多个订单库存控制模型
供应链管理中的库存控制模型构建方法

供应链管理中的库存控制模型构建方法在供应链管理中,库存控制是一个至关重要的环节。
库存的合理管理可以最大限度地减少企业的成本,并提高运营的效率。
为了实现库存控制的优化,构建适合供应链管理的库存控制模型是必不可少的。
一、ABC分类法ABC分类法是供应链管理中常用的一种库存控制模型构建方法。
该方法将库存的物料按照其重要性和消耗度进行分类,从而实现对库存的优化管理。
ABC分类法的核心思想是将物料划分为三类,A类为最重要的物料,B类为次重要的物料,C类为最不重要的物料。
具体划分依据可以采用销售额、利润贡献度等指标进行评估。
对于A类物料,需要定期监控和补充,以保证供应链的稳定性;对于B类物料,可以适量存放一定数量的库存,以应对供应链的突发需求;而对于C类物料,则可以采取定期盘点或订单到货的方式进行管理。
二、EOQ模型经济订货数量(EOQ)模型是另一种常用的库存控制模型构建方法。
该模型旨在通过平衡订货成本和库存成本,实现库存控制的最优化。
EOQ模型的核心是计算出一个最经济的订货数量,使得订货成本和库存成本的总和达到最小。
具体计算方法为使用以下公式:EOQ = √((2DS)/H),其中D表示需求量,S表示订货成本,H表示单位存储成本。
通过计算EOQ,企业可以找到一个经济订货数量,从而避免了采购成本和库存成本之间的过度投入,并确保了供应链的高效运转。
三、安全库存模型安全库存模型是为应对供应链中存在的不确定性和风险而设计的一种库存控制模型。
该模型通过保留一定数量的安全库存,以应对突发需求、交通延误、生产故障等不可控因素,确保供应链的平稳运营。
安全库存的计算可以基于统计方法,如基于需求量的标准差和平均需求量进行预测;也可以基于供应链的可靠性指标,如供应商的交货准确率和交货时间进行评估。
在实际运用中,安全库存模型需要进行动态调整,以应对供应链环境的变化。
通过灵活地调整安全库存的数量,可以在保证供应链稳定运行的同时,避免库存过量和过期等问题。
库存问题的基本模型

库存问题的基本模型库存问题是指在供应链中管理和控制物料和产品的数量,以达到成本最小化和客户满意度最大化的目标。
库存问题的基本模型包括以下几个要素:供应商、制造商、分销商和最终客户。
首先,供应商是指提供原材料和零件的供应商。
他们与制造商建立合作关系,提供所需的物料。
在库存问题中,包括考虑供应商的交货时间、供应能力以及货物成本等因素。
其次,制造商是指将原材料和零件制造成最终产品的组织。
制造商需要根据市场需求来计划生产,并确保在生产过程中的库存水平合理。
在库存问题中,制造商需要考虑生产设备的利用率、生产率和生产规模等因素。
然后,分销商是指将最终产品分销给最终客户的组织。
分销商需要根据市场需求和销售预测来制定库存策略,并确保库存水平能够满足客户需求。
在库存问题中,分销商需要考虑订单接收、物流配送和销售预测等因素。
最后,最终客户是指购买最终产品的个人或组织。
最终客户的需求是库存问题的决定性因素,因为所有的供应链活动都是为了满足最终客户的需求。
在库存问题中,最终客户的需求可以通过市场调研、销售预测和订单管理等方式进行预测和控制。
综上所述,库存问题的基本模型是一个以供应商、制造商、分销商和最终客户为核心的供应链模型。
在这个模型中,各个组织之间需要进行信息交流和协调,以实现库存的合理管理和控制,从而最大限度地降低成本,提高客户满意度。
库存问题是供应链管理中的一个重要方面,对企业的运营和业务效率有着直接的影响。
有效地管理和控制库存,可以降低企业的成本,提高资源利用率,减少产品滞销和返工等问题,从而提高客户满意度和企业竞争力。
在库存问题中,最基本的模型是库存控制模型,其中包括安全库存、订货量和库存周转率等关键指标。
安全库存是指为了应对不确定的需求、供应变动或突发事件而预留的一定量的库存。
订货量是指供应商和分销商根据需求预测和订单量确定的每次采购或生产的数量。
库存周转率是反映库存利用效率的指标,可以通过销售额与平均库存量的比值来计算。
供应链库存管理模型

通过对VMI和JMI两种模式的分析可得出:VMI就是以系统的、集成的管理思想进行库存管理,使供应链系统能够获得同步化的优化运行。
通过几年的实施,VMI和JMI被证明是比较先进的库存管理办法,但VMI和JMI也有以下缺点:①VMI是单行的过程,决策过程中缺乏协商,难免造成失误;②决策数据不准确,决策失误较多;③财务计划在销售和生产预测之前完成,风险较大;④供应链没有实现真正的集成,使得库存水平较高,订单落实速度慢;⑤促销和库存补给项目没有协调起来;⑥当发现供应出现问题(如产品短缺)时,留给供应商进行解决的时间非常有限;VMI过度地以客户为中心,使得供应链的建立和维护费用都很高。
随着现代科学技术和管理技术的不断提升,VMI和JMI中出现的种种弊端也得到改进,提出了新的供应链库存管理技术,CPFR(共同预测、计划与补给)。
CPFR有效地解决了VMI和JMI的不足,成为现代库存管理新技术。
协同规划、预测和补给(Collaborative Planning ForecastingReplenishment,简称CPFR)是一种协同式的供应链库存管理技术,它能同时降低销售商的存货量,增加供应商的销售量。
CPFR最大的优势是能及时准确地预测由各项促销措施或异常变化带来的销售高峰和波动,从而使销售商和供应商都能做好充分的准备,赢得主动。
同时CPFR采取了一种"双赢'的原则,始终从全局的观点出发,制定统一的管理目标以及方案实施办法,以库存管理为核心,兼顾供应链上的其它方面的管理。
因此,CPFR能实现伙伴间更广泛深入的合作,它主要体现了以下思想。
1)合作伙伴构成的框架及其运行规则主要基于消费者的需求和整个价值链的增值。
2)供应链上企业的生产计划基于同一销售预测报告。
销售商和制造商对市场有不同的认识,在不泄露各自商业机密的前提下,销售商和制造商可交换他们的信息和数据,来改善他们的市场预测能力,使最终的预测报告更为准确、可信。
库存控制模型技术与仿真概述

库存控制模型技术与仿真概述库存控制模型技术是指通过数学和统计方法对企业的库存进行科学管理和控制的技术。
它涉及到库存管理的各个方面,包括库存水平的确定、订货点的计算、定量经济订货模型的建立等。
而仿真是一种通过模拟实验,模拟真实情况的方法,可以用于对库存控制模型的验证和优化。
1.经验模型:基于经验的库存控制模型是根据企业历史数据和经验进行库存控制的方法。
它没有依据数学和统计的理论,主要依赖经验和直觉。
虽然这种方法简单易实施,但是缺乏科学性和准确性。
2.定量经济订货模型:定量经济订货模型是库存控制模型技术中的经典方法,包括经济批量模型、经济周期模型和定期检查模型等。
这些模型基于数学和统计的方法,通过优化数学模型,确定最优的库存水平和订货策略。
-经济批量模型(EOQ模型)是最著名的定量经济订货模型之一,它通过平衡订货成本和库存成本,确定最经济的订货数量。
-经济周期模型(EPQ模型)是另一种常用的定量经济订货模型,它考虑了补充订单的时间和成本,以及库存的消耗速率,确定最优的订货批量和订货周期。
-定期检查模型是一种周期性检查库存水平,并根据需要补充库存的模型。
它适用于那些无法预测需求的产品,通过定期检查库存,确定补充库存的时间和数量。
3.风险模型:风险模型在库存控制中考虑了需求和供应的不确定性,以及库存的风险成本。
它通过对不确定性和风险的考虑,确定最优的库存水平和订货策略,从而降低库存风险和成本。
4.模拟优化模型:模拟优化模型将仿真技术与优化算法相结合,通过对库存控制模型进行仿真实验和优化,寻找最优的库存管理策略。
这种方法可以考虑更多的因素和复杂的情况,提供更优化的解决方案。
库存控制模型技术在企业的库存管理中起到重要的作用。
通过科学的方法和模型,可以确定最优的库存水平和订货策略,降低库存成本,提高供应链效率。
而仿真技术则可以用于对库存控制模型的验证和优化,通过模拟实验,找到最佳的库存管理策略,并预测和应对不确定性和风险。
库存管理的基本模型介绍
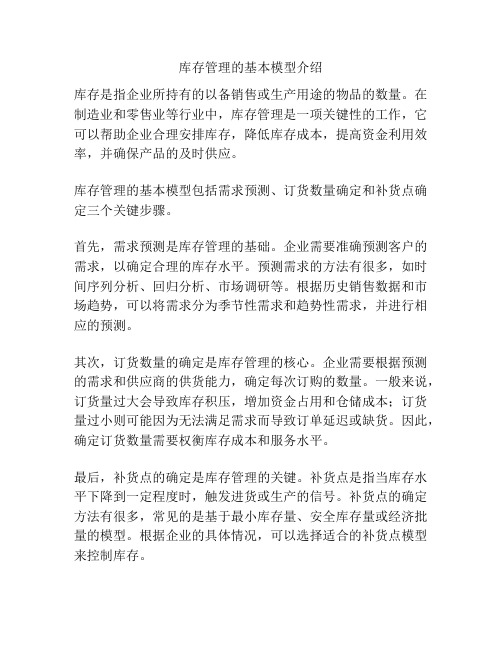
库存管理的基本模型介绍库存是指企业所持有的以备销售或生产用途的物品的数量。
在制造业和零售业等行业中,库存管理是一项关键性的工作,它可以帮助企业合理安排库存,降低库存成本,提高资金利用效率,并确保产品的及时供应。
库存管理的基本模型包括需求预测、订货数量确定和补货点确定三个关键步骤。
首先,需求预测是库存管理的基础。
企业需要准确预测客户的需求,以确定合理的库存水平。
预测需求的方法有很多,如时间序列分析、回归分析、市场调研等。
根据历史销售数据和市场趋势,可以将需求分为季节性需求和趋势性需求,并进行相应的预测。
其次,订货数量的确定是库存管理的核心。
企业需要根据预测的需求和供应商的供货能力,确定每次订购的数量。
一般来说,订货量过大会导致库存积压,增加资金占用和仓储成本;订货量过小则可能因为无法满足需求而导致订单延迟或缺货。
因此,确定订货数量需要权衡库存成本和服务水平。
最后,补货点的确定是库存管理的关键。
补货点是指当库存水平下降到一定程度时,触发进货或生产的信号。
补货点的确定方法有很多,常见的是基于最小库存量、安全库存量或经济批量的模型。
根据企业的具体情况,可以选择适合的补货点模型来控制库存。
以上是库存管理的基本模型介绍,它应用了预测方法、订货数量确定和补货点确定等技术手段,帮助企业合理安排库存水平,降低库存成本,提高资金利用效率,并确保产品的及时供应。
库存管理对于企业的运营效率和利润率都具有重要影响,因此,企业应重视库存管理,并不断进行优化和改进。
库存管理是现代企业管理中的重要环节之一,对企业运营效率、成本控制以及顾客满意度具有重要影响。
在如今竞争激烈的市场环境下,企业需要通过优化库存管理,实现供需平衡,减少资金占用和仓储成本,提高企业的竞争力。
库存管理主要包括库存的控制和库存的优化,通过合理选择合适的库存策略和技术手段,实现库存的动态调整和最优化管理。
库存的控制包括库存的定量管理和库存的质量管理;库存的优化包括优化进货周期、优化订货量和优化供应链管理。
库存控制基本模型

库存控制的基本模型库存控制的基本模型包括单周期库存基本模型和多周期库存基本模型,所谓的单周期是指订购的物料或商品如果在一个决策周期内没有使用或者没有按正常价格售出,就需要做出相应的处理,也就是说剩余的物料或商品不会结转到下一个决策周期,而多周期是指上一周期剩余的库存可以在下一个决策周期内被继续使用。
一、单周期库存模型对于单周期需求来说,库存控制的关键在于确定订货批量。
对于单周期库存问题,订货量就等于预测的需求量。
由于预测误差的存在,根据预测确定的订货量和实际需求量不可能一致。
如果需求量大于订货量,就会失去潜在的销售机会,导致机会损失—订货的机会(欠储)成本。
另一方面,假如需求量小于订货量,所有未销售出去的物品将可能以低于成本的价格出售,甚至可能报废,还要另外文付一笔处理费。
这种由于供过于求导致的费用称为陈旧(超储)成本。
显然,最理想的情况是订货量恰恰等于需求量。
为了确定最佳订货量,需要考虑各种由订货引起的费用。
由于只发出一次订货和只发生一次订购费用,所以订货费用为一种沉没成本,它与决策无关。
库存费用也可视为一种沉没成本,因为单周期物品的现实需求无法准确预计,而且只有通过一次订货满足。
所以即使有库存,其费用的变化也不会很大。
因此,只有机会成本和陈旧成本对最佳订货量的确定起决定性的作用。
确定最佳订货量可采用期望损失最小法、期望利润最大法或边际分析法。
期望损失最小法1、基本思想顾名思义,期望损失最小法就是比较不同订货量下的期望损失,取期望损失最小的订货量作为最佳订货量。
已知库存物品的单位成本为C,单位售价为P,实际需求量为d n,若在预定的时间内卖不出去,则单价只能降为S(S<C)卖出,单位超储损失为C o=C-S;若需求超过存货,则单位缺货损失(机会损失)C o=P-C。
设订货量为Q时的期望损失为E L(Q),则取使E L(Q)最小的Q作为最佳订货量。
E L(Q)可通过下式计算:2、期望利润最大法基本思想顾名思义,期望利润最大法就是比较不同订货量下的期望利润,取期望利润最大的订货量作为最佳订货量。
库存控制的基本模型和库存控制的方法
库存控制的基本模型和库存控制的方法库存控制是企业管理中非常重要的一项工作,它涉及到企业的物流、生产计划、资金运作等多个方面。
库存控制的目标是实现库存的合理化管理,既要确保生产和销售的顺利进行,又要降低库存管理成本,提高资金周转率和利润率。
在实际操作中,库存控制常常采用一些基本模型和方法。
1.定量模型:定量模型主要关注库存水平的决策,通常采用一些定量分析方法和数学模型进行求解。
其中较为常见的模型有:EOQ(经济订货量)模型、EPQ(经济生产量)模型、ABC(库存分类)模型等。
-EOQ模型是库存管理中最常用的模型之一,它基于一系列假设,通过计算经济订货量来决定最优的订货批量,从而实现最低的库存总成本。
该模型假设需求稳定、存货成本固定、采购成本恒定等。
-EPQ模型是在EOQ模型的基础上引入了生产批量的概念,适用于生产环境下的库存管理。
该模型考虑了生产成本和订货成本,通过计算经济生产量来实现最低的库存总成本。
-ABC模型是根据存货金额或交易频率将存货分为A、B、C三类,采取不同的库存控制策略。
A类存货金额较高或交易频率较高,需要精确控制;B类存货金额和交易频率居中,需要较精确控制;C类存货金额较低或交易频率较低,可以采用一些简化的控制策略。
2.定时模型:定时模型主要关注库存更新的时机,通过设定库存更新的时间间隔和方法来实现库存的控制。
其中常见的模型有:固定时间点重新订货法、周期盘点法等。
- 固定时间点重新订货法又称为P系统(Periodic Review System),它是根据固定的时间点对库存进行盘点,然后根据需求量和补货时间确定订货量。
该模型适用于需求变化较为平稳的情况,通过集中管理库存以降低成本。
-周期盘点法是根据固定的周期对库存进行盘点,例如每个季度、半年或年终进行库存盘点。
通过这种周期性的盘点,企业可以更好地掌握库存情况,并及时进行调整。
1.安全库存法:安全库存法是通过设定一定的安全库存量来应对需求的波动或供应的不确定性。
库存控制模型
(Q, R)策略
(R, S)策略
(t, S)策略
(t, R, S)策略
1、(Q,R)策略和(R,S)策略
库存量
(S)
Q
Q
R
LT
时间
对库存进行连续性检查,当库存降低到订货点R时, 即发出一个订货。
适用:需求量大,缺货费用高,需求波动性大的情形
库存量
2、(t,S)策略
(S)
S-I1
S-I2 Q
当库存量Q Q 3 时,Q=5+3*2.54-12.62,则用户需求的服务可靠性
水平为: 50%+99.73%*1/2=99.87%
②确定经济订货批量 Q。*
等式两端对 Q 求导数:
dTC dQ
0 (
DK Q2
)
C 2
0
求得经济订货批量: Q* 2DK C
即计算公式为:
经济批量=
2每次订购费用年需用量 物料单价年保管费用率
EOQ库存控制模型
例1:某仓库某种商品年需求量为16000箱, 单位商品年保管费2元,每次订货成本为40 元,求经济订货批量Q*。
3、订货点的确定
需求量和提前订货时间随机波动,订货点的库存量就需要根据历史的 波动数据求得平均和平均提前订货时间,或者根据最大提前时间来计算。
为了抵消随机波动的影响,此时就要增加安全库存量ss,计算方法是:
订货点库存量=日(月)平均需求量*平均提前订货时间+安全库存量
即
Q0 dt ss
随机型存储控制模型
缺货情况与安全库存量:
在定量订货方式中,每当库存量降至存货点s是,即按一定批量
Q(Q=S-s)
库存分析与控制课件,单周期库存和多周期库存模型知识
22
2、期望利润最大法:
比较不同订货量下的期望利润,取期望利润最
大的订货量作为最佳订货量: 超储时的利润
欠储时的利润 机会成本不考虑
Ep(Q) [Cud - Co(Q- d)]p(d) CuQp(d)
单库存周期和 多周期库存模型 知识讲解
1
库存具有二重性,它一方面保障了正常生产活动 的进行,另一方面却又是生产的负担,其本身 就构成了一对矛盾。
业界人士称库存如同煮青蛙/糖尿病,库存控制已 经是库存管理的核心。
2
对库存的不良控制会导致库存的不足或过剩。 因此,企业必须做到在库存成本的合理范 围内达到满意的顾客服务水平—库存管理 的总目标。
P(d):需求量为d时的概率 S:预定时间卖不出去的售价
20
某商店挂历的需求分布概率
需求d(份) 0
10
20
30
40
50
概率p(d) 0.05 0.15
0.20
0.25
0.20
0.15
已则知每, 份每挂份历挂只历能进按价S=C3=05元0元卖,出每,份求售该价商P店=应80该元进。多若少在挂一历右失个上好,月半。成内角等卖为差不欠(出储10去时*3的,0)损
购买费和加工费:购买或加工的批量,可能会有价格折扣。
生产管理费:加工批量大,为每个工件做出安排的工作量就小
缺货损失费:批量大,则发生缺货损失的情况就少。
27
(3)库存总费用
年维持库存费用(Holding cost):以CH表示,是维持库存所必须的费 用。包括(1)中的费用。
库存控制模型
随机型存储控制模型
缺货情况与安全库存量:
在定量订货方式中,每当库存量降至存货点s是,即按一定批量
Q(Q=S-s)
订货补充。如图所示:
Q(t)
S
Q
s S
ss
S:最高库存量 s:订货点 ss:安全库存
0 T
时间(t)
随机型存储控制模型
如果订货后交货并在交货期间无过量使用,并不动用安全库存量ss,如果订货 后不按时交货,出现延误时间,将要动用安全库存量,以应对延误时间内的用 量;如果在订货到交货期间,出现过量使用,库存量下降速率增加,则也要动 用安全库存量,以应付缺货情况。
第二节 ABC库存控制法
ABC库存控制法
ABC库存控制法
三、ABC分析法的应用
A类商品的管理方法 (1)采取定期订货方式,定期调整库存; (2)增加盘点次数,以提高对库存量的精确掌握; (3)尽量减小货物出库量的波动,使仓库的安全储备量降低; (4)A类商品必须保证不拖延交货期; (5)A类商品是价值分析的对象; (6)货物放置于便于进出的地方; (7)货物包装尽可能标准化,以提高库场利用率。
3、订货点的确定
需求量和提前订货时间随机波动,订货点的库存量就需要根据历史的 波动数据求得平均和平均提前订货时间,或者根据最大提前时间来计算。
- 1、下载文档前请自行甄别文档内容的完整性,平台不提供额外的编辑、内容补充、找答案等附加服务。
- 2、"仅部分预览"的文档,不可在线预览部分如存在完整性等问题,可反馈申请退款(可完整预览的文档不适用该条件!)。
- 3、如文档侵犯您的权益,请联系客服反馈,我们会尽快为您处理(人工客服工作时间:9:00-18:30)。
多个订单库存控制模型
库存控制模型多为被用在原材料、在制品,或完成货物需要超过一个时间或在一个正在进行的基础。
他们是最常见的生产管理和库存管理模型,在他们是常见的内部和外部供应链的步骤和客户送货在多个订单下的材料或产品的客户。
当只有一个订单或一把库存决策这被视为一个订单库存模型。
大多数库存软件设计为多个订单库存应用,有些人比别人更好的投资特点。
多个秩序的库存模型加以分类,是什么导致供应/生产/采购订单在供应。
供应、生产、采购订单可以被库存水平,通常是一个缓冲区或安全库存水平,为固定的顺序数量或一个规定的时间跨度。
这类文章的例子库存控制模型是以下几点:
异秩序和库存水平库存控制
经济订货批量(EOQ)
双仓制度
ABC仓储库存模型
优先发出(FIFO)
时间间隔库存控制
时间间隔的库存模型
一箱系统
当选择任何这些存货模型是重要的考虑:
-总库存成本包括控股成本
层——基础货架和库存
-可预见性
-重量比
多个秩序的库存模型也可以划分为建立秩序或建立股票的系统。
使用这些库存模型进行分析可以发现他们在各自的层面里。
经济订货批量(EOQ)库存管理模型
经济订货批量订单(EOQ)是多元的库存模型决定了一个最优固定订货量。
一旦库存水平下降到某一点上,称为采购点。
该模型也被称为问模型、固定的顺序数量模型,还是锯齿库存模型。
它是用来在库存管理,避免产品停工待料当有一定的交货时间,产品和稳定的需求模式。
该模型使用的以下信息产品被命令:
年度需求为产品(D)
假设年需求稳定
设置每一个订单成本为放置(S)
订单交货期在天(L)
一年一度的库存持有成本(H)
最优订货量Q)
库存订单触发水平(R)
推导了最优订货量(Q)是以下几点:
问=[(2 * D *)/ H]^(1/2)
^(1/2)=平方根的计算
答案Q是最优的订单量放置在同一时间当总库存水平达到库存订单触发水平(R)。
该模型也可用于安全库存。
推导了库存订单触发水平(右)如下:
R = d * L
在日常需求d产品。
这其中最受欢迎的库存控制模型,被广泛应用在许多行业、企业、和库存软件来管理库存水平和生产计划。
在一些生产的管理中,它是用于双箱形式库存系统双箱库存管理系统
双箱系统是常见的对装配系统和移动生产线在组件的增加对产品或项目正在建设。
这双箱系统就像它的名字所表示的那样,它是由两个组件或材料开始。
作为一个彬开始生产耗尽的材料和其他,充当缓冲区或安全库存。
当第一个箱是完全耗尽这个工人或是装配线上的工人切换到其他箱,类似于一个“先进先出”系统。
箱的开关可以被理解为一项看板信号的供应进程的特殊的组件制造、供应这个组件中,就在第二个槽时间耗完了所有的材料。
看板信号也可以产生一半在前箱、根据交货期为组件提供。
该系统在某种程度上类似的EOQ模型和安全库存盘点。
这是一个非常常见的系统应用于车辆生产的方法。
大小或数目每箱部件的使用通常是确定EOQ模型或一个时间周期库存模型。
ABC仓储和库存控制
在ABC仓储库存管理模型所有项目在库存分类仓库或由他们的美元体积分为三类,A、B、C型项目。
这允许库存细分控制器分离最重要的库存物品不太重要的项目,并允许控制器,以更专注于更好地管理存货价值较高的项目包括正确数量的安全库存避免停工待料。
美元的体积体积意味着库存使用或出售其在一年内美元价值乘以单位。
这个措施给一个明确的指示库存的重要性,不经常使用的物品可能是很有价值的,需要严密监测。
这库存系统通常被用来当库存管理资源稀缺和/或缺乏适当的库存管理系统的现状。
一旦分割的库存物品的职代会案例已完成仓库库存储存的地方,能够得到贯彻执行。
这些步骤来实现一种ABC仓储物流系统:
1 -行为调查/盘点的仓库里的所有库存物品
2 -编写需求数据和生产数据在过去的12个月内为每个项目成本为每项
3 名单存货有百分之多少的每一个项目的总库存。
4 -确定第一个几项加起来就是60% - 70%的总库存。
然后才能确定下一批存货项目之间加起来20 - 30%的总库存,这些将是B类的物品。
其余的物品留在名单被认为是C类型的项目。
这种情况应该非常相似的帕累托原理,可以在帕累托图图标表示
5-代替库存控制措施严格的项目和B项如果可能的话,要么以一个经济订货批量,或时间间隔管理模式。
6 -重新安排库存储存区域仓库或使一个项目是接近其使用分或者生产线,其次是B项,然后C项目。
确保正确的股票旋转和仓储物流系统如FIFO在不同的产品分类系统。
首先在先进先出的库存控制-先进先出法
一个FIFO仓库系统是一个库存管理系统,在第一次或先用古老的股票和证券或库存,最近收到的是只生产或使用或清理出去,直到所有库存在仓库里或储存之前被使用或清理出去。
这确保了最古老的股市是先使用,降低库存成本的过时。
它也被认为是理想的股票转动系统。
这库存系统的许多行业常用的有时是结合其他仓库、库存管理和库存系统模型等其他多种秩序模型 EOQ库存模型。
一种解释该股票的上市公司控股系统下图:
先进先出库存
第一个月第二个月第8个月第10个月
航运顾客或下一个工艺步骤第一新生产的单位购买
库存管理模型的时间间隔
时间间隔的库存模型存货管理模式库存订货、依靠期刊使用时间的推移引起的数量来回顾盘点库存持有并把订单。
该模型不需要不断的跟踪和库存水平只是在设定的时间间隔了,每天,每周,两周、月或甚至年刊。
它并没有与后果之模型探讨其复杂程度。
这是一个最好的留给项目模型缓慢移动或有很可预见的需求。
使用缓冲区或安全库存通常是推荐给任何要求,吸收异常侍立。
库存控股包括安全库存有可能成为过时的如果没有股票的旋转。
一个垃圾桶系统是一种典型的时间间隔库存管理模型。
模型依赖的时间间隔的平均每日的交货时间,需求及新秩序的时间间隔到达,历史的分析,以建立定单量。
推导了订货数量:
问= d(T + L)-q
在D:日常需求的物品或产品
在T:之间的时间间隔库存订单吗
在D:每天的平均需求为项目或产品
在Q:目前库存现货吗
同样重要的是要考虑库存已订购如果订货时间间隔短于订单交货时间。
存货缓冲区或安全库存如果需要可以确定的一个既定百分比大小或通过假设订单需求正态分布,利用z概率统计等数倍标准差标准差的需求量项目。
单一订单库存模型使用这个概率的方法。
一个箱库存控制系统
一个箱库存系统是一个简单的库存控制系统,取决于供给在固定的时间间隔。
必须将这些时间间隔按照槽尺寸、需求和交货时间的时间要补充箱。
物料或产品拉了下来,然后当它达到一个特定的时间点供应产生和看板是补充供应来源。
从本质上来说就是一个时间间隔管理模式。
一个箱库存系统是有用的,当需求库存系统是可以预测的,稳定的,过程中不需要大量的安全库存,这是双箱库存系统的对比。
库存管理成本
存货成本都是相关费用订货,保存和管理存货或股票操作和商业活动。
这些库存成本包括订购成本、持有成本,和短缺的成本。
管理存货成本是很重要的,因为它们可以是一个实质性的营商的成本,并可能会有所变动,从10%到40%的价值的库存。
因此,重要的是去理解和有能力管理好这些不同的存货成本制造生产、采购、物流、或库存持有尺寸确定决策包括安全库存水平。
精益生产原则可以用来管理库存量更有效率,从而有更严格的控制库存成本。
一些库存软件包允许来追踪某些存货成本,这个功能可以对一些生意是非常有用的。
不同的库存成本进一步解释如下:
-y订购成本:
这些包括订购一批费用、生产运行,或者购买了部分体外或产品。
成本,比如管理,订单成本包括成本批准运行一个库存管理和命令系统都包括在这一类。
-持有成本:
这些都是在握住库存费用或股票在贮存、仓库和管理其交货给顾客。
大部分这些成本可以量化的容易。
一些常见的库存持有成本包括:
仓储和物流成本、保险、腐败/破碎损失,过时的库存写清洗液,绑在一起的资本机会成本。
过时的库存成本通常是写出高库存建造或生产系统可能有某些股份有限转动和单个订单库存情况。
-短缺成本:
指亏成本费用,无形,跑步缺货,不能为客户提供商品的需求在一定时间和交货时间。
大多数的这些费用是难以量化。
影响一个库存短缺,和成本,主要涉及了销售和利润,失去顾客,缺货罚款和合同纠纷。