氨裂解制氢及与甲醇裂解制氢技术比较
甲醇制氢在硅钢行业的首次应用
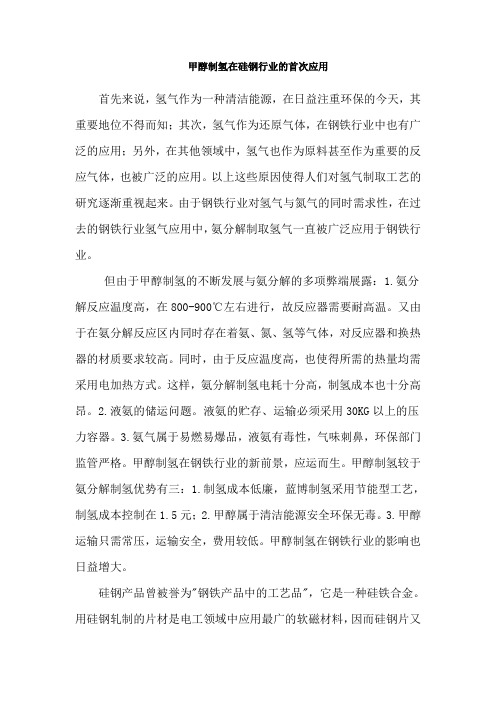
甲醇制氢在硅钢行业的首次应用首先来说,氢气作为一种清洁能源,在日益注重环保的今天,其重要地位不得而知;其次,氢气作为还原气体,在钢铁行业中也有广泛的应用;另外,在其他领域中,氢气也作为原料甚至作为重要的反应气体,也被广泛的应用。
以上这些原因使得人们对氢气制取工艺的研究逐渐重视起来。
由于钢铁行业对氢气与氮气的同时需求性,在过去的钢铁行业氢气应用中,氨分解制取氢气一直被广泛应用于钢铁行业。
但由于甲醇制氢的不断发展与氨分解的多项弊端展露:1.氨分解反应温度高,在800-900℃左右进行,故反应器需要耐高温。
又由于在氨分解反应区内同时存在着氨、氮、氢等气体,对反应器和换热器的材质要求较高。
同时,由于反应温度高,也使得所需的热量均需采用电加热方式。
这样,氨分解制氢电耗十分高,制氢成本也十分高昂。
2.液氨的储运问题。
液氨的贮存、运输必须采用30KG以上的压力容器。
3.氨气属于易燃易爆品,液氨有毒性,气味刺鼻,环保部门监管严格。
甲醇制氢在钢铁行业的新前景,应运而生。
甲醇制氢较于氨分解制氢优势有三:1.制氢成本低廉,蓝博制氢采用节能型工艺,制氢成本控制在1.5元;2.甲醇属于清洁能源安全环保无毒。
3.甲醇运输只需常压,运输安全,费用较低。
甲醇制氢在钢铁行业的影响也日益增大。
硅钢产品曾被誉为"钢铁产品中的工艺品",它是一种硅铁合金。
用硅钢轧制的片材是电工领域中应用最广的软磁材料,因而硅钢片又称电工钢片。
硅钢片广泛用于电动机、发电机、变压器、扼流圈、电磁机构、继电器及测量仪表中。
中国武钢硅钢厂、宅钢冷轧厂、晶龙集团、青拓集团等都是国内硅钢行业的领跑者,甚至在国际上都是名列前茅的。
2016年晶龙集团与青拓集团联合建立的5万吨/年取向硅钢生产线,首次将蓝博大型甲醇制氢应用于生产线,在硅钢行业开启了先河,也奠定了甲醇制氢在硅钢行业的基础,与开辟了甲醇制氢的新天地。
取向硅钢也称冷轧变压器钢, 是一种应用于变压器( 铁芯) 制造行业的重要硅铁合金。
制氢方式对比
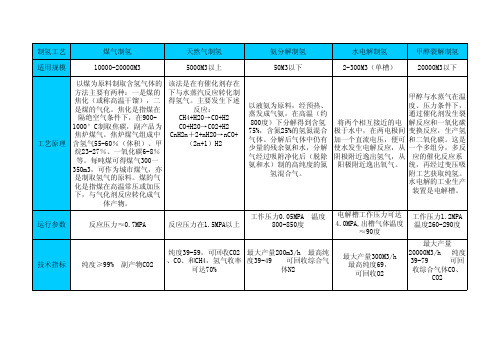
煤0.73kg
电0.355kw/h
原料天然气0.48m3 燃料天然气0.12m3 锅炉给水1.7kg 电 0.2kw/h ≈1.9元(天然气的价格 在上涨)
பைடு நூலகம்
电1.3KW/h 液氨0.52kg/m3 2.6--2.8元 1.氨分解反应温度高,在 800-900℃左右进行,故反 应器需要耐高温。又由于 在氨分解反应区内同时存 在着氨、氮、氢等气体, 对反应器和换热器的材质 要求较高。同时,由于反 应温度高,也使得所需的 热量均需采用电加热方式 。这样,氨分解制氢电耗 十分高。 2.液氨的储运问题。液氨 的贮存、运输必须采用 30KG 以上的压力容器 3.氨气属于易燃易爆品 4.液氨有毒性,气味刺 鼻,环保部门监管严格。
甲醇与水蒸气在温 度、压力条件下, 通过催化剂发生裂 解反应和一氧化碳 变换反应,生产氢 和二氧化碳。这是 一个多组分,多反 应的催化反应系 统,再经过变压吸 附工艺获取纯氢。 水电解的工业生产 装置是电解槽。
工作压力0.05MPA 800-850度
温度
电解槽工作压力可达 4.0MPA,出槽气体温度 ≈90度 最大产量300M3/h 最高纯度69, 可回收O2
流程简单、运行稳定、 操作简便,可实现无人 值守全自动操作,并可 随用氢量的变化实现负 荷的自动调节。
1.甲醇属于清洁能 源安全环保无毒。 2.甲醇运输只需常 压,运输安全,费 用较低
占地面积 (1000m3为 例)建设地 点 优先领域
100m x 80m
50m x 30m,受限于天然 气的供应 中高要求、大规模
运行参数反应压力07mpa反应压力在15mpa以上工作压力005mpa温度800850度电解槽工作压力可达40mpa出槽气体温度90度工作压力12mpa温度260290度技术指标纯度99副产物co2纯度3959可回收co2co和ch4氢气收率可达70最大产量200m3h最高纯度3949可回收综合气体n2最大产量300m3h最高纯度69可回收o2最大产量20000m3h纯度3979可回收综合气体coco2主要消耗m3煤073kg电0355kwh原料天然气048m3燃料天然气012m3锅炉给水17kg电02kwh电13kwh液氨052kgm3脱盐水082kg电55kwh电00556kwh甲醇052kg经营成本0612元19元天然气的价格在上涨2628元56元16元技术安全环保工艺流程较长操作环境较差环境污染严重三废排放中含有大量的灰渣酸性气体和污水废水排放方面排放少量的锅炉污水
化石燃料制氢、甲醇裂解制氢等四种燃料电池制氢法对比分析
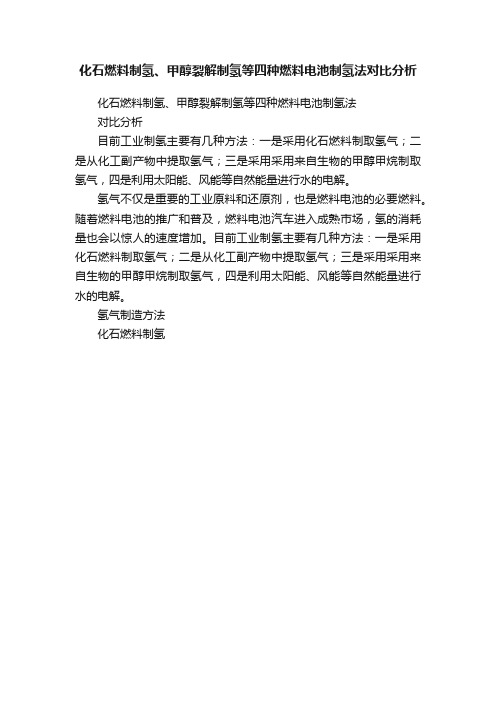
化石燃料制氢、甲醇裂解制氢等四种燃料电池制氢法对比分析
化石燃料制氢、甲醇裂解制氢等四种燃料电池制氢法
对比分析
目前工业制氢主要有几种方法:一是采用化石燃料制取氢气;二是从化工副产物中提取氢气;三是采用采用来自生物的甲醇甲烷制取氢气,四是利用太阳能、风能等自然能量进行水的电解。
氢气不仅是重要的工业原料和还原剂,也是燃料电池的必要燃料。
随着燃料电池的推广和普及,燃料电池汽车进入成熟市场,氢的消耗量也会以惊人的速度增加。
目前工业制氢主要有几种方法:一是采用化石燃料制取氢气;二是从化工副产物中提取氢气;三是采用采用来自生物的甲醇甲烷制取氢气,四是利用太阳能、风能等自然能量进行水的电解。
氢气制造方法
化石燃料制氢。
甲醇裂解制取氢气技术介绍

甲醇裂解制取氢气
前言
甲醇裂解-变压吸附联合工艺制取氢气是我公司自行开发设计的、适用于中小型用氢规模的制氢装置技术,我公司经过近十年的研究改进,已经达到国际先进水平,并先后成功地在一百多家企业得到工业化运用,同时先后获得数项国家专利。
该技术主要是以甲醇、水为原料,经催化转化,变压吸附分离技术得到氢气。
该技术充分体现了流程简洁、占地小,投资省、产品成本低等特点,特别是随着我国生产甲醇装置的大规模建设(内蒙古鄂尔多斯500万吨甲醇/年、海南120万吨甲醇/年、重庆90万吨甲醇/年、黑龙江鹤岗120万吨甲醇/年、新疆石河子60万吨甲醇/年、陕西神木60万吨甲醇/年、山东30万吨甲醇/年等等),可以预见,随着这些装置的不断投产,甲醇裂解制取氢气的生产成本,也会大幅度降低,客户产品的竞争力将得到不断的提高。
技术特点
·生产技术成熟,运行安全可靠。
·原料来源容易,运输贮存方便,价格稳定。
·流程简洁。
·装置自动化程度高,操作简单、容易。
·占地小,投资省,回收期短。
·能耗低,产品成本低。
·无环境污染。
工艺流程简述
甲醇和脱盐水经混合、加压、汽化、过热进入反应器,在催化剂作用下,反应生成H2、CO2、CO等混合气,混合气经变压吸附(PSA)分离技术一次性获得高纯氢气。
制氢技术比较及分析报告
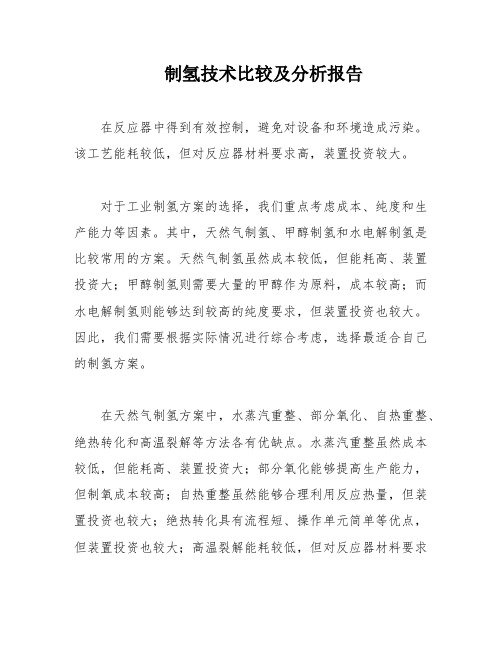
制氢技术比较及分析报告在反应器中得到有效控制,避免对设备和环境造成污染。
该工艺能耗较低,但对反应器材料要求高,装置投资较大。
对于工业制氢方案的选择,我们重点考虑成本、纯度和生产能力等因素。
其中,天然气制氢、甲醇制氢和水电解制氢是比较常用的方案。
天然气制氢虽然成本较低,但能耗高、装置投资大;甲醇制氢则需要大量的甲醇作为原料,成本较高;而水电解制氢则能够达到较高的纯度要求,但装置投资也较大。
因此,我们需要根据实际情况进行综合考虑,选择最适合自己的制氢方案。
在天然气制氢方案中,水蒸汽重整、部分氧化、自热重整、绝热转化和高温裂解等方法各有优缺点。
水蒸汽重整虽然成本较低,但能耗高、装置投资大;部分氧化能够提高生产能力,但制氧成本较高;自热重整虽然能够合理利用反应热量,但装置投资也较大;绝热转化具有流程短、操作单元简单等优点,但装置投资也较大;高温裂解能耗较低,但对反应器材料要求高,装置投资也较大。
因此,我们需要根据实际情况进行选择,综合考虑成本、生产能力和环保等因素。
总之,选择适合自己的制氢方案需要综合考虑多方面因素,包括成本、纯度、生产能力和环保等。
在具体方案选择时,需要根据实际情况进行综合分析和评估,以达到最优的制氢效果。
制氢技术有多种方法,其中包括电解水制氢、聚合电解质薄膜电解制氢、光电解制氢、生物光解制氢和热化学水解。
电解水制氢技术成熟,设备简单,运行可靠,管理方便,不产生污染,可制得氢气纯度高,杂质含量少,适用于各种应用场合。
聚合电解质薄膜电解制氢技术相对成本高,容量小,效率低,使用期短,目前尚不成熟。
光电解制氢是利用太阳能制氢,而生物光解制氢是一种生物制氢工程。
热化学水解技术目前尚不成熟,需要进一步商业化发展。
在制氢方案对比中,天然气水蒸汽重整制氢、甲醇水蒸汽重整制氢和电解水制氢是主要的三种方案。
大型制氢中,天然气水蒸汽重整制氢占主导地位,因为天然气既是原料气也是燃料气,无需运输,氢能耗低,消耗低,氢气成本最低。
甲醇制氢

汽化过热 转化反应 变压吸附 (PSA-H2)-
产品氢气
脱盐水
循环液 冷却、吸收
解吸气
系统操作参数
• 氢气气量: 500--1000NM3/H(温度:常温, 纯度:99.99%,杂质CO≤10PPm、 CO2≤10PPm) • 操作压力:1.0 MPa • 操作温度:230~300℃
0.2%)系统保压0.4MPa。
紧急停车
• 当装置突然停电、停水、停气或装置突然 出现故障时,则需要紧急停车,步骤如下: 1、关闭产品出口阀,关闭裂解气至PSA切断 阀。PSA停止运行。 2、迅速将转化器切至副线,(只关闭转化器 入口阀以免转化器憋压)。 3、导热油开始降温。此时降温的幅度可加大 至20-30℃/h
催化剂保护
1、在任何情况下,催化剂层温度禁止超过300℃。
2、还原后的催化剂绝对禁止与氧气或空气接触。 3、催化剂使用中应尽量避免中途停车。每停一 次车,尽管采取了钝化或氮气保护操作,还是会影
响催化剂使用寿命。
催化剂保护
• 4、 催化剂的升温和降温都必须缓 慢进行,禁止急速升温和降温。 • 5、 在满足生产能力、产率的前提 下,催化剂应在低温下操作,有利 于延长催化剂使用寿命。
换热器
• 利用废热将原料加热。
• 使裂解气降温。
汽化过热器
• 汽化过热器用于将经过换热后的原料液汽 化并过热至接近于反应温度。 • 加热介质是导热油。
冷凝器
• 用循环冷却水将裂解气进一步降温。
• 冷却后的重整气温度小于40℃。
原料罐和脱盐水罐
• 用于储存原料,其材料选用1Cr18Ni9Ti。 (304不锈钢)。
4、停混合液原料泵。
5、联系各部门查明原因及恢复时间,若短时 间能够恢复不做处理,待正常后系统恢复生 产。若长时间不能恢复,则按系统停车处理。
氨裂解制氢综述
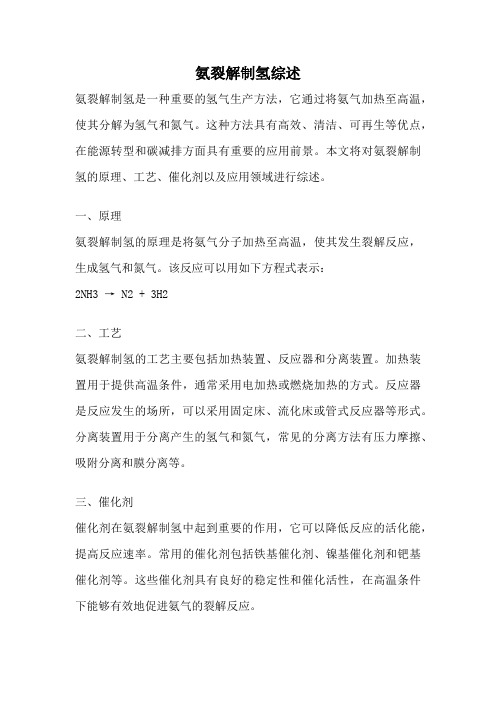
氨裂解制氢综述氨裂解制氢是一种重要的氢气生产方法,它通过将氨气加热至高温,使其分解为氢气和氮气。
这种方法具有高效、清洁、可再生等优点,在能源转型和碳减排方面具有重要的应用前景。
本文将对氨裂解制氢的原理、工艺、催化剂以及应用领域进行综述。
一、原理氨裂解制氢的原理是将氨气分子加热至高温,使其发生裂解反应,生成氢气和氮气。
该反应可以用如下方程式表示:2NH3 → N2 + 3H2二、工艺氨裂解制氢的工艺主要包括加热装置、反应器和分离装置。
加热装置用于提供高温条件,通常采用电加热或燃烧加热的方式。
反应器是反应发生的场所,可以采用固定床、流化床或管式反应器等形式。
分离装置用于分离产生的氢气和氮气,常见的分离方法有压力摩擦、吸附分离和膜分离等。
三、催化剂催化剂在氨裂解制氢中起到重要的作用,它可以降低反应的活化能,提高反应速率。
常用的催化剂包括铁基催化剂、镍基催化剂和钯基催化剂等。
这些催化剂具有良好的稳定性和催化活性,在高温条件下能够有效地促进氨气的裂解反应。
四、应用领域氨裂解制氢的应用领域非常广泛。
首先,它可以用于氢能源的生产和储存。
氢气是一种清洁、高效的能源载体,可以用于燃料电池、燃料电池车辆等领域。
其次,氨裂解制氢还可以用于工业领域的氢气需求,如合成氨、加氢裂化等过程。
此外,氨裂解制氢还可以与其他能源转化技术相结合,如太阳能、风能等,实现可持续能源的生产和利用。
氨裂解制氢是一种重要的氢气生产方法,具有高效、清洁、可再生等优点。
随着能源转型和碳减排的需求增加,氨裂解制氢在未来将有更广泛的应用前景。
然而,目前仍存在一些挑战,如催化剂的稳定性和选择性、工艺的能耗和成本等。
因此,需要进一步的研究和开发,以提高氨裂解制氢的效率和经济性,推动其在能源领域的应用。
甲醇制氢

3、当汽化塔塔釜液位达10%时,开启汽化塔顶放空 阀,缓慢开启塔釜导热油进口阀旁路阀、前后阀,用 调节阀调节进汽化塔导热油量。当塔顶排放气量稳定 时,开启过热器底部排污阀,无液珠排出时关闭排污 阀,即可转入转化炉开车。
变压吸附
变压吸附气体分离技术有3个主要要素,即 吸附剂、 程序控制阀和操作工艺
吸附剂
用于甲醇裂解气变压吸附分离的吸附剂, 经多次研制改进、筛选,强度、寿命、对 杂质的动态吸附量、分离效率等各方面性 能达到世界先进水平,氢气回收率可达 90%。
程控阀
变压吸附装置中使用的程序控制阀现采用 的是防冲刷、阀杆密封自补偿型的第四代 气动程序控制阀,具有密封性好、外泄漏 量小、使用寿命长等特点
与氨裂解制氢技术相比具有反应条件 温和,原料运输和储存方便。
工艺原理
本工艺以来源方便的甲醇和脱盐水为原料,在220~ 280℃下,专用催化剂上催化转化为组成为主要含氢和 二氧化碳转化气。
其原理如下:
主反应: CH3OH=CO+2H2
+90.7 KJ/mol
CO+H2O=CO2+H2 -41.2 KJ/mol
检查消防和安全设施是否齐备完好。
操作人员、分析人员、管理和维修人员经 技术培训,并考核合格方能上岗。
2 开车操作程序 投料开车程序应在催化剂还原结束后进行,
无时间间隔。开车时序一般为:水冼塔开车、汽 化塔开车、转化炉开车、系统升压。还原结束后, 关闭还原系统阀,开启转化炉后直到放空管线间 所有阀门,关闭有关阀门,准备系统开车。
- 1、下载文档前请自行甄别文档内容的完整性,平台不提供额外的编辑、内容补充、找答案等附加服务。
- 2、"仅部分预览"的文档,不可在线预览部分如存在完整性等问题,可反馈申请退款(可完整预览的文档不适用该条件!)。
- 3、如文档侵犯您的权益,请联系客服反馈,我们会尽快为您处理(人工客服工作时间:9:00-18:30)。
氨裂解制氢流程及与甲醇裂解制氢比较
一、氨裂解制氢流程简述
利用液氨为原料,氨经裂解后,每公斤液氨裂解可制得2.64 Nm3混合气体,其中含75%的氢气和25%的氮气。
所得的气体含杂质较少(杂质中含水汽约2 g/ m3,残余氨约1000ppm), 再通过分子筛吸附纯化器,气体的露点可降至-600C 以下,残余氨可降至3 ppm以下。
原料氨容易得到,价格低廉,原料消耗较少。
氨裂解来制取保护气体具有投资少,体积小,效率高等优点
二、氨裂解制氢工作原理
氨气化后在一定温度下,经催化剂作用下裂解为75%的氢气和25%的氮气,并吸收21.9千卡热量,其主要反应为:
2NH3=3H2+N2 −21.9kcal
整个过程因是吸热膨胀反应,温度的提高有利于氨的裂解,同时它又是体积扩大的反应,降低压力有利于氨的分解,升高温度和降低压力可以使氨裂解制氢设备保持最佳状态。
三、氢气纯化原理
当氨裂解制氢设备所产生的氢气合格时进入氢气纯化设备作进一步提纯处理,裂解所得氢气的纯度很高,其中挥发性杂质只有微量的残氨和水份,只须除去微量残氨和水份即可获得高纯度气体。
气体的提纯采用变温吸附技术。
变温吸附(TSA)技术是以吸附剂(多孔固体)内部表面对气体分子在不同温度下吸附性能不同为基础的一种气体分离纯化工艺。
常温时吸附杂质气,加温时脱附杂质气,分子筛表面全是微孔,在常温常压下可吸附相当于自重20%(静态吸附时)的水份和杂质,而在350℃左右的温度下,可以再生完全,每24小时切换一次,以得到纯度和杂质含量均合格的产品气体。
吸附塔为两塔并联交替使用,可实现连续供气。
四、氨裂解制氢催化剂及纯化吸附剂
1.催化剂:采用高温烧结型镍催化剂,对液氨的分解效果好,具有分解活性高、不易粉化、催化剂且不容易老化。
2.吸附剂:采用美国UOP生产的沸石5A分子筛,该分子筛具有很强的吸附性能,较同类产品具有吸附量大,吸附深度深等优点,在常温常压下可吸附相当于自重20%的水气和杂质气,吸附后气体露点可达-60℃以下,用其纯化氨裂解产生的氢氮气,可有效地脱除微量氨和微量水,产生高品质的纯净气体。
五、甲醇裂解制氢简述
甲醇和脱盐水按一定比例混合后经换热器预热后送入汽化塔,汽化后的水蒸气、甲醇蒸汽经加热到220 - 300℃后在压力0.1 – 5 MPa进入转化器在催化剂床层进行催化裂解和变换反应,产出转化气含约74%的H2和24%的CO2,经换热、冷却冷凝后进入水洗吸收塔,塔釜收集未转化完的甲醇和水供循环使用,塔顶气送变压吸附装置提纯。
这是一个多组份、多反应的气固催化反应系统。
反应方程如下:
CH3OH=CO+2H2 −90.7kJ/mol
CO+H2O=CO2+2H2 +41.2kJ/mol
CH3OH+H2O=CO2+3H2 −49.5kJ/mol
反应为吸热反应,重整反应生成的H2和CO2,再经过变压吸附法(PSA)将H2和CO2分离,得到高纯氢气。
六、氨裂解制氢与甲醇裂解制氢比较。