后钢板弹簧吊耳的加工工艺设计详解
{生产工艺技术}后钢板弹簧吊耳工艺设计说明书附工艺卡

{生产工艺技术}后钢板弹簧吊耳工艺设计说明书附工艺卡一、产品简介后钢板弹簧吊耳是一种用于吊装物体的金属零件,常用于汽车、机械等行业的装配过程中。
它由钢板经过冲压成形,具有轻巧、坚固和可靠的特点。
二、工艺流程1.材料准备:选择优质的高强度钢板作为原材料。
根据产品图纸和要求,将钢板切割成合适的尺寸和形状。
2.表面处理:对钢板进行酸洗处理,去除表面的氧化物和杂质,以提高表面质量和粘附力。
3.工装设计:根据产品图纸和要求,设计制作冲压模具和模具夹具,确保工艺的精度和效率。
4.冲压成形:将经过表面处理的钢板放入冲床中,通过冲压模具施加压力,使钢板按照产品图纸的形状和尺寸进行成形。
5.冲孔:根据产品要求,在钢板上进行冲孔处理,以便后续组装和连接。
6.清洗:将冲压成形的钢板进行清洗,去除冲床过程中产生的切屑和残留物,保证产品的整洁和质量。
7.表面处理:对清洗后的钢板进行防锈处理,以提高产品的抗腐蚀性能和表面光洁度。
8.检验:对成品进行严格的质量检验,包括外观质量、尺寸精度和冲孔位置等方面,确保产品符合技术要求。
三、工艺卡工艺卡是对整个工艺流程的详细记录和规范,包括每个工序的操作步骤、质量控制要点和注意事项等。
下面是后钢板弹簧吊耳的一份工艺卡示例:工序:冲压成形设备:冲床操作员:XXX日期:XXXX年XX月XX日产品:后钢板弹簧吊耳1.将经过表面处理的钢板放置在冲床上,调整模具的位置和夹具的固定度。
2.打开冲床电源,调整冲床的压力和行程,以适应钢板的厚度和冲孔要求。
3.进行冲压成形,注意观察冲床的运行情况和成形效果,及时调整和纠正。
4.冲床完成后,取出成品,并进行必要的清洗和防锈处理。
5.进行产品的质量检验,包括外观质量、尺寸精度和冲孔位置等方面。
6.合格产品进行包装,不合格产品返工或报废。
四、总结后钢板弹簧吊耳的生产工艺按照以上流程进行,能够保证产品的质量和性能。
工艺卡的使用和记录对于工艺的规范和改进具有重要意义,要经常总结经验教训,不断改进和优化工艺流程,提高产品的质量和生产效率。
机械制造基础课程设计后钢板弹簧吊耳的加工工艺
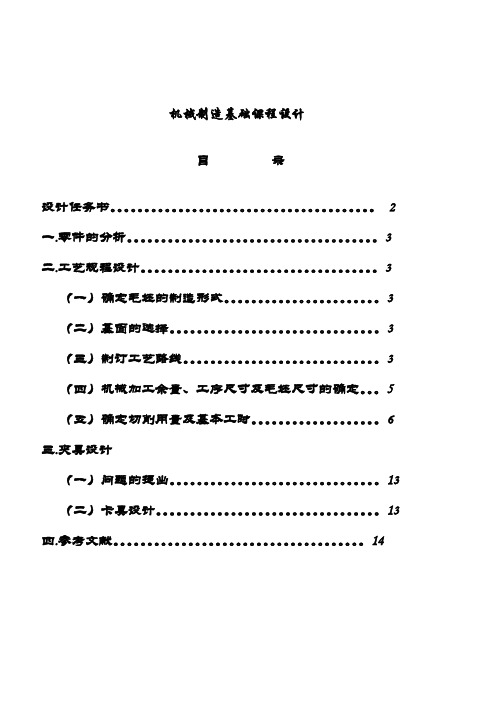
机械制造基础课程设计目录设计任务书。
2一.零件的分析。
3二.工艺规程设计。
3(一)确定毛坯的制造形式。
3 (二)基面的选择。
3 (三)制订工艺路线。
3 (四)机械加工余量、工序尺寸及毛坯尺寸的确定。
5 (五)确定切削用量及基本工时。
6 三.夹具设计(一)问题的提出。
13 (二)卡具设计。
13 四.参考文献。
14题目:制定后钢板弹簧吊耳的加工工艺,钻Ø30孔的钻床夹具要求:1.中批生产;2.尽量选用通用夹具。
内容:1.填写设计任务书;2.制订一个中等零件的加工工艺过程,填写工艺过程卡和工序卡各一张;3.设计指导教师指定的工序夹具,绘制全套夹具图纸,要求用计算机绘图;4.编写设计说明书一份,按照毕业论文的格式写,要求打印文稿。
一.零件的分析零件的工艺分析后钢板弹簧吊耳共有三组加工表面,现分述如下:1)以Ø3705.00+mm 孔为中心的加工表面这一组加工表面包括:一个Ø3705.00+mm 的孔,尺寸为762.06.0+-mm 的与Ø3705.00+mm 孔相垂直的平面,其中主要加工表面为Ø3705.00+mm 的孔; 2)以Ø30045.00+mm 孔为中的加工表面这一组加工表面包括:两个Ø30045.00+mm 的孔,以及尺寸为77074.00+与两个Ø30045.00+mm 孔相垂直的内平面,以及两个孔的外表面;3)以Ø10.5mm 孔为中心的加工表面 这一组加工表面包括:两个Ø10.5mm 的孔一. 工艺规程设计(一) 确定毛坯的制造形式零件材料为35钢,考虑到该零件在汽车中的受力并保证零件的工作可靠性,零件为中批生产,因此,毛坯可采用模锻成型 (二) 基面的选择基准面选择是工艺规程设计中的重要工作之一。
基面选择的正确与合理,可以使加工质量得到保证,生产效率得以提高。
否则,加工工艺过程中会问题百出,更有甚者,还会造成零件大批报废,使生产无法正常进行。
后钢板弹簧吊耳加工工艺及夹具设计
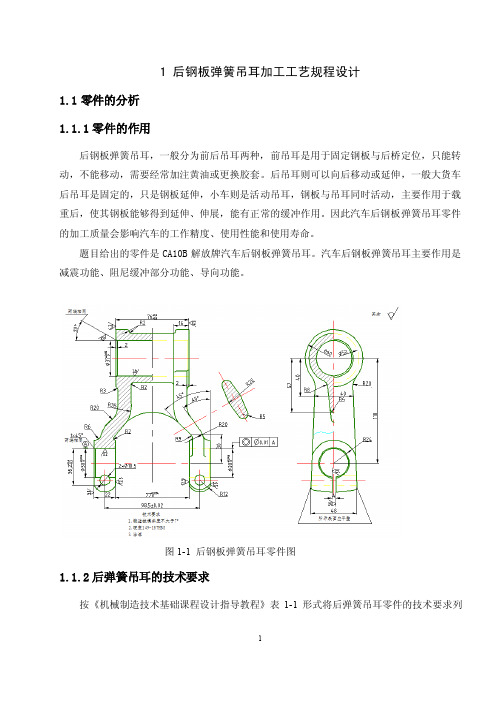
1 后钢板弹簧吊耳加工工艺规程设计1.1零件的分析1.1.1零件的作用后钢板弹簧吊耳,一般分为前后吊耳两种,前吊耳是用于固定钢板与后桥定位,只能转动,不能移动,需要经常加注黄油或更换胶套。
后吊耳则可以向后移动或延伸,一般大货车后吊耳是固定的,只是钢板延伸,小车则是活动吊耳,钢板与吊耳同时活动,主要作用于载重后,使其钢板能够得到延伸、伸展,能有正常的缓冲作用。
因此汽车后钢板弹簧吊耳零件的加工质量会影响汽车的工作精度、使用性能和使用寿命。
题目给出的零件是CA10B解放牌汽车后钢板弹簧吊耳。
汽车后钢板弹簧吊耳主要作用是减震功能、阻尼缓冲部分功能、导向功能。
图1-1 后钢板弹簧吊耳零件图1.1.2后弹簧吊耳的技术要求按《机械制造技术基础课程设计指导教程》表1-1形式将后弹簧吊耳零件的技术要求列于下表2-1中:表1-1 后弹簧吊耳零件的技术要求表加工表面 尺寸及技术要求 公差及精度等级表面粗糙度Ra/m μ 形位公差/mmmm 60φ两外圆端面mm2.06.076-- IT12 6.3mm 05.0037+φ孔mm 05.0030+IT8 1.6 R24内侧面 54mm IT12 12.5 R24外侧面54mmIT13 50mm 045.0030+φ孔mm 045.0030+IT8 1.6 ◎ φ0.01 Amm 5.10φ孔 mm 5.10IT12 12.5 开口槽4mmIT13501.1.3后钢板弹簧吊耳的工艺分析由后钢板弹簧吊耳零件图知可将其分为两组加工表面。
它们相互间有一定的位置要求。
现分析如下:(1)以60mm φ两外圆端面为主要加工表面的加工面。
这一组加工表面包括:。
60mm φ两外圆端面的铣削,加工mm 05.0037φ的孔,其中60mm φ两外圆端面表面粗糙度要求为 6.3Ra m μ,mm 05.0037φ的孔表面粗糙度要求为 1.6Ra m μ(2)以mm 045.0030φ孔为主要加工表面的加工面。
后钢板弹簧吊耳工艺流程设计(修改整合版)讲解
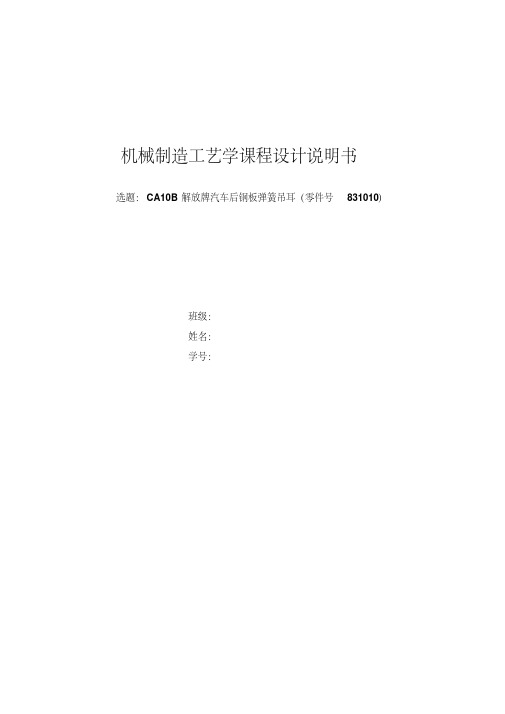
机械制造工艺学课程设计说明书选题:CA10B解放牌汽车后钢板弹簧吊耳(零件号831010)班级:姓名:学号:一、零件的分析(一)零件的作用题目给出的零件是CA10B解放牌汽车后钢板弹簧吊耳。
后钢板弹簧吊耳的主要作用是载重后,使钢板能够得到延伸,伸展,能有正常的缓冲作用。
因此汽车后钢板弹簧吊耳零件的加工质量会影响汽车的工作精度、使用性能和寿命。
汽车后钢板弹簧吊耳主要作用是减震功能、阻尼缓冲部分功能、导向功能。
两端的卷耳用销子铰接在车架的支架上。
这样,通过钢板弹簧将车桥与车身连接起来,起到缓冲、减振、传力的作用。
图2.1 后钢板弹簧吊耳零件图(二)零件的工艺分析由后钢板弹簧吊耳零件图知可将其分为两组加工表面。
它们相互间有一定的位置要求。
现分析如下:(1)以两外圆端面为主要加工表面的加工面。
这一组加工表面包括:两外圆端面的铣削,加工的孔,其中两外圆端面表面粗糙度要求为,的孔表面粗糙度要求为(2)以孔为主要加工表面的加工面。
这一组加工表面包括:2个的孔,2个的孔、2个孔的内外两侧面的铣削,宽度为4的开口槽的铣削,2个在同一中心线上数值为的同轴度要求。
其中2个的孔表面粗糙度要求为,2个的孔表面粗糙度要求为,2个的孔的内侧面表面粗糙度要求为,2个的孔外侧面表面粗糙度要求为,宽度为4的开口槽的表面粗糙度要求为。
在两组加工表面之间没有一定的位置要求,先加工哪一组表面都可以,现计划是加工第一组表面,再以第一组为基准加工第二组表面。
二、工艺规程设计(一)确定毛坯的制造形式零件材料为35钢。
考虑零件在工作中的情况,零件在汽车后后钢板中支架钢板,受到各种不同的振荡,有减震功能、阻尼缓冲部分功能、导向功能作用,因此应该选择锻件,以使金属纤维尽量不被切断,保证零件工作可靠。
在初定义,本零件为大批量生产,而且零件的轮廓尺寸不大,在造型中可采用模锻成型。
(二)基准的选择基准选择是工艺规程设计中的重要工作之一。
基准选择得正确与合理,可以使加工质量得到保证,生产率得以提高。
机械工艺夹具毕业设计5后钢板弹簧吊耳的加工工艺
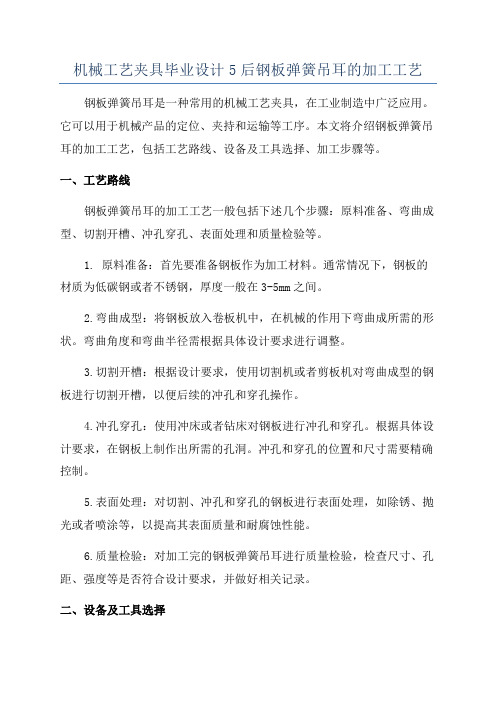
机械工艺夹具毕业设计5后钢板弹簧吊耳的加工工艺钢板弹簧吊耳是一种常用的机械工艺夹具,在工业制造中广泛应用。
它可以用于机械产品的定位、夹持和运输等工序。
本文将介绍钢板弹簧吊耳的加工工艺,包括工艺路线、设备及工具选择、加工步骤等。
一、工艺路线钢板弹簧吊耳的加工工艺一般包括下述几个步骤:原料准备、弯曲成型、切割开槽、冲孔穿孔、表面处理和质量检验等。
1. 原料准备:首先要准备钢板作为加工材料。
通常情况下,钢板的材质为低碳钢或者不锈钢,厚度一般在3-5mm之间。
2.弯曲成型:将钢板放入卷板机中,在机械的作用下弯曲成所需的形状。
弯曲角度和弯曲半径需根据具体设计要求进行调整。
3.切割开槽:根据设计要求,使用切割机或者剪板机对弯曲成型的钢板进行切割开槽,以便后续的冲孔和穿孔操作。
4.冲孔穿孔:使用冲床或者钻床对钢板进行冲孔和穿孔。
根据具体设计要求,在钢板上制作出所需的孔洞。
冲孔和穿孔的位置和尺寸需要精确控制。
5.表面处理:对切割、冲孔和穿孔的钢板进行表面处理,如除锈、抛光或者喷涂等,以提高其表面质量和耐腐蚀性能。
6.质量检验:对加工完的钢板弹簧吊耳进行质量检验,检查尺寸、孔距、强度等是否符合设计要求,并做好相关记录。
二、设备及工具选择根据上述加工工艺路线,需要选用以下设备和工具:1.卷板机:用于将钢板进行弯曲成型。
2.切割机或者剪板机:用于对弯曲成型的钢板进行切割开槽。
3.冲床或者钻床:用于对钢板进行冲孔和穿孔。
4.表面处理设备:如除锈机、抛光机或者喷涂设备等,根据需要选择合适的设备。
5. 测量工具:如卷尺、micrometer千分尺等,用于对加工尺寸进行测量。
6.保护设备:如手套、护目镜、防护罩等,用于保护操作人员的安全。
三、加工步骤钢板弹簧吊耳的加工步骤如下:1.准备好加工所需的钢板材料,确保其尺寸和材质符合设计要求。
2.将钢板放入卷板机中,根据设计要求将其进行弯曲成型。
3.取出弯曲成型的钢板,根据设计要求进行切割开槽。
后钢板弹簧吊耳加工工艺及夹具设计

后钢板弹簧吊耳加工工艺及夹具设计引言后钢板弹簧吊耳是一种常见的机械零部件,用于连接弹簧和机械结构,起到支撑和悬挂的作用。
本文将介绍后钢板弹簧吊耳的加工工艺以及夹具设计的相关内容。
弹簧吊耳加工工艺弹簧吊耳的加工工艺主要包括以下几个步骤:第一步:材料准备根据设计要求,选取合适的材料进行加工。
常用的材料有碳素钢、不锈钢等。
材料的选择要考虑到强度、硬度和耐腐蚀性等因素。
第二步:材料切割将选取的材料按照尺寸要求进行切割。
常用的切割方式有剪切、切割机和激光切割等。
切割时要注意材料的尺寸和形状的精准度,避免产生裂纹和变形。
第三步:弯曲成型将切割好的材料放入弯曲机中进行成型。
根据设计要求和工艺要求,将材料弯曲成所需的形状。
弯曲时要控制好弯曲角度和弯曲半径,避免产生裂纹和变形。
第四步:表面处理对成型后的弹簧吊耳进行表面处理,以提高强度和耐腐蚀性。
常用的表面处理方式有镀锌、喷涂和电泳等。
表面处理后的弹簧吊耳外观更加美观,能够延长使用寿命。
第五步:组装将表面处理好的弹簧吊耳连接到机械结构上。
根据设计要求和安装要求,采用焊接、螺纹连接或其他连接方式进行组装。
组装时要保证弹簧吊耳与机械结构之间的连接牢固,避免发生松动或脱落。
夹具设计夹具是用来固定工件的工具,用于在加工和装配过程中保持工件的稳定性和一致性。
在后钢板弹簧吊耳的加工过程中,夹具设计起到了至关重要的作用。
夹具设计的主要考虑因素如下:工件定位在夹具设计中,首先要考虑的是工件的定位。
通过合理的定位方式,保证工件在加工过程中的位置和姿态的一致性,以保证加工精度。
夹持力夹具设计还要考虑到夹持力的大小。
夹持力要足够大,以确保工件在加工过程中不会发生移动或变形。
同时,夹持力应该均匀分布,避免对工件造成不均匀的应力。
刀具接近夹具设计还要考虑刀具与工件之间的距离。
刀具要能够充分接近工件,以提高加工效率和加工质量。
局部加强结构夹具设计中,对于高应力区域需要进行局部加强结构设计。
通过在夹具的关键部位增加加强筋或支撑结构,来增强夹具的刚度和稳定性。
后钢板弹簧吊耳加工工艺及其夹具设计-加工工艺设计-毕业论文

目录1 摘要---------------------------------------------------------------------------------------------------12后钢板弹簧吊耳加工工艺流程设计-----------------------------------22.1 零件分析----------------------------------------------------------------------------------22.2定位基准的选择-----------------------------------------------------------------32.3制定工艺路线----------------------------------------------------------------42.4确定工序尺寸及加工余量--------------------------------------------52.5确定切削用量及基本工时-----------------------------------------73铣削后钢板弹簧吊耳内侧面的夹具设计----------------------------------14 3.1粗铣后钢板弹簧吊耳内侧面的夹具设计--------------------------------------14 3.2定位基准的选择以及定位方案的分析--------------------------------------14 3.3夹紧力和铣削力的计算-------------------------------------------------------143.4对刀装置的设计---------------------------------------------------------------154加工φ30mm孔的夹具设计-----------------------------------------------164.1加工φ30mm孔的夹具设计--------------------------------------------164.2定位基准的选择以及定位方案的分析--------------------------------174.3夹紧力和铣削力的计算------------------------------------------------194.4夹具的精度分析---------------------------------------------------------224.5夹具装置的简要说明------------------------------------------------------225加工φ10.5mm孔的夹具设计-----------------------------------------------235.1加工φ10.5mm孔的夹具设计------------------------------234.2定位基准的选择以及定位方案的分析--------------------------------174.3夹紧力和铣削力的计算------------------------------------------------194.4夹具的精度分析---------------------------------------------------------224.5夹具装置的简要说明------------------------------------------------------22摘要在夹具的设计过程中,最重要的主要是被加工零件的定位、夹紧等问题。
后钢板弹簧吊耳工艺流程设计
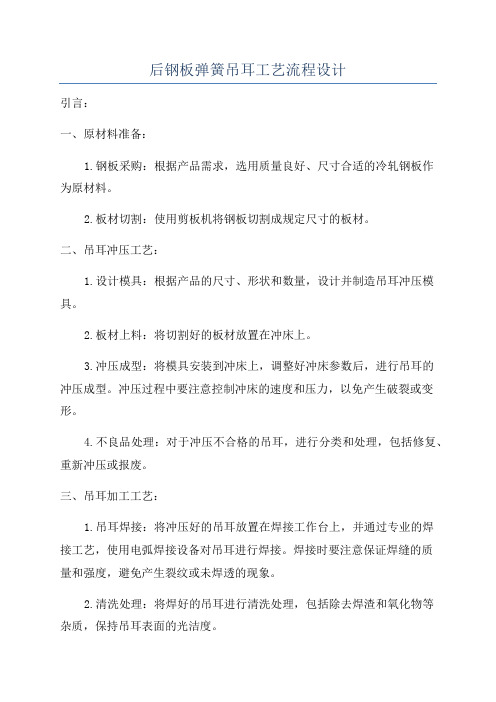
后钢板弹簧吊耳工艺流程设计引言:一、原材料准备:1.钢板采购:根据产品需求,选用质量良好、尺寸合适的冷轧钢板作为原材料。
2.板材切割:使用剪板机将钢板切割成规定尺寸的板材。
二、吊耳冲压工艺:1.设计模具:根据产品的尺寸、形状和数量,设计并制造吊耳冲压模具。
2.板材上料:将切割好的板材放置在冲床上。
3.冲压成型:将模具安装到冲床上,调整好冲床参数后,进行吊耳的冲压成型。
冲压过程中要注意控制冲床的速度和压力,以免产生破裂或变形。
4.不良品处理:对于冲压不合格的吊耳,进行分类和处理,包括修复、重新冲压或报废。
三、吊耳加工工艺:1.吊耳焊接:将冲压好的吊耳放置在焊接工作台上,并通过专业的焊接工艺,使用电弧焊接设备对吊耳进行焊接。
焊接时要注意保证焊缝的质量和强度,避免产生裂纹或未焊透的现象。
2.清洗处理:将焊好的吊耳进行清洗处理,包括除去焊渣和氧化物等杂质,保持吊耳表面的光洁度。
3.表面处理:根据客户要求,对吊耳进行防锈、喷涂、镀铬等表面处理,提高吊耳的耐腐蚀性和美观度。
四、产品检验和包装:1.外观检验:对吊耳进行外观检验,包括尺寸、形状、焊接质量等方面的检查。
2.力学性能测试:使用拉力试验机对吊耳的负荷能力进行测试,保证吊耳的可靠性。
3.包装:将合格的吊耳进行包装,通常采用纸箱或木箱进行包装,标明产品名称、规格、数量等信息,确保产品的安全运输。
五、工艺优化:1.模具设计和制造:根据实际生产情况,对模具进行优化,提高冲压效率和质量。
2.自动化生产设备投资:引进自动化冲压设备和焊接设备,实现生产过程的自动化,提高生产效率和产品质量。
3.工艺参数调整:通过对各个工艺环节的工艺参数进行调整和优化,降低生产成本,提高产品质量。
结论:通过对后钢板弹簧吊耳工艺流程进行设计和优化,可以提高生产效率、降低生产成本、提高产品质量,从而满足市场需求,提升企业竞争力。
同时,工艺优化还可以减少能源消耗和废品产生,实现可持续发展的目标。
- 1、下载文档前请自行甄别文档内容的完整性,平台不提供额外的编辑、内容补充、找答案等附加服务。
- 2、"仅部分预览"的文档,不可在线预览部分如存在完整性等问题,可反馈申请退款(可完整预览的文档不适用该条件!)。
- 3、如文档侵犯您的权益,请联系客服反馈,我们会尽快为您处理(人工客服工作时间:9:00-18:30)。
机械制造基础课程设计题目:制定后钢板弹簧吊耳的加工工艺,设计铣4mm工艺槽的铣床夹具班级:学生:指导教师:目录设计任务书……………………………………………一.零件的分析………………………………………二.工艺规程设计………………………………………(一)确定毛坯的制造形式………………………………(二)基面的选择…………………………………………(三)制订工艺路线………………………………………(四)机械加工余量、工序尺寸及毛坯尺寸的确定……(五)确定切削用量及基本工时…………………………三.夹具设计(一)问题的提出…………………………………………(二)卡具设计……………………………………………四.参考文献…………………………………………………哈尔滨理工大学机械制造工艺及夹具课程设计任务书题目:制定后钢板弹簧吊耳的加工工艺,钻Ø37孔的钻床夹具要求:1.中批生产;2.尽量选用通用夹具。
内容:1.填写设计任务书;2.制订一个中等零件的加工工艺过程,填写工艺过程卡和工序卡各一张;3.设计指导教师指定的工序夹具,绘制全套夹具图纸,要求用计算机绘图;4.编写设计说明书一份,按照毕业论文的格式写,要求打印文稿。
一.零件的分析零件的工艺分析后钢板弹簧吊耳共有三组加工表面,现分述如下:1)以Ø3705.0+mm孔为中心的加工表面这一组加工表面包括:一个Ø3705.0+mm的孔,尺寸为762.06.0+-mm的与Ø3705.00+mm孔相垂直的平面,其中主要加工表面为Ø3705.0+mm的孔;2)以Ø30045.0+mm孔为中的加工表面这一组加工表面包括:两个Ø30045.0+mm的孔,以及尺寸为77074.00+与两个Ø30045.00+mm 孔相垂直的内平面,以及两个孔的外表面;3)以Ø10.5mm孔为中心的加工表面这一组加工表面包括:两个Ø10.5mm的孔一.工艺规程设计(一)确定毛坯的制造形式零件材料为35钢,考虑到该零件在汽车中的受力并保证零件的工作可靠性,零件为中批生产,因此,毛坯可采用模锻成型(二)基面的选择基准面选择是工艺规程设计中的重要工作之一。
基面选择的正确与合理,可以使加工质量得到保证,生产效率得以提高。
否则,加工工艺过程中会问题百出,更有甚者,还会造成零件大批报废,使生产无法正常进行。
(1)粗基准的选择。
以Ø30mm孔一侧端面为粗基准,以消除z,x,y三个自由度,然后加一个辅助支承。
(2)精基准的选择。
根据基准重合和互为基准原则,选用设计基准作为精基准,当设计基准与工序基准不重合时,应该进行尺寸换算。
(三)制订工艺路线制订工艺路线的出发点,应当是使零件的几何形状,尺寸精度及位置精度等技术要求得到合理的保证。
在生产纲领为中批生产的条件下,可以考虑采用万能性机床配以专用夹具来提高生产效率。
除此以外,还应当考虑经济效率,以便使生产成本尽量下降。
1.工艺路线方案一工序Ⅰ粗铣Ø37mm孔端面。
工序Ⅱ粗镗Ø37mm孔,倒角1.5×45°。
工序Ⅲ粗铣Ø30mm孔外端面。
工序Ⅳ粗铣Ø30mm孔内端面。
工序Ⅴ扩,粗铰Ø 30mm孔并加工倒角1×45°。
工序Ⅵ粗镗Ø37mm孔。
工序Ⅶ半精铣Ø37mm孔端面。
工序Ⅷ半精铣Ø37mm孔端面。
工序Ⅸ钻2-Ø10.5mm孔。
工序Ⅹ铣宽为4mm的槽工序Ⅺ去毛刺。
工序Ⅻ检查。
2.工艺路线方案二工序Ⅰ粗铣Ø37mm孔端面。
工序Ⅱ粗镗Ø37mm孔,倒角1.5×45°。
工序Ⅲ粗铣Ø30mm孔外端面。
工序Ⅳ粗铣Ø30mm孔内端面。
工序Ⅴ扩,粗铰Ø 30mm孔并加工倒角1×45°。
工序Ⅵ粗镗Ø37mm孔。
工序Ⅶ半精铣Ø37mm孔端面。
工序Ⅷ半精铣Ø37mm孔端面。
工序Ⅸ钻2-Ø10.5mm孔。
工序Ⅹ铣宽为4mm的槽工序Ⅺ去毛刺。
工序Ⅻ检查。
工艺方案的比较与分析上述两个工艺方案的特点在于:方案一是先加工Ø37mm孔端面,再以该加工平面为基准加工其余平面,最后加工各个孔;方案二是先以Ø30mm孔外端面为基准加工Ø37mm孔端面,再以Ø37mm孔端面为基准加工其它端面和孔。
两相比较可以看出,方案二遵循互为基准原则能够较好的保证加工精度,对设备要求较低,而方案一工序比较集中,考虑实际设备条件,可将两个方案进行综合考虑。
具体工艺过程如下:工序Ⅰ锻造毛坯工序Ⅱ时效处理去应力工序Ⅲ铣Ø37mm孔端面。
工序Ⅳ扩,粗铰,精铰Ø37mm孔并加工倒角1.5×45°。
工序Ⅴ 铣尺寸为77mm 的孔端面。
工序Ⅵ 粗铣Ø30mm 孔端面。
工序Ⅶ 钻2-Ø 10.5mm 孔。
工序Ⅷ 扩,粗铰Ø 30mm 孔并加工倒角1×45° 工序Ⅸ 铣宽为4mm 的槽 工序Ⅹ 去毛刺 工序Ⅺ 检查。
(四)机械加工余量、工序尺寸及毛坯尺寸的确定“后钢板弹簧吊耳”零件材料为35钢,毛坯重量约为2.6Kg ,生产 类型为中批生产,采用锻造。
根据上述原始资料及加工工艺,分别确定各加工表面的饿机械加工余量 工序尺寸及毛坯尺寸如下: 1.Ø37mm 孔毛坯为空心,参照《机械加工工艺手册》,确定工序尺寸为 Z=2.6mm 。
由锻件复杂系数为S1,锻件材质系数取M1, 毛坯尺寸为Ø34.46.12.1+-。
根据《机械加工工艺手册》加工余量分别为:粗镗:Ø36mm 2Z=1.6mm精镗:Ø36mm 2Z=1.0mm 2.Ø30mm 孔毛坯为空心,参照《机械加工工艺手册》,确定工序尺寸为 Z=2.0mm 。
由锻件复杂系数为S1,锻件材质系数取M1, 毛坯尺寸为Ø265.01.1+-根据《机械加工工艺手册》加工余量分别为:扩孔:Ø29.8mm 2Z=1.8mm铰孔:Ø30mm 2Z=0.2mm43. Ø37mm 孔、Ø30mm 孔端面的加工余量参照《机械加工工艺手册》,取加工精度F2 ,由锻件复杂系数为S3, 两孔外侧单边加工余量为Z=2mm 。
锻件材质系数取M1, 复杂系数为S3, 确定锻件偏差为2.16.0+- mm 和1.15.0+-mm 。
根据《机械加工工艺手册》加工余量分别为: Ø37mm 孔端面:粗铣 2Z=3.0mm精铣 2Z=1.0mm Ø30mm 孔端面:粗铣 2Z=4.0mm4. Ø10.5mm 孔毛坯为实心,不出孔 ,为自由工差。
根据《机械加工工艺手册》加工余量分别为: 钻孔:Ø10.5mm 2Z=10.5mm由于本设计规定的零件为中批生产,可采用调整法加工,因此在计算最大、最小加工余量时,可按调整法加工方式予以确定。
毛坯名义尺寸:122+2×2=126mm 毛坯最大尺寸:126+2×1.3=128.6mm 毛坯最小尺寸:126-2×0.7=124.6mm 铣后最大尺寸:122+0=122mm铣后最小尺寸:122-0.17=121.83mm将以上计算的工序间尺寸及公差整理成下表: (mm )(五)确定切削用量及基本工时工序Ⅲ:粗铣Ø37mm孔端面。
本设计采用查表法确定切削用量。
1.加工条件工件材料:35钢,锻造。
加工要求:铣Ø37mm端面,Ra6.3μm。
机床:X51立式铣床。
刀具:YT15硬质合金面铣刀,齿数Z=5,w d =100mm 。
2. 计算切削用量根据《切削手册》 20.0=z f mm/z 切削速度:根据相关手册 取118=v m/min 8.37510011810001000=⨯⨯==ππdw v n s (r/min ) 现采用X51立式铣床,根据机床说明书,取n w =375 r/min 。
故实际切削速度 5.11710003751001000=⨯⨯==ππww n d v (m/min )当n w =375 r/min 时,工作台每分钟进给量m f 应为 37537552.0=⨯⨯==w z m zn f f (mm/min ) 查机床说明书,取 375=m f mm/min 切削工时 27.037510021==++=m m f l l l t (min ) m t 为加工一侧端面的时间,总工时 528.0264.02=⨯=t (min ) 工序Ⅳ 扩,粗铰,精铰Ø37mm 孔并加工倒角1.5×45°。
根据《机械加工工艺手册》查得加工Ø37mm 孔的进给量ƒ=0.3——1.0mm ,按机床 规格取f =0.6mm ,切削速度,根据相关手册及机床说明书,取v=30mm/s ,加工孔径0d =Ø36mm 。
则4.2653630100010000=⨯⨯==ππd v n s (r/min ) 根据机床选取n w =300 r/min 。
实际切削速度 9.3310003003610000=⨯⨯==ππvd v (m/min )切削工时 48.06.0300107621=⨯+=++=f n l l l t w (min ) 工序Ⅴ 铣尺寸为77mm 的孔端面。
根据《切削手册》 20.0=z f mm/z切削速度:根据相关手册 取118=v m/min 刀具与工序Ⅰ所使用刀具相同 125=w d mm 4=z 30012511810001000=⨯⨯==ππdw v n s (r/min ) 现采用X51立式铣床,根据机床说明书,取n w =300 r/min 。
故实际切削速度 11810003001251000=⨯⨯==ππww n d v (m/min )当n w =300 r/min 时,工作台每分钟进给量m f 应为 24030042.0=⨯⨯==w z m zn f f (mm/min )查机床说明书,取 2.235=m f mm/min切削工时 45.02.235406521=+=++=m m f l l l t (min ) m t 为加工一侧端面的时间,总工时 90.045.02=⨯=t (min ) 工序Ⅵ 粗铣Ø30mm 孔两端面。
根据《切削手册》 20.0=z f mm/z切削速度:根据相关手册 取118=v m/min 刀具与工序Ⅰ所使用刀具相同 125=w d mm 4=z 30012511810001000=⨯⨯==ππdw v n s (r/min ) 现采用X51立式铣床,根据机床说明书,取n w =300 r/min 。