制程检验程序(含表格)
HSF制程管制与检验管理程序
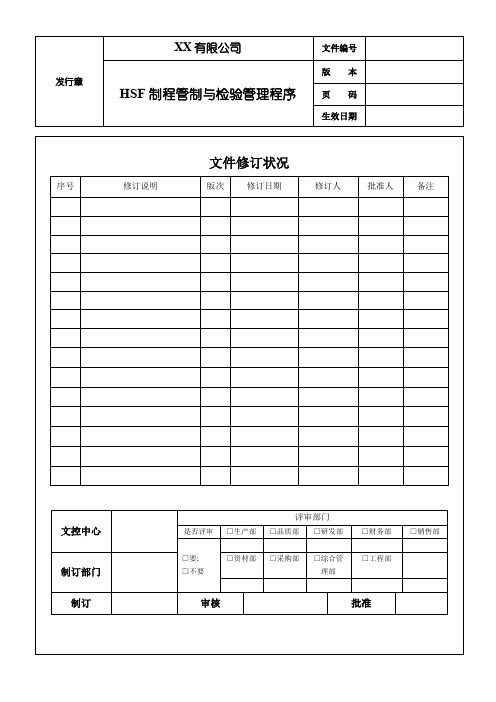
a、新产品每次导入时,由供应商提供有害物质测试报告。
b、每次检测之数据1年内保持有效。
c、供货商提供之有害物质测试报告,由品质部专人维护,在报告到期前一个月MAIL通知采购,由采购通知供应商提供更新有害物质测试报告。如在上一期报告到期日,但新报告还未提供者,则由我司直接送测,送测费用由供货商负担。
6.2.《HSF异常控制程序》
6.3.《HSF产品标识与追溯管理程序》
6.4《风险辨识和评价控制程序》
6.5.《HSF采购管理程序》
7.0.相关记录
7.1《产品批次流转卡》
7.2《质量状态标签》
7.3《生产日报表》
7.4.《首检记录》
7.5.《首件确认单》
7.6.《出货检验报告》
7.7《质量检验记录》
4.流程图:
无
5.程序内容:
5.1进料检验:
5.1.1.品质部进料检验员接到仓库开出的《采购收货报检单》后需核对以下信息:
1)确认供应商是否在《合格供应商名录》中,若不在合格供应商名录中的供应商送货,则及时将现况上报主管,并依照其指示做批退处理。
2)来料HSF标识及外箱标识(来料厂商名称、材料品名及规格、料号)是否清晰及符合我司要求;
文件修订状况
序号
修订说明
版次
修订日期
修订人
批准人
备注
文控中心
评审部门
是否评审
□生产部
□品质部
□研发部
□财务部
□销售部
□要;
□不要
制订部门
□资材部
□采购部
□综合管理部
□工程部
制订
审核
批准
1.目的:
为保证进入我司之所有原材料、辅助材料及出货成品均符合HSF(有害物质限制或消除)管理相关要求,以预防非环保品流入客户端,特制定本程序。
制程检验程序

制程检验管理程序(IATF16949/ISO9001-2015)1目的:1.1防止制程中品质变异提早发现不良原因避免不良品大量产生。
1.2增进作业人员对品质标准的认识,作为自主检查与巡回检查之基准,进而达到降低成本,提高市场竞争力。
2适用范围:自零、配件原料开始上线制造到成品包装入库完成为止均适用本办法,模具依『模具制程管理程序』。
3职责:3.1生管负责生产进度安排及物料、成品之发(领)料及保存。
3.2制造于制程中依制程作业标准书之规定做自主检查,并予以记录。
3.3品保对制程中或入库前作全程的品质检核,包括巡回检验及成品检验。
4名词定义:4.1发(领)料:仓库依生产计划发料至制造单位或由制造领料之作业。
4.2自主检查:作业人员对工作站制品自我检查并记录。
4.3巡回检查:品检人员于制程中作不定时依品质管制计划表的检查频率对现场及产品查核并予记录。
5制程检验内容:5.1作业程序5.2执行方法:5.2.1生管每月底前依客户需求排定生产计划。
5.2.2领发料作业:5.2.2.1生管依生产计划需求,以成套领发退料单依指定数量标示明确,发料至现场指定区,并经制造单位签收。
5.2.2.2.螺丝帽等法定标准件或指定物料制造单位就现场库存需求,以领料单向生管领取。
5.2.3生产作业:制造单位每日依生产计划派工,并查核所需人力、材料、设备条件等是否正确,合格后即依制程作业标准书进行生产作业及首件检查、自主检查。
5.2.4自主检查:5.2.4.1首件检查之时机:每日开机后之首件换线后之首件设备修理后之首件作业人员更换后之首件作业条件变更后之首件停电后再开机之首件。
5.2.4.2专机(线)生产之产品或生产期间长,中途有休息停机者均需做首中件检查,作业员于每日上、下午开机时做首件检查,中间休息后再开机生产时做中件检查,小批量短期间生产之产品则做首末件检查。
5.2.4.3首中件检查由作业员检查壹件,依检查项目实施并记录于自主检查表中,并在检查部品上签名,注明时间,放置于检具上或易于目视之规定处,至中件检查后再放入料架中,中件检查作业亦同,至末件检查时放入料架中。
PQC检验程序(含表格)
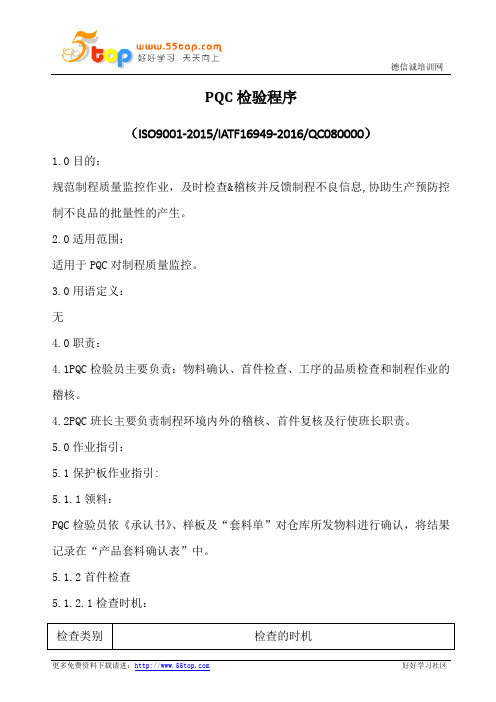
PQC检验程序(ISO9001-2015/IATF16949-2016/QC080000)1.0目的:规范制程质量监控作业,及时检查&稽核并反馈制程不良信息,协助生产预防控制不良品的批量性的产生。
2.0适用范围:适用于PQC对制程质量监控。
3.0用语定义:无4.0职责:4.1PQC检验员主要负责:物料确认、首件检查、工序的品质检查和制程作业的稽核。
4.2PQC班长主要负责制程环境内外的稽核、首件复核及行使班长职责。
5.0作业指引:5.1保护板作业指引:5.1.1领料:PQC检验员依《承认书》、样板及“套料单”对仓库所发物料进行确认,将结果记录在“产品套料确认表”中。
5.1.2首件检查5.1.2.1检查时机:5.1.2.2检查项目5.1.3注意事项:PQC检验员在领料确认时及检查首件时:1)检查产品所有物料的品牌、型号、规格、封装及环保标识是否与《承认书》中“材料清单”规定的是否一致。
2)核对受控样板,确认产品所用的PCB版本、颜色和产品上的材料型号、版本(丝印)颜色、外形是否和样板一致。
5.1.4检查不合格处理:若发现产品有不合格时,知会生产,对其不合格产品进行隔离,加红色拒收标签标识清楚不良原因,按《不合格品控制程序》规定进行处理。
5.2制程检验5.2.1检查标准依《SMT外观检验标准》5.2.2检验方式/要求a.佩戴防静电手环或防静电手套。
b.使用放大镜、显微镜、万用表、电子负载、恒流源、保护板测试仪等检验仪器。
c.目视外观时采用由上而下、由左而右,从90度、45度等多视角进行外观检验。
d.若发现不良缺陷,在不良缺陷处或不良品上贴上红色不良箭头标签。
e.检验项目及标准:检验依照《SMT外观检验标准》、《保护板性能测试QC作业指引》、《承认书》内容及受控样板标准检验。
f.异常反馈/处理:抽检中如果发现有严重品质异常和品质隐患时,必须及时向PQC/生产班长反馈,组织相关部门人员现场分析改善,品质部门进行记录与追踪结果确认。
制程检验作业流程及不合格品处理流程流程

制程检验作业流程流程图1.0目的为保证产品在生产制程中得到有效检验作业,控制制程品质,降低制程返工、报废,提升产品合格率,提高不良出来的时效性,特制定本作业流程。
2.0 范围适用于(备料车间、白身车间、油漆车间、包装车间)生产过程中的检验与控制及不良品处理。
3.0 职责3.1 PMC部:计划课负责生产指令的下达,参与生产异常处理;仓务课负责完成不良品的回仓分类保管、标识确认及不良品退料的督促工作。
3.2 各生产车间:负责制程产品材料确认,首件产品品质确认及生产过程中的自检、互检工作。
反馈、参与生产异常处理;3.3品管部:首件产品确认及生产过程中的巡检、完工后检验,反馈、主导或参与品质异常处理工作,并对数据记录保存、统计、分析、改善,持续改善;3.4 相关部门:主导或参与品质异常处理及异常分析工作。
4.0 作业程序4.1 PMC部下发《生产日计划》给各生产车间主管,各生产车间主管根据《生产日计划》,组织安排操作工做好生产前的准备工作;4.2 各车间组长、技术员准备工装夹具、测量量具、签样等,按样品或产品工程作业标准书等准备物料进行生产。
备料、白身、总装车间:工装夹具、测量量具、签样、作业指导书、图纸、模具等。
油漆车间:色板、签样、作业指导书、图纸等。
包装车间: 签样、作业指导书、图纸、产品包装示意图、模具等。
4.3组长、技术员对首件先自检,合格报制程检验员对首件进行检验,详细参考《首件检验控制卡》。
4.4制程检验员全检或按规定频次(正常情况下每天不少于6次)及工艺图纸等要求巡检各工序制程品质状况,巡检要有相关侧重点,填写巡检记录,若不符图纸和工艺要求,则知会操作员异常状况;当生产操作工自检发现不良现象时及时隔离和标识;当产生不良品超标时,发现人即时通知本组组长到现场确认,组长到现场确认后,按《生产异常提报控制卡》进行操作,必要时组长填写《品质异常报告和处理单》交责任单位处理(来料引起的不良交品管部处理;制程引起的不良交本部车间主管处理)。
制程检验流程

1、目的:为确保公司内部加工零件质量符合公司品质要求,避免因加工过程中的不合格零件流入下道工序而影响模具的制作周期与品质。
2、适用范围适用公司内部各工序加工的零件与装配中的模具。
3、定义:无4、职责:4.1 各工序操作员对本工序的加工零件自检并填写《工件尺寸检测记录表》以及报检,加工组长复查后并签名。
4.2 钳工组长负责加工后以及装配过程中工件的复检。
4.3 品质部制程检验员负责零件加工完成的检验制程巡检和关键零件终检, 监督纠正预防措施的实施。
4.4品质部文员负责将《异常处理单》及时交相关人员签批并将签批完成后的《异常处理单》复印给相关部门。
4.5品质工程师负责《异常处理单》的审核以及每月制程异常数据的统计与分析。
5.程序内容:5.1 操作员报检、制程检验员巡检5.1.1 各工序操作员在该工序加工完成后,严格按照加工要求以及零件图对外观、重点尺寸进行自检并填写好《工件尺寸检测记录表》,自检确认合格将《工件尺寸检测记录表》交加工组长审核后放置于指定位置报检。
5.1.2 制程检验员不停对机台巡检,收到机台操作员的报检信息或发现待检验区有已加工完成的零件根据加工要求和零件图,结合电脑3D图对其外观、尺寸进行详细的检测。
5.1.3如零件较复杂需要超过一小时的检测时间,需提前与制模组长沟通,以防止模具因非加工、装配停留的时间过长而延误交期;检验完成后,《工件尺寸检测记录表》由品质部制程检验组保存。
5.2 检验标准与测量方法5.2.1车床、钻床、铣床检验标准与测量5.2.2 CNC与数控车加工检验标准与测量方法5.2.3 EDM加工检验标准与测量方法5.2.4 线割加工检验标准与测量方法5.3品质判定5.3.1经过检验若零件外观、尺寸、性能等均符合加工要求则判定该零件此加工工序的品质状态为合格。
5.3.2经过检验若零件外观、尺寸、性能等有一项或多项不符合加工要求则判定该零件此加工工序的品质状态为不合格。
5.4 品质标识检验完成后,根据其零件的品质状态在物料上做好相应的品质状态标识(物料质量合格贴绿色“QC.PASS”标签,不合格贴红色“QC.REJ”标签),必要时在物料上用油性笔标识好模号、零件号等信息。
制程检验程序(含表格)

制程检验程序(ISO9001:2015)1.0目的为规范制程检验,预防产出批量不合格的产品,减少(杜绝)制程异常的发生。
不断降低生产制程不良率,提升产品品质,确保产品品质符合客户要求。
2.0范围适用于本公司生产制程品质检验控制。
3.0定义3.1首件:指生产制程中加工生产的产品,判定符合要求后,拟批量生产前的第一台(个)产品(半成品,成品)。
3.2全检:对制程中的产品或产品的某些检验项目进行100%检验。
3.3巡检:对生产过程中影响产品品质的因素(工位)进行随机抽样检验,确认。
4.0权责4.1品质部4.1.1负责制程中产品外观,检验流程,检验标准,检验规范,检验工位的编制和设置。
4.1.2IPQC:负责对产品,物料首件确认的主导工作,并对产品首件做出合格与否的判定;制程品质检控,品质异常的确认与追踪;主导不合格品或品质异常问题的提出,跟进,落实及改善效果确认。
4.2项目部4.2.1新产品首件的确认,负责制程中电气/结构性能测试流程,测试工位的编制和设置;品质异常,不合格品原因的分析及改善对策的提出。
4.2.2负责制程中设备,仪器的使用规范的制订;机器,设备,仪器,仪表,治夹具,工具运行状况的监控,正常运转的巡视及点检/保养工作的监督。
4.3生产部4.3.1负责首件的制作与送样确认;全检工位的人员配置。
4.3.2制程中4M1E的落实及制程过程的监控,配合IPQC与PE的工作;品质异常的受理与改善,改善对策的具体实施。
4.3.3负责制程中设备,仪器,仪表,治夹具,工具的日常点检/保养工作。
5.0程序5.1生产,检验前作业准备5.1.1生产部5.1.1.1在开拉生产前进行自我核查,发现不符合项及异常,采取措施,立即纠正。
5.1.1.2在开拉生产前须查核领用物料是否与[生产计划排程表]相符,是否有相应的BOM,技术规范;生产环境是否符合产品需求,各作业工位是否悬挂对应的SOP,作业人员对作业方法,产品品质是否清楚了解。
LED灯具制程巡检规范(含表格)
LED灯具制程巡检规范(ISO9001:2015)1、目的:规范半成品、成品制程巡检检测项目、方法、频率及标准,确保生产过程符合工艺要求和作业规范,从而保证产品质量符合客户要求;同时通过制程巡检收集生产制程的数据,有效地监控制程的变化,并以此推动制程的持续改善。
2、范围:所有LED应用产品半成品和成品制程。
3、定义:IPQC(InPutProcessQualityControl):制程控制,是指产品从物料投入生产到产品最终包装过程的品质控制。
4、权责:4.1QE:负责制定制程巡检的作业规范。
4.2检验员:负责按制程巡检作业指导书进行检验。
5、内容:5.1巡检项目:制程巡检项目频率(小时/次)抽测数(pcs)使用仪器记录表焊接锡膏检查 2 5 目视巡检记录表工段自动/手动贴片检测 2 5 目视巡检记录表焊点检测 2 5 目视巡检记录表回流焊温度每次开机 1 电脑监控巡检记录表回流焊速度每次开机 1 电脑监控巡检记录表高温焊台温度每天 1 电脑监控巡检记录表贴片测试 2 5 变压器巡检记录表组装工段作业环境 2 1 目视巡检记录表烙铁温度每班 1 温度计巡检记录表电源绝缘防护 2 5 目视巡检记录表基板连接 2 5 目视巡检记录表组装工段输出线焊接 2 5 目视巡检记录表点胶检测 2 5 目视巡检记录表粘贴遮光胶布 2 5 目视巡检记录表基板固定 2 5 目视巡检记录表输入线防护 2 5 目视巡检记录表铆钉固定 2 5 目视巡检记录表线头处理 2 5 目视巡检记录表灯罩固化 2 5 目视巡检记录表透镜安装 2 5 目视巡检记录表堵头安装 2 5 目视巡检记录表螺丝固定 2 5 目视巡检记录表漏光检测 2 5 目视巡检记录表包装压灯头 2 5 目视巡检记录表工段功能检测 2 5 目视巡检记录表标贴检测 2 5 目视巡检记录表配件检测 2 5 目视巡检记录表机械老化工段打标检测 2 5 目视巡检记录表震动检测 2 1 目视巡检记录表烧机检测 2 1 目视巡检记录表5.2检测方法:5.2.1锡膏检查:基板焊盘上锡膏不得有连锡、短路、拉尖、少锡、漏印和多锡。
制程检验作业流程图
制程检验作业流程流程图1.0目的为保证产品在生产制程中得到有效检验作业,控制制程品质,降低制程返工、报废,提升产品合格率,提高不良出来的时效性,特制定本作业流程。
2.0 范围适用于(备料车间、白身车间、油漆车间、包装车间)生产过程中的检验与控制及不良品处理。
3.0 职责3.1 PMC部:计划课负责生产指令的下达,参与生产异常处理;仓务课负责完成不良品的回仓分类保管、标识确认及不良品退料的督促工作。
3.2 各生产车间:负责制程产品材料确认,首件产品品质确认及生产过程中的自检、互检工作。
反馈、参与生产异常处理;3.3品管部:首件产品确认及生产过程中的巡检、完工后检验,反馈、主导或参与品质异常处理工作,并对数据记录保存、统计、分析、改善,持续改善;3.4 相关部门:主导或参与品质异常处理及异常分析工作。
4.0 作业程序4.1 PMC部下发《生产日计划》给各生产车间主管,各生产车间主管根据《生产日计划》,组织安排操作工做好生产前的准备工作;4.2 各车间组长、技术员准备工装夹具、测量量具、签样等,按样品或产品工程作业标准书等准备物料进行生产。
备料、白身、总装车间:工装夹具、测量量具、签样、作业指导书、图纸、模具等。
油漆车间:色板、签样、作业指导书、图纸等。
包装车间: 签样、作业指导书、图纸、产品包装示意图、模具等。
4.3组长、技术员对首件先自检,合格报制程检验员对首件进行检验,详细参考《首件检验控制卡》。
4.4制程检验员全检或按规定频次(正常情况下每天不少于6次)及工艺图纸等要求巡检各工序制程品质状况,巡检要有相关侧重点,填写巡检记录,若不符图纸和工艺要求,则知会操作员异常状况;当生产操作工自检发现不良现象时及时隔离和标识;当产生不良品超标时,发现人即时通知本组组长到现场确认,组长到现场确认后,按《生产异常提报控制卡》进行操作,必要时组长填写《品质异常报告和处理单》交责任单位处理(来料引起的不良交品管部处理;制程引起的不良交本部车间主管处理)。
制程及成品检验管理程序(含表格)
制程及成品检验管理程序(IATF16949/ISO9001-2015)1、目的为确保生产制程及成品的质量能有效管理,以满足客户要求,特制订本程序。
2、范围适用于本公司生产现场所生产之半成品、加工品、成品等检验的管理。
3、术语和定义 (无)4、制程及成品检验管理过程乌龟图制程及成品检验管理过程过程输出/Process output1、已检/试验的产品2、检验/试验记录3、不合格品的处理记录4、纠正预防措施处理单过程输入/Process input 1、检验规范 2、控制计划3、图纸4、样件5、抽样接收准则 过程衡量指标/Process measurement indicator: 1、漏检率如何做(方法, 程序, 技术)/how to do(method, procedure, technology): 1、制程及成品检验管理程序 2、产品标识与追溯程序 3、不合格品管理程序 4.纠正与预防措施程序使用资源/Resource1、监视测量2、检验场地3、检测室过程拥有者(责任者)/Process owner:1、质量管理部部长5、 工作流程和内容编号 作业流程图权责部门/人作业要求 使用表单5.1制造部班/线长 5.1生产前对来料进行确认,确认内容包括:零部件/半成品种类,质量状况,外观,数量等相关信息 5.2制造部5.2.1首件生产时间: a.每日刚开始生产时;b.换机、换人、换产品生产时。
c.修机、异常处理后重新生产时。
5.3制造部5.3.1 自检负责人:线组长/线组长指定的员工 5.3.2首件生产完后依照工艺卡执行首件自检,并按照要求填写自检记录 5.3.3 自检不合格执行《不合格品管理程序》 5.3.4自检合格交与质量管理部进行首件确认5.3.5 质量管理部在首件确认前,制造部不得进行批量生产《自检记录表》5.4质量管理部 5.4.1首件确认人员可包括:巡检员/下线检验员/质量工程师5.4.2首件确认人员胜任要求:对产品故障模式熟悉,对产品的质量要求非常熟悉,了解产品市场故障动态5.4.3质量管理部在执行首件确认后务必按实填写《巡检表》中的首件确认栏5.4.4首件确认合格后通知制造部投入批量生产,并做好《首检合格标签》,在生产线指定区域悬挂首件,当班生产完成,首件随当班产品入库。
质量检验控制程序(含表格)
质量检验控制程序(IATF16949-2016/ISO9001-2015)1.0目的规范公司原物料、半成品、成品的品质检验流程,以使产品质量过程得到有效控制。
2.0范围本系统适用于全厂范围。
3.0术语定义IQC:进料品质控制PQC:制程品管OQC:出货品质控制SIP:检验规范SOP:操作规范4.0职责4.1 品质部:主导编制检验规范、执行检验作业、检治具维护、检验记录维护。
4.2 工程部:协助品质部进行检验规范制作。
4.3 生产部:依SOP进行制程自检,维护自检记录。
5.0总体要求5.1 检验规范制作5.1.1 在产品开发过程中,正式量产前,工程部应对所有新物料进行测试验证,确认其符合产品要求。
并根据物料特性制作其关键品质要求,如关键尺寸、关键物理性能、关键化学性能等。
此数据提交品质部专案工程师。
品质部专案工程师根据获得的客户标准信息,制作SIP。
SIP应包括:外观检验要求、尺寸检验要求、性能检验要求等项目;并明确列出检验方法、检验工具、检验环境要求、检验频率等项目。
SIP格式如(附件一)。
在产品开发过程中,正式量产前,工程部应对制程进行验证,确认产品制程的关键控制点,并制作《产品工艺流程图及关键控制点》(附件二)。
品质部针对对关键控制点,制定控制计划,并制作或要求相关单位制作相关控制文件。
控制文件包括:设备操作规范,针对产品的设备参数控制表,各工站的SOP(应包含自检品质要求),品管人员SIP等。
5.1.2 进料检验品质部对所有直接使用于产品的原物料必须制作进料SIP。
仓库接收原物料后,将物料置于待验仓,并张贴物料标识单,填写《进货验收单》通知IQC进行检验。
IQC人员按SIP执行检验作业,并将检验记录填写进《进货验收单》附件八。
并填写来料《品质履历表》附件七。
每日、周、月、年,IQC人员须对所有检验产品数据进行登录、统计、分析,并要求制程PQC人员提供制程中发现的来料品质状况数据,以得到供应商来料品质状况趋势、批退率、良品率等数据。
- 1、下载文档前请自行甄别文档内容的完整性,平台不提供额外的编辑、内容补充、找答案等附加服务。
- 2、"仅部分预览"的文档,不可在线预览部分如存在完整性等问题,可反馈申请退款(可完整预览的文档不适用该条件!)。
- 3、如文档侵犯您的权益,请联系客服反馈,我们会尽快为您处理(人工客服工作时间:9:00-18:30)。
制程检验程序
(ISO9001:2015)
1.0目的
为规范制程检验,预防产出批量不合格的产品,减少(杜绝)制程异常的发生。
不断降低生产制程不良率,提升产品品质,确保产品品质符合客户要求。
2.0范围
适用于本公司生产制程品质检验控制。
3.0定义
3.1首件:指生产制程中加工生产的产品,判定符合要求后,拟批量生产前的第一台(个)产品(半成品,成品)。
3.2全检:对制程中的产品或产品的某些检验项目进行100%检验。
3.3巡检:对生产过程中影响产品品质的因素(工位)进行随机抽样检验,确认。
4.0权责
4.1品质部
4.1.1负责制程中产品外观,检验流程,检验标准,检验规范,检验工位的编制和设置。
4.1.2IPQC:负责对产品,物料首件确认的主导工作,并对产品首件做出合格与
否的判定;制程品质检控,品质异常的确认与追踪;主导不合格品或品质异常问题的提出,跟进,落实及改善效果确认。
4.2项目部
4.2.1新产品首件的确认,负责制程中电气/结构性能测试流程,测试工位的编制和设置;品质异常,不合格品原因的分析及改善对策的提出。
4.2.2负责制程中设备,仪器的使用规范的制订;机器,设备,仪器,仪表,治夹具,工具运行状况的监控,正常运转的巡视及点检/保养工作的监督。
4.3生产部
4.3.1负责首件的制作与送样确认;全检工位的人员配置。
4.3.2制程中4M1E的落实及制程过程的监控,配合IPQC与PE的工作;品质异常的受理与改善,改善对策的具体实施。
4.3.3负责制程中设备,仪器,仪表,治夹具,工具的日常点检/保养工作。
5.0程序
5.1生产,检验前作业准备
5.1.1生产部
5.1.1.1在开拉生产前进行自我核查,发现不符合项及异常,采取措施,立即纠正。
5.1.1.2在开拉生产前须查核领用物料是否与[生产计划排程表]相符,是否有相应的BOM,技术规范;生产环境是否符合产品需求,各作业工位是否悬挂对
应的SOP,作业人员对作业方法,产品品质是否清楚了解。
5.1.1.3仪器,设备,作业工具等是否处于正常状态,烙铁温度,电批扭力等设置是否符合SOP规定。
5.1.1.4原材料外观全检工位,高压测试工位,电性能参数测试工位,成品外观全检工位等工位须准备好各自的报表,如:[电气性能测试制程检验记录表],[制程巡检报表],[静电环点检记录表],[烙铁温度测试记录表]等。
5.1.2品质部
5.1.2.1在生产开拉前,查核是否有与生产产品相应的BOM,图纸,样板,产品规格书。
检验标准等。
5.1.2.2准备好[IPQC日报表],[首件确认单],[LED灯板表面温度测量记录表],[制程巡检表],[品质异常内部联络单]。
5.1.2.3查核卡尺,万用表,热电偶,功率计,变频电源等检验仪器,工具是否处于正常状态,是否在校验有效期内。
5.1.2.4依照生产工单,BOM表,图纸查核生产部领用的物料是否正确,物料状态标示是否完整。
5.2首件确认
5.2.1首件作业时机
新产品上线时,更换机种时,工程设计变更时
5.2.2首件作业数量
首件作业数量一般为1-3PCS,首件作业加严时为3-5PCS
5.2.3首件作业流程
5.2.3.1生产部门依据[生产计划排程表],BOM表,客户需求进行量(试)产,先由产线自行进行首件确认,确认OK后,再将其中的1件作为首件;填写好[首件确认通知单]相关内容,连同首件送品管IPQC(试产首件交PE)进行首件检验。
5.2.3.2IPQC(PE)接到[首件确认单]及首件产品后,对首件产品外观,使用物料材质,规格,产品电流,功率,功率因素等依据客户订单,BOM,图纸,产品性能规格表,样板,检验规范等资料实施检验,并将结果记录于[首件确认单]上。
5.2.3.3IPQC(PE)经检验后,将[首件确认单]连同首件移送其直接上级进行确认,其直接上级须对首件进行全方位确认。
5.2.3.4新产品上线时,更换机种时,工程设计变更时首件确认须填写[首件确认单],并须项目部产品负责人对首件进行确认。
5.2.3.5每日开拉时,人员变更时,作业方法变更时,客户特殊要求时,纠正措施实施时的首件由生产部门自查自检,IPQC进行稽核,将稽核结果记录于[制程巡检表]里,无需单独填写[首件确认单]。
5.2.4首件确认结果的处理
5.2.4.1首件检验合格时,生产部门方可进行量产。
5.2.4.2首件检验不合格时,生产部按要求现场纠正不合格项目,重新经过首
件确认后,开始进行量产;必要时,由IPQC开出[品质异常内部联络单]交项目部PE或其直接上级,具体按《不合格品处理管理程序》执行。
5.2.4.3首件检验不合格时,其不合格项目现场不能即时纠正(如设计问题,来料问题),生产部应停止批量生产。
品质部IPQC开出[品质异常内部联络单]交给PE或直接上级分析,并追踪问题的根本解决。
并重新首件确认合格后,生产部才能批量生产。
5.2.5首件检验管理
5.2.5.1产品品质的某些特殊项目判定无法在短时间内得到结论(如可靠性)。
这些特殊项目应于新产品试制或物料承认时进行检测,首件检验时,可不检验这些项目。
5.2.5.2检验合格的首件,做好标示作为生产部批量生产的样品,保存为本批量生产完结为止。
5.3巡检作业
5.3.1巡检作业时机
5.3.1.1IPQC巡检作业时间:每2小时巡检一次,特殊原因除外。
5.3.1.2生产部组长巡检作业时机:不定时间,随时。
5.3.1.3PE巡检作业时机:每日上下午各巡检一次,特殊原因除外。
5.3.2巡检数量:IPQC每次巡检数量抽10—20PCS/工序,特殊原因加大检验数量或巡检频次。