氩弧焊接常见缺陷产生原因及处理(内容清晰)
氩弧焊技术工艺及常见缺陷与控制措施

氩弧焊技术工艺及常见缺陷与控制措施氩弧焊是一种常用的金属焊接方法,其优点在于焊接质量高、焊缝美观、焊接变形小等。
然而,氩弧焊也存在一些常见的缺陷,如气孔、裂纹、夹杂等。
为了保证氩弧焊的质量,必须采取相应的控制措施。
一、氩弧焊技术工艺氩弧焊的技术工艺包括预处理、焊接参数的选择、焊接过程控制等。
1. 预处理在氩弧焊前,必须对焊接材料进行预处理。
首先,要清洁焊接表面,去除油污、氧化物等杂质。
其次,要对焊接材料进行加热处理,以消除内部应力和改善焊接性能。
2. 焊接参数的选择氩弧焊的焊接参数包括电流、电压、焊接速度等。
这些参数的选择应根据焊接材料的种类、厚度、形状等因素进行调整。
一般来说,焊接电流越大,焊接速度越快,焊接质量越好。
3. 焊接过程控制在氩弧焊的过程中,需要控制焊接速度、焊接电流、焊接电压等参数,以保证焊接质量。
同时,还需要注意氩气流量、电极角度、焊接位置等因素的控制。
二、常见缺陷及控制措施1. 气孔气孔是氩弧焊中常见的缺陷之一,其产生原因主要是焊接材料中含有气体或气体被吸入焊接池中。
为了避免气孔的产生,可以采取以下控制措施:(1)焊接前对焊接材料进行预热处理,以消除内部应力和气体。
(2)控制氩气流量,保证焊接池中的气体被排出。
(3)控制焊接速度和焊接电流,以保证焊接池中的气体被充分熔化。
2. 裂纹裂纹是氩弧焊中另一个常见的缺陷,其产生原因主要是焊接材料中含有过多的碳、硫等元素,或者焊接过程中温度变化过大。
为了避免裂纹的产生,可以采取以下控制措施:(1)选择低碳、低硫的焊接材料。
(2)控制焊接过程中的温度变化,避免过快的冷却。
(3)采用预热和后热处理,以消除内部应力和改善焊接性能。
3. 夹杂夹杂是氩弧焊中另一个常见的缺陷,其产生原因主要是焊接材料中含有杂质或者焊接过程中未能完全熔化的材料。
为了避免夹杂的产生,可以采取以下控制措施:(1)选择纯净的焊接材料。
(2)控制焊接过程中的氩气流量和焊接速度,以保证焊接池中的杂质被排出。
氩弧焊机常见故障及排除方法
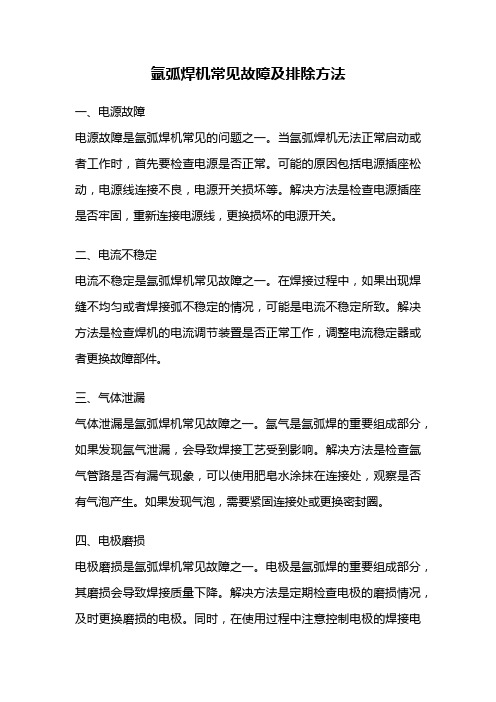
氩弧焊机常见故障及排除方法一、电源故障电源故障是氩弧焊机常见的问题之一。
当氩弧焊机无法正常启动或者工作时,首先要检查电源是否正常。
可能的原因包括电源插座松动,电源线连接不良,电源开关损坏等。
解决方法是检查电源插座是否牢固,重新连接电源线,更换损坏的电源开关。
二、电流不稳定电流不稳定是氩弧焊机常见故障之一。
在焊接过程中,如果出现焊缝不均匀或者焊接弧不稳定的情况,可能是电流不稳定所致。
解决方法是检查焊机的电流调节装置是否正常工作,调整电流稳定器或者更换故障部件。
三、气体泄漏气体泄漏是氩弧焊机常见故障之一。
氩气是氩弧焊的重要组成部分,如果发现氩气泄漏,会导致焊接工艺受到影响。
解决方法是检查氩气管路是否有漏气现象,可以使用肥皂水涂抹在连接处,观察是否有气泡产生。
如果发现气泡,需要紧固连接处或更换密封圈。
四、电极磨损电极磨损是氩弧焊机常见故障之一。
电极是氩弧焊的重要组成部分,其磨损会导致焊接质量下降。
解决方法是定期检查电极的磨损情况,及时更换磨损的电极。
同时,在使用过程中注意控制电极的焊接电流和电极间距,以延长电极的使用寿命。
五、接地故障接地故障是氩弧焊机常见故障之一。
焊接时,如果接地不良,会导致焊接质量下降,甚至引发危险。
解决方法是检查焊机的接地线是否牢固,是否与焊接工件有良好接触。
可以使用万用表检测接地电阻,确保接地良好。
六、过热保护过热保护是氩弧焊机常见故障之一。
当焊机过热时,会自动断开电源,以保护焊机和焊工的安全。
解决方法是检查焊机散热系统是否正常工作,清理散热风扇和散热片,并确保使用环境通风良好。
七、故障代码显示一些高级氩弧焊机具有故障代码显示功能。
当焊机故障时,会显示相应的故障代码,方便快速排除故障。
解决方法是查阅焊机的使用说明书,找到对应故障代码的解决方法,并按照说明进行操作。
氩弧焊机常见故障包括电源故障、电流不稳定、气体泄漏、电极磨损、接地故障、过热保护和故障代码显示等。
针对不同的故障,我们可以采取相应的解决方法,保证氩弧焊机的正常工作和焊接质量。
熔化极氩弧焊焊缝中常见的缺陷

熔化极氩弧焊焊缝中常见的缺陷熔化极氩弧焊是一种常用的焊接方法,广泛应用于金属制品的生产和加工过程中。
然而,在熔化极氩弧焊焊缝中,常常会出现一些缺陷,这些缺陷可能会导致焊接接头的质量下降,甚至影响整个产品的使用寿命和安全性。
本文将针对熔化极氩弧焊焊缝中常见的缺陷进行详细的介绍和分析。
1. 气孔缺陷气孔是熔化极氩弧焊焊缝中最常见的缺陷之一。
气孔是由于焊接过程中未能将气体排除干净,导致气体在焊缝中形成的小孔。
气孔会降低焊接接头的强度和密封性,使焊接接头容易腐蚀和断裂。
造成气孔的原因有多种,如焊材表面有油污或氧化物、焊接过程中气体保护不足等。
2. 焊缝不饱满焊缝不饱满是熔化极氩弧焊焊缝中常见的另一种缺陷。
当焊接过程中焊丝供给不均匀或焊接速度过快时,会导致焊缝的形成不饱满。
焊缝不饱满会影响焊接接头的强度和密封性,降低焊接接头的质量。
3. 焊缝裂纹焊缝裂纹是熔化极氩弧焊焊缝中常见的缺陷之一。
焊缝裂纹是由于焊接过程中产生的应力过大,导致焊缝出现裂纹。
焊缝裂纹会降低焊接接头的强度和密封性,使其易受外界环境的侵蚀和破坏。
4. 焊渣残留焊渣残留是熔化极氩弧焊焊缝中常见的缺陷之一。
焊渣是焊接过程中产生的金属氧化物和杂质等物质,它们未能完全熔化并与焊缝结合在一起,形成了焊接接头中的残留物。
焊渣残留会影响焊接接头的整体质量和密封性。
5. 未熔透未熔透是熔化极氩弧焊焊缝中常见的缺陷之一。
未熔透是指焊接过程中焊缝未能完全熔化并与母材结合在一起,导致焊接接头的强度和密封性下降。
未熔透一般是由于焊接电流过小、焊接速度过快等原因造成的。
为了避免以上缺陷的出现,我们可以采取一些措施来提高熔化极氩弧焊焊缝的质量。
首先,焊接前要对焊材进行处理,保证焊材表面的清洁和无油污、氧化物等杂质。
其次,在焊接过程中要严格控制焊接电流和焊接速度,确保焊缝的形成饱满和熔化透彻。
此外,还要加强焊接操作人员的培训,提高其对焊接过程的控制能力和质量意识。
熔化极氩弧焊焊缝中的缺陷对焊接接头的质量和性能有着重要的影响。
氩弧焊禁忌与不良产生原因《预防措施》、英杰职业教育

氩弧焊禁忌与不良产生原因《预防措施》、英杰职业教育在相当长一段时间内,有焊接同仁跟我探讨的时候就问“为什么我在用氩弧焊焊接的时候成型这么难看?怎么解决?”这个问题其实很多经验丰富的焊接技师都很难一下子定义出是一个具体什么原因,因为这些个是一些经验的问题和付出功夫练习的问题,只有多接触各种金属的氩弧焊,各种角度的氩弧焊及各种工矿环境下的氩弧焊才可以有资格去归类每一种成型不良的原因。
1、氩弧焊成型不良产生的原因及防止措施:1.焊接参数选择不正确。
焊机功能键不是真正了解或者焊接工艺上的参数调节不正确,这些是一个要主要系统学习各种金属各种尺寸和各种接头的工艺参数调节的。
2.焊枪操作不均匀。
这个是纯一可以完全控制了的问题,就是练习加练习,提高焊枪和焊丝的配合操作技能。
3.送丝方法不对。
4.熔池温度控制不好。
氩弧焊的过程中还会出现成型焊缝比较脏,发黑,或者焊缝有黑点等等这对于产品的美观来说是很要命的,总结一下如下原因及解决办法。
《现象》1.气体纯度不够。
2.母体的表面不干净.3.选择的焊丝质量不行,体现在焊丝冶炼杂质比较多,表面氧化膜处理控制质量不好,建议选用正规焊丝。
《措施》1.检查送气软管是否有泄漏情况,是否有抽风,气嘴是否有松动,保护气体使用是否正确。
2.使用正确的存储或者和供应商联系。
3.在使用其他的机械清理前,先将油和油脂类物质清除掉。
4.为了保证特别好的焊接质量可以用专用不锈钢刷进行表面氧化膜清理,一般情况下的焊接因为考虑到效率问题不会刻意去注意氧化膜的清理。
2、氩弧焊成型不良大体可以归纳几种:1.焊缝高低不平,有太高的,有下陷的。
2.焊缝宽窄不一,有太宽的,有太窄熔池都没有打开的。
3.尺寸过大或者过小。
4.角焊缝单边以及焊脚尺寸,有焊角低的。
3、氩弧焊接忌采用简易焊接流程焊接流程过于简单,易产生明显的焊缝凹陷、气孔和裂纹缺陷,对热裂纹倾向较大的材料更甚。
正常的焊接流程应该是在氩气保护自爱进行引弧和收弧,以免钨极和焊缝金属氧化,影响焊缝质量。
不锈钢氩弧焊接工艺特点及常见缺陷的防治措施
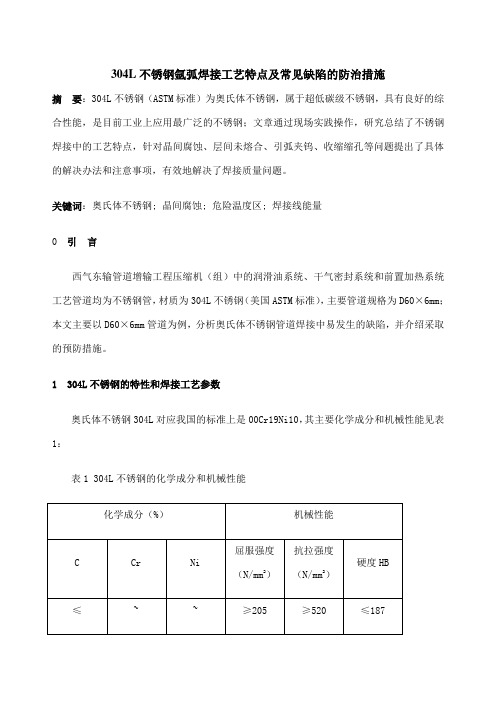
304L不锈钢氩弧焊接工艺特点及常见缺陷的防治措施摘要:304L不锈钢(ASTM标准)为奥氏体不锈钢,属于超低碳级不锈钢,具有良好的综合性能,是目前工业上应用最广泛的不锈钢;文章通过现场实践操作,研究总结了不锈钢焊接中的工艺特点,针对晶间腐蚀、层间未熔合、引弧夹钨、收缩缩孔等问题提出了具体的解决办法和注意事项,有效地解决了焊接质量问题。
关键词:奥氏体不锈钢; 晶间腐蚀; 危险温度区; 焊接线能量0 引言西气东输管道增输工程压缩机(组)中的润滑油系统、干气密封系统和前置加热系统工艺管道均为不锈钢管,材质为304L不锈钢(美国ASTM标准),主要管道规格为D60×6mm;本文主要以D60×6mm管道为例,分析奥氏体不锈钢管道焊接中易发生的缺陷,并介绍采取的预防措施。
1 304L不锈钢的特性和焊接工艺参数奥氏体不锈钢304L对应我国的标准上是00Cr19Ni10,其主要化学成分和机械性能见表1:表1 304L不锈钢的化学成分和机械性能304L不锈钢的导热率较低,约为碳钢的1/3,电阻率约为碳钢的5倍,线膨胀系数比碳钢约大50%,密度大于碳钢;由于不锈钢存在众多与碳钢不同的特性,其焊接工艺规范也与碳钢有所不同,对于不锈钢304L钢管(?60×6mm)我们采用的焊丝为ER308L,焊接工艺参数见表2:表2 304L不锈钢的焊接工艺参数注:焊接坡口角度为75±5°2 304L不锈钢焊接工艺特点晶间腐蚀及应对措施晶间腐蚀是在腐蚀介质作用下,起源于金属表面的晶界并且沿晶粒边界深入金属内部产生在晶粒之间的一种腐蚀。
晶间腐蚀是奥氏体不锈钢常见的焊接缺陷。
Cr是奥氏体不锈钢中具用耐腐蚀性的基本元素,当Cr含量低于12%时,就不再具用耐腐蚀性了。
304L不锈钢在焊接过程中存在焊接危险温度区间(为450~850℃),见图1。
当温度达到这一范围时,奥氏体中过饱和的碳向晶界处迅速扩散并在晶粒边界析出,析出的碳和铬形成碳化铬(Cr23C6)。
氩弧焊焊接缺陷产生原因及对策
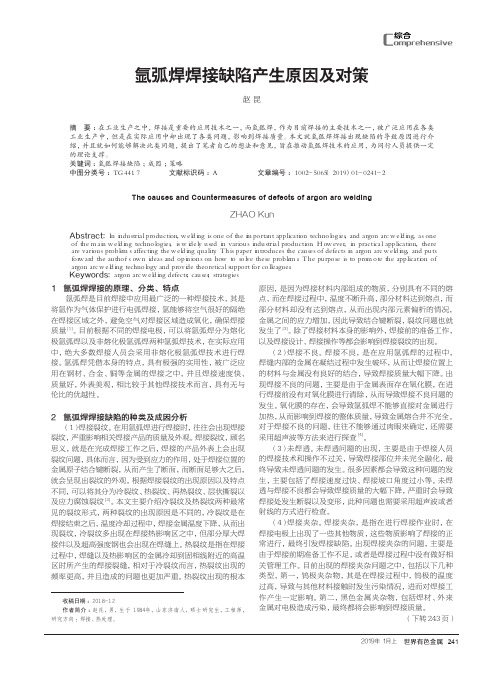
氩弧焊焊接缺陷产生原因及对策赵 昆(中国重型汽车集团有限公司部件制造部,山东 济南 250220)摘 要:在工业生产之中,焊接是重要的应用技术之一,而氩弧焊,作为目前焊接的主要技术之一,被广泛应用在各类工业生产中,但是在实际应用中却出现了各类问题,影响到焊接质量。
本文就氩弧焊焊接出现缺陷的导致原因进行介绍,并且就如何能够解决此类问题,提出了笔者自己的想法和意见,旨在推动氩弧焊技术的应用,为同行人员提供一定的理论支撑。
关键词:氩弧焊接缺陷;成因;策略中图分类号:TG441.7 文献标识码:A 文章编号:1002-5065(2019)01-0241-2The causes and Countermeasures of defects of argon arc weldingZHAO Kun(Manufacturing Department of China National Heavy Duty Truck Group Co., Ltd.,Ji'nan 250220,China)Abstract: In industrial production, welding is one of the important application technologies, and argon arc welding, as one of the main welding technologies, is widely used in various industrial production. However, in practical application, there are various problems affecting the welding quality. This paper introduces the causes of defects in argon arc welding, and puts forward the author's own ideas and opinions on how to solve these problems. The purpose is to promote the application of argon arc welding technology and provide theoretical support for colleagues.Keywords: argon arc welding defects; causes; strategies1氩弧焊焊接的原理、分类、特点氩弧焊是目前焊接中应用最广泛的一种焊接技术,其是将氩作为气体保护进行电弧焊接,氩能够将空气很好的隔绝在焊接区域之外,避免空气对焊接区域造成氧化,确保焊接质量[1]。
浅谈氩弧焊焊接质量缺陷及预控措施

夹钨 、咬边 、焊缝余高不合格 ,夹渣等。
的焊接电流 ,焊接速度 ,尽量使用短弧焊接 。e.检查定位焊的焊接质
2.1焊接气孔 。产生原 因 :焊丝 、母材材 质不 匹配 ;焊接速度 过 量是 否符合标 准。
快 ,焊接 线能量不合适 ;氩气 纯度不够 ;管 口清理 不干净 ,施焊环 境 2.7过热或过烧 。原因 :焊接时 电流过大 ,氩气流量大 ;焊接速度
况 ,对接接头组对情况 ,作业环境 ,焊工的操作技能及对焊接 工艺规 接线 能量小 ,焊速快 ,导致熔池 中溶化 的杂质未浮出而熔 池凝 固。
程执行力 ,责任心都会 直接影响焊接质量 。氩弧焊焊接 中常见 的质 预控措施 :a.焊丝油污清理干净。b.焊件焊接坡 口 20mm表面范
量缺 陷主要有 :焊接气孔 、未熔 合 、未焊透 、裂纹 、过热或过烧 、引弧 围内打磨 清理干净 。c.多层多道焊接时 ,层 间清理干净 。d.选择合适
能量 要合适 ,焊接速度不能过快 。e.氩气纯度锆及 锆合金不应低 于 弧推力。
99.9989,其 它材质不 应低于 99.999,国家 标准(氩 )GBf4842规定 , 2.8引弧夹钨 。原 因 :氩弧焊机未装 引弧装置 (高压脉 冲发 生器
氩气 流量合适 ,保持 与焊 接速度相 匹配。£焊 工在焊接 时需仔细 观 或高频振荡器 )在引弧时经常夹钨 ,造 成钨极损 坏严重 ,在 焊缝 中产
1氩弧焊焊接 的原理 、分类、特点
短弧焊接 ,增加 穿透力 。c.采用 多层焊 的方法 ,第 一层 的焊透焊缝根
氩弧焊是使用氩作为保护气体的一种气体保护 电弧焊技 术 ,就 部为 主。
是在 电弧 焊的周 围通 上氩气作 为保 护气体 ,将空 气隔离在 焊区之 2.5裂纹 。原因 :焊接母材材质不一致 ;焊接环境影响 ;未按设计
高破片用钢氩弧焊接常见缺陷及控制

( )焊接后尽快 ( 5 热影响 区温度 ≥10 0 ̄ C)进
行 去 应 力 回火 ( 5  ̄ ≤2 0C,6 h 。 ~8 )
( )尽量避免焊件表面 的焊接 缺陷和划伤 , 6
合 理控 制 焊缝 的余 高 。
形成粗大马氏体 ,同时释放残余应力。
( )焊 后 热 处 理 因为 冷 裂 纹 与 氢 、 残 余 应 4 力 密 切相 关 ,所 以为 防止 产生 延 迟冷 裂 纹 ,使焊 缝
根据焊材的选用原则 ,由于是异种钢焊接 ,按
弱强 匹 配的 原 则选 用 与 较低 强 度Q3 5 材相 匹配 4 D母
接接头 的含氢量 。 ②高破 片用钢 的碳和合 金元素 含量较 高 ,焊缝 凝 固结 晶时 ,结 晶温 度 区间大 , 偏析倾 向也较大 ,焊接时具 有较 大的热裂 纹敏感
性 。 ③ 高 破 片 用 钢 还 具 有 应 力 腐 蚀 开 裂 敏 感性 。
( )焊前严格 清理 母材、填充材料上污物 , 3
焊接 电流2 0 0 A,保证孔底部四周充分熔合 , 8 ~3 0
厚 度 3 mm,然 后 进 行 填 充焊 和 盖 面 焊 。填 丝 , ~4
( 上接第6页 ) 6 金元素 的熔入 ,中间焊 时为提高生产 效率 ,采 用
GM AW 。
不 得低 于 预 热温 度 。③采 用 短 弧 窄焊 道 焊接 。每 焊 完 一 层用 小锤 击 焊 道表 面 , 目的是 击 碎 晶粒 ,防 止
以下 措施 。
氏体 ( 尤其是高碳粗大马氏体 )组织 ,导致严重脆 化 。②高破片用钢焊接前为调质状态的钢材时 ,热
- 1、下载文档前请自行甄别文档内容的完整性,平台不提供额外的编辑、内容补充、找答案等附加服务。
- 2、"仅部分预览"的文档,不可在线预览部分如存在完整性等问题,可反馈申请退款(可完整预览的文档不适用该条件!)。
- 3、如文档侵犯您的权益,请联系客服反馈,我们会尽快为您处理(人工客服工作时间:9:00-18:30)。
焊接常见缺陷产生原因及措施
1、焊缝截面不饱满或加强高过高。
(焊缝余高)
原因:a、焊接层数选择不当;b、焊接速度选择不当;c、焊接规范选择不当;d、枪头摆动幅度选择不当。
措施:a、选择合适的焊接层数;b、选择合适的焊接速度;c、选择合适的焊接规范;d、选择合适的枪头摆动幅度。
2、焊缝宽窄不均匀。
(焊缝边缘直线度)
原因:a、焊接规范不稳定;b、操作不稳定;c、焊接速度不均匀。
措施:a控制电弧长均匀。
(看好熔合线)
3、咬边(焊缝边缘母材上被电弧烧熔的凹槽称咬边)
原因:a、焊接速度过快;b、焊接电压过高;c、焊接电流过大;d、停顿时间不足;e、焊枪角度选择不当。
措施:a、适当放慢速度;b、降低电压;c、减小电流;d、增加坡口两边停留时间;e、调整焊枪角度以利克服咬边。
4、气孔(焊缝凝固过程中气体来不及溢出而存在焊缝中形成气孔)
原因:a、氩气保护的覆盖率不够;b、氩气纯度不够;c、焊丝被污染了;d 坡口被污染了;e、电压太高,电弧太长;f 、焊丝外伸太长,飞溅大。
措施:a、增大氩气流量,但不能太大否则产生紊流对保护不利,检查防风措施;b、使用合格的氩气,不同的母材使用不同纯度的氩气;c、使用清洁干净的焊丝;d、用物理、化学、机械清理的办法清理坡口及两侧焊接区域的油、水、锈、污物等;e、降低电压,压低电弧。
调整焊丝外伸量。
5、夹渣(钨)电流过大或过小。
6、裂纹(表面裂纹、内部裂纹)
原因:a、接缝结构设计不合理;b、热输入太大;c、坡口太窄(尤其是根部);d、焊缝根部弧坑处的冷却过快;e、坡口内杂质过多,形成低熔共晶物。
措施:a、选择便于焊接的凹槽结构;b、降低电流、电压、适当提高焊速;c、降低焊速,增大焊接截面;d、通过回焊技术,将弧坑填满,消除弧坑;e、清除坡口内杂质。
7、未熔合与未焊透(焊缝与母材未通过电弧融合在一起和不完全焊透)
原因:a、焊缝区有油膜或过量的氧化物;b、坡口热输入不足;c、坡口太宽;d、坡口角度太小e、焊接速度太快。
措施:a、焊接之前,用物理、化学、机械方法除油和氧化物;b、增加电流和电压及降低焊接速度;c、焊枪要均匀摆动,在坡口边做即刻停留,是焊枪直接指向坡口两侧,坡口角度要足够大以便根部焊接;d、降低焊接速度;e、对口间隙要合适。
8、焊瘤(正常焊缝外多余的金属瘤)
原因:焊接速度太慢及电流选择不合适。
措施:提高焊速、选择适当电流。
9、弧坑(收弧处产生的下陷)
原因:收弧时未停留。
措施:收弧时做适当的停留使金属填满弧坑在收弧。
10、电弧擦伤(焊枪与焊件接触,发生短路形成的电弧擦伤,电弧擦伤易形成淬火脆化)
原因:操作不当(引弧不当)
措施:机械打磨处理。
11、过烧
原因:a、焊接线能量太大;b焊接层温太高。
措施:a、降低电流电压、提高焊速;b、降低层温。
(横)
12、焊接飞溅(焊接过程中,金属颗粒飞溅出去,没有形成焊缝的一部分)
原因:电流太高,焊速太快。
措施:降低电流和焊速。
所以焊接完毕后必作自检(也包括焊接过程中)焊接每遍清理。
关于氩弧焊接出现气孔
焊缝附近要清理干净,有油,锈,水,污渍,氧化层,都容易造成气孔,打磨的范围稍微大一些,里面如果有条件也尽量清理氩气质量一定要好,不纯容易出气孔。
焊的速度别太快,走得太快了容易出气孔。
枪要稳,不稳容易漏气进去。
钨极伸出的尽量短些,在你技术能控制的范围内。
最后别忘了后收气。
氩弧焊因采用惰性气体保护,熔池保护方式比较单一,容易受到各种因素的影响从而产生气孔。
它产生的气孔大致为两类:1、因气体保护不好产生的氮气孔,该气孔的特征为密集分布或成蜂窝状;2、因工件或焊丝表面的油、锈等未清理干净产生的H气孔,他的特征是断面为螺钉状,内壁光滑,上大小小呈喇叭口状。
第二种我们很好解决,只要我们做好焊前的清理工作,就可以避免。
第一种气体保护不好的原因很多。
我总结有以下几个方面:
1、气体纯度达不到要求。
在正式焊接之前在清理干净的铁板试焊,不要加丝,如出现气孔则需更换气体。
2、气流量过大,或过小。
气流量的大小应根据喷嘴的大小来调节,一般喷嘴越大,气流量越大。
3、气体紊流。
当喷嘴内有飞溅物,或钨极夹头膨胀。
4、气管破损。
当气管破损时,在焊接起弧或起弧不久产生气孔时就会出现气孔,之后又会恢复到正常。
5、环境气流过大。
一般当风速达到3m/s以上是容易吹散保护气体。
6、喷嘴的直径过大,或过小。
7、钨极的伸出长度。
一般为钨极直径的2~3倍。