焊接飞溅产生的原因及克服途径
焊接复习资料

焊接复习资料1.co2气体保护焊产生飞溅的原因是什么?产生飞溅的措施有哪些及后果?答:①由冶金反应引起飞溅co2=co+【o];②由极点电压产生飞溅,尤其是直流正接的时候,机械冲刷力大,产生飞溅。
③融滴短路时引起飞溅。
④非轴向颗粒过渡飞溅。
⑤焊接工艺参素选择不当引起的飞溅。
措施:①采用硅锰元素脱氧,降低焊丝的含碳量。
②采用直流反接法。
③调节短路电流的增长速度。
④保证喷嘴气流速度均匀。
⑤正确选择工艺参素。
⑥采用co2潜伏焊(I↑U↓)。
后果:①增加了焊丝及电能的消耗。
②飞溅金属溅到喷嘴内壁上产生气流不均保护效果差。
③飞溅金属伤害到非焊接工作表面影响质量。
④飞溅引起烫伤或火灾。
2.试述交流TIG直流分量产生的原因、后果及措施。
答:原因由于在交流焊接Pb、Mg及合金时,正半周电流大,作用时间大,用于焊接过程而在负半周电流小、作用时间短主要用于清除Al2O3杂质。
(阳极破碎作用)。
可以把电流看成2部分,一部分是真正的交流电,另一部分是产生的直流分量。
危害:①负半周作用时间t2太小,所以削弱了阴极破碎作用。
②使变压器铁芯发热损坏设备。
消除装置:①在焊接回路中串接直流电源(大小相等,方向相反)。
②在焊接回路中串接二极管和电阻。
③焊接回路中串联电容,起通交流阻直流作用。
3.氧——乙炔按混合比不同可分为几种火焰?它的性质及应用范围如何?答:中性焰碳化焰氧化焰中性焰氧气与乙炔的比例为1.1至1.2 火焰温度3050至3050 氧与乙炔充分燃烧,既无过剩氧,也无过剩的乙炔。
焰心明亮,轮廓清楚,内焰具有一定的还原性,适用于焊接、切割、低碳钢和中低合金钢碳化焰气与乙炔的比例小于1.1 火焰温度2700至3000 乙炔过剩,火焰中有游离的碳和氢,具有较强的还原作用,也有一定的渗碳作用碳化焰整过火焰比中性焰长,适用于焊高碳钢、铸铁、中高合金钢氧化焰气与乙炔的比例大于1.2 火焰温度3100至3300 火焰中有过量的氧,具有强烈的氧化性,整过火焰较短,内焰和外焰层次不错,适用于黄铜4.双弧产生的原因是什么?防止措施及后果?产生原因:由于喷嘴在冷却水的作用下,在电弧周围形成了冷气膜冷气膜的两大作用;①绝热作用保护喷嘴②绝缘作用保证产生一根弧柱,当冷却效果变差使喷嘴某处的冷气膜消失,则在该点会产生另一根电弧,这就是双弧现象措施:①正确使用喷嘴的结构参数②增大喷嘴的冷却效果③控制离子流量不能过大④调整喷嘴端面与工件表面的距离不能过大⑤控制电弧电流不能过大⑥保证乌极轴心线与孔道轴心线同轴后果:①使热量不集中能量分散②使焊接或切割的成型性变差③容易烧穿喷嘴④易发生触电事故⑤工件热影响区大1.钎焊是采用比(母材)熔点低的的金属材料作(钎料),将(焊件)和(钎料)加热至高于(钎料)熔点的温度利用(液态钎料)润湿母材,填充接头间隙并与母材相互扩散实现连接焊件的方法。
防止焊渣飞溅的措施

防止焊渣飞溅的措施焊接是一种常见的制造工艺,但在焊接过程中,焊接材料会产生高温、高压的气体和液体,导致焊渣飞溅,从而给工人的身体健康带来威胁,也会对设备和环境造成损害。
因此,采取防止焊渣飞溅的措施是非常必要的。
一、选择合适的焊接材料和设备选择合适的焊接材料和设备是防止焊渣飞溅的第一步。
应根据所需的焊接工艺和材料性质选择适当的焊接方法和设备。
例如,在焊接不锈钢时,应选择适合不锈钢的焊接材料和设备,以避免产生过多的焊渣。
二、控制焊接电流和电压焊接电流和电压是影响焊接质量的重要因素。
如果电流和电压过高,将导致焊接过程中产生过多的气体和液体,从而产生大量的焊渣。
因此,在焊接过程中,应根据焊接材料和设备的要求,控制电流和电压,以减少焊渣的产生。
三、使用气体保护焊接气体保护焊接是一种常见的焊接方法,通过使用气体来保护焊接区域,可以减少焊接过程中产生的气体和液体,从而减少焊渣的产生。
常用的气体保护焊接方法包括TIG焊接、MIG/MAG焊接等。
四、采取防护措施为了保护工人的身体健康,应采取必要的防护措施。
例如,在焊接过程中,应穿戴防护服、手套、面罩等防护用具,以避免焊渣飞溅伤害工人的皮肤和眼睛。
五、定期维护和清洁设备设备的维护和清洁也是防止焊渣飞溅的关键。
定期清理焊接设备和周围环境的焊渣和杂物,可以保持设备的清洁和正常运行,减少焊渣的产生。
综上所述,防止焊渣飞溅是非常必要的。
通过选择合适的焊接材料和设备、控制焊接电流和电压、使用气体保护焊接、采取防护措施和定期维护和清洁设备等措施,可以有效地减少焊渣的产生,保护工人的身体健康和设备的正常运行。
飞溅产生原因
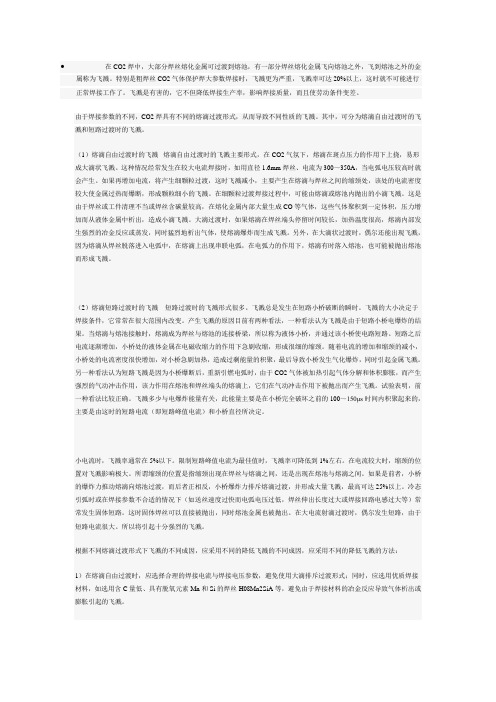
•在CO2焊中,大部分焊丝熔化金属可过渡到熔池,有一部分焊丝熔化金属飞向熔池之外,飞到熔池之外的金属称为飞溅。
特别是粗焊丝CO2气体保护焊大参数焊接时,飞溅更为严重,飞溅率可达20%以上,这时就不可能进行正常焊接工作了。
飞溅是有害的,它不但降低焊接生产率,影响焊接质量,而且使劳动条件变差。
由于焊接参数的不同,CO2焊具有不同的熔滴过渡形式,从而导致不同性质的飞溅。
其中,可分为熔滴自由过渡时的飞溅和短路过渡时的飞溅。
(1)熔滴自由过渡时的飞溅熔滴自由过渡时的飞溅主要形式,在CO2气氛下,熔滴在斑点压力的作用下上挠,易形成大滴状飞溅。
这种情况经常发生在较大电流焊接时,如用直径1.6mm焊丝、电流为300~350A,当电弧电压较高时就会产生。
如果再增加电流,将产生细颗粒过渡,这时飞溅减小,主要产生在熔滴与焊丝之间的缩颈处,该处的电流密度较大使金属过热而爆断,形成颗粒细小的飞溅。
在细颗粒过渡焊接过程中,可能由熔滴或熔池内抛出的小滴飞溅。
这是由于焊丝或工件清理不当或焊丝含碳量较高,在熔化金属内部大量生成CO等气体,这些气体聚积到一定体积,压力增加而从液体金属中析出,造成小滴飞溅。
大滴过渡时,如果熔滴在焊丝端头停留时间较长,加热温度很高,熔滴内部发生强烈的冶金反应或蒸发,同时猛烈地析出气体,使熔滴爆炸而生成飞溅。
另外,在大滴状过渡时,偶尔还能出现飞溅,因为熔滴从焊丝脱落进入电弧中,在熔滴上出现串联电弧,在电弧力的作用下,熔滴有时落入熔池,也可能被抛出熔池而形成飞溅。
(2)熔滴短路过渡时的飞溅短路过渡时的飞溅形式很多。
飞溅总是发生在短路小桥破断的瞬时。
飞溅的大小决定于焊接条件,它常常在很大范围内改变。
产生飞溅的原因目前有两种看法,一种看法认为飞溅是由于短路小桥电爆炸的结果。
当熔滴与熔池接触时,熔滴成为焊丝与熔池的连接桥梁,所以称为液体小桥,并通过该小桥使电路短路。
短路之后电流逐渐增加,小桥处的液体金属在电磁收缩力的作用下急剧收缩,形成很细的缩颈。
焊接时焊渣飞溅的原因及措施

焊接时焊渣飞溅的原因及措施
嘿,朋友们!今天咱来聊聊焊接时那让人头疼的焊渣飞溅问题!你知道吗,就好像一场混乱的战斗,那些焊渣到处飞溅,真是让人又气又无奈啊!
咱先说原因哈。
电流电压没调好,这不就像是给焊接这场战斗派了不合适的兵力,能不乱套嘛!就好比炒菜盐放多了或者放少了,味道肯定不对劲。
再就是焊条角度不对,哎呀呀,这就好比射击瞄歪了,能打中目标才怪呢!还有焊接速度过快或过慢,这和跑步似的,跑太快或者太慢都容易出问题呀!
那咋办呢?别着急,咱有办法!首先得把电流电压调好啊,就像给战士找到最适合的武器装备。
你得认真琢磨,多试试,找到那个最佳的点。
焊条角度也得注意,要找到最合适的姿势,就像打拳要有个标准的架势一样。
还有啊,焊接速度要把握好,不快不慢,稳稳当当,可别像没头苍蝇似的乱焊一通。
我记得有一次,我和老张一起干活,就因为他没注意这些,结果焊渣飞溅得到处都是,把旁边的东西都弄脏了,还差点烫到人呢!老张自己也懊恼得不行。
所以啊,朋友们,可千万要重视起来。
焊接可不是小事,那焊渣飞溅看似不起眼,一不小心就能惹出大麻烦。
咱得把这些问题都解决好,才能做出漂亮的焊接活儿。
别小看这一点点细节,往往就是细节决定成败啊!就像建大楼,一块砖没砌好可能整栋楼都不稳。
大家说是不是这个理儿?让我们一起重视起来,把焊接时的焊渣飞溅问题彻底解决掉!。
焊接飞溅

焊接飞溅产生的原因及克服途径在CO2焊中,大部分焊丝熔化金属可过渡到熔池,有一部分焊丝熔化金属飞向熔池之外,飞到熔池之外的金属称为飞溅。
特别是粗焊丝CO2气体保护焊大参数焊接时,飞溅更为严重,飞溅率可达20%以上,这时就不可能进行正常焊接工作了。
飞溅是有害的,它不但降低焊接生产率,影响焊接质量,而且使劳动条件变差。
由于焊接参数的不同,CO2焊具有不同的熔滴过渡形式,从而导致不同性质的飞溅。
其中,可分为熔滴自由过渡时的飞溅和短路过渡时的飞溅。
(1)熔滴自由过渡时的飞溅熔滴自由过渡时的飞溅主要形式,在CO2气氛下,熔滴在斑点压力的作用下上挠,易形成大滴状飞溅。
这种情况经常发生在较大电流焊接时,如用直径1.6mm焊丝、电流为300~350A,当电弧电压较高时就会产生。
如果再增加电流,将产生细颗粒过渡,这时飞溅减小,主要产生在熔滴与焊丝之间的缩颈处,该处的电流密度较大使金属过热而爆断,形成颗粒细小的飞溅。
在细颗粒过渡焊接过程中,可能由熔滴或熔池内抛出的小滴飞溅。
这是由于焊丝或工件清理不当或焊丝含碳量较高,在熔化金属内部大量生成CO等气体,这些气体聚积到一定体积,压力增加而从液体金属中析出,造成小滴飞溅。
大滴过渡时,如果熔滴在焊丝端头停留时间较长,加热温度很高,熔滴内部发生强烈的冶金反应或蒸发,同时猛烈地析出气体,使熔滴爆炸而生成飞溅。
另外,在大滴状过渡时,偶尔还能出现飞溅,因为熔滴从焊丝脱落进入电弧中,在熔滴上出现串联电弧,在电弧力的作用下,熔滴有时落入熔池,也可能被抛出熔池而形成飞溅。
(2)熔滴短路过渡时的飞溅短路过渡时的飞溅形式很多。
飞溅总是发生在短路小桥破断的瞬时。
飞溅的大小决定于焊接条件,它常常在很大范围内改变。
产生飞溅的原因目前有两种看法,一种看法认为飞溅是由于短路小桥电爆炸的结果。
当熔滴与熔池接触时,熔滴成为焊丝与熔池的连接桥梁,所以称为液体小桥,并通过该小桥使电路短路。
短路之后电流逐渐增加,小桥处的液体金属在电磁收缩力的作用下急剧收缩,形成很细的缩颈。
焊接飞溅的控制

这种现象其实也是与温度有关,通常食 用油的温度能够加热到200多度。而室温的 冷水也能达到10几度,温差约在200度左右, 可反应飞溅就如此剧烈回过头来看从熔滴 4000度到落入熔池1770的温差悬殊是极大 的,可想而知反应之剧烈飞溅之密集。
知识拓展 飞溅的存在对焊接的影响是怎样的呢?
1、飞溅消耗了焊接材料,带走了大量的热量造成了能源 的浪费。 2、飞溅带走了大量的合金元素,影响了合金元素的过 渡降低了焊缝的强度。
熔池的温度
1670℃
1770℃
三相温度对比
电弧5370——7730℃
温 度 下 降 走 势
熔滴温度4000℃
熔池温度1670——1770℃
熔池飞溅的产生
飞溅现象解析 举列:平时在家炒菜或看见别人炒菜时 当把油加热后,我们把室温的菜呀、肉 呀或者说手上的冷水呀落入锅里后将发 生什么现象呢? 引起剧烈的飞溅
焊接实训:飞溅形成的原因
一、复习旧知与引课
1、大家思考过这样一个问题没有?在我们焊 接操作过程中伴随着弧光闪闪、焊花飞溅制造 绚丽的同时我们操作者也在不断地挨烫,这种 现象是什么原因造成的呢?
、学习任务
1、焊接时飞溅形成的原因
<1>液态小桥爆断引起的飞溅
<2>熔池温差引起的飞溅
2、改善和降低飞溅的措施
•5)长弧焊的时在CO2 中加入Ar 气。在CO2 气体中加入Ar 气后,改变了纯二氧化 碳气体的导热率高,分解吸热,消耗电弧热能高易导致弧柱及电弧斑点强烈收缩,阻 碍熔滴过渡的物理化学性质。随着Ar 气比例增大,飞溅逐渐减少。CO2+Ar 混合 气体除可克服飞溅外,也改善了焊缝成型,对焊缝溶深、焊缝高度及余高都有影响。 实践证明80%Ar+20%CO2 时飞溅率最低。6)采用低飞溅率焊丝。①实芯焊丝。 在保证机械性能的前提下,应尽可能降低其中含碳量,并添加适量的钛、铝等合金 元素。无论颗粒过度焊接或短路过度焊接都可显著减少由CO 等气体引起的飞溅。 ②采用以Cs2CO3,K2CO3 等物质活化处理过的焊丝,进行正极性焊接。③采用 药芯焊丝。采用药芯焊丝的金属飞溅率越为实心焊丝的1/3。此外,在焊接回路中 串联大的电感,使短路电流上升慢些也可以适当的减少飞溅。
co2焊飞溅的原因及防治措施
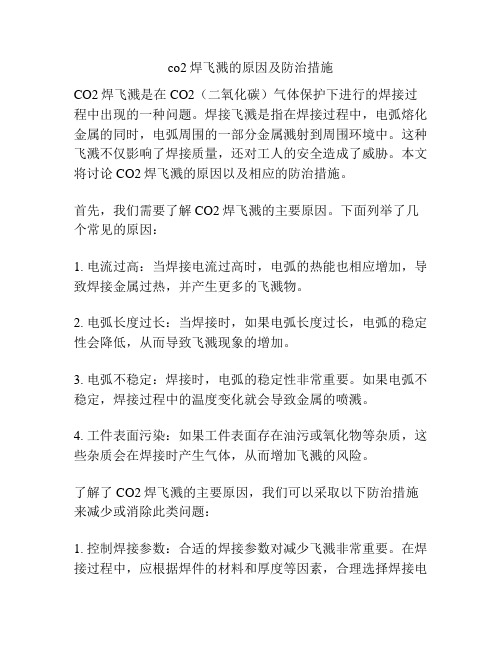
co2焊飞溅的原因及防治措施CO2焊飞溅是在CO2(二氧化碳)气体保护下进行的焊接过程中出现的一种问题。
焊接飞溅是指在焊接过程中,电弧熔化金属的同时,电弧周围的一部分金属溅射到周围环境中。
这种飞溅不仅影响了焊接质量,还对工人的安全造成了威胁。
本文将讨论CO2焊飞溅的原因以及相应的防治措施。
首先,我们需要了解CO2焊飞溅的主要原因。
下面列举了几个常见的原因:1. 电流过高:当焊接电流过高时,电弧的热能也相应增加,导致焊接金属过热,并产生更多的飞溅物。
2. 电弧长度过长:当焊接时,如果电弧长度过长,电弧的稳定性会降低,从而导致飞溅现象的增加。
3. 电弧不稳定:焊接时,电弧的稳定性非常重要。
如果电弧不稳定,焊接过程中的温度变化就会导致金属的喷溅。
4. 工件表面污染:如果工件表面存在油污或氧化物等杂质,这些杂质会在焊接时产生气体,从而增加飞溅的风险。
了解了CO2焊飞溅的主要原因,我们可以采取以下防治措施来减少或消除此类问题:1. 控制焊接参数:合适的焊接参数对减少飞溅非常重要。
在焊接过程中,应根据焊件的材料和厚度等因素,合理选择焊接电流、电压和电弧长度。
2. 提高电弧稳定性:采取适当的焊接姿势和合适的电弧长度,可以提高电弧的稳定性,减少飞溅的问题。
3. 清洁工件表面:在进行焊接之前,必须保证工件表面的清洁。
通过去除油污、氧化物和其他杂质,可以减少飞溅的概率。
4. 使用抗飞溅剂:抗飞溅剂是一种特殊的涂层剂,可以在焊接过程中有效地减少飞溅。
这些剂涂覆在焊接区域,可以形成一层保护膜,阻止金属喷溅并减少飞溅。
5. 增加气体流量:适当增加CO2气体的流量可以帮助稳定电弧,并减少飞溅物的产生。
6. 定期维护和保养设备:焊接设备的定期维护和保养对于减少飞溅非常重要。
保持设备的良好状态可以提高焊接的稳定性,减少飞溅现象。
总之,CO2焊飞溅是一种常见的焊接问题,可能影响焊接质量和工人的安全。
通过控制焊接参数、提高电弧稳定性、清洁工件表面、使用抗飞溅剂、增加气体流量和定期维护设备等措施,可以有效地减少或消除飞溅现象。
焊接过程中飞溅突然增大的原因

焊接过程中飞溅突然增大的原因
1. 电流和电压设置不当,焊接过程中,如果电流和电压设置不合适,可能会导致电弧不稳定,从而增加飞溅的可能性。
过高的电流和电压会导致电弧过于强大,增加飞溅的风险。
2. 电极材料选择不当,使用不合适的电极材料也可能导致焊接飞溅增大。
例如,使用磷化涂层太厚的焊条或者含有过多氧化物的焊条,都可能导致飞溅增加。
3. 焊接速度过快或过慢,焊接速度过快会导致焊接材料无法充分熔化,从而增加飞溅的可能性;而焊接速度过慢则会导致焊接材料过热,同样增加飞溅的风险。
4. 焊接材料表面清洁不当,焊接材料表面的油污、氧化物或其他杂质会影响焊接质量,导致飞溅增加。
5. 气体保护不足,焊接过程中使用的保护气体不足或者气流不稳定也会导致飞溅增加。
6. 焊接位置不当,焊接位置不当,如上下坡焊接时,焊接飞溅
增加的可能性也会提高。
综上所述,焊接过程中飞溅突然增大可能是由于电流和电压设置、电极材料选择、焊接速度、材料表面清洁、气体保护以及焊接位置等多种因素导致的。
在实际操作中,需要综合考虑这些因素,及时调整焊接参数和操作方法,以减少飞溅的产生。
- 1、下载文档前请自行甄别文档内容的完整性,平台不提供额外的编辑、内容补充、找答案等附加服务。
- 2、"仅部分预览"的文档,不可在线预览部分如存在完整性等问题,可反馈申请退款(可完整预览的文档不适用该条件!)。
- 3、如文档侵犯您的权益,请联系客服反馈,我们会尽快为您处理(人工客服工作时间:9:00-18:30)。
焊接飞溅产生的原因及克服途径
在CO2焊中,大部分焊丝熔化金属可过渡到熔池,有一部分焊丝熔化金属飞向熔池之外,飞到熔池之外的金属称为飞溅。
特别是粗焊丝CO2气体保护焊大参数焊接时,飞溅更为严重,飞溅率可达20%以上,这时就不可能进行正常焊接
工作了。
飞溅是有害的,它不但降低焊接生产率,影响焊接质量,而且使劳动条件变差。
由于焊接参数的不同,CO2焊具有不同的熔滴过渡形式,从而导致不同性质的飞溅。
其中,可分为熔滴自由过渡时的飞溅和短路过渡时的飞溅。
(1)熔滴自由过渡时的飞溅:
在CO2气氛下,熔滴在斑点压力的作用下上挠,易形成大滴状飞溅。
这种情况经常发生在较大电流焊接时,如用直径1.6mm焊丝、电流为300~350A,当
电弧电压较高时就会产生。
如果再增加电流,将产生细颗粒过渡,这时飞溅减小,主要产生在熔滴与焊丝之间的缩颈处,该处的电流密度较大使金属过热而爆断,形成颗粒细小的飞溅。
在细颗粒过渡焊接过程中,可能由熔滴或熔池内抛出的小滴飞溅。
这是由于焊丝或工件清理不当或焊丝含碳量较高,在熔化金
属内部大量生成CO等气体,这些气体聚积到一定体积,压力增加而从液体金
属中析出,造成小滴飞溅。
大滴过渡时,如果熔滴在焊丝端头停留时间较长,加热温度很高,熔滴内部发生强烈的冶金反应或蒸发,同时猛烈地析出气体,使熔滴爆炸而生成飞溅。
另外,在大滴状过渡时,偶尔还能出现飞溅,因为熔滴从焊丝脱落进入电弧中,在熔滴上出现串联电弧,在电弧力的作用下,熔滴有时落入熔池,也可能被抛出熔池而形成飞溅。
(2)熔滴短路过渡时的飞溅:
熔滴短路过渡时的飞溅形式很多。
飞溅总是发生在短路小桥破断的瞬时。
飞溅的大小决定于焊接条件,它常常在很大范围内改变。
产生飞溅的原因目前有两种看法,一种看法认为飞溅是由于短路小桥电爆炸的结果。
当熔滴与熔池接触时,熔滴成为焊丝与熔池的连接桥梁,所以称为液体小桥,并通过该小桥使电路短路。
短路之后电流逐渐增加,小桥处的液体金属在电磁收缩力的作用下急剧收缩,形成很细的缩颈。
随着电流的增加和缩颈的减小,小桥处的电流密度很快增加,对小桥急剧加热造成过剩能量的积聚,最后导致小桥发生气化爆炸,同时引起金属飞溅。
另一种看法认为短路飞溅是因为小桥爆断后,重新引
燃电弧时,由于CO2气体被加热引起气体分解和体积膨胀而产生强烈的气动冲
击作用,该力作用在熔池和焊丝端头的熔滴上,它们在气动冲击作用下被抛出而产生飞溅。
试验表明,前一种看法比较正确。
飞溅多少与电爆炸能量有关,
此能量主要是在小桥完全破坏之前的100~150μs时间内积聚起来的,主要是由这时的短路电流(即短路峰值电流)和小桥直径所决定。
小电流时,飞溅率通常在5%以下。
限制短路峰值电流为最佳值时,飞溅率可降低到1%左右。
在电流较大时,缩颈的位置对飞溅影响极大。
所谓缩颈的位
置是指缩颈出现在焊丝与熔滴之间,还是出现在熔池与熔滴之间。
如果是前者,小桥的爆炸力推动熔滴向熔池过渡,而后者正相反,小桥爆炸力排斥熔滴
过渡,并形成大量飞溅,最高可达25%以上。
冷态引弧时或在焊接参数不合适
的情况下(如送丝速度过快而电弧电压过低,焊丝伸出长度过大或焊接回路电感过大等)常常发生固体短路。
这时固体焊丝可以直接被抛出,同时熔池金属也被抛出。
在大电流射滴过渡时,偶尔发生短路,由于短路电流很大。
所以将引起十分强烈的飞溅。
根据不同熔滴过渡形式下飞溅的不同成因,应采用不同的降低飞溅的不同成因,应采用不同的降低飞溅的方法:
(1)在熔滴自由过渡时,应选择合理的焊接电流与焊接电压参数,避免使用大滴排斥过渡形式;同时,应选用优质焊接材料,如选用含C量低、具有脱氧元素Mn和Si的焊丝H08Mn2SiA等,避免由于焊接材料的冶金反应导致气体析出或膨胀引起的飞溅。
(2)在短路过渡时,可以采用(Ar+ CO2)混合气体代替CO2以减少飞溅。
如加入φ(Ar)=20%~30%的Ar。
这是由于随着含氩量的增加,电弧形态和
熔滴过渡特点发生了改变。
燃弧时电弧的弧根扩展,熔滴的轴向性增强。
这一方面使得熔滴容易与熔池会合,短路小桥出现在焊丝和熔池之间。
另一方面熔滴在轴向力的作用下,得到较均匀的短路过渡过程,短路峰值电流也不太高,有利于减少飞溅率。
在纯CO2气氛下,通常通过焊接电流波形控制法,降低短路初期电流以及短路
小桥破断瞬间的电流,减少小桥电爆炸能量,达到降低飞溅的目的。
通过改进送丝系统,采用脉冲送丝代替常规的等速送丝,使熔滴在脉动送进的情况下与熔池发生短路,使短路过渡频率与脉动送丝的频率基本一致,每个短路周期的电参数的重复性好,短路峰值电流也均匀一致,其数值也不高,从而降低了飞溅。
如果在脉动送丝的基础上,再配合电流波形控制,其效果更佳。
采用不同控制方法时,焊接飞溅率与焊接电流之间的关系。
本文编辑:糖糖。