催化剂制备工艺
甲醇合成催化剂生产工艺

甲醇合成催化剂生产工艺甲醇合成催化剂分两期进行生产,甲醇合成催化剂每批生产周期(从物料加入到得到产品)为24小时,每批产品为500kg,一期年生产批数为2000批,总计为1000吨。
一期甲醇合成催化剂以电解铜、电解锌、碱式碳酸铜、碱式碳酸锌、碳酸氢钠、硝酸、氧化铝、石墨为原料,经备料、反应、过滤、烘干、焙烧、成型得到产品。
(1)备料①化铜先将电解铜和水加入5m3化铜罐中,再加入95%硝酸,化铜罐内设有冷却水盘管,用冷却水控制反应温度为60~70℃,铜和硝酸反应生成硝酸铜。
该工序涉及反应方程式如下:3Cu + 8HNO3 = 3Cu(NO3)2 + 2NO↑+4H2O②化锌先将电解锌和水加入5m3化锌罐中,再加入95%硝酸,化锌罐内设有冷却水盘管,用冷却水控制反应温度为60~70℃,锌和硝酸反应生成硝酸锌。
该工序涉及反应方程式如下:3Zn + 8HNO3 = 3Zn(NO3)2 + 2NO↑+4H2O将上述制备好的硝酸铜和硝酸锌溶液打入15m3混合液罐中进行混合,混合均匀后打入计量罐用作反应工序原料。
备料过程会有含氮氧化物废气产生,送二级低温水+二级尿素水溶液吸收系统处理。
(2)反应先向12m3反应罐加入一定量水,再夹套内通入蒸汽升温至60~65℃,开启搅拌器,然后加入碳酸氢钠。
保持罐内温度为60℃~65℃,将制备的硝酸铜、硝酸锌混合液经过计量后匀速加入反应罐中,硝酸铜、硝酸锌与碳酸氢钠发生反应生成碱式碳酸铜、碱式碳酸锌沉淀,碱式碳酸铜、碱式碳酸锌为难溶性物质,溶解度均小于0.01g/100g 水。
该工序涉及反应方程式如下:2Cu(NO3)2 + 4NaHCO3 = Cu2(OH)2CO3↓+4NaNO3 + H2O + 3CO2↑2Zn(NO3)2 + 4NaHCO3 = Zn2(OH)2CO3↓+4NaNO3 + H2O + 3CO2↑反应结束后,将称量好的碱式碳酸铜、碱式碳酸锌、氧化铝依次放入反应罐中,继续搅拌20~30分钟,然后静止沉降得到反应浆液。
化学反应中催化剂的制备方法

化学反应中催化剂的制备方法化学反应中催化剂是一个极其重要的组成部分,它能够促进反应速度,降低所需要的温度及压力,降低反应活化能等。
在化学工业中,催化剂是不可或缺的组成部分,对于一些复杂的反应而言,催化剂也是非常关键的。
那么,如何制备催化剂呢?催化剂的制备方法有很多种,不同的反应需要不同的催化剂,因此催化剂的制备方法也各不相同。
下面,我们将从三个方面来讨论催化剂的制备方法。
一、物理化学法制备催化剂物理化学法是制备催化剂的常用方法之一。
它通过改变催化剂的表面结构,改变催化剂的形貌、形态,来达到提高催化剂效率的目的。
比如,采用热处理、电化学方法、物理吸附等方法可以制备出具有均匀孔径、大比表面积等特点的催化剂。
这种方法制备出来的催化剂具有高效、稳定、易于再生等优点,被广泛应用于各种化学反应中。
二、化学合成法制备催化剂化学合成法是一种较为常用的制备催化剂的方法。
它利用化学反应的原理,采用一定的方法及工艺条件来合成催化剂。
这种方法可以得到具有特定功能的催化剂,可以对催化剂进行定制,使其具有其他传统制备方法所不具备的性质。
例如,在金属催化剂的制备中,常常采用化学还原、溶胶-凝胶等方法。
这些方法不仅可以得到纳米尺寸的催化剂,还可以通过添加不同的催化剂过渡金属、调控反应条件等方法得到具有特定性质的催化剂。
三、生物制备法制备催化剂除了物理化学法和化学合成法以外,生物制备法也是一种较为新颖的催化剂制备方法。
生物体内合成各种酶类可以作为参考,设计合成人工酶,以替代催化剂,来实现反应过程的加速,降低催化剂对环境的污染等目的。
生物制备法中,核壳结构的金属纳米粒子成功应用于大量的催化反应中,例如,银纳米颗粒,由于具有特殊的光学性质,已经成功应用于光催化反应中。
生物制备法制备的催化剂,不仅性能稳定,而且具有良好的环保性和可再生性,因此受到越来越多的关注和研究。
总之,催化剂是化学反应中不可或缺的重要组成部分,催化剂的制备方法也是很多的。
催化剂的组成
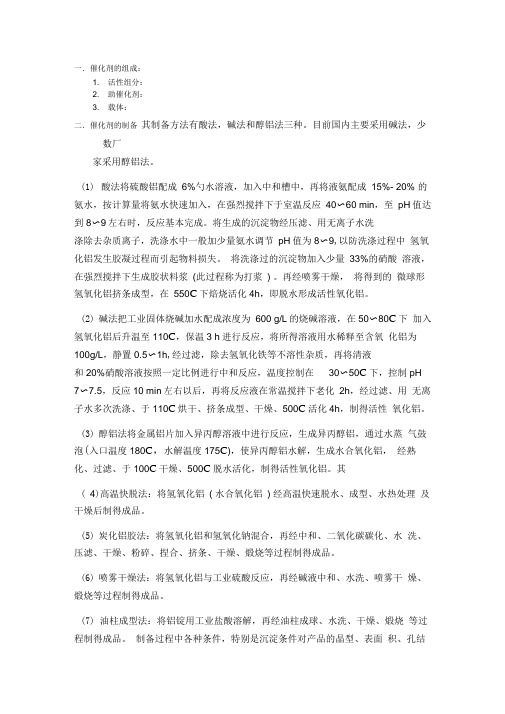
一.催化剂的组成:1. 活性组分:2. 助催化剂:3. 载体:二.催化剂的制备其制备方法有酸法,碱法和醇铝法三种。
目前国内主要采用碱法,少数厂家采用醇铝法。
(1)酸法将硫酸铝配成6%勺水溶液,加入中和槽中,再将液氨配成15%- 20% 的氨水,按计算量将氨水快速加入,在强烈搅拌下于室温反应40〜60 min,至pH值达到8〜9左右时,反应基本完成。
将生成的沉淀物经压滤、用无离子水洗涤除去杂质离子,洗涤水中一般加少量氨水调节pH值为8〜9,以防洗涤过程中氢氧化铝发生胶凝过程而引起物料损失。
将洗涤过的沉淀物加入少量33%的硝酸溶液,在强烈搅拌下生成胶状料浆(此过程称为打浆) 。
再经喷雾干燥,将得到的微球形氢氧化铝挤条成型,在550C下焙烧活化4h,即脱水形成活性氧化铝。
(2)碱法把工业固体烧碱加水配成浓度为600 g/L的烧碱溶液,在50〜80C下加入氢氧化铝后升温至110C,保温3 h进行反应,将所得溶液用水稀释至含氧化铝为100g/L,静置0.5〜1h,经过滤,除去氢氧化铁等不溶性杂质,再将清液和20%硝酸溶液按照一定比例进行中和反应,温度控制在30〜50C下,控制pH 7〜7.5,反应10 min左右以后,再将反应液在常温搅拌下老化2h,经过滤、用无离子水多次洗涤、于110C烘干、挤条成型、干燥、500C活化4h,制得活性氧化铝。
(3)醇铝法将金属铝片加入异丙醇溶液中进行反应,生成异丙醇铝,通过水蒸气鼓泡(入口温度180C,水解温度175C),使异丙醇铝水解,生成水合氧化铝,经熟化、过滤、于100C干燥、500C脱水活化,制得活性氧化铝。
其( 4)高温快脱法:将氢氧化铝( 水合氧化铝) 经高温快速脱水、成型、水热处理及干燥后制得成品。
(5)炭化铝胶法:将氢氧化铝和氢氧化钠混合,再经中和、二氧化碳碳化、水洗、压滤、干燥、粉碎、捏合、挤条、干燥、煅烧等过程制得成品。
(6)喷雾干燥法:将氢氧化铝与工业硫酸反应,再经碱液中和、水洗、喷雾干燥、煅烧等过程制得成品。
催化剂常用制备方法

催化剂常用制备方法固体催化剂的构成●载体(Al2O3 )●主催化剂(合成NH3中的Fe)●助催化剂(合成NH3中的K2O)●共催化剂(石油裂解SiO2-Al2O3催化剂制备的要点●多种化学组成的匹配–各组分一起协调作用的多功能催化剂●一定物理结构的控制–粒度、比表面、孔体积基本制备方法:⏹浸渍法(impregnating)⏹沉淀法(depositing)⏹沥滤法(leaching)⏹热熔融法(melting)⏹电解法(electrolyzing)⏹离子交换法(ion exchanging)⏹其它方法固体催化剂的孔结构(1)比表面积Sg比表面积:每克催化剂或吸附剂的总面积。
测定方法:根据多层吸附理论和BET方程进行测定和计算注意:测定的是总表面积,而具有催化活性的表面积(活性中心)只占总表面的很少一部分。
内表面积越大,活性位越多,反应面越大。
(2)催化剂的孔结构参数密度:堆密度、真密度、颗粒密度、视密度比孔容(Vg):1克催化剂中颗粒内部细孔的总体积.孔隙率(θ):颗粒内细孔的体积占颗粒总体积的分数.(一) 浸渍法⏹通常是将载体浸入可溶性而又易热分解的盐溶液(如硝酸盐、醋酸盐或铵盐等)中进行浸渍,然后干燥和焙烧。
⏹由于盐类的分解和还原,沉积在载体上的就是催化剂的活性组分。
浸渍法的原理●活性组份在载体表面上的吸附●毛细管压力使液体渗透到载体空隙内部●提高浸渍量(可抽真空或提高浸渍液温度)●活性组份在载体上的不均匀分布浸渍法的优点⏹第一,可使用现成的有一定外型和尺寸的载体材料,省去成型过程。
(如氧化铝,氧化硅,活性炭,浮石,活性白土等)⏹第二,可选择合适的载体以提供催化剂所需的物理结构待性.如比表面、孔径和强度等。
⏹第三,由于所浸渍的组分全部分布在载体表面,用量可减小,利用率较高,这对贵稀材料尤为重要。
⏹第四,所负载的量可直接由制备条件计算而得。
浸渍的方法⏹过量浸渍法⏹等量浸渍法⏹喷涂浸渍法⏹流动浸渍法1.1、过量浸渍法⏹即将载体泡入过量的浸渍液中,待吸附平衡后,过滤、干燥及焙烧后即成。
工业催化--第八章 工业催化剂制备原理

– 待沉淀析出后,加入较大量热水稀释,以减少杂 质在溶液中的浓度,同时使一部分被吸附的杂质 转入溶液。
加入热水后,一般不宜放置,而应立即过滤,以防沉 淀进一 步凝聚,并避免表面吸附的杂质包裹在沉淀内 部不易洗净。
洗涤操作的主要目的是除去沉淀中的杂质。
均匀沉淀法常用的类似沉淀母体见下表:
4、浸渍沉淀法
浸渍沉淀法是在普通浸渍法的基础上辅以沉淀 法发展起来的一种新方法。
– 待盐溶液浸渍操作完成之后,再加沉淀剂,而使待 沉淀组分沉积在载体上。
5、导晶沉淀法
借助晶化导向剂(晶种)引导非晶型沉淀转化为 晶型沉淀的快速而有效的方法。
– 普遍用来制备以水玻璃为原料的高硅钠型分子筛, 包括丝光沸石,Y型与X型合成分子筛。
对沉淀剂选择有以下要求:
(1) 尽可能使用易分解并含易挥发成分的沉淀剂
– 常用的沉淀剂有:
碱类(NH4OH、NaOH、KOH); 碳酸盐[(NH4)2CO4、Na2CO4、CO2]; 有机酸(乙酸、草酸)等。 最处理常时用容的易是除NH去4O,H一和般(N不H会4)2遗CO留4,在因催为化铵剂盐中在,洗使涤催和化热剂
如此反复溶解、沉积的结果,消除了细晶体,获得了颗 粒大小均匀的粗晶体。
此时孔隙结构和表面积也发生了相应的变化。
–粗晶体表面积较小,吸附杂质少,吸留在细晶粒之 中的杂质也随溶解过程转入溶液。
– 老化的时间、温度及母液pH值等为老化应考虑的 几项影响因素。
在晶形催化剂制备过程中,老化对催化剂性 能的影响显著。
凝胶法特别适用于主要成分是氧化铝或二氧化 硅的催化剂或载体。
凝胶过程大致可分为缩合与凝结二个阶段。
催化剂生产工艺流程

催化剂生产工艺流程
催化剂是一种能够在化学反应中改变反应速率和选择性的物质。
催化剂的生产工艺流程主要包括原料准备、配制烧结、活化处理和成品制备等几个关键环节。
首先是原料准备。
催化剂的制备需要用到多种原材料,包括金属氧化物、稀土元素等。
这些原料需要经过采购、检测等环节,确保原料的质量和纯度。
接下来是配制烧结。
原料按照一定的配方比例进行配制,并进行烧结处理。
这一步的目的是将原料中的物质相互结合,形成固体颗粒状的催化剂。
然后是活化处理。
烧结后的催化剂需要进行特殊处理,以增加其活性和稳定性。
活化处理通常包括还原、氧化等步骤,通过调整反应条件和添加适量的添加剂,使催化剂获得理想的活性和选择性。
最后是成品制备。
经过活化处理后的催化剂需要进行筛分、干燥等工序,最终得到成品催化剂。
成品催化剂会进行产品的质量检验,包括活性测试、组元分析等,确保催化剂的质量符合产品标准。
催化剂的生产工艺流程需要严格的控制和操作,以确保催化剂的活性和稳定性。
其中,原料的选择和配比是关键的步骤,直接影响到催化剂的性能。
活化处理的过程中,需要对反应条件、时间等参数进行精确控制,以获得理想的催化效果。
此外,成
品制备环节的筛分和干燥等操作也需要谨慎处理,以避免催化剂的破损或氧化。
总之,催化剂的生产工艺流程是一个复杂而关键的过程。
通过准备原料、配制烧结、活化处理和成品制备等环节的精确控制和操作,可以获得具有理想活性和稳定性的催化剂产物。
催化剂的生产工艺流程对于催化剂的性能和应用具有重要意义。
04第四讲:工业催化剂的制备
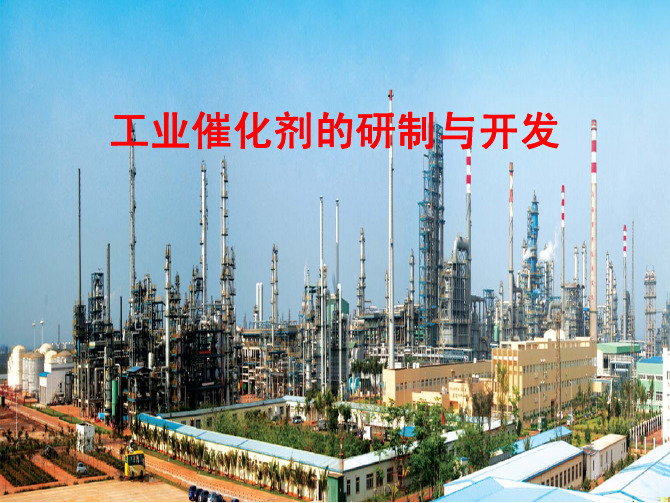
美国氰胺公司
品牌:
– Aero HDS-2钼酸钴系列 – Aero HDS-3钼酸镍系列
载体制备专利技术
– 偏铝酸钠-硫酸铝法,金属铝醋酸水解法制氢氧化铝 – 挤条成型,聚丙烯酰胺助挤剂 – 发展助滤剂,改善氢氧化铝过滤状况
浸渍技术
– 采用三氧化钼、碳酸镍、磷酸代替钼酸铵、硝酸镍配制 浸渍液 – 浸渍方法仍以喷淋细孔饱和法为主,也发展循环浸渍法
混捏方式、强度、时间
孔体积、孔分布、堆密度
挤出设备型式
双螺杆挤条机
59
钼镍磷浸渍液的配制
文献方法: 三氧化钼加入到鳞酸中,溶解后再加入碱式碳酸镍;或先 将碱式碳酸镍加入到鳞酸中,溶解后再加入三氧化钼。时 间长,要求磷酸过量,影响活性 配制的影响因素:
– – – – 三氧化钼性质:钼酸铵的性质和焙烧条件 加料的顺序 升温条件、PH值 P/MoO3, MoO3/NiO比,绘制可配制区图
金属盐
釜式操作
金属盐
T,pH控制
沉淀剂
沉淀或共沉淀法制备负载型催化剂
NaOH水溶液
NaOH水溶液
悬浮的载体 金属盐 金属盐和铝盐
可能存在的问题:
较难控制,重复性差 成核过程更易于在溶液中发生,而不是发生 在载体上 生成的金属颗粒较大,均匀性低
7
沉淀过程中的助剂
所谓添加剂是沉淀过程中非必须存在的物质, 但可能强化沉淀过程或最终产品的性质。 最广泛使用的助剂是有机物,它们可能控制孔 的形成。 例如在中孔SiO2或SiO2-Al2O3(MCM-41)的自组 装表面活性剂,如十六烷基三甲基胺。
在沸石的阳离子点引入金属
–Pt, Pd –过渡金属
精细调变孔
–KA 0.3nm, CaA 0.5nm –丝光或ZSM-5有类似作用
催化剂生产工艺流程

催化剂生产工艺流程催化剂生产工艺流程催化剂是一种能够促使化学反应发生,提高反应速率和选择性的物质。
在化工工艺中,催化剂扮演着重要的角色。
下面将介绍一种常见的催化剂生产工艺流程。
1. 原料准备:催化剂的制备通常需要使用一些原料,如金属盐、有机化合物等。
首先,需要按照配方准确地称取这些原料,并进行粉碎、干燥等处理,使其达到制备催化剂的要求。
2. 催化剂伴载物的制备:在一些情况下,为了提高催化剂的性能,需要将活性组分负载在一种或多种材料上,形成催化剂的载体。
例如,使用氧化铝、硅胶等作为载体材料。
制备载体通常需要将原料溶解或悬浮在适当的溶剂中,然后进行混合、搅拌、烘干等步骤,最后得到均匀的载体。
3. 活性组分的制备:活性组分是催化剂的核心部分,它决定了催化剂的催化性能。
活性组分的制备通常需要将金属盐或有机化合物与适当的溶剂进行溶解或反应,得到金属离子或有机活性物质。
然后,通过对溶液进行调节、过滤等步骤,得到纯净的活性组分。
4. 催化剂的制备:将载体与活性组分进行混合,形成催化剂的前驱体。
混合过程中需要控制各组分的比例和时间,以确保活性组分均匀地分散在载体上。
然后,将混合物进行干燥、煅烧等处理,以去除溶剂和形成稳定的催化剂。
5. 催化剂的形状处理:根据不同的应用需求,催化剂需要具有特定的形状,如颗粒、丝状、块状等。
通过粉碎、造粒、压制等方法,将催化剂前驱体加工成所需的形状。
6. 催化剂的活化:催化剂的活化是为了提高其催化性能。
活化过程通常需要在适当的温度和气氛下进行,以去除催化剂表面的杂质或不稳定物质,使催化剂表面具有更高的催化活性。
7. 催化剂的包装和存储:将制备好的催化剂进行包装,以防止因外界环境的影响导致催化剂质量下降。
催化剂通常存放在干燥、防尘的条件下,以延长其有效使用期限。
总之,催化剂的生产工艺流程涉及原料准备、载体制备、活性组分制备、催化剂制备、形状处理、催化剂的活化以及催化剂的包装和存储等步骤。
- 1、下载文档前请自行甄别文档内容的完整性,平台不提供额外的编辑、内容补充、找答案等附加服务。
- 2、"仅部分预览"的文档,不可在线预览部分如存在完整性等问题,可反馈申请退款(可完整预览的文档不适用该条件!)。
- 3、如文档侵犯您的权益,请联系客服反馈,我们会尽快为您处理(人工客服工作时间:9:00-18:30)。
催化剂制备工艺催化剂制备工艺1 催化剂的载体甲烷自热重整所用催化剂的载体需要具有适当的晶相组成、比表面和孔结构,以有利于反应物分子在催化剂表面吸附、活化,同时也有利于产物分子脱附而离开催化剂表面,防止积炭反应的发生此外载体还应具有较好的机械强度。
目前研究较多的载体有Al2O3、MgO、SiO2、TiO2、CeO2、ZrO2、SiO2-Al2O3 Y型分子筛等。
Bhattacharya等考察了在温度为1023K,空速为5000h-1,CH4/O2为8:1时,负载在不同载体上的Pt催化剂的部分氧化反应结果。
所用的催化剂载体分别为IIIA,IVA金属氧化物和稀土金属氧化物,γ-AL2O3和SiO2。
研究表明,因载体不同,甲烷转化率在33.4%到66.9%之间变化,除SiO2外,其它载体担载的催化剂一氧化碳的选择性均超过99%以上。
曹立新等对5种不同载体(Al2O3、ZrO2、SrTiO3、SiO2、TiO2)上担载l0%NiO所制得的催化剂进行甲烷氧化制合成气影响的考察。
实验结果表明该系列催化剂的活性顺序为:NiO/Al2O3>NiO/ZrO2>NiO/SrTiO3>NiO/SiO2NiO/TiO2。
TPR结果显示NiO与不同载体之间经1073K焙烧都有不同程度的相互作用。
TPD表明催化剂表面相对较强的碱中心有利于甲烷分子的活化,并能增加催化剂抗积炭性能。
因为载体表面的酸碱性对催化剂的活性和抗积炭能力有很大影响,所以选择催化剂载体时,也要考虑载体表面的酸碱性。
一般认为,催化剂表面有相对较强的碱性中心,将有利于增强催化剂的抗积炭能力。
Zhang等研究了以A12O3、TiO2、SiO2、MgO、La2O3、YSZ为载体的0.5wt.%Rh催化剂的二氧化碳重整的反应性能。
结果表明:在923K,CH4/CO2=1.0的反应条件下,重整的初活性顺序是YSZAl2O3TiO2SiO2La2O3MgO。
在1023K,20%CH4,20%CO2,60%He 的反应条件下,在Rh/SiO2和Rh/YSZ上进行50h的重整反应,没有发现催化剂的失活。
可以看出,各个载体间的差异很大,Al2O3由于具有适宜的比表面和孔结构可以用作CH4自热重整催化剂的载体,而且不同类型Al2O3的反应活性也有所不同。
李振花等分别采用α-Al2O3、θ-Al2O3、γ-Al2O3为载体,测定了载体对甲烷部分氧化制合成气的活性和CO选择性的影响。
发现催化剂在773K下用H2还原后,10%Ni/θ-Al2O3、Ni/γ-Al2O3对甲烷部分氧化反应无活性,只有10%Ni/α-Al2O3对反应有活性。
XRD测试结果表明,10%Ni/γ-Al2O3催化剂在1123K下反应4h后,其载体的晶型由γ-Al2O3转变为α-Al2O3。
余林等考察了Ni负载量为8%的Ni/γ-Al2O3,Ni/δ-Al2O3,Ni/θ-Al2O3,Ni/α-Al2O3四种催化剂的甲烷部分氧化活性及选择性。
结果表明:在1043K下,甲烷转化率及CO和H2的选择性排序为Ni/γ-Al2O3Ni/δ-Al2O3Ni/θ-Al2O3 ≈Ni/α-Al2O3。
表征结果显示,不同Ni/Al2O3催化剂体系上的反应活性及选择性的差异是由不同结构Al2O3载体的性质不同所致。
以Al2O3作为载体,不仅提供了反应物与催化剂活性中心的接触表面,而且Al2O3与活性组分Ni会发生作用,形成NiA12O4尖晶石结构,对催化反应的活性及积炭都有较大影响。
Sahli等将用凝胶溶胶法制备的NiAl2O4的催化剂用于二氧化碳重整反应。
结果表明,Ni/Al低于尖晶石结构的催化剂因镍粒子的高度分散,不仅具有高的二氧化碳重整活性,而且能够抗积炭的生成。
Requies等研究了Ni/MgO和Ni/La2O3催化剂的甲烷部分氧化的反应性能。
结果表明:在1073-1273K的温度范围内,这两种催化剂都具有高的部分氧化活性。
对于Ni/La2O3,NiO2通过固态反应与La2O3形成LaNiO3,LaNiO3在H2气氛或反应过程中还原成与La2O3晶格紧密接触、高度分散的镍原子。
这种镍原子的存在是催化剂具有高催化活性的原因。
Ni/MgO具有比Ni/La2O3更高的活性和稳定性。
这是因为NiO与MgO形成了(Mg,Ni)O固溶体。
在反应过程中,高度分散的镍具有优良的甲烷部分氧化性能。
另外,稳定性实验表明Ni/MgO比Ni/La2O3具有更高的活性和稳定性。
作者把这一发现归结为高温下生成更多(Mg,Ni)O固溶体所致。
Barbero等在考察以MgO、La2O3和ZrO2为载体的镍基催化剂对甲烷部分氧化反应的催化行为时,得出了与Requies等相似的结果。
此外他们还指出,对于Ni/ZrO2催化剂,由于金属镍粒子与载体结合较弱,催化剂在反应过程中易因粒子烧结而失活。
然而,Li等认为虽然Ni/ZrO2上的二氧化碳重整活性很高,但催化剂易因积炭而失活。
Mehr等研究了在不同MgO负载量下,NiO/MgO/α-Al2O3的水蒸汽和二氧化碳重整反应的反应性能。
结果表明:MgO的加入不仅减少了积炭,而且减少反应所需的热能。
作者将催化剂高稳定性和很少积炭归于碱性MgO的影响。
载体的储氧能力也对甲烷部分氧化反应性能有影响。
所谓储氧能力是指载体与气相浓度相适应的可逆储存和释放大量氧的能力。
一般认为,具有较高储氧能力的载体有利于部分氧化反应的进行。
Takeguchi等考察了NiO/CeO2CZrO2催化剂的甲烷部分氧化反应活性。
结果表明,催化剂的催化活性随着固溶体储氧能力的增加而增加。
同时作者指出,甲烷的部分氧化反应是以氧化还原机理进行的。
Dong等通过比较Ni/ZrO2,Ni/CeO2和Ni/CeCZrO2三个催化剂体系用于甲烷部分氧化反应的特点,指出,在Ni/CeO2催化剂上,甲烷在镍表面裂解所形成的炭系迁移到Ni-截面处与CeO2上的晶格氧结合形成CO,加速了甲烷的转化。
ZrO2的加入增加了催化剂的储氧能力,改善了催化剂的抗积炭性能和催化部分氧化活性。
Seo等考察了常压下分别以CeO2,SiO2和Al2O3负载5wt.%Rh 和Ni催化剂的部分氧化催化剂反应特点,得出结论以CeO2为载体的催化剂有较高的初活性,经过30h的稳定性实验后,催化剂没有出现失活。
他们把以CeO2为载体的催化剂的高催化活性和稳定性归于CeO2的氧化还原能力。
严前古等研究了以TiO2为载体的Ni基催化剂。
结果发现,由于TiO2作为载体的催化剂具有更好的储氧的能力,能避免碳物种在催化剂表面积累积,因此有利于催化剂稳定性的提高。
2 催化剂的活性组分甲烷氧化和重整气反应所用催化剂主要是负载型的金属催化剂,其金属活性组分分为两类:贵金属如Pd、Ru、Rh、Pt、Ir等和非贵金属如Ni、Co、Fe等Ⅷ族过渡金属。
Schmidt工作组在整体型陶瓷上分别负载Ni、Rh、Pt、Ir、Pd、Fe、Co、Re、Ru活性组分制备成整体型催化剂。
通过比较这些催化剂的甲烷部分氧化的反应性能,作者发现,其中负载Ni和Rh的催化剂具有高活性和高选择性。
当温度为1273K,GHSV为1.0×105h-1时,负载型Rh催化剂上的甲烷转化率、氢气和一氧化碳的选择性分别为89%,90%,95%,且长时间运行未出现失活。
负载型Ni催化剂虽有和Rh相近的活性和选择性,然而易出现失活。
他们发现Rh的陶瓷整体型催化剂与Pt催化剂相比能够产生更多的氢和更少的水,与催化剂表面反应物种的吸附、脱附和反应特性有关。
Hegarty等在673K到1073K的温度范围内,分别考察了以ZrO2为载体分别负载Co,Cu,Fe,Ni,Pd,Pt的催化剂进行水蒸汽重整反应的反应性能。
结果发现:负载Ni,Pd,Pt的催化剂具有高的重整活性。
1073K下的稳定性试验表明只有Pt催化剂不因积炭而失活。
Kikuchi等研究水蒸汽重整反应时发现,在SiO2上担载(5wt.%)不同金属上,其活性大小依次为:Ru≈RhNiIrPd=PtCO≈Fe。
而且Ru和Rh 是其中最稳定的催化剂。
朱全力等制备了含有少量Ni,Co,Cu或K的Mo2C/Al2O3催化剂,用于甲烷部分氧化制合成气反应,并用程序升温表面反应(TPSR)进行了表征。
发现,Ni可以促进氧化钼被氢气还原,进而促进氧化钼的碳化及甲烷的活化,故Ni改性催化剂具有很高的催化活性和选择性,并且有很高的稳定性。
Co也有相似的情况。
虽Cu改性催化剂在开始阶段表现出对甲烷转化的促进作用,但随后促进作用消失。
K的添加不利于氧化钼的碳化及甲烷的活化,故K改性催化剂的催化活性和选择性较低。
Claridge等系统研究了一些过渡金属上CH4部分氧化反应的积碳性能,发现积碳量依次为NiPdRh、Ru、Pt和Ir。
Pt和Ir具有非常好的抗积碳性能,但活性组分容易烧结和流失,从而引起催化剂失活。
一般来说,Pt、Rh、Ru、Pd、Ir等贵金属催化剂的对CH4部分氧化反应的催化活性顺序为:RhPtRuPdIr,其中Pt和Rh以其优异的反应活性和抗积碳性能而倍受关注。
非贵金属催化剂对甲烷部分氧化反应的活性顺序为NiCoFe。
对甲烷水蒸气重整反应的催化剂活性顺序为:Ru≈RhNiIrPd=PtCO≈Fe。
因此用于甲烷自热重整的理想催化剂是Rh、Ni、Ru。
但是,贵金属的价格较为昂贵,镍基催化剂的催化性能较好且价格便宜,具有很好的研究和应用前景,但Ni基催化剂存在严重的积碳等失活问题。
and Tungsten Carbide.J.Catal.,1998,180(1):85~1003 催化剂制备(1)载体的制备。
商用r-Al203直接做载体:在500-750℃温度中,煅烧3h,经粉碎机碾磨成180~250um的颗粒大小形成载体。
或者- Al203(刚玉)在高于1200℃下煅烧。
(2)单金属Ni催化剂。
用硝酸镍Ni(NO3)26H2O溶液,在80℃热水浴中浸渍γ-Al2O3载体,110℃烘10小时蒸发去除溶液,再在焙烧温度为650℃,焙烧时间为4h,Ni的负载量为10%。
制备的催化剂表示为Ni/Al2O3。
(3)单金属Pt催化剂。
用硝酸镍H2PtCl6的水溶液,在80℃热水浴中浸渍γ-Al2O3载体,110℃烘10小时蒸发去除溶液,再在焙烧温度为650℃,焙烧时间为4h,Pt的负载量为1%。
制备的催化剂表示为Pt/Al2O3。
(4)双金属催化剂。
①分步浸渍法:用等体积硝酸镍Ni(NO3)26H2O溶液,在80℃热水浴中浸渍γ-Al2O3载体,110℃烘10小时蒸发去除溶液,再在焙烧温度为650℃,焙烧时间为4h。
再用等体积硝酸镍H2PtCl6的水溶液,在80℃热水浴中浸渍γ-Al2O3载体,110℃烘10小时蒸发去除溶液,再在焙烧温度为650℃,焙烧时间为4h。