事故案例及原因分析安全操作和防火防爆安全技术化工行业已成为共40页文档
化工火灾爆炸事故案例分析总结
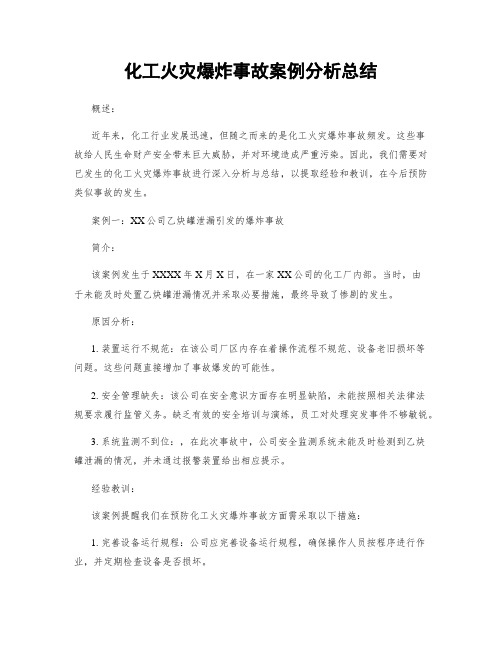
化工火灾爆炸事故案例分析总结概述:近年来,化工行业发展迅速,但随之而来的是化工火灾爆炸事故频发。
这些事故给人民生命财产安全带来巨大威胁,并对环境造成严重污染。
因此,我们需要对已发生的化工火灾爆炸事故进行深入分析与总结,以提取经验和教训,在今后预防类似事故的发生。
案例一:XX公司乙炔罐泄漏引发的爆炸事故简介:该案例发生于XXXX年X月X日,在一家XX公司的化工厂内部。
当时,由于未能及时处置乙炔罐泄漏情况并采取必要措施,最终导致了惨剧的发生。
原因分析:1. 装置运行不规范:在该公司厂区内存在着操作流程不规范、设备老旧损坏等问题。
这些问题直接增加了事故爆发的可能性。
2. 安全管理缺失:该公司在安全意识方面存在明显缺陷,未能按照相关法律法规要求履行监管义务。
缺乏有效的安全培训与演练,员工对处理突发事件不够敏锐。
3. 系统监测不到位:,在此次事故中,公司安全监测系统未能及时检测到乙炔罐泄漏的情况,并未通过报警装置给出相应提示。
经验教训:该案例提醒我们在预防化工火灾爆炸事故方面需采取以下措施:1. 完善设备运行规程:公司应完善设备运行规程,确保操作人员按程序进行作业,并定期检查设备是否损坏。
2. 加强安全意识培养:加强宣传教育,提高员工对于化工火灾爆炸事故风险的认识和防范意识。
同时组织定期培训和演练,以增强员工应对紧急情况的能力。
3. 安装先进监测系统:引进和使用先进的化学品泄漏监测系统,及时准确地获取关键指标数据,并做好预警准备。
案例二:XX市XX工厂氰化物泄露引发大规模火灾简介:该案例发生于XXXX年X月X日,位于XX市的一家化工工厂中,该工厂主要生产化学品。
当时,由于氰化物泄露溢出并遇到火源,火灾迅速蔓延且扩大,导致了严重的环境污染和人员伤亡。
原因分析:1. 安全设施缺失:该公司安全设备不齐全、维护保养不到位。
在事故发生前没有作出及时反应和应对。
2. 废水处理系统失效:该工厂废水处理设备存在严重故障,并未及时检修维护。
安全生产事故案例分析

安全生产事故案例分析安全生产是企业发展的重要保障,也是社会稳定的基石。
然而,在实际生产过程中,由于各种原因,安全生产事故时有发生,给企业和个人带来了巨大的损失。
本文将通过对几个典型的安全生产事故案例进行分析,探讨事故发生的原因、教训以及预防措施,以期为广大企业和从业人员提供有益的借鉴。
案例一:某化工厂爆炸事故事故经过在某年某月某日,某化工厂的一个生产车间发生了剧烈的爆炸。
事故发生时,现场有多名工人正在进行生产作业。
爆炸瞬间,火光冲天,浓烟滚滚,整个车间被夷为平地。
事故造成了多人伤亡和巨大的财产损失。
事故原因分析1、违规操作经过调查发现,事故发生前,操作人员在未严格按照操作规程的情况下,擅自对生产设备进行了调整,导致了化学反应失控。
2、设备老化该化工厂的部分生产设备长期运行,未得到及时的维护和更新,存在严重的安全隐患。
化工厂的安全管理制度不完善,对员工的安全教育培训不到位,日常安全检查流于形式,未能及时发现和消除安全隐患。
事故教训1、严格遵守操作规程操作人员必须经过专业培训,熟悉操作规程,不得擅自违规操作。
2、加强设备维护和更新企业要定期对生产设备进行检查、维护和更新,确保设备的安全运行。
3、完善安全管理制度建立健全的安全管理制度,加强对员工的安全教育培训,提高员工的安全意识和操作技能。
预防措施1、强化安全培训定期组织员工参加安全培训,包括操作规程、应急处理等方面的内容,使员工充分认识到安全的重要性。
2、建立设备档案对每台设备建立详细的档案,记录设备的运行、维护和维修情况,以便及时发现问题。
设立专门的安全监督部门,对生产过程进行实时监控,及时发现并纠正违规行为。
案例二:某建筑工地坍塌事故事故经过在某建筑工地,一座正在施工的高楼突然发生坍塌。
当时,有许多工人在现场作业,事故造成了多人被埋,伤亡惨重。
事故原因分析1、施工方案不合理施工单位在制定施工方案时,没有充分考虑到地质条件和建筑物的结构特点,导致施工过程中出现了问题。
某年化工事故案例文字说明
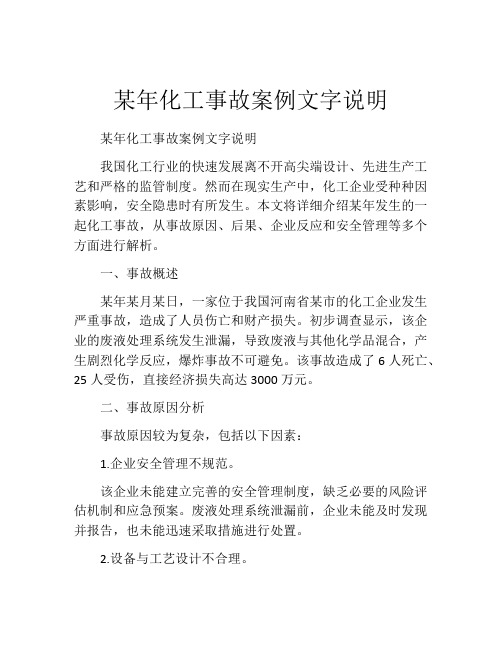
某年化工事故案例文字说明某年化工事故案例文字说明我国化工行业的快速发展离不开高尖端设计、先进生产工艺和严格的监管制度。
然而在现实生产中,化工企业受种种因素影响,安全隐患时有所发生。
本文将详细介绍某年发生的一起化工事故,从事故原因、后果、企业反应和安全管理等多个方面进行解析。
一、事故概述某年某月某日,一家位于我国河南省某市的化工企业发生严重事故,造成了人员伤亡和财产损失。
初步调查显示,该企业的废液处理系统发生泄漏,导致废液与其他化学品混合,产生剧烈化学反应,爆炸事故不可避免。
该事故造成了6人死亡、25人受伤,直接经济损失高达3000万元。
二、事故原因分析事故原因较为复杂,包括以下因素:1.企业安全管理不规范。
该企业未能建立完善的安全管理制度,缺乏必要的风险评估机制和应急预案。
废液处理系统泄漏前,企业未能及时发现并报告,也未能迅速采取措施进行处置。
2.设备与工艺设计不合理。
该企业废液处理系统的容量设计不足,过程设计缺乏完善的控制措施和应急反应措施。
因此,当泄漏事故发生后,整个系统无法承受剧烈的化学反应和高温等影响,造成大规模的爆炸。
3.员工安全意识偏低。
该企业在员工培训和安全意识教育方面投入不足,员工缺乏必要的知识和技能,无法迅速反应和处理突发事件,给事故造成严重后果。
上述原因交织在一起,造成了公司废液处理系统的事故爆发。
三、事故后果该事故给受害者的人身安全与企业经济发展带来了沉重的打击。
据报道,有6人不幸遇难,25人受伤。
此外,公司的生产线、设备和产能都受到严重影响,经济损失较大。
同时,该事故也影响了该市化工行业在整个国际市场中的声誉。
四、企业反应该企业事故后极度重视,彻查事故原因并采取严厉措施进行整改。
企业提高了员工安全意识和技能,建立了完善的安全管理制度、风险评估机制和应急预案。
同时,加强了设备监控和质量检测,健全了废液处理系统的故障检测和维护保养机制。
企业还大幅度提升了企业社会责任的认识,通过各种渠道加强公众安全意识,努力避免类似事件再次发生。
安全典型案例剖析

安全典型案例剖析安全典型案例剖析:某化工厂重大火灾事故背景介绍某化工厂(以下简称“该厂”)位于我国某地,主要从事化工产品的生产和销售。
该厂拥有较为完善的安全管理制度和设施,但在一次生产过程中,发生了重大火灾事故,造成严重的人员伤亡和财产损失。
本文将对这一典型案例进行剖析,分析事故原因、应对措施及教训。
事故经过事故发生时,该厂正在进行某化工产品的生产。
由于设备故障,导致原料泄漏,遇到火源引发火灾。
火势迅速蔓延,导致整个生产车间陷入火海。
事故发生后,厂方立即启动应急预案,组织人员进行扑救,并报警求助。
经过数小时的努力,火势得到控制,但已造成重大损失。
事故原因1. 设备老化:经调查,事故发生的主要原因在于生产设备老化,未能及时进行维修和更换,导致泄漏事故。
2. 管理不善:虽然该厂有安全管理制度,但在实际生产过程中,管理人员对安全生产的重视程度不够,对设备的维护保养不到位。
3. 操作不规范:操作人员在进行生产操作时,未严格按照操作规程进行,对设备故障未能及时发现和处理。
4. 应急预案不完善:虽然厂方有应急预案,但在实际应对火灾事故时,部分环节仍存在不足,如救援设备不齐全、人员疏散不及时等。
应对措施1. 加强设备维护:厂方应定期对生产设备进行检查、维修和更换,确保设备安全运行。
2. 提高管理水平:加强安全生产培训,提高管理人员和操作人员的安全意识,确保各项安全制度得到有效执行。
3. 规范操作流程:对操作人员进行规范化培训,确保严格按照操作规程进行生产操作。
4. 完善应急预案:修订和完善应急预案,加强应急演练,提高应对突发事件的能力。
5. 配齐救援设备:购置必要的救援设备,如消防器材、防护用品等,确保在事故发生时能迅速展开救援。
教训1. 安全生产意识需加强:企业应时刻保持安全生产意识,将安全生产纳入日常经营管理工作中,确保各项安全制度得到有效执行。
2. 设备管理至关重要:企业应加强对设备的维护保养,定期进行检查,确保设备安全运行。
安全事故案例及原因分析全新
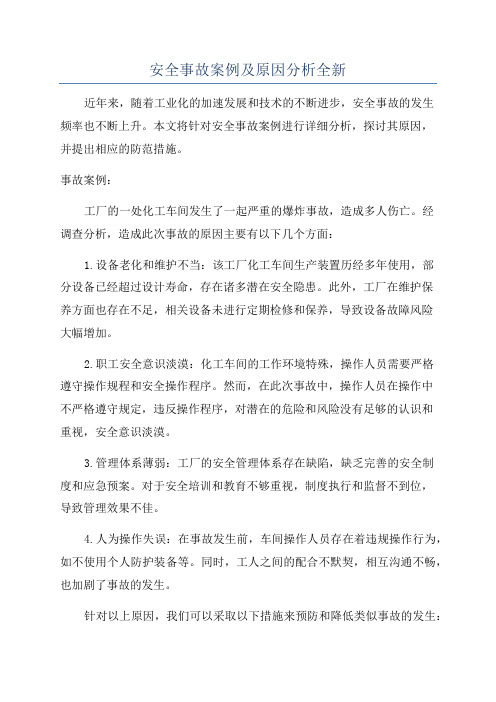
安全事故案例及原因分析全新近年来,随着工业化的加速发展和技术的不断进步,安全事故的发生频率也不断上升。
本文将针对安全事故案例进行详细分析,探讨其原因,并提出相应的防范措施。
事故案例:工厂的一处化工车间发生了一起严重的爆炸事故,造成多人伤亡。
经调查分析,造成此次事故的原因主要有以下几个方面:1.设备老化和维护不当:该工厂化工车间生产装置历经多年使用,部分设备已经超过设计寿命,存在诸多潜在安全隐患。
此外,工厂在维护保养方面也存在不足,相关设备未进行定期检修和保养,导致设备故障风险大幅增加。
2.职工安全意识淡漠:化工车间的工作环境特殊,操作人员需要严格遵守操作规程和安全操作程序。
然而,在此次事故中,操作人员在操作中不严格遵守规定,违反操作程序,对潜在的危险和风险没有足够的认识和重视,安全意识淡漠。
3.管理体系薄弱:工厂的安全管理体系存在缺陷,缺乏完善的安全制度和应急预案。
对于安全培训和教育不够重视,制度执行和监督不到位,导致管理效果不佳。
4.人为操作失误:在事故发生前,车间操作人员存在着违规操作行为,如不使用个人防护装备等。
同时,工人之间的配合不默契,相互沟通不畅,也加剧了事故的发生。
针对以上原因,我们可以采取以下措施来预防和降低类似事故的发生:1.设备维护升级:对老化设备进行检测评估,尽快更换超过寿命的设备,并建立设备维护保养计划,进行定期检修和维护,确保设备处于良好状态。
2.安全意识培养:加强安全意识教育培训,提高职工对安全的认知和重视程度,确保他们能够正确使用防护设备,并定期开展安全演习和模拟演练,加强应急反应能力。
3.建立健全的管理体系:完善安全管理制度和应急预案,确保其具有可操作性和实际有效性。
加强对管理制度的执行和监督,建立安全隐患排查制度,及时发现和整改存在的安全隐患。
4.强化人员培训和沟通交流:定期组织岗位培训,使操作人员熟悉操作程序和安全风险,提高工人之间的配合默契度。
同时,加强沟通交流,建立及时沟通机制,确保信息畅通。
化工厂事故案例分析

化工厂事故案例分析
化工厂作为重要的生产基地,其安全生产一直备受关注。
然而,化工厂事故时有发生,给人们的生命财产安全带来了严重威胁。
本文将通过分析一个化工厂事故案例,探讨其原因和应对措施,以期引起人们对化工厂安全生产的重视。
案例分析:
某化工厂发生了一起严重的爆炸事故,造成了数十人伤亡和大量财产损失。
经过调查,事故的原因主要有以下几点:
首先,化工厂在生产过程中存在严重的安全隐患。
例如,设备老化、维护不及时、操作不规范等问题长期得不到有效解决,导致了事故的发生。
其次,化工厂管理层存在严重的安全管理漏洞。
在事故发生前,管理层对安全生产的重视不够,缺乏有效的安全培训和演练,员工的安全意识薄弱,无法正确应对突发情况。
再次,化工厂在事故后的应对措施不力。
事故发生后,化工厂缺乏有效的紧急预案和救援措施,导致伤亡人数和财产损失进一步扩大。
应对措施:
针对以上问题,化工厂应该采取以下措施来提高安全生产水平:
首先,加强设备维护和更新,确保设备的安全可靠运行。
定期对设备进行检修和更新,及时消除安全隐患。
其次,加强安全管理,建立健全的安全管理制度,加强对员工的安全培训和教育,提高员工的安全意识和应急处理能力。
再次,建立健全的应急预案和救援措施,确保一旦发生事故能够迅速有效地进行应对和救援,最大限度地减少人员伤亡和财产损失。
结论:
化工厂事故给人们敲响了安全生产的警钟,必须高度重视化工厂安全生产工作。
化工企业要加强安全管理,加大安全投入,提高员工安全意识,确保化工生产安全稳定。
只有这样,才能有效避免化工厂事故的发生,保障人们的生命和财产安全。
化工厂爆炸事故案例分析
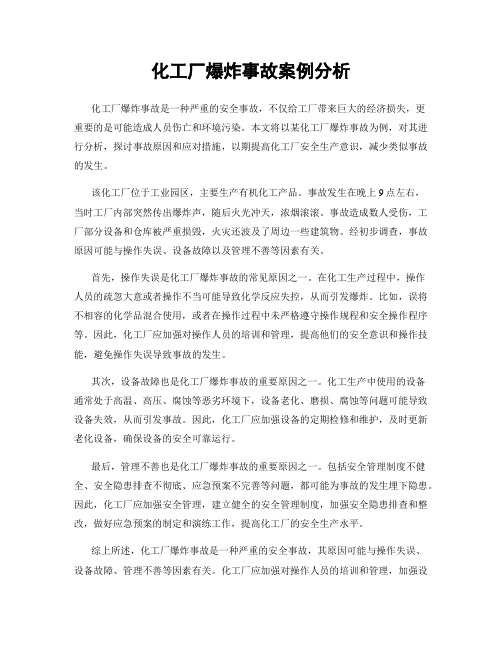
化工厂爆炸事故案例分析化工厂爆炸事故是一种严重的安全事故,不仅给工厂带来巨大的经济损失,更重要的是可能造成人员伤亡和环境污染。
本文将以某化工厂爆炸事故为例,对其进行分析,探讨事故原因和应对措施,以期提高化工厂安全生产意识,减少类似事故的发生。
该化工厂位于工业园区,主要生产有机化工产品。
事故发生在晚上9点左右,当时工厂内部突然传出爆炸声,随后火光冲天,浓烟滚滚。
事故造成数人受伤,工厂部分设备和仓库被严重损毁,火灾还波及了周边一些建筑物。
经初步调查,事故原因可能与操作失误、设备故障以及管理不善等因素有关。
首先,操作失误是化工厂爆炸事故的常见原因之一。
在化工生产过程中,操作人员的疏忽大意或者操作不当可能导致化学反应失控,从而引发爆炸。
比如,误将不相容的化学品混合使用,或者在操作过程中未严格遵守操作规程和安全操作程序等。
因此,化工厂应加强对操作人员的培训和管理,提高他们的安全意识和操作技能,避免操作失误导致事故的发生。
其次,设备故障也是化工厂爆炸事故的重要原因之一。
化工生产中使用的设备通常处于高温、高压、腐蚀等恶劣环境下,设备老化、磨损、腐蚀等问题可能导致设备失效,从而引发事故。
因此,化工厂应加强设备的定期检修和维护,及时更新老化设备,确保设备的安全可靠运行。
最后,管理不善也是化工厂爆炸事故的重要原因之一。
包括安全管理制度不健全、安全隐患排查不彻底、应急预案不完善等问题,都可能为事故的发生埋下隐患。
因此,化工厂应加强安全管理,建立健全的安全管理制度,加强安全隐患排查和整改,做好应急预案的制定和演练工作,提高化工厂的安全生产水平。
综上所述,化工厂爆炸事故是一种严重的安全事故,其原因可能与操作失误、设备故障、管理不善等因素有关。
化工厂应加强对操作人员的培训和管理,加强设备的定期检修和维护,建立健全的安全管理制度,提高化工厂的安全生产水平,以减少类似事故的发生。
希望本文的案例分析能够引起化工企业的重视,促进化工行业的安全生产工作。
事故案例及原因分析安全操作与防火防爆安全技术化工行业已成为
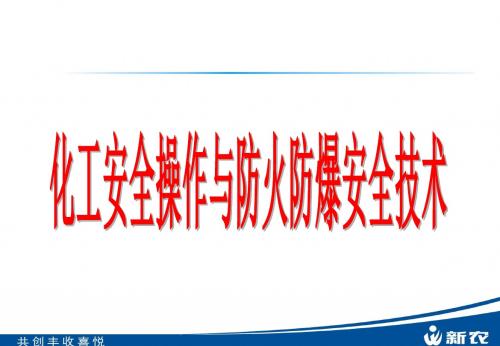
1984年12月,美国联合碳化物公司在印度中央邦首府博帕
二、事故案例及原因分析
尔市的一家农药厂发生45吨剧毒的甲基异氰酸酯泄漏事故,死亡2500 余人,20万人中毒受伤且其中大部分人双目失明,67万人受到残留毒 气的影响,大批牲畜死亡,空气、水源受到严重污染。 事故主要原因:
二、事故案例及原因分析
约5分钟,合成车间即发生系统性化学爆炸。爆炸时,2名工人不幸当 场死亡,另1名因严重烧伤,抢救无效于当晚死亡,同时造成3人重伤, 16人轻伤。爆炸事故造成7#压缩机彻底炸毁,缸体阀腔大部分炸飞, 其中一气阀阀座击穿厂房屋面飞出室外,一块重约30Kg的碎片飞离 原位达87米。3#铜液塔顶操作平台有一块20Kg的钢板飞离塔顶远达 100多米,塔体从框架坠落。陷入地下一米多深。7#压缩机主辅机、 3#铜液塔、2#碱液塔等15处着火燃烧。合成主厂房、铜洗厂房以及 框架、配电室等构建物均遭到不同程度的破坏,电气、仪表装置大部 分被烧毁或震坏。
一、概述 二、事故案例及原因分析 三、安全操作与防火防爆安全技术
一、概述
化工行业已成为五大高危行业之一(矿山、建筑、化工、烟花 爆竹制作和道路机动车辆驾驶)。在化学工业生产中,采用的原料 或生产出的中间体和化工产品,大都是可燃或易燃物质。这些物质 以不同的状态与空气形成爆炸性混合物。若在较小的着火源作用下 能引起严重的燃烧和爆炸事故。尤其是在现代化学工业生产中,生 产连续性强,处理危险物品种数量大,生产方法多,工艺流程复杂, 而且一般都在高温、高压、高速、真空、低温或负压等复杂的工艺 条件下操作。因此很容易发生泄漏、喷溅、腐蚀、着火、爆炸等事 故。一旦事故发生,将会造成人员伤亡、设备设施及建窗玻璃全部被毁,事后在抢修中,需更换门窗玻璃达三吨之多。这 次爆炸威力约等于400~2000KgTNT炸药当量,经济损失达400万元。 爆炸事故原因:根据当时工况和记录表明,水洗气中含氧量超标,高达 5~11%(正常生产要求低于0.2%),形成爆炸性混合气体,遇激发 能源而引起爆炸。水洗气中混入氧气的主要原因:在2#油气化炉停车 检修完后,进行最后一次充氮,准备投油时当班操作人员忘记关掉气 化炉上Ф32mm和Ф40mm两只充氮阀门,造成氧蒸汽倒入氮气总管, 当合成车间合成工段打开配氮阀后,使氧气进入水洗系统,因而造成 7#压缩机爆炸着火事故。