塑料异型材挤出工艺流程介绍
塑料异型材挤出工艺流程介绍

塑料异型材产品工艺流程介绍一、工艺流程PVC →各种助剂→高速搅拌捏合→挤出→冷却真空定型→牵引→定长切割→成品→检验→包装入库二、主要设备1、主机:车间大部分机台使用的为SJZ65/132型双螺杆挤出机,长径比:1∶22 ,螺杆转速7r/ min~48r/ min ,螺杆的旋转方向: 异向向外旋转。
2、辅机:(1) 冷却定型装置:,由气水分流器、活动台板、调整机构组成。
真空冷却段数:4 段,水环真空泵电机功率:10kW。
(2) 牵引装置:大平面橡胶带牵引。
(3) 锯切装置:配有计长装置,能跟踪切割的气动式锯切机。
(4) 堆放装置:气动式可翻转托架。
三、生产工艺要点型材的挤出成型是利用螺杆旋转加压方式,连续地将塑化好的成型物料从挤出机料筒中挤入机头,熔融物料通过机头口模成型为与口模形状相仿的型坯,用牵引装置将成型制品连续地从模具中拉出,同时冷却定型,制得所需形状的制品。
要获得外观与内在质量均优良的型材制品,需要对挤出工艺条件进行控制,控制要点主要为混料、成型温度、螺杆冷却与转速、挤出压力、冷却定型等。
混料混料过程先将PVC 树脂以及配方计量加入其它组份加入到热混机,高速搅拌升温到120℃进行混合,混合均匀后,放到冷混机中边混料边冷却至45℃,形成松散、易流动的粉状混合物,然后出料备用。
混料时温度控制很重要,混合温度过高,物料易发粘、结块、塑化不均;混合温度过低,则物料混合不充分,达不到预塑目的。
所以一般情况下,高温混合终点温度控制在(115~120) ℃,高混时间10min~15min ,冷混出料温度45 ℃。
挤出成型温度生产产品选用的是有排气装置的异向向外旋转的双螺杆挤出机。
挤出机经过预热、加料之后通过输送、排气、熔化等过程,将物料均匀塑化形成熔体,到达机头后进一步均化,通过机头压力,压实成型为密实的型坯,以流动状态连续通过口模成型。
挤出成型温度是促使成型物料塑化和熔体流动的必要条件,它对挤出成型过程中物料塑化、型材制品的质量和产量均有十分重要的影响。
PVC型材挤出工艺
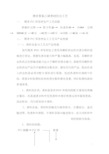
硬质聚氯乙烯型材挤出工艺一、硬质PVC异型材生产工艺流程原辅料过筛配方称量高速热混冷混过筛储料风送挤出定型牵引检验入库二、硬质PVC异型材加工工艺及产品性能(一)、混料设备与工艺及产品性能现代硬质PVC异型材加工使用双螺杆挤出机对混合粉料直接进行挤出,其塑化混合能力和产量大幅提高。
但是,双螺杆挤出机的正位移输送能力远大于螺杆的混合能力,直接用双螺杆挤出机挤出产品仍不能得到分散良好、塑化均匀的产品,因此在进入挤出机前必须对配方原料进行预混,包括热混和冷混两个阶段,使混合料取得较好的的预分散和塑化效果,同时取得较高的表观密度。
1、混料的目的:混料就是将PVC和助剂按配方要求经准确计量后,在高速混合机中经热混和冷混后使其达到半凝胶度高,流动性好,均匀密实的干混料。
2、混料设备:原材料的输送与储存部分、计量部分、盒式输送带,热混和冷混锅、干混料存储与输送部分、动力风机和中央控制部分组成。
3、混料的流程:PVC储罐 PVC秤群青辅料罐热混冷混缓冲罐筛分机辅料秤干混料罐微料罐中间仓4、混料工艺:混料过程中一方面是助剂的均匀分散,另一方面则是使树脂半凝胶化,凝胶化:PVC树脂即有颗粒细化,粒径均匀的形态变化,形成松散的粉料。
它的工艺控制点、加料量、冷却水温度、混料温度和时间等是控制干混料质量和产量的关键因素。
A、加料量与升温速度有一定的关系,即热混机中物料的热量只是搅拌叶片剪切和物料之间产生产热量。
所以投料量有一个的最佳值,如果加料量太多,物料翻腾阻力大影响升温速度,致使转速下降,给混料带来不利。
加料量少内部剪切热达不到,混料时间长直接影响混料效率。
经实验控制在70%左右为最佳。
B、混料温度:混料温度的影响干粉料性能的主要因素之一。
热混温度在一般为120℃左右冷混卸料温度一般低于40℃。
原料的含水量必须合乎优质品的要求,并应通过排气以除去物料中的水分。
C、冷却水温度:冷混缸的冷却水温度通常控制在13~15℃。
挤出成型工艺—挤出成型原理(塑料成型加工课件)
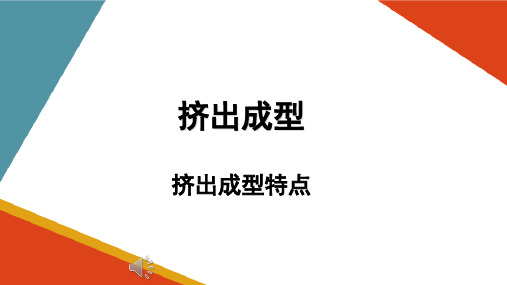
二、挤出成型过程
既有混合过 程,也有成 型过程
树脂原料 加热黏流 塑料熔体
助剂
混合过程
加压 挤出连续体
一定规格的 制品
切割 成型连续体
冷却定型
成型过程
以 管 材 挤 出 原料 成型为例
挤出连续体
熔体
定型连续体
制品
三、挤出成型特点
1. 可以连续化生产,生产效率高。 2. 设备自动化程度高,劳动强度低。 3. 生产操作简单,工艺控制容易。 4. 原料适应性强,适用大多数热塑性树脂和少数热固性 树脂。 5. 可生产的产品广泛,同一台挤出机,只要更换不同的 辅机,就可以生产不同的制品。
挤出成型
挤出成型特点
一、挤出成概述
挤出成型又叫挤出模塑,是利用加热使塑料熔融塑化成 为流动状态,然后在机械力(螺杆或柱塞的挤压)的作用下, 使熔融塑料通过一定形状的口模制成具有恒定截面连续的制 品,适用于绝大部分热塑性树脂和部分热固性树脂。
除了用于挤出造粒、染色、树脂掺和等共混改性,还可用于塑 料薄膜、网材、带包覆层的产品、截面一定、长度连续的管材、板 材、片材、棒材、打包带、单丝和异型材等塑料制品的生产。
料表面接近或达到黏流温度,表面发黏。
要求:输送能力要稍高于熔融段和均化段。
2. 压缩段 (熔融段)
位置:螺杆中部一段。 作用:输送物料,使物料受到热和剪切作用熔 融塑化,并进一步压实和排出气体。 特点:物料逐渐由玻璃态转变为粘流态,在熔 融段末端物料为粘流态。 要求:螺杆结构逐渐紧密,使物料进一步压实。
(3)横流(环流) 由垂直于螺棱方向的分速
度引起的使物料在螺槽内产生翻 转运动。对生产能力没有影响, 但能促进物料的混合和热交换。
(4)漏流 由机筒与螺棱间隙处形成的
异型材挤出成型—异型材成型辅机(塑料挤出成型课件)

异型材机头分类
异型材机头分类
思考:板式机头和流线型机头各自优缺点?
1. 板式机头
• 特点:结构简单,成本低,口模更换容易,适合多品种、小批量生产 • 缺点:横截面急剧变化,易形成局部滞料和死角,型材尺寸准确性不高 • 适用:聚烯烃,软聚氯乙烯的生产
2.流线型机头
• 设计要求:机头内流道必须为圆形过渡,各处不得有急剧过渡或死角。 • 特点:能克服流道急剧变化,保证挤出成型质量,适合大批量生产。
为什么?
滚轮式牵引装置
1一型材;2一主动轮;3一调节杆;4一手轮; 5一从动轮
由2~5对上下牵引滚轮组成。滚轮和型材之间面或线接触,牵引力小,只适用于 小型异型材制品的生产。要注意滚轮的形状尺寸应与异型材的形状和尺寸相适应。
由二条或二条以上的履带组成。由于牵 引履带与型材的接触面积大,牵引力也 较大,且不易打滑,特别适用于薄壁或 型材尺寸较大的制楞板时,预先挤出的板材 经波纹形辊筒压成粗波纹,接着通 过上图所示的滑移式定型模,冷却 定型成为所要求的波纹板。
将从平缝模挤出的板材在滑移式 定型模中折弯成需要的截面形状,冷 却定型。此法能用简单的模具制造出 复杂的大型异型材。
定型方法
3. 真空(外)定型
1. 特点:由于采用间接水冷方式,有效抑制了内应力和形变。 2. 方法:定型模周围壁上的细孔或缝口抽真空产生负压区,使型材的外壁与真空
牵引装置
牵引、切割装置
• 作用:克服型材在定型模内的摩擦阻力而均匀地牵引型 材,使挤出过程稳定进行。
• 由于异型材形状复杂,有效面积上摩擦阻力大,要求牵 引力也较大,同时为保证型材壁厚、尺寸公差、性能及 外观要求,必须使型材挤出速度和牵引速度匹配。
• 异型材挤出常用牵引机有辊轮式、履带式和皮带式三种。
硬PVC门窗异型材挤出成型工艺

硬PVC门窗异型材挤出成型工艺一、生产工艺流程硬PVC门窗异型材的生产工艺路线主要有单螺杆挤出成型工艺和双螺杆挤出成型工艺两种,而两种工艺挤出用的原料都是前道工序按一定配方配好的混合粉料。
目前,硬PVC 门窗异型材的挤出大多采用锥形螺杆挤出生产线。
(一)单螺杆挤出成型单螺杆挤出成型工艺特别适用于小批量、小规格异型材的生产。
其工艺流程如下:混合粉料→单螺杆挤出造粒→单螺杆挤出成型→定型→牵引→切割→翻转台→成品(二)双螺杆挤出成型双螺杆挤出成型工艺可用粉料直接成型,生产能力大,特别适用于大批量常规型材和大规格异型材的生产。
其工艺流程如下:混合粉料→双螺杆挤出成型→定型→牵引→切割→翻转台→成品二、双螺杆挤出机挤出硬PVC门窗异型材工艺控制要点硬PVC门窗异型材的挤出过程可简述如下:改性PVC混合料在机筒内经过螺杆混炼,在内磨擦热和电加热的作用下,物料逐渐变成熔融粘流态,物料在旋转螺杆的流动下向机头方向螺旋运动。
进入机头模具后,在高温、高压下经过机头模具型腔进行分流压缩成型,挤出近似制品断面的型坯,再经过定型模具对型坯真空冷却定型,达到制品设计要求。
成型温度、定型冷却、螺杆转速、牵引速度、加料速度等都是影响异型材制品质量的重要因素,现分述如下:(一)温度控制PVC混合粉料进入挤出机后,要完成压实、输送、熔融、均化以及在较低温度下挤出。
为获得高质量、高产量型材,各段的温度需反复调节、准确控制,使物料在挤出成型过程中,始终在熔融温度与分解温度区间进行。
要正确设定温度,则需充分考虑和指导物料成型温度的相关因素。
1影响物料加工温度的因素1)配方及原料质量对加工温度影响最大的是配方,不同原料组成的混合物料其塑化温度不同。
配方确定后,加工温度也就基本确定了,只需视产品质量作小范围的调节;同一配方不同厂家生产的原料,挤出成型温度往往也有差异,只有通过生产实践,依据塑料型坯的质量,适时调整设定温度。
2)挤出速度在正常生产工艺条件下,提高挤出速度会使物料磨擦生热,所以应适当降低加热温度。
异型材挤出成型—异型材成型工艺(塑料挤出成型课件)
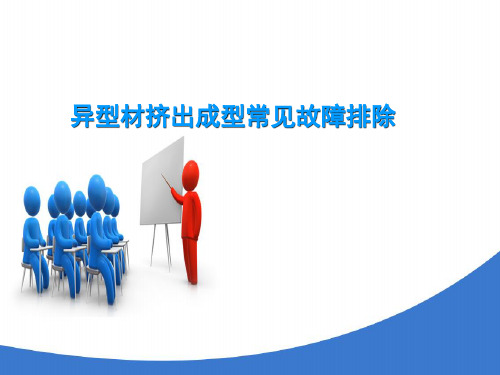
机头 压力 不足
定型段 物料 入机头 配方中 物料 分料筋 挤出 长度 未充分 料流 外润滑性 流动性 处熔体 速度 不足 汇流 偏低 过强 太差 温度偏低 太快
调整 物料 流量
增加 机头 压力
增加 定型段 长度
在模芯 支架后 设置 物料池
增大机头 入口处的 树脂流道
降低 混料的 外润滑性
采用 流动性好 的物料
冷却水对 型材冷却过快
关小冷却水
真空压力过大
定型模与冷却水箱 不在同一直线上
减小真空吸力
调整定型模与水箱 在同一水平直线上
异型材挤出成型工艺规程
异型材挤出工艺规程
1、开机前准备 检查水电供应、辅机是否正常,辅助工具
是否准备齐全,人员是否到位。
2、升温 升温并观察温度变化,打开螺杆油温,开启水阀,
(2)待停机料挤出后,依次关闭定型真空、风机,停止主 机螺杆,关闭螺杆油泵、冷却油泵。牵引机待料条牵引完 毕后关闭;
(3)后退定型台,松动模头紧固螺丝,松开连接法兰螺丝, 整体拆下模头,模具交付模具工清理;
(4)松开定型模底脚紧固丝,关闭主水阀,拔掉水、气管。 (5)关闭总电源,收拾工具,打扫现场卫生。 注:停机清理定型模执行(1)(2),清理模头还需执行
比如850r/min左右,低速排料, 转 速150r/min左右。
(4)混合温度:视冷热混合情况而定。 (5)混合时间:一般为5-15min。
二、异型材成型工艺控制
物料混合包括热混和冷混。
热混的目的是将物料中各个组
分颗粒达到最大程度的分布,使 物料升温,达到预塑化,如PVC 热混温度控制在115~120℃。
挥发物含量过多 产生分解气体
大
增加螺杆压缩比, 使排气完全
挤出工艺过程

• c.橡胶挤出机则不一样。
• 为了便于物料的容易加入、输送、熔融、均化 以及在低温下挤出,获得高质量、高产量的制 品,每一种物料的挤出过程应有一条合适的温 度轮廓曲线。
12
应当指出,物料的温度轮廓曲线、料筒的温度 轮廓曲线和螺杆的温度轮廓曲线是不相同的。
一般情况下我们测得的温度轮廓线是料筒的, 而不是物料的。物料的温度测量较难,由上 图可见,其温度轮廓线有一个变化的幅度。 螺杆的温度轮廓线较料筒的温度轮廓线为低, 而较物料温度轮廓线为高。 应当指出,料筒和螺杆的设计对挤出过程的热 量的产生有很大影响。
13
• 3)温度波动 • 上图所示的温度轮廓线只是稳定挤出过程温
• 1、加料段---输送并开始压实物料
• 螺槽为松散的固体粒子(或粉末)所充满,胶料 开始被压实。
• 2、压缩段
• 1)由于阻力,物料被压实
• 由于螺槽逐渐变浅,以及滤网、分流板和机头的 阻力,在塑料中形成了很高的压力,把物料压得 很密实。
2
• 2)外热、内热的作用,物料熔融
• 同时,在料筒外热和螺杆、料筒对物料 的混合、剪切作用所产生的内摩擦热的 作用下,塑料的温度逐渐升高。对于常 规三段全螺纹螺杆来说,大约在压缩段 的三分之一处,与料筒壁相接触的某一 点的塑料温度达到粘流温度,开始熔融。
的几何形状和尺寸。再经过冷却定型和其它工序, 就得到成型好的制品。
5
(二)参变量
描写这一过程的参量有温度、压力、流率(或挤 出量、产量)和能量(或功率)。有时也用物料 的粘度,因其不易直接测得,而且它与温度有关, 故一般不用它来讨论挤出过程。
6
1、温度
温度是挤出过程得以进行的重要条件之一。 如前所述,物料从加入料斗到最后成型为制 品是经历了一个复杂的温度过程的。
第八章挤出异型材

4)实心异型材
具有椭圆、矩形、三角形等非圆形断面 的实心异型材。
5)复合异型材 在异型材中镶嵌钢、铝等金属型材或织 物、木材等。
T型护栏 D型护栏 C型护栏60、 E型铝导轨
16—2认识生产线及控制面板
一、异型材生产用挤出机 二、异型材机头 三、冷却定型装置
四、牵引装置
五、切割装置
一、异型材生产用挤出机
冷却
牵引
切割
堆放
控制形式
二、双螺杆挤出机挤出硬PVC门窗异型材工艺控制要点 硬PVC门窗异型材的挤出过程可简述如下:改性PVC混合料 在机筒内经过螺杆混炼,在内磨擦热和电加热的作用下,物 料逐渐变成熔融粘流态,物料在旋转螺杆的流动下向机头方 向螺旋运动。进入机头模具后,在高温、高压下经过机头模 具型腔进行分流压缩成型,挤出近似制品断面的型坯,再经 过定型模具对型坯真空冷却定型,达到制品设计要求。成型 温度、定型冷却、螺杆转速、牵引速度、加料速度等都是影 响异型材制品质量的重要因素,现分述如下:
③机头及口模温度要高。为获得型材较好的 外观及力学性能,以及减小熔体出模膨胀, 一般控制机身温度较低,机头及口模温度较 高。在具体操作中应根据不同的异型材截面、 不同的电热板结构、合理调节温差。其大致 原则为:截面复杂、截面积大、壁厚及转角部 分,温度控制应稍高;反之温度控制应稍低; 截面对称、厚薄均匀部位一般不允许有温差。
(二)真空度控制及冷却定型
PVC异型材在挤出过程中,刚出口模时完全处于软化态,进入真空定型模 后,借助负压的作用,异型材紧紧吸附在定型腔模型上,经模型内冷冻 水的冷却,异型材被引出真空定型模后,就能获得理想的形状及尺寸。 通常,真空度应大于67lPa。但真空度过大,会增中牵引机负荷,同时 还将延缓、甚至阻碍产品顺利进入真空定型模,导致口模与真空定型之 间积料堵塞,此外,还会降低产量,缩短真空泵使用寿命;而真空度过 小,则吸力不足,导致严重变形或不成型,无法保证产品的外观质量及 尺寸精度。 真空定型模的冷却水通常是由定型套后部流人,前部流出,使水流方向 与型材前进方面逆向而行,这可使型材冷却较缓和,内应力较小,同时 定型套前端温度较高,型材易于吸收。硬PVC异型材冷却水要求在20℃ 以下,以15-20℃较理想。由于硬PVC异型材往往是不对称产品;可采 用若干个真空定型模来冷却定型,这样可避免元规则的弯曲变形。
- 1、下载文档前请自行甄别文档内容的完整性,平台不提供额外的编辑、内容补充、找答案等附加服务。
- 2、"仅部分预览"的文档,不可在线预览部分如存在完整性等问题,可反馈申请退款(可完整预览的文档不适用该条件!)。
- 3、如文档侵犯您的权益,请联系客服反馈,我们会尽快为您处理(人工客服工作时间:9:00-18:30)。
塑料异型材产品工艺流程介绍
工艺流程
PVC f各种助剂f咼速搅拌捏合f挤出f冷却真空定型f牵引f定长切割f成品f检验f包装入库
冷却真空定型PVC干混料
锯切
共
挤
模
头
号生产线rltfpL
干SA
燥 二、主要设备
1、 主机:
车间大部分机台使用的为SJZ65/132型双螺杆挤出机,长径比:1 : 22 ,螺杆 转速
7r/ min 〜48r/ min ,螺杆的旋转方向:异向向外旋转。
2、 辅机:
(1) 冷却定型装置:,由气水分流器、活动台板、调整机构组成。
真空冷却段数:4 段,水环真空泵电机功率:10kW 。
(2) 牵引装置:大平面橡胶带牵引。
(3) 锯切装置:配有计长装置,能跟踪切割的气动式锯切机。
(4) 堆放装置:气动式可翻转托架。
三、 生产工艺要点
型材的挤出成型是利用螺杆旋转加压方式, 连续地将塑化好的成型物料从挤 出机料筒中挤入机头, 熔融物料通过机头口模成型为与口模形状相仿的型坯, 用 牵引装置将成型制品连续地从模具中拉出, 同时冷却定型,制得所需形状的制品。
要获得外观与内在质量均优良的型材制品, 需要对挤出工艺条件进行控制, 控制 要点主要为混料、成型温度、螺杆冷却与转速、挤出压力、冷却定型等。
3.1 混料
混料过程先将 PVC 树脂以及配方计量加入其它组份加入到热混机 , 高速搅 拌升温到120C 进行混合,混合均匀后,放到冷混机中边混料边冷却至45C ,形成 松散、易流动的粉状混合物 , 然后出料备用。
混料时温度控制很重要 , 混合温度过 高, 物料易发粘、结块、塑化不均;混合温度过低 , 则物料混合不充分 , 达不到预 塑目的。
所以一般情况下,高温混合终点温度控制在(115〜120) T ,高混时间 10min 〜15min ,冷混出料温度45 C 。
3.2 挤出成型温度
生产产品选用的是有排气装置的异向向外旋转的双螺杆挤出机。
挤出机经过 预热、加料之后通过输送、 排气、熔化等过程 , 将物料均匀塑化形成熔体 , 到达机 头后进一步均化 , 通过机头压力 , 压实成型为密实的型坯 , 以流动状态连续通过口 模成型。
共挤
机
挤出成型温度是促使成型物料塑化和熔体流动的必要条件,它对挤出成型过程中物料塑化、型材制品的质量和产量均有十分重要的影响。
料筒和口模的温度是控制的重点,因为PVC的加工温度与分解温度颇为接近,因此要严格控制。
通常挤出机的温度控制主要由料筒加料段到挤出段的温度控制,使物料从固态粉料或粒料逐渐被融化,达到物料良好的塑化状态。
一般各段温度要根据挤出机的特点、物料的配方加工特性以及制品的质量要求来确定。
挤出成型的温度一般指塑料熔体的温度,该温度很大程度上取决于料筒和螺杆温度,实际生产中位测量和控制方便,常用机筒温度来近似熔体温度,利用热电偶来测量控制。
在用双螺杆挤出机挤出时,加料段的温度应高于树脂的熔融温度,加料段、压缩段、排气段和均化段的温度分布一般呈马鞍型曲线。
机头温度对挤出形成的影响很大。
机头温度必须控制在合理的温度范围,才能获得良好的型材外观和力学性能,减小熔体出口膨胀,一般机头设定温度高于料筒温度。
根据配方要求,挤出温度设定在170 C〜180 C之间,过高PVC就会分解变色,机头口模温度最高可达190 C〜210 C。
3.3螺杆冷却与螺杆转速
由于PVC熔体粘度高,会因摩擦生出过多热量而引起螺杆粘料分解,使型材内壁粗
糙, 故采用螺杆冷却以减少PVC 熔体与螺杆表面的摩擦热, 但冷却温度要控制在70〜
90 C ,冷却温度过低,会减少挤出量和影响塑化质量,不利于产品质量。
螺杆转速时控制挤出速率、产量和制品质量的重要工艺参数。
若提高螺杆转速和剪切速率、熔体表观粘度则下降,有利于物料均化,可以适当提高制品的冲击强度、弯曲强度及拉伸强度等力学性能;但螺杆转速过高,离模膨胀加大,物料在料筒内停留时间过短,也会影响制品的质量。
3.4挤出压力
物料在成型过程中需要一定的压力来克服其流动的阻力和自身的粘性摩擦。
挤出压力是保证物料塑化质量、得到均匀密实、质量合格制品的必要条件,机头压力的大小也是影响产品质量和产量的一个重要因素。
挤出机的工作压力由螺杆、口模特性及熔融物料的流动性决定的。
熔体挤出时, 需要足够的压力, 才能得到密度适宜、物理性能较好的制品。
但机头压力过大, 易有溢料, 且物料会因摩擦过度生热而分解,一般控制在18~22MPa当然,机头压力过小也会导致产品质量问题, 如制品不密实, 易产生翘曲。
3.5牵引速度
牵引塑化直接影响制品的壁厚、尺寸公差、性能及外观。
因此要求牵引速度必须稳定,牵引塑化与型材挤出速度相匹配,正常生产时牵引速度要稍快于挤出速度,以克服制品的离模膨胀。
3.6冷却与定型真空
型材产品的冷却定型采用的是干湿相结合的冷却方式。
使用湿式真空冷却定型虽然可以加快挤出速度, 但型材因冷水的冲击会造成制品内应力, 从而引起挠曲变形; 使用干式真空冷却定型, 水没有直接接触型材表面, 而热量是通过定型冷却套由水带走的, 冷却效率较低, 要想提高冷却效率, 就需要加长冷却定型器的长度。
因此, 采用将干真空定型和湿真空定型串联起来的冷却方法, 既保证了产品的精度, 减少内应力, 又大大提高了成型速度。
具体方式是以干真空定型缓冷后, 再在湿真空水槽中使整个制品减压冷却, 由此可以防止制品冷却时产生变形, 减少内应力, 高速成型精度高的制品。
真空定型在型材的挤出过程中,被挤出口模的熔融物料直接进入真空定型模,借助真空负压作用,物料被紧紧吸附在定型模的模壁上,经真空定型模内的冷却水冷却固化,真空度控制恰当与否将直接影响制品质量,若真空度太低,对型坯的吸附力不足,制品难以达到预定形状,外观质量和尺寸精度较差;真空度太高,阻力加大,会导致与真空定型模入口间积料,严重时甚至拉断型材。
型材挤出过程中要求冷却水温在18C〜22C较为理想,有效水压应大于0.2MPa。
结语:生产工艺是影响塑料异型材挤出产品质量的重要因素,要保证型材产品的质量,关键在于严格控制混料、挤出生产工艺,要对挤出过程中的工艺参数进行严格监视和定期监测,及时把握异型材的表面、外形质量和各项物理力学性能,进行必要的控制和调整,不断分析质量状况,提高工艺控制水平。