甲醇裂解制氢装置VPSA脱碳部分的操作规程
制氢装置PSA氢提纯单元装置的操作
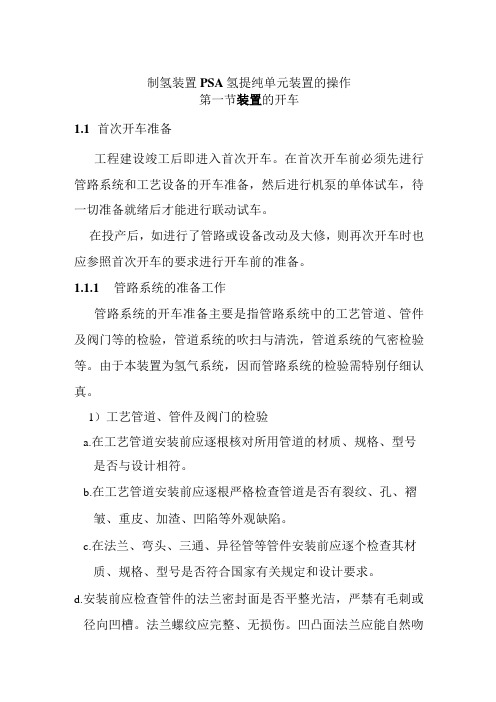
制氢装置PSA氢提纯单元装置的操作第一节装置的开车1.1首次开车准备工程建设竣工后即进入首次开车。
在首次开车前必须先进行管路系统和工艺设备的开车准备,然后进行机泵的单体试车,待一切准备就绪后才能进行联动试车。
在投产后,如进行了管路或设备改动及大修,则再次开车时也应参照首次开车的要求进行开车前的准备。
1.1.1管路系统的准备工作管路系统的开车准备主要是指管路系统中的工艺管道、管件及阀门等的检验,管道系统的吹扫与清洗,管道系统的气密检验等。
由于本装置为氢气系统,因而管路系统的检验需特别仔细认真。
1)工艺管道、管件及阀门的检验a.在工艺管道安装前应逐根核对所用管道的材质、规格、型号是否与设计相符。
b.在工艺管道安装前应逐根严格检查管道是否有裂纹、孔、褶皱、重皮、加渣、凹陷等外观缺陷。
c.在法兰、弯头、三通、异径管等管件安装前应逐个检查其材质、规格、型号是否符合国家有关规定和设计要求。
d.安装前应检查管件的法兰密封面是否平整光洁,严禁有毛刺或径向凹槽。
法兰螺纹应完整、无损伤。
凹凸面法兰应能自然吻合,凸面高度不得低于凹面深度。
e.在法兰连接时,法兰间应保持平行,其偏差不大于法兰外径的L5%。
,且小于2mm,禁止用强紧螺栓的方法消除歪斜。
f.石棉橡胶等非金属密封垫应质地柔韧,无老化变质、分层现象及折痕、皱纹等缺陷;金属密封垫的尺寸、精度应符合规范,无裂纹、毛刺、凹槽、径向划痕等缺陷。
g.在安装前应检查各种工艺阀门的规格、型号、压力等级、材质是否符合设计要求。
h.在安装前所有阀门均应作强度和严密性试验。
试验应用洁净水进行。
i.阀门的强度试验压力为公称压力的L5倍,试验时间不少于五分钟,以壳体和填料无渗漏为合格。
j∙阀门的严密性试验在公称压力下按国家有关规定进行,试验完成后应排净积水,关闭阀门,密封出入口,密封面应图防锈油脂(需脱脂的阀门除外)。
k.安全阀在安装前,首先应检查其规格、型号、压力等级、材质是否符合设计要求,并按设计规定进行调试与整定。
甲醇裂解变压吸附制氢装置操作手册
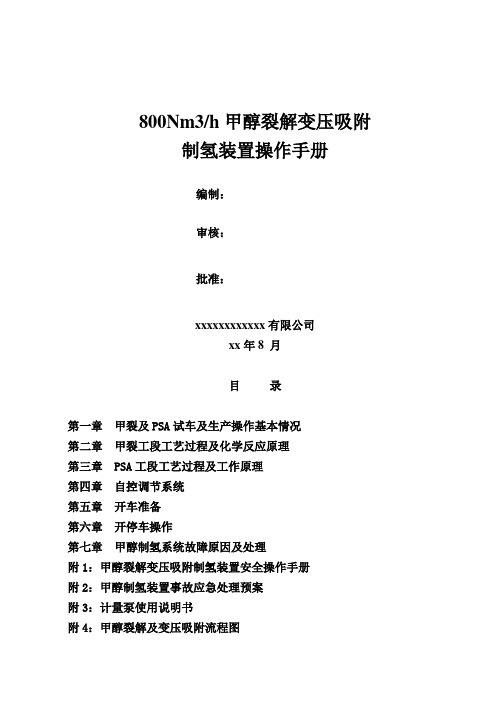
800Nm3/h甲醇裂解变压吸附制氢装置操作手册编制:审核:批准:xxxxxxxxxxxx有限公司xx年8 月目录第一章甲裂及PSA试车及生产操作基本情况第二章甲裂工段工艺过程及化学反应原理第三章 PSA工段工艺过程及工作原理第四章自控调节系统第五章开车准备第六章开停车操作第七章甲醇制氢系统故障原因及处理附1:甲醇裂解变压吸附制氢装置安全操作手册附2:甲醇制氢装置事故应急处理预案附3:计量泵使用说明书附4:甲醇裂解及变压吸附流程图第一章甲裂及PSA试车及生间操作基本情况一、试车及生产操作人员小组人员配置试车组长或生产主管:(业主配置)技术指导:(业主配置)工艺操作工:2人/班分析操作工:1人/班仪表值班:1人/班电气值班:1人/班机械值班:1人/班公用工程协调(调度):1人/班应急对外协作:1人/班安全员:1人/班二、试车时间及地点时间:2019年10月。
地点:甲醇裂解制氢生产区三、工艺指标1.甲醇:符合GB338—2004标准优等品要求。
2.脱盐水:Cl -≤ 1ppmSO42-≤ 1ppm90℃以下稳定,对碳钢、不锈钢无腐蚀电导率≤10μs/cm。
3.温度汽化塔进料温度 140~160℃汽化塔底部温度 160~180℃汽化塔顶部温度~180℃进转化器温度 220~250℃出转化器温度 230~250℃导热油温度 250~280℃出换热器转化气温度 120~140℃出冷凝器转化气温度≤40℃4.压力导热油进口压力0.4~0.6MPa进工段冷却水压力≥0.3 MPa进工段仪表空气压力≥0.4~0.6 MPa 5.浓度甲醇~50%(Wt)水~50%(Wt)转化气组成如下:H273~74.5%23~24.5%CO2CO 0~1%≤ 200ppmCH46.产品气H2≥99.99%(v/v)7.分析内容第二章甲裂工段工艺过程及化学反应原理第一节工艺过程甲醇催化裂解、转化工艺过程包括:原料汽化过程、催化裂解转化反应、转化气冷却冷凝、气液分离等。
甲醇制氢操作规程完整

400Nm3/h甲醇制氢操作规程目录目录 (I)操作规程 (1)一岗位管辖及任务 (1)1.1岗位管辖围 (1)1.2岗位任务: (1)二、工艺说明及流程示意图: (1)2.1工艺说明 (1)2.2流程示意图 (4)三岗位工艺指标: (5)3.1温度指标: (5)3.2流量指标: (5)3.3压力指标:MPa (5)3.4液位: (6)3.5分析指标 (6)四:装置启动初次开车及停车后的再启动 (6)4.1管道的试漏、保压 (6)4.2催化剂的装填 (6)4.3设备、仪表的调校 (9)4.6投料启动 (10)4.7停车后再启动 (10)4.8催化剂的卸出 (12)五正常停车步骤和紧急停车: (12)5.1正常停车 (12)5.2紧急停车 (14)5.3临时停车 (14)六常见故障及处理方法: (14)6.1外界供给条件失常 (14)6.2操作失调 (15)6.3 PLC故障 (16)5.4操作注意事项 (17)七巡回检查制度: (17)八岗位责任制: (17)九设备维护保养制度: (18)十设备润滑管理制度: (19)十一安全注意事项: (19)操作规程一岗位管辖及任务1.1岗位管辖围界区所有管道、设备、阀门、电气及仪表等均属于岗位管辖围。
1.2岗位任务:利用甲醇和水的重整反应制氢,重整气组成为氢气约75%,二氧化碳约25%,还有微量的甲烷,二乙醚的等杂质,之后在通过变压吸附分离提氢,改变变压吸附(PSA)操作条件可生产不同纯度的氢气,氢气纯度最好可达99.999%以上。
二、工艺说明及流程示意图:2.1工艺说明2.1.1重整工段甲醇进入界区后直接进入混配罐中,通过液位控制甲醇进料量,无离子水进入界区后直接进入混配罐中,通过控制液位控制无离子水进料量,两台混配罐一台陪料,一台使用。
混配罐甲醇、水混合液体能维持一个班八小时的工作用量。
混配罐中的混合液经计量泵输送到换热器中。
本工艺现场配备三台计量泵,其中一台输送混合液体,一台给水洗塔输送无离子水,另一台备用,三台泵型号、结构完全相同,开二备一。
制氢装置PSA氢提纯单元装置的操作
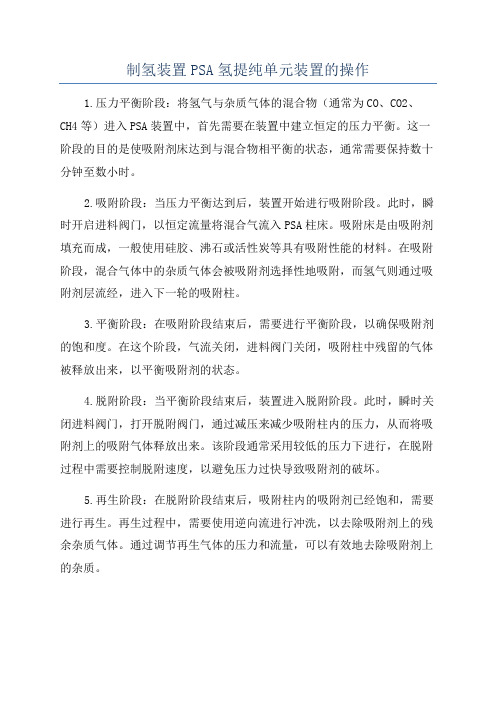
制氢装置PSA氢提纯单元装置的操作1.压力平衡阶段:将氢气与杂质气体的混合物(通常为CO、CO2、CH4等)进入PSA装置中,首先需要在装置中建立恒定的压力平衡。
这一阶段的目的是使吸附剂床达到与混合物相平衡的状态,通常需要保持数十分钟至数小时。
2.吸附阶段:当压力平衡达到后,装置开始进行吸附阶段。
此时,瞬时开启进料阀门,以恒定流量将混合气流入PSA柱床。
吸附床是由吸附剂填充而成,一般使用硅胶、沸石或活性炭等具有吸附性能的材料。
在吸附阶段,混合气体中的杂质气体会被吸附剂选择性地吸附,而氢气则通过吸附剂层流经,进入下一轮的吸附柱。
3.平衡阶段:在吸附阶段结束后,需要进行平衡阶段,以确保吸附剂的饱和度。
在这个阶段,气流关闭,进料阀门关闭,吸附柱中残留的气体被释放出来,以平衡吸附剂的状态。
4.脱附阶段:当平衡阶段结束后,装置进入脱附阶段。
此时,瞬时关闭进料阀门,打开脱附阀门,通过减压来减少吸附柱内的压力,从而将吸附剂上的吸附气体释放出来。
该阶段通常采用较低的压力下进行,在脱附过程中需要控制脱附速度,以避免压力过快导致吸附剂的破坏。
5.再生阶段:在脱附阶段结束后,吸附柱内的吸附剂已经饱和,需要进行再生。
再生过程中,需要使用逆向流进行冲洗,以去除吸附剂上的残余杂质气体。
通过调节再生气体的压力和流量,可以有效地去除吸附剂上的杂质。
6.压缩阶段:再生后的吸附剂已经恢复到初始状态,可以进行下一轮的吸附阶段。
在压缩阶段,需要通过压缩机将氢气压缩至所需的压力水平,以便用于后续的工艺或应用。
以上便是PSA氢提纯单元装置的基本操作流程,由压力平衡、吸附、平衡、脱附、再生和压缩组成。
不同的PSA装置可能会有一些细微的差异,但总体操作流程大致相同。
操作人员需要严格按照工艺要求进行操作,确保装置的正常运行和氢气的提纯效果。
PSA提纯氢气装置开车操作规程
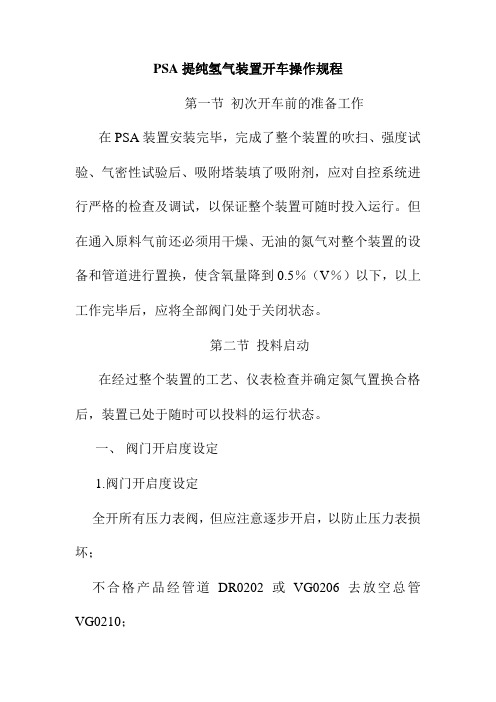
PSA提纯氢气装置开车操作规程第一节初次开车前的准备工作在PSA装置安装完毕,完成了整个装置的吹扫、强度试验、气密性试验后、吸附塔装填了吸附剂,应对自控系统进行严格的检查及调试,以保证整个装置可随时投入运行。
但在通入原料气前还必须用干燥、无油的氮气对整个装置的设备和管道进行置换,使含氧量降到0.5%(V%)以下,以上工作完毕后,应将全部阀门处于关闭状态。
第二节投料启动在经过整个装置的工艺、仪表检查并确定氮气置换合格后,装置已处于随时可以投料的运行状态。
一、阀门开启度设定1.阀门开启度设定全开所有压力表阀,但应注意逐步开启,以防止压力表损坏;不合格产品经管道DR0202或VG0206去放空总管VG0210;全开WG0202管路上截止阀,半开WG0203管路上截止阀。
2.调节阀和连锁阀的设定(见表4-1)表4-1 调节阀和连锁阀的设定3门。
二、PSA程序控制设定将微机控制器退到停机状态,在上位机设置自动工作状态,各步骤时间按正常运行的操作参数设定。
三、启动1渐开进气阀,将原料气流量控制在每一吸附周期使吸附塔压力均匀升高的速度。
2当吸附塔压力升至吸附压力时,可将吸附压力自动调节系统(PICA-0201)投入自动操作。
在升压过程中,通过顺放流量手动遥控(HV-0201)和终充流量手动遥控系统(HV-0202),随时调整顺放和最终升压流量。
3当吸附塔的吸附压力升到1.4Mpa时,可将原料气流量逐步增大,同时通过调整终充流量调节系统(HV-0202)将最终升压终止时压力调整到比吸附压力低0.01~0.05,通过调整顺放流量手操遥控系统(HV-0201)将顺放压差调整在0.2~0.3Mpa。
4产品达到要求后,通知后续工段准备接受纯H2产品。
四、正常运行调节1.1#工艺变压吸附系统主要操作参数(见表4-2)表4-2 变压吸附系统个步骤压力及时间分配2.2#工艺变压吸附系统主要操作参数(见表4-3)表4-3 变压吸附系统各步骤压力及分配时间分配2、运行检查项目和调整、为了良好的运行,在运行期间要检查和调整下列项目;●吸附压力。
制氢装置PSA氢提纯单元安全规程
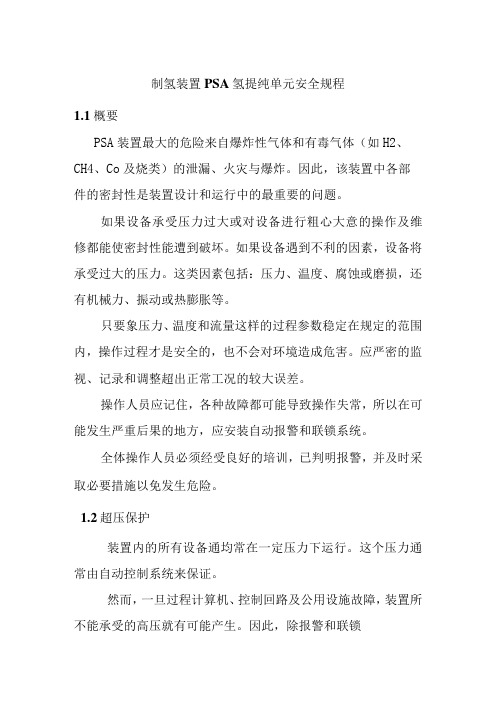
制氢装置PSA氢提纯单元安全规程1.1概要PSA装置最大的危险来自爆炸性气体和有毒气体(如H2、CH4、Co及烧类)的泄漏、火灾与爆炸。
因此,该装置中各部件的密封性是装置设计和运行中的最重要的问题。
如果设备承受压力过大或对设备进行粗心大意的操作及维修都能使密封性能遭到破坏。
如果设备遇到不利的因素,设备将承受过大的压力。
这类因素包括:压力、温度、腐蚀或磨损,还有机械力、振动或热膨胀等。
只要象压力、温度和流量这样的过程参数稳定在规定的范围内,操作过程才是安全的,也不会对环境造成危害。
应严密的监视、记录和调整超出正常工况的较大误差。
操作人员应记住,各种故障都可能导致操作失常,所以在可能发生严重后果的地方,应安装自动报警和联锁系统。
全体操作人员必须经受良好的培训,已判明报警,并及时采取必要措施以免发生危险。
1.2超压保护装置内的所有设备通均常在一定压力下运行。
这个压力通常由自动控制系统来保证。
然而,一旦过程计算机、控制回路及公用设施故障,装置所不能承受的高压就有可能产生。
因此,除报警和联锁系统外,还应安装安全泄放设备,以便保护操作人员和设备。
☆安全设计基础——ASME(美国机械工程师学会)压力容器规范第Vnl章第一节。
——《石油化工企业设计防火规范》GB50160-92——《爆炸和火灾危险环境电力装置设计规范》GB50058-92——《石油化工企业职业安全卫生设计规范》SH3047-93——《工业企业噪声控制设计规范》GBH87-85——《职业性接触毒物危害程度分级》GB5044-85——《工业企业设计卫生标准》TH36-79——《生产设备安全卫生设计规范》GB5083-85☆吸附床的保护整个PSA装置的吸附塔通过安全阀释放高压而得到保护。
而高压一般是由上游高压气源或外部“火源”导致吸附床内气体膨胀而产生的。
如果某只吸附床受到附近的火源的热辐射,便可产生上述情况。
这时应用消防水冷却该容器的表面,以防这个容器过长时间地遭受热冲击。
甲醇裂解制氢装置的操作规程
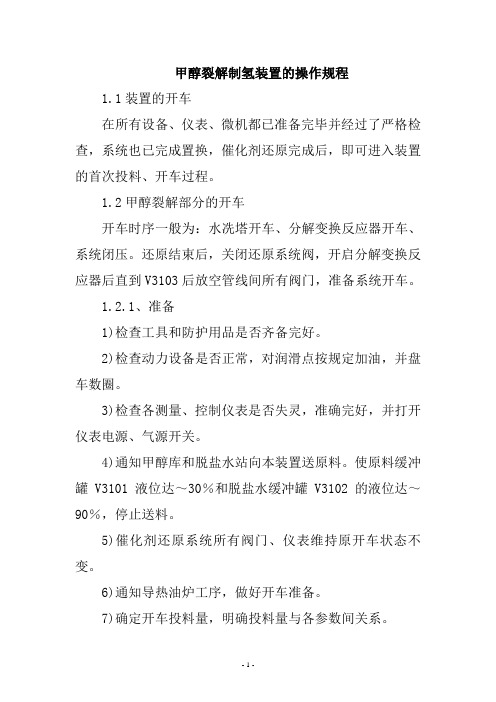
甲醇裂解制氢装置的操作规程1.1装置的开车在所有设备、仪表、微机都已准备完毕并经过了严格检查,系统也已完成置换,催化剂还原完成后,即可进入装置的首次投料、开车过程。
1.2甲醇裂解部分的开车开车时序一般为:水冼塔开车、分解变换反应器开车、系统闭压。
还原结束后,关闭还原系统阀,开启分解变换反应器后直到V3103后放空管线间所有阀门,准备系统开车。
1.2.1、准备1)检查工具和防护用品是否齐备完好。
2)检查动力设备是否正常,对润滑点按规定加油,并盘车数圈。
3)检查各测量、控制仪表是否失灵,准确完好,并打开仪表电源、气源开关。
4)通知甲醇库和脱盐水站向本装置送原料。
使原料缓冲罐V3101液位达~30%和脱盐水缓冲罐V3102的液位达~90%,停止送料。
5)催化剂还原系统所有阀门、仪表维持原开车状态不变。
6)通知导热油炉工序,做好开车准备。
7)确定开车投料量,明确投料量与各参数间关系。
1.2.2、水冼塔开车1)开脱盐水罐出料阀、P3102进口阀、旁路阀,启动泵P3102,使泵运转正常。
2)开泵P3102出口阀,关P3102旁路阀,开液位调节阀LV3202,当水洗塔T3101塔釜出现液位后,开塔底排污手阀,与调节阀LV3202一起控制T3101液位LICA3202在30~40%。
4)开泵P3103进口阀、旁路阀,启动泵P3103,使泵运转正常。
5)开泵P3103出口阀,关P3103旁路阀,开流量调节阀FV3205,与调节阀LV3202及塔底手阀一起控制T3101液位在30~40%。
1.2.3、分解变换反应器开车1)开原料缓冲罐出料阀、P3101进口阀、旁路阀,启动P3101泵,使泵运转正常。
2)开泵P3101出口阀,关P3101旁路阀,开流量调节阀FV3108,开流量调节阀FV3105向换热器送料。
3)使导热油炉温度稳定至230℃,检查装置设备、管线、阀门、仪表等运转是否正常,并观察各工艺参数间关系,若无异常现象便可进行系统闭压。
PSA—提氢工段操作规程
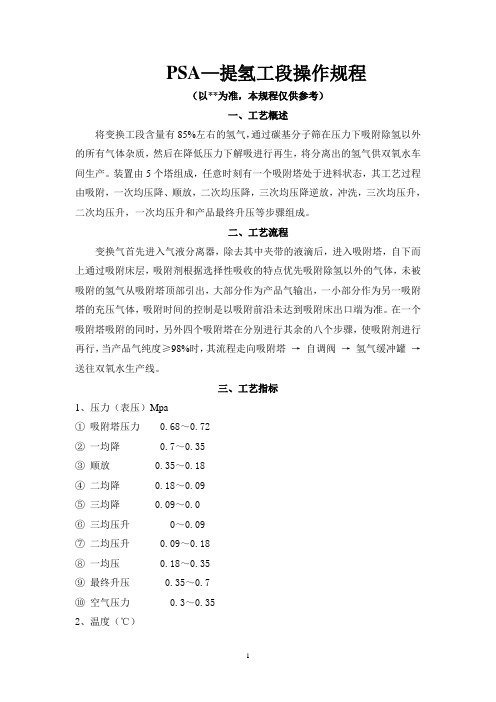
PSA—提氢工段操作规程(以**为准,本规程仅供参考)一、工艺概述将变换工段含量有85%左右的氢气,通过碳基分子筛在压力下吸附除氢以外的所有气体杂质,然后在降低压力下解吸进行再生,将分离出的氢气供双氧水车间生产。
装置由5个塔组成,任意时刻有一个吸附塔处于进料状态,其工艺过程由吸附,一次均压降、顺放,二次均压降,三次均压降逆放,冲洗,三次均压升,二次均压升,一次均压升和产品最终升压等步骤组成。
二、工艺流程变换气首先进入气液分离器,除去其中夹带的液滴后,进入吸附塔,自下而上通过吸附床层,吸附剂根据选择性吸收的特点优先吸附除氢以外的气体,未被吸附的氢气从吸附塔顶部引出,大部分作为产品气输出,一小部分作为另一吸附塔的充压气体,吸附时间的控制是以吸附前沿未达到吸附床出口端为准。
在一个吸附塔吸附的同时,另外四个吸附塔在分别进行其余的八个步骤,使吸附剂进行再行,当产品气纯度≥98%时,其流程走向吸附塔→自调阀→氢气缓冲罐→送往双氧水生产线。
三、工艺指标1、压力(表压)Mpa①吸附塔压力 0.68~0.72②一均降 0.7~0.35③顺放 0.35~0.18④二均降 0.18~0.09⑤三均降 0.09~0.0⑥三均压升 0~0.09⑦二均压升 0.09~0.18⑧一均压 0.18~0.35⑨最终升压 0.35~0.7⑩空气压力 0.3~0.352、温度(℃)①入吸附塔的气体温度≤35②产品气的温度≤353、时间240秒(暂定)①吸附 240②均压 30③均升(一、二、三均压升)240④逆向放压 30⑤均压降 30⑥顺向放压,逆向冲洗(一、二、三均压降)2404、气体成份①产品气纯度≥98%,硫含量≤0.1ppm②空气、无油、无水、无粉尘5、精脱硫后的水、气分离器每小时排放一次,严禁吸附剂带水。
四、主要设备及性能1、PSA—98型程控机主要功能:①电源开关(机内)整机电源②输出开关(机内)如不打开此开关,执行输出,电磁阀无动作,但各显示功能照常。
- 1、下载文档前请自行甄别文档内容的完整性,平台不提供额外的编辑、内容补充、找答案等附加服务。
- 2、"仅部分预览"的文档,不可在线预览部分如存在完整性等问题,可反馈申请退款(可完整预览的文档不适用该条件!)。
- 3、如文档侵犯您的权益,请联系客服反馈,我们会尽快为您处理(人工客服工作时间:9:00-18:30)。
甲醇裂解制氢装置VPSA脱碳部分的操作规程一、VPSA部分介绍1.装置规模公称产氢能力:10000Nm3/h;装置操作弹性:60〜110%;年生产时数:8000小时2.装置组成本单元由10台脱碳吸附塔和3台真空泵等设备组成。
3.工艺流程来自甲醇裂解部分的甲醇裂解气自塔底进入脱碳吸附塔。
其中绝大部分CO2 及一些杂质气体被吸附下来,脱碳后的氢气等气体进入提氢单元。
吸附塔吸附的CO2等气体通过真空泵抽真空被解吸后高点排放。
4.原料气规格本装置的设计允许原料气组分和压力在较宽的范围内变化,但在不同的原料气条件下吸附参数应作相应的调整以保证产品的质量,同时产品氢收率也将随原料而变化。
当原料气条件变化时,物料平衡也将发生相应的变化。
在原料气条件不变的情况下,所有的调节均可由计算机自动完成。
本单元设计的原料气为:甲醇裂解气其详细规格如下:5.产品规格本单元的主要产品为脱碳气,副产品为脱碳解吸气。
在实际生产中,脱碳气的纯度可通过改变PSA单元的操作条件进行调节,而解吸气的组成也会随原料气和产品气的不同而略有不同。
以下为设计的产品气规格:脱碳气脱碳气纯度:CO2 <3.98 v%脱碳气产量:13650Nm3/h脱碳气温度:40℃脱碳气压力:2.5MpaG脱碳解吸气脱碳解吸气温度:40℃脱碳解吸气压力:0.02MpaG二、工艺过程说明1.基本原理吸附是指:当两种相态不同的物质接触时,其中密度较低物质的分子在密度较高的物质表面被富集的现象和过程。
具有吸附作用的物质(一般为密度相对较大的多孔固体)被称为吸附剂,被吸附的物质(一般为密度相对较小的气体或液体)称为吸附质。
吸附按其性质的不同可分为四大类,即:化学吸着、活性吸附、毛细管凝缩、物理吸附。
其中物理吸附是指依靠吸附剂与吸附质分子间的分子力(即范德华力)进行的吸附。
其特点是:吸附过程中没有化学反应,吸附过程进行得极快,参与吸附的各相物质间的平衡在瞬间即可完成,并且这种吸附是完全可逆的。
PSA制氢装置中的吸附主要为物理吸附。
2.吸附剂及吸附力工业PSA制氢装置所用的吸附剂都是具有较大比表面积的固体颗粒,主要有:活性氧化铝类、活性炭类、硅胶类和分子筛类。
不同的吸附剂由于有不同的孔隙大小分布、不同的比表面积和不同的表面性质,因而对混合气体中的各组分具有不同的吸附能力和吸附容量。
2.1本单元所用吸附剂的特性如下:1).A-AS吸附剂A-AS吸附剂对H2O具有很高的吸附能力,同时再生非常容易,并且该吸附剂还具有很高的强度和稳定性,因而适合于装填在吸附塔的底部脱除水分和保护上层吸附剂。
2).HXSI-01 吸附剂本装置所用PSA专用HXSI-01吸附剂属于一种高孔隙率的无定型二氧化硅,化学特性为惰性,无毒、无腐蚀性.其中规格为①2-4球状的吸附剂装于吸附塔中下部,用于吸附水分和CO2。
3.2吸附剂的处理几乎所有的吸附剂都是吸水的,特别是HX5A-98H吸附剂具有极强的亲水性,因而在吸附剂的保管和运输过程中应特别注意防潮和包装的完整性,如果受潮,则必须作活化处理。
对于废弃的吸附剂,一般采用深埋或回收处理。
但应注意:在卸取吸附剂时,必须先用氮气进行置换以确保塔内没有有毒或爆炸性气体。
在正常使用情况下,PSA工段的吸附剂一般是和装置同寿命的。
4.3吸附力在物理吸附中,各种吸附剂对气体分子之所以有吸附能力是由于处于气、固相分界面上的气体分子的特殊形态。
由于吸附剂对混合气体中的氢组分吸附能力很弱,而对其它组分吸附能力较强,因而通过装有不同吸附剂的混合吸附床层,就可将各种杂质吸附下来,得到提纯的氢气。
下图为不同组分在分子筛上的吸附强弱顺序示意图吸附能力☆ 弱 ☆ ☆☆ ☆☆ ☆☆☆ ☆☆☆ ☆☆☆☆ ☆☆☆☆☆☆ ☆☆☆☆☆☆ ☆☆☆☆☆☆☆ 丙烷 ☆☆☆☆☆☆☆ 异丁烷☆☆☆☆☆☆☆☆ 丙烯☆☆☆☆☆☆☆☆ 戊烷☆☆☆☆☆☆☆☆ 丁 烯☆☆☆☆☆☆☆☆☆ 硫 化氢☆☆☆☆☆☆☆☆☆☆ 硫醇☆☆☆☆☆☆☆☆☆☆ 戊烯☆☆☆☆☆☆☆☆☆☆☆ 苯☆☆☆☆☆☆☆☆☆☆☆☆ 甲苯☆☆☆☆☆☆☆☆☆☆☆☆ 乙基苯☆☆☆☆☆☆☆☆☆☆☆☆☆☆ 苯乙烯☆☆☆☆☆☆☆☆☆☆☆☆☆☆☆☆☆ 水 ☆☆☆☆☆☆☆☆☆☆☆☆☆☆☆☆☆☆☆☆☆☆强2.4吸附平衡吸附平衡是指在一定的温度和压力下,吸附剂与吸附质充分接触,最后吸附质组分氮气氢气氧气氩气氮气一氧化碳甲烷二氧化碳乙烷乙烯在两相中的分布达到平衡的过程。
在实际的吸附过程中,吸附质分子会不断地碰撞吸附剂表面并被吸附剂表面的分子引力束缚在吸附相中;同时吸附相中的吸附质分子又会不断地从吸附剂分子或其它吸附质分子得到能量,从而克服分子引力离开吸附相;当一定时间内进入吸附相的分子数和离开吸附相的分子数相等时,吸附过程就达到了平衡。
对于物理吸附而言,动态吸附平衡很快就能完成,并且在一定的温度和压力下,对于相同的吸附剂和吸附质,平衡吸附量是一个定值。
由于压力越高单位时间内撞击到吸附剂表面的气体分子数越多,因而压力越高平衡吸附容量也就越大;由于温度越高气体分子的动能越大,能被吸附剂表面分子引力束缚的分子就越少,因而温度越高平衡吸附容量也就越小。
三、工艺条件与装置处理能力的关系原料气组成:吸附塔的处理能力与原料气组成的关系很大。
原料气中氢含量越高时,吸附塔的处理能力越大;原料气杂质含量越高,特别是净化要求高的有害杂质含量越高时,吸附塔的处理能力越小。
原料气温度:原料气温度越高,吸附剂的吸附量越小,吸附塔的处理能力越低。
吸附压力:原料气的压力越高,吸附剂的吸附量越大,吸附塔的处理能力越高。
解吸压力:解吸压力越低,吸附剂再生越彻底,吸附剂的动态吸附量越大,吸附塔的处理能力越高。
产品纯度:产品纯度越高,吸附剂的有效利用率就越低,吸附塔的处理能力越低。
四、氢气回收率影响因素由于PSA装置的氢气损失来源于吸附剂的再生阶段,因而吸附塔的处理能力越高,则再生的周期就可以越长,单位时间内的再生次数就越少,氢气损失就越少,氢回收率就越高。
不同工艺流程对氢气回收率的影响:在不同的工艺流程下,所能实现的均压次数不同,吸附剂再生时的压力降也就不同,而吸附剂再生时损失的氢气量随再生压力降的增大而增大。
一般来讲,PSA流程的均压次数越多,再生压力降越小,氢气回收率越高。
但从另一方面考虑,均压次数太多,容易将部分杂质带入下一吸附塔并在吸附塔顶部形成二次吸附,从而使该塔在转入吸附时因顶部被吸附的杂质随氢气带出而影响产品氢纯度。
因此在保证纯度的情况下,只有适宜的均压次数才是最佳的,通常操作压力越高,均压次数越多。
对于冲洗流程和真空流程来讲,冲洗流程需消耗一定量氢气用于吸附剂再生,而真空流程则是通过抽真空降低被吸附组分的分压使吸附剂得到再生,故采用冲洗流程时,氢气回收率较低,但真空流程的投资和能耗较高,同时解吸气稳定性差。
产品氢纯度与氢回收率的关系:在原料气处理量不变的情况下,产品氢纯度越高,穿透进入产品氢中的杂质量越少,吸附剂利用率越低,每次再生时从吸附剂死空间中排出的氢气量越大,氢气回收率越低.吸附压力对氢气回收率的影响:吸附压力越高,吸附剂对各种杂质的动态吸附量越大.在原料气处理量和产品氢纯度不变的情况下,吸附循环周期越长,单位时间内解吸次数越少,氢气回收率越高。
冲洗过程对氢气回收率的影响:由于被吸附的大量杂质是通过产品氢的回流冲洗而解吸,故冲洗时间的长短、冲洗气量的大小、冲洗速度的快慢都将影响氢气的回收率。
一般来讲,冲洗时间越长,冲洗过程越均匀,冲洗气量越大,吸附剂的再生越彻底,在纯度不变的情况下,吸附时间越长,氢气回收率越高。
但是,由于冲洗气来自均压结束后的顺放过程,如冲洗气量过大,则顺放过程压力降太大,也可能引起部分杂质穿透,反而不利于冲洗。
因此应控制合理的冲洗气量。
吸附时间(或吸附循环周期)对氢气回收率的影响:在原料气流量和其他工艺参数不变的条件下,延长吸附时间就意味着单位时间内的再生次数减少,再生过程损失的氢气也就越少,氢气回收率越高.但是,在同样条件下,吸附时间越长,进入吸附剂床层的杂质量越大,因吸附剂动态吸附量不变,故穿透进入产品氢的杂质量将增大,这势必会使产品氢纯度下降. 由此可见,吸附时间的改变将同时影响产品氢的纯度和收率.在PSA制氢装置的实际操作过程中,为了提高PSA装置运行的经济性,我们应在保证产品氢中杂质含量不超标的前提下,尽可能的延长吸附时间以提高氢气回收率。
五、产品氢纯度的影响因素原料气流量对纯度的影响:在气体工艺条件及工艺参数不变的条件下,原料气流量的变化对纯度的影响很大,原料气流量越大,每一循环周期内进入吸附塔的杂质量越大,杂质也就越容易穿透,产品氢纯度越低.相反,原料气流量减小,则有利于提高产品氢纯度。
解吸再生条件对产品氢纯度的影响:如前所述,解吸的压力越低,冲洗氢气越多,冲洗再生时间越长,冲洗气流越均匀,则吸附剂的解吸效果也就越好,吸附剂上的残余杂质越少,这样也就越容易保证更高的产品氢纯度。
均压次数对产品氢纯度的影响:原料气处理量和吸附循环周期不变,均压次数越多,均压过程的压力降越大,被吸附的杂质也就越容易穿透进入下一吸附塔并在吸附剂床层顶部被吸附,致使该塔在转入下一次吸附时杂质很容易被氢气带出,影响产品氢纯度.综上所述,为了提高氢气回收率进而提高装置的经济效益,在原料气组成、流量以及温度一定的情况下应尽量提高吸附压力、降低解吸压力、延长吸附时间、适当降低产品纯度(在允许范围内);在原料气流量发生变化时,应适当调整吸附时间以保证产品氢纯度。
六、工业吸附分离流程的主要工序吸附工序一在常温、高压下吸附杂质,出产品。
减压工序一通过一次或多次的均压降压过程,将床层死空间氢气回收。
顺放工序一通过顺向减压过程获得吸附剂再生气源(采用抽真空方式再生时无此工序)。
逆放工序一逆着吸附方向减压使吸附剂获得部分再生冲洗(抽真空)工序一用产品氢冲洗(或抽真空)降低杂质分压,使吸附剂完成最终的再生。
(本装置脱碳部分采用抽真空再生,提氢部分采用冲洗再生)升压工序一通过一次或多次的均压升压和产品气升压过程使吸附塔压力升至吸附压力,为下一次吸附作好准备本单元吸附塔的工作步序包括:吸附、一均降、二均降、三均降、四均降、五均降、六均降、逆放、抽真空、六均升、五均升、四均升、三均升、二均升、一均升、产品脱碳气终升共十六个工艺步序。
七、工艺流程说明7.1流程简述脱碳部分采用10-1-6VPSA流程,即:装置的10个吸附塔中有1个吸附塔始终处于进料吸附的状态,其它9个吸附塔则处于再生的不同工作阶段。
其吸附和再生工艺过程由吸附、连续六次均压降压、逆放、抽真空、连续六次均压升压和产品脱碳气最终升压等步骤组成。
脱碳吸附塔的工作过程如下:1)吸附过程压力为2.6MPa.G,温度为40℃的甲醇裂解气自塔底进入正处于吸附状态的吸附塔(始终有1个吸附塔处于吸附状态)。