反应再生器安全技术
SH 3504-2000催化裂化装置反应再生系统设备施工及验收规范

2 壳体直径允许偏差为 mm,同一断面上最大直径与最小直径之差不得大于设计 0
直径的 0.5%。筒体直段的长度允许偏差为±3mm; 3 锥体表面用 300mm 钢板尺沿母线检查,其局部凸凹值不得大于 lmm。锥体下端插
入灰斗内的长度允许偏差+50 mm; 4 螺旋顶板表面应平整,螺旋线应圆滑过渡; 5 焊缝按设计要求检验完毕,内部焊缝加强高度均应打磨平滑,其局部凸凹值不
UDC
中 华 人 民 共 和 国 行业 标 准
P
SH 3504-2000
催化裂化装置反应再生系统设备
施工及验收规范
Specification for construction and acceptance of Reactor-regenerator system equipment of catalytic crakdng unit
4
b 一、二级旋风分离器接口处断面中心线应与筒体直段轴线平行,其平行度偏差不 应大子 2mm。
9 旋风分离器总长允许偏差为 ± 8 mm,同一装置中同一级任意两个旋风分离器总长 之差不得超过 6mm;
10 已衬里后供货的旋风分离器尚应检查衬里的质量,衬里质量应符合《隔热耐磨 混凝土衬里技术规范》SH3531 的有关要求。 3.2.2 翼阀制造质量应符合设计图样要求,若设计无要求,则应符合下列规定:
主编单位: 中国石化集团第四建设公司 主编部门: 中 国 石 油 化 工 集 团 公 司 批准部门: 国 家 石 油 和 化 学 工 业 局
2000—10—26 发布
2001—03—01 实施
国家石油和化学工业局 发 布
关于批准《石油化工厂区绿化设计规范》
等 27 项石油化工行业标准的通知
催化裂化工艺流程及主要设备

2023催化裂化工艺流程及主要设备pptcontents •概述•催化裂化工艺流程•催化裂化主要设备•工艺特点和操作规程•安全与环保•常见故障及排除方法•发展方向和新技术应用目录01概述催化裂化是一种将重质烃类转化为轻质烃类和液化气的过程,是石油化工中重要的二次加工手段之一。
催化裂化工艺主要采用流化床反应器,催化剂作为床层中的介质,在适宜的温度、压力和空速条件下进行反应。
催化裂化基本概念1催化裂化主要设备23流化床反应器是催化裂化的主要设备之一,分为单器、双器和多器系统。
反应器再生器是催化裂化中的重要设备,用于烧去催化剂表面的积炭,恢复催化剂活性。
再生器旋风分离器用于将反应和再生两个工艺流程分开,同时将催化剂从反应器物料中分离出来。
旋风分离器催化裂化工艺流程简介原料油进入反应器,在适宜的温度、压力和空速条件下进行反应。
分离出的催化剂进入再生器,烧去积炭恢复活性。
反应后的物料进入旋风分离器,将催化剂从物料中分离出来。
再生后的催化剂回到反应器物料中,继续参与反应。
02催化裂化工艺流程原料油缓冲在催化裂化工艺中,原料油首先需要进入缓冲罐,进行初步的脱水和脱盐处理。
原料油加热原料油通过加热炉加热到一定温度,以便能够进行催化裂化反应。
原料预处理催化裂化主要流程加热后的原料油被送到催化裂化反应器中,同时加入催化剂。
进料在催化裂化反应器中,原料油在催化剂的作用下发生裂化反应,生成轻质油品和小分子烃类。
裂化反应裂化反应后的油气和催化剂分离,油气进入分馏塔进行分离。
催化剂分离分离后的催化剂进入再生器烧焦再生,循环使用。
催化剂循环油气在分馏塔中根据沸点不同,分离成不同沸点的油品,如汽油、柴油和重油。
油品分馏分离出的油品通过一系列精制过程,如脱硫、脱氮、脱氧等处理,提高油品质量。
油品精制催化裂化过程中产生的气体,通过压缩、冷却和分离等步骤,得到液态烃和干气。
气体分离经过处理的油品和气体分别进入相应的储罐或装置进行储存或进一步加工。
什么是化工本质安全?本质安全详解
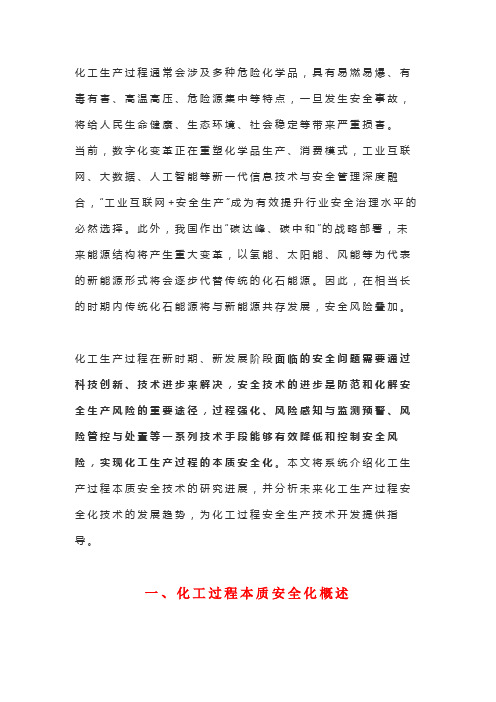
化工生产过程通常会涉及多种危险化学品,具有易燃易爆、有毒有害、高温高压、危险源集中等特点,一旦发生安全事故,将给人民生命健康、生态环境、社会稳定等带来严重损害。
当前,数字化变革正在重塑化学品生产、消费模式,工业互联网、大数据、人工智能等新一代信息技术与安全管理深度融合,“工业互联网+安全生产”成为有效提升行业安全治理水平的必然选择。
此外,我国作出“碳达峰、碳中和”的战略部署,未来能源结构将产生重大变革,以氢能、太阳能、风能等为代表的新能源形式将会逐步代替传统的化石能源。
因此,在相当长的时期内传统化石能源将与新能源共存发展,安全风险叠加。
化工生产过程在新时期、新发展阶段面临的安全问题需要通过科技创新、技术进步来解决,安全技术的进步是防范和化解安全生产风险的重要途径,过程强化、风险感知与监测预警、风险管控与处置等一系列技术手段能够有效降低和控制安全风险,实现化工生产过程的本质安全化。
本文将系统介绍化工生产过程本质安全技术的研究进展,并分析未来化工生产过程安全化技术的发展趋势,为化工过程安全生产技术开发提供指导。
一、化工过程本质安全化概述本质安全(i n h e r en t sa f e t y)概念最早由英国的T re vo r K l e tz 于1976年提出,其理念是从工艺源头上永久地消除风险,而不是单独靠控制系统、报警系统、联锁系统的使用来减小事故发生概率和减轻事故后果的严重性。
本质安全是绝对安全的理想状态,生产运行上很难达到,实际中需要通过本质安全化(i n h e r e n t l y s af e r)的一系列技术措施降低过程风险,使化工过程本质上更安全。
化工过程全生命周期的本质安全如图1所示,最小化、替代、缓和、简化这4个本质安全化策略适用于研发、设计、建设、操作、变更和维护等化工过程的整个生命周期。
工艺过程的本质安全化与被动型、主动型和程序型安全防护措施一起构成了化工过程的保护层,其中本质安全化工艺技术在所有保护层中处于最核心的部分,对安全风险控制起到决定性作用。
加氢装置实习报告

一、实习背景随着我国石油化工行业的快速发展,加氢技术在炼油、化工等领域发挥着越来越重要的作用。
为了深入了解加氢装置的操作原理、工艺流程以及设备维护等方面知识,我于2023年在某石油化工企业进行了为期一个月的加氢装置实习。
二、实习目的1. 熟悉加氢装置的工艺流程和设备结构;2. 掌握加氢装置的操作方法和安全注意事项;3. 增强实际操作能力,提高对化工生产过程的认知;4. 为今后的工作积累实践经验。
三、实习内容1. 加氢装置工艺流程加氢装置主要分为反应部分、再生部分和冷却部分。
反应部分包括固定床反应器、进料预热器、分离器等;再生部分包括再生加热炉、催化剂再生器等;冷却部分包括冷却器、分离器等。
(1)反应部分:加氢反应在固定床反应器中进行,原料油在加热炉加热后进入反应器,与催化剂接触,发生加氢反应。
反应后的油气混合物进入分离器,分离出氢气和反应产物。
(2)再生部分:催化剂在反应过程中逐渐失活,需要定期进行再生。
再生加热炉将催化剂加热至一定温度,使其活性恢复。
再生后的催化剂进入再生器,冷却、干燥,再次投入反应。
(3)冷却部分:反应后的油气混合物在冷却器中冷却,分离出液体和气体。
液体进入分离器,分离出汽油、柴油等产物;气体进入氢气分离器,分离出氢气。
2. 设备结构及操作(1)固定床反应器:反应器由筒体、管板、催化剂筐等组成。
操作时,需注意催化剂的装填、反应温度、压力等参数。
(2)再生加热炉:加热炉由炉膛、燃烧器、烟道等组成。
操作时,需注意燃料供应、空气流量、炉膛温度等参数。
(3)冷却器:冷却器由壳体、管束、进出口等组成。
操作时,需注意冷却水流量、进出口温度等参数。
3. 安全注意事项(1)操作人员需穿戴好防护用品,如安全帽、防护眼镜、手套等。
(2)严格遵守操作规程,不得擅自更改工艺参数。
(3)定期检查设备,发现异常情况及时上报。
(4)保持现场整洁,严禁烟火。
四、实习收获1. 通过实习,我对加氢装置的工艺流程、设备结构以及操作方法有了更深入的了解。
催化裂化装置操作安全技术(二篇)
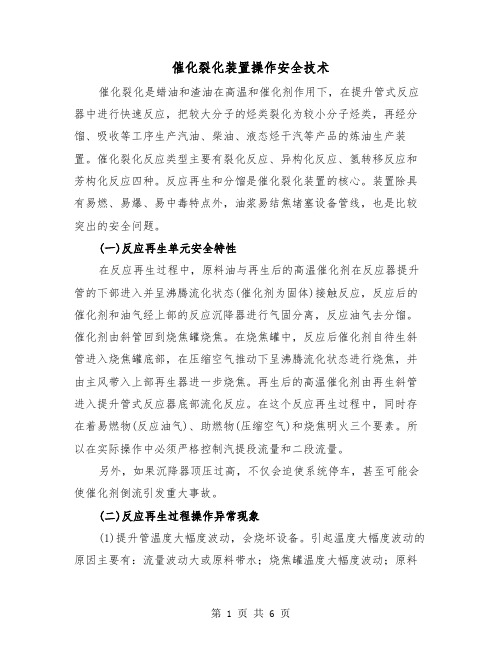
催化裂化装置操作安全技术催化裂化是蜡油和渣油在高温和催化剂作用下,在提升管式反应器中进行快速反应,把较大分子的烃类裂化为较小分子烃类,再经分馏、吸收等工序生产汽油、柴油、液态烃干汽等产品的炼油生产装置。
催化裂化反应类型主要有裂化反应、异构化反应、氢转移反应和芳构化反应四种。
反应再生和分馏是催化裂化装置的核心。
装置除具有易燃、易爆、易中毒特点外,油浆易结焦堵塞设备管线,也是比较突出的安全问题。
(一)反应再生单元安全特性在反应再生过程中,原料油与再生后的高温催化剂在反应器提升管的下部进入并呈沸腾流化状态(催化剂为固体)接触反应,反应后的催化剂和油气经上部的反应沉降器进行气固分离,反应油气去分馏。
催化剂由斜管回到烧焦罐烧焦。
在烧焦罐中,反应后催化剂自待生斜管进入烧焦罐底部,在压缩空气推动下呈沸腾流化状态进行烧焦,并由主风带入上部再生器进一步烧焦。
再生后的高温催化剂由再生斜管进入提升管式反应器底部流化反应。
在这个反应再生过程中,同时存在着易燃物(反应油气)、助燃物(压缩空气)和烧焦明火三个要素。
所以在实际操作中必须严格控制汽提段流量和二段流量。
另外,如果沉降器顶压过高,不仅会迫使系统停车,甚至可能会使催化剂倒流引发重大事故。
(二)反应再生过程操作异常现象(1)提升管温度大幅度波动,会烧坏设备。
引起温度大幅度波动的原因主要有:流量波动大或原料带水;烧焦罐温度大幅度波动;原料预热温度大幅度波动;两器差压波动;催化剂量波动;再生滑阀控制失灵。
对温度波动要查明原因,有针对性地采取措施。
如对原料进行脱水,稳定进料量和原料预热温度,稳定烧焦温度,调节两器差压。
如仪表失灵改用手动等。
(2)沉降器压力大幅波动。
如果沉降器出现压力大幅度波动,首先要准确判断异常原因,采取对应的处理措施。
如果是原料带水,要立即进行脱水。
进料量波动大时要稳定进料量。
其它原因如汽提蒸汽量及压力波动大,催化剂循环波动量大,以及分馏塔釜液位过高等,都要及时采取对应的调节控制措施。
催化裂化装置操作安全技术

催化裂化装置操作安全技术催化裂化装置是石油炼制过程中重要的装置之一,它能将较重的石油烃类分解成低碳烃和芳烃,提高汽油和石脑油的产量和质量。
然而,催化裂化装置操作安全技术至关重要,它关系到人身安全、生产效率和环境保护。
下面将介绍催化裂化装置操作安全技术的一些重要方面。
一、工艺检查与确认在催化裂化装置运行之前,必须进行详细的工艺检查与确认,以确保各种设备、管道和阀门的正常状态。
首先要检查催化剂的寿命和性能,确保其能够正常进行催化作用。
其次,需检查反应器和再生器的温度、压力、流量等参数,确保其在正常范围内。
此外,还需检查其它辅助设备和系统,如催化剂循环系统、冷却水系统等,以确保其正常运行。
只有在确认工艺安全性的前提下,才可以进行操作。
二、操作人员培训与资质要求催化裂化装置操作人员应接受系统的培训,并具备相应的资质要求。
在催化裂化装置的操作过程中,操作人员需熟悉各种设备的工作原理和操作方法,能够准确判断和处理不同的操作情况。
同时,操作人员还需掌握应急处置措施,能够迅速应对突发情况,确保安全。
三、标记与防护装置催化裂化装置中的各种设备和管道都应有明确的标记,以便操作人员识别和判断。
标记应包括设备和管道的名称、功能、压力、温度等信息。
此外,还需设置相应的防护装置,如喷淋系统、泄漏报警系统等,以及警示标志,提醒操作人员注意安全。
这样可以避免由于操作失误或设备故障造成的事故。
四、操作程序与规程催化裂化装置的操作应按照相应的程序和规程进行,包括开机、停机、换料、调整等各个环节。
操作程序应详细记录每个步骤的操作要求、注意事项和安全措施,操作人员需按照程序进行操作,确保各个步骤的顺利进行。
同时,还需定期检查和更新操作程序和规程,以适应不同的情况和要求。
五、事故预防与应急处置催化裂化装置操作过程中,事故的预防至关重要。
操作人员需严格遵守操作规程,不得违反操作程序进行操作。
同时,需定期检查设备和管道的状态,发现异常情况及时处理。
UOP连续重整第三代再生技术的应用
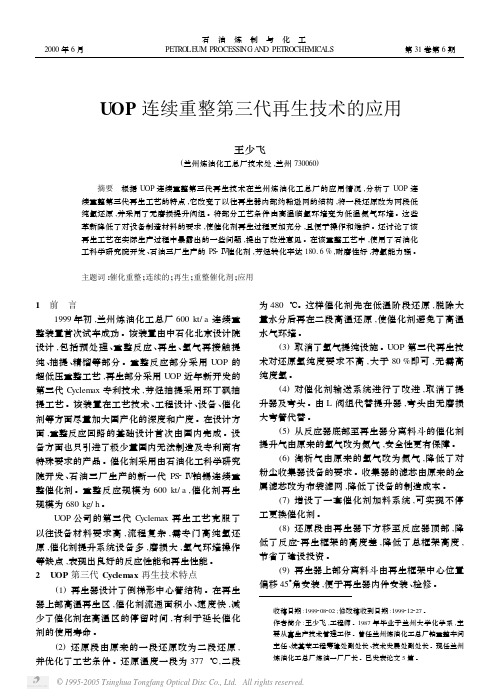
UOP连续重整第三代再生技术的应用王少飞(兰州炼油化工总厂技术处,兰州730060) 摘要 根据UOP连续重整第三代再生技术在兰州炼油化工总厂的应用情况,分析了UOP连续重整第三代再生工艺的特点,它改变了以往再生器内部约翰逊网的结构,将一段还原改为两段低纯氢还原,并采用了无磨损提升阀组。
将部分工艺条件由高温临氢环境变为低温氮气环境。
这些革新降低了对设备制造材料的要求,使催化剂再生过程更加充分,且便于操作和维护。
还讨论了该再生工艺在实际生产过程中暴露出的一些问题,提出了改进意见。
在该重整工艺中,使用了石油化工科学研究院开发、石油三厂生产的PS2Ⅳ催化剂,芳烃转化率达180.6%,耐磨性好,持氯能力强。
主题词:催化重整;连续的;再生;重整催化剂;应用1 前 言1999年初,兰州炼油化工总厂600kt/a连续重整装置首次试车成功。
该装置由中石化北京设计院设计,包括预处理、重整反应、再生、氢气再接触提纯、抽提、精馏等部分。
重整反应部分采用UOP的超低压重整工艺,再生部分采用UOP近年新开发的第三代Cyclemax专利技术,芳烃抽提采用环丁砜抽提工艺。
该装置在工艺技术、工程设计、设备、催化剂等方面尽量加大国产化的深度和广度。
在设计方面,重整反应回路的基础设计首次由国内完成。
设备方面也只引进了极少量国内无法制造及专利商有特殊要求的产品。
催化剂采用由石油化工科学研究院开发、石油三厂生产的新一代PS2Ⅳ铂锡连续重整催化剂。
重整反应规模为600kt/a,催化剂再生规模为680kg/h。
UOP公司的第三代Cyclemax再生工艺克服了以往设备材料要求高,流程复杂,需专门高纯氢还原,催化剂提升系统设备多,磨损大,氢气环境操作等缺点,表现出良好的反应性能和再生性能。
2 U OP第三代Cyclem ax再生技术特点(1)再生器设计了倒梯形中心管结构。
在再生器上部高温再生区,催化剂流通面积小、速度快,减少了催化剂在高温区的停留时间,有利于延长催化剂的使用寿命。
重整再生器检修方案

26
进口切割机
1台
27
钢丝绳
1.2m、2.5m、5m
各4件
28
安全带
8个
29
盲板
DN700 2块 DN650 2块 DN300 2块 DN50 15块 DN80 2块
23块
30
绳梯
4付
六、人力资源
本次作业为抢修作业,为了提高检修效率,将检修人员分为9个小组,每个小组完成不同的工作,各工种需要密切配合,采取24小时不间断作业。(具体工作见附录1)
加热炉集合管
件
8
10
0
2011.5.30
57
金属缠绕垫片
D500-5.0
D311人孔
件
2
0
2
2011.5.30
58
金属缠绕垫片
D200-5.0 2323
D311
件
12
5
7
2011.5.30
59
双头螺栓
M33*225 25CrMOVA
D311
件
5
0
5
2011.5.30
60
金属缠绕垫
C250-2.0
D308
2套
15
手钳
8寸 3把
3
16
毛刷
6
17
气密试验用喷壶
2
18
气密试验用塑料小筒
2
19
气密试验用肥皂粉
按需领取
20
记号笔
6
21
铜刷
10
22
钢丝刷
10
23
铜棒
Φ50 2个、Φ30 2个、Φ20 2个
6
24
焊接材料
- 1、下载文档前请自行甄别文档内容的完整性,平台不提供额外的编辑、内容补充、找答案等附加服务。
- 2、"仅部分预览"的文档,不可在线预览部分如存在完整性等问题,可反馈申请退款(可完整预览的文档不适用该条件!)。
- 3、如文档侵犯您的权益,请联系客服反馈,我们会尽快为您处理(人工客服工作时间:9:00-18:30)。
仅供参考[整理] 安全管理文书
反应再生器安全技术
日期:__________________
单位:__________________
第1 页共5 页
反应再生器安全技术
(1)进料量减少
(2)再生剂循环量过大,易造成分馏系统大幅度波动,只产气体,下部液体少,冲塔等事故
(1)原料油带水严重
(2)再生器循环量减少或中断,造成沉降压力上升,气体段藏量急降,待生催化剂带油,再生器超温,严重时烟囱带黄烟
④减少待生催化剂,去再生器的量
⑤温度太低(重催低于485℃)启动原料自动保护联锁装置切断进料
(2)再生剂循环量减少或中断
检查再生滑阀并且手动控制
滑阀无问题要考虑是否是再生管被堵塞,尤其是滑阀无问题,催化剂中断,应停工处理
(3)分馏塔液面高
(4)分馏冷回流启动大或冷空出现问题(5)气压机故障停车,易造成反应--再生器压力波动大,沉降器油气压力波动大,再生器超温,烧坏设备。
沉降器旋风分离器工作不稳定造成油浆中固体含量增加,若处理不好,造成油浆系统堵塞不畅等
(2)降低分馏塔底页面多甩油浆,提高分馏塔下部温度少产油浆(3)检查好塔顶空冷冷却温度等
(4)必要时启动原料自动保护联锁装置
(2)重油催化、原料轻重不均
(3)再生取热系统故障造成再生器以及烟气后部系统内构件损坏,
第 2 页共 5 页
损坏烟道,催化剂跑损等
(2)调整好重油催化的重油与蜡油的比例
(3)分析再生取热系统故障原因后要加大取热量以降低再生温度,自动联锁启用,保护装置安全
(2)两器开工升温不按升温曲线,升温波动大
(3)两器超温频繁,反应再生出现热点(壁温在500℃以上)强度降低,增加磨损,产生催化剂泄露,处理不当,停工斜管、提升管衬里脱落,造成再生滑阀堵塞,斜管堵塞,催化剂循环量减少或中止,装置大幅度降量或停工
(1)严把施工质量关,选用好的绝缘耐磨衬里
(2)两器尤其在装置第一次开工,严格按升温要求烘干衬里
(3)严格操作,做到原料、操作条件平衡,保证水、电、气、风平衡,防止两器频繁超温
(4)加强两器日常检查,使用红外温度计和夜间闭烟检查,及早发现过热点,及早维护
(3)再生压力控制或烟机突然故障停车
(4)再生器取热管爆管再生器超压易引起主风机、增压机飞动,从而引起无主风,引起催化剂倒入,主风机恶性事故或再生压力太高,再生剂压空,空气要进入沉降室的重大恶性事故(催化剂倒流)(1)再生压力控制手动,控制好再生压力
(2)再生器主风进量改手动,控制入再生器风量稳定
(3)三机组时烟机停车则主风机要减少一半(二台主风机并联操作),反应再生降压操作,若烟机与主风机分体,只发电,则控制好烟气放空
第 3 页共 5 页
(4)取热器坏,停用取热器,同时要调解好原料,降低生焦油量以保证热平衡
(5)造成倒流迹象启动主风、原料自动保护联锁装置
(2)沉降室中油气停留时间长
(3)大气管线保温不好,结焦焦块堵塞,能分离造成催化剂进分馏系统,加速油浆系统磨损和堵塞,进入待生斜管或在待生催化剂出口结焦、造成待生催化剂进不了再生器而停工
(1)选用新型提升管出口的快速分离器,减少油气在沉降室中停留时间
(2)大油气线改用冷壁管,降低油气管的温差,减少结焦
(3)采用新型汽提段,采用滤油设施,防止焦块进入待生斜管
(4)采用高效喷嘴,提高原料雾化粒度
第 4 页共 5 页
仅供参考[整理] 安全管理文书
整理范文,仅供参考!
日期:__________________
单位:__________________
第5 页共5 页。