FANUC数控铣床对刀操作步骤
数控铣床对刀操作方法

数控铣床对刀操作方滕一、FANUC绻统对刀操作、设置方滕 工件帺寸100*100,选用Ф10刀具1、必须完成回零操作。
2、装夹好刀具、工件。
3、选择手动方式(JOG),使刀具接近工件。
4、选择MDI方式,输入转速如M3S400,按下启动键 。
5、选择手轮方式,选择合适的位移速度。
6、选择X轴,使刀具侧刃刚好切到工人件右侧面。
7、抬起主轴(X向不能移动)。
8、按下 键进入坐标绻设定界面,接着再按下 ,此时CRT显示如下:9、帆光标移动到G54后X上,如上图,输入X55再按 软键,完成X方向对刀。
(55=50+5,即工件宽度一半加上刀具半径,如在左侧对刀输入X-55,再测量)10、用同样的方滕试切工件里侧(Y轴正方向),帆光标移到G54后Y上,输入Y55再按键。
(如在靠近自己一侧,即Y轴负方向,输入Y-55,再测量)11、当X、Y轴设置完成后,用刀具端面轻轻接触工件上表面,当刀具刚好碰到工件时停止移到。
帆光标移到G54后Z 上,输入Z0后按下 ,完成Z方向对刀设置。
12、帆主轴抬起,把刀具移至安全位置。
二、SIEMENS绻统对刀操作、设置方滕工件帺寸100*100,选用Ф10刀具1、必须完成回零操作。
2、装夹好刀具、工件。
3、选择手动方式(JOG),使刀具接近工件。
4、选择MDI方式,输入转速如M3S400,按下启动键 。
5、选择手轮方式,选择合适的位移速度。
6、选择X轴,使刀具侧刃刚好切到工人件右侧面。
7、抬起主轴(X向不能移动)。
8、按下―→进入坐标绻设定界面,此时CRT显示如下:9、按下软健,进入X轴设定状态,①、帆光标移到“存储在”后面的上,再用进行选择,使Basic变为G54。
②、帆光标移到“方向”后的 上,再用进行选择,使左侧刀具与工件示意图上的刀具在工件的右侧,即X轴正方向(如在左侧对刀用“选择/切换键”,帆刀具示意图上的刀具变换在左侧,即X轴负方向)③、帆光标移到“设置位置到”后 上,输入55后按 软键,完成X设定。
FANUC数控铣床对刀操作步骤

FANUC数控铣床对刀操作步骤
1.准备工作
在进行对刀操作之前,需要准备好以下工具和材料:对刀仪、螺丝刀、日光灯、底座块、对刀块、校验块、刀柄和对刀块夹紧螺丝等。
2.将对刀仪安装在机床上
将对刀仪安装在机床的主轴上,并用螺丝刀固定好。
3.安装刀柄和刀具
将刀柄和刀具正确安装在主轴上,并用螺丝刀夹紧。
4.移动主轴至刀具测量点
根据加工程序要求,使用机床的手动模式将主轴移动至刀具测量点,
即刀具尖端的位置。
5.设置对刀块
将底座块和校验块放置在工件上,然后将对刀块放到刀具尖端上,并
用对刀块夹紧螺丝将其固定住。
6.开启对刀程序
在机床的控制面板上选择对刀程序,并按照提示操作,开始对刀操作。
7.确认对刀结果
对刀程序运行结束后,查看对刀仪的显示结果,确认刀具尖端与刀具
所在位置的偏差。
8.调整刀具偏差
根据对刀结果,调整刀具的位置,确保刀具尖端的位置准确无误。
9.完成对刀操作
当确认刀具尖端位置准确无误后,即完成了对刀操作。
10.完善记录
在对刀操作完成后,及时将对刀结果记录下来,并保存到相应的文件中,以备将来查阅。
总结起来,FANUC数控铣床对刀操作步骤包括准备工作、安装对刀仪、安装刀柄和刀具、移动主轴至刀具测量点、设置对刀块、开启对刀程序、
确认对刀结果、调整刀具偏差、完成对刀操作和完善记录。
通过严格按照
以上步骤进行对刀操作,可以确保刀具正确安装,提高加工效率和精度,
保证产品质量。
数控机床(FANUC系统)对刀步骤
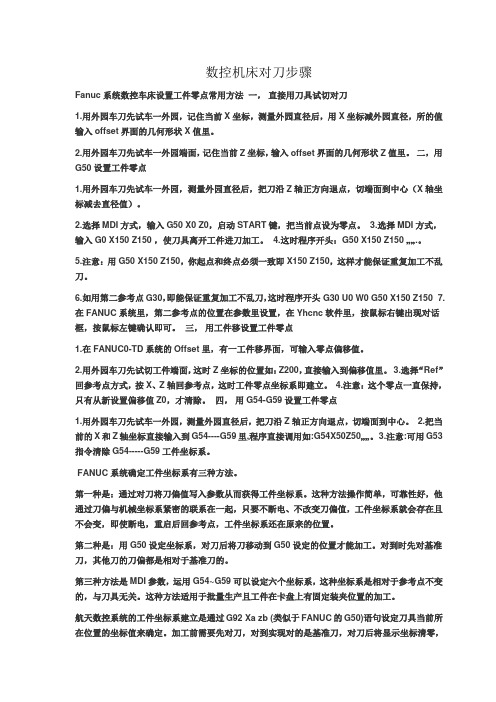
数控机床对刀步骤Fanuc系统数控车床设置工件零点常用方法一,直接用刀具试切对刀1.用外园车刀先试车一外园,记住当前X坐标,测量外园直径后,用X坐标减外园直径,所的值输入offset界面的几何形状X值里。
2.用外园车刀先试车一外园端面,记住当前Z坐标,输入offset界面的几何形状Z值里。
二,用G50设置工件零点1.用外园车刀先试车一外园,测量外园直径后,把刀沿Z轴正方向退点,切端面到中心(X轴坐标减去直径值)。
2.选择MDI方式,输入G50 X0 Z0,启动START键,把当前点设为零点。
3.选择MDI方式,输入G0 X150 Z150 ,使刀具离开工件进刀加工。
4.这时程序开头:G50 X150 Z150 …….。
5.注意:用G50 X150 Z150,你起点和终点必须一致即X150 Z150,这样才能保证重复加工不乱刀。
6.如用第二参考点G30,即能保证重复加工不乱刀,这时程序开头 G30 U0 W0 G50 X150 Z1507.在FANUC系统里,第二参考点的位置在参数里设置,在Yhcnc软件里,按鼠标右键出现对话框,按鼠标左键确认即可。
三,用工件移设置工件零点1.在FANUC0-TD系统的Offset里,有一工件移界面,可输入零点偏移值。
2.用外园车刀先试切工件端面,这时Z坐标的位置如:Z200,直接输入到偏移值里。
3.选择“Ref”回参考点方式,按X、Z轴回参考点,这时工件零点坐标系即建立。
4.注意:这个零点一直保持,只有从新设置偏移值Z0,才清除。
四,用G54-G59设置工件零点1.用外园车刀先试车一外园,测量外园直径后,把刀沿Z轴正方向退点,切端面到中心。
2.把当前的X和Z轴坐标直接输入到G54----G59里,程序直接调用如:G54X50Z50……。
3.注意:可用G53指令清除G54-----G59工件坐标系。
FANUC系统确定工件坐标系有三种方法。
第一种是:通过对刀将刀偏值写入参数从而获得工件坐标系。
数控铣床对刀的步骤与方法

数控铣床对刀的步骤与方法数控铣床对刀的步骤与方法1、首先对z轴对刀:将主轴上刀上相应的刀具——手动方式下启动主轴——用JOG方式和V AR方式让刀具正好停在工作的上表面上——记下此进机床坐标系下Z轴的坐标值。
2、再对Y轴进行对刀:将刀具向X轴向的工件外边缘上靠——用JOG方式和V AR方式让刀具正好停在X方向的工件外边缘上——记下此时的坐标值——将坐标值加上刀具的半径值。
3、再对X轴进行对刀:将刀具向Y轴向的工件外边缘上靠——用JOG方式和V AR方式让刀具正好停在Y方向的工件外边缘上——记下此时的坐标值——将坐标值加上刀具的半径值。
4、将上述XYZ的坐标输到参数的零点偏置的G54下。
5、验证对刀是否正确:选用MDA工作方式——输入程序段“G54 G0 X0 Z0”——看是否刀具停在编程坐标称的原点位置。
主程序XING.MPFN01 G54 建立工件坐标系N02 G0G94G90F200S300M3T4D1 确定工艺参数N03 X60Y40Z5 设定钻削循环参数N04 R101=5R102=2R103=9R104=-17.5R105=2 调用钻削循环N05 LCYC82N06 M6T01 换刀N07 R116=60R117=40R118=60R119=40N08 R120=8 R121=4 R122=120 R123=300N09 R124=0.75 R125=0.5 R126=2 R127=1N10 LCYC75 调用加工循环N11 M2 程序结束G54G90G94M03S1200M6T1G0Z100X0 Y0G0Z10R101=10.000 R102=5.000R103=0.000 R104=-17.500R116=0.000 R117=0.000R118=100.000 R119=80.000 R120=8.000 R121=1.000R122=100.000 R123=1000.000 R124=0.100 R125=0.100R126=2.000 R127=1.000 LCYC75G0Z100M30。
详述数控铣床的对刀流程
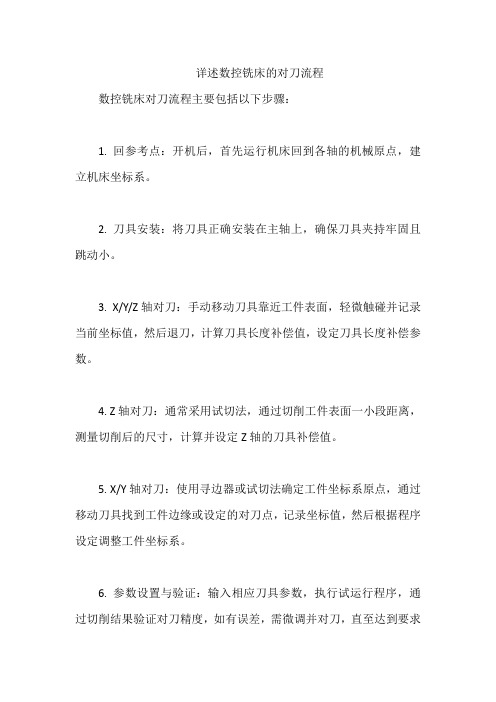
详述数控铣床的对刀流程
数控铣床对刀流程主要包括以下步骤:
1. 回参考点:开机后,首先运行机床回到各轴的机械原点,建立机床坐标系。
2. 刀具安装:将刀具正确安装在主轴上,确保刀具夹持牢固且跳动小。
3. X/Y/Z轴对刀:手动移动刀具靠近工件表面,轻微触碰并记录当前坐标值,然后退刀,计算刀具长度补偿值,设定刀具长度补偿参数。
4. Z轴对刀:通常采用试切法,通过切削工件表面一小段距离,测量切削后的尺寸,计算并设定Z轴的刀具补偿值。
5. X/Y轴对刀:使用寻边器或试切法确定工件坐标系原点,通过移动刀具找到工件边缘或设定的对刀点,记录坐标值,然后根据程序设定调整工件坐标系。
6. 参数设置与验证:输入相应刀具参数,执行试运行程序,通过切削结果验证对刀精度,如有误差,需微调并对刀,直至达到要求
精度。
FANUC数控铣床对刀操作步骤
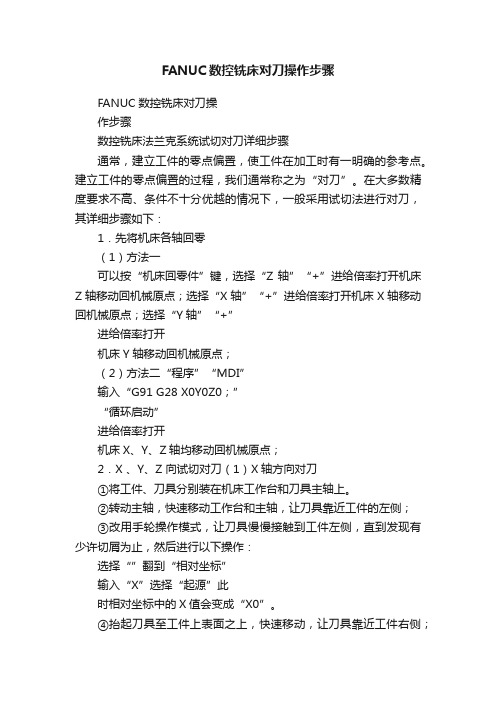
FANUC数控铣床对刀操作步骤FANUC数控铣床对刀操作步骤数控铣床法兰克系统试切对刀详细步骤通常,建立工件的零点偏置,使工件在加工时有一明确的参考点。
建立工件的零点偏置的过程,我们通常称之为“对刀”。
在大多数精度要求不高、条件不十分优越的情况下,一般采用试切法进行对刀,其详细步骤如下:1.先将机床各轴回零(1)方法一可以按“机床回零件”键,选择“Z轴”“+”进给倍率打开机床Z轴移动回机械原点;选择“X轴”“+”进给倍率打开机床X轴移动回机械原点;选择“Y轴”“+”进给倍率打开机床Y轴移动回机械原点;(2)方法二“程序”“MDI”输入“G91 G28 X0Y0Z0;”“循环启动”进给倍率打开机床X、Y、Z轴均移动回机械原点;2.X 、Y、Z 向试切对刀(1)X轴方向对刀①将工件、刀具分别装在机床工作台和刀具主轴上。
②转动主轴,快速移动工作台和主轴,让刀具靠近工件的左侧;③改用手轮操作模式,让刀具慢慢接触到工件左侧,直到发现有少许切屑为止,然后进行以下操作:选择“”翻到“相对坐标”输入“X”选择“起源”此时相对坐标中的X值会变成“X0”。
④抬起刀具至工件上表面之上,快速移动,让刀具靠近工件右侧;⑤改用手轮操作模式,让测头慢慢接触到工件左侧,直到发现有少许切屑为止,记下此时机械坐标系中的X 坐标值,如,然后进行以下操作:选择“”翻到“相对坐标”输入“”选择“预定”此时相对坐标中的X值会变成“”。
(2)Y轴方向对刀操作与X轴同。
假设按上面同样的操作步骤后得出“”。
(3)Z轴方向对刀①转动刀具,快速移动到工件上表面附近;②改用手轮操作模式,让刀具慢慢接触到工件上表面,直到发现有少许切屑为止,然后进行以下操作:选择“”翻到“相对坐标”输入“Z”选择“起源”此时相对坐标中的Z值会变成“Z0”。
此时此刻,相对坐标值不再作改动。
将刀具移到某一安全位置,假设移到相对坐标值显示为“X0、、”的位置处。
(4)设偏置补偿选择“”“坐标系”光标移动到G54的位置上,输入相对坐标当前值进行测量,具体操作如下:输入“X0”“测量”输入“”“测量”输入“”“测量”此时刀具偏置的补偿已经建立,等待操作者的调用后即生效。
斯沃数控仿真对刀说明(可编辑)(可编辑)
→按→→ →→→ →第一章Fanuc oi 对刀1.1 FANUC OiT 对刀1、T01 刀(外圆刀)对刀①手动模式→试切工件端面→Z 方向不动,沿 X方向退出 进入参数输入界面。
图 1图 2②→如图 1→输入 z0→T01 刀 Z 轴对刀完毕。
③ 试切外圆→X 方向不动,沿 Z 方向退出→工具条中测量直径(假设测量得直径φ96.17)→进入参数输入界面,按 →→输入测量的直径 X96.17→→T01 刀(外圆刀)X 方向对刀完毕。
2、T02 刀(割刀)对刀①换 T02 刀(割刀)→碰工件端面→Z 方向不动,沿 X方向退出→进入参数 输入界面,按→→光标移到 2 号刀补→输入 z0→→T02刀 Z 轴 对刀完毕。
② 试切外圆→X 方向不动,沿 Z方向退出→工具条中测量直径(假设测量得直径φ95.67) 进入参数输入界面,按 → →光标移到 2 号刀补→输入测 量的直径 X95.67→T02 刀(割刀)X 方向对刀完毕。
3、T03 刀(螺纹刀)对刀①换 T03 刀(螺纹刀)→碰工件端面→Z 方向不动,沿 X方向退出→进入参 数输入界面,按→→光标移到 3 号刀补→输入 z0→T03 刀 Z 轴对刀完毕。
② 试切外圆→X 方向不动,沿 Z方向退出→工具条中测量直径(假设测量得直径φ94.67) 进入参数输入界面,按 → →光标移到 3 号刀补→输入测 量的直径 X94.67→T03 刀(割刀)X 方向对刀完毕→对刀全部完成。
→1.2.FANUC oiM 对刀手动模式→使刀具沿 Z 方向与工件上表面接触→按进入参数输入界面,如:图 3 图 4 按出现图 4,移动光标至 G54 坐标系处→输入 Z120→→此时,Z 轴即对刀完毕。
移动刀具,使刀具在 X 轴的正方向与工件相切→按进入参数输入界面(如图 3)按→移动光标至 G54 坐标系处→输入主轴中心到所要设定的工件坐标系原点之间 的距离值(本例题的值为 X135)→→此时,X 轴即对刀完毕。
FANUC数控铣床对刀操作步骤
FANUC数控铣床对刀操作步骤FANUC数控铣床是一种非常常见的数控设备,用于在工件上进行高精度的铣削加工。
对刀操作是数控铣床的一项重要工作,正确的对刀操作可以保证加工质量和工作效率。
下面将详细介绍FANUC数控铣床的对刀操作步骤。
1.准备工作-确保数控铣床和工作区域内没有杂物,并确保刀具安装台上没有其他刀具。
-打开数控铣床的电源,确保设备供电正常。
-检查刀具库存,确保有足够的合适刀具供使用。
2.刀具安装-确保选择合适的刀具,根据工件的加工要求选择不同的切削刀具。
-使用合适的刀具夹具将刀具安装到刀具安装台上。
-使用扳手紧固刀具,确保刀具安装牢固。
3.刀具测量-选择合适的刀具测量装置,可以是机床上的刀具测量装置或外部刀具测量装置。
-将刀具测量装置安装到数控铣床上,确保连接稳定。
-启动数控铣床,通过刀具测量装置完成对刀。
-根据刀具测量装置的指示,调整刀具位置,确保刀具测量装置能够精确检测到刀具的位置。
4.刀具长度补偿-输入刀具长度补偿指令,设置刀具长度补偿值。
-根据实际需求,可以设置正数或负数的刀具长度补偿值。
5.刀具半径补偿-输入刀具半径补偿指令,设置刀具半径补偿值。
-根据实际需求,可以设置正数或负数的刀具半径补偿值。
6.保存刀具补偿值-按照提示,输入需要保存的刀具编号和刀具补偿值。
-确认保存操作,将刀具补偿值保存到数控铣床的库存中。
以上就是FANUC数控铣床对刀操作的基本步骤。
在实际操作中,应严格按照操作规程进行,并根据具体情况进行操作。
对刀操作是数控铣床加工过程中的重要环节,需要经过专业的培训和实践,确保操作的准确性和安全性。
FANUC_Series_0i_MD数控铣床面板操作和对刀
数控铣床面板操作与对刀(一) Fanuc-Oi MD数控系统简介图2-1 Fanuc-Oi MD数控系统CRT/MDI面板Fanuc Oi Mate-MD数控系统面板由系统操作面板和机床控制面板三部分组成。
1 系统操作面板系统操作面板包括CRT显示区 MDI编辑面板。
如图2-1。
(1) CRT显示区:位于整个机床面板的左上方。
包括显示区和屏幕相对应的功能软键(图2-2)。
(2)编辑操作面板(MDI面板):一般位于CRT显示区的右侧。
MDI面板上键的位置(如图:2-3)和各按键的名称及功能见表2-1和表2-2。
图2-2 Fanuc Oi Mate-MD数控系统CRT显示区1 功能软键2 扩展软键图2-3 MDI面板表2-1 Fanuc Oi MD系统MDI面板上主功能键与功能说明按键符号名称功能说明序号1 位置显示刀具的坐标位置。
表2-2 Fanuc Oi MD系统MDI面板上其他按键与功能说明2 机床控制面板Fanuc Oi Mate-MD数控系统的控制面板通常在CRT显示区的下方(如图:2-3),各按键(旋钮)的名称及功能见表2-3。
图2-3 Fanuc Oi Mate-MD数控系统的控制面板表2-3 Fanuc Oi Mate-MD数控系统的控制面板各按键及功能序号按键旋钮符号按键旋钮名称功能说明1系统电源开关按下左边绿色键,机床系统电源开;按下右边红色键,机床系统电源关。
2急停按键紧急情况下按下此按键,机床停止一切的运动。
3循环启动键在MDI或者MEM模式下,按下此键,机床自动执行当前程序。
序号按键旋钮符号按键旋钮名称功能说明4 循环启动停止键在MDI或者MEM模式下,按下此键,机床暂停程序自动运行,直接再一次按下循环启动键。
5 进给倍率旋钮以给定的F指令进给时,可在0—150%的围修改进给率。
JOG方式时,亦可用其改变JOG速率。
6 机床的工作模式1) DNC:DNC工作方式2) EDIT:编辑方式3) MEM:自动方式4) MDI:手动数据输入方式5) JOG:手动进给方式6) MPG:手轮进给方式7) ZRN:手动返回机床参考零点方式序号按键旋钮符号按键旋钮名称功能说明7 轴进给方向键在JOG或者RAPID模式下,按下某一运动轴按键,被选择的轴会以进给倍率的速度移动,松开按键则轴停止移动。
FANUC对刀方法
FANUC对刀方法
1、启动主轴
(1)按MDI键。
(2)按程序键(PROG)(画面显示程序名O0000)→输入M03 S400。
(3)按EOB键。
(4)按插入键(INSERT)。
(5)按循环启动键(CYCLE START)主轴正转。
2、调刀方式是在MDI方式下(以调一号刀为例)。
(1)按MDI键。
(2)按程序键(PROG)。
(3)输入T0100→按EOB键。
(4)按插入键(INSERT)。
(5)按循环启动键(CYCLE START),1号刀调到当前位置。
3、设置X、Z向的刀具偏置值(设定工件坐标系)
Z轴对刀:
(1)选择一号刀具(外圆刀),按手摇键(HANDLE)。
(2)按主轴正转键(CW ),主轴正转。
(3)按位置(POS)键,再按软键(综合)。
(4)选择坐标轴,摇动手摇脉冲发生器,试切工件端面至中心,Z轴不动,沿X轴退刀。
(5)按刀补键(OFFSET∕SETTING)。
(6)按软键(刀偏)。
(7)按软键(形状)后,将光标移到与刀具号相对应的刀补参数(如1号刀,则将光标移至“G01”行)。
(8)输入“Z0”,按软键(测量),Z轴刀具偏置参数即自动存入。
X轴对刀:
(1)试切工件外圆车一段距离,X轴不动,刀具沿Z轴退出,停主轴,测量外圆直径并记录下数值(如测量直径为43.98mm)。
(2)在刀补画面“G001”行输入“X43.98”→按软键(测量),X轴的刀具偏移参数即自动存入,1号刀具偏置设定完成。
- 1、下载文档前请自行甄别文档内容的完整性,平台不提供额外的编辑、内容补充、找答案等附加服务。
- 2、"仅部分预览"的文档,不可在线预览部分如存在完整性等问题,可反馈申请退款(可完整预览的文档不适用该条件!)。
- 3、如文档侵犯您的权益,请联系客服反馈,我们会尽快为您处理(人工客服工作时间:9:00-18:30)。
步骤
数控铳床法兰克系统试切对刀详细步骤
通常,建立工件的零点偏置, 使工件在加工时有一明确的参考点。建立工件的零点偏置的过
程,我们通常称之为“对刀”。在大多数精度要求不高、条件不十分优越的情况下,一般采 用试切法进行对刀,其详细步骤如下:
1.先将机床各轴回零
(1)方法一
可以按“机床回零件”键, 选择“Z轴”"+”进给倍率打开机床Z轴移动回机械原点;选
让测头慢慢接触到工件左侧, 直到发现.300 ,然后进行以下操作:
选择翻到“相对坐标” 输入“X60.15”选择“预定” 此时相对坐标中的X值会变成“X60.15”。
(2) Y轴方向对刀操作与X轴同。 假设按上面同样的操作步骤后得出“Y55.63”。(3) Z轴方向对刀
选择
"坐标系"光标移动到G54的位置上,输入相对坐标当前
值进行测量,具体操作如下:
输入“X0”“测量”输入“Y10.5”“测量”输入“Z105.2”
“测量”
此时刀具偏置的补偿已经建立,等待操作者的调用后即生效。(5)调用坐标补偿
“MDI'
输入“M3 S1500; G90 G54 G01X0Y0Z100F1000“循
1转动刀具,快速移动到工件上表面附近;
2改用手轮操作模式,让刀具慢慢接触到工件上表面,直到发现有少许切屑为止,然后进行
以下操作:
选择翻到“相对坐标” 输入“Z'选择"起源”此
时相对坐标中的Z值会变成“Z0”。 此时此刻,相对坐标值不再作改动。 将刀具移到某一安全位置,假设移到相对坐标值显示为
“X0、Y10.5、Z105.2”的位置处。(4)设偏置补偿
环启动"
进给倍率慢慢打开
观察刀具轴移动的方向的趋势,判断是否会与机床、
工件发生干涉如果没发生干涉或碰撞,此时,若“绝对坐标”与“相对坐
标"数值相同,证明对刀已经接近成功。
“MDI”
输入“M3 S1500; G90 G54 G01X0Y0Z0F1000“循环
启动”观察到刀具如果正好落在工件上表面中心,表明对刀已经成功,谢谢!
择“X轴” "+”进给倍率打开机床X轴移动回机械原点;选择“Y轴” "+”
进给倍率打开
机床Y轴移动回机械原点;
(2)方法二“程序”“MDI”输入 “G91 G28 X0Y0ZQ ”
"循环启动” 进给倍率打开 机床X、Y、Z轴均移动回机械原点;
2.X、Y、Z向试切对刀(1) X轴方向对刀
1将工件、刀具分别装在机床工作台和刀具主轴上。
2转动主轴,快速移动工作台和主轴,让刀具靠近工件的左侧;
3改用手轮操作模式,让刀具慢慢接触到工件左侧,直到发现有少许切屑为止,然后进行以 下操作:
选择翻到“相对坐标” 输入“X”选择“起源”此 时相对坐标中的X值会变成“X0”。
4抬起刀具至工件上表面之上,快速移动,让刀具靠近工件右侧;⑤改用手轮操作模式,