。
若产生裂纹,应从以下方面检查,排除故障:1)高压水除鳞是否正常,轧机轧辊的冷却水路是否堵塞或偏离轧槽。
2)导卫是否偏离轧制线,有否氧化铁皮堵塞在某个导卫中。
3)轧槽是否过度磨损或因处理堆钢事故时损伤了轧槽。
4)精轧机是否有错辊,导卫是否对中及尺寸是否对应于所轧的规格。
2.2 折叠线材表面沿轧制方向平直或弯曲的细线,以任意角度渗入线材的表面内,在横断面上与表面呈小角度交角状的缺陷多为折叠[1]。
通常折叠较长,但亦有不连续的,在线材的长度方向上都有分布。
折叠的两侧伴有脱碳层或部分脱碳层,折叠中间常存在氧化铁夹杂。
坯料中如存在缩孔、偏析、夹杂等缺陷,或者坯料修整不好都有可能产生此类折叠缺陷。
在轧制中可能产生折叠的原因有:孔型中过充满、欠充满;机架间张力太大;导卫对中不好可出现单侧充满从而造成折叠;轧机调整不当,轧件尺寸不符合工艺要求或导卫磨损严重;坯料加热温度不均匀。
若产生折叠,应从以下方面检查,排除故障:检查轧辊冷却,粗轧机中氧化铁皮堆积过多可能产生间断折叠;是否有某个导卫偏离了轧制中心线引起过充满;导卫故障,检查滑动导卫内部是否有异物堆积或磨损超标,滚动导卫中导辊是否正常;轧件尺寸是否符合工艺要求,是否过充满或欠充满;检查张力情况;检查坯料出炉温度,沿坯料长度上温度不均也可导致间断性过充满。
热轧带钢缺陷图谱
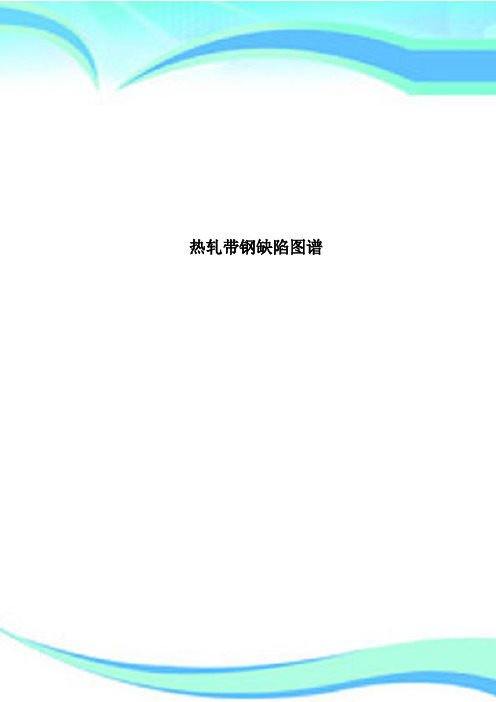
热轧带钢缺陷图谱————————————————————————————————作者: ————————————————————————————————日期:ﻩ热轧带钢外观缺陷Visual Defects inHot Rolled Strip 2.1 不规则表面夹杂(夹层)(IrregularShells)【定义与特征】板带钢表面的薄层折叠,缺陷常呈灰白色,其大小、形状不一,不规则分布于板带钢表面。
【产生原因】板坯表面或皮下有非金属夹杂,这些夹杂在轧制过程中被破碎或暴露而形成夹层状折叠。
【预防与纠正】优化炼钢、精炼工艺,提高钢质纯净度。
【鉴别与判定】肉眼检查,钢板和钢带不得有夹层。
2.2 带状表面夹杂(夹层)(Seams)【定义与特征】板带钢表面的夹杂呈线状或带状不规则地沿轧向分布,有时以点状或舌状逐渐消失。
【产生原因】板坯皮下的夹杂在轧制出现剧烈延伸、破裂而造成。
【预防与纠正】优化炼钢、精炼工艺,提高钢质纯净度。
【鉴别与判定】肉眼检查,钢板和钢带不得有夹层。
2.3 气泡(Blisters)【定义与特征】板带钢表面凸起内有气体,分布无规律,有闭口气泡和开口气泡之分。
【产生原因】板坯由于大量气体在凝固过程中不能逸出,被封闭在内部而形成气体夹杂。
在热轧时,空洞与孔穴被拉长,并随着轧材厚度减薄,被带至产品的表面或边部。
最终,高的气体压力使产品表面或边部出现圆顶状的凸起物或挤出物。
【预防与纠正】优化精炼工艺,保证吹氩时间,使钢水搅拌均匀,避免气体残留;保证中间包烘烤时间;保护渣要符合工艺要求,避免受潮。
【鉴别与判定】肉眼检查,钢板和钢带不得有气泡。
2.4 结疤(重皮)(Scabs)【定义与特征】以不规则的舌状、鱼鳞状、条状或M状的金属薄片分布于带钢表面。
一种与带钢基体相连;另一种与带钢基体不相连,但粘合到表面上,易于脱落,脱落后形成较光滑的凹坑。
【产生原因】由于板坯表面有结疤、毛刺,轧后残留在带钢表面。
冷轧缺陷图谱

精心整理目录冷轧卷缺陷辊印 (2)粘结 (3)咯伤 (4)边裂 (5)平整纹 (7)划伤 (8)05011.图例2.陷;②平整辊印与轧机辊印的区分:平整辊印伤疤处无粗糙度且发亮;轧机辊印伤疤处发暗,有一定的粗糙度。
3.产生原因及危害①轧钢辊表面受损;②轧辊表面粘有异物;③退火过程产生氧化皮后,脱落粘附在平整机轧辊上,平整时产生;④生产过程中其它辊面受损。
危害:①外观不良,加工(冲压)时易发生破裂;②影响镀层效果。
4.5.05021.图例2.②一般粘结分三种:月牙状、折皱状、以及牡丹花状,一般存在于罩式炉的生产中才会产生此缺陷3.产生原因及危害①板形不良②轧机卷取张力过大③退火冷却速度过快④退火前钢卷边部受冲击危害:外观不良,加工(冲压)时易发生破裂4.预防及消除方法①保证前工序板形良好;②退火工艺周期的适当调整;轧机的卷取张力的调整,以及根据轧钢过程中材质和5.05031.图例2.3.①生产过程中各辊上粘有凸起的异物引起;②钢卷摆放位置有异物,导致产生;③小车压痕;④行车吊钩撞击后产生对产品的影响。
危害:①外观不良,镀层后更加明显;②制造用面板无法使用。
4.预防及消除方法①生产过程中对辊面的检查,发现不良及时处理;②钢卷应搬运在适当的优越位置(放置位置环境良好);③对操作工教育,提高操作水平;5.05041.图例2.3.③在酸洗过程中,带钢跑偏或浪形严重导致边部与设备摩擦,边部间断轻折边,经冷轧后边部形成锯齿状;④带钢成分异常;危害:①对产品的外观有直接的影响;②边部无法镀层。
③后道工序生产过程中可能导致断带事故。
4.预防及消除方法①吊运的时候防止撞伤;②酸洗过程中,对中装置适当的调整避免跑偏事故;③严格控制带钢成分及原料卷形、板形缺陷。
5.05051.图例2.3.危害:①对产品的外观有直接的影响;②产品要冲压或深加工时很容易造成开裂。
4.预防及消除方法①应保持轧钢及平整压下量的均衡;②需保持工作辊的适当弯曲度及钢带的对中;③在酸洗过程中对钢带厚度实测,确认热轧的厚度是否均匀。
轧制缺陷及质量控制

轧制缺陷及质量控制一、引言轧制是金属加工中的一种重要工艺,用于将金属坯料通过轧机进行塑性变形,以获得所需的形状和尺寸。
然而,在轧制过程中,由于各种因素的影响,会产生一些缺陷,如裂纹、夹杂物、表面缺陷等,这些缺陷会严重影响产品的质量和性能。
因此,对轧制缺陷进行有效的控制和管理,是确保产品质量的关键。
二、轧制缺陷的分类1. 表面缺陷:包括轧痕、轧花、氧化皮、划伤等。
2. 内部缺陷:包括夹杂物、裂纹、孔洞等。
3. 尺寸偏差:包括厚度偏差、宽度偏差等。
三、轧制缺陷的原因分析1. 材料因素:原材料的质量和成份会直接影响轧制过程中的缺陷产生。
如含有夹杂物、氧化皮等。
2. 工艺参数:轧制过程中的轧制力、轧制速度、轧制温度等参数的控制不当,会导致缺陷的产生。
3. 设备状况:轧机的磨损、不平衡等问题会影响轧制质量。
4. 操作人员:操作人员的技术水平和经验也会对轧制质量产生影响。
四、轧制缺陷的质量控制方法1. 前期控制:在轧制前对原材料进行严格的检查和筛选,确保材料的质量符合要求。
2. 工艺参数控制:根据产品的要求和轧制材料的特性,合理设置轧制力、轧制速度、轧制温度等参数,以减少缺陷的产生。
3. 设备维护:定期对轧机进行检修和维护,确保设备的正常运行,减少设备因素对轧制质量的影响。
4. 操作人员培训:加强对操作人员的培训和技术指导,提高其对轧制过程中缺陷产生原因的认识和处理能力。
5. 检测方法:采用先进的无损检测技术,如超声波检测、磁粉检测等,对轧制产品进行全面的检测,及时发现和排除缺陷。
6. 质量管理体系:建立完善的质量管理体系,包括质量控制计划、质量检验记录、质量问题分析等,确保轧制产品的质量稳定可控。
五、案例分析某钢铁厂在轧制过程中,时常浮现轧制缺陷问题,导致产品质量不稳定,客户投诉频繁。
经过对生产过程的分析和改进,采取了以下措施:1. 强化原材料的筛选工作,严格控制夹杂物和氧化皮的含量。
2. 优化工艺参数,合理调整轧制力、轧制速度和轧制温度,降低缺陷的产生率。
热轧工序典型质量缺陷产生原因与预防措施
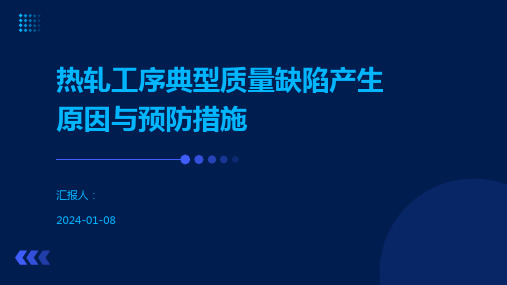
工艺参数设置不合理、工艺流程不完善等工艺因素是导致热轧工序质量缺陷的 重要原因。
详细描述
加热温度、轧制速度、道次压下量等工艺参数的设置对热轧产品的质量有显著 影响。工艺流程中的不合理之处,如冷却速度控制不当、轧制道次不足等,也 可能导致产品出现各种缺陷。
设备因素
总结词
设备故障、维护不当等设备因素是热轧工序中常见的质量缺 陷原因。
热轧工序典型质量缺陷产生 原因与预防措施
汇报人: 2024-01-08
目录
• 热轧工序简介 • 典型质量缺陷类型 • 产生原因分析 • 预防措施 • 案例分析 • 结论与展望
01
热轧工序简介
热轧工序的定义和重要性
定义
热轧工序是将金属材料在高温下 进行轧制的过程,目的是改变材 料的形状并获得所需的机械性能 。
钢材内部碳化物分布不均,导致钢材 性能不均一。
03
产生原因分析
原料因素
总结词
原料质量不均、成分偏析等原料因素 是导致热轧工序质量缺陷的主要原因 之一。
详细描述
原料的化学成分、微观组织结构、夹 杂物含量等因素可能影响热轧过程中 的流动性和变形行为,从而导致产品 出现裂纹、孔洞、夹杂等缺陷。
工艺因素
板形不良产生的原因可能是轧辊磨损严重、轧 制工艺参数设置不合理,或者是来料温度和厚 度波动过大。
厚度超差产生的原因可能是轧辊间隙调整不当 、轧制过程中张力控制不准确,或者是轧制润 滑条件不佳,导致金属流动不均匀。
预防措施实施效果评估
对于表面裂纹,通过优化轧制温 度和润滑条件,加强轧辊检查和 维护,可以显著减少裂纹的产生
2
针对这些质量缺陷,需要采取有效的预防措施, 如控制工艺参数、优化设备参数和加强质量检测 等。
轧制缺陷图谱、形成原因分析以及预防措施

缺陷名称纵裂Longitudinal Crack照片缺陷形貌及特征:缺陷形貌及特征纵裂纹是距钢板边部有一定距离的沿轧制方向裂开的小裂口或有一定宽度的线状裂纹。
板厚大于20mm的钢板出现纵裂纹的机率较大。
缺陷成因:1. 板坯凝固过程中坯壳断裂,出结晶器后进一步扩展形成板坯纵向裂纹,在轧制过程中沿轧制方向扩展并开裂;2. 板坯存在横裂,在横向轧制过程中扩展和开裂形成。
预防:防止纵列纹产生的有效措施是使板坯坯壳厚度均匀,稳定冶炼,连铸工艺是减少纵裂纹产生的关键推荐处理措施:1. 深度较浅的纵裂可采用修磨去除。
2. 修磨后剩余厚度不满足合同要求的钢板可采用火切切除、改规的方法,由于纵裂有一定长度,一般不采用焊补的方法挽救;3. 纵裂面积较大时钢板可直接判次或判废可能混淆的缺陷1. 边部折叠2. 边部线状缺陷缺陷名称横裂Transverse Crack缺陷形貌及特征:缺陷形貌及特征:裂纹与钢板轧制方向呈30°~90°夹角,呈不规则的条状或线状等形态,有可能呈M或Z型,横向裂纹通常有一定的深度。
缺陷成因:板坯在凝固过程中,局部产生超出材料迁都极限的拉伸应力导致板坯横裂,在轧制过程中扩展和开裂形成。
有可能是板坯振痕过深,造成钢坯横向微裂纹;钢坯中铝,氮含量较高,促使AIN沿奥氏体晶界析出,也可能诱发横裂纹;二次冷却强度过高也会造成板坯上的横裂预防:1. 减少板坯振痕;2. 控制板坯表面温度均匀并尽量减少板坯表面和边部的温度差;3. 根据钢中不同合力选用保护渣;4. 合理控制钢中的铝、氮含量。
推荐处理措施:1. 深度较浅的横裂可用修磨的方法去除;2. 修磨后剩余厚度不满足合同要求的钢板可采用厚度改规或切除缺陷后改尺的方法;3. 缺陷面积较大时钢板可直接判次或判废;可能混淆的缺陷1. 夹渣2. 折叠3. 星型裂纹缺陷名称边裂Edge Crack缺陷形貌及特征:边部裂纹是钢板边部表面开口的月牙型,半圆型裂口,通常位于钢板单侧或两侧100mm 范围内,一般沿钢板边部密集分布。
热轧卷缺陷图谱(勿删)
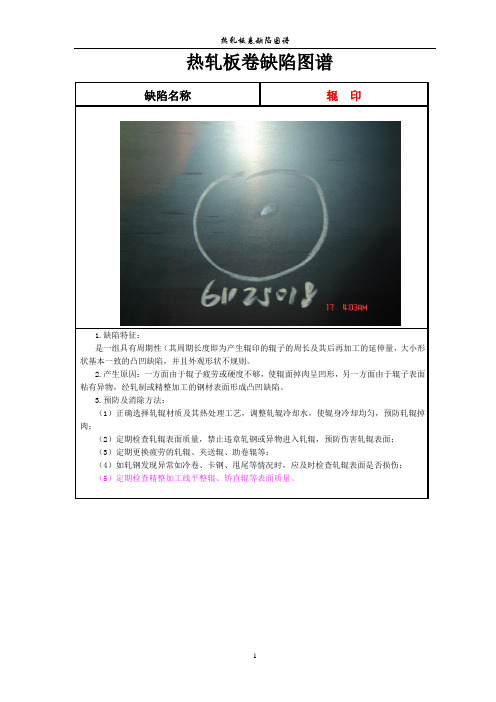
热轧板卷缺陷图谱热轧板卷缺陷图谱缺陷特征:是一组具有周期性(其周期长度即为产生辊印的辊子的周长及其后再加工的延伸量,大小形状基本一致的凸凹缺陷,并且外观形状不规则。
产生原因:一方面由于辊子疲劳或硬度不够,使辊面掉肉呈凹形,另一方面由于辊子表面粘有异物,经轧制或精整加工的钢材表面形成凸凹缺陷。
预防及消除方法:)正确选择轧辊材质及其热处理工艺,调整轧辊冷却水,使辊身冷却均匀,预防轧辊掉)定期检查轧辊表面质量,禁止违章轧钢或异物进入轧辊,预防伤害轧辊表面;)定期更换疲劳的轧辊、夹送辊、助卷辊等;)如轧钢发现异常如冷卷、卡钢、甩尾等情况时,应及时检查轧辊表面是否损伤;)定期检查精整加工线平整辊、矫直辊等表面质量。
缺陷特征:氧化铁皮一般粘附在钢板表面上,分布于板面局部或全部,铁皮有的疏松易脱落;不易脱落。
根据其外观形态不同可分为:红铁皮、线条状铁皮、木纹状铁皮、流线状铁皮、纺锤状铁皮、拖曳状铁皮或散沙状铁皮等。
产生原因:板坯加热制度不合理或加热操作不当生成较厚且较致密的铁皮,除鳞时难以除尽,轧制时被压入钢板表面上;)由于高压除鳞水压力低、水咀堵塞、水咀角度安装不合理或操作不当等原因,使钢坯上的铁皮未除尽,轧制时被压入到钢板表面上。
)氧化铁皮在沸腾钢中发生较多,含硅较高的钢中易产生红铁皮。
缺陷图片缺陷特征:沿钢板的轧制方向呈现高低起伏的波浪形的弯曲。
根据分布的部位不同,分为中间浪、单边浪和双边浪。
产生原因:)辊形曲线不合理,轧辊磨损不均匀;)压下量分配不合理;)轧辊辊缝调整不良或轧件跑偏;缺陷特征:钢卷端部不齐,呈面包状称塔形。
卷边上下错动称卷边错动。
产生原因:)卷取机张力设定不合理;)卷取机前侧导板、夹送辊、助卷辊调整不当;)带钢进卷取机时不对中,带钢跑偏;)带钢存在较大的镰刀弯或板型不良;)卷取机卸卷时将钢卷头部曳出。
缺陷特征:钢卷未卷紧,层与层之间有间隙称松卷。
产生原因:)卷取张力设定不合理;)带钢有严重浪形或因卷取机故障带钢在辊道上温度降低变形;)打捆机故障打捆不紧或吊运过程中断带;)卷取完毕后,因故卷筒反转等。
冷轧板带缺陷及消除方法

冷轧板带缺陷及消除方法浪形浪形是指沿轧制方向高低起伏呈波浪形弯曲,根据分布部位不同分为中间浪、单侧浪、双侧浪、二肋浪等。
浪形的大小是用单位长度内浪峰的高度来衡量的。
浪形发生在钢板边部称为边浪,钢板一侧有浪为单边浪,两侧有浪称为双边浪。
浪形发生在钢板中间的叫中间浪(如图1-25,1-26所示),发生在边部与中部之间的位置上称二肋浪。
如果波形周期性出现则称为周期浪。
各种浪形缺陷的形态、产生原因如表1-12所示表1-12浪形缺陷比较1、严格把好原料关,保证来料板形。
2、按轧制周期定期换辊。
3、合理调节弯曲与倾斜,分段冷却:(1)通过合理调节轧辊倾斜,改善或消除单边浪。
(2)对于双边浪,合理增大弯辊力改善或消除。
(3)合理减小弯辊力改善或消除中间浪。
(4)根据二肋浪产生部位正确选择分段冷却来改善或消除瓢曲瓢曲是指带钢中间呈凸形向上或向下鼓起,切成钢板时,四角向上翘起。
(一)产生原因:1、工作辊凸度太大,或在轧制时轧辊中间温度太高,使带钢中间延伸大于两边。
2、由于某种原因压下量变小,产生中心延伸大于两边。
3、原料瓢曲大,轧后不易消除。
4、板形调节不当。
(二)改善或消除措施:1、合理分配辊型,正确分配压下量。
2、精心操作,勤观察板形。
3、原料横向厚度公差应尽量小。
三辊印辊印是一种常见的缺陷,各工序都能产生。
一般由辊面凸凹缺陷引起,缺陷的部位确定并有周期性。
酸洗辊辊印主要是金属碎块粘在张力辊表面上,又压在带钢表面上产生,压印有规律性。
轧制辊印种类比较多,但其特点是周期出现,印坑形状大小相同。
周期长度L Y 与工作辊径D 有关,即:L Y = u 冗D在成品道次时u= l,其它道次可根据延伸情况计算出来。
按缺陷特点辊印可分为4 种形式:第一种是粘辊辊印。
它是由于轧辊表面粘有金属,从而在轧制时,在带钢表面形成压印。
其形状与粘有金属形式一致,多呈点状、条状或块状。
当原料有破边、折叠等缺陷进入轧机,或者穿带、甩尾时,辊缝不大,带钢与轧辊接触并相对滑动,造成金属粘于轧辊表面上,称做粘辊,如不磨除干净,就在轧制时造成辊印。
- 1、下载文档前请自行甄别文档内容的完整性,平台不提供额外的编辑、内容补充、找答案等附加服务。
- 2、"仅部分预览"的文档,不可在线预览部分如存在完整性等问题,可反馈申请退款(可完整预览的文档不适用该条件!)。
- 3、如文档侵犯您的权益,请联系客服反馈,我们会尽快为您处理(人工客服工作时间:9:00-18:30)。
缺陷名称纵裂Longitudinal Crack照片缺陷形貌及特征:缺陷形貌及特征纵裂纹是距钢板边部有一定距离的沿轧制方向裂开的小裂口或有一定宽度的线状裂纹。
板厚大于20mm的钢板出现纵裂纹的机率较大。
缺陷成因:1. 板坯凝固过程中坯壳断裂,出结晶器后进一步扩展形成板坯纵向裂纹,在轧制过程中沿轧制方向扩展并开裂;2. 板坯存在横裂,在横向轧制过程中扩展和开裂形成。
预防:防止纵列纹产生的有效措施是使板坯坯壳厚度均匀,稳定冶炼,连铸工艺是减少纵裂纹产生的关键推荐处理措施:1. 深度较浅的纵裂可采用修磨去除。
2. 修磨后剩余厚度不满足合同要求的钢板可采用火切切除、改规的方法,由于纵裂有一定长度,一般不采用焊补的方法挽救;3. 纵裂面积较大时钢板可直接判次或判废可能混淆的缺陷1. 边部折叠2. 边部线状缺陷缺陷名称横裂Transverse Crack缺陷形貌及特征:缺陷形貌及特征:裂纹与钢板轧制方向呈30°~90°夹角,呈不规则的条状或线状等形态,有可能呈M或Z型,横向裂纹通常有一定的深度。
缺陷成因:板坯在凝固过程中,局部产生超出材料迁都极限的拉伸应力导致板坯横裂,在轧制过程中扩展和开裂形成。
有可能是板坯振痕过深,造成钢坯横向微裂纹;钢坯中铝,氮含量较高,促使AIN沿奥氏体晶界析出,也可能诱发横裂纹;二次冷却强度过高也会造成板坯上的横裂预防:1. 减少板坯振痕;2. 控制板坯表面温度均匀并尽量减少板坯表面和边部的温度差;3. 根据钢中不同合力选用保护渣;4. 合理控制钢中的铝、氮含量。
推荐处理措施:1. 深度较浅的横裂可用修磨的方法去除;2. 修磨后剩余厚度不满足合同要求的钢板可采用厚度改规或切除缺陷后改尺的方法;3. 缺陷面积较大时钢板可直接判次或判废;可能混淆的缺陷1. 夹渣2. 折叠3. 星型裂纹缺陷名称边裂Edge Crack缺陷形貌及特征:边部裂纹是钢板边部表面开口的月牙型,半圆型裂口,通常位于钢板单侧或两侧100mm 范围内,一般沿钢板边部密集分布。
照片:缺陷形貌及特征:星形裂纹是钢板表面呈不闭合多边形或簇状的裂口,由于其分布类似于多边形的星星形状,故此得名。
星形裂纹深浅不一,但通常清晰可见,在钢板表面的分布位置较为复杂。
一般低合金钢种比碳素钢种更易发生星形裂纹,钢板越厚,出现星形裂纹的机率也越大可能成因:星形裂纹大多出现在锰、硅、铜、铝含量的钢种,由于硅酸盐类夹杂物和铜原子在奥氏体晶界上的富集降低了晶界的强度,从而在板坯上形成星形裂纹。
在板坯加热和轧制过程中进一步扩展和演变成钢板表面的星形裂纹预防:1. 采用热装热送,减少铜原子的富集程度;2. 合理选用保护渣,控制结晶器给水温度;3. 防止板坯过热,过烧;推荐处理措施:1. 深度较浅的星形裂纹可修磨去除:2. 修磨后剩余厚度不满足合同要求的钢板可采用厚度改规或切除缺陷后改尺的方法;3. 面积较大且较深的星形裂纹可直接判次或判废可能混淆的缺陷1. 横裂2. 龟裂缺陷名称龟裂Chap照片缺陷形貌及特征:龟裂是钢板表面呈龟贝状(网纹状)的裂口,一般长度较短,多产生在碳含量或合金含量较高的钢种;缺陷成因:1. 板坯低温火焰清理时,局部温度骤升形成的热应力或冷却过程中产生的组织应力,使板坯表面炸裂;2. 板坯表面固有的网状裂纹在轧制过程中扩展和开裂;3. 板坯加热局部过热并出现较深的脱碳层,在轧制过程中因塑性降低而开裂。
预防:1. 控制板坯火焰清理时板坯余温;2. 防止板坯加热过烧推荐处理措施:1. 较浅的龟裂可修磨去除:2. 修磨后剩余厚度不满足合同要求的钢板可采用厚度改规或切除缺陷后改尺的方法;若合同允许焊补,对于裂纹数量和面积较小的钢板可进行焊补挽救;可能混淆的缺陷:星形裂纹缺陷名称夹渣Slag 照片照片缺陷形貌及特征:在钢板的切割断面上呈现一条或多条平行的缝隙,即钢板局部存在基本平行于钢板表面的未焊合界面。
缺陷成因:1. 板坯中的夹杂物,在轧制后延展为片状并逐渐长大,直至形成分层;2. 板坯中心区域低溶质物质富集,中心偏析带内存在硫化物聚集,形成夹杂性裂纹;3. 板坯内部本身存在内裂,分层,疏松或缩孔等缺陷,轧制后形成分层;4. 板坯氢含量较高,轧制后气体释放不尽,形成氢致裂纹。
预防:1. 炼钢过程中控制钢水的纯净度,减少夹杂物或促使夹杂物充分上浮;2. 控制钢水中的气体含量,控制中间包和覆盖剂的水份含量;推荐处理措施:1. 分层如果分布密集或具有一定的面积应作判次或判废处理;2. 夹杂性分层如果分布比较弥散,且不具有明显的长度和宽度,一般不影响使用。
为保证钢板的质量,一般均用切除的方法消除分层缺陷。
可能混淆的缺陷切边不足缺陷名称翘皮Shell照片缺陷形貌及特征:翘皮是指钢板表面出现材料搭叠区域,其形状通常呈舌状或山峰状,有闭合的,有张开的,缺陷根部与钢板基体相连。
缺陷成因:1. 板坯本身的皮下气泡在轧制过程破裂延伸造成;2. 连铸过程中非金属夹杂物卷入板坯,在轧制过程中夹杂物破碎而形成;3. 板坯表面有较深的沟槽,或板坯清理表面缺陷后形成的沟槽宽深比过小,在轧制过程中由于表面延伸而形成双金属搭叠;预防:1. 稳定连铸工艺,提高坯料质量;2. 严格遵守板坯清理的有关规定;推荐处理措施:1. 深度较浅的翘皮可用修磨去除,修磨后如果厚度低下限可采用厚度改规或切除缺陷后改尺的方法;2. 严重的翘皮可直接采用切除后改尺的方法;可能混淆的缺陷折叠缺陷名称端部折叠Head fold 照片照片缺陷形貌及特征:边部折叠是指钢板单侧或双侧边部的多条平行于钢板轧制方向的表面裂口,通常呈连续或断续密集分布,表面裂口一般略有弯曲。
展宽比大的钢板边部折叠离开边部的距离较大。
可能成因:1. 板坯边部清理形状不佳,板坯断面有裂纹,在轧制过程中形成边部折叠。
2. 展宽轧制过程中钢板的翘头扣头在转钢90度后被卷入钢板边部,形成距边部一定距离的表面裂口缺陷。
预防:1. 严格按规定进行板坯边部清理。
2. 对展宽比较大的钢板合理控制展宽轧制过程中的翘扣头。
3. 控制板坯加热后的上下表面温差。
推荐处理措施:1. 边部折叠深浅不一,较浅的缺陷可通过修磨去除,较深的需要切除并可能造成钢板该规。
2. 发现批量缺陷且可能导致改规时,可根据缺陷距边的距离通知轧钢适当增加宽度余量。
3. 控制双边剪跑偏可以减少切除缺陷后改规的可能性。
可能混淆的缺陷:1. 边部线状缺陷2. 边裂缺陷名称边部线状缺陷Edge line shape defect照片缺陷形貌及特征:边部线状缺陷是指钢板单侧或双侧边部平行于轧制方向的呈笔直线状的表面裂口,缺陷通常有一定的长度,也有可能与轧制方向形成一个较小的夹角。
展宽比大的钢板边部线状缺陷离开边部的距离较大。
可能成因:1. 展宽轧制过程中钢板的翘扣头在转钢90度后被卷入钢板边部,形成距边部一定的表面裂口缺陷。
2. 板坯边部清理形状不佳,板坯断面有裂纹,在轧制过程中形成边部线状缺陷。
预防:1. 对展宽比较大的钢板合理控制展宽轧制过程中的翘扣头。
2. 严格按规定进行板坯边部清理3. 控制板坯加热后的上下表面温差。
推荐处理措施:1. 较浅的边部线状缺陷可通过修磨去除,较深的需要切除并可能造成钢板改规。
2. 发现批量缺陷且可能导致改规时,可根据缺陷距边的距离通知轧钢适当增加宽度余量。
3. 控制双边剪跑偏可以减少切除缺陷后改规的可能性可能混淆的缺陷:1. 边部折叠2. 边裂缺陷名称一次氧化铁皮Rolling scale照片缺陷形貌及特征:一次氧化铁皮是指板坯加热过程中生成的氧化铁皮在轧制过程中被压入钢板表面的一种缺陷,颜色通常呈灰褐色,其成分为F e3O4,形态呈小斑点,大块斑痕或带状条纹等形式,通常伴有铁氧照片缺陷形貌及特征:二次氧化铁皮是指钢板在轧制过程中生成的氧化铁皮被压入钢板表面的一种缺陷,颜色通常呈红棕色,其成分为F e2O3或F e O,呈散布的点状,块状或条状分布。
缺陷成因:轧机除鳞系统压力不足,喷嘴堵塞或水泵跳电等原因,轧制过程中生成的二次氧化铁皮未能得到有效的清除,造成部分氧化铁皮呈片状或块状被压入钢板本体预防:提高轧机除鳞系统的除鳞效能。
推荐处理措施:1. 对缺陷程度进行确认,不满足合同要求的缺陷可通过修磨去除,当修磨处剩余厚度不满足合同要求时可采取厚度改规或切除缺陷后改尺的方法。
2. 面积较大或深度较深的缺陷也可直接采用切除缺陷改尺的方法或直接判废次。
3. 出现批量氧化铁皮时应及时通知轧钢。
可能混淆的缺陷:一次氧化铁皮缺陷名称氧化铁皮麻坑Scale pit照片缺陷形貌及特征:氧化铁皮麻坑是指钢板表面局部或成片的粗糙面,在钢板抛丸后比较多见。
抛丸前氧化铁皮麻坑附近常伴有氧化物。
缺陷形貌及特征:氧化铁渣压入是钢板表面点状或块状不规则分布的铁氧化物压入,缺陷颜色一般呈黑色,缺陷表面通常高于钢板本体。
缺陷成因:1. 除鳞时从板面上清除的氧化铁皮粘附或堆积在轧机导板、护板、切水板等部位,当受到外力振动时这些氧化铁渣掉落到钢板表面并被压入钢板本体。
2. 氧化铁皮粘附在轧辊表面并被压入钢板。
3. 钢板有翘扣头,在轧制过程中卷入轧机导板外的氧化铁渣并被压入钢板下表面。
预防:1. 定期检查并清理轧机机架各部分堆积的氧化铁渣。
2. 轧制过程中利用除鳞水冲洗,防止氧化铁渣堆积。
推荐处理措施:通常可修磨去除,当修磨处最小厚度不满足合同要求时可切除缺陷改尺或厚度改规可混淆的缺陷:夹渣缺陷名称氧化铁渣麻坑照片缺陷形貌及特征:氧化铁渣麻坑是指钢板表面块状的底部粗糙的凹坑,有时在附近有残留的氧化铁渣,形状各异。
缺陷成因:1. 除鳞时从板面上清除的氧化铁皮粘附或堆积在轧机导板、护板、切水板等部位,当受到外力振动时这些氧化铁渣掉落到钢板表面并被压入钢板本体。
2. 氧化铁皮粘附在轧辊表面并被压入钢板。
3. 钢板有翘扣头,在轧制过程中卷入轧机导板外的氧化铁渣并被压入钢板下表面。
4. 在轧后冷却过程中钢板上的氧化铁渣压入缺陷收缩脱落,或者由于受到外力振动导致钢板上的氧化铁渣压入脱落,形成底面粗糙的麻坑。
预防:1. 定期检查并清理轧机机架部分的氧化铁渣。
2. 轧制过程中利用除鳞水冲洗,防止氧化铁渣堆积。
推荐处理措施:通常可修磨去除,修磨处最小厚度不满足合同要求时可切除缺陷改尺或厚度改规。
可混淆的缺陷:凹坑夹渣压入缺陷名称轧制凹坑Rolling pit照片缺陷形貌及特征:轧制凹坑是指钢板表面点状或块状的热态凹坑,轧制凹坑分布无规则,缺陷形状各异,凹照片缺陷形貌及特征:轧制毛刺压入是指钢板表面呈细条状的热态压痕,缺陷形状通常呈弯曲的细条状,缺陷底面有高温下形成的氧化铁膜,压痕底面的颜色与钢板本体相近缺陷成因:钢板轧制过程中钢板与轧机设备刮擦,形成的毛刺被压入钢板表面。