我国目前铝合金表面处理的工艺及其环境效应
铝合金表面改性工艺与性能研究

铝合金表面改性工艺与性能研究近年来,随着工业技术的不断进步,铝合金作为一种轻质、高强度、耐腐蚀的材料,被广泛应用于航空航天、汽车制造等领域。
然而,尽管铝合金具有许多优点,但其表面的一些缺陷和局限性也限制了其应用。
因此,研究铝合金的表面改性工艺与性能已经成为一个热门的话题。
一、铝合金表面改性工艺的分类铝合金表面改性工艺可以分为化学改性工艺、物理改性工艺和机械改性工艺三类。
化学改性工艺主要是利用化学物质对铝合金表面进行处理,形成保护膜或改善表面性能。
常见的化学改性工艺包括阳极氧化、化学镀膜和化学抛光等。
阳极氧化是一种通过电解在铝合金表面形成氧化膜的方法,不仅可以增加表面硬度和耐腐蚀性能,还可以改善铝合金的装饰性。
化学镀膜则是通过浸泡铝合金在含有金属离子的溶液中,在表面形成一层金属镀层,以提高其耐磨损性能。
化学抛光主要是利用酸性或碱性溶液对铝合金进行溶解和腐蚀,使表面得到更好的光洁度和平整度。
物理改性工艺主要是通过物理手段改变铝合金表面的结构和形貌。
常见的物理改性工艺包括热处理、喷涂和喷砂等。
热处理是一种利用加热和冷却过程改变铝合金晶体结构和性能的方法,可以显著提高铝合金的强度和硬度。
喷涂主要是利用喷枪将涂料喷涂在铝合金表面,以增加其耐腐蚀性能和装饰性。
喷砂则是利用高速喷射砂粒将铝合金表面的氧化膜和氧化皮除去,以增加其粗糙度和增加附着力。
机械改性工艺主要是利用机械力对铝合金表面进行加工,从而改变其形貌和性能。
常见的机械改性工艺包括切削、冷压和电刷等。
切削是一种通过刀具对铝合金表面进行去材加工的方法,可以改善表面的光洁度和平整度。
冷压则是利用一定的压力对铝合金进行变形加工,以提高其机械性能和表面硬度。
电刷是利用电动机驱动金刷对铝合金表面进行刷磨,使表面得到更好的清洁度和平整度。
二、铝合金表面改性工艺的性能研究铝合金表面改性工艺对材料的性能有着重要的影响。
首先,表面改性可以显著提高铝合金的耐磨损性能。
通过改变表面的硬度和摩擦系数,可以减少表面的磨损和磨料的损伤,延长材料的使用寿命。
铝合金的表面处理技术研究

铝合金的表面处理技术研究一、引言铝合金是一种轻质高强度的金属材料,具有广泛的应用前景,是现代工业制造中不可或缺的材料之一。
但是,铝合金不仅容易受到氧化影响,而且其表面性质也不够优良,因此需要对其进行表面处理,以提高其性能和使用寿命。
二、表面处理技术分类常见的铝合金表面处理技术可分为机械处理、化学处理和电化学处理三类。
1. 机械处理机械处理是通过切削、研磨、抛光等方式来改善铝合金表面粗糙度、光洁度和平整度等性能。
其主要优点是处理效果稳定,但需要消耗大量的人力、时间和机械设备。
2. 化学处理化学处理是利用酸碱等化学作用来改善铝合金表面性质,包括蚀刻、酸洗、氧化等方法。
这种方法简单易行,可以在较短时间内达到较好的处理效果,但操作不当也有可能导致环境污染和安全隐患。
3. 电化学处理电化学处理是利用电化学反应来改善铝合金表面性能,其中包括阳极氧化、电镀等方法。
这种方法工艺复杂,需要严格控制工艺参数和电化学处理介质的成分,但可以同时获得较好的防腐和装饰效果。
三、铝合金表面处理技术案例分析1. 阳极氧化处理阳极氧化是一种比较常见的铝合金表面处理技术,其原理是将铝材件作为阳极,通过外加电势在氧化电解液中引起氧化反应,从而在其表面形成一层多孔的氧化层。
该氧化层具有较好的氧化防护和装饰效果。
该方法可应用于各种类型的铝合金材料,如6061铝合金、7075高强度铝合金等。
2. 硬质阳极氧化处理硬质阳极氧化是通过改变氧化液体系和工艺参数来获得更厚、更致密、更具耐磨性的氧化层。
该方法适用于铝合金零部件的耐磨、耐蚀、装饰等方面的应用,如航空、汽车、机械等领域。
3. 电镀处理电镀处理是将一种金属沉积在另一种金属表面的方法,通过电流作用使金属离子在电解液中还原成金属沉积在工件表面。
铝合金材料可以采用铬酸钾、硫酸铝铜等电解液进行电镀处理,其处理效果包括提高外观质量、增强耐蚀性和耐磨性等。
四、结论铝合金表面处理技术是提高铝合金材料性能和扩展其应用领域的关键技术之一。
铝合金表面处理的方法及应用
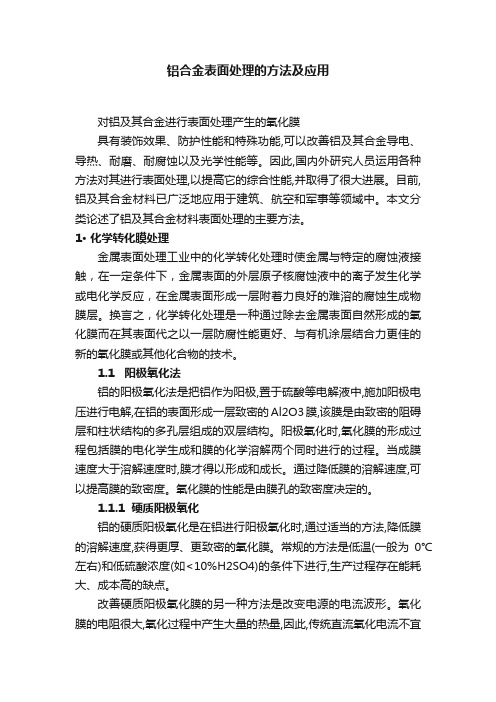
铝合金表面处理的方法及应用对铝及其合金进行表面处理产生的氧化膜具有装饰效果、防护性能和特殊功能,可以改善铝及其合金导电、导热、耐磨、耐腐蚀以及光学性能等。
因此,国内外研究人员运用各种方法对其进行表面处理,以提高它的综合性能,并取得了很大进展。
目前,铝及其合金材料已广泛地应用于建筑、航空和军事等领域中。
本文分类论述了铝及其合金材料表面处理的主要方法。
1· 化学转化膜处理金属表面处理工业中的化学转化处理时使金属与特定的腐蚀液接触,在一定条件下,金属表面的外层原子核腐蚀液中的离子发生化学或电化学反应,在金属表面形成一层附着力良好的难溶的腐蚀生成物膜层。
换言之,化学转化处理是一种通过除去金属表面自然形成的氧化膜而在其表面代之以一层防腐性能更好、与有机涂层结合力更佳的新的氧化膜或其他化合物的技术。
1.1 阳极氧化法铝的阳极氧化法是把铝作为阳极,置于硫酸等电解液中,施加阳极电压进行电解,在铝的表面形成一层致密的Al2O3膜,该膜是由致密的阻碍层和柱状结构的多孔层组成的双层结构。
阳极氧化时,氧化膜的形成过程包括膜的电化学生成和膜的化学溶解两个同时进行的过程。
当成膜速度大于溶解速度时,膜才得以形成和成长。
通过降低膜的溶解速度,可以提高膜的致密度。
氧化膜的性能是由膜孔的致密度决定的。
1.1.1 硬质阳极氧化铝的硬质阳极氧化是在铝进行阳极氧化时,通过适当的方法,降低膜的溶解速度,获得更厚、更致密的氧化膜。
常规的方法是低温(一般为0℃左右)和低硫酸浓度(如<10%H2SO4)的条件下进行,生产过程存在能耗大、成本高的缺点。
改善硬质阳极氧化膜的另一种方法是改变电源的电流波形。
氧化膜的电阻很大,氧化过程中产生大量的热量,因此,传统直流氧化电流不宜过大,运用脉冲电流或脉冲电流与直流电流相叠加,可以极大地降低阳极氧化所需要的电压,并且可使用更高的电流密度,同时还可以通过调节占空比和峰值电压,来提高膜的生长速度,改善膜的生成质量,获得性能优良的氧化膜。
我国铝型材表面处理工艺的发展回顾及未来思考

近 20 年来, 我国铝合 金建筑型 材的发展 非常迅 速。上世纪 80 年代中期, 我国分别从东亚和西欧引进 了 2 条手动卧式生产线, 其年产量只有 3 000 , t 90 年代 末期从日本引进了全自动阳极氧化电泳涂装大型立式 生产线 , 年产量超过了 30 000 t 。 80 年代中期, 我国以 锡盐电解着色稳定剂、 氟化镍冷封孔添加剂、 长寿命碱 洗添加剂及其相配套的工艺制度, 形成了综合东西方 技术特点的表面处理生产体系, 到本世纪建成了多家 特大型企业 , 从事阳极氧化电泳涂漆生产。现在, 我国 的建筑铝型材表面处理年产量已经超过 500 10 , t超
2 阳极氧化工艺主要配置、 存在问题及改进
2 . 1 工艺配置及问题 目前, 我国铝型材阳极氧化的主要工艺路线见图 1 。在实施化学和电化学处理 , 即 型材上排 !之前 ,
[ 7]
8
温度必须进行严格的控制。 2 . 2 改进措施 2 . 2 . 1 从环境保护角度考虑 ( 1) 弃用氟化氢铵酸浸蚀 该工艺可以降低铝耗 , 得到平整的表面 , 如铝耗 2 %以下就可以去除铝型材表 面的挤压条纹, 大大低于铝耗 5 % 以上的碱洗水平 , 但 是采用高浓度氟离子槽液 , 严重污染了环境 , 另外铝表 面存在不溶性的氟化铝膜 , 改变了金属质感 , 使其表面 晦暗无光。因此 , 应尽量弃用。 ( 2) 回收氢氧化铝 日本常用的碱回收装置将碱 洗槽液引至结 晶槽, 沉 淀出氢氧 化铝, 并直接 回收利 用 , 但设备的一次性投资 增加。欧洲的长寿命添加剂 虽然延长了沉淀析出时间 , 避免槽内结块 , 但仍需要清 理污泥。目前, 我国使用长寿命添加剂较多 , 不可避免 地带来了环境污染问题, 干扰了沉淀污泥中氢氧化铝 的直接有效回收、 利用。因此 , 应采取碱回收装置回收 氢氧化铝。 ( 3) 电解着色液的选用与回收 阳极氧化是建筑 铝型材的表面处理的首选工艺, 具有很好的耐候性 , 国 内外电解着色主要是镍盐或锡盐槽液。镍盐比锡盐污 染严重 , 锡盐价格较低、 污染 较轻, 槽液对杂质不太敏 感 , 应多采用硫酸亚锡槽液电解着色。镍盐电解着色 , 选用镍盐回收技术也可以达到比较理想的环境效果。 如一条没有硫酸镍回收装置的镍盐着色生产线, 硫酸 镍消耗达 6 kg / , t 其中有 2 / 3溶解在清洗水中并随之排 出 ; 如果配置有效的回收装置 , 硫酸镍的消耗可以降低 到 2 kg / t以下。因此, 镍盐电解着色生产线配置有效 的回收装置 , 既可以降低生产成本, 又能够降低镍离子 污染。 ( 4) 改进冷封孔工艺 以氟离子与镍离子为冷封 孔槽液主成分 , 不利于环 境保护。中温封孔虽然没有 氟离子 , 但是以乙酸镍为主成分 , 仍然存在污染情况。 目前, 国内外希望既能提高膜的封孔质量和膜的塑性 , 又能彻底解决环境污染问题, 正在开发的无镍或无重 金属的封孔剂还没有被实践所佐证。目前, 改变冷封 孔工艺最现实的措施还是热封孔 ( 沸水封孔或高温水 蒸气封孔 )或电泳涂漆封孔 ( 有机物封孔 ) 。 2 . 2 . 2 从节能节资减耗角度考虑 ( 1) 淘汰氟化氢铵酸浸蚀 先机械喷砂或机械扫 纹消除铝型材挤压条纹后, 再进行碱洗。这样, 既可以 迅速去除挤压的条纹 , 又 可以减少铝耗。欧洲多采用 机械预处理工艺 , 并已具有较完备的机械装备, 只要投 资机械喷砂或机械扫纹设备。 ( 2)优化工艺设备及参数 能耗占阳极氧化生产 成本的比重很大, 主要是在阳极氧化和槽液冷却方面。 阳极氧化电源的选择、 系统电接触好坏、 槽液冷却时降 温过度等都会显著增加电能消耗。为了降低阳极氧化 的操作成本, 必须选择好电源设备、 冷冻设备及参数控 制技术等。 ( 3)正确使用电解着色液 这决定于膜的颜色要 求和工艺成本。镍盐和锡盐各有优缺点 及使用范围。 锡盐曾以对槽液杂质宽容度大、 易管理而占优势 , 目前 全自动立式阳极氧化生产线基本使用特殊电源的镍盐 电解着色技术。一般而论, 镍盐适合于浅色调着色, 锡 盐适合于深色调着色。硫酸镍的价格可能高于硫酸亚 锡, 但实际生产成本并不太高, 生产消耗应根据实际情 况而定。也就是 说, 在 权衡经 济、 技术和 产品性 能之 后, 再决定槽液类型的选择。 ( 4)适当进行封孔处理 冷封孔工艺能耗较低 , 对 水质要求较低, 这是我国长期选用的原因 之一。冷封 孔膜容易开裂 , 必须辅以热水处理, 或者改变冷封孔工 艺。基于冷封孔阳极氧化膜性能方面的缺 陷, 目前较 多转向中温封孔工艺, 或许还会启用热封 孔工艺。中 温封孔能耗高于冷封孔。因此 , 选择封孔技术应综合 考虑环境、 能耗、 质量和经济等因素。 2 . 2 . 3 从阳极氧化膜性能角度考虑 随着铝型材阳极氧化膜应用范围的扩大 , 其性能 方面出现了一些新的突出问题 , 如因机械应力或热应 力导致膜开裂。为此, 提出以下改进建议。 ( 1)机械喷砂除去铝型材挤压条纹, 节能、 降耗 , 有 利于环境 , 但其阳极氧化膜质量即使能通过检测 , 也难 以通过 CASS 试验。这可能是喷砂凹坑中的阳极氧化 膜不完整所致, 目前还没有发现影响其使用性能的证 据, 也未找到解决喷砂阳极氧化膜 CASS 试验性能较差 的办法, 需作进一步研究。 ( 2)恒电流阳极氧化膜厚达 20 m 或更高, 但封孔 质量和外观平整度都不理想 , 这与厚膜的散热效果较 差有关系。从阳极氧化膜结构看, 厚膜存在微孔 喇叭 口 !而影响正常封孔 , 用脉冲阳极氧化替代恒电流阳极 氧化是提高厚膜质量的有效途径。 ( 3)锡盐或镍盐电解着色的封孔质量都较理想 , 而 硒盐 ( 钛金色 ) 、 铜盐 ( 紫铜色 ) 、 锰盐 ( 金黄色 ) 电解着 色, 可能影响阳极氧化膜的封孔质量 , 或者在热水封孔 或电泳涂漆时发生褪色现象。这与微孔底部没有发生 电解沉积 , 部分电解沉积物又发生溶出有关。通常, 需 要 预封孔 !, 如在乙酸镍溶液中浸渍 10 m in, 使电解着
铝合金的表面处理工艺

铝合金表面处理工艺
铝合金表面处理分类:
1.氧化
2.二次氧化
3.表面拉丝
4.喷砂
5.高光
6.喷涂、印刷
1.氧化
1‐1目的与意义
铝合金表面很容易生成一层极薄的氧化铝膜(0.01um~0.02um),有一定的抗腐蚀能力。
但由于这层氧化膜是非晶的,使铝件表面失去原有的光泽。
此外,这种氧化膜疏松多孔,不均匀,抗腐蚀能力不强,容易沾染污迹。
因此,铝合金制品通常进行特殊的氧化处理,在氧化处理之前,用化学和物理的方法对制品表面进行必要的清洗,使其裸露纯净的金属基体,以利氧化着色顺利进行,从而获得与基体结合牢固 、色泽与厚度都满足要求。
铝合金的表面处理的方法及原因

铝合金的表面处理的方法及原因
铝合金型材表面处理的目的是要解决或提高材料防腐性、装饰性和功能性三方面的性能。
铝合金型材表面处理电泳、喷漆、喷塑、普通阳极氧化、硬质阳极氧化、光亮阳极氧化、瓷质阳极氧化、氟碳喷涂、具体要看技术要求!!现在一般的铝合金表面处理使用的普通阳极氧化,低档的使用电泳处理!!
其中硬质阳极氧化及瓷质阳极氧化防腐性能、装饰性和功能性是铝型材中最好的,相对来说成本也较高!!!
一、表面机械处理:
是进行工件表面处理的预处理,可提高和改善零件外观,为后续的表面处理提供优良的表面质量打下良好的基础.主要方法有:喷砂、磨光、机械抛光、滚光及刷光.
二、表面化学处理:
是通过化学方法对工件表面进行处理的工艺方法,可提高和改善零件外观,提高金属零件表面的耐蚀性、耐磨性,减少摩擦,增加磨合性,改善机械配合,也可以提供特殊的物理性能或者为后续的表面处理提供优良的表面质量.表面化学处理通常包括化学抛光、氧化和磷化等处理方法.
三、表面电化学处理:
是指通过利用直流电或交流电设备,通过电化学过程对金属零件表面进行处理,提高金属零件表面的平整度、降低粗糙度,或者使金属零件表面形成一层氧化层或金属沉积层的过程.表面电化学处理包括电解抛光、电化学氧化和电镀等方面,铝合金主要是阳极氧化处理,其最大的特点是包含有电化学过程.
四、表面涂覆:
在零件表面涂覆一层其他物质,以达到提高表面性能、改变表面特性、提高装饰性能.铝合金主要是表面的氧化膜染色处理,如各种易拉罐表面的染色处理.。
铝合金表面处理工艺
铝合金表面处理工艺
铝合金表面处理工艺如下
1、高光切削
使用精雕机对铝合金表面的某些零件进行切削,让这些切削面呈现出高亮的区域。
这种处理工艺一般是运用在手机、高端电视上比较多,特别是那些高端电视更是使用了这种工艺,让电视机外表变得更加具有时尚感,同时还呈现出科技的锐利感。
2、喷沙
这种工艺是利用了高速砂流的冲击作用,对铝合金表面进行清理和粗化,从而让铝合金表面可以获得一定的清洁度和不同程度的粗糙度。
经过喷沙工艺的铝合金,它的机械性能可以得到改善,从而提高了铝合金产品的炕抗疲劳性,同时还增加了铝合金产品和表面涂层的附着力以及耐久性。
3、拉丝
这种工艺是指使用砂纸对铝合金表面反复进行磨刮,直到刮出线条。
拉丝的种类有很多,例如:直条、乱纹、螺纹、旋纹等等。
经过拉丝工艺的铝合金,它的表面可以非常清晰的看到每一根线条,同时铝合金产品的金属亚光中会呈现出细密的发丝光泽,从而让铝合金产品变得更加具有时尚感和科技感。
4、抛光
这种工艺是指使用机械方法或者是化学方法或者是电化学方法对铝合金产品表面进行抛光,从而降低铝合金产品的表面粗糙度,
让铝合金产品表面变得更加的平整、光亮。
经过抛光工艺的铝合金产品,它的表面效果接近于不锈钢的镜面效果,可以给人一种非常高档、时尚的视觉效果。
铝合金表面常见的表面处理工艺
铝合金表面常见的表面处理工艺
铝合金是一种广泛应用的材料,它的表面处理工艺对于提高其性能和
美观度至关重要。
常见的铝合金表面处理工艺包括阳极氧化、电镀、
喷涂和机械加工等,下面将详细介绍这些处理工艺的主要内容。
一、阳极氧化
阳极氧化是一种通过电化学反应形成氧化层的表面处理技术。
该技术
可使铝合金表面形成致密、均匀、具有较高硬度和耐腐蚀性的氧化层,从而提高其抗磨损性能和耐久性。
此外,阳极氧化还可以改变铝合金
表面颜色,并增加其装饰效果。
二、电镀
电镀是利用电解作用在铝合金表面沉积一层金属或非金属覆盖物的技术。
常见的电镀方法包括镍、铬、锌等金属电镀以及陶瓷涂层等。
通
过电镀可以改善铝合金表面的耐腐蚀性能,增加其硬度和光泽度,并
且可以实现多种颜色和纹理效果。
三、喷涂
喷涂是将一层涂料或者粉末喷涂在铝合金表面的一种表面处理技术。
该技术可以实现多种颜色和纹理效果,同时还可以提高铝合金表面的耐腐蚀性能和装饰效果。
常见的喷涂方法包括喷漆、粉末涂料等。
四、机械加工
机械加工是通过机械力量对铝合金表面进行切削、磨削或拉伸等处理的技术。
该技术可以改变铝合金表面形态和纹理,从而实现不同的装饰效果。
此外,机械加工还可以提高铝合金表面的平整度和光泽度。
综上所述,铝合金表面处理工艺包括阳极氧化、电镀、喷涂和机械加工等多种方法。
这些处理方法各有优缺点,在实际应用中需要根据具体情况进行选择,以达到最佳的效果。
铝及铝合金阳极氧化工艺的现状及发展趋势
铝及铝合金阳极氧化工艺的现状及发展趋势1 前言铝及其合金材料由于其高的强度/重量比,易成型加工以及优异的物理、化学性能,成为目前工业中使用量仅次于钢铁的第二大类金属材料。
然而,铝合金材料硬度低、耐磨性差,常发生磨蚀破损,因此,铝合金在使用前往往需经过相应的表面处理以满足其对环境的适应性和安全性,减少磨蚀,延长其使用寿命。
在工业上越来越广泛地采用阳极氧化的方法在铝表面形成厚而致密的氧化膜层,以显著改变铝合金的耐蚀性,提高硬度、耐磨性和装饰性能。
阳极氧化是国现代最基本和最通用的铝合金表面处理的方法。
阳极氧化可分为普通阳极氧化和硬质阳极氧化。
铝及铝合金电解着色所获得的色膜具有良好的耐磨、耐晒、耐热和耐蚀性,广泛应用于现代建筑铝型材的装饰防蚀。
然而,铝阳极氧化膜具有很高孔隙率和吸附能力,容易受污染和腐蚀介质侵蚀,心须进行封孔处理,以提高耐蚀性、抗污染能力和固定色素体。
2 铝及铝合金的阳极氧化2.1 普通阳极氧化铝及其合金经普通阳极氧化可在其表面形成一层Al2O3膜,使用不同的阳极氧化液,得到的Al2O3膜结构不同。
阳极氧化时,铝表面的氧化膜的成长包含两个过程:膜的电化学生成和化学溶解过程。
只有膜的成长速度大于溶解速度时,氧化膜才能成长、加厚。
普通阳极氧化主要有硫酸阳极氧化、铬酸阳极氧化、草酸阳极氧化和磷酸阳极氧化等,以下介绍一些普通阳极氧化新工艺。
2.1.1 宽温快速阳极氧化[1]硫酸阳极氧化电解液的温度要求在23℃以下,当溶液的温度高于25℃时,氧化膜变得疏松、厚度薄、硬度低、耐磨性差,因此在原硫酸溶液中加入氧化添加剂对原工艺进行改进,改进后的溶液配方为:硫酸(ρ=1.84g/cm3)150-200g/L(最佳值160g/L)CK-LY添加剂20-35g/L (最佳值30g/L)铝离子 0.5-20g/L (最佳值5g/L)CK-LY氧化添加剂包括特定的有机酸和导电盐,前者能提高电解液的工作温度,抑制阳极氧化膜的化学溶解,在较高的温度下对抑制氧化膜疏松有良好的作用;后者能增强电解液的导电性,提高电流密度,加快成膜速度。
铝合金材料表面处理及其实现技术的研究
铝合金材料表面处理及其实现技术的研究铝合金是一种广泛应用的材料,因其具有轻质、强度高等特点而深受各行业的青睐。
但铝合金表面容易受到化学、电化学等因素的影响,导致其表面性能下降,甚至发生腐蚀。
因此,铝合金表面处理技术的研究和发展也日益重要。
一、铝合金表面处理方法1. 电化学氧化法电化学氧化法是一种常见的表面处理方法,通过电解氧化溶液,使铝表面形成一层细密的氧化膜,提高其耐腐蚀性和硬度。
常用的电解液有硫酸、草酸、磷酸等。
2. 化学氧化法化学氧化法是利用化学反应的原理,在铝表面形成氧化膜。
常用的氧化剂有硫酸铬、亚硝酸铁、亚硝酸钠等。
其优点是处理时间短,成本低,缺点是膜质量不如电化学氧化膜。
3. 电镀法电镀法也是一种常用的表面处理方法,可在铝表面镀上一层金属膜,提高其硬度和耐腐蚀性。
常用材料有镍、铬、锌等。
4. 喷涂法喷涂法也是一种常见的表面处理方法,通过喷涂涂料,使铝表面形成一层耐腐蚀的涂层。
常用的涂层有环氧树脂、聚氨酯、丙烯酸等。
二、铝合金表面处理实现技术1. 电化学氧化方法电化学氧化方法实现的关键是控制电解液的组成、电解条件和工艺流程。
在电解液组成上,应根据不同的铝合金种类和性质,选择适合的氧化液。
在电解条件上,需控制电解液浓度、温度、电压电流等参数。
在工艺流程上,则需控制预处理、清洗、脱脂、表面修整等。
2. 化学氧化法化学氧化法实现的关键是选择合适的氧化剂和反应条件。
在氧化剂的选择上,应根据铝合金表面的材质和性质选择不同类型的氧化剂。
在反应条件上,需控制氧化剂浓度、反应时间、温度等参数。
3. 电镀法电镀法实现的关键是选择适合的电镀液和电解条件。
在电镀液的选择上,应根据铝合金表面的情况和所需的涂层类型,选择适合的电镀液。
在电解条件上,需控制电压电流、电解时间、电极间距等参数。
4. 喷涂法喷涂法实现的关键是选择适合的涂料和粘合剂,并控制喷涂厚度和均匀性。
在涂料和粘合剂的选择上,应根据铝合金表面的材质和性质选择不同类型的涂料和粘合剂。
- 1、下载文档前请自行甄别文档内容的完整性,平台不提供额外的编辑、内容补充、找答案等附加服务。
- 2、"仅部分预览"的文档,不可在线预览部分如存在完整性等问题,可反馈申请退款(可完整预览的文档不适用该条件!)。
- 3、如文档侵犯您的权益,请联系客服反馈,我们会尽快为您处理(人工客服工作时间:9:00-18:30)。
我国目前铝合金表面处理的工艺及其环境效应我国铝合金型材的表面处理工艺包括阳极氧化,阳极氧化后电泳涂漆,化学转化后喷粉,化学转化后喷漆等四种工艺。
它们虽然源自西欧和日本的工艺,但在我国得到了融合、提升和发展。
但是在过去引进国外技术及国产化过程中,重点放在结合我国的当时技术水平、资源特点、并从方便管理和降低成本等因素考虑较多,环境效应关注不够。
因此有关废水、废气的处理思路、方案和措施,甚至在某些工艺路线方面,从新的环境效益的视角去审视,都存在不少问题,其中包括若干亟待解决的问题,本文在此基础上提出一些技术设想和新建议。
一、铝材表面处理生产线废水废气的排放标准各行业的不同工艺需要控制的污染物质并不相同,为此废水的排放的浓度标准也不可能相同。
对于铝合金加工行业,废水的排放标准可执行国家标准GB 8978-1988 “污水综合排放标准”。
排放标准按地面水域使用功能要求和污水排放去向,对于向地面水水域排放和城市下水道排放的污水分别执行一、二、三级的标准。
对排入重点保护水域、生活饮用水水源地、一般经济渔业水域、重要风景游览区等水域的污水需要执行一级标准。
对排入一般保护水域,一般工业用水区、景观用水区及农业用水区等水域的污水执行二级标准。
对排入城镇下水道并进入二级污水处理厂,进行生物处理的污水执行三级标准。
在某些情形下,不仅排放的要求更高,而且对于中水的回收使用比例要求更高,例如最近华加日对于新厂的废水排放,不仅排放的“废水”需要达标,而且回收利用率要达到90%,没有新的环境保护思路和高标准的环境治理措施是不可能达到的。
国家标准GB 8978-1988还把排放的69种污染物按性质分为两类,读者需要时可以直接查阅标准。
第一类污染物是指能在环境或动植物体内蓄积,对人体健康产生长远不良影响者。
含有此类有害污染物质的污水,不分行业和污水排放方式,也不分受纳水体的功能类别,一律在车间或车间处理设施排出口取样,其最高允许排放浓度必须符合表1的规定。
第二类污染物是指其长远影响小于第一类的污染物质,在排污单位排出口取样,其最高允许排放浓度和部分行业最高允许排水定额必须符合表2的规定。
经过环保处理的废水必须达到上述指标才能排放,在一、二类污染物中,排放废水的pH值是最直观的检测指标,也是废水处理操作人员的重点控制因素。
废水的pH值在反应池中就应该调节到符合排放标准,在调节pH值的操作中,需要反复测量废水的pH值,掌握其变化规律,并逐渐减少中和剂的添加量,最终达到pH 6~9的排放标准。
在废水处理工艺完善、废水处理装置运行正常、操作人员严格按要求操作的情况下,是可以保证废水的pH值达到排放标准的。
阳极氧化电解着色(镍盐)可能应该按照电镀污染物的标准排放,那么实际要求明显地比GB 8978-1988的要求严格许多,国家标准GB21900-2008”电镀污染物排放标准”[2] 的废水排放限制见表3所示。
表3 水污染物特别排放限值[2]铝材阳极氧化生产线的废气主要是酸雾、碱雾,通常采用湿法净化的吸收方法进行处理,只要设计正确,处理方法基本上没有技术难度问题。
如果阳极氧化生产线包括三酸化学抛光工序,硝酸挥发引起的氧化氮的废气污染极为严重,不论是黄烟还是白烟的气体污染的问题都非常严重,也就是一氧化氮和二氧化氮同样是极其有害的污染。
事实上白烟对于钢铁设备的腐蚀性可能更强,虽然看起来不像黄烟那么可怕而已,一般的湿法净化的方法难于进行氧化氮气体的彻底治理。
铝合金静电喷漆生产线的废气还有挥发性有机化合物(VOC),而静电喷粉存在悬浮粉尘,都是极其有害的污染源,构成严重的大气污染和环境腐蚀,必须彻底进行治理。
二、阳极氧化的工艺路线及存在的环境问题我国目前阳极氧化的工艺路线按照国家标准如图1所示,如果没有电泳涂漆可直接进行封孔处理,目前我国的封孔工艺以冷封孔或中温封孔为主。
如果进行电泳涂漆,则舍弃封孔处理而代之热水洗再进行电泳涂漆即可。
在图1的阳极氧化的工艺路线中,其中脱脂、阳极氧化、去灰和中和(图中以绿色表示)一般没有毒性较高的污染源,只有污染程度不高的酸性或碱性溶液问题。
而碱洗、电解着色、染色和封孔(图中以红色表示)存在多种对环境有害的有机或无机化合物,可能存在比较严重污染问题,必须认真治理。
某些阳极氧化生产线可能安排含氟化氢铵的“酸浸蚀”处理,更存在严重的氟离子的污染问题,在图1的典型生产流程中没有表示。
图1 铝型材阳极氧化典型工艺流程图[1]根据图1表示的流程,结合我国目前的主要工业实践,并重点从环境污染的角度进行以下简单的补充说明和评述。
(1) 脱脂—我国主要采用硫酸脱脂,一般并不添加表面活性物质,为此槽液和水洗液均为普通的酸性物质,如硫酸根等,并不存在严重的环境污染的有毒物质。
如果添加表面活性物质,还需要考虑有机化合物的处理;(2) 碱洗—目前我国主要采用源自欧洲的长寿命碱洗添加剂工艺,添加剂中含有大量无机和有机化合物,极少采取碱回收装置。
此工艺尽管避免了槽内结块,仍然存在大量槽内的“沉淀污泥”,需要另行堆放处理,还要排放清洗中长寿命添加剂中某些污染成分。
由于碱洗槽液的“沉淀污泥”并不是单纯氢氧化铝,含有长寿命添加剂而影响其有效回收利用;(3) 氟化氢铵酸浸蚀—部分生产线一度采取氟化氢铵的酸浸蚀除去挤压条纹,尽管可以在降低铝耗的条件下达到除去挤压条纹的目的,却带来非常严重的氟化物废水的环境污染问题。
由于近年来环境保护措施的强化,同时由于氟化氢铵处理后影响铝型材表面的金属质感,目前氟化氢铵的酸浸蚀工艺已经有所限制,使用范围明显缩小;(4) 去灰—鉴于节约资源的考虑,我国目前较多使用阳极氧化槽的“废硫酸溶液”去灰,因此槽液和水洗液均为普通的酸性物质,如硫酸根等;(5) 阳极氧化-—我国建筑铝型材基本采取恒电流硫酸溶液的阳极氧化工艺,较少选取脉冲阳极氧化和其他溶液,槽液和水洗液均为酸性物质,主要是硫酸,一般也不存在严重的环境污染物质;(6) 电解着色—目前除自动化立式生产线采用单镍盐以外,卧式生产线基本上以采用单锡盐或锡镍混合盐的电解着色为主。
单镍盐存在镍离子的污染,应通过环境保护措施设法消除或降低镍离子的排放,总镍排放量低于0.1 mg/L并不是容易的事。
如果采用锡盐电解着色,为了维持二价锡的稳定性,单锡盐或锡镍混合盐槽液中都存在大量有机还原剂和络合剂等抗氧化的化合物,如酚类或苯酚类化合物,都存在较严重的废水污染;(7) 染色—通常为有颜色的有机化合物,存在污染问题;(8) 封孔—我国长期以来主要选择以以氟化镍为主成分的冷封孔工艺,尽管浓度不高,溶液和清洗水均存在镍离子和氟离子的污染。
目前虽已开发以乙酸镍为主要成分的中温封孔,仍然以镍盐为主要成分而带来镍离子的环境污染。
虽然镍离子含量远低于镍盐电解着色槽液,仍然需要考虑环境保护的处理。
三、阳极氧化生产线的现有废水处理流程应该改进从上面的阳极氧化工艺路线图可知,脱脂,阳极氧化,去灰及其清洗水均系酸性溶液,而碱洗及其清洗水属碱性溶液,经过集中的中和处理(一般还需要添加酸或碱),通过凝集和沉淀,分离为沉淀污泥和清澈液体。
尽管通过这一套长期使用的集中式中和的处理流程,基本上可以达到排放要求,但是既耗费大量用水和化学药品,又会排放大量固相和液态物质。
只要改变这种集中排放再进行处理的方式,替代为各工序独立的闭路循环的环境处理系统,就可以显著降低排出废水量、提高水利用率、提升化学试剂回收利用水平。
举例说,如果碱洗采用碱回收体系(需要投资建立设备),经过BAYER方式加水进行分解后,将得到的氢氧化钠溶液和氢氧化铝(氧化铝余渣)分别回收使用,减少污泥沉淀结块量,直接回收烧碱和氧化铝,降低工艺成本。
更值得一提的是,全面更新废水处理的思路,提高了废水处理的技术水平。
如果加上酸回收体系,对阳极氧化工厂里的阳极氧化槽中的AL浓度进行管理, 要按生产量比例、对液体进行排放、利用酸回收装置对回收的硫酸和废弃硫酸进行分离、把回收硫酸放到氧化槽里重新利用。
有关阳极氧化各工序闭路循环处理废水的思路,将在本文第2部分结合工艺过程集中介绍。
四、静电喷涂的工艺路线及存在的环境问题静电喷粉和静电喷漆的工艺路线比较简单,请见图2的工艺流程示意图。
通过化学预处理(图中的脱脂和酸洗)以后,喷涂之前的铬酸盐转化处理(红色方框)为其特有的工序,铬酸盐化学转化之前可以采用比较便捷的含氟离子的所谓“三合一”处理(即替代了脱脂,碱洗和酸洗去灰)。
从目前的生产情况分析,由于铬酸盐化学转化处理带来十分严重的环境污染困扰,已经成为目前静电喷涂的头等严重的污染问题。
如果无铬化学转化工艺成功,不论是钛/锆体系还是(尤其是)有机硅烷体系,对于铝材表面洁净度的要求明显提高,无铬转化的化学预处理可能与铬酸盐处理的化学与处理有所不同,以保证无铬化学转化处理的品质稳定。
静电喷涂除了化学转化处理的六价铬的环境污染外,喷漆工艺的VOC(挥发性有机化合物)大气污染安问题、有机溶剂的着火问题,粉末涂料的爆燃问题等都有不容忽视的严重环境损害。
图2 有机聚合物静电喷涂典型工艺流程图[2]在静电喷涂的生产工艺中,化学转化处理是必不可缺的工艺,目前主要采用铬酸盐或磷铬酸盐化学转化处理,因此废水中会有较高浓度的Cr6+离子。
含六价铬的废水一般是利用氧化还原方法进行处理(见图3),即用硫酸亚铁、亚硫酸钠等还原剂将废水中Cr6+还原成Cr3+(反应池1),再将废水pH调到7~8,使Cr3+形成Cr(OH)3沉淀(反应池2)。
再通过絮凝、沉降、压滤脱水形成氢氧化铬(三价铬)污泥。
这种方法属于间歇式处理,设备投资和运行费用并不高,但是处理工艺必须严格执行,以彻底消除六价铬的危害。
含铬废水处理方法与其他废水处理方式明显不同,所以含铬的废水不应该与其它废水混合,宜单独进行收集、存放和处理,典型的含铬废水处理流程如图3所示。
对于静电喷漆生产线,有机化合物废气治理的常用的方法有:吸附法、吸收法、直接燃烧法和催化燃烧法等。
对于静电喷涂涂装那样的大流量、低浓度的有机废气,直接燃烧或催化燃烧处理费用太高,并不经济。
活性炭吸附具有处理低浓度和大气量废气的优势,先用活性炭捕获废气中的有机化合物,然后用很小流量的热空气来脱附,这样可以使挥发性有机化合物,即所谓VOC富集,浓度提高10~15倍,大大减少了待处理废气的体积,使后处理设备的规模也大幅度降低。
把浓缩后的废气送到催化燃烧装置中,利用催化燃烧处理较高浓度废气的特点来消除VOC。
催化燃烧放出的热量可以通过间壁换热器来预热进入炭吸附床的脱附气,降低系统的热能使用量。
该技术利用炭吸附处理低浓度和大气量的特点,又利用催化床处理适中流量、高浓度的优势,形成一套非常有效的集成技术。
图3 典型的含铬废水的处理工艺流程图[3]。