超精密加工与超高速加工技术
_超高速加工技术

2、超高速主轴系统动态特性及热态特性研究:动刚度、固有 频率等参数的影响。 3、超高速主轴系统的润滑和冷却技术研究:润滑充分问题、 冷却效果问题。 4、超高速主轴系统多目标优化设计、虚拟设计技术研究。
第四节 超高速加工进给单元制造技术
超高速加工进给单元是超高速加工机床的重要组成部分。 一、超高速加工进给单元的基本要求: 1、要求具有大的加、减速度:在瞬时达到高速,瞬时准停。 2、要求具有搞的定位精度:能精确控制零件的尺寸精度。 二、超高速加工进给单元的关键技术: 1、高速位置环芯片研制;
4、超高速加工中工件状态的测试技术; 5、超高速加工中自适应控制技术; 6、超高速加工中智能控制技术。
第五节 超高Βιβλιοθήκη 加工测试技术从某种意义上讲,超高速加工测试技术是超高速加工得到应 用的技术关键。 一、超高速加工测试技术的概念: 主要是指在超高速加工过程中,通过传感、分析、信号处理 等,对超高速机床及系统的状态进行实时在线监测和控制的监测 技术。 监测主要基于对切削力、声发射、切削功率和温度等信息参 数检测,来监测加工状态。 二、超高速加工测试的关键技术: 1、基于监控参数的在线检测技术; 2、超高速加工的多传感器融合检测技术; 3、超高速加工机床中各单元系统功能部件的测试技术;
3、超高速进给单元制造技术; 4、超高速加工用刀具和磨具材料; 5、超高速机床支承; 6、超高速加工测试技术。
二、超高速切削机理: 1、萨洛蒙超高速切削理论: 三个切削速度区: ⑴ 常规的切削速度区:现行的切削加工速度范围; ⑵ 不能切削区:此区切削速度下,切削温度过高,刀具不能 承受; ⑶ 高速切削区:当切削速度达到某一数值后,切削温度不再 升高,反而随切削速度继续增加,切削温度呈下降趋势,切削 温度降到刀具能承受的切削速度时,即为高速切削的最低速度。 试验表明,萨洛蒙超高速切削理论并不适用于所有的加工 材料,有些材料在超高速切削时不存在不能切削区。 2、超高速磨削最大切屑厚度hmax理论: 在保持其它参数不变,仅增大磨削速度情况下, hmax会减 小,每个磨削刃上的作用切削力也会减小。
超高速超精密加工技术主要内容

加工方法及机理研究 刀具、 刀具、磨具的研究 加工装备技术研究 测量技术研究
超精密加工技术的应用 超精密加工技术的发展趋势
作 业
(1)超高速、超精密加工技术二者选择其一。 超高速、超精密加工技术二者选择其一。 (2)按照上述提纲要求查阅文献,然后归纳总结写出 按照上述提纲要求查阅文献, 文献综述” “文献综述”。 (3)要求条理清晰,内容精练,3000~5000字。 要求条理清晰,内容精练,3000~5000字 (4)必需手写,不能打印。 必需手写,不能打印。 (5)该作业作为本课程平时成绩的一部分,占15%。 该作业作为本课程平时成绩的一部分, 15%。
超高速超精密加工技术主要内容
一 超高速加工技术
超高速加工技术的内涵 超高速加工技术的关键技术(重点) 超高速加工技术的关键技术(重点)
加工机理研究 主轴单元制造技术研究 进给单元制造技术研究 刀具、 刀具、磨具研究
Байду номын сангаас
超高速加工技术的应用 超高速加工技术的发展趋势
二 超精密加工技术
超精密加工技术的内涵 超精密加工技术的关键技术(重点) 超精密加工技术的关键技术(重点)
七.先进加工技术
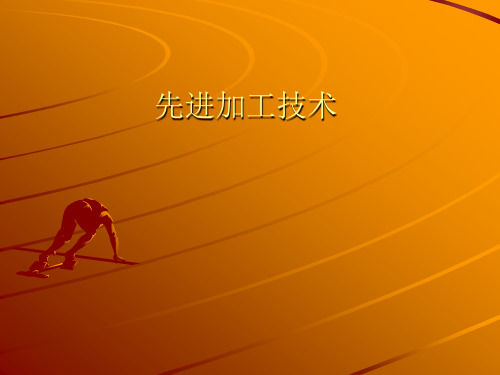
生物工程
Bioengineering
制造工程
Manufacturing Engineering
生物制造
Biomanufacturing
组织和器官之假体与活体制造
பைடு நூலகம்
目的: 1. 提高生产率 2. 改善加工情况 实现: 1. 主轴的零传动:高速主轴单元——电主轴 2. 进给的零传动:直线电机
超高速加工的优点:
1. 显著提高生产效率 2. 切削力可以降低30%以上 3. 切削过程迅速,95%以上的切削热被切
屑带走,工件可以保持冷态。
4. 工作稳定振动小,远离了“机床——工 件——刀具”工艺系统的固有频率范围, 可加工非常精密,光洁的零件。
5. 表面残余应力很小。
不足: 目前只在铝合金和铸铁加工方面应用。 钢的超高速加工还有一些困难
四、超精密加工技术:
分为三种:一般加工、精密加工、超精密加工 动态变化的: 目前标准: 尺寸精度高于0.1μm 表面粗糙度高于0.025μm 形位精度高于0.1μm 从亚微米级向纳米级发展 机械去除法的极限:0.01μm。金刚刀车刀加工有
变形加工:热流动:锻造 粘滞流动:铸造、等静压成形、压铸、注塑 分子定向:液晶定向
超精密加工的要求: 高精度:静态和动态 高刚度:静刚度和动刚度 高稳定性 高度自动化,智能化:减少人为因素
目前超精密加工的主要手段: 1. 金刚石刀具超精密切削 2. 金刚石砂轮和CBN砂轮超精密磨削 3. 超精密研磨和抛光 4. 精密特种加工和复合加工
实现超精密加工的主要条件: 1. 超精密加工机床与装、夹具 2. 刀具、刀具材料、刃磨技术 3. 加工工艺 4. 加工环境控制(恒温、隔振、洁净控制等) 5. 测控技术
超高速超精密加工技术研究与应用

超高速超精密加工技术研究与应用随着科技日益发展,加工技术也在不断更新迭代。
超高速超精密加工技术已成为当下最具前沿性的研究领域之一。
该技术通过高速旋转和高频振荡等方式,实现对物体表面微观方面的加工。
具有加工精度高、效率快、环保等优点,广泛应用于航空、航天、汽车、电子等行业,并有望在未来成为制造业不可或缺的一环。
一、超高速超精密加工技术发展历程1960年代,美国的机械工程师Jean Wang第一次提出了超精密加工的概念,并开始研究如何在微尺度下进行高效率的加工。
80年代,日本和欧洲等国家开始着手研究这一新型加工技术,并加速了其发展进程。
随着技术的不断成熟,超高速超精密加工技术已经形成了多种类别,包括微加工技术、脉冲激光微成型技术、电子束微细加工技术等。
二、超高速超精密加工技术特点超高速超精密加工技术可以实现对物体表面微观方面的加工,具有以下优点:1. 高效率。
超高速超精密加工技术直接控制物体表面的微观结构,可大大缩短加工时间,提高加工效率。
2. 加工精度高。
该技术能够实现微米甚至纳米级别的加工精度,大大提高了产品的质量和可靠性。
3. 环保。
超高速超精密加工技术不需要使用任何化学物质,对环境没有影响。
三、超高速超精密加工技术应用领域超高速超精密加工技术已经广泛应用于多个领域,以下列举几个典型应用领域:1. 航空航天领域。
超高速超精密加工技术可以制造航空航天器件的复杂结构,并提高其性能。
2. 汽车制造领域。
超高速超精密加工技术可以加工汽车发动机零部件的表面,提高其耐磨性、减少磨擦,并增加其使用寿命。
3. 电子领域。
超高速超精密加工技术可以制造微型电子器件,并提高电子设备的性能。
四、超高速超精密加工技术研究进展目前,超高速超精密加工技术的研究主要集中在以下方面:1. 技术优化。
研究如何进一步提高超高速超精密加工技术的加工效率、精度和稳定性,开发更多更优化的加工工具。
2. 新型材料的加工。
研究如何将超高速超精密加工技术应用于新型材料的加工,比如先进的合金材料和光学材料等。
超高速精密加工技术研究

超高速精密加工技术研究超高速精密加工技术是近年来制造领域的重要技术之一,它可以实现对各种材料的高速、高精度、高质量的加工,广泛应用于航空、航天、光学、电子、汽车等领域。
本文将从技术发展、应用领域以及未来发展等方面对超高速精密加工技术进行探讨。
一、技术发展超高速精密加工技术最早起源于日本,1975年,日本理化学研究所研制成功了激光磨削技术,这使得加工速度和精度大大提高。
1980年代初,随着计算机数控技术的发展,超高速加工被广泛应用于模具加工和精密加工领域。
此后,各种新的超高速加工技术如电解加工、电火花加工、等离子体加工、水喷射加工、纳米加工等相继出现,使得加工精度和速度更加突出。
二、应用领域在航空领域,超高速精密加工技术被广泛应用于航空发动机叶片制造、螺旋桨制造等方面。
这些领域对零件要求的精度和表面质量非常高,超高速加工技术可以保证零件的质量和稳定性。
在航天领域,超高速精密加工技术可以用于制造太阳能电池板、航天器外壳、反射镜等。
这些零件的加工难度非常大,超高速加工技术可以大大提高生产效率和品质。
在电子领域,超高速精密加工技术主要应用于半导体芯片加工、各类机械零件加工等方面。
这些领域对零件尺寸和表面精度要求非常高,超高速加工技术可以极大提高生产效率和品质。
在汽车领域,超高速精密加工技术主要应用于发动机零件加工、车身零件加工等方面。
这些领域对零件质量和精度要求较高,超高速加工技术可以保证零件的生产效率和品质。
三、未来发展未来,超高速精密加工技术将继续向深度化和高效化方向发展。
一方面,随着新材料的出现,超高速加工技术将有更广泛的应用领域。
另一方面,随着机械、电子、计算机等技术手段的不断提高,超高速加工技术将更具创新性和智能化。
四、结语超高速精密加工技术是当前制造领域中具有重要地位的技术之一,它的发展对制造业的发展具有重要意义。
未来,随着技术手段的不断提高和领域的不断拓展,超高速加工将更好地服务于制造业的进步和发展。
机械制造的新工艺和新方法
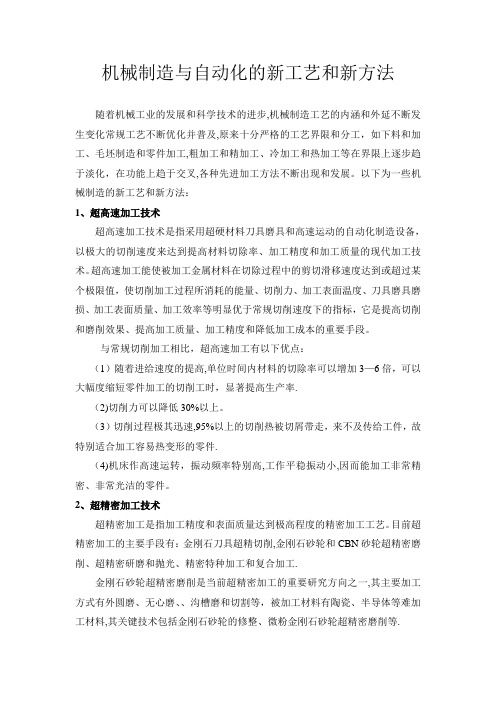
机械制造与自动化的新工艺和新方法随着机械工业的发展和科学技术的进步,机械制造工艺的内涵和外延不断发生变化常规工艺不断优化并普及,原来十分严格的工艺界限和分工,如下料和加工、毛坯制造和零件加工,粗加工和精加工、冷加工和热加工等在界限上逐步趋于淡化,在功能上趋于交叉,各种先进加工方法不断出现和发展。
以下为一些机械制造的新工艺和新方法:1、超高速加工技术超高速加工技术是指采用超硬材料刀具磨具和高速运动的自动化制造设备,以极大的切削速度来达到提高材料切除率、加工精度和加工质量的现代加工技术。
超高速加工能使被加工金属材料在切除过程中的剪切滑移速度达到或超过某个极限值,使切削加工过程所消耗的能量、切削力、加工表面温度、刀具磨具磨损、加工表面质量、加工效率等明显优于常规切削速度下的指标,它是提高切削和磨削效果、提高加工质量、加工精度和降低加工成本的重要手段。
与常规切削加工相比,超高速加工有以下优点:(1)随着进给速度的提高,单位时间内材料的切除率可以增加3—6倍,可以大幅度缩短零件加工的切削工时,显著提高生产率.(2)切削力可以降低30%以上。
(3)切削过程极其迅速,95%以上的切削热被切屑带走,来不及传给工件,故特别适合加工容易热变形的零件.(4)机床作高速运转,振动频率特别高,工作平稳振动小,因而能加工非常精密、非常光洁的零件。
2、超精密加工技术超精密加工是指加工精度和表面质量达到极高程度的精密加工工艺。
目前超精密加工的主要手段有:金刚石刀具超精切削,金刚石砂轮和CBN砂轮超精密磨削、超精密研磨和抛光、精密特种加工和复合加工.金刚石砂轮超精密磨削是当前超精密加工的重要研究方向之一,其主要加工方式有外圆磨、无心磨、、沟槽磨和切割等,被加工材料有陶瓷、半导体等难加工材料,其关键技术包括金刚石砂轮的修整、微粉金刚石砂轮超精密磨削等.金刚石砂轮的修整包括整形和修锐两部分,对于密实型无气孔的金刚石砂轮,如金属结合剂金刚石砂轮,一般在整形后还需要修锐;有气孔型陶瓷结合剂金刚石砂轮在整形后即可使用。
先进制造技术第4章超高速加工技术

目前市场上出现的铣削加工机床主轴转速在 20000~60000r/min,最高达到150000 r/min;
20世纪80年代,计算机控制的自动化生产技术的 高速发展成为国际生产工程的突出特点,工业发达国 家机床的数控化率已高达70%~80%。随着数控机 床、加工中心和柔性制造系统在机械制造中的应用, 使机床空行程动作(如自动换刀、上下料等)的速度和 零件生产过程的连续性大大加快,机械加工的辅助工 时大为缩短。在这种情况下,再一味地减少辅助工时, 不但技术上有难度,经济上不合算,而且对提高生产 率的作用也不大。这时辅助工时在总的零件单件工时 中所占的比例已经较小,切削工时占去了总工时的主 要部分,成为主要矛盾。只有大幅度地减少切削工时, 即提高切削速度和进给速度等,才有可能在提高生产 率方面出现一次新的飞跃和突破。这就是超高速加工 技术(Ultra-high speed machining UHSM)得以 迅速发展的历史背景。。
日本约在20世纪60年代开始了对超高速切削机 制的研究,田中义信利用来复枪改制的超高速切削 装置,实现了高达200~700m/s的超高速切削,对主 切削力和加工表面的变形层性能进行研究。指出: 超高速切屑形成完全是剪切作用的结果,随着切削 速度的提高,剪切角急剧增大,工件材料的变质层 厚度与普通速度下相比降低了50%。
W9Mo3Cr4V等。
硬质合金:是由高硬难熔金属碳
化物粉末,以钴或镍为粘接剂,用粉末
冶金的方法制成的。它的硬度可达
74 ~82(90)HRC。目前多用于制 造各种简单刀具,如车刀、铣刀、刨刀 的刀片等。
超高速加工技术
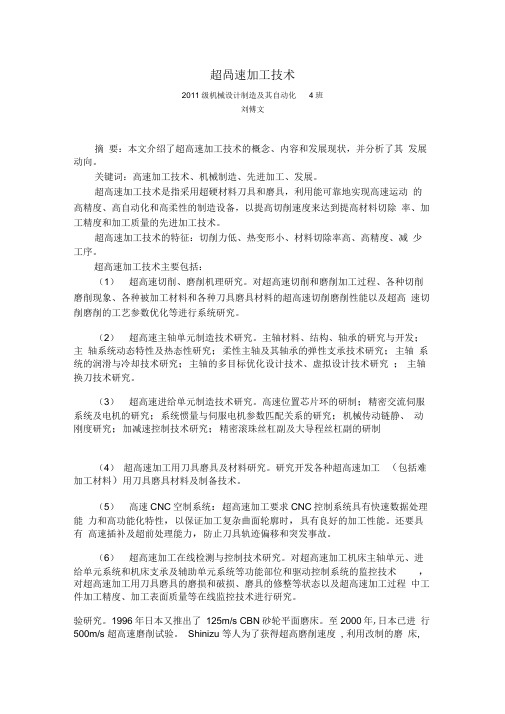
超咼速加工技术2011级机械设计制造及其自动化4班刘傅文摘要:本文介绍了超高速加工技术的概念、内容和发展现状,并分析了其发展动向。
关键词:高速加工技术、机械制造、先进加工、发展。
超高速加工技术是指采用超硬材料刀具和磨具,利用能可靠地实现高速运动的高精度、高自动化和高柔性的制造设备,以提高切削速度来达到提高材料切除率、加工精度和加工质量的先进加工技术。
超高速加工技术的特征:切削力低、热变形小、材料切除率高、高精度、减少工序。
超高速加工技术主要包括:(1)超高速切削、磨削机理研究。
对超高速切削和磨削加工过程、各种切削磨削现象、各种被加工材料和各种刀具磨具材料的超高速切削磨削性能以及超高速切削磨削的工艺参数优化等进行系统研究。
(2)超高速主轴单元制造技术研究。
主轴材料、结构、轴承的研究与开发;主轴系统动态特性及热态性研究;柔性主轴及其轴承的弹性支承技术研究;主轴系统的润滑与冷却技术研究;主轴的多目标优化设计技术、虚拟设计技术研究;主轴换刀技术研究。
(3)超高速进给单元制造技术研究。
高速位置芯片环的研制;精密交流伺服系统及电机的研究;系统惯量与伺服电机参数匹配关系的研究;机械传动链静、动刚度研究;加减速控制技术研究;精密滚珠丝杠副及大导程丝杠副的研制(4)超高速加工用刀具磨具及材料研究。
研究开发各种超高速加工(包括难加工材料)用刀具磨具材料及制备技术。
(5)高速CNC空制系统:超高速加工要求CNC控制系统具有快速数据处理能力和高功能化特性,以保证加工复杂曲面轮廓时,具有良好的加工性能。
还要具有高速插补及超前处理能力,防止刀具轨迹偏移和突发事故。
(6)超高速加工在线检测与控制技术研究。
对超高速加工机床主轴单元、进给单元系统和机床支承及辅助单元系统等功能部位和驱动控制系统的监控技术,对超高速加工用刀具磨具的磨损和破损、磨具的修整等状态以及超高速加工过程中工件加工精度、加工表面质量等在线监控技术进行研究。
验研究。
- 1、下载文档前请自行甄别文档内容的完整性,平台不提供额外的编辑、内容补充、找答案等附加服务。
- 2、"仅部分预览"的文档,不可在线预览部分如存在完整性等问题,可反馈申请退款(可完整预览的文档不适用该条件!)。
- 3、如文档侵犯您的权益,请联系客服反馈,我们会尽快为您处理(人工客服工作时间:9:00-18:30)。
术工技加工与超高速加超精密一、技术概述超高速加工技术是指采用超硬材料的刃具,通过极大地提高切削速。
技术和加工质量的现代加工度和进给速度来提高材料切除率、加工精度超高速加工的切削速度范围因不同的工件材料、不同的切削方式而异。
目前,一般认为,超高速切削各种材料的切速范围为:铝合金已超过1600m/min,铸铁为1500m/min,超耐热镍合金达300m/min,钛合金达150~1000m/min,纤维增强塑料为2000~9000m/min。
各种切削工艺的切速范围为:车削700~7000m/min,铣削300~6000m/min,钻以上等等。
削250m/s削200~1100m/min,磨超高速加工技术主要包括:超高速切削与磨削机理研究,超高速主轴单元制造技术,超高速进给单元制造技术,超高速加工用刀具与磨具等。
术在线自动检测与控制技制造技术,超高速加工-c超精密加工当前是指被加工零件的尺寸精度高于0.1μm,表面粗糙度Ra 小于0.025μm,以及所用机床定位精度的分辨率和重复性高于0.01μm 的加工技术,亦称之为亚微米级加工技术,且正在向纳米级加工技术发展。
超精密加工技术主要包括:超精密加工的机理研究,超精密加工的设备制造技术研究,超精密加工工具及刃磨技术研究,超精密测量技术研究。
条件和误差补偿技术研究,超精密加工工作环境展趋势外发二、现状及国内高速加工.超1工业发达国家对超高速加工的研究起步早,水平高。
在此项技术中,意大利等。
国、主要有德国、日本、美处于领先地位的国家在超高速加工技术中,超硬材料工具是实现超高速加工的前提和先决条件,超高速切削磨削技术是现代超高速加工的工艺方法,而高速数控机床和加工中心则是实现超高速加工的关键设备。
目前,刀具材料已从碳素钢和合金工具钢,经高速钢、硬质合金钢、陶瓷材料,发展到人造金刚石及聚晶金刚石(PCD)、立方氮化硼及聚晶立方氮化硼(CBN)。
切削速度亦随着刀具材料创新而从以前的12m/min 提高到1200m/min 以上。
砂轮材料过去主要是采用刚玉系、碳化硅系等,美国G.E 公司50 年代首先在金刚石人工合成方面取得成功,60 年代又首先研制成功CBN。
90 年代陶瓷或树脂结合剂CBN 砂轮、金刚石砂轮线速度可达125m/s,有的可达150m/s,而单层电镀CBN 砂轮可达250m/s。
因此有人认为,随着新刀具(磨具)材料的不断发展,每隔十年切削速度要提高一倍,亚音速乃至超遥远了。
会太声速加工的出现不在超高速切削技术方面,1976 年美国的Vought 公司研制了一台超高速铣床,最高转速达到了20000rpm。
特别引人注目的是,联邦德国统系年开始1978从)PTW与机床研究所(程工工业大学生产Darmstadt地进行超高速切削机理研究,对各种金属和非金属材料进行高速切削试验,联邦德国组织了几十家企业并提供了2000 多万马克支持该项研究工作,自八十年代中后期以来,商品化的超高速切削机床不断出现,超高速机床从单一的超高速铣床发展成为超高速车铣床、钻铣床乃至各种高速加工中心等。
瑞士、英国、日本也相继推出自己的超高速机床。
日本日立精机的HG400III 型加工中心主轴最高转速达36000~40000r/min,公Ingersoll36~40m/min。
采用直线电机的美国工作台快速移动速度为。
60m/min速度为速司的HVM800 型高加工中心进给移动六西格玛品质论坛在高速和超高速磨削技术方面,人们开发了高速、超高速磨削、深切缓进给磨削、深切快进给磨削(即HEDG)、多片砂轮和多砂轮架磨削等许多高速高效率磨削,这些高速高效率磨削技术在近20 年来得到长足的发展及应用。
德国Guehring Automation 公司1983 年制造出了当时世界第一台最具威力的60kw 强力CBN 砂轮磨床,Vs 达到140~160m/s。
德国阿享工业大学、Bremen 大学在高效深磨的研究方面取得了世界公认的高水平成果,并积极在铝合金、钛合金、因康镍合金等难加工材料方面进行高效深磨的研究。
德国Bosch 公司应用CBN 砂轮高速磨削加工齿轮齿形,采用电镀CBN 砂轮超高速磨削代替原须经滚齿及剃齿加工的工艺,加工16MnCr5材料的齿轮齿形,Vs=155m/s,其Q'达到811mm3/mm.s,德国Kapp 公司应用高速深磨加工泵类零件深槽,工件材料为100Cr6 轴承钢,采用电镀CBV达300m/Q140mm3/mm.削加工中,将淬火后的叶片泵转子10 个一次装夹,一次磨出转子槽,磨削时工件进给速度为 1.2m/min,平均每个转子加工工时只需10 秒钟,槽宽精度可保证在2μm,一个砂轮可加工1300 个工件。
目前日本工业实用磨削速度已达200m/s,美国Conneticut 大学磨削研究中心,1996 年其无心外圆高速磨。
250m/s,最高砂轮磨削速度达上床梦里非梦断肠魂,黄粱犹怯武林途;豪情一朝风云起,英雄血洒江湖路。
风云霭霭七星光,雷雨潇潇神龙踪;绘影丹青群雄图,山河万里齐争王。
nickwu#读手必新手老--全问题大见常坛论6SQ ]广告[曉楓)nickwu (#2黑带中级小中大使用道具加为好友短消息资料个人空间发表于2007-5-13 11:43近年来,我国在高速超高速加工的各关键领域如大功率高速主轴单元、但进行了较多的研究,、陶瓷滚动轴承等方面也高加减速直线进给电机总体水平同国外尚有较大差距,必须急起直追。
质量-SPC,six工2.超精密加超精密加工技术在国际上处于领先地位的国家有美国、英国和日本。
83076UID也度高术不仅总体成套水平,而且商品化的程这些国家的超精密加工技0精华非常高。
2570积分美国是开展超精密加工技术研究最早的国家,也是迄今处于世界领先2921帖子地位的国家。
早在50 年代末,由于航天等尖端技术发展的需要,美国首2271黑带分先发展了金刚石刀具的超精密切削技术,称为“SPDT 技术”(Single Point 2356金币Diamond Turning)或“微英寸技术”(1 微英寸=0.025μm),并发展了阅读622 热心相应的空气轴承主轴的超精密机床。
用于加工激光核聚变反射镜、战术导注册100权限室和验实等等。
如美国LLL弹及载人飞船用球面非球面大型零件2006-6-5月研制成功大型超精密金年7部支持下,于1983 12Y-工厂在美国能源三十六蝕羽窟来自重量4500kg、3DTM-型,该机床可加工最大零件?2100mm刚石车床镜零件、大型天体望远金的激光核聚变用的各种属反射镜、红外装置用度可达到形状误差为工X 光天体望远镜)等。
该机床的加精(包括。
工表面粗糙度为12.5nm,加为Ra4.2nm径),圆度和平28nm(半面度起仍是现在LODTM 超精密车床一大型与该实验室该机床1984 年研制的密度最高的大型金刚石超精技术水平最高、精世界上公认的车床。
,FMEAS16949,MSAsigma,T质量-SPC,sixz*^在超精密加工技术领域,英国克兰菲尔德技术学院所属的克兰菲尔德精密工程研究所(简称CUPE)享有较高声誉,它是当今世界上精密工程的研究中心之一,是英国超精密加工技术水平的独特代表。
如CUPE 生产的Nanocentre(纳米加工中心)既可进行超精密车削,又带有磨头,也可进行超精密磨削,加工工件的形状精度可达0.1μm ,表面粗糙度Ra<。
10nm日本对超精密加工技术的研究相对于美、英来说起步较晚,但是当今世界上超精密加工技术发展最快的国家。
日本的研究重点不同于美国,前者是以民品应用为主要对象,后者则是以发展国防尖端技术为主要目标。
所以日本在用于声、光、图象、办公设备中的小型、超小型电子和光学零了美国。
过进和具有优势的,甚至超件的超精密加工技术方面,是更加先我国的超精密加工技术在70 年代末期有了长足进步,80 年代中期出现了具有世界水平的超精密机床和部件。
北京机床研究所是国内进行超精密加工技术研究的主要单位之一,研制出了多种不同类型的超精密的精密轴m 0.025μ达度精度测试仪器等,如精高机床、部件和相关的.承、JCS-027 超精密车床、JCS-031 超精密铣床、JCS-035 超精密车床、超精密车床数控系统、复印机感光鼓加工机床、红外大功率激光反射镜、超精密振动-位移测微仪等,达到了国内领先、国际先进水平。
航空航天工业部三零三所在超精密主轴、花岗岩坐标测量机等方面进行了深入研究及产品生产。
哈尔滨工业大学在金刚石超精密切削、金刚石刀具晶体定向和刃磨、金刚石微粉砂轮电解在线修整技术等方面进行了卓有成效的研究。
清华大学在集成电路超精密加工设备、磁盘加工及检测设备、微位移工作台、超精密砂带磨削和研抛、金刚石微粉砂轮超精密磨削、非圆截面超精密切削等方面进行了深入研究,并有相应产品问世。
此外中科院长春光学精密机械研究所、华中理工大学、沈阳第一机床厂、成都工具研究所、国防科技大学等都进行了这一领域的研究,成绩显著。
但总的来说,我国在超精密加工的效率、精度可*性,特别是规相有与生产实际要求比,还格(大尺寸)和技术配套性方面与国外比,当大的差距。
六西格玛品质论坛)x-f、更高效率方向发展;向趋势是:向更高精超精密加工技术发展度大型化、微型化方向发展;向加工检测一体化方向发展;机床向多功能模块化方向发展;不断探讨适合于超精密加工的新原理、新方法、新材料。
21 世纪初十年将是超精密加工技术达到和完成纳米加工技术的关键十年。
梦里非梦断肠魂,黄粱犹怯武林途;豪情一朝风云起,英雄血洒江湖路。
风云霭霭七星光,雷雨潇潇神龙踪;绘影丹青群雄图,山河万里齐争王。
nickwu#情查看详,制下载限读阅无使用,身,终费一次交员,加入铁杆会]广告[曉楓)nickwu (#3黑带中级小中大使用道具加为好友短消息个人空间发表于2007-5-13 11:44 资料内容研究十五”目标及主要三、“.目标1用,主轴最高转速达基本实现工业应超高速加工到2005 年;削速度达100~150m/s给速度达40~60m/min,砂轮磨进15000r/min,超精密加工基本实现亚微米级加工,加强纳米级加工技术应用研究,达到83076UID。
平国际九十年代初期水0精华容内2.主要研究2570积分(1)超高速切削、磨削机理研究。
对超高速切削和磨削加工过程、2921帖子各种切削磨削现象、各种被加工材料和各种刀具磨具材料的超高速切削磨2271黑带分行系统研究。
进削的工艺参数优化等削性能以及超高速切削磨2356金币622热心^:wO100阅读权限2006-6-5注册究(2)超高速主研轴材料、结构、轴承的轴单元制造技术研究。
主来自三十六蝕羽窟与开发;主轴系统动态特性及热态性研究;柔性主轴及其轴承的弹性支承技术、计技滑与冷却技术研究;主轴的多目标优化设术研究;主轴系统的润换刀技术研究。