冲裁工艺及冲裁模设计
第2章6-7节(冲裁工艺及冲裁模设计)
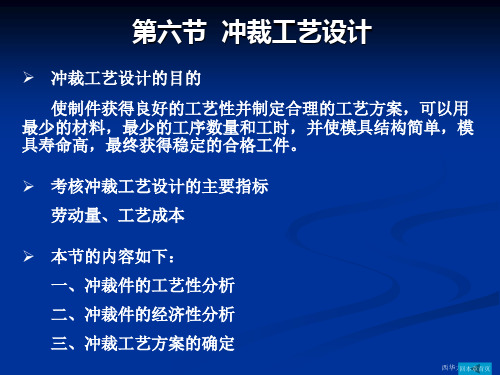
用途 薄件、平整要求高的零件、 薄件、平整要求高的零件、易分层的非金属件
西华大学 张晓洪
2、冲孔模 、
普通板坯冲孔模结构与落料模相似。 普通板坯冲孔模结构与落料模相似。 冲孔的多样性导致冲孔模有更多自己的特点。 冲孔的多样性导致冲孔模有更多自己的特点。
典型的冲孔模有: 典型的冲孔模有: (1)冲侧孔模 ) (2)单工序多凸模冲孔模 ) (3)导板式冲小孔模 )
西华大学 张晓洪
倒装复合模
冲制垫圈的复合冲裁模 适用条件 0.3mm以上低平直度要求件(刚性推件未压紧制件部分,卸 以上低平直度要求件(刚性推件未压紧制件部分, 以上低平直度要求件 料板也未压紧条料) 料板也未压紧条料) 特点 卸料板兼承料平面, 卸料板兼承料平面,冲前无法预压 凸凹模若直刃段长,则胀裂力大,须控制其最小壁厚 凸凹模若直刃段长,则胀裂力大, 条料废料部分: 条料废料部分:冲裁时有上下动作 改进 若上部改为弹性推件,则可加工 若上部改为弹性推件,则可加工0.3mm以下的冲件 以下的冲件
西华大学 张晓洪
… … …冲裁件的形状和尺寸 冲裁件的形状和尺寸
6、孔径不能太小; 、孔径不能太小; 自由凸模的最小尺寸 带护套凸模的最小尺寸 最小孔间距
西华大学 张晓洪
(二)冲裁件的尺寸精度和表面粗糙度要求
冲裁件的经济精度:一般不高于 冲裁件的经济精度:一般不高于IT11,冲孔比落料高一级 , 1、冲裁件外形与内孔尺寸公差表 、 2、冲裁件两孔孔心距公差表 、 3、冲裁件断面表面粗糙度表 、 4、冲裁件断面允许的毛刺高度表 、
第六节
冲裁工艺设计的目的
冲裁工艺设计
使制件获得良好的工艺性并制定合理的工艺方案, 使制件获得良好的工艺性并制定合理的工艺方案,可以用 最少的材料,最少的工序数量和工时,并使模具结构简单, 最少的材料,最少的工序数量和工时,并使模具结构简单,模 具寿命高,最终获得稳定的合格工件。 具寿命高,最终获得稳定的合格工件。 考核冲裁工艺设计的主要指标 劳动量、 劳动量、工艺成本 本节的内容如下: 本节的内容如下: 一、冲裁件的工艺性分析 二、冲裁件的经济性分析 三、冲裁工艺方案的确定
冲裁工艺和冲裁模设计
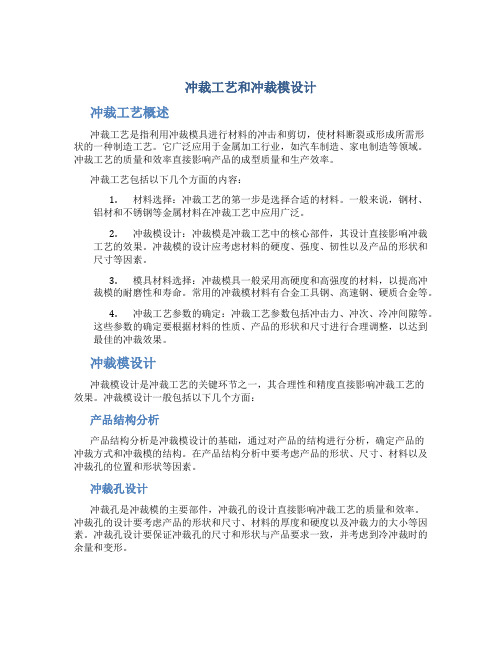
冲裁工艺和冲裁模设计冲裁工艺概述冲裁工艺是指利用冲裁模具进行材料的冲击和剪切,使材料断裂或形成所需形状的一种制造工艺。
它广泛应用于金属加工行业,如汽车制造、家电制造等领域。
冲裁工艺的质量和效率直接影响产品的成型质量和生产效率。
冲裁工艺包括以下几个方面的内容:1.材料选择:冲裁工艺的第一步是选择合适的材料。
一般来说,钢材、铝材和不锈钢等金属材料在冲裁工艺中应用广泛。
2.冲裁模设计:冲裁模是冲裁工艺中的核心部件,其设计直接影响冲裁工艺的效果。
冲裁模的设计应考虑材料的硬度、强度、韧性以及产品的形状和尺寸等因素。
3.模具材料选择:冲裁模具一般采用高硬度和高强度的材料,以提高冲裁模的耐磨性和寿命。
常用的冲裁模材料有合金工具钢、高速钢、硬质合金等。
4.冲裁工艺参数的确定:冲裁工艺参数包括冲击力、冲次、冷冲间隙等。
这些参数的确定要根据材料的性质、产品的形状和尺寸进行合理调整,以达到最佳的冲裁效果。
冲裁模设计冲裁模设计是冲裁工艺的关键环节之一,其合理性和精度直接影响冲裁工艺的效果。
冲裁模设计一般包括以下几个方面:产品结构分析产品结构分析是冲裁模设计的基础,通过对产品的结构进行分析,确定产品的冲裁方式和冲裁模的结构。
在产品结构分析中要考虑产品的形状、尺寸、材料以及冲裁孔的位置和形状等因素。
冲裁孔设计冲裁孔是冲裁模的主要部件,冲裁孔的设计直接影响冲裁工艺的质量和效率。
冲裁孔的设计要考虑产品的形状和尺寸、材料的厚度和硬度以及冲裁力的大小等因素。
冲裁孔设计要保证冲裁孔的尺寸和形状与产品要求一致,并考虑到冷冲裁时的余量和变形。
模具结构设计模具结构设计是指冲裁模的结构设计,包括上模、下模、定位销、导向销、顶出销等部件的位置和尺寸设计。
模具结构设计要考虑产品的形状和尺寸、冲裁力的大小以及模具的可靠性和耐磨性等因素。
模具结构设计应合理布置冲裁孔和模具部件,以提高冲裁工艺的质量和效率。
冲裁模材料选择冲裁模的材料选择是冲裁模设计的重要方面,合适的材料能够提高冲裁模的硬度、强度和耐磨性,延长冲裁模的使用寿命。
冲裁及冲裁模设计
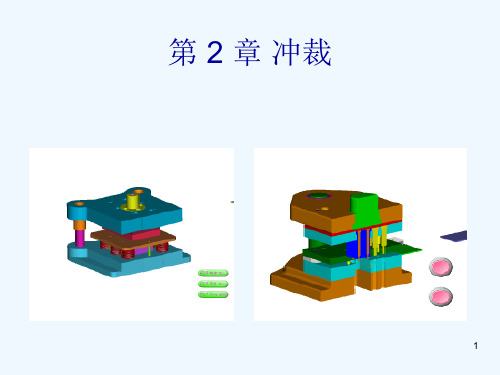
第 2 章 冲裁
2 -2 冲裁模具间隙
2.2.1 间隙对冲裁件质量的影响
冲裁件的质量:断面质量、尺寸精度 a 间隙对断面质量的影响 小间隙、合理间隙、大间隙情况下的剪切过程 断面特征值与间隙的关系图。
17
第 2 章 冲裁
2-2 冲裁模间隙
间隙对断面质量的影响
18
第 2 章 力、变形和冲裁件正常的断面状况 a)冲孔件 b)落料件
第 2 章 冲裁
2 -2 冲裁模具间隙
间隙的概念 模具凸凹模刃口缝隙间的距离。 单边间隙c、双边间隙z。 间隙对冲裁件的质量、模具寿命、冲裁力都有很大 的影响,是冲裁工艺和模具设计中的最重要的工艺参数。 2.2.1 间隙对冲裁件质量的影响 2.2.2 间隙对冲裁力的影响 2.2.3 间隙对模具寿命的影响 2.2.4 间隙的确定
12
第 2 章 冲裁
2-1 冲裁变形机理
2.1.5 断面特征
1)圆角带:冲裁过程中,纤维的弯曲与拉伸形成, 软材料圆角大。 2)光亮带:塑剪变形时,由于相对移动,凸凹模侧 压力将毛料压平形成的光亮垂直断面。
3)断裂带:刃口微裂纹受拉应力不断扩展形成的撕 裂面,导致断面粗糙并有斜度。 4)毛刺:由微裂纹位置与冲裁间隙等引起,是金属 拉断而形成的金属刺残留在冲裁件上
板 坯
F v 1
F v 2
F h 2
F h 2
F v 2
凹 模
板坯受力简图 Diagram of sheet metal under load
10
第 2 章 冲裁
2-1 冲裁变形机理
2.1.3 裂纹的形成与发展 裂纹产生的条件:当变形区的应变达到极限塑性应变值时, 就产生微裂纹 裂纹扩展的方向:沿着最大剪切应变速度的方向扩展 裂纹的成长过程:裂纹首先在低应力区产生,由于变形过 程中最大剪切应变的速度方向发生变化,使得新的裂纹不断产 生,旧裂纹的扩展不断停止,然后在旧裂纹的前端附近重新产 生新的裂纹,不断产生的微裂纹的根部汇成了一条主裂纹 极限塑性应变值除和材质外,还和应力状态、变形历史(损 伤程度)有关。
冲裁工艺与冲裁模设计

2.1 典型案例 (1)垫圈
垫圈是标准化的零件,具有通用性和互换性,材 料一般为普通碳素钢(如Q215),属于大批量生产。
t=1mm
(2)电机转子与电机定子 要求其具有较好的形状一致性,不存在(或存在
较小的)毛刺,材料一般为电工硅钢(如D31),属 于大批量生产。
(3)录音机机芯自停杆 材料一般为优质碳素结构钢(如10F),属于成批
录音机机芯暂停杆展开件(直对排)
录音机机芯暂停杆展开件(斜排)
2.5.3 材料利用率的计算
(1)条料宽度尺寸的确定 3
1)有侧压装置:B=(L+2b)-Δ
2 2)无侧压装置:B=(L+2b+C) –Δ
1
式中: L——制件垂直于送料方向的基本尺寸; Δ——条料的宽度公差(见表2-16); b——侧面搭边值; C——送料保证间隙: B≤100,C=0.5~1.0;B>100,C=1.0~1.5。
冲裁间隙是指冲裁模凸模与凹模刃口间缝隙的距离。
Z=Dp-Dd 式中
Z——冲裁间隙(mm); Dd——凹模刃口尺寸(mm); Dp——凸模刃口尺寸(mm)。
(1)间隙对冲裁件断面质量的影响 播放动画
间隙过小 间隙适合 间隙过大
(2)冲裁间隙对冲裁件尺寸精度的影响 冲裁件的尺寸偏差主要是由两个方面造成的:一是冲模的制造偏差,二是冲裁件实际尺寸
2.6.2 凸、凹模刃口尺寸计算的原则 ①落料尺寸取决于凹模尺寸,冲孔尺寸取决于凸模尺寸。
②根据磨损规律,设计落料模时,凹模基本尺寸应取制件尺寸公差范围内的较小尺寸;设计冲 孔模时,凸模基本尺寸则应取制件孔尺寸公差范围内的较大尺寸。
③冲裁间隙一般采用最小合理间隙值。 ④刃口尺寸的制造偏差方向,原则上单向注向金属实体内部。
冲裁工艺与模具设计-冲裁模设计步骤及实例
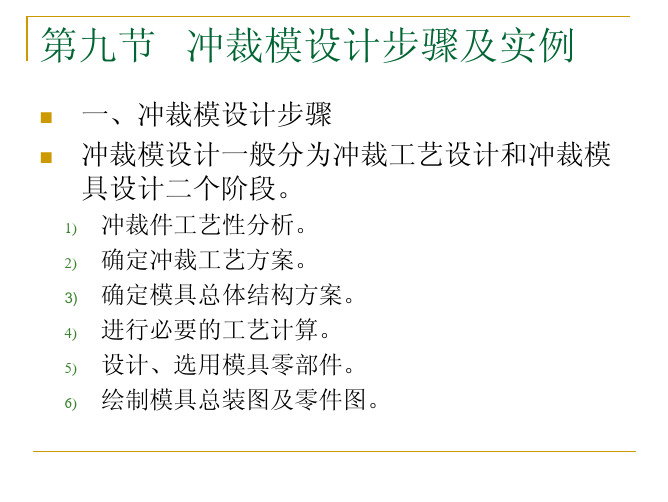
第2章 冲裁工艺及冲裁模设计
实际确定冲裁工艺方案时,通常可以先拟定出 几种不同的工艺方案,然后根据冲件的生产批 量、尺寸大小、精度高低、复杂程度、材料厚 度、模具制造、冲压设备及安全操作等方面进 行全面分析和研究,从中确定技术可行、经济 合理、满足产量和质量要求的最佳冲裁工艺方 案。
或级进冲裁; 冲件尺寸较大时,料薄时可用复合冲裁或单工序冲裁,料厚时受
压力机压力限制只宜采用单工序冲裁; 冲件上孔与孔之间或孔与边缘之间的距离过小时,受凸凹模强度
限制,不宜采用复合冲裁而宜用级进冲裁,但级进模轮廓尺寸受 压力机台面尺寸限制,所以级进冲裁宜适应尺寸不大、宽度较小 的异形冲件; 形状复杂的冲件,考虑模具的加工、装配与调整方便,采用复合 冲裁比级进冲裁较为适宜,但复合冲裁时其出件和废料清除较麻 烦,工作安全性和生产率不如级进冲裁。
《冲压工艺及模具设计》
第2(章1冲)裁模具工类艺型及冲裁模设计
模具类型主要是指单工序模、复合模、级进模三种。有些单件试 制或小批量生产的情况下,也采用简易模或组合模。
模具类型应根据生产批量、冲件形状与尺寸、冲件质量要求、材 料性质与厚度、冲压设备与制模条件、操作与安全等因素确定。
(2)操作与定位方式
《冲压工艺及模具设计》
第2章 冲裁工艺及冲裁模设计
4 进行必要的工艺计算 在冲裁工艺与模具结构方案确定以后,为了进
一步设计模具零件的具体结构,应进行以下有 关工艺与设计方面的计算:
《冲压工艺及模具设计》
第2(章1冲)裁排工样艺设及计冲与裁计模算设计 根据冲件形状特征、质量要求、模具类型与结构方 案、材料利用率等方面因素进行冲件的排样设计。设 计排样时,在保证冲件质量和模具寿命的前提下,主 要考虑材料的充分利用,所以,对形状复杂的冲件, 应多列几种不同排样方案 (特殊形状件可用纸板按冲 件比例作出样板进行实物排样),估算材料利用率, 比较各种方案的优缺点,选择出最佳排样方案。 排样方案确定以后,查出搭边值,根据模具类型和定 位方式画出排样图,计算条料宽度、进距及材料利用 率,并选择板料规格,确定裁板方式 (纵裁或横 裁),进而确定条料长度,计算一块条料或整块板料 的材料利用率。
冲裁工艺与冲裁模的设计
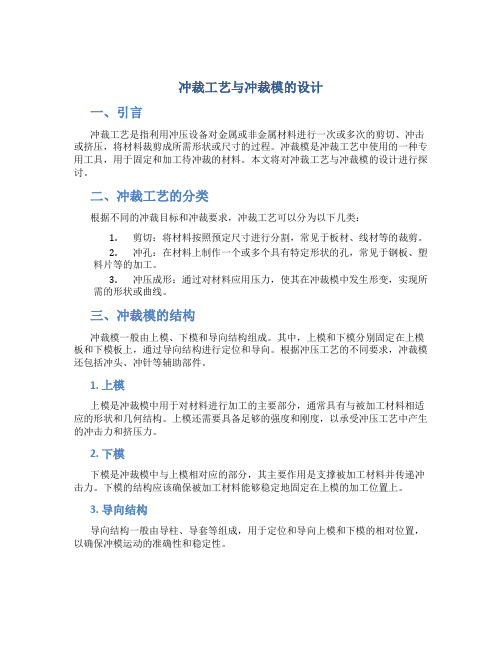
冲裁工艺与冲裁模的设计一、引言冲裁工艺是指利用冲压设备对金属或非金属材料进行一次或多次的剪切、冲击或挤压,将材料裁剪成所需形状或尺寸的过程。
冲裁模是冲裁工艺中使用的一种专用工具,用于固定和加工待冲裁的材料。
本文将对冲裁工艺与冲裁模的设计进行探讨。
二、冲裁工艺的分类根据不同的冲裁目标和冲裁要求,冲裁工艺可以分为以下几类:1.剪切:将材料按照预定尺寸进行分割,常见于板材、线材等的裁剪。
2.冲孔:在材料上制作一个或多个具有特定形状的孔,常见于钢板、塑料片等的加工。
3.冲压成形:通过对材料应用压力,使其在冲裁模中发生形变,实现所需的形状或曲线。
三、冲裁模的结构冲裁模一般由上模、下模和导向结构组成。
其中,上模和下模分别固定在上模板和下模板上,通过导向结构进行定位和导向。
根据冲压工艺的不同要求,冲裁模还包括冲头、冲针等辅助部件。
1. 上模上模是冲裁模中用于对材料进行加工的主要部分,通常具有与被加工材料相适应的形状和几何结构。
上模还需要具备足够的强度和刚度,以承受冲压工艺中产生的冲击力和挤压力。
2. 下模下模是冲裁模中与上模相对应的部分,其主要作用是支撑被加工材料并传递冲击力。
下模的结构应该确保被加工材料能够稳定地固定在上模的加工位置上。
3. 导向结构导向结构一般由导柱、导套等组成,用于定位和导向上模和下模的相对位置,以确保冲模运动的准确性和稳定性。
4. 冲头和冲针冲头和冲针是一些特殊冲裁工艺中常用的辅助部件。
冲头一般是用于在材料上打孔、压印等操作,而冲针常用于冲切较薄材料或特殊形状的材料。
四、冲裁模的设计原则在进行冲裁模的设计时,需要考虑以下几个原则:1.结构合理:冲裁模的结构应该能够满足冲裁工艺的要求,并能够方便材料的定位和加工。
2.强度与刚度:冲裁模需要具备足够的强度和刚度,以承受冲击力、挤压力等工艺中产生的载荷。
3.导向准确:冲裁模的导向结构应该具备高精度的定位和导向能力,以确保冲裁过程的准确性和稳定性。
第二章 冲裁工艺与冲裁模设计

线表示冲压位置。
第二章 冲裁工艺与冲裁模设计
零件形状不同材料利用情况的对比
第二章 冲裁工艺与冲裁模设计
第二章 冲裁工艺与冲裁模设计
第六节 冲裁力和压力中心的计算
一、冲裁力的计算
冲裁力:冲裁过程中凸模对板料施加的压力。
用普通平刃口模具冲裁时,冲裁力F一般按下式计算:
F KLt b
注: F——冲裁力; L——冲裁周边长度; t——材料厚度; b——材料抗剪强度; K——系数。一般取K=1.3
三、压力机公称压力的确定
压力机的公称压力必须大于或等于各种冲压工艺力的总和Fz
采用弹性卸料装置和下出料方式的冲裁模时: FZ F FX FT
采用弹性卸料装置和上出料方式的冲裁模时:
FZ F FX FD
采用刚性卸料装置和下出料方式的冲裁模时: FZ F FT
第二章 冲裁工艺与冲裁模设计
第二章 冲裁工艺与冲裁模设计
一、材料的合理利用(续)
2.提高材料利用率的方法(续)
减少工艺废料的有力措施是:
设计合理的排样方案; 选择合适的板料规格和合理的裁板法 (减少料头、料尾和边余料); 利用废料作小零件(如表2.5.1中的混合排样)等。
利用结构废料的措施有:
当材料和厚度相同时,在尺寸允许的情况下,较小尺寸的冲 件可在较大尺寸冲件的废料中冲制出来。
第二章 冲裁工艺与冲裁模设计
内容简介: 冲裁是最基本的冲压工序。
在分析冲裁变形过程及冲裁件质量影响因素的基础上, 介绍冲裁工艺计算、工艺方案制定和冲裁模设计。涉及冲 裁变形过程分析、冲裁件质量及影响因素、间隙确定、刃 口尺寸计算原则和方法、排样设计、冲裁力与压力中心计 算、冲裁工艺性分析与工艺方案制定、冲裁典型结构、零 部件设计及模具标准应用、冲裁模设计方法与步骤等。
第二章冲裁工艺与冲裁模设计

7.冲压设备选择 冲压设备选择关系到其合理使用、安全、产
品质量、模具寿命、生产效率及成本等。 设备类型的选择主要取决于冲压的工艺要求
和生产批量。设备选择主要包括设备类型和规格 两个方面。
设备规格主要取决于冲压力,变形功、模具 闭合高度和模板平面轮廓尺寸等。
2020/7/7
8.凸、凹模结构设计 根据冲件的形状和尺寸,冲模的加工以及装
(2)级进工艺
(3)复合工艺 即采用一副复合模一次冲裁完成。
2020/7/7
分析比较: (1)单工序工艺:模具结构简单,制造成本较 低,但制件内外形的位置精度难以得到保证,且 所占用设备及工人较多,生产效率低。
(2)级进工序工艺:制件内外形位置精度较易 得到保证,易于实现自动化生产,生产效率高, 但模具结构较复杂,制造成本较高。
冲压件上未注公差尺寸,要根据工件的公 差等级,进行公差标注。
标准步骤: 1.根据冲压件的公差等级与基本尺寸,查找冲压
基准件公差数值表,找到对应的公差,一般采 取单性偏差;
2020/7/7
2.判断该尺寸的偏差方向; 采用“入体原则”、可先画出该冲压件的假
想磨损图。所示工件的假想磨损图用双点划线画 出,再根据以下方法进行判断。如该尺寸磨损后 变小为负偏差;变大为正偏差;不变则为正负偏 差。
案例分析:电机定子 工序性质: 冲孔、落料
2020/7/7
案例分析:机芯自停杆 工序性质: 冲孔、落料
2020/7/7
案例分析:电位器接线片 工序性质: 落料
2020/7/7
(2)基本工序的数目 案例分析:
案例1为3个; 案例2和案例3为2个; 案例4为1个。
(3)基本工序的顺序 案例分析:
- 1、下载文档前请自行甄别文档内容的完整性,平台不提供额外的编辑、内容补充、找答案等附加服务。
- 2、"仅部分预览"的文档,不可在线预览部分如存在完整性等问题,可反馈申请退款(可完整预览的文档不适用该条件!)。
- 3、如文档侵犯您的权益,请联系客服反馈,我们会尽快为您处理(人工客服工作时间:9:00-18:30)。
冲裁工艺及冲裁模设计一、填空题1. 冲裁既能够直截了当冲制________,又能够为其他__________制备毛坯。
2.一样来讲,冲裁工艺要紧是指_____和_____工序。
3.冲裁变形过程大致可分为_______、________、________三个时期。
4.冲裁件的切断面由______、______、_______、_____四个部分组成。
5.光亮带是紧挨圆角带并与________的光亮部分,它是在塑性变形过程中凸模与凹模挤压切入材料,使其受到_______和________的作用而形成的。
6.冲裁毛刺是在刃口邻近的側面上材料显现________时形成的。
7.塑性差的材料,断裂倾向严峻,_______增宽,而________所占比例较少,毛刺和圆角带____;反之,塑性好的材料,光亮带__________。
8.冲裁凸模和凹模之间的________,不仅对冲裁件的质量有极重要的阻碍,而且还阻碍模具_____、_______、______和推件力等。
9.冲裁间隙越大,冲裁件断面光亮带区域越_____,毛刺越_____;断面上显现二次光亮带是因间隙太_____而引起的。
10.阻碍冲裁件毛刺增大的缘故是________、_______大。
11.冲裁件的尺寸精度是指冲裁件的_____________的差值,差值______,则精度_______。
12.所选间隙值的大小,直截了当阻碍冲裁件的_____和_______精度。
13.阻碍冲裁件尺寸精度的因素有两大方面,一是_____________,二是冲裁终止后冲裁件相关于________尺寸的偏差。
阻碍冲裁件尺寸精度的因素有______、材料______、工件的__________、材料的_______等,其中______起主导作用。
14.当间隙较大时,冲裁后因材料的弹性回复使____________凹模尺寸;冲孔件的孔径_____________。
15.当间隙较小时,冲裁后因材料的弹性回复使落料件尺寸__________,冲孔件的孔径________。
16.冲模的制造精度______,则冲裁件的精度_____。
17.冲裁间隙的数值,等于_______与_______刃口部分尺寸之差。
18.在设计和制造新模具时,应采纳______的合理间隙。
19.合理间隙值和许多因素有关,其要紧受__________和__________因素的阻碍。
20.在冲压实际生产中,要紧依照冲裁件的___________、__________和__________三个因素给间隙规定一个范畴值。
21.冲孔时,凸模刃口的尺寸应______或________冲孔件的______极限尺寸。
22.落料件的尺寸与_____刃口尺寸相等,冲孔件的尺寸与_______尺寸相等。
23.冲裁模凸模和凹模的制造公差与冲裁件的________、_________、刃口尺寸磨损有关。
24.落料时,因落料件的大端尺寸与凹模尺寸相等,应先确定凹模尺寸,即以凹模尺寸为基础,为保证凹模磨损到一定程度仍能冲出合格的零件,故落料凹模差不多尺寸应取_________,而落料凸模差不多尺寸则按凹模差不多尺寸__________。
25.冲孔时,因工件的小端尺寸与凸模尺寸一致,应先确定凸模尺寸,即以凸模尺寸为基础,为保证凸模磨损到一定程度仍能冲出合格的零件,故冲孔凸模差不多尺寸应取________,而冲孔凹模差不多尺寸则按凸模差不多尺寸___________。
26.落料时,应以______为基准配制_______,凹模刃口尺寸按磨损的变化规律分不进行运算。
27.冲孔时,应以______为基准配制________,凸模刃口尺寸按磨损的变化规律分不进行运算。
28.配制加工凸、凹模的特点是模具的间隙由_______保证,_______比较简单,不必校核δ凸+δ凹≤2c max-2c min的条件,同时可放大________的制造公差,使制造容易。
29.冲孔用的凹模尺寸应依照凸模的________及_________间隙配制。
30.冲裁件的工艺性,是指冲裁件对冲裁工艺的________。
31.冲裁件的工艺性分析,要紧从冲裁件的_________、冲裁件的_____和冲裁件的_________等三方面进行。
32.冲裁件在条料、带料或板料上的_________叫排样。
33.材料的利用率是指________面积与_____面积之比,它是衡量合理利用材料的指标。
34.冲裁产生的废料可分为两类,一类是________,另一类是________。
35.减少工艺废料的措施是:设计合理的__________,选择合理的________和合理的搭边值;利用_________。
36.排样的方法,按有无废料的情形可分为_______排样、_______排样和_______排样。
37.排样时,冲裁件之间以及_________留下的工艺废料叫搭边。
38.搭边是一种________废料,但它能够补偿_______误差和______误差,确保制件合格.39.手工送料,有侧压装置的搭边值能够____,刚性卸料的比弹性卸料的搭边值________。
40.在冲裁终止时,由于材料的弹性回复及摩擦的存在,将使冲落部分的材料梗塞在________,而冲裁剩下的材料则紧箍在________。
41.从凸模或凹模上卸下的废料或冲件所需的力称________,将梗塞在凹模内的废料或冲件顺冲裁方向推出所需的力称______,逆冲裁方向将冲件从凹模内顶出所需的力称______。
42.采纳弹压卸料装置和下出件方式冲裁时,冲压力等于_______、________、________之和;采纳刚性卸料装置和下出料方式冲裁时,冲压力等于______、______之和;采纳弹性卸料装置和上出料方式冲裁时,冲压力等于______、________、_______、_________之和。
43.为了实现小设备冲裁大工件或使冲裁过程平稳以减少压力机的震动,常用__________法、__________法和__________法来降低冲裁力。
44.在几个凸模直径相差较大、距离又较近的情形下,为了能幸免小直径凸模由于承担材料流淌的侧压力而产生的折断或倾斜现象,凸模应采纳______布置,立即_____做短一些。
如此可保证冲裁时,_______凸模先冲。
45.阶梯冲裁时,大凸模长度应比小凸模长度____,能够保证冲裁时____凸模先冲。
46.模具压力中心确实是冲压力______的作用点。
模具的压力中心应该通过压力机滑块的_________。
47.冲裁模的形式专门多,按送料、出件及排除废料的自动化程度可分为______、_________和________等三种。
48.按工序组合程度分,冲裁模可分为_______、______和______等几种。
49.在压力机的一次行程中,__________冲压工序的冲模称为单工序模。
50.在条料的送进方向上,具有______________,并在压力机的一次行程中,在不同的工位上完成_________________的冲压工序的冲模称为级进模。
51.在压力机的一次行程中,在模具的_______位置上,完成___________的冲压工序的模具,叫复合模。
52.冲裁模具零件可分为_________、________。
53.在冲模中,直截了当对毛坯和板料进行冲压加工的零件称为_______。
54.定位零件是指用于确定_______在模具中的正确位置的零件。
55.级进模中,典型的定位结构有__________和________等两种。
56.由于级进模的工位较多,因而在冲制零件时必须解决条料或带料的_____咨询题,才能保证冲压件的质量。
常用的定位零件是_______和______。
57.应用级进模冲压,排样设计专门重要,它不但要考虑材料的________,还应考虑制件的_______、冲压成形规律、模具_____等咨询题。
58.全部为冲裁工步的级进模,一样是先_______后______。
先冲出的孔可作为后续工位的_______,若该孔不适合______或定位要求较高时,则应冲出____________。
59.按照落料凹模的位置不同,复合模分为_______和_________两种。
60.凸凹模在________,落料凹模在_______的复合模称为顺装复合模。
61.凸模的结构形式,按其断面形状分为________、_______;按刃口形状有_______、________等;按结构分为______、______、________、________和带护套式等。
62.圆形凸模常用的固定方法有______和_______。
63.凹模的类型专门多,按外形分有______、方形或_______,按结构分有_______和_______;按刃口形式分有______和_______。
64.复合模的凸凹模壁厚最小值与冲模结构有关,顺装式复合模的凸凹模壁厚可____些;倒装式复合模的凸凹模壁厚应_____些。
65.镶拼结构的凸、凹模设计原则是:力求改善_____工艺性,减少_____工作量,提高_______精度;66.条料在模具送料平面中必须有两个方向的限位,一是在与___________方向上的限位,保证条料沿正确的方向送进,称为送进导向。
二是在送料方向上的限位,操纵___________,称为送料定距。
67.导料销导正定位多用于________中。
使用导正销的目的是排除_________和_________或______等粗定位的误差。
导正销通常与________,也可与______配合使用。
68.条料在送进方向上的______距离称为步距。
69.弹压卸料板既起________作用,又起________作用,所得的冲裁件质量较好,平直度较_____,因此,质量要求较高的冲裁件或_________宜用弹压卸料装置。
70.精冲凸、凹模的间隙专门_____。
二、判定题(正确的打√,错误的打×)1.冲裁间隙过大时,断面将显现二次光亮带。
()2.冲裁件的塑性差,则断面上毛面和塌角的比例大。
()3.形状复杂的冲裁件,适于用凸、凹模分开加工。
()4.对配作加工的凸、凹模,其零件图无需标注尺寸和公差,只讲明配作间隙值。
()5.利用结构废料冲制冲件,也是合理排样的一种方法。
()6.采纳斜刃冲裁或阶梯冲裁,不仅能够降低冲裁力,而且也能减少冲裁功。
()7.冲裁力是由冲压力、卸料力、推料力及顶料力四部分组成。
()8.模具的压力中心确实是冲压件的重心。
()9.冲裁规则形状的冲件时,模具的压力中心确实是冲裁件的几何中心。
()10.在压力机的一次行程中完成两道或两道以上冲孔(或落料)的冲模称为复合模。