亚克力制作工艺
亚克力注塑加工方法和工艺
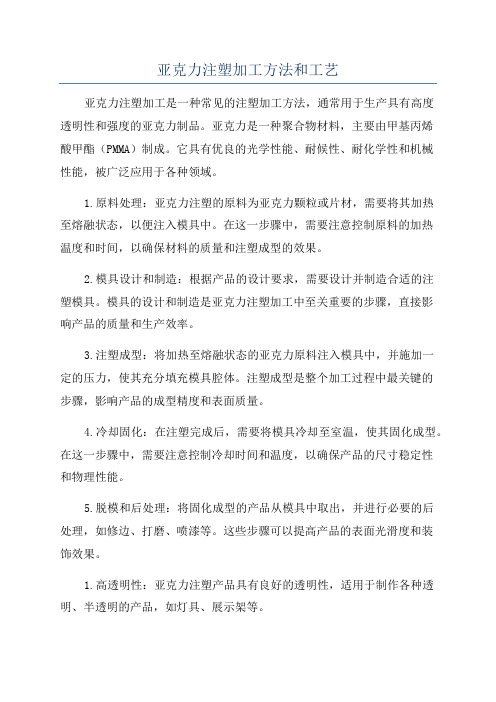
亚克力注塑加工方法和工艺亚克力注塑加工是一种常见的注塑加工方法,通常用于生产具有高度透明性和强度的亚克力制品。
亚克力是一种聚合物材料,主要由甲基丙烯酸甲酯(PMMA)制成。
它具有优良的光学性能、耐候性、耐化学性和机械性能,被广泛应用于各种领域。
1.原料处理:亚克力注塑的原料为亚克力颗粒或片材,需要将其加热至熔融状态,以便注入模具中。
在这一步骤中,需要注意控制原料的加热温度和时间,以确保材料的质量和注塑成型的效果。
2.模具设计和制造:根据产品的设计要求,需要设计并制造合适的注塑模具。
模具的设计和制造是亚克力注塑加工中至关重要的步骤,直接影响产品的质量和生产效率。
3.注塑成型:将加热至熔融状态的亚克力原料注入模具中,并施加一定的压力,使其充分填充模具腔体。
注塑成型是整个加工过程中最关键的步骤,影响产品的成型精度和表面质量。
4.冷却固化:在注塑完成后,需要将模具冷却至室温,使其固化成型。
在这一步骤中,需要注意控制冷却时间和温度,以确保产品的尺寸稳定性和物理性能。
5.脱模和后处理:将固化成型的产品从模具中取出,并进行必要的后处理,如修边、打磨、喷漆等。
这些步骤可以提高产品的表面光滑度和装饰效果。
1.高透明性:亚克力注塑产品具有良好的透明性,适用于制作各种透明、半透明的产品,如灯具、展示架等。
2.良好的表面质量:亚克力注塑产品表面平整、光滑,具有良好的装饰效果,适用于制作高档产品。
3.高强度和耐冲击性:亚克力注塑产品具有较高的强度和硬度,耐冲击性能优良,适用于制作要求较高的产品。
4.耐候性和耐化学性:亚克力注塑产品具有良好的耐候性和耐化学性,能够在各种环境条件下保持稳定性。
亚克力注塑加工在各种行业中都有广泛的应用,如电子、汽车、家具、灯具等领域。
随着科技的不断进步和市场需求的不断增长,亚克力注塑加工技术也在不断改进和创新,为生产高质量、高性能的亚克力制品提供了更多的可能性。
论亚克力吸塑广告字的具体制作工艺
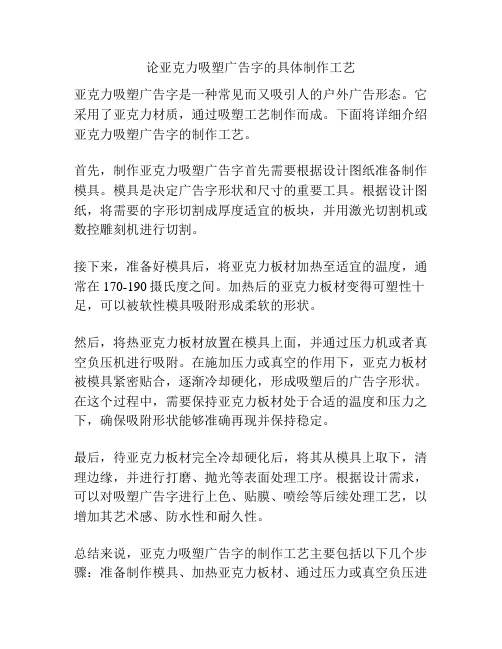
论亚克力吸塑广告字的具体制作工艺亚克力吸塑广告字是一种常见而又吸引人的户外广告形态。
它采用了亚克力材质,通过吸塑工艺制作而成。
下面将详细介绍亚克力吸塑广告字的制作工艺。
首先,制作亚克力吸塑广告字首先需要根据设计图纸准备制作模具。
模具是决定广告字形状和尺寸的重要工具。
根据设计图纸,将需要的字形切割成厚度适宜的板块,并用激光切割机或数控雕刻机进行切割。
接下来,准备好模具后,将亚克力板材加热至适宜的温度,通常在170-190摄氏度之间。
加热后的亚克力板材变得可塑性十足,可以被软性模具吸附形成柔软的形状。
然后,将热亚克力板材放置在模具上面,并通过压力机或者真空负压机进行吸附。
在施加压力或真空的作用下,亚克力板材被模具紧密贴合,逐渐冷却硬化,形成吸塑后的广告字形状。
在这个过程中,需要保持亚克力板材处于合适的温度和压力之下,确保吸附形状能够准确再现并保持稳定。
最后,待亚克力板材完全冷却硬化后,将其从模具上取下,清理边缘,并进行打磨、抛光等表面处理工序。
根据设计需求,可以对吸塑广告字进行上色、贴膜、喷绘等后续处理工艺,以增加其艺术感、防水性和耐久性。
总结来说,亚克力吸塑广告字的制作工艺主要包括以下几个步骤:准备制作模具、加热亚克力板材、通过压力或真空负压进行吸附形状、冷却硬化、取模、表面处理及装饰。
这些步骤的精确操作和合理控制是亚克力吸塑广告字能够准确重现设计效果的关键。
通过这些工艺,制作出来的亚克力吸塑广告字能够耐久、装饰性强、适应各种室外环境,并且能够更好地吸引人们的注意力。
亚克力吸塑广告字是一种非常常见且广受欢迎的户外广告形式。
它可以应用于各种场所,如商店门头、露天广告牌、楼宇立面等,通过鲜明的色彩和立体感,吸引人们的注意力,同时展现出广告主的品牌形象和信息。
制作亚克力吸塑广告字涉及到一系列复杂的工艺和技术,下面将进一步介绍。
首先,制作亚克力吸塑广告字的关键是制作模具。
模具的质量直接影响到吸塑形状的准确程度和精细程度。
亚克力生产工艺流程
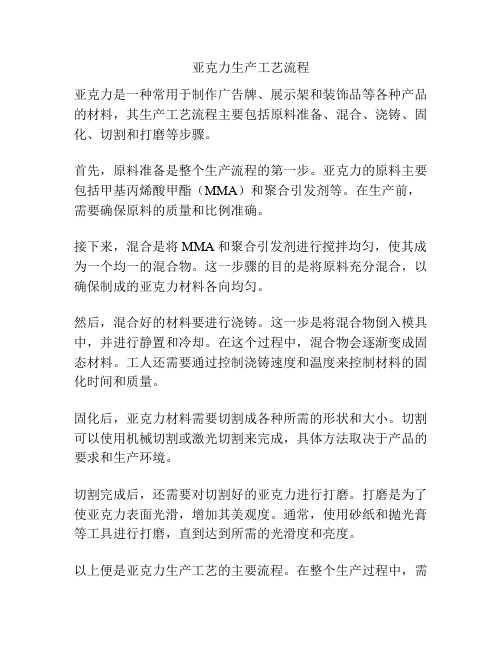
亚克力生产工艺流程
亚克力是一种常用于制作广告牌、展示架和装饰品等各种产品的材料,其生产工艺流程主要包括原料准备、混合、浇铸、固化、切割和打磨等步骤。
首先,原料准备是整个生产流程的第一步。
亚克力的原料主要包括甲基丙烯酸甲酯(MMA)和聚合引发剂等。
在生产前,需要确保原料的质量和比例准确。
接下来,混合是将MMA和聚合引发剂进行搅拌均匀,使其成为一个均一的混合物。
这一步骤的目的是将原料充分混合,以确保制成的亚克力材料各向均匀。
然后,混合好的材料要进行浇铸。
这一步是将混合物倒入模具中,并进行静置和冷却。
在这个过程中,混合物会逐渐变成固态材料。
工人还需要通过控制浇铸速度和温度来控制材料的固化时间和质量。
固化后,亚克力材料需要切割成各种所需的形状和大小。
切割可以使用机械切割或激光切割来完成,具体方法取决于产品的要求和生产环境。
切割完成后,还需要对切割好的亚克力进行打磨。
打磨是为了使亚克力表面光滑,增加其美观度。
通常,使用砂纸和抛光膏等工具进行打磨,直到达到所需的光滑度和亮度。
以上便是亚克力生产工艺的主要流程。
在整个生产过程中,需
要确保原料的质量和比例准确,以及控制浇铸速度和温度等参数,以确保制成的亚克力材料具有所需的性能和质量。
亚克力作为一种常用的工艺装饰材料,广泛应用于各个领域。
其生产工艺流程简单而有效,经过准确的操作和处理,可以制成各种不同形状和尺寸的亚克力制品。
随着技术的不断进步和创新,亚克力生产工艺也将不断完善和改进,以满足市场的需求和消费者的期望。
亚克力热压成型工艺(一)

亚克力热压成型工艺(一)亚克力热压成型工艺简介•什么是亚克力热压成型工艺?•工艺原理及特点优点•高精度加工•复杂形状的成型•高质量的表面光洁度步骤1.原料准备2.制作模具3.条件调节4.加热和热压成型5.冷却和固化6.后处理材料选用•透明亚克力板•亚克力颜料•添加剂设备•热压机•温度控制系统•压力控制系统应用领域•广告牌制作•电子产品外壳•室内装饰品注意事项•操作员需要具备专业技能•工艺参数需要合理调节•安全措施要到位结论亚克力热压成型工艺具有高精度、高质量等优点,广泛应用于广告牌制作、电子产品外壳及室内装饰品等领域。
在使用过程中,需要操作员具备专业技能,并注意合理调节工艺参数,保证安全操作。
亚克力热压成型工艺将为我们提供更多高质量、复杂形状的制品。
亚克力热压成型工艺简介亚克力热压成型工艺是一种常用的亚克力板加工方法,通过热压模具对亚克力板进行塑性变形,以实现所需形状和尺寸的制作过程。
该工艺能够让亚克力板表面保持一定的光亮度,同时具备高精度和高质量的特点。
优点亚克力热压成型工艺具有以下优点: 1. 高精度加工:通过热压成型,亚克力板能够获得高度精确的形状和尺寸,确保产品的准确性。
2. 复杂形状的成型:亚克力热压成型工艺可以制作出复杂的形状,如凹凸不平的曲面、弧形等,满足各种设计需求。
3. 高质量的表面光洁度:热压模具可以使亚克力板表面光滑均匀,具有高度的光洁度和透明度。
步骤亚克力热压成型工艺包括以下步骤: 1. 原料准备:选用透明亚克力板作为原料,并根据设计要求进行切割。
2. 制作模具:根据产品的形状和尺寸,制作符合需求的热压模具。
3. 条件调节:根据亚克力板的特性和设计要求,调节热压机的加热温度和压力参数。
4.加热和热压成型:将预热的亚克力板放入热压机中,在设定温度下进行加热软化。
5. 冷却和固化:待亚克力板冷却后,进行固化处理,使其恢复硬度和稳定性。
6. 后处理:去除余料、毛刺等,并进行必要的修整和抛光工作。
亚克力滴塑工艺

亚克力滴塑工艺亚克力滴塑工艺是一种应用广泛的加工技术,它通过将亚克力材料加热至液态,再通过滴塑的方式使其成型。
这种工艺的主要优势在于可以制作出各种形状复杂、透明度高的产品。
在亚克力滴塑工艺中,首先需要将亚克力材料加热至一定温度,使其变得粘稠。
然后,通过滴塑的方式将亚克力液体滴落到模具中,并等待其自然凝固。
在凝固过程中,亚克力材料会逐渐变硬,并且保持着所滴塑的形状。
最后,将凝固的亚克力产品从模具中取出,经过一系列的后处理工艺,如修边、抛光等,使其表面平整光滑。
亚克力滴塑工艺的应用领域非常广泛。
在建筑领域,亚克力滴塑材料可以用于制作透明的窗户、天花板、墙面等装饰材料。
在家居领域,亚克力滴塑产品可以用于制作各种家具、照明设备等。
此外,亚克力滴塑工艺还可以应用于汽车、电子产品、玩具等行业。
亚克力滴塑工艺的优点不仅在于其制作出的产品形状多样、透明度高,而且亚克力材料本身具有良好的耐候性和耐化学性,能够在各种恶劣的环境中长时间使用。
此外,亚克力滴塑产品还具有良好的表面光泽和触感,给人一种高质量的感觉。
然而,亚克力滴塑工艺也存在一些挑战和限制。
首先,亚克力材料的成本较高,使得滴塑产品的价格相对较高。
其次,亚克力滴塑工艺对操作者的要求较高,需要具备一定的技术和经验。
此外,亚克力滴塑产品的尺寸较大时,可能存在收缩和变形的问题,需要通过优化工艺来解决。
总的来说,亚克力滴塑工艺是一种重要的加工技术,它能够制作出形状复杂、透明度高的产品。
这种工艺的应用广泛,可以满足建筑、家居、汽车等行业的需求。
虽然亚克力滴塑工艺存在一些挑战和限制,但随着技术的不断进步和工艺的不断优化,相信它会在未来得到更广泛的应用。
亚克力工艺流程

亚克力工艺流程
《亚克力工艺流程》
亚克力是一种常用于制作工艺品和装饰品的材料,其具有透明度高、耐磨、耐腐蚀等优点,因此深受人们的喜爱。
亚克力工艺流程是指使用亚克力材料进行工艺制作的具体步骤,下面我们将简要介绍一下亚克力工艺流程。
首先是设计稿的制作。
设计稿是工艺品的灵魂,好的设计稿能够为工艺品增色不少。
在设计稿完成后,需要将其转化为数字图稿。
接下来是数控雕刻。
将数字图稿输入到数控雕刻机中,通过程序控制雕刻机进行雕刻,制作出所需的亚克力零部件。
这一步是亚克力工艺制作的关键环节,需要精准的操作和高质量的设备支持。
然后是拼接组装。
将雕刻好的零部件按照设计稿的要求进行组装,需要有一定的手工技巧和经验,才能保证工艺品的完美呈现。
最后是抛光和打磨。
将组装好的工艺品进行抛光和打磨,使其表面更加光滑、透明度更高,达到最终的制作要求。
总的来说,亚克力工艺流程包括设计稿制作、数控雕刻、拼接组装和抛光打磨这几个主要环节。
每个环节都需要精心制作和
细致操作,只有这样才能制作出精美的亚克力工艺品。
希望以上介绍对您有所帮助,如有不足之处,还请谅解。
亚克力生产工艺流程
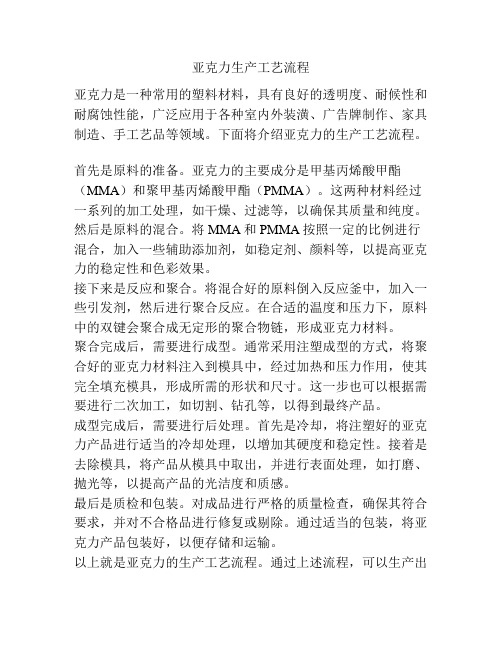
亚克力生产工艺流程亚克力是一种常用的塑料材料,具有良好的透明度、耐候性和耐腐蚀性能,广泛应用于各种室内外装潢、广告牌制作、家具制造、手工艺品等领域。
下面将介绍亚克力的生产工艺流程。
首先是原料的准备。
亚克力的主要成分是甲基丙烯酸甲酯(MMA)和聚甲基丙烯酸甲酯(PMMA)。
这两种材料经过一系列的加工处理,如干燥、过滤等,以确保其质量和纯度。
然后是原料的混合。
将MMA和PMMA按照一定的比例进行混合,加入一些辅助添加剂,如稳定剂、颜料等,以提高亚克力的稳定性和色彩效果。
接下来是反应和聚合。
将混合好的原料倒入反应釜中,加入一些引发剂,然后进行聚合反应。
在合适的温度和压力下,原料中的双键会聚合成无定形的聚合物链,形成亚克力材料。
聚合完成后,需要进行成型。
通常采用注塑成型的方式,将聚合好的亚克力材料注入到模具中,经过加热和压力作用,使其完全填充模具,形成所需的形状和尺寸。
这一步也可以根据需要进行二次加工,如切割、钻孔等,以得到最终产品。
成型完成后,需要进行后处理。
首先是冷却,将注塑好的亚克力产品进行适当的冷却处理,以增加其硬度和稳定性。
接着是去除模具,将产品从模具中取出,并进行表面处理,如打磨、抛光等,以提高产品的光洁度和质感。
最后是质检和包装。
对成品进行严格的质量检查,确保其符合要求,并对不合格品进行修复或剔除。
通过适当的包装,将亚克力产品包装好,以便存储和运输。
以上就是亚克力的生产工艺流程。
通过上述流程,可以生产出具有良好质量和外观的亚克力制品。
当然,不同的产品可能会有略微的变化和细节处理,但总体流程基本相同。
亚克力制品具有广泛的应用前景和市场需求,因此对于亚克力生产工艺的研究和改进也具有很大的意义。
亚克力镜片生产工艺
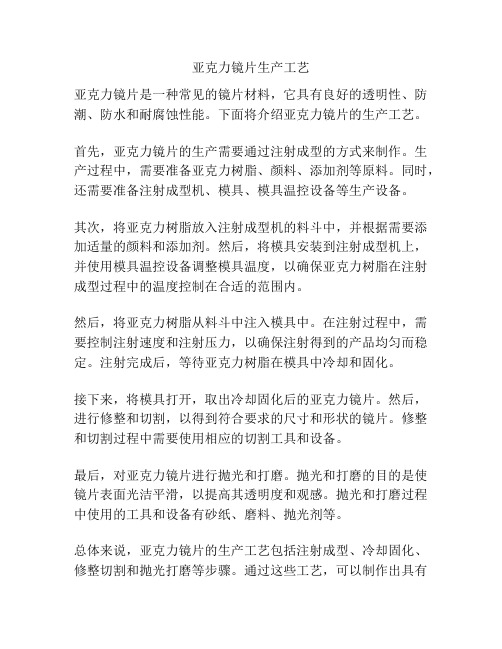
亚克力镜片生产工艺
亚克力镜片是一种常见的镜片材料,它具有良好的透明性、防潮、防水和耐腐蚀性能。
下面将介绍亚克力镜片的生产工艺。
首先,亚克力镜片的生产需要通过注射成型的方式来制作。
生产过程中,需要准备亚克力树脂、颜料、添加剂等原料。
同时,还需要准备注射成型机、模具、模具温控设备等生产设备。
其次,将亚克力树脂放入注射成型机的料斗中,并根据需要添加适量的颜料和添加剂。
然后,将模具安装到注射成型机上,并使用模具温控设备调整模具温度,以确保亚克力树脂在注射成型过程中的温度控制在合适的范围内。
然后,将亚克力树脂从料斗中注入模具中。
在注射过程中,需要控制注射速度和注射压力,以确保注射得到的产品均匀而稳定。
注射完成后,等待亚克力树脂在模具中冷却和固化。
接下来,将模具打开,取出冷却固化后的亚克力镜片。
然后,进行修整和切割,以得到符合要求的尺寸和形状的镜片。
修整和切割过程中需要使用相应的切割工具和设备。
最后,对亚克力镜片进行抛光和打磨。
抛光和打磨的目的是使镜片表面光洁平滑,以提高其透明度和观感。
抛光和打磨过程中使用的工具和设备有砂纸、磨料、抛光剂等。
总体来说,亚克力镜片的生产工艺包括注射成型、冷却固化、修整切割和抛光打磨等步骤。
通过这些工艺,可以制作出具有
优良性能和美观外观的亚克力镜片。
亚克力镜片在日常生活中有着广泛的应用,例如装饰、家具、建筑等领域,它的生产工艺的完善和提高可以满足人们对高品质亚克力镜片的需求。
- 1、下载文档前请自行甄别文档内容的完整性,平台不提供额外的编辑、内容补充、找答案等附加服务。
- 2、"仅部分预览"的文档,不可在线预览部分如存在完整性等问题,可反馈申请退款(可完整预览的文档不适用该条件!)。
- 3、如文档侵犯您的权益,请联系客服反馈,我们会尽快为您处理(人工客服工作时间:9:00-18:30)。
亚克力加工工艺聚甲基丙烯酸甲酯可以采用浇铸、注塑、挤出、热成型等工艺。
1.浇铸成型浇铸成型用于成型有机玻璃板材、棒材等型材,即用本体聚合方法成型型材。
浇铸成型后的制品需要进行后处理,后处理条件是60℃下保温2h,120℃下保温2h 2.注塑成型注塑成型采用悬浮聚合所制得的颗粒料,成型在普通的柱塞式或螺杆式注塑机上进行。
表1是聚甲基丙烯酸甲酯注塑成型的典型工艺条件。
工艺参数螺杆式注塑机柱塞式注塑机料筒℃温度后部180-200 180-200 中部190-230 前部180-210 210-240 喷嘴温度℃180-210 210-240 模具温度℃40-80 40-80 注射压力MPa 80-120 80-130 保压压力MPa 40-60 40-60 螺杆转速rp.m-1 20-30 注塑制品也需要后处理消除内应力,处理在70-80℃热风循环干燥箱内进行,处理亚克力棒时间视制品厚度,一般均需4h左右。
3.挤出成型聚甲基丙烯酸甲酯也可以采用挤出成型,用悬浮聚合生产的颗粒料制备有机玻璃板材、棒材、管材、片材等,但这样制备的型材,特别是板材,由于聚合物分子量小,力学性能、耐热性、耐溶剂性均不及浇注成型的型材,其优点是生产效率高,特别是对于管材和其它用浇注法时模具。
难以制造的型材。
挤出成型可采用单阶或双阶排气式挤出机,螺
杆长径比一般在20-25。
表2是挤出成型的典型工艺条件。
工艺参数片材棒材螺杆压缩比 2 2 料筒℃温度后部150-180 150-180 中部170-200 170-200 前部170-230 170-200 挤出压力MPa 2.8-12.4 0.7-3.4 进料口温度℃50-80 50-80 口模温度℃180-200 170-190 4.热成型热成型是将有机玻璃板材或片材制成各种尺寸形状制品的过程,将裁切成要求尺寸的坯料夹紧在模具框架上,加热使其软化,再加压使其贴紧模具型面,得到与型面相同的形状,经冷却定型后修整边缘即得制品。
加压可采用抽真空牵伸或用对带有型面的凸模直接加压的方法。
热成型温度可参照表3推荐的温度范围。
采用快速真空低牵伸成型制品时,宜采用接近下限温度,成型形状复杂的深度牵伸制品时宜采用接近上限温度,一般情况下采用正常温度。