人造革
天然革和人造革的区别
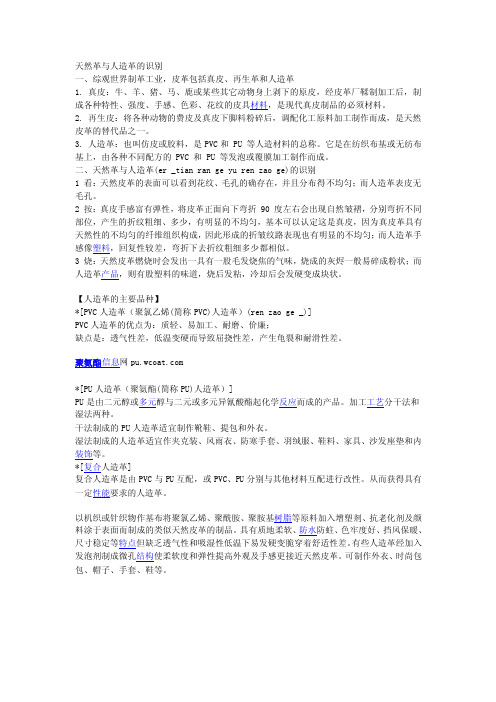
天然革与人造革的识别一、综观世界制革工业,皮革包括真皮、再生革和人造革1. 真皮:牛、羊、猪、马、鹿或某些其它动物身上剥下的原皮,经皮革厂鞣制加工后,制成各种特性、强度、手感、色彩、花纹的皮具材料,是现代真皮制品的必须材料。
2. 再生皮:将各种动物的费皮及真皮下脚料粉碎后,调配化工原料加工制作而成,是天然皮革的替代品之一。
3. 人造革:也叫仿皮或胶料,是PVC和 PU 等人造材料的总称。
它是在纺织布基或无纺布基上,由各种不同配方的 PVC 和 PU 等发泡或覆膜加工制作而成。
二、天然革与人造革(er _tian ran ge yu ren zao ge)的识别1 看:天然皮革的表面可以看到花纹、毛孔的确存在,并且分布得不均匀;而人造革表皮无毛孔。
2 按:真皮手感富有弹性,将皮革正面向下弯折 90 度左右会出现自然皱褶,分别弯折不同部位,产生的折纹粗细、多少,有明显的不均匀,基本可以认定这是真皮,因为真皮革具有天然性的不均匀的纤维组织构成,因此形成的折皱纹路表现也有明显的不均匀;而人造革手感像塑料,回复性较差,弯折下去折纹粗细多少都相似。
3 烧:天然皮革燃烧时会发出一具有一股毛发烧焦的气味,烧成的灰烬一般易碎成粉状;而人造革产品,则有股塑料的味道,烧后发粘,冷却后会发硬变成块状。
【人造革的主要品种】*[PVC人造革(聚氯乙烯(简称PVC)人造革)(ren zao ge _)]PVC人造革的优点为:质轻、易加工、耐磨、价廉;缺点是:透气性差,低温变硬而导致屈挠性差,产生龟裂和耐滑性差。
聚氨酯信息网*[PU人造革(聚氨酯(简称PU)人造革)]PU是由二元醇或多元醇与二元或多元异氰酸酯起化学反应而成的产品。
加工工艺分干法和湿法两种。
干法制成的PU人造革适宜制作靴鞋、提包和外衣。
湿法制成的人造革适宜作夹克装、风雨衣、防寒手套、羽绒服、鞋料、家具、沙发座垫和内装饰等。
*[复合人造革]复合人造革是由PVC与PU互配,或PVC、PU分别与其他材料互配进行改性。
人造革工艺介绍

人造革工艺介绍
摘要:
1.人造革的定义与分类
2.人造革的主要原料
3.人造革的生产工艺
4.人造革的应用领域
5.人造革的环保问题及解决方案
正文:
1.人造革的定义与分类
人造革,又称仿皮或胶皮,是一种以纺织品、塑料等为基材,通过加工制成的具有皮革外观和性能的制品。
人造革主要分为两大类:PVC 人造革和PU 人造革。
PVC 人造革是以PVC(聚氯乙烯)为原料制成,而PU 人造革则是以聚氨酯为原料制成。
2.人造革的主要原料
人造革的主要原料包括纺织品、聚氯乙烯(PVC)或聚氨酯(PU)等。
纺织品作为基材,PVC 或PU 则作为涂层,通过一系列工艺制成具有皮革特性的人造革。
3.人造革的生产工艺
人造革的生产工艺主要包括以下几个步骤:
(1)基材准备:选择合适的纺织品作为基材,并进行处理,如染色、烘干等。
(2)涂层制备:将PVC 或PU 与助剂、颜料等混合,制备成涂层。
(3)涂层涂覆:将制备好的涂层均匀涂覆在基材上。
(4)烘干固化:将涂覆好的人造革进行烘干,使其涂层固化。
(5)后整理:对人造革进行打磨、抛光等后整理,以提高其外观和性能。
4.人造革的应用领域
人造革因其成本低、性能稳定等优点,被广泛应用于家具、汽车内饰、鞋子、箱包、服装等领域。
5.人造革的环保问题及解决方案
人造革生产过程中可能产生一定程度的污染,如废水、废气等。
为解决环保问题,企业需加强对生产过程的环保管理,采用环保型生产工艺,如低污染生产技术、废水处理技术等,以降低生产过程中的污染排放。
人造革的定义及品种

人造革的定义及品种人造革(Artificial leather)是一种由自然革经过化学处理加工而成的合成材料,具有类似天然革的外观、质感和性能。
它广泛应用于鞋子、手袋、沙发、衣物等各个领域,是替代天然革的一种重要材料。
人造革的品种繁多,下面将介绍其中几种主要的品种。
1. PVC人造革(Polyvinyl Chloride Artificial Leather):PVC人造革是最常见且最早出现的一种人造革。
它由聚氯乙烯树脂通过加工而成,具有高强度、柔软、耐磨、易清洁等特点。
然而,PVC人造革会释放出有害物质,对环境和健康有一定影响。
2. PU人造革(Polyurethane Artificial Leather):PU人造革是PVC人造革的替代品,目前应用较为广泛。
它由聚氨酯树脂和其他辅助材料经过加工而成,具有质感好、呼吸性好、耐磨耐折、环保等特点。
PU人造革可以在外观上模拟各种天然革的纹理和光泽度,且易于清洁和保养。
3. 微纤维人造革(Microfiber Artificial Leather):微纤维人造革是一种以超细纤维为原料制成的人造革。
它具有柔软、透气、透湿、耐磨、易清洗等特点。
微纤维人造革的纤维细度很小,可以模拟天然革的细腻质感和外观效果,广泛用于高档鞋子、箱包和家具等领域。
4. 真皮复合人造革(Bonded Leather):真皮复合人造革是通过混合一定比例的真皮粉末与塑料基材,经过加工制成的一种人造革。
它既保留了部分天然革的质感和纹理,又具有较好的强度和耐磨性,价格相对较低。
5. 仿麂皮人造革(Suede Artificial Leather):仿麂皮人造革是一种模仿麂皮外观和质感的人造革。
它具有绒毛质感,柔软舒适,透气性好,广泛应用于鞋子、包包和家居用品等领域。
以上是人造革的几种主要品种,每种品种都有各自的特点和应用领域。
随着科技的发展和人们环保意识的提高,人造革的品质和性能将继续改良和提升,为人们提供更多替代天然革的选择。
人造革基本知识
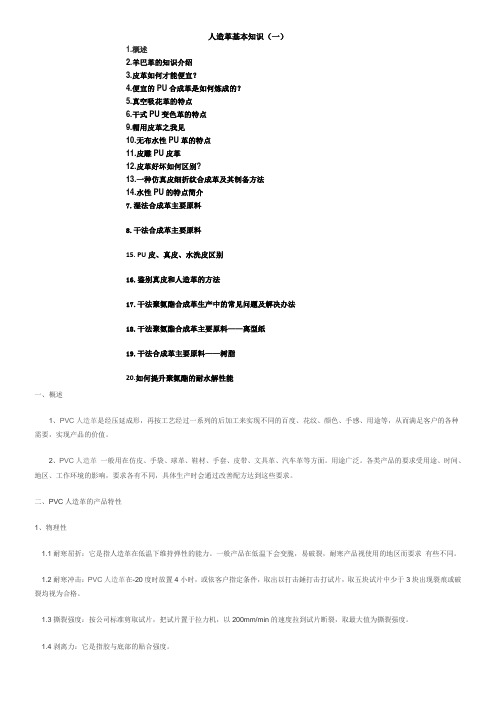
人造革基本知识(一)1.概述2.羊巴革的知识介绍3.皮革如何才能便宜?4.便宜的PU合成革是如何炼成的?5.真空吸花革的特点6.干式PU变色革的特点9.帽用皮革之我见10.无布水性PU革的特点11.皮雕PU皮革12.皮革好坏如何区别?13.一种仿真皮细折纹合成革及其制备方法14.水性PU的特点简介7.湿法合成革主要原料8.干法合成革主要原料15. PU皮、真皮、水洗皮区别16.鉴别真皮和人造革的方法17.干法聚氨酯合成革生产中的常见问题及解决办法18.干法聚氨酯合成革主要原料——离型纸19.干法合成革主要原料——树脂20.如何提升聚氨酯的耐水解性能一、概述1、PVC人造革是经压延成形,再按工艺经过一系列的后加工来实现不同的百度、花纹、颜色、手感、用途等,从而满足客户的各种需要,实现产品的价值。
2、PVC人造革一般用在仿皮、手袋、球革、鞋材、手套、皮带、文具革、汽车革等方面。
用途广泛。
各类产品的要求受用途、时间、地区、工作环境的影响,要求各有不同,具体生产时会通过改善配方达到这些要求。
二、PVC人造革的产品特性1、物理性1.1耐寒屈折:它是指人造革在低温下维持弹性的能力。
一般产品在低温下会变脆,易破裂,耐寒产品视使用的地区而要求有些不同。
1.2耐寒冲击:PVC人造革在-20度时放置4小时,或依客户指定条件,取出以打击錘打击打试片,取五块试片中少于3块出现裂痕或破裂均视为合格。
1.3撕裂强度:按公司标准剪取试片,把试片置于拉力机,以200mm/min的速度拉到试片断裂,取最大值为撕裂强度。
1.4剥离力:它是指胶与底部的贴合强度。
1.5坚牢度:指油墨或处理浆粘附产品表面的能力。
1.6色牢度:指颜色维持不变的特性1.7手感:指用手触摸人造革的感觉,包括软硬度、手感表面和Q感。
软硬度指产品之软硬程度;表面手感是指同一方向触摸样板与附板表面,并对触摸感觉进行比较:Q感(抓感)指抓过产品表面放开后,胶布是否容易恢复,是否存在折白。
生活养生-人造革和真皮的区别
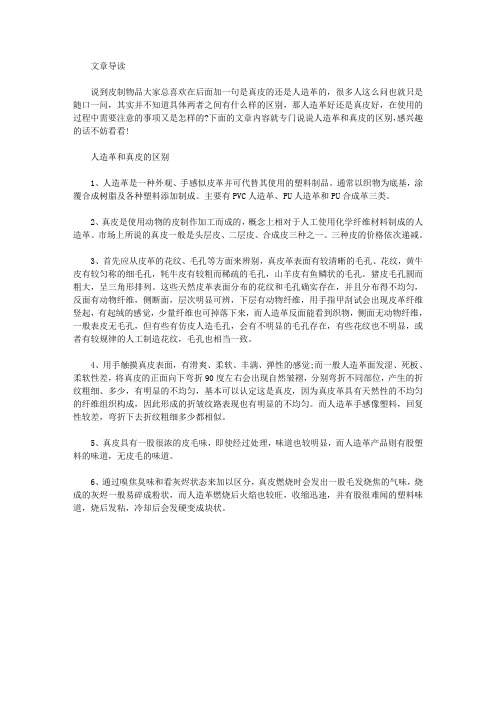
文章导读说到皮制物品大家总喜欢在后面加一句是真皮的还是人造革的,很多人这么问也就只是随口一问,其实并不知道具体两者之间有什么样的区别,那人造革好还是真皮好,在使用的过程中需要注意的事项又是怎样的?下面的文章内容就专门说说人造革和真皮的区别,感兴趣的话不妨看看!人造革和真皮的区别1、人造革是一种外观、手感似皮革并可代替其使用的塑料制品。
通常以织物为底基,涂覆合成树脂及各种塑料添加制成。
主要有PVC人造革、PU人造革和PU合成革三类。
2、真皮是使用动物的皮制作加工而成的,概念上相对于人工使用化学纤维材料制成的人造革。
市场上所说的真皮一般是头层皮、二层皮、合成皮三种之一。
三种皮的价格依次递减。
3、首先应从皮革的花纹、毛孔等方面来辨别,真皮革表面有较清晰的毛孔、花纹,黄牛皮有较匀称的细毛孔,牦牛皮有较粗而稀疏的毛孔,山羊皮有鱼鳞状的毛孔。
猪皮毛孔圆而粗大,呈三角形排列。
这些天然皮革表面分布的花纹和毛孔确实存在,并且分布得不均匀,反面有动物纤维,侧断面,层次明显可辨,下层有动物纤维,用手指甲刮试会出现皮革纤维竖起,有起绒的感觉,少量纤维也可掉落下来,而人造革反面能看到织物,侧面无动物纤维,一般表皮无毛孔,但有些有仿皮人造毛孔,会有不明显的毛孔存在,有些花纹也不明显,或者有较规律的人工制造花纹,毛孔也相当一致。
4、用手触摸真皮表面,有滑爽、柔软、丰满、弹性的感觉;而一般人造革面发涩、死板、柔软性差,将真皮的正面向下弯折90度左右会出现自然皱褶,分别弯折不同部位,产生的折纹粗细、多少,有明显的不均匀,基本可以认定这是真皮,因为真皮革具有天然性的不均匀的纤维组织构成,因此形成的折皱纹路表现也有明显的不均匀。
而人造革手感像塑料,回复性较差,弯折下去折纹粗细多少都相似。
5、真皮具有一股很浓的皮毛味,即使经过处理,味道也较明显,而人造革产品则有股塑料的味道,无皮毛的味道。
6、通过嗅焦臭味和看灰烬状态来加以区分,真皮燃烧时会发出一股毛发烧焦的气味,烧成的灰烬一般易碎成粉状,而人造革燃烧后火焰也较旺,收缩迅速,并有股很难闻的塑料味道,烧后发粘,冷却后会发硬变成块状。
人造革标准
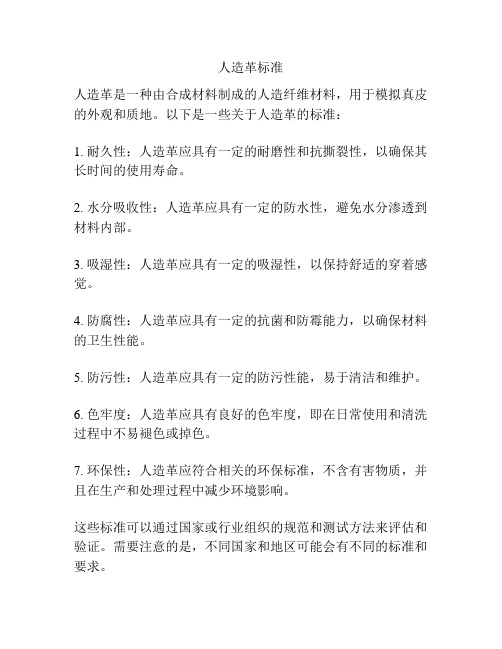
人造革标准
人造革是一种由合成材料制成的人造纤维材料,用于模拟真皮的外观和质地。
以下是一些关于人造革的标准:
1. 耐久性:人造革应具有一定的耐磨性和抗撕裂性,以确保其长时间的使用寿命。
2. 水分吸收性:人造革应具有一定的防水性,避免水分渗透到材料内部。
3. 吸湿性:人造革应具有一定的吸湿性,以保持舒适的穿着感觉。
4. 防腐性:人造革应具有一定的抗菌和防霉能力,以确保材料的卫生性能。
5. 防污性:人造革应具有一定的防污性能,易于清洁和维护。
6. 色牢度:人造革应具有良好的色牢度,即在日常使用和清洗过程中不易褪色或掉色。
7. 环保性:人造革应符合相关的环保标准,不含有害物质,并且在生产和处理过程中减少环境影响。
这些标准可以通过国家或行业组织的规范和测试方法来评估和验证。
需要注意的是,不同国家和地区可能会有不同的标准和要求。
人造合成革分类
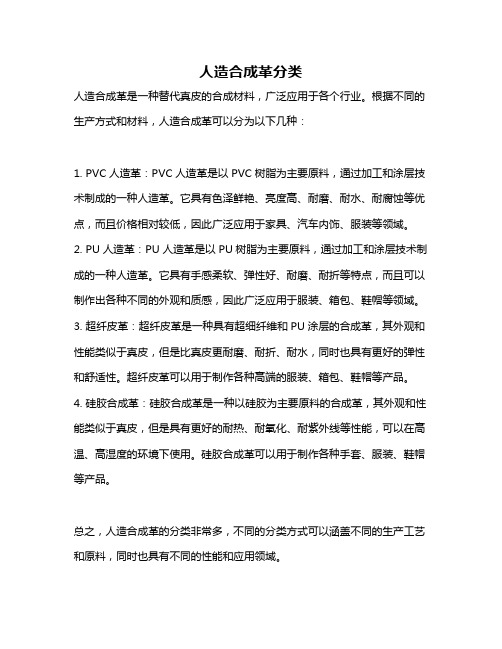
人造合成革分类
人造合成革是一种替代真皮的合成材料,广泛应用于各个行业。
根据不同的生产方式和材料,人造合成革可以分为以下几种:
1. PVC人造革:PVC人造革是以PVC树脂为主要原料,通过加工和涂层技术制成的一种人造革。
它具有色泽鲜艳、亮度高、耐磨、耐水、耐腐蚀等优点,而且价格相对较低,因此广泛应用于家具、汽车内饰、服装等领域。
2. PU人造革:PU人造革是以PU树脂为主要原料,通过加工和涂层技术制成的一种人造革。
它具有手感柔软、弹性好、耐磨、耐折等特点,而且可以制作出各种不同的外观和质感,因此广泛应用于服装、箱包、鞋帽等领域。
3. 超纤皮革:超纤皮革是一种具有超细纤维和PU涂层的合成革,其外观和性能类似于真皮,但是比真皮更耐磨、耐折、耐水,同时也具有更好的弹性和舒适性。
超纤皮革可以用于制作各种高端的服装、箱包、鞋帽等产品。
4. 硅胶合成革:硅胶合成革是一种以硅胶为主要原料的合成革,其外观和性能类似于真皮,但是具有更好的耐热、耐氧化、耐紫外线等性能,可以在高温、高湿度的环境下使用。
硅胶合成革可以用于制作各种手套、服装、鞋帽等产品。
总之,人造合成革的分类非常多,不同的分类方式可以涵盖不同的生产工艺和原料,同时也具有不同的性能和应用领域。
人造革研究报告

人造革研究报告
人造革作为一种新型的人造材料,在近些年来得到了广泛的应用,其中包括用于制造衣物的服装鞋帽,用于运动用品的护具和用于装饰的各种家居产品等。
因此,了解关于人造革的结构、性质、用途和未来发展趋势,对于开发人造革的新产品以及提高产品质量,都有十分重要的意义。
一、人造革的结构及性质
人造革由聚氨酯树脂和革状材料组成。
它具有良好的拉伸性能,弹性和抗老化性能,光泽度,硬度和综合耐久性能等特点,以及抗污性能,耐水性能和防腐性能等优势。
此外,它还具有耐温性能,并且不会缩水,具有透气性和耐磨性,可以保证产品可以在各种环境条件下正常使用。
二、人造革用途
1、服装鞋帽:人造革因具有良好的抗拉伸性能,抗老化性能和
防水性能等优势,能够被用于制造服装、鞋帽等。
2、护具:人造革因其具有良好的弹性,抗紫外线性能和耐水性
能等特点,能够被用于生产防护类运动护具,使用这类产品可以有效的保护运动者的安全。
3、家具:人造革具有良好的柔软性,抗褪色性能和抗污染性能
等优点,能够被用于制作家具,比如沙发,椅子等,起到装饰和实用作用。
三、人造革的未来发展趋势
预计,未来几年,人造革将得到更广泛的应用,在服装鞋帽、护具、家居等领域都将大为发展。
伴随着科学技术的进步,人造革将在性能上有更大的改善,并开发出更多可以满足市场需求的产品,成为未来发展的重要方向。
综上所述,人造革是一种新型的人造材料,具有优良的性能及良好的用途,未来发展前景广阔,将发挥重要的作用。
因此,我们应当努力研究和开发人造革,以满足市场的需要,促进相关行业的发展。
- 1、下载文档前请自行甄别文档内容的完整性,平台不提供额外的编辑、内容补充、找答案等附加服务。
- 2、"仅部分预览"的文档,不可在线预览部分如存在完整性等问题,可反馈申请退款(可完整预览的文档不适用该条件!)。
- 3、如文档侵犯您的权益,请联系客服反馈,我们会尽快为您处理(人工客服工作时间:9:00-18:30)。
最简单的人造革是将一层塑料薄膜贴在布上。
找个黑塑料袋,撕一块,用万能胶粘在布上,你就制成一块人造革。
跟做自行车雨披的那种料子差不多。
聚氯乙烯(PVC)是一种塑料,有一种是悬浮法合成,粉状,加了增塑剂后,变成浆糊,涂在布上面,烘一下,就塑化成薄膜且粘在布上。
这是直接涂布法PVC人造革。
把PVC糊刮涂在一种特制纸上,烘干塑化成薄膜,再在上面涂胶水,贴上布,将纸剥掉,得到革,有点象撕伤风止痛膏。
纸上有立体花纹的话,革上就有花纹,深浅高低相反。
这是间接涂布法PVC人造革。
聚氨脂(PU)树脂原材料是很稠硬的糊,加溶剂变稀,也可以涂在布上纸上,用类似PVC直接刮涂,间接刮涂制革,称为干法PU人造革。
想想把油漆涂在光溜的油纸上,再压贴上胶布,撕开,漆膜贴在胶布上,得到有涂层的布。
这成了革。
还有一种PVC,粉状,加增塑剂还是粉状,把它倒在两根平行并列,同时向内旋转的热辊之间,PVC 粉就挤拉剪切成胶团.成薄膜,象和面擀胶子皮。
薄膜贴上布就成。
这是PVC压延法人造革。
还有螺杆挤出的,不多见.如果只将人造革看作塑料薄膜贴在布上,则过于简单,进一步改进如下在薄膜和布之间加一夹层,PVC发泡层,象馒头海绵那种结构,皮革变厚,丰满弹性比真皮还好,更别提以假乱真了。
绝大多数人造革都有这一层。
也就是一面层一发泡层一层布,共三层。
两层的太原始。
以上的那些PVC,PU材料里加上色料,就有各种颜色。
那些塑料膜只在加热后象橡皮泥一样有塑性,刻了立体花纹的钢辊可在上面压出花纹,冷却后花纹固定定型了,这是人造革除得到立体纹路的一种方法,叫压花。
通过这些途径,人造革就有各种色彩纹路了。
鉴别人造革与真皮的一个办法是看材料的切口,有布基的是人造革。
于是用无纺布来代替布,无纺布是纤维涂上胶水,压粘成片,毛乎乎的,有点象真皮的底层。
因为仿真度更高一点,称为合成革。
合成革同人造革的区别是基布不同,但还是改不了不透气的毛病。
合成革最高境界是超纤。
用超细纤维做的无纺布,真皮看作由超细蛋白纤维交织而成,差别在一粘一织,不细看很难区分。
PU浆料放在水里,溶剂会被水萃取,浆料结成膜。
将浆料涂在布上,浸在水里,可得到胶膜复合布,这种工艺称湿法PU。
这种方法得到的膜有一些细微的小孔,有一定的透气性。
价格也高。
如果布是用超纤,采用PU湿法工艺,结构和性能都与真皮相近,十分完美,但价格已高出大部分低档真皮了。
太贵。
这种产品颠覆了合成革不透气,合成革比真皮便宜的说法。
这是高档货,大部分品牌运动鞋采用这种材料。
有单列出合成革自成一家的趋势。
为什么一定要用底布呢?不用的话,合成革很容易撕烂,机械强度不够。
进一步加强成了塑料片,同皮革差别很大,不能以假乱真,卖不出好价.只有象皮革才有好价钱仪表板表皮加工技术的介绍及最新进展搪塑成型表皮(Slush Moulded Skin)搪塑工艺是对带皮纹的搪塑模具(采用镍制壳)对背面或整体进行加热,模具和搪塑粉末的粉箱对接后旋转或一边加热一边旋转,粉箱中的塑料粉末自然落入模具中融化,热模表面上就会形成一个形状与模具一致的带皮纹的表皮,然后取下粉箱,对模具进行冷却后人工取下得到的表皮。
模具的加热主要通过热风,热砂或热油来进行。
冷却的话通过冷油,冷冻空气或冷水等媒介。
每一个成型周期都是一次模具的加热和冷却过程,温度从四五十度升高到二百多度,再降低到原来的四五十度,时间搪塑成型表皮(Slush Moulded Skin)搪塑工艺是对带皮纹的搪塑模具(采用镍制壳)对背面或整体进行加热,模具和搪塑粉末的粉箱对接后旋转或一边加热一边旋转,粉箱中的塑料粉末自然落入模具中融化,热模表面上就会形成一个形状与模具一致的带皮纹的表皮,然后取下粉箱,对模具进行冷却后人工取下得到的表皮。
模具的加热主要通过热风,热砂或热油来进行。
冷却的话通过冷油,冷冻空气或冷水等媒介。
每一个成型周期都是一次模具的加热和冷却过程,温度从四五十度升高到二百多度,再降低到原来的四五十度,时间也就是五六分钟,因此模具受到的热应力冲击很大,主要是用镍作为原料加工。
模具的寿命很短。
一般就是2~4万次。
目前全球的汽车仪表板搪塑模具制造商只有五六家,都在日本和德国等发达国家,而且由于其制作过程很大程度上依赖于技术熟练的技师,因此成本相对来说比较高。
搪塑工艺加工出来的表皮的花纹均匀,手感好,表皮的厚度均匀性也相对好,生产过程便于控制,易于掌握,但生产过程中的能耗很大的。
搪塑表皮的设计宽容度在现有的几种模塑表皮技术里面是最高的。
搪塑表皮的R角最小只能加工到1。
5毫米,再小的话,模具在承受热应力冲击时会损坏。
目前在中国的汽车行业内,PVC搪塞塑表皮被广泛应用在各种中高档车型的仪表板上,几乎超过80%的中高档车型采用了PVC材料。
因为PVC具有比较低的成本,比较成熟的应用历史,因而是很多公司的设计人员的首选。
但PVC的环保方面的不足及低温脆性一直为行业内人士所诟病。
因为低温脆性可能导致安全气囊的低温爆破实验不能通过。
另外一种用得比较多的材料是热塑性聚氨酯(TPU),主要是在日本的中高档车上,例如丰田的凯美瑞,日产的08款天籁,马自达6等。
与PVC 相比,TPU 的优点是:抗紫外线和长期热老化性能好,密度低15%,且可在原用PVC 的加工设备上生产。
其材料价格大概比PVC 高出3 倍多。
但是采用TPU从经济角度考虑是合算的。
其原因是TPU 密度较小且可省去若干项其他工序和操作。
Bayer 公司和Textron汽车公司共同开发了热塑型聚氨酯(TPU)仪表板面层Texin DPT-3014,以取代PVC,并用于ChryslerConcorde,Chrysler LHS,Chrysler 300M 等车型上。
TPU不含任何增塑剂和卤素,而且在低温时仍具有很好的弹性,因此在寒冷环境下不易开裂,这对安全气囊的安全性能是至关重要的。
此外,美国DELPHI公司曾经开发过TPO的材料用于搪塑,只是未能得到推广和应用。
聚氨酯喷涂成型表皮(PU Spray Skin)聚氨酯喷涂成型表皮(PU Spray Skin)的加工工艺过程是:将两组分的聚氨酯原料在经过计量设备精确计量后增压至高压状态,再经高压混合反应,然后喷涂到镍壳模具上,聚氨酯附着在镍壳上成为一张表皮。
在此过程中,两组分聚氨酯的混合反应属于化学反应,反应完成后起形状和尺寸及固定下来.它不像热塑性材料那样容易受使用外部物理条件的影响,因此材料具有良好环境适用性能。
一般上,表皮的厚度可以通过喷涂的时间和流量来调节和控制。
该工艺过程中,喷涂混合头一般由机器人操纵,为了便于机器人在很小的空间内灵活地移动,通常要求机器人的结构要紧凑,体积要小。
原料冲混合头出来是为液态,流动性非常好. 作为中高档汽车A面表皮的应用量逐渐增加的加工方法之一,聚氨酯喷涂成型工艺具有如下优点: ●可产生清晰的表皮纹理;而且皮纹的深度可以达到300微米,是目前皮纹复制性最好的技术●表皮的手感非常好,给人的感觉好像不是塑料●表皮具有良好的抗紫外线照射性能;●表皮颜色具有良好的一致性;●可较为容易地实现双色或者多色●设计宽容度高,●可以加工小至0。
5毫米的R角,更好地满足造型要求●可以嵌入其他材料,例如织物或塑料,真皮等●耐热性和耐老化性能好;●可以生产光泽度较低的表皮●可以采用多种模具,模具使用寿命长;而且可以在同一模具的不同区域实现不同的花纹对于采用隐形安全气囊的仪表板而言,上述优点尤为明显,聚氨酯材料在低温下的弹性仍然很好,低温爆破实验很容易满足实验要求.。
该工艺的不足之处主要体现在生产的节拍时间比较长,同时表皮的厚度的控制在某些情况下相对搪塑要难一些.在欧洲和美国,聚氨酯喷涂成型工艺主要被用于中高档汽车上,如宝马3、5系,奔驰C,E,S级,大众PASSAT B6,通用凯迪拉克CTS等。
尽管目前其应用还不及搪塑和吸塑那样广泛,但其优点正在逐渐为业内所认可,因此应用范围正在逐渐扩大。
在国内,目前已经有几款车型采用了该工艺技术,例如上海大众的斯科达明锐,宝马的3系和5系,奔驰的C级车和E级车,VOLVO的S80等。
目前的材料分为两个体系, 脂肪族和芳香族. 其中脂肪族的抗紫外线性性能好,但价格较高. 芳香族的耐侯性差, 作为仪表板表皮时需要喷涂一层抗紫外线的油漆,但价格稍低. 瑞克赛尔公司目前已经开发了新一代的材料,COLOR-SENSE, 将脂肪族的材料做为外表面, 达到比较好的抗紫外线的效果, 同时以芳香族的材料作为底层, 在满足物理性能要求的情况下降低材料成本. 图:嵌入纺织面料的双色仪表板表皮注射成型的聚氨酯表皮(RIM-Skin) 利用高压注射机对PU原料进行计量和混合,然后将其注入到模具内成型,从而可生成注射成型的聚氨酯表皮(RIM-SKIN)。
与喷涂成型工艺所不同的是,注射成型技术在短短的几秒钟内即可完成,原料在充模后能够很快进入固化状态,表皮厚度一般与模具型腔高度完全一致。
该工艺的优点是产品的设计自由度较大。
但是,由于是在闭模状态下进行注射,再加上表皮厚度通常比较小,因此为充模带来了一定的难度,要求上下模闭合后要形成密闭的型腔。
此外,为了保证产品的最终质量,与A面表皮接触的模具部分最好采用镍壳或钢材料,这些都使模具成本明显提高。
除了具有聚氨酯材料本身的优点之外,注射成型表皮的另一主要优点的表皮的厚度可以得到有效的控制,厚度均匀度可以做得很好。
注射成型的时间也非常短,因此生产效率比较高。
该工艺的不足之处是设计宽容度不高,模具的成本很高。
同时,结构比较复杂的零件可能由于充模不满的问题导致表皮的报废。
目前在欧洲投产的斯科达SUPERB的仪表板手套箱的表皮就是采用注射成型的表皮,该技术在我国也已经投入使用。
图:注射成型仪表板表皮的OPEL ASTRA 真皮(Leather)真皮作为高档次和高品质的代名词, 在各种消费品领域得到广泛的应用. 汽车行业也不例外. 真皮在高档的汽车上也得到了广泛的应用. 真皮毛孔清晰、细小、紧密、排列不规律,表面丰满细致,富有弹性及良好的透气性,使用舒适耐久且美观。
人们不仅把真皮装饰当做一件享受的舒适化装备,更把它当做是显示档次、体现豪华的标志。
真皮的背部发泡目前,高档汽车的内饰表皮大多采用真皮。
以宝马7系车型为例,该车型最高配置版本中的仪表板就是采用真皮背部发泡(Leather Back Foaming)工艺制成的。
其工艺过程是:首先进行真皮的预成型,然后将真皮转移至发泡模具内并定位好,最后进行背部发泡。
通常,由于真皮非常柔软,因此其表皮的预成型不是采用搪塑或喷涂成型的方法,而是采用先裁剪再缝制的方式加工出来,加工好的表皮也主要由人工将其定位到模具内,然后进行背部发泡。
这个过程一般需要30~60分钟的时间,而这也正是采用该工艺进行批量生产的不足之处。