焊接缺陷产生原因及防止措施
常见焊接缺陷产生原因及防止措施
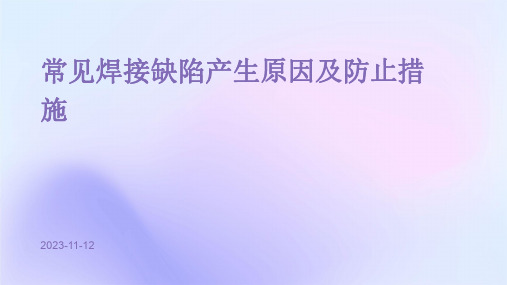
2023-11-12•焊接缺陷概述•常见焊接缺陷产生原因•焊接缺陷防止措施•焊接缺陷实例分析•焊接缺陷的检测方法与工具目录01焊接缺陷概述焊缝尺寸不符合要求焊缝宽度、高度、平整度等不符合设计要求,影响焊接质量和强度。
气孔焊接过程中熔融金属内产生的气泡未被充分排除,在焊缝表面形成气孔。
未焊透焊接过程中未能完全熔透金属,导致焊接接头强度降低。
未熔合焊接过程中焊缝金属与母材之间未能完全熔合,影响焊接接头强度。
夹渣焊接过程中熔渣残留在焊缝中,降低焊接质量。
咬边焊接过程中母材边缘被电弧烧蚀,形成的凹陷或沟槽。
焊接缺陷的类型降低焊接接头的强度和致密性,影响设备的安全运行和使用寿命。
引起应力集中,增加焊接接头的脆性,降低其抗冲击性能。
影响设备的外观质量,增加维修成本。
焊接缺陷的影响02常见焊接缺陷产生原因金属表面有水分、锈迹、油污等杂质,在焊接高温下形成气孔。
焊接前未将焊缝周围的杂质清理干净,导致焊接时气体被包裹在焊缝中。
焊接速度过快,气体未完全排出。
焊接操作不当,如电弧过长、电流过大等,导致气体进入焊缝。
焊接材料中存在杂质,如碳、硫、磷等元素含量过高,导致焊缝韧性不足,产生裂纹。
结构设计不合理,焊缝承受的应力过大,导致裂纹产生。
焊接过程中温度过高或冷却速度过快,导致焊缝热影响区产生裂纹。
焊接操作不当,如电弧过长、电流过大等,导致焊缝金属过热,产生裂纹。
夹渣焊接前未将焊缝周围的杂质清理干净,导致焊接时杂质被包裹在焊缝中。
焊接材料质量不好,含有杂质,导致焊缝中夹渣。
焊接速度过快,气体未完全排出,导致焊缝中夹渣。
焊接操作不当,如电流过小、电弧过长等,导致焊缝金属熔化不均匀,产生夹渣。
未焊透焊接速度过快,导致焊缝未完全熔合。
焊接材料质量不好,含有杂质,导致熔合不完全。
焊接电流过小,导致焊缝金属熔化不均匀。
焊缝角度不正确,导致熔合不完全。
焊接速度过快,导致焊缝未完全熔合。
焊缝角度不正确,导致熔合不完全。
焊接材料质量不好,含有杂质,导致熔合不完全。
史上最全!!常见焊接缺陷产生原因、危害及防止措施
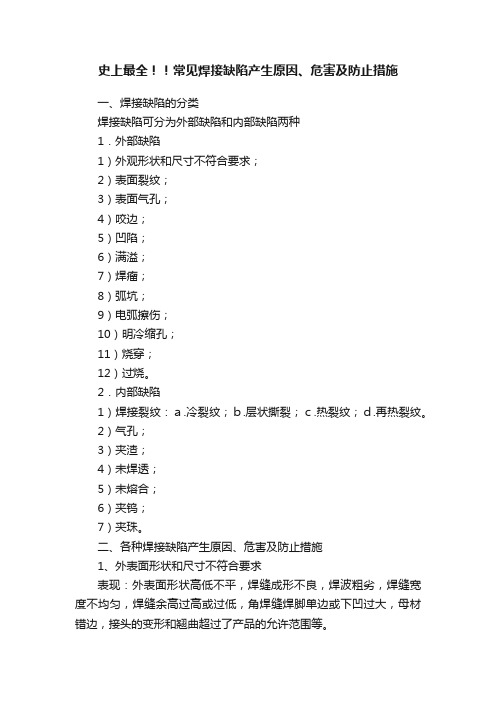
史上最全!!常见焊接缺陷产生原因、危害及防止措施一、焊接缺陷的分类焊接缺陷可分为外部缺陷和内部缺陷两种1.外部缺陷1)外观形状和尺寸不符合要求;2)表面裂纹;3)表面气孔;4)咬边;5)凹陷;6)满溢;7)焊瘤;8)弧坑;9)电弧擦伤;10)明冷缩孔;11)烧穿;12)过烧。
2.内部缺陷1)焊接裂纹:a.冷裂纹;b.层状撕裂;c.热裂纹;d.再热裂纹。
2)气孔;3)夹渣;4)未焊透;5)未熔合;6)夹钨;7)夹珠。
二、各种焊接缺陷产生原因、危害及防止措施1、外表面形状和尺寸不符合要求表现:外表面形状高低不平,焊缝成形不良,焊波粗劣,焊缝宽度不均匀,焊缝余高过高或过低,角焊缝焊脚单边或下凹过大,母材错边,接头的变形和翘曲超过了产品的允许范围等。
危害:焊缝成形不美观,影响到焊材与母材的结合,削弱焊接接头的强度性能,使接头的应力产生偏向和不均匀分布,造成应力集中,影响焊接结构的安全使用。
产生原因:焊件坡口角度不对,装配间隙不匀,点固焊时未对正,焊接电流过大或过小,运条速度过快或过慢,焊条的角度选择不合适或改变不当,埋弧焊焊接工艺选择不正确等。
防止措施:选择合适的坡口角度,按标准要求点焊组装焊件,并保持间隙均匀,编制合理的焊接工艺流程,控制变形和翘曲,正确选用焊接电流,合适地掌握焊接速度,采用恰当的运条手法和角度,随时注意适应焊件的坡口变化,以保证焊缝外观成形均匀一致。
2、焊接裂纹表现:在焊接应力及其他致脆因素共同作用下,焊接接头中局部地区的金属原子结合力遭到破坏形成的新界面所产生的缝隙,具有尖锐的缺口和大小的长宽比特征。
按形态可分为:纵向裂纹、横向裂纹、弧坑裂纹、焊趾裂纹、焊根裂纹、热影响区再热裂纹等。
危害:裂纹是所有的焊接缺陷里危害最严重的一种。
它的存在是导致焊接结构失效的最直接的因素,特别是在锅炉压力容器的焊接接头中,因为它的存在可能导致一场场灾难性的事故的发生,裂纹最大的一个特征是具有扩展性,在一定的工作条件下会不断的“生长”,直至断裂。
焊接的六大缺陷及其产生原因、危害、预防措施

焊接的六大缺陷及其产生原因、危害、预防措施一、外观缺陷外观缺陷(表面缺陷)是指不用借助于仪器,从工件表面可以发现的缺陷。
常见的外观缺陷有咬边、焊瘤、凹陷及焊接变形等,有时还有表面气孔和表面裂纹。
单面焊的根部未焊透等。
A、咬边是指沿着焊趾,在母材部份形成的凹陷或者沟槽,它是由于电弧将焊缝边缘的母材熔化后没有得到熔敷金属的充分补充所留下的缺口。
产生咬边的主要原因:是电弧热量太高,即电流太大,运条速度太小所造成的。
焊条与工件间角度不正确,摆动不合理,电弧过长,焊接次序不合理等都会造成咬边。
直流焊时电弧的磁偏吹也是产生咬边的一个原因。
某些焊接位置( 立、横、仰 )会加剧咬边。
咬边减小了母材的有效截面积,降低构造的承载能力,同时还会造成应力集中,发展为裂纹源。
咬边的预防:矫正操作姿式,选用合理的规范,采用良好的运条方式都会有利于消除咬边。
焊角焊缝时,用交流焊代替直流焊也能有效地防止咬边。
B、焊瘤焊缝中的液态金属流到加热缺陷未熔化的母材上或者从焊缝根部溢出,冷却后形成的未与母材熔合的金属瘤即为焊瘤。
焊接规范过强、焊条熔化过快、焊条质量欠佳(如偏芯),焊接电源特性不稳定及操作姿式不当等都容易带来焊瘤。
在横、立、仰位置更易形成焊瘤。
焊瘤常伴有未熔合、夹渣缺陷,易导致裂纹。
同时,焊瘤改变了焊缝的实际尺寸,会带来应力集中。
管子内部的焊瘤减小了它的内径,可能造成流动物阻塞。
防止焊瘤的措施:使焊缝处于平焊位置,正确选用规范,选用无偏芯焊条,合理操作。
C、凹坑凹坑指焊缝表面或者反面局部的低于母材的部份。
凹坑多是由于收弧时焊条(焊丝)未作短期停留造成的(此时的凹坑称为弧坑),仰立、横焊时,常在焊缝反面根部产生内凹。
凹坑减小了焊缝的有效截面积,弧坑常带有弧坑裂纹和弧坑缩孔。
防止凹坑的措施:选用有电流衰减系统的焊机,尽量选用平焊位置,选用合适的焊接规范,收弧时让焊条在熔池内短期停留或者环形摆动,填满弧坑。
D、未焊满未焊满是指焊缝表面上连续的或者断续的沟槽。
常见焊接缺陷及防止措施
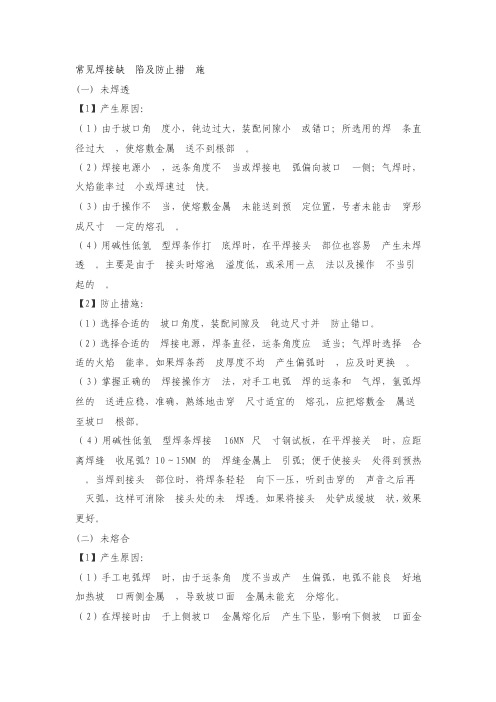
常见焊接缺陷及防止措施(一) 未焊透【1】产生原因:(1)由于坡口角度小,钝边过大,装配间隙小或错口;所选用的焊条直径过大,使熔敷金属送不到根部。
(2)焊接电源小,远条角度不当或焊接电弧偏向坡口一侧;气焊时,火焰能率过小或焊速过快。
(3)由于操作不当,使熔敷金属未能送到预定位臵,号者未能击穿形成尺寸一定的熔孔。
(4)用碱性低氢型焊条作打底焊时,在平焊接头部位也容易产生未焊透。
主要是由于接头时熔池溢度低,或采用一点法以及操作不当引起的。
【2】防止措施:(1)选择合适的坡口角度,装配间隙及钝边尺寸并防止错口。
(2)选择合适的焊接电源,焊条直径,运条角度应适当;气焊时选择合适的火焰能率。
如果焊条药皮厚度不均产生偏弧时,应及时更换。
(3)掌握正确的焊接操作方法,对手工电弧焊的运条和气焊,氩弧焊丝的送进应稳,准确,熟练地击穿尺寸适宜的熔孔,应把熔敷金属送至坡口根部。
(4)用碱性低氢型焊条焊接16MN尺寸钢试板,在平焊接关时,应距离焊缝收尾弧?10~15MM的焊缝金属上引弧;便于使接头处得到预热。
当焊到接头部位时,将焊条轻轻向下一压,听到击穿的声音之后再灭弧,这样可消除接头处的未焊透。
如果将接头处铲成缓坡状,效果更好。
(二) 未熔合【1】产生原因:(1)手工电弧焊时,由于运条角度不当或产生偏弧,电弧不能良好地加热坡口两侧金属,导致坡口面金属未能充分熔化。
(2)在焊接时由于上侧坡口金属熔化后产生下坠,影响下侧坡口面金属的加热熔化,造成“冷接”。
(3)横接操作时,在上、下坡口面击穿顺序不对,未能先击穿下坡口后击穿上坡口,或者在上、下坡口面上击穿熔孔位臵未能错开一定的距离,使上坡口熔化金属下坠产生粘接,造成未熔合。
(4)气悍时火焰能率小,氩弧焊时电弧两侧坡口的加热不均,或者坡口面存在污物等。
焊接常见缺陷产生的原因及其预防措施
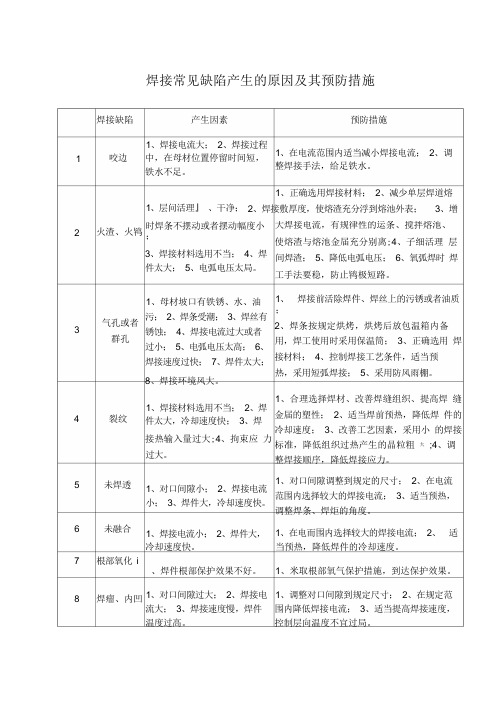
焊接常见缺陷产生的原因及其预防措施1 2 3 45 6 7 8 焊接缺陷咬边火渣、火鸨气孔或者群孔裂纹未焊透未融合根部氧化i焊瘤、内凹产生因素1、焊接电流大;2、焊接过程中,在母材位置停留时间短,铁水不足。
预防措施1、在电流范围内适当减小焊接电流;2、调整焊接手法,给足铁水。
1、正确选用焊接材料;2、减少单层焊道熔1、层问活理』、干净;2、焊接敷厚度,使熔渣充分浮到熔池外表;3、增时焊条不摆动或者摆动幅度小;3、焊接材料选用不当;4、焊件太大;5、电弧电压太局。
1、母材坡口有铁锈、水、油污;2、焊条受潮;3、焊丝有锈蚀;4、焊接电流过大或者过小;5、电弧电压太高;6、焊接速度过快;7、焊件太大;8、焊接环境风大。
1、焊接材料选用不当;2、焊件太大,冷却速度快;3、焊接热输入量过大;4、拘束应力过大。
1、对口间隙小;2、焊接电流小;3、焊件大,冷却速度快。
1、焊接电流小;2、焊件大,冷却速度快。
、焊件根部保护效果不好。
1、对口间隙过大;2、焊接电流大;3、焊接速度慢,焊件温度过高。
大焊接电流,有规律性的运条、搅拌熔池、使熔渣与熔池金届充分别离;4、子细活理层间焊渣;5、降低电弧电压;6、氧弧焊时焊工手法要稳,防止鸨极短路。
1、焊接前活除焊件、焊丝上的污锈或者油质;2、焊条按规定烘烤,烘烤后放包温箱内备用,焊工使用时采用保温筒;3、正确选用焊接材料;4、控制焊接工艺条件,适当预热,采用短弧焊接;5、采用防风雨棚。
1、合理选择焊材、改善焊缝组织、提高焊缝金届的塑性;2、适当焊前预热,降低焊件的冷却速度;3、改善工艺因素,采用小的焊接标准,降低组织过热产生的晶粒粗大;4、调整焊接顺序,降低焊接应力。
1、对口间隙调整到规定的尺寸;2、在电流范围内选择较大的焊接电流;3、适当预热,调整焊条、焊炬的角度。
1、在电而围内选择较大的焊接电流;2、适当预热,降低焊件的冷却速度。
1、米取根部氧气保护措施,到达保护效果。
常见焊接缺陷产生原因及防止措施
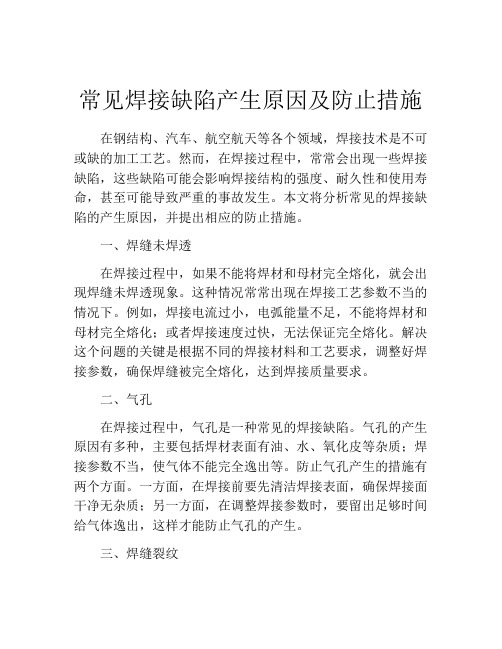
常见焊接缺陷产生原因及防止措施在钢结构、汽车、航空航天等各个领域,焊接技术是不可或缺的加工工艺。
然而,在焊接过程中,常常会出现一些焊接缺陷,这些缺陷可能会影响焊接结构的强度、耐久性和使用寿命,甚至可能导致严重的事故发生。
本文将分析常见的焊接缺陷的产生原因,并提出相应的防止措施。
一、焊缝未焊透在焊接过程中,如果不能将焊材和母材完全熔化,就会出现焊缝未焊透现象。
这种情况常常出现在焊接工艺参数不当的情况下。
例如,焊接电流过小,电弧能量不足,不能将焊材和母材完全熔化;或者焊接速度过快,无法保证完全熔化。
解决这个问题的关键是根据不同的焊接材料和工艺要求,调整好焊接参数,确保焊缝被完全熔化,达到焊接质量要求。
二、气孔在焊接过程中,气孔是一种常见的焊接缺陷。
气孔的产生原因有多种,主要包括焊材表面有油、水、氧化皮等杂质;焊接参数不当,使气体不能完全逸出等。
防止气孔产生的措施有两个方面。
一方面,在焊接前要先清洁焊接表面,确保焊接面干净无杂质;另一方面,在调整焊接参数时,要留出足够时间给气体逸出,这样才能防止气孔的产生。
三、焊缝裂纹焊缝裂纹是一种比较危险的焊接缺陷。
它常常由以下原因引起:焊接材料的拉伸强度不均,焊接接头部位过于脆弱,或者是焊接温度过高、冷却过快等。
为了防止焊缝裂纹的产生,可以采取以下措施。
一是控制焊接参数,避免过高的焊接温度和过快的冷却速度。
二是在焊接过程中,注意焊接的连续性,确保焊接成形完整。
三是在焊接过程中,采用预热的方法,改善焊接材料的拉伸强度,避免裂纹的出现。
四、过度熔深焊接过度熔深是由于焊接材料熔化过度,穿过母材嵌入焊接面内,使得焊缝结构松散,焊接强度降低。
过度熔深的原因有多种,如焊接电流过大,焊接速度过慢等。
预防过度熔深可以通过调整焊接参数、控制熔化深度和焊接速度等措施实现。
总之,焊接缺陷的产生原因可能有很多,需要针对具体情况采取相应的防止措施。
这需要焊接工艺人员有丰富的焊接经验和专业知识,对焊接材料和工艺有深入的了解,才能确保焊接质量达到要求。
焊接质量缺陷原因分析及预防、治理措施
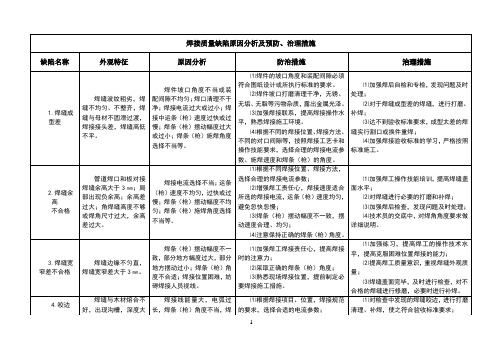
⑷根据自己的操作技能,选择合适的线能量、焊接速度和操作手法。
厚度符合标准要求;
⑵加强打底练习,熟练掌握操作手法以及对应的焊接线能量及焊接速度等。
18.管道焊口根部焊瘤、凸出、凹陷
⑷注意周围焊接施工环境,搭设防风设施,管子焊接无穿堂风;
⑸氩弧焊时,氩气纯度不低于%,氩气流量合适;
⑹尽量采用短弧焊接,减少气体进入熔池的机会;
⑺焊工操作手法合理,焊条、焊枪角度合适;
⑻焊接线能量合适,焊接速度不能过快;
⑼按照工艺要求进行焊件预热。
⑴严格按照预防措施执行;
⑵加强焊工练习,提高操作水平和责任心;
⑴严格按照规程和作业指导书的要求准备各种焊接条件;
⑵提高焊接操作技能,熟练掌握使用的焊接方法;
⑶采取合理的焊接顺序等措施,减少焊接应力等。
⑴针对每种产生裂纹的具体原因采取相应的对策;
⑵对已经产生裂纹的焊接接头,采取挖补措施处理。
11.焊缝表面不清理或清理不干净,电弧擦伤焊件
焊缝焊接完毕,焊接接头表面药皮、飞溅物不清理或清理不干净,留有药皮或飞溅物;焊接施工过程中不注意,电弧擦伤管壁等焊件造成弧疤。
⑶发现问题及时采取必要措施。
14.气孔
在焊缝中出现的单个、条状或群体气孔,是焊缝内部最常见的缺陷。
根本原因是焊接过程中,焊接本身产生的气体或外部气体进入熔池,在熔池凝固前没有来得及溢出熔池而残留在焊缝中。
⑴焊条要求进行烘培,装在保温筒内,随用随取;
⑵焊丝清理干净,无油污等杂质;
⑶焊件周围10~15㎜范围内清理干净,直至发出金属光泽;
⑴焊件的坡口角度和装配间隙必须符合图纸设计或所执行标准的要求。
焊接内部缺陷原因分析及预防措施
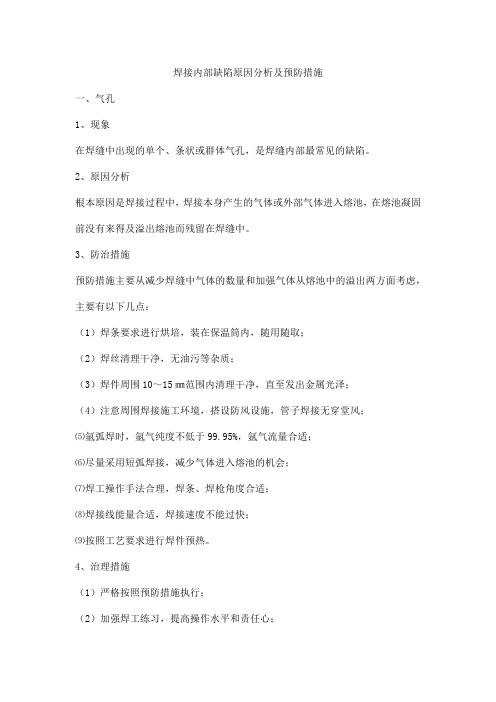
焊接内部缺陷原因分析及预防措施一、气孔1、现象在焊缝中出现的单个、条状或群体气孔,是焊缝内部最常见的缺陷。
2、原因分析根本原因是焊接过程中,焊接本身产生的气体或外部气体进入熔池,在熔池凝固前没有来得及溢出熔池而残留在焊缝中。
3、防治措施预防措施主要从减少焊缝中气体的数量和加强气体从熔池中的溢出两方面考虑,主要有以下几点:(1)焊条要求进行烘培,装在保温筒内,随用随取;(2)焊丝清理干净,无油污等杂质;(3)焊件周围10~15㎜范围内清理干净,直至发出金属光泽;(4)注意周围焊接施工环境,搭设防风设施,管子焊接无穿堂风;⑸氩弧焊时,氩气纯度不低于99.95%,氩气流量合适;⑹尽量采用短弧焊接,减少气体进入熔池的机会;⑺焊工操作手法合理,焊条、焊枪角度合适;⑻焊接线能量合适,焊接速度不能过快;⑼按照工艺要求进行焊件预热。
4、治理措施(1)严格按照预防措施执行;(2)加强焊工练习,提高操作水平和责任心;(3)对在探伤过程中发现的超标气孔,采取挖补措施。
二、夹渣1、现象焊接过程中药皮等杂质夹杂在熔池中,熔池凝固后形成的焊缝中的夹杂物。
2、原因分析(1)焊件清理不干净、多层多道焊层间药皮清理不干净、焊接过程中药皮脱落在熔池中等;(2)电弧过长、焊接角度部队、焊层过厚、焊接线能量小、焊速快等,导致熔池中熔化的杂质未浮出而熔池凝固。
3、防治措施(1)焊件焊缝破口周围10~15㎜表面范围内打磨清理干净,直至发出金属光泽;(2)多层多道焊时,层间药皮清理干净;(3)焊条按照要求烘培,不使用偏芯、受潮等不合格焊条;(4)尽量使用短弧焊接,选择合适的电流参数;⑸焊接速度合适,不能过快。
4、治理措施(1)焊前彻底清理干净焊件表面;(2)加强练习,焊接操作技能娴熟,责任心强;(3)对探伤过程中发现的夹渣超标缺陷,采取挖补等措施处理。
三、未熔合1、现象未熔合主要时根部未熔合、层间未熔合两种。
根部未熔合主要是打底过程中焊缝金属与母材金属以及焊接接头未熔合;层间未熔合主要是多层多道焊接过程中层与层间的焊缝金属未熔合。
- 1、下载文档前请自行甄别文档内容的完整性,平台不提供额外的编辑、内容补充、找答案等附加服务。
- 2、"仅部分预览"的文档,不可在线预览部分如存在完整性等问题,可反馈申请退款(可完整预览的文档不适用该条件!)。
- 3、如文档侵犯您的权益,请联系客服反馈,我们会尽快为您处理(人工客服工作时间:9:00-18:30)。
焊接缺陷产生原因及防止措施
焊接接头的不完整性称为焊接缺陷,主要有焊接裂纹、未焊透、夹渣、气孔和焊缝外观缺陷等。
这些缺陷减少焊缝截面积,降低承载能力,产生应力集中,引起裂纹;降低疲劳强度,易引起焊件破裂导致脆断。
一缺陷名称:气孔(Blow Hole)
二缺陷名称咬边(Undercut)
三缺陷名称:夹渣(Slag Inclusion)
焊接方式发生原因防止措施
手工电弧焊(1)前层焊渣未完全清除.
(2)焊接电流太低.
(3)焊接速度太慢.
(4)焊条摆动过宽.
(5)焊缝组合及设计不良.
(1)彻底清除前层焊渣.
(2)采用较高电流.
(3)提高焊接速度.
(4)减少焊条摆动宽度.
(5)改正适当坡口角度及间隙.
CO2气体电弧焊(1)母材倾斜(下坡)使焊渣超
前.
(2)前一道焊接后,焊渣未清洁
干净.
(3)电流过小,速度慢,焊着量
多.
(4)用前进法焊接,开槽内焊渣
超前甚多.
(1)尽可能将焊件放置水平位置.
(2)注意每道焊道之清洁.
(3)增加电流和焊速,使焊渣容易浮起.
(4)提高焊接速度
埋弧焊接(1)焊接方向朝母材倾斜方向,
因此焊渣流动超前.
(2)多层焊接时,开槽面受焊丝
溶入,焊丝过于靠近开槽的侧
边.
(3)在焊接起点有导板处易产
生夹渣.
(4)电流过小,第二层间有焊渣
留存,在焊接薄板时容易产生
裂纹.
(5)焊接速度过低,使焊渣超前.
(6)最后完成层电弧电压过高,
使得游离焊渣在焊道端头产
生搅卷.
(1)焊接改向相反方向焊接,或将母材
尽可能改成水平方向焊接.
(2)开槽侧面和焊丝之间距离,最少要
大于焊丝直径以上.
(3)导板厚度及开槽形状,需与母材相
同.
(4)提高焊接电流,使残留焊渣容易熔
化.
(5)增加焊接电流及焊接速度.
(6)减小电压或提高焊速,必要时盖面
层由单道焊改为多道焊接.
自保护药芯焊丝(1)电弧电压过低.
(2)焊丝摆弧不当.
(3)焊丝伸出过长.
(4)电流过低,焊接速度过慢.
(5)第一道焊渣,未充分清除.
(6)第一道结合不良.
(7)坡口太狭窄.
(1)调整适当.
(2)加多练习.
(3)依各种焊丝使用说明.
(4)调整焊接参数.
(5)完全清除
(6)使用适当电压,注意摆弧.
(7)改正适当坡口角度及间隙.
四缺陷名称:未焊透(Incomplete Penetration)
五缺陷名称:裂纹(Crack)
手工电弧焊(1)焊件含有过高的碳、锰等合
金元素.
(2)焊条品质不良或潮湿.
(3)焊缝拘束应力过大.
(4)母条材质含硫过高不适于
焊接.
(5)施工准备不足.
(6)母材厚度较大,冷却过速.
(7)电流太强.
(8)首道焊道不足抵抗收缩应
力.
(1)使用低氢系焊条.
(2)使用适宜焊条,并注意干燥.
(3)改良结构设计,注意焊接顺序,焊
接后进行热处理.
(4)避免使用不良钢材.
(5)焊接时需考虑预热或后热.
(6)预热母材,焊后缓冷.
(7)使用适当电流.
(8)首道焊接之焊着金属须充分抵抗
收缩应力.
CO2气体保护焊(1)开槽角度过小,在大电流焊
接时,产生梨形和焊道裂纹.
(2)母材含碳量和其它合金量
过高(焊道及热影区).
(3)多层焊接时,第一层焊道过
小.
(4)焊接顺序不当,产生拘束力
过强.
(5)焊丝潮湿,氢气侵入焊道.
(6)套板密接不良,形成高低不
平,致应力集中.
(7)因第一层焊接量过多,冷却
缓慢(不锈钢,铝合金等).
(1)注意适当开槽角度与电流的配合,
必要时要加大开槽角度.
(2)采用含碳量低的焊条.
(3)第一道焊着金属须充分能抵抗收
缩应力.
(4)改良结构设计,注意焊接顺序,焊
后进行热处理.
(5)注意焊丝保存.
(6)注意焊件组合之精度.
(7)注意正确的电流及焊接速度.
埋弧焊接(1)对焊缝母材所用的焊丝和
焊剂之配合不适当(母材含碳
量过大,焊丝金属含锰量太
少).
(2)焊道急速冷却,使热影响区
发生硬化.
(3)焊丝含碳、硫量过大.
(4)在多层焊接之第一层所生
焊道力,不足抵抗收缩应力.
(5)在角焊时过深的渗透或偏
析.
(6)焊接施工顺序不正确,母材
(1)使用含锰量较高的焊丝,在母材含
碳量多时,要有预热之措施.
(2)焊接电流及电压需增加,焊接速度
降低,母材需加热措施.
(3)更换焊丝.
(4)第一层焊道之焊着金属须充分抵
抗收缩应力.
(5)将焊接电流及焊接速度减低,改变
极性.
(6)注意规定的施工方法,并予焊接操
作施工指导.
(7)焊道宽度与深度的比例约为1:1:
六缺陷名称:变形(Distortion)
七其他缺陷
-焊穿-
-搭叠-
-焊道蛇形-。