手工砂型铸造流程
砂型铸造
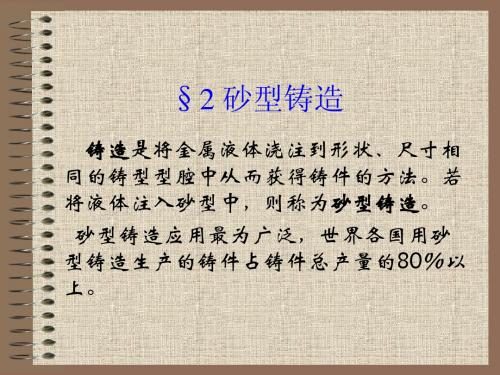
2. 浇注位置的选择
•浇注位置:铸件在铸型中的空间位置。 选择原则 1)主要加工面或主要受力面应置于下部以确保 质量; 2)应利于铸型的填充和型腔中的气体排除; 3)壁厚不均需要补缩时宜将厚大部分置于上部 或侧面; 4)应将铸件的大平面置于铸型的下部并使铸型 侧斜浇注。
1 应) 置主 于要 下加 工 部 面 以 或 确 主 保 要 质 受 量 力 面
2. 铸造收缩率 铸件冷却过程体积要收缩,通常需增 大模样尺寸,才能保证收缩后的铸件 达到所需尺寸。铸件尺寸<模型尺寸。
铸件的收缩率与合金的种类、铸件的大小 和铸件固态收缩受阻的情况有关。 普通灰口铸铁在 0.7 ~ 1% 左右,铸钢为 1.3~2.0左右,有色金属大多在1%左右。
3. 拔模斜度 为便于把模样(或型芯)从砂型(或从 芯盒)中取出,铸件上垂直于分型面的各 个侧面应有一定斜度。 拔模斜度在铸造工艺图中需标出,其大 小取决于立壁的高度、造型方法、模样材 质及该侧面在型腔中的位置。 通常3°~ 15°。
地坑造型 单件、小批生产, 大中型铸件。
2. 机器造型
填砂、紧实、起模整个造型过程有机器完成。 • 特点:与手工造型相比,生产效率↑、铸 件精度高、表面质量好,劳动强度↓。 • 但造型设备及工装投资较大,生产准备周 期长,适于大批生产。
震 压 式 造 型
无箱射压造型
抛 砂 造 型
射 砂 制 芯
分模造型 适于铸件的最大截 面在中间的铸件。
挖砂造型 适于单件,小批生产
成型底板造型 适于成批生产需要 挖砂的铸件。
活块造型 适于单件,小批生产 带有突出部分阻碍起 模的铸件。
刮板造型 适于单件或小批生 产回转体或等截面 的铸件。
地坑造型 适于单件或小批生 产大型铸件。
砂型铸造流程
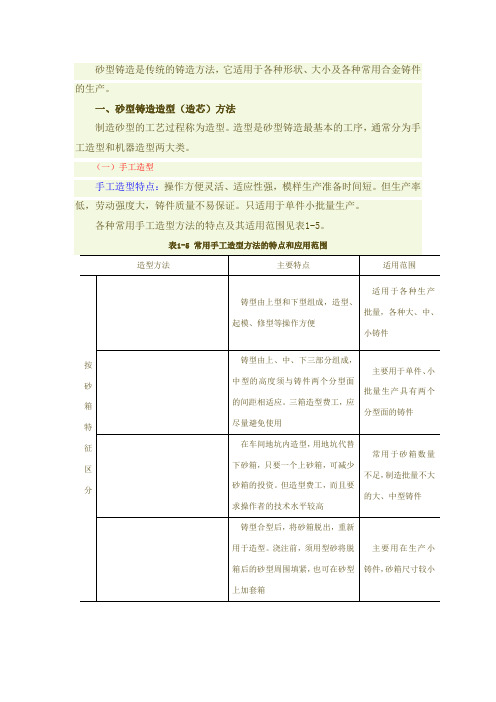
直于分型面的立壁,制造模样时必须留出一定的倾斜度,此倾斜度称为起模斜度,
如图1-29所示。
在铸造工艺图上,加工表面上的起模斜度应结合加工余量直接表示出,而不
加工表面上的斜度(结构斜度)仅需用文字注明即可。
图1-29 起模斜度
3. 收缩率 铸件冷却后的尺寸比型腔尺寸略为缩小,为保证铸件的应有尺 寸,模样尺寸必须比铸件放大一个该合金的收缩率。铸造收缩率 K 表达式为:
手工造型误差大,余量应加大。铸钢件因表面粗糙,余量应加大;非铁合金铸件
价格昂贵,且表面光洁,余量应比铸铁小。铸件的尺寸愈大或加工面与基准面之
间的距离愈大,尺寸误差也愈大,故余量也应随之加大。浇注时铸件朝上的表面
因产生缺陷的机率较大,其余量应比底面和侧面大。灰铸铁的机械加工余量见表
1-6。
表1-6 灰铸铁的机械加工余量
箱后的砂型周围填紧,也可在砂型 铸件,砂箱尺寸较小
上加套箱
模样是整体的,多数情况下,型 腔全部在下半型内,上半型无型 腔。造型简单,铸件不会产生错型 缺陷
适用于一端为最 大截面,且为平面的 铸件
模样是整体的,但铸件的分型面 是曲面。为了起模方便,造型时用 手工挖去阻碍起模的型砂。每造一 件,就挖砂一次,费工、生产率低
图1-27 车床床身铸件
3.尽量使型腔及主要型芯位于下型 这样便于造型、下芯、合箱和检验铸件 壁厚。但下型型腔也不宜过深,并尽量避免使用吊芯和大的吊砂。如图1-28所示。
图1-28 机床支架
注意:选择分型面的上述诸原则,对于某个具体的铸件来说难以全面满足,
有时甚至互相矛盾。因此,必须抓住主要矛盾、全面考虑,至于次要矛盾,则应
注意:为了提高型芯的刚度和强度,需在型芯中放入芯骨;为了提高型芯的 透气性,需在型芯的内部制作通气孔;为了提高型芯的强度和透气性,一般型芯 需烘干使用。
砂型铸造的基本过程 Jun-2014

•砂型铸造的基本过程/20111213/62031.html•砂型铸造有六个基本步骤:1) 把模样放入砂中制成一个模具。
2) 在浇注系统中把原型和砂子接合起来。
3) 把模样去掉。
4) 把模具的空隙用熔化了的金属填充起来。
5) 让金属冷却。
6) 把砂型模具敲掉取出铸件。
砂型铸造案例项目导入:轴承座铸件的造型工艺方案。
铸件简图:轴承座如图2-1所示。
铸件材料:HT150。
体积参数:轮廓尺寸240mm´65mm´75mm,铸件重量约5kg。
生产性质:单件生产。
项目要求:确定铸件的造型工艺方案并完成造型操作。
图2-1 轴承座将液体金属浇入用型砂捣实成的铸型中,待凝固冷却后,将铸型破坏,取出铸件的铸造方法称为砂型铸造。
砂型铸造是传统的铸造方法,它适用于各种形状、大小及各种常用合金铸件的生产。
套筒的砂型铸造过程如图2-2所示,主要工序包括制造模样型芯盒、制备造型材料、造型、制芯、合型、熔炼、浇注、落砂、清理与检验等。
图2-2 套筒的砂型铸造过程铸件生产前需根据零件图绘制出铸造工艺图,铸造工艺图是在零件图上用各种工艺符号及参数表示出铸造工艺方案的图形。
其中包括:浇注位置,铸型分型面,型芯的数量、形状、尺寸及其固定方法,加工余量,收缩率,浇注系统,起模斜度,冒口和冷铁的尺寸和布置等。
铸造工艺图是指导模样(型芯盒)设计、生产准备、铸型制造和铸件检验的基本工艺文件。
砂型铸造主要工序包括:(1) 根据零件图制造模样和型芯盒;(2) 配制性能符合要求的型(芯)砂;(3) 用模样和型芯盒进行造型和造芯;(4) 烘干型芯(或砂型)并合型;(5) 熔炼金属并进行浇注;(6) 落砂、清理和检验。
2.1.1 常用造型工模具1. 砂箱制造砂型时,需要用一种无底、无盖并围绕砂型的框架,以防型砂捣实时向外挤出,这种框架就叫做砂箱,砂箱的作用是便于造型,便于翻转砂型及搬运砂型。
砂箱可紧固着在它里面所捣实的型砂,它的四壁可承受金属液对型砂的侧压力,砂箱附有合型时的对准装置及吊运翻箱和夹紧装置,如图2-3所示。
砂型铸造工艺一般流程

砂型铸造工艺一般流程目录1.型砂,芯砂配制工艺规程-----------------22.制芯工艺守则--------------------------23.砂芯烘干工艺规程----------------------34.造型,下芯,合箱操作规程----------------45.浇注工艺规程--------------------------76.落砂工艺操作规程----------------------107.清理工艺守则--------------------------11XXXX机械有限公司工艺文件砂型铸造通用工艺规程 SXJZ-2011-01-20001.型砂.芯砂配制参见《混砂工艺规程》2.制芯工艺守则2.1芯盒检验,芯盒在车间使用超过半个月,每半个月检验芯盒1次,芯盒磨损以芯盒图纸为准。
2.2制芯.2.2.1舂砂时紧实度要均匀,芯子表面要致密光滑,不得有松砂现象,字要清晰完整,刮砂面要用工具刮子压光.2.2.2芯头用Ф8毫米的气眼针扎透.2.2.3 砂芯应尽量轻轻在专用工作台上均匀敲出或磕出芯盒.2.2.4以修整的砂芯,其几何形状及尺寸必须符合要求,不得有凸凹毛刺,多材,缺陷.2.2.5对于大芯子,烘烤前停放时间不应过长以防蠕变.2.3检芯.2.3.1砂芯必须件件进行检验.2.3.2砂芯几何形状完整,清晰,不得有凸凹毛刺,多材,裂纹等缺陷,表面应致密,光滑.2.3.3检查刹车面外缘处,芯子两侧平面不得大于0.3毫米,厚度尺寸不小于芯盒磨损极限尺寸.2.4码放保存.2.4.1检验合格的芯子应按操作者号在指定位置摆放整齐.3.砂芯烘干工艺规程3.1准备.3.1.1炉衬无裂纹,倒塌等损坏现象,炉内无异物.3.1.2炉门启闭灵活,不变形.3.1.3烟道畅通,烟道闸门启闭灵活.3.1.4台车牢固可靠,运转灵活.3.1.5测温装置准确可靠.3.1.6装炉前去掉外观不合格砂芯.3.1.7根据炉膛内,高处高温低处低温的特点,大复杂件尽量放在高处,装卸时要轻拿轻放.3.1.8在芯子悬空处做好随行砂胎,砂芯停放时间不宜过长,以防变形.3.2烘芯.3.2.1煤窑升温160-200℃,电室升温至260-280℃,时间不超过2小时(电阻炉)或2.5小时.时间要适当,以防哄干不足或过烧.室式燃煤烘干工艺规程,同上.4.造型,下芯,合箱操作规程4.1造型前的准备.4.1.1检查生产装备.4.1.1.1模样的起模装置及吊运装置安装合不合适.4.1.1.2砂箱有下列情况不能使用.a)箱把脱落或有严重变形.b)箱壁破裂未经修补.c)砂箱翘曲变形严重.d)定位销,定位销套孔磨损超过极限偏差.e)销套孔内有严重锈皮或粘砂未清除.4.1.1.3检查出砂,背砂是否符合工艺要求.4.1.1.4准备所需冷铁,芯撑,垫片,不允许有油,水,锈存在.4.1.1.5准备所需脱模剂或分型粉,及其它工具.4.1.1.6机器造型前,尚需检查造型设备.4.1.2 手工造型需要清理,平整场地.4.2 造型.4.2.1 模样和模底板清理干净,撒分型粉或喷涂和刷擦脱模剂.4.2.2采用面砂时,面砂应均匀的覆盖模样及浇注系统上,紧实后的厚度为15-45mm.4.2.3准备安装冷铁.4.2.4为提高砂型强度,在砂型的在平面和凸缘拐角界处插钉子加固.4.2.5砂型紧实应均匀全面,紧实后硬度要达到70-90,捣好后刮平.4.2.6扎气眼时,气孔离型腔20-30mm,气孔Ф10-Ф64.2.7起模要平稳并保持垂直.4.2.8直模后,检查砂型硬度,发现局部松软或破损处,应用同类砂修补.4.3下芯4.3.1检查砂芯质量,不允许将有缺陷的砂芯下入型内,砂芯干燥深度不少于6mm,同时不得过烧.4.3.2按顺序下芯,重要件可用样板控制砂芯位置,做到位置准确, 安放牢固.4.3.3堵塞芯头与芯座的间隙,防止跑铁液.4.3.4下芯完后,应清除型内余砂.4.4合箱.4.4.1合箱前,检查铸型质量,如发现砂芯偏移,芯撑漏放和型内有散砂时,应采取措施解决. 4.4.2合箱按导向销准确平稳操作.4.4.3按工艺要求,放置浇口杯和冒口圈,并用铁板或纸盖好.4.4.4脱箱造型时,脱箱后埋好箱,箱与箱之间扎通气孔.4.4.5合箱后安放压铁,压铁重量,位置应合适.5.浇注工艺规程5.1浇注前的准备.5.1.1浇注时必须了解待浇注件所需铁液牌号及重量.5.1.2检查起吊设备是否正常,包括:5.1.2.1吊车运行是否正常.5.1.2.2吊车的回转机械是否灵活可靠.5.1.3检查浇包数量,修包质量,以及烘干预热是否合格.5.1.4备好保温聚渣,材料及工具.5.1.5检查压铁重量和位置是否合适,浇口杯是否安放妥当.5.1.6根据炉前结果对于铁水质量不合格,温度不高的铁水不得浇注.5.2按浇注工艺要求进行浇注.5.2.2开炉后的第一包铁液(约一至二批料)浇注不重要铸件.5.2.3第一次盛铁液的浇包,至发现沸腾现象应立即停止出铁液,该包铁液不允许浇注铸件,可浇芯骨或回炉料.5.2.4出铁时,铁液不得冲在包壁或塞杆上,出铁完毕,应清除表面渣子,及时用草灰等材料覆盖保温.5.2.5吊包中铁液面应低于包口30mm以上.5.2.6根据铸件要求的浇注温度进行浇注.5.2.7浇注时应有挡渣措施,浇包嘴应尽量接近浇口杯,浇口杯应保持充满并不得引起铁液飞溅或产生漩涡.5.2.8 浇注开始后,应立即引气,大型铸件应点燃出气孔旁的引火材料.5.2.9浇注时如发生铁液猛烈沸腾并从冒口连续喷出铁液时应立即停止浇注.5.2.10当冲天炉不间隔熔炼两个牌号的铸铁时,应准确估计交界铁液进入前炉的时间和数量,交界铁液不可浇注重要铸件.5.2.11浇注时应一次性充满,尽量避免补浇.5.2.12浇注剩余的铁液或不合格铁液应倒入盛回炉料的铁模或倒入废砂中.5.3安全注意事项.5.3.1车间应制定安全技术规则,工作时穿戴好工作服,防热皮鞋,手套,帽子,防护眼镜等.5.3.3吊车工吊运铁液时须鸣铃并不得从现场人员头上经过.5.3.4浇注时不得用眼睛正视冒口.5.3.5挡渣人员不得位于包嘴正面操作.5.3.6浇注完毕后应全面检查,清理场地,并熄灭火源.6.落砂工艺操作规程6.1控制冷却时间,浇注后刹车盘8分钟,大型壳体类3小时方可落砂,生产线上浇注的铸件应控制输送小车的速度,不可大范围调整.6.2去除砂箱上的残铁和残留砂块.6.3浇冒口必须在完全凝固后方能打掉,以防带肉和影响补缩.6.4落砂前先将箱上及地面上的铁片,铁豆打扫收集.6.5落砂后的砂箱堆放整齐备用.6.6清理平整工作场地.7.清理工艺守则7.1准备工作.7.1.1了解铸件结构及清理工艺要求.7.1.2熟悉设备性能及操作规程并严格执行.7.1.3检查设备是否运转正常,发现故障用时排除.7.1.4准备好所用的工具,检查是否完好,安全.7.1.5按规定穿戴好劳保用品.7.2清砂的一般要求.7.2.1工作前应先检查铸件表面有无严重缺陷,如有严重陷,应报告检查员处理.7.2.2铸件内表面所有附着的型.芯应清理干净,飞边,毛刺应铲除掉.7.2.3清砂时不许损伤铸件的边缘,棱角,禁止重锤敲打.7.2.4清除浇冒口时应正确选择敲击方向和敲击力量,以免铸件缺肉损伤.7.2.5铸件转运,堆放清铲过程中不准扔砸撞磕,以免损坏铸件,造成废品.7.3铸件表面清理.7.3.1使用清理设备应严格执行安全操作规程.7.3.2装入的铸件应无导致报废的缺陷.7.3.3经常检查清理设备易损部位和易损件,按要求及时更换,更换叶片时,应使叶轮运转平衡.7.3.4铸件上的披缝,飞刺,多肉,胀箱和错箱造成的不平处应去除磨平.7.3.5粗糙不平的内外圆柱非加工面要用砂轮磨光.7.3.6铸件表面上的夹砂,夹层等缺陷中的砂子应铲除干净.(此页无正文)附加说明本标准由科研所提出本标准由工艺科起草本标准的主要起草人:XXXX机械有限公司工艺文件砂型铸造通用工艺规程编号:SXJZ-2011-01-2000版号:2.0序号:2000-05-01发布 2000-05-08实施XXXX机械有限公司发布。
有色金属手工砂型铸造操作工艺
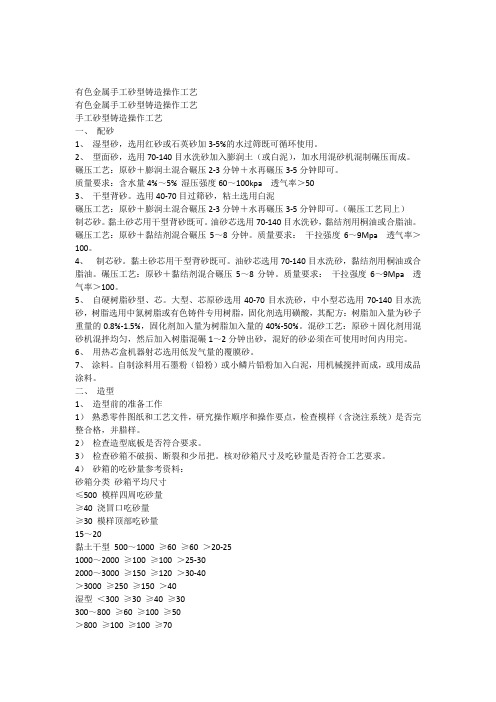
有色金属手工砂型铸造操作工艺有色金属手工砂型铸造操作工艺手工砂型铸造操作工艺一、配砂1、湿型砂,选用红砂或石英砂加3-5%的水过筛既可循环使用。
2、型面砂,选用70-140目水洗砂加入膨润土(或白泥),加水用混砂机混制碾压而成。
碾压工艺:原砂+膨润土混合碾压2-3分钟+水再碾压3-5分钟即可。
质量要求:含水量4%~5% 湿压强度60~100kpa 透气率>503、干型背砂。
选用40-70目过筛砂,粘土选用白泥碾压工艺:原砂+膨润土混合碾压2-3分钟+水再碾压3-5分钟即可。
(碾压工艺同上)制芯砂。
黏土砂芯用干型背砂既可。
油砂芯选用70-140目水洗砂,黏结剂用桐油或合脂油。
碾压工艺:原砂+黏结剂混合碾压5~8分钟。
质量要求:干拉强度6~9Mpa 透气率>100。
4、制芯砂。
黏土砂芯用干型背砂既可。
油砂芯选用70-140目水洗砂,黏结剂用桐油或合脂油。
碾压工艺:原砂+黏结剂混合碾压5~8分钟。
质量要求:干拉强度6~9Mpa 透气率>100。
5、自硬树脂砂型、芯。
大型、芯原砂选用40-70目水洗砂,中小型芯选用70-140目水洗砂,树脂选用中氮树脂或有色铸件专用树脂,固化剂选用磺酸,其配方:树脂加入量为砂子重量的0.8%-1.5%,固化剂加入量为树脂加入量的40%-50%。
混砂工艺:原砂+固化剂用混砂机混拌均匀,然后加入树脂混碾1~2分钟出砂,混好的砂必须在可使用时间内用完。
6、用热芯盒机器射芯选用低发气量的覆膜砂。
7、涂料。
自制涂料用石墨粉(铅粉)或小鳞片铅粉加入白泥,用机械搅拌而成,或用成品涂料。
二、造型1、造型前的准备工作1)熟悉零件图纸和工艺文件,研究操作顺序和操作要点,检查模样(含浇注系统)是否完整合格,并腊样。
2)检查造型底板是否符合要求。
3)检查砂箱不破损、断裂和少吊把。
核对砂箱尺寸及吃砂量是否符合工艺要求。
4)砂箱的吃砂量参考资料:砂箱分类砂箱平均尺寸≤500 模样四周吃砂量≥40 浇冒口吃砂量≥30 模样顶部吃砂量15~20黏土干型500~1000 ≥60 ≥60 >20-251000~2000 ≥100 ≥100 >25-302000~3000 ≥150 ≥120 >30-40>3000 ≥250 ≥150 >40湿型<300 ≥30 ≥40 ≥30300~800 ≥60 ≥100 ≥50>800 ≥100 ≥100 ≥705)检查造型砂是否符合要求,造型工具是否齐备。
砂型铸造工艺流程

砂型铸造工艺流程一、砂型铸造简介砂型铸造是一种常用的铸造方法,通过使用砂模来制造金属铸件。
砂型铸造工艺流程包括模具制备、砂型制备、浇铸、冷却、脱模和后处理等步骤。
本文将详细介绍砂型铸造的工艺流程及每个步骤的具体操作。
二、模具制备在砂型铸造中,模具是制作砂型的重要工具。
首先需要准备好铸造所需的模子。
模子可以使用木模、金属模或者其他材料制作而成。
模具制备的具体步骤如下:1.设计模具结构–根据所需铸件的结构和尺寸,设计模具的内外形状和结构。
–考虑到铸件的收缩率和热胀冷缩等因素,在设计模具时需要留出相应的缩孔和浇口。
2.制作模具–根据设计图纸,选择合适的模具材料进行制作。
–使用机械加工或者手工加工的方式,按照设计图纸的要求制作模具的内外形状。
3.组装模具–将制作好的模具组装在一起,确保模具内外表面的高度一致,以保证最终铸件的尺寸精度。
–使用螺栓或者其他连接方式将模具牢固地固定在一起。
三、砂型制备砂型是铸造的关键步骤之一,其质量直接影响到最终铸件的质量。
砂型制备的具体步骤如下:1.选择砂料–根据铸件的性质和金属的种类,选择适合的砂料。
–砂料应具有良好的塑性和耐高温的特性,以便能够更好地填充模具。
2.调配砂料–将砂料和适量的粘结剂混合,用水使其充分搅拌均匀。
–确保砂料的湿度适中,既能够起到黏合作用,又不会因过度湿润而影响成型效果。
3.成型砂型–将调配好的砂料倒入模具中,使用工具进行压实,确保砂料填充整个模具空间。
–模具中的芯子应根据需要放置在合适的位置,以形成中空的铸件结构。
4.敲击模具–使用锤子等工具敲击模具的四周和底部,以去除空气泡并提高砂型的密实度。
–确保模具表面平整光滑,以便于浇铸过程中金属的流动。
5.脱模–等待砂型充分硬化后,将模具分离并轻轻敲击,使铸件和砂型分离。
–检查铸件和砂型的质量,并进行必要的修整和清理。
四、浇铸浇铸是将熔融金属倒入砂型中的过程。
在浇铸之前,需要进行一系列准备工作:1.预热砂型–在浇铸之前,将砂型预热以提高砂型的温度稳定性。
砂型铸造流程
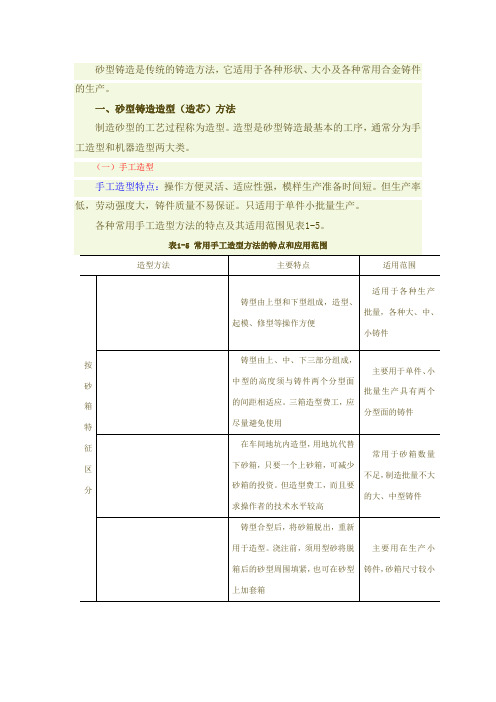
最小铸出孔的参考数值见表1-7。对于零件图上不要求加工的孔、槽以及弯曲孔
等,一般均应铸出。
表1-7 铸件毛坯的最小铸出孔(mm)
生产批量
大量生产 成批生产 单件、小批量生产
最小铸出孔的直径 d
灰铸铁件
铸钢件
12~15
—
15~30
30~50
30~50
50
2. 起模斜度 为了使模样(或型芯)易于从砂型(或芯盒)中取出,凡垂
注意:为了提高型芯的刚度和强度,需在型芯中放入芯骨;为了提高型芯的 透气性,需在型芯的内部制作通气孔;为了提高型芯的强度和透气性,一般型芯 需烘干使用。
二、砂型铸造工艺设计 目的:为了获得健全的合格铸件,减小铸型制造的工作量,降低铸件成本, 在砂型铸造的生产准备过程中,必须合理地制订出铸造工艺方案,并绘制出铸造 工艺图。 铸造工艺图:在零件图中用各种工艺符号表示出铸造工艺方案的图形,其中 包括:铸件的浇注位置;铸型分型面;型芯的数量、形状、固定方法及下芯次序; 加工余量;起模斜度;收缩率;浇注系统;冒口;冷铁的尺寸和布置等。铸造工 艺图是指导模样(芯盒)设计、生产准备、铸型制造和铸件检验的基本工艺文件。 依据铸造工艺图,结合所选造型方法,便可绘制出模样图及合箱图。图1-19为支 座的铸造工艺图、模样图及合箱图。
式中 ——模样或芯盒工作面的尺寸,单位为 mm; ——铸件的尺寸,单位为 mm。
通常,灰铸铁的铸造收缩率为0.7%~1.0%,铸造碳钢为1.3%~2.0%,铸造锡青 铜为1.2%~1.4%。
4. 型芯头 型芯头可分为垂直芯头和水平芯头两大类,如图1-30所示。
图1-30 型芯头的构造 a)垂直芯头 b)水平芯头 (四)铸造工艺设计的一般程序
铸造工艺设计:在生产铸件之前,编制出控制该铸件生产工艺的技术文件。 铸造工艺设计主要是画铸造工艺图、铸件毛坯图、铸型装配图和编写工艺卡片等, 它们是生产的指导性文件,也是生产准备、管理和铸件验收的依据。因此,铸造 工艺设计的好坏,对铸件的质量、生产率及成本起着决定性的作用。
铸件的落砂和清理

表7-2 地面浇注时,中、小型铸铁件的冷却时间
铸件重量/kg
<5 5~10 10~30 30~50
铸件壁厚/mm <8 <12 <18 <25
冷却时间/min 20~30 25~40 30~60 50~ 100
12
表7-2 地面浇注时,中、小型铸铁件的冷却时间
铸件重量/kg 铸件壁厚/mm
50~ 100~ 250~ 500~ 100 250 500 1000
▪ (2)砂轮机表面清理 首先根据铸件 材质选定砂轮材料。铸件材料越硬, 砂轮材料应越软,反之亦然。其清理 操作要点如下:
26
27
转台台车复合型抛喷丸清理机操作 须知
QTZD30转台台车复合型抛喷丸清理机可用于 对大中型铸铁件、锻件等的抛丸清理,使凹凸 表面的弹丸覆盖率≥95%,以去除工件表面的 粘砂、铁锈、氧化皮、污物等,使工件表面呈 现金属本色,消除工件内部应力,并最终达到 提高工件表面及质量的目的。
▪ 若工作完毕设备需要自动停机,按下自 动停止按钮,该设备按如下顺序停机; 抛丸器(1#~5#);螺旋输送器;提 升机;分离器;除尘系统。打开大门, 开出台车,卸下工件,拉下总电源。 33
4:故障状态显示
▪ 在正常状态时,故障指示灯不亮,出现故 障时故障指示灯亮。
▪ 斗提机故障:当斗提机的转速检测开关检 测到速度低于规定时,该灯闪烁,供丸闸 门自动关闭,同时斗提机、分离器、抛丸 器停机,查明故障原因并排除故障后,重 新开机。
▪ 常见的表面清理方法其特点和应用范 围见表7-6。
▪ 下面简单介绍生产中常用的滚筒清理 和砂轮机清理的操作要点
20
表7-6 表面清理方法、特点及应用
表面清理方法 所用设备(工 应用范围 具)与特点
- 1、下载文档前请自行甄别文档内容的完整性,平台不提供额外的编辑、内容补充、找答案等附加服务。
- 2、"仅部分预览"的文档,不可在线预览部分如存在完整性等问题,可反馈申请退款(可完整预览的文档不适用该条件!)。
- 3、如文档侵犯您的权益,请联系客服反馈,我们会尽快为您处理(人工客服工作时间:9:00-18:30)。
可编辑ppt
砂盒 型砂
9
形状完备但取不出来的球体
可编辑ppt
10
分型面
分型面
可编辑ppt
11
分型面
可编辑ppt
12
造型时分型面与 分模面平齐一致
可编辑ppt
13
球形空腔
Hale Waihona Puke 可编辑ppt14在球形空腔上置浇道
可编辑ppt
15
更平稳的浇注系统
可编辑ppt
16
无冒口系统时的铸件
可编辑ppt
17
吃砂量
砂型装配示意图
可编辑ppt
箱把:翻 箱及吊运 操作等 紧固夹紧防 止跑火等
18
实际的砂型铸造 动手操作
注意 安全
可编辑ppt
19
可编辑ppt
20
此课件下载可自行编辑修改,此课件供参考! 部分内容来源于网络,如有侵权请与我联系删除!感谢你的观看!
砂型铸造工艺流程
可编辑ppt
1
砂型铸造
将熔融的金属倒入砂型铸型中,凝固后 获得获得一定形状和性能铸件的成型方 法。
可编辑ppt
2
砂型铸造工艺流程
铸造产品
STEP 1
制备型砂和 芯砂
根据零件图绘 制模样和芯盒
STEP 2
STEP 3
毛坯
合型浇注
STEP 5
砂型制造
可编辑ppt
STEP 4
落砂和清理 3
1
根据零件图绘制模样和芯盒
可编辑ppt
4
2 可塑性
强度
制备型砂和芯砂
耐火度
可编辑ppt
透气性 退让性
5
3
砂型制造
可编辑ppt
6
4
合型浇注
人力式浇包
起重吊式浇包
可编辑ppt
注意 1、浇注前 需要将金 属液表面 的熔渣去 掉。 2、过程中 不允许断 流和飞溅。
7
5
落砂和清理
可编辑ppt
8
制造铸型。