海上风电场单桩基础施工技术方案研究
近海风电场大直径单桩沉桩施工
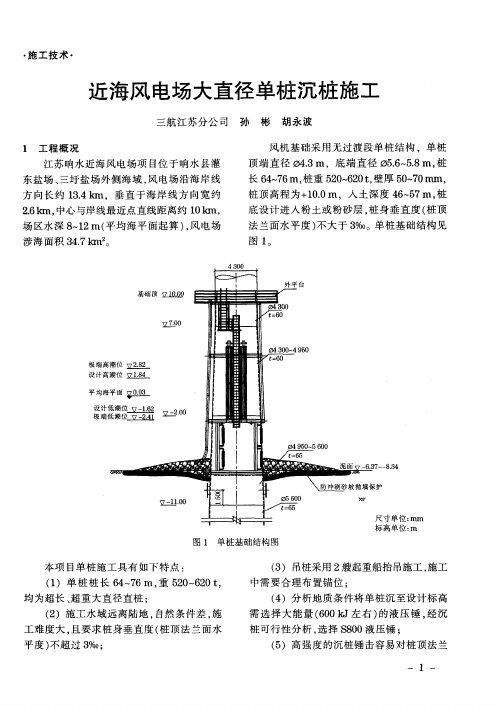
根 单 桩 桩 位 处 地 质 资料 ,辅 助 桩 采 用 桩 长
4 1 . 5 m、 桩径 2 . 0 m、 壁厚 2 4 mm 的钢 管桩 ,
单 桩 自重 入 土 V 7 —. 1 8 . 0 O
桩顶标 高+ 1 0 . 5 m, 平面位置允许偏差 1 5 0 mm。
单位 : m
图 2 辅 助 平 台 示意 图
径处 可兼 作辅 助平 台搁 置之 用 。打 桩船 上 配
本 项 目中单 桩 长度 最 大为 7 6 m. 按最 不
备外 海沉 桩定位 系 统 ,以确保 辅 助桩 的平 面
位 置不超 过 l 5 0mm。
利低 潮位 一 2 m 考 虑 起重 船 吊钩 吊高 吊钩离
表 l
起重 船 , 根据计 算 , 单桩 翻身 吊耳 最大 受力 为
2 7 9 t , 需 增加 一艘 5 0 0t 起 重船 ( 下称 辅 吊船 ) 抬 吊立桩 。
3 . 2 桩锤 的选 择
结 合 现 场 地 质 资 料 进 行 沉 桩 可 打 性 分
析, 以夹砂 层较 厚 达 3 0m 的 Z K1 l 号 机位 进
因此 ,主 吊船 需选 用 吊高 超过 8 6 m 的
辅助 平 台采 用起 重船 整体 起 吊安装 。辅 助平 台上设 置 一套 由数个 5 0t 和l 0 0t 千斤 顶组成 的顶 撑系 统 , 提 供约 8 0t 的水平 推力 ,
以此来 调 整大 直径 钢管桩 的垂 直度 。 3 船机 设备 的 选择 3 . 1 船 机 的选择
涉海 面积 3 4 . 7 k m。 。
桩 顶 高程 为+ 1 0 . 0 m ,入 土深度 4 6 ~ 5 7 m, 桩
海上风机单桩基础沉桩施工工艺与应用
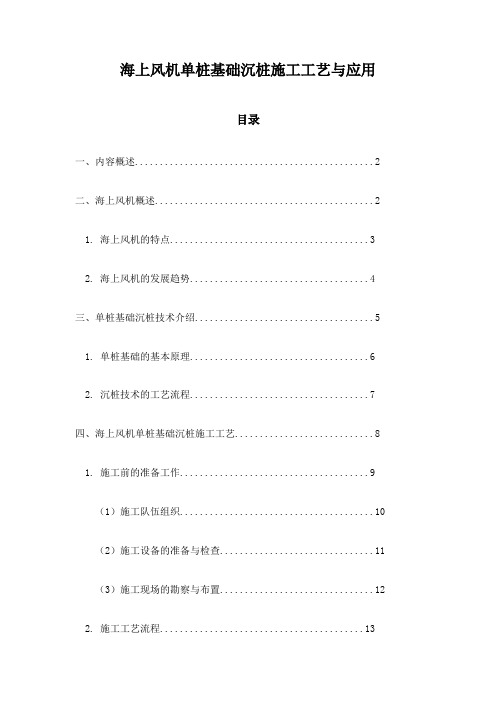
海上风机单桩基础沉桩施工工艺与应用目录一、内容概述 (2)二、海上风机概述 (2)1. 海上风机的特点 (3)2. 海上风机的发展趋势 (4)三、单桩基础沉桩技术介绍 (5)1. 单桩基础的基本原理 (6)2. 沉桩技术的工艺流程 (7)四、海上风机单桩基础沉桩施工工艺 (8)1. 施工前的准备工作 (9)(1)施工队伍组织 (10)(2)施工设备的准备与检查 (11)(3)施工现场的勘察与布置 (12)2. 施工工艺流程 (13)(1)桩位的确定与布置 (14)(2)桩基础制作与运输 (15)(3)沉桩作业的实施 (16)(4)质量检测与评估 (17)3. 施工中的注意事项 (19)五、海上风机单桩基础沉桩施工应用实例分析 (20)1. 工程概况与地质条件分析 (21)2. 单桩基础设计与选型依据 (22)3. 施工过程描述与实施效果评价 (23)4. 经验总结与问题解决方案分享 (24)六、海上风机单桩基础沉桩技术的优化方向与建议 (26)1. 技术优化方向分析 (27)2. 施工过程中的改进措施建议 (28)3. 政策法规与行业标准的建议与期望 (29)七、结论与展望 (30)1. 研究成果总结 (31)2. 未来发展趋势与展望 (32)一、内容概述随着全球能源需求的不断增长,海上风电作为一种清洁、可再生的能源形式,得到了越来越广泛的关注和应用。
海上风机单桩基础沉桩施工工艺与应用是海上风电场建设中的关键环节,对于保证风电机组的安全稳定运行和提高风电场的经济性具有重要意义。
本文主要围绕海上风机单桩基础沉桩施工工艺与应用展开论述,包括沉桩施工的基本原理、技术要求、施工方法、质量控制以及实际应用案例等方面的内容,旨在为海上风电场建设提供科学、可行的技术支持。
二、海上风机概述海上风力发电作为一种可再生能源技术,在全球范围内得到了广泛的关注和应用。
海上风机作为海上风力发电系统的核心部分,其结构设计和施工工艺直接影响着整个发电系统的运行效率和安全性。
超大型海上风电单桩基础发运技术研究及应用

运输船排载速度与模块车上船速度相匹配。对于江苏等区域超 差要求较大,尽量在大潮汛期间装船。在发运过程中尽量使用 拖轮稳船,防止走锚现象导致安全事故。该技术具备发运成本 低、时间快、运输过程稳定等优点,但是存在发运成本高、发 运时间不可控等不足,适合在无大型龙门吊制造厂家使用[3]。
4 海上风电基础滑移发运 海上风电单桩滑移主要采用顶升滑移装置进行滑移。
1 海上风电单桩基础发运概述 目前国内海上风电基础主要采用导管架、单桩基础、高
桩承台等形式。因单桩基础承载力高,水平抗弯性好、施工简 单、对环境扰动小等优点,已经被越来越多的海上风电项目所 应用和推广[1]。
随着海上风电项目建设速度加快,项目逐步向深水区域推 进,广东、福建等深水区域1500T以上单桩数量不断增加,如 何解决1500T以上超大型单桩发运问题显得越来越重要。目前 针对1500T以上单桩,国内制桩厂家主要有吊装、滚装和滑移 三种发运方式。现就三种发运技术进行研究并在后期项目中应 用推广。
3 海上风电单桩基础滚装发运 海上风电单桩滚装主要使用轴线车滚装技术。1500T单桩
基础按照1.3的安全系数,需要轴线车载重量达到2000T左右。 该技术一般采用2个PPU, 至少56个35T的轴线小车,要求运输 船舶在7000T以上(如双桩发运需要求在8000T以上),型深要 求在6.5米以上,排载量在1200T/h以上。模块车组进行软、硬 连接,通过液压油缸0~700mm的行程来调整平衡,实现潮水、 运输船、单桩之间的协调。运输船通过装载计算机进行计算, 按照25%,50%,75%,100%的装载量分多步进行滚装,确保
引言 根据国家能源局出台的《风电发展“十三五”规划》,积
极稳妥地推进海上风电建设,到2020年全国海上风电开工建设 规模达到1000万千瓦,力争累计并网容量达到500万千瓦以上。 根据权威机构预测2020年、2021年将新增海上风电并网容量 34.13GW、5.02GW;累计并网容量将于2020年底、2025年底分 别达到10.84GW、40.34GW。如推进顺利,前述2025年底累计 装机容量(40.34GW)较2018年底(3.63GW)将实现逾10倍增 长。可见,我国海上风电建设将在近几年迎来快速发展的黄金 时期。
复杂条件下近海风电机组单桩基础设计及优化
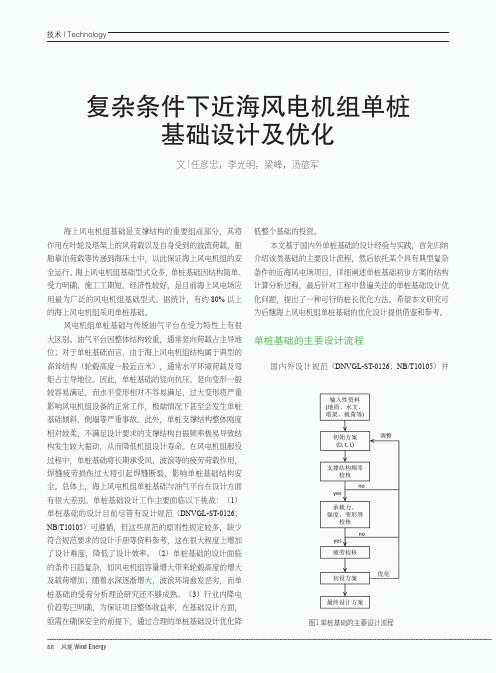
国 内 外 设 计 规 范(DNVGL-ST-0126;NB/T10105) 并
矩占主导地位。因此,单桩基础的竖向抗压、竖向变形一般
较容易满足,而水平变形相对不容易满足,过大变形将严重
影响风电机组设备的正常工作,极端情况下甚至会发生单桩
基础倾斜、倒塌等严重事故。此外,单桩支撑结构整体刚度
相对较柔,不满足设计要求的支撑结构自振频率极易导致结
机组 1p 和 3p 频率带,支撑结构通常有 3 种可选方式(如图 土体力学性状差异显著。本文仅针对场区一种典型地层介绍
2 所示),即自振频率小于 1p 下限的“柔-柔”型式、自 单桩基础方案的初步设计过程,表 1 给出了相应的地层分布
振频率大于 1p 上限且小于 3p 下限的“刚-柔”型式、自振 及土体参数取值。可以看出,海床面整体较低(85 高程标
的海上风电机组采用单桩基础。
为后继海上风电机组单桩基础的优化设计提供借鉴和参考。
风电机组单桩基础与传统油气平台在受力特性上有很
大区别。油气平台因整体结构较重,通常竖向荷载占主导地 单桩基础的主要设计流程
位;对于单桩基础而言,由于海上风电机组结构属于典型的
高耸结构(轮毂高度一般近百米),通常水平环境荷载及弯
全运行。海上风电机组基础型式众多,单桩基础因结构简单、 条件的近海风电场项目,详细阐述单桩基础初步方案的结构
受力明确、施工工期短、经济性较好,是目前海上风电场应 计算分析过程,最后针对工程中普遍关注的单桩基础设计优
用最为广泛的风电机组基础型式。据统计,有约 80% 以上 化问题,提出了一种可行的桩长优化方法。希望本文研究可
桩长 L。其次,根据风电机组厂商允许的频率窗口,校核支
撑结构频率,避免因支撑结构自振频率与风轮转动频率(1p)
海上风电单桩基础结构设计关键问题探讨

海上风电单桩基础结构设计关键问题探讨摘要:单桩基础因其结构形式简单、施工技术成熟,在国内外海上风电场中均得到了广泛应用。
目前我国已建成的单桩基础风电项目大部分位于江苏沿海地区,这些地区的地基为软基。
关键词:海上风电单桩基础结构设计前言:海上风电与陆上风电最大的不同在于基础的不同,基础成本约占整个海上风电场投资的25%,因此降低基础成本有利于提高整个风电场的经济性,推动海上风电的发展。
欧洲已经为海上风电设计、施工了将近2000 台基础,其中70% 为单桩基础。
国内上海东大桥海上风电项目为高桩承台式基础,该基础现场作业时间长、工作量大、成本高。
一、海上风机基础分析海上风电机组的基础平台由油气工业中的海上采油平台形式发展而来,目前海上风力发电机组的基础有单桩、三脚架、导管架式基础、重力基础、负压桶基和浮动平台结构等几种。
每种基础都有其各自的优缺点,适应不同的海况条件,当设计开发大型海上风电场时,设计一种适合海上风机特殊要求和特定海况条件的基础能够节省前期投入。
虽然国外在基础设计方面有很多成功经验,但是国内缺乏海上风机基础设计经验,海上风机基础设计研究对推动我国海上风力技术的发展将起到至关重要的作用。
海上风机基础的设计是一个复杂的系统工程,涉及到海洋环境、港口航道、市场经济、海洋结构物的设计、近海桩基工程、海上风机基础特殊载荷、结构分析、基础与地基动力相互作用、风机一塔架一地基一基础系统分析等多个方面,包含众多的设计变量,不同的海上风场特性不同,如何处理其中的多种矛盾,做出合理的设计是很有意义的。
国内海上风机桩基础设计研究处于起步阶段,海上风机基础设计研究能够为将来海上风力发电提供参考,对将来进行海上风机基础结构优化设计提供借鉴,对中国海上风力发电事业的腾飞具有举足轻重的意义。
桩基础是目前国外海上风机普遍采用的一种相对成熟的基础形式,很多企业和组织在海上风机桩基础的设计和工程施工方面有丰富的经验,但是,各个风场的海况条件不同,结合海上采油平台的丰富经验,海上风机基础的设计优化空间还相当大。
海上风电场工程钻机单桩施工技术

用户■施工CONSUMERS & CONSTRUCTIONA海上风电扬工程钻机单桩施工技木■王海波平煤建工集团彳寺殊凿井工程有限公司,河南郑州450016摘要:针对海上风力发电单粧基础施工,采用工程钴机施工。
工程钻机在海底中硬岩中钻进中高效快速,能够适应变直径钢管粧, 改变了传统海上风电基础施工工艺,具有广阔的市场前景。
关键词:海上风力发电、工程钻机、单桩施工1引言多年来,国外大扭矩高性能海上风电嵌岩桩钻机凭借 高技术含量、高可靠性,在全球市场一直垄断地位。
国外 海上风电嵌岩单桩钻机价格昂贵,采购成本高,为了改变 这一现状,自主研发此类钻机已经势在必行。
Z D Z D-100 型多用重型工程钻机是平煤特凿公司,总结国内大口径工 程钻机和大型矿山竖井钻机技术和施工经验的基础上,研 制的迄今国内作业能力最强的一款多用途工程钻机。
2017 年1月,该机在国内首根海上风电嵌岩单桩试桩成功,填 补了国产海上风电大型钻机的空白。
2工程概况龙源莆田南日岛400M W海上风电场工程位于莆田市 南日岛东北侧海域,规划布罝100台单机容量4.0M W的风 力发电机组,风电场分A、B两个场区。
如图1所示。
图1海上风电场工程地貌该工程有三大特点:一是地质条件较为复杂。
根据钻 孔揭露的地层结构、岩性特征、埋藏条件及物理力学性质,结合区域地质资料,工程区浅部为第四系全新统冲海积层 淤泥混粗砂、淤泥质粉质粘土,中部为粉质粘土、粉砂等,下部为坡积层粘性土夹砂,下伏基岩岩性为燕山期花岗岩。
中风化花岗岩最大饱和抗压强度为130MPa (—般仅为80 ~120MPa) 〇二是工程的难点大。
风电场海域内岛屿、岛礁分布较多,水深范围大,水文地质条件复杂;岩石强度高(抗压强度 130M P a以上),钻孔难度大;莆田地处福建沿海中部,为 台风多发地区,施工作业受台风(7 ~ 10月份台风高发期)、季风影响严重。
三是使用的单桩种类多。
海上风电基础施工方案
海上风电基础施工方案一、前言随着可再生能源的发展和对环境保护的日益重视,海上风电逐渐成为清洁能源领域发展的热点。
本文将针对海上风电基础施工方案进行探讨和分析,为海上风电项目的建设提供参考。
二、施工前准备1.勘测与设计阶段在进行海上风电基础施工前,需要对风力资源进行详细的勘测,确定风电场布局和选址等。
同时,还需要进行海洋环境勘测,包括水深、波浪、潮流等参数的测量,以便为基础施工提供准确的数据支持。
2.材料采购与准备根据设计方案,需要提前计划并采购所需的施工材料,包括钢材、混凝土、缆绳等。
同时,也需要准备相关的设备和工具,如起重机、打桩机等,以确保施工过程的顺利进行。
三、基础施工技术1.桩基施工针对海上风电的桩基施工,常见的方法有打桩法和冲洗法。
打桩法适用于土质较硬的海床,通过大型钢管桩或钢筋混凝土桩的打桩作用来固定风机基础。
而冲洗法适用于软土、半流沙等地质条件,通过将水压引入管道,冲刷地层并使土壤流动,形成孔洞来安装和固定基础。
2.浮式施工考虑到海上环境的复杂性和水深的限制,浮式施工成为一种常见的施工方式。
通过搭建浮式平台,实现基础的装配和安装。
这种施工方式灵活、高效,适应性强,可以有效提高施工进度和效率。
3.海底电缆敷设海上风电项目中,电缆是将风机与陆地电网相连接的重要纽带。
为了保证电缆的安全敷设,需要采取合适的方法,如水下拖航、潜水员布放等。
在电缆敷设过程中,需要严格控制敷设的张力、弯曲半径等参数,以免损坏电缆。
四、施工安全与质量控制1.安全措施海上风电基础施工具有一定的风险性和复杂性,需要严格遵守安全操作规程。
施工人员应定期进行安全培训,并全程佩戴必要的防护装备。
同时,施工现场应设立合适的警示标志和隔离措施,确保施工过程中人员的安全。
2.质量控制为了保证施工质量,应建立完善的质量管理体系。
施工人员需要熟悉工程图纸和技术规范,进行严格的施工操作。
建立质量检测体系,对施工过程中的关键节点进行监测和检验,确保基础的稳固性和安全性。
海上风电场单桩基础施工技术方案研究
海上风电场单桩基础施工技术方案研究发表时间:2019-09-05T09:58:08.447Z 来源:《中国电业》2019年第08期作者:夏艳慧[导读] 随着国内海上风电的开发,风电场建设各方面技术均日益成熟。
风机机组逐步大型化,风机基础随之呈现多样化趋势。
(中国电建集团华东勘测设计研究院有限公司,浙江杭州 311122)摘要:随着国内海上风电的开发,风电场建设各方面技术均日益成熟。
风机机组逐步大型化,风机基础随之呈现多样化趋势。
单桩基础为主流基础型式之一,国内针对大体型单桩基础的施工方案随着江苏、福建等海域的海上风电场工程的建设,进行了深入细致的研究,各种施工方案代表了目前国内近海海域单桩基础施工的先进施工思路与水平,船机设备的选择也符合目前国内现有大型工程船只的资源条件。
关键词:海上风电;单桩基础;浮式起重船近年来,国内海上风电建设飞速发展,风机基础型式多样化,目前已经应用的海上风电基础施工方案有单桩基础、多桩基础、重力式基础等,其中单桩基础因其结构简单、施工方便快捷、造价相对较低等优点,受到施工单位和建设单位的青睐,是目前海上风电基础的主要类型。
单桩基础由大直径钢管桩与附属构件组成,根据目前国内海上风电项目的最新数据获悉,单桩基础的钢管桩直径已达到8m以上,桩重则突破1500t。
钢管桩由液压冲击锤沉入海床,海上沉桩系统主要包括打桩船、运桩船、抛锚艇、拖轮与交通艇等船舶组合,其中以打桩船为主要施工设备。
施工前,需根据钢管管桩设计参数与海洋环境的特点对沉桩的各环节进行分析,选择合适的设备配置。
根据目前各海上风电场工程的实施,单桩基础包括非嵌岩桩和嵌岩桩两种情况,本文主要介绍非嵌岩单桩基础常规采用的浮式起重船施工方案。
1.船只设备的选择单桩基础常采用起重船配置打桩锤进行吊打施工。
大型浮式起重船在单桩基础施工中,主要承担单桩结构的起吊、立桩、进龙口、稳桩、定位等作业,吊打沉桩之前全部的准备工作将由其完成,因此对浮式起重船的性能要求很高。
海上风电基础施工方案
海上风电基础施工方案1. 引言海上风电作为清洁能源的一种重要形式,正逐渐成为全球能源转型的关键领域之一。
而海上风电基础施工则是构建海上风电场的第一步,对保证海上风电设施的稳定和安全运行具有重要意义。
本文将重点讨论海上风电基础施工的方案,旨在提供一个详细且可行的解决方案。
2. 施工前准备在开始海上风电基础施工之前,需要进行一系列的准备工作,包括但不限于以下内容:•选址和勘察:通过海洋勘探和环境评估确定风电场的最佳位置,并进行地下地质、海洋底质等方面的详细勘察。
•设计方案:根据选址和勘察结果,确定风电基础的类型(如单桩式、桩帽式、桩-筒等),并进行详细设计。
•物资采购:预先采购所需的施工设备、材料和工具。
•人员培训:组织相关人员进行必要的培训,包括安全操作、救援等方面的知识。
3. 施工流程3.1 海上基础建设海上风电基础的施工流程一般包括以下步骤:1.安装施工平台:搭建安装施工平台,为后续工作做好准备。
平台的选型应根据实际情况确定,可以是浮动平台、钢管桩等。
2.打桩:根据设计要求,在海洋底部进行打桩,将风电基础与海底固定连接。
打桩过程中需要根据海底地质情况进行调整,以确保基础的稳定性和安全性。
3.安装钢筋骨架:在打桩完成后,安装预先制作的钢筋骨架,以增强基础的承载能力。
4.混凝土浇筑:在钢筋骨架安装完成后,进行混凝土浇筑。
根据设计要求,可采用自卸船输送混凝土,保证施工过程的连续性和质量。
5.基础固化:待混凝土凝固后,进行基础固化处理。
在此过程中,需要进行加固、防腐等工作,以保证基础的稳定性和耐久性。
3.2 海上风机安装在海上风电基础施工完成后,需要进行海上风机的安装。
安装过程一般包括以下步骤:1.起重准备:准备好起重设备和吊装工具,确保安全的起重操作。
2.吊装风机组件:根据实际情况,通过吊装设备将风机的叶片、塔筒等组件吊装至基础上。
吊装过程需要精确控制吊装高度和角度,以保证安全和准确。
3.组装风机:将吊装到基础上的风机组件进行组装,包括连接叶片、塔筒等部件。
海上风电单桩基础防冲刷抛石施工技术
海上风电单桩基础防冲刷抛石施工技术海上风电单桩基础防冲刷抛石施工技术,那可真是个大工程,咱们可得好好聊一聊。
听到“海上风电”几个字,大家第一反应肯定是:风车!对吧?不过这个风车不是普通的风车,不是那种你在田野里看到的,哗啦啦转着的玩意儿,这个是“巨无霸”,在海上耸立的那种,个头大得不行!不过不管多大的风车,咱们得先做好基础工作。
你说,是不是每个“大楼”都得有个结实的地基,风电平台也不例外。
问题就来了,海上水深,浪大,水流快,怎么让这些巨大的风车稳稳地屹立在大海中?这时候,单桩基础就成了关键。
说到“单桩”,大伙也许会有点迷糊。
单桩就是一个大铁柱子,打进海底,支撑起风电机组。
想象一下,它就像一根大大的柱子,立在海底,承受着风车的巨大重量。
嗯,光有这根柱子可不行,还得考虑到一个问题——冲刷。
你知道的,海浪不断地拍打,水流一冲,这基础不牢固,风车就有可能岿然不动,甚至有点“动摇”的危险。
那怎么办呢?防冲刷就成了施工中的大难题了。
这个防冲刷可不是儿戏,说起来有点像是在“给海底打个‘防晒霜’”。
海底的水流就像是一群顽皮的小孩子,不停地在周围打转。
如果不加以防范,时间一长,周围的泥土、沙子就会被冲走,桩基就可能露出来,甚至倒塌。
为了让桩基保持稳固,这时就需要一种叫做“抛石”的技术。
你别看“抛石”听着挺简单,实则里面学问大着呢。
抛石施工其实挺考验技术的。
操作工人得精准地把石头一块块抛到桩基周围,这些石头的目的就是“挡水”,形成一个天然的“防护层”,让海水不能轻易侵蚀桩基。
别看这些石头是“调皮捣蛋”,但它们可是构成了防冲刷的第一道防线!每块石头的大小、形状、投放位置都得严格控制,太小了不够坚固,太大了就会让水流绕过去,不管用。
说起来,抛石施工不光是抛几块石头就完事了。
可得讲究技巧,工人们得在海浪不断冲击的环境中精准操作,简直比打高尔夫还讲究。
海上风大浪急,风电平台本身的稳定性、施工船只的起伏,都让这项工作变得格外不容易。
- 1、下载文档前请自行甄别文档内容的完整性,平台不提供额外的编辑、内容补充、找答案等附加服务。
- 2、"仅部分预览"的文档,不可在线预览部分如存在完整性等问题,可反馈申请退款(可完整预览的文档不适用该条件!)。
- 3、如文档侵犯您的权益,请联系客服反馈,我们会尽快为您处理(人工客服工作时间:9:00-18:30)。
海上风电场单桩基础施工技术方案研究
摘要:随着国内海上风电的开发,风电场建设各方面技术均日益成熟。
风机机组逐步大型化,风机基础随之呈现多样化趋势。
单桩基础为主流基础型式之一,国内针对大体型单桩基础的施工方案随着江苏、福建等海域的海上风电场工程的建设,进行了深入细致的研究,各种施工方案代表了目前国内近海海域单桩基础施工的先进施工思路与水平,船机设备的选择也符合目前国内现有大型工程船只的资源条件。
关键词:海上风电;单桩基础;浮式起重船
近年来,国内海上风电建设飞速发展,风机基础型式多样化,目前已经应用的海上风电基础施工方案有单桩基础、多桩基础、重力式基础等,其中单桩基础因其结构简单、施工方便快捷、造价相对较低等优点,受到施工单位和建设单位的青睐,是目前海上风电基础的主要类型。
单桩基础由大直径钢管桩与附属构件组成,根据目前国内海上风电项目的最新数据获悉,单桩基础的钢管桩直径已达到8m以上,桩重则突破1500t。
钢管桩由液压冲击锤沉入海床,海上沉桩系统主要包括打桩船、运桩船、抛锚艇、拖轮与交通艇等船舶组合,其中以打桩船为主要施工设备。
施工前,需根据钢管管桩设计参数与海洋环境的特点对沉桩的各环节进行分析,选择合适的设备配置。
根据目前各海上风电场工程的实施,单桩基础包括非嵌岩桩和嵌岩桩两种情况,本文主要介绍非嵌岩单桩基础常规采用的浮式起重船施工方案。
1.船只设备的选择
单桩基础常采用起重船配置打桩锤进行吊打施工。
大型浮式起重船在单桩基础施工中,主要承担单桩结构的起吊、立桩、进龙口、稳桩、定位等作业,吊打沉桩之前全部的准备工作将由其完成,因此对浮式起重船的性能要求很高。
如采用无法单独完成钢管桩空中翻身工作的全回转式起重船,则需配置辅助起重船,采用双船抬吊的方式完成管桩的空中起吊、翻身的工作。
辅助起重船可利用全回转起重船配合完成,主臂架操作灵活,便于与主起重船的协调配合进行空中操作。
2.锤击沉桩系统
目前大型的海上打桩机械主要有筒式柴油打桩锤、液压打桩锤、液压振动锤三种型式,其中以柴油打桩锤应用最为广泛,但考虑到海上风电单桩基础钢管桩属于超长大直径钢管桩,承载力要求高,对锤击能力要求较高,同时采用吊打的沉桩施工方式,使用柴油锤需增加一定的临时设施才可以进行沉桩施工,降低了其使用优越性。
根据国内已施工的风机单桩基础相关施工经验,通常选择大型液压冲击锤进行锤击沉桩。
液压冲击锤属于大当量打击能力的打桩锤,根据地质条件、钢管桩的特性选择合适的打桩锤,并可采用GRLWEAP等软件进行沉桩可打性分析。
在国内龙源振华、中交三航局、中铁大桥局、中海油等多家海上施工单位具有S1200、S1800、S2000、S3000等级别大型液压打桩锤可供选择。
3.辅助定位稳桩平台
辅助定位稳桩平台设施是保证单管桩沉桩施工精度控制的主要配套设施,也是整个施工方案的关键工艺。
稳桩平台上需设置扶正、导向装置,以调整大直径钢管桩的垂直度,稳桩平台的安装位置决定了钢桩沉桩的桩位,故必须严格控制稳桩平台的测量放样定位的准确度,特别要控制下桩龙口的定位精度。
定位稳桩平台一般由4根工艺桩、平台主体及平台与桩的连接系统组成。
可
根据工程地质条件进行计算确定钢管桩直径和桩长等参数。
平台主体采用整体制作,现场整体安装,根据工期要求可投入多套周转使用,结构示意图如图1所示。
定位平台上下层分别均匀布置数个千斤顶作为单桩沉桩扶正、导向装置,以调整大直径
钢管桩的垂直度,导向滚轮为高分子材料,能够有效保护钢管桩防腐涂层。
稳桩平台沉桩工
艺已经成功应用在江苏如东、响水、东台等多个海上风电场工程中,有效地保证桩身垂直度
在3‰以内,并取得了较好工程效果。
4.单桩沉桩
4.1 船位布置
定位稳桩平台搭设完成后,由现场船舶调度指挥船舶进点就位。
主起重船顺潮流方向就位,使定位稳桩平台位于主起重船的左舷或右舷,且船头方向与稳桩平台龙口方向一致。
辅
起重船同样顺潮流方向就位,船头方向与稳桩平台龙口方向相对。
起重船就位完成后,运桩
驳停靠辅起重船且桩顶方向尽量向主起重船船头方向靠拢,使吊耳位于主起重船主吊钩下方。
4.2 抬吊
待现场人员检查确认无误后,主起重船与辅起重船开始同步起吊,当桩完全离开运桩驳
甲板大约0.5m时,暂停起吊,再次检查钢丝绳受力情况,无异常后继续起吊,当桩距离运
桩驳甲板6~7m时运桩驳退出施工区域。
4.3 立桩
运桩驳退出后,两条起重船相互配合完成竖桩。
竖桩完成后辅起重船继续下放吊钩,使
钢丝绳不受力,同时主起重船继续上升吊钩,使单桩翻身吊耳处在水面上2~3m位置时安排
交通船将单桩翻身卸扣抽出。
4.4单桩入龙口
解扣完成后,主起重船继续起吊单桩,当桩底提升到适当高度时,旋转起重机,完成入
龙口操作。
桩处于稳桩平台龙口中间区域时开始下放单桩,当单桩翻身吊耳距离平台顶面大
约1m时,停止下放单桩。
安排翻身吊耳割除施工,同时完成稳桩平台上层平台外龙口梁安装,测量桩身姿态,调整各千斤顶完成预抱紧操作。
4.5自沉入土
单桩在自重作用下,下沉至泥面下一定深度后停滞下沉,单桩在自沉过程中,不断测量
监控桩身垂直度,通过吊机和液压千斤顶调整纠正,直至钢管桩自沉入泥稳定,即稳桩完成。
单桩确认稳定后,主吊船继续下放吊钩,使钢丝绳处于不受力且不脱钩状态。
观察15分钟
时间桩身无变化后,再进行下一道工序施工。
4.6压锤
单桩确认稳定后,解除主吊耳处钢丝绳,起重船吊机吊液压冲击锤套入钢管桩,开始压锤。
套锤过程中,必须保证锤、桩的中轴线相吻合,当桩与锤接触后,逐步下放吊钩,使压
桩重量逐步增加,此过程需全过程跟踪观测。
4.7 液压沉桩
主起重船吊液压锤套入桩顶后,分析自沉完成后土层的性能,采用最小能量点动沉桩,
测量控制桩身垂直度不断调整。
桩身入泥基本稳定后,才能稳定能量及合理频率锤击沉桩,
测量全过程控制桩身垂直度,施工如图5所示。
辅助平台拆除
在单桩沉桩完毕后,开始拆除辅助平台。
起重船下钩,工人在平台的吊耳处安装吊索具,上拉钢丝绳,使得钢丝绳受力,气割工人开始割除辅助平台与辅助桩之间的连接钢板。
割除
完毕后,起重船起钩,将辅助平台吊至运输船上,辅助桩采用起重船吊振动锤拔除。
6.防冲刷砂被施工
单桩基础由于桩径较大,且对冲刷敏感性较高,冲刷深度较大,采用铺设防护材料的防
冲刷处理措施能有效防止单桩基础冲刷坑的形成。
基础保护所需砂被及砂袋通过驳船运输至风机基础区域,利用起重船辅以人工进行铺设施工。
7附属设施安装
单桩基础常采用集成式附属构件,即将外平台、栏杆、爬梯、电缆护管、靠船构件等附属构件在陆上加工厂整体组装为一个集成式套笼结构,通过驳船运输至风电场拟安装机位,采用起重船整体吊装至钢管桩上,施工时需注意套笼的方向满足设计要求。
8.单桩沉桩要点
(1) 沉桩施工前充分做好起重船、拖轮、锚艇以及施工人员的技术和安全交底工作。
(2) 对天气预报跟踪分析,做好天气预测,选择合适的施工窗口期。
(3) 单桩基础施工前,仔细研究机位地勘资料,沉桩时做到桩、船分离,做好沉桩遭遇不良地层的预判,制定详细预案,采取相应响应措施。
(4) 单桩桩顶为无过渡段桩顶法兰,沉桩时法兰面应做好充分保护。
(5) 在立桩进龙口、插桩时密切观察定位架的情况,如发生位移等应停止插桩,必要时将桩吊起重新插桩;
(6) 单桩沉桩垂直度要求高,在下桩和沉桩过程中控制桩身垂直度,稳桩、套锤、沉桩过程中应多次观测。
(7) 沉桩过程中如有异常情况,立即与监理、设计、业主等有关方面取得联系,共同研究确定迅速做出处理。
结语
本文主要介绍了单桩基础采用大型浮式起重船吊液压锤沉桩,定位稳桩平台辅助配合的施工作业流程。
除以上施工方案外,单桩还可采用自升式平台船进行沉桩施工,目前国内已有多艘自升式平台船,最大起重能力可达到2000吨,采用自带抱桩器的自升平台船进行单桩沉桩的施工方式也在某些海上风电场建设中得到了成功的应用。
随着我国海上风电建设的发展,机组逐步大型化,离岸距离越来越远,地形条件复杂,施工难度也随之增加。
因此,不断优化施工工艺,提高施工设备能力,施工工效,是海上风电发展必然经历的过程。
参考文献:
【1】陈强,刘凤松,肖纪升潮间带风电场无过渡段单桩基础施工关键技术中国港湾建设2016年6月
【2】李海军,张泉泉,胡永波海上风电支腿船单桩沉桩技术海洋开发与管理 2018年 S1。