工业控制的应用现状和发展趋势
工业控制系统的技术发展和趋势
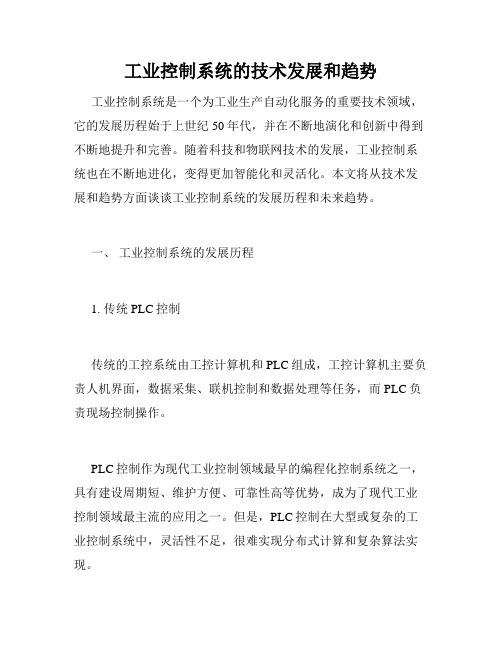
工业控制系统的技术发展和趋势工业控制系统是一个为工业生产自动化服务的重要技术领域,它的发展历程始于上世纪50年代,并在不断地演化和创新中得到不断地提升和完善。
随着科技和物联网技术的发展,工业控制系统也在不断地进化,变得更加智能化和灵活化。
本文将从技术发展和趋势方面谈谈工业控制系统的发展历程和未来趋势。
一、工业控制系统的发展历程1. 传统PLC控制传统的工控系统由工控计算机和PLC组成,工控计算机主要负责人机界面,数据采集、联机控制和数据处理等任务,而PLC负责现场控制操作。
PLC控制作为现代工业控制领域最早的编程化控制系统之一,具有建设周期短、维护方便、可靠性高等优势,成为了现代工业控制领域最主流的应用之一。
但是,PLC控制在大型或复杂的工业控制系统中,灵活性不足,很难实现分布式计算和复杂算法实现。
2. DCS随后,随着工业控制领域的不断发展和智能化趋势,DCS(分布式控制系统)等控制策略应运而生。
DCS控制针对大型复杂工业系统,其主要优点在于强大的控制能力、多点测量、多点操作,其相对于PLC控制而言为一种灵活高效的分布式控制方法,而且DCS可以方便的实现大规模的集群控制,是工业控制系统的发展之一。
3. PC控制现代工业控制系统中,随着工控技术的不断进步和计算机性能的不断提高,基于PC控制的技术应运而生。
它基于通用计算机平台,摆脱了传统的特殊硬件和编程方式,使得整个系统的开发成本大大降低,同时也提高了整个系统的可定制性和可升级性。
4. 大数据大数据技术的发展给现代工业控制系统带来了重要影响。
在控制系统中,消息传递和大数据分析应用价值非常高,可以利用大数据技术来分析工业控制中的各种问题,包括控制精度、稳定性、系统故障等,有效提高工业生产的效率和质量。
二、工业控制系统的未来趋势1. 智能化化、网络化、集成化现代工业控制要实现智能化,那么工业控制系统就需要更加智能。
随着制造业的深入开展,自动化成为未来产业中一项不可或缺的技术,未来工业控制系统将向网络化、智能化、集成化的方向发展,将很多机器和设备的信息通过物联网或其他技术进行互联,以实现更加丰富、精准、可靠的处理和控制,以达到更好的结果。
控制系统的未来发展趋势:探讨控制系统的未来发展趋势和应用前景
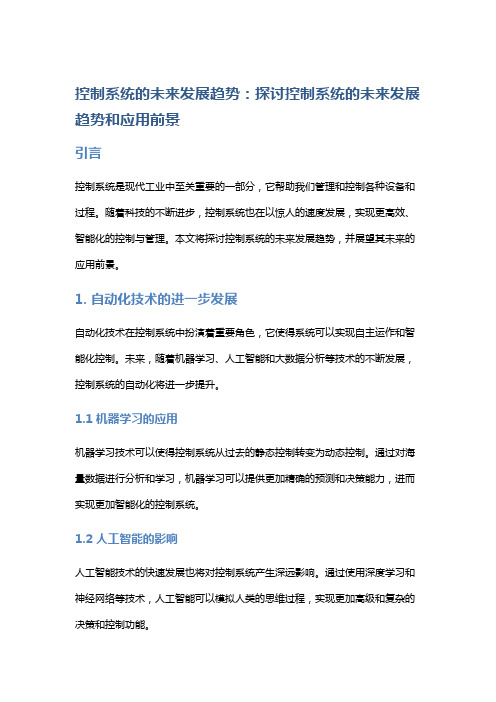
控制系统的未来发展趋势:探讨控制系统的未来发展趋势和应用前景引言控制系统是现代工业中至关重要的一部分,它帮助我们管理和控制各种设备和过程。
随着科技的不断进步,控制系统也在以惊人的速度发展,实现更高效、智能化的控制与管理。
本文将探讨控制系统的未来发展趋势,并展望其未来的应用前景。
1. 自动化技术的进一步发展自动化技术在控制系统中扮演着重要角色,它使得系统可以实现自主运作和智能化控制。
未来,随着机器学习、人工智能和大数据分析等技术的不断发展,控制系统的自动化将进一步提升。
1.1 机器学习的应用机器学习技术可以使得控制系统从过去的静态控制转变为动态控制。
通过对海量数据进行分析和学习,机器学习可以提供更加精确的预测和决策能力,进而实现更加智能化的控制系统。
1.2 人工智能的影响人工智能技术的快速发展也将对控制系统产生深远影响。
通过使用深度学习和神经网络等技术,人工智能可以模拟人类的思维过程,实现更加高级和复杂的决策和控制功能。
2. 多领域融合的趋势控制系统作为一个广泛应用于各个领域的技术,未来的发展将更加注重多领域融合。
不同领域的知识和技术相互结合,将为控制系统带来更多的创新和应用。
2.1 工业控制系统的进化工业控制系统的发展已经成为工业领域的重要趋势。
随着工业4.0的普及,各个工业过程将更加智能化和自动化。
通过将传感器、机器人和数据分析等技术应用于控制系统中,工业控制系统将实现更高效、精确和可靠的控制。
2.2 建筑控制系统的创新建筑控制系统也将受益于多领域融合的趋势。
通过将建筑设计、能源管理和环境控制等领域的知识结合,建筑控制系统将实现更加智能和节能的控制。
例如,通过智能化的照明系统和空调系统,建筑可以自动适应人员的需求,提高能源利用效率。
2.3 交通控制系统的发展随着城市化的进程,交通管控成为一个重要的挑战。
控制系统在交通领域的应用也将不断发展。
通过将交通流量分析、信号控制和优化算法等技术融合,交通控制系统可以实现更加高效和安全的交通管理。
工业控制的应用现状
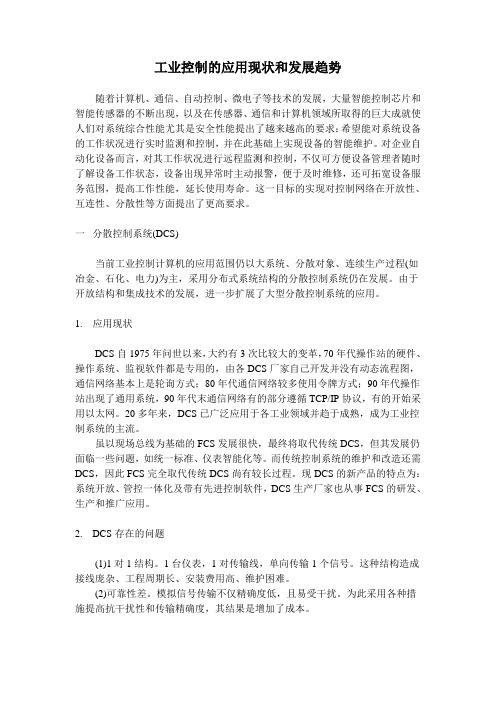
工业控制的应用现状和发展趋势随着计算机、通信、自动控制、微电子等技术的发展,大量智能控制芯片和智能传感器的不断出现,以及在传感器、通信和计算机领域所取得的巨大成就使人们对系统综合性能尤其是安全性能提出了越来越高的要求:希望能对系统设备的工作状况进行实时监测和控制,并在此基础上实现设备的智能维护。
对企业自动化设备而言,对其工作状况进行远程监测和控制,不仅可方便设备管理者随时了解设备工作状态,设备出现异常时主动报警,便于及时维修,还可拓宽设备服务范围,提高工作性能,延长使用寿命。
这一目标的实现对控制网络在开放性、互连性、分散性等方面提出了更高要求。
一分散控制系统(DCS)当前工业控制计算机的应用范围仍以大系统、分散对象、连续生产过程(如冶金、石化、电力)为主,采用分布式系统结构的分散控制系统仍在发展。
由于开放结构和集成技术的发展,进一步扩展了大型分散控制系统的应用。
1. 应用现状DCS自1975年问世以来,大约有3次比较大的变革,70年代操作站的硬件、操作系统、监视软件都是专用的,由各DCS厂家自己开发并没有动态流程图,通信网络基本上是轮询方式;80年代通信网络较多使用令牌方式;90年代操作站出现了通用系统,90年代末通信网络有的部分遵循TCP/IP协议,有的开始采用以太网。
20多年来,DCS已广泛应用于各工业领域并趋于成熟,成为工业控制系统的主流。
虽以现场总线为基础的FCS发展很快,最终将取代传统DCS,但其发展仍面临一些问题,如统一标准、仪表智能化等。
而传统控制系统的维护和改造还需DCS,因此FCS完全取代传统DCS尚有较长过程。
现DCS的新产品的特点为:系统开放、管控一体化及带有先进控制软件,DCS生产厂家也从事FCS的研发、生产和推广应用。
2. DCS存在的问题(1)1对1结构。
1台仪表,1对传输线,单向传输1个信号。
这种结构造成接线庞杂、工程周期长、安装费用高、维护困难。
(2)可靠性差。
模拟信号传输不仅精确度低,且易受干扰。
工业控制自动化的现状及趋势

浅谈工业控制自动化的现状及趋势摘要:工业控制自动化技术的产生对现代制造业领域产生了重大的影响,大大提高了企业生产过程中的效率,完成了很多复杂重要的工业生产。
本文就我国工业控制自动化发展中存在的优缺点进行总结,并展望了将来的发展趋势,以期为我国工业控制自动化技术的发展及相关从业人员提供理论或者实际参考意见。
关键词:工业控制;自动化;现状;趋势中图分类号:tp273 文献标识码:a 文章编号:1007-9599 (2013) 02-0000-02工业控制自动化技术是一种先进的工业制造技术,其技术水平已成为衡量一个国家国民经济发展水平和现代化程度的标志。
据统计,对自动化控制系统投入和企业效益方面提升产出比约在1:4 至1:6之间,是实现大规模工业生产安全、平稳、优质、高效的基本条件和重要保证,是传统产业优化升级的有效手段,对钢铁、石化、冶金、电力、纺织等支柱性产业的技术进步具有重要作用。
工业控制自动化的产品和技术大力推广了中国的制造业自动化进程,为中国现代化的建设做出了巨大的贡献。
1 工业控制自动化现状我国工业自动化制造产业经过一段时间发展,已经逐步实现国产化的过程。
在下游冶金、石化等行业的需求以及自动化率提升的双重带动下,我国工业自动化控制系统装置制造产业取得了长足的发展。
但是,我国工业自动化具有自己的特点,下面就对我国自动化的优势和劣势进行简要总结。
1.1 我国工业控制自动化的优势从整体上看,我国工业控制自动化具有以下优势,第一、工业控制自动化产品技术含量高,专业性强,而且产品繁多,业内第一门户网站;中国自动化学会的唯一门户网站及合作网站中国工控网目前分类达16个大项,200余个小项,第二、厂商众多,全球厂商达20万家,仅变频器的生产商就达2000余家;第三、市场巨大,90年代以来,我国工业自动化控制系统装置制造产业的产量一直保持在年增长20%以上,2009年我国仪器仪表行业规模以上企业5,363个,完成工业总产值4,047亿元,销售产值3,947亿元,其中工业自动控制系统装置占比约21.26%,达到843亿元。
工业自动化控制的现状和发展趋势
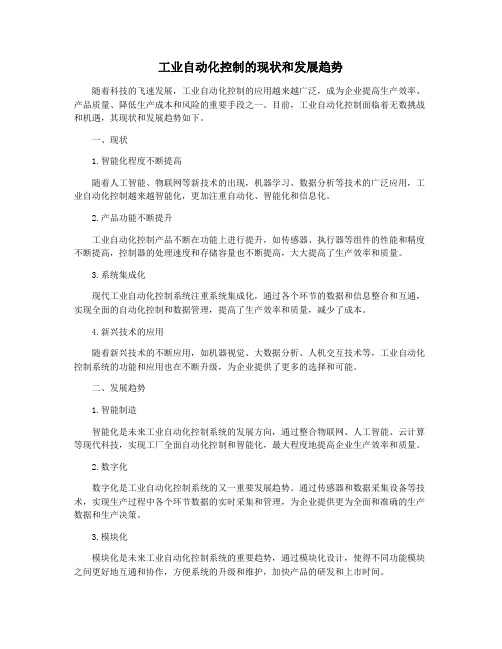
工业自动化控制的现状和发展趋势随着科技的飞速发展,工业自动化控制的应用越来越广泛,成为企业提高生产效率、产品质量、降低生产成本和风险的重要手段之一。
目前,工业自动化控制面临着无数挑战和机遇,其现状和发展趋势如下。
一、现状1.智能化程度不断提高随着人工智能、物联网等新技术的出现,机器学习、数据分析等技术的广泛应用,工业自动化控制越来越智能化,更加注重自动化、智能化和信息化。
2.产品功能不断提升工业自动化控制产品不断在功能上进行提升,如传感器、执行器等组件的性能和精度不断提高,控制器的处理速度和存储容量也不断提高,大大提高了生产效率和质量。
3.系统集成化现代工业自动化控制系统注重系统集成化,通过各个环节的数据和信息整合和互通,实现全面的自动化控制和数据管理,提高了生产效率和质量,减少了成本。
4.新兴技术的应用随着新兴技术的不断应用,如机器视觉、大数据分析、人机交互技术等,工业自动化控制系统的功能和应用也在不断升级,为企业提供了更多的选择和可能。
二、发展趋势1.智能制造智能化是未来工业自动化控制系统的发展方向,通过整合物联网、人工智能、云计算等现代科技,实现工厂全面自动化控制和智能化,最大程度地提高企业生产效率和质量。
2.数字化数字化是工业自动化控制系统的又一重要发展趋势。
通过传感器和数据采集设备等技术,实现生产过程中各个环节数据的实时采集和管理,为企业提供更为全面和准确的生产数据和生产决策。
3.模块化模块化是未来工业自动化控制系统的重要趋势,通过模块化设计,使得不同功能模块之间更好地互通和协作,方便系统的升级和维护,加快产品的研发和上市时间。
4.可持续性发展在工业自动化控制系统的设计和开发过程中,可持续性发展也越来越受到重视,通过采用低耗能、低碳排放的技术手段,实现对环境的有效保护和节能减排,最大限度地提升社会效益。
综上所述,工业自动化控制作为现代工业制造的重要手段,正处于快速发展和变革的阶段,其智能化、数字化、模块化等趋势将越来越明显地影响着工业自动化的发展方向和趋势。
工业控制技术的研究和应用

工业控制技术的研究和应用随着科技的不断发展,工业控制技术越来越得到人们的重视,成为工业生产领域中不可或缺的一部分。
本文将从工业控制技术的基本概念、研究方向以及应用领域等多个方面阐述这一领域的研究现状以及未来的发展方向。
一、工业控制技术的基本概念工业控制技术是一门应用技术学科,主要研究如何通过对工业过程进行测量和控制,实现工业生产的自动化、智能化和优化化。
具体来讲,它包括数字信号处理、嵌入式系统、自动控制、供电系统、计算机网络等众多技术领域。
其中,嵌入式控制技术作为工业控制技术的一个重要分支,是指将微处理器和外围部件(包括传感器、执行器等)集成到单个微控制器中,用于实现对工业过程的控制。
工业控制技术的应用范围非常广泛,包括了各种制造业领域,如汽车制造、电子制造、机械制造等。
此外,它也可以应用在电力、交通、航空等基础设施领域中,如可编程逻辑控制器(PLC)工业自动化系统、建筑安全控制系统、智能交通系统等。
二、工业控制技术的研究方向在当前这个数字化和信息化的时代,工业控制技术的研究方向也在不断地发生变化,主要体现在以下几个方面:1.可编程控制技术:可编程控制器是一种特殊的计算机,它能够实现控制器和执行器之间的信息交互,实现工业过程的自动化。
目前,可编程控制技术在工业制造和生产控制中已得到广泛应用,尤其是在现代智能工厂建设中。
2.新型传感技术:随着微电子技术、纳米技术的发展,新型传感器的应用前景越来越广阔。
目前,新型传感技术已经实现了微传感器、光纤传感、生物电传感等多种形式。
这些传感器的应用将为工业控制技术提供更加精准和灵活的测量手段。
3.人工智能技术:人工智能技术的发展和应用不仅推动了工业控制技术本身的发展,同时也带来了对传统工业制造模式的挑战。
在工业制造领域,人工智能技术主要应用于生产管理、质量检测、供应链管理等领域,帮助企业实现智能化和自动化。
三、工业控制技术的应用领域在工业控制技术的应用领域中,生产自动化和智能化生产是其中的重要部分。
2024年工控市场前景分析
2024年工控市场前景分析引言工业控制系统(Industrial Control System,简称ICS)是指用于监控和控制工业过程的计算机系统和网络。
工控系统广泛应用于各个行业,如能源、制造、交通等。
本文旨在对工控市场的前景进行分析,探讨其发展趋势和商机。
工控市场的现状目前的工控市场已经建立了一套较为成熟的基础架构,包括硬件设备、软件系统和通信网络等。
工控系统在实现自动化、提高生产效率和质量的过程中发挥着重要作用。
然而,随着科技的不断进步和市场需求的变化,工控市场正在面临一些新的挑战和机遇。
工控市场的发展趋势1. 云计算与大数据云计算和大数据技术的发展使得工控系统能够更好地收集、存储和分析数据。
通过云计算平台,工控系统可以实现数据共享、远程访问和智能化决策,提高生产效率和资源利用率。
2. 物联网技术的应用物联网技术的快速发展为工控市场带来了新的机遇。
通过将工业设备和传感器连接到互联网,工控系统可以实现实时监控、远程诊断和智能控制,进一步提高生产过程的安全性和可靠性。
3. 人工智能与机器学习人工智能和机器学习技术的应用可以使工控系统具备更智能化的功能。
通过分析和学习大量的数据,工控系统可以自动调整参数、预测故障并提供优化方案,帮助企业提高生产效率和产品质量。
4. 安全性的提升随着工控系统的互联化和智能化程度的提高,安全性问题变得更加重要。
工控系统面临来自网络攻击、数据泄露和设备故障等多重威胁。
因此,工控系统安全性的提升成为未来发展的重点和挑战。
工控市场的商机随着工控市场的发展,相关企业和服务供应商面临着巨大的商机。
以下是一些可能的商机:1.硬件设备供应商:工控系统需要大量的硬件设备,包括传感器、执行器和控制器等。
相关供应商可以利用市场需求开发出更先进和可靠的设备。
2.软件系统开发商:定制化、灵活且智能化的软件系统是工控系统的核心。
软件开发商可以开发更加高效和安全的控制系统,帮助企业提升生产效率。
工业自动化控制的现状和发展趋势
工业自动化控制的现状和发展趋势工业自动化控制,是指通过计算机、传感器、执行器等先进技术,实现对生产过程的自动化控制。
随着科技的不断发展,工业自动化控制的应用范围越来越广泛,但同时也存在着一些问题。
本文将从现状和发展趋势两个方面对工业自动化控制进行探讨。
一、现状目前,工业自动化控制已成为工业生产中不可或缺的一部分。
自动化技术的应用,使得生产效率得到了大幅度提升,同时极大地减少了人工操作的出错率,缩短了生产周期,降低了生产成本。
工业自动化控制已在制造、能源、交通、医疗、通信等领域得到了广泛应用。
1.工业机器人机器人技术是工业自动化控制的重要组成部分,已经成为现代制造业的重要工具之一。
在国内,目前工业机器人市场规模以及行业内竞争压力不断增加,预计未来市场需求会进一步扩大。
2.无人工厂随着工业自动化技术不断的普及和发展,未来的工厂将会实现无人化生产操作。
生产自动化后,不仅可以提升生产效率,还可以降低生产成本,实现更高的利润。
3.智能化在未来的自动化系统中,更多地将采用人工智能技术,实现自动控制。
智能自控技术,具有更高的适应性和自我调整能力,将会让生产效率更高、生产线更稳定,也能减少人力成本。
二、发展趋势随着工业自动化技术的持续发展,人们对其发展趋势也越来越关注。
未来,工业自动化技术将会呈现以下几个发展趋势:1.信息化与数字化未来的工业自动化设备将会进一步实现信息化与数字化,实现更高效的互联网通信。
同时,数字化的工业自动化系统也能大大提升整个生产环节的智能化程度,从而实现更高的生产效率。
2.开放性与标准化未来工业自动化系统将更多采用开放式数据接口,能够更好地灵活应用第三方技术。
同时,更多采用标准化协议的自动化系统将更加易于集成和操作,并且具有更高的稳定性和安全性。
总之,工业自动化控制为我们带来了很多便利,从极大地提升了生产效率。
而未来发展趋势的变化也让我们对工业自动化设备和系统进一步关注和研究,在未来发展中有更好的应用前景。
中国工控系统行业发展前景展望
中国工控系统行业发展前景展望一、工控系统概述工业控制系统是对诸如图像、语音信号等大数据量、高速率传输的要求,又催生了当前在商业领域风靡的以太网与控制网络的结合。
这股工业控制系统网络化浪潮又将诸如嵌入式技术、多标准工业控制网络互联、无线技术等多种当今流行技术融合进来,从而拓展了工业控制领域的发展空间,带来新的发展机遇。
1、结构从生产控制类工业软件图谱来看,其种类丰富,主要包括过程控制系统、先进过程控制与优化以及生产执行与管理三类,国产化布局相对充分,且处于企业经营管理的关键位置。
生产控制类工业软件分类示意图生产控制类工业软件分类示意图数据来源:公开资料,产业研究院整理2、发展历程我国工控系统行业是伴随着改革开放起步的,从发展路径上看,大部分企业是在引进成套设备和各种工业自动化系统的同时进行消化吸收,然后进行二次开发和应用;也有一部分企业通过引进国外技术,与外商合作合资生产工控自动化产品。
经过多年的技术积累和应用实践,我国工业自动化控制技术、产业和应用有了很大发展。
中国工控系统行业发展历程示意图中国工控系统行业发展历程示意图数据来源:公开资料,产业研究院整理二、发展背景1、政策因素站在当前时点,我国经济已经步入新常态新阶段,由高速增长阶段转向高质量发展。
由此,2017年中央经济工作会议提出“推动高质量发展是当前和今后一个时期确定发展思路、制定经济政策、实施宏观调控的根本要求”,要深化供给侧结构性改革,推进中国制造向中国创造转变,中国速度向中国质量转变,制造大国向制造强国转变。
这也促进我国工控系统行业快速发展。
中国工控系统行业相关政策梳理中国工控系统行业相关政策梳理数据来源:各政府门户网站,产业研究院整理2、社会因素工控安全事件频发,存在较大威胁。
2017年中国工业信息安全高、超危漏洞数量占比为53.6%,根据数据显示,2021年该数据已超过60%,工业信息安全问题形势严峻,涉及到国家安全和各行各业发展,因此工控系统发展势在必得。
工业自动化控制的现状和未来发展趋势
正 在 逐渐 增长 。当前 , Ehr e技 术 的扩 展 是控 制领 域 很重 要 的一 个发 展 t en t 趋 势 , PC 随 了 这 一 潮 流 。 现 在 有 的 P C 产 企 业 开 始 向 客 户 提 供 L也 L生 Eh r e接 口,使得P C t en t L 控制 系统 的开 放性 更加 广泛 。 ( )D S 2 E 控制 系 统到 现 场 总线 ( 英文 缩 写  ̄F S 的发 展 。基 于3 技 PC) c 术 的D S C 开始 向基 于 现场 总 线 的FS 向发 展 ,这 个 新方 向 的特 点是 本着 全 C方
前 ,P C L 的生产 主要 以 国外生 产厂 家 的业务 为主 ,约 3 0 型号左 右 的P C 0种 L 产
软 件 将 从人 机 界 面 朝着 先 进 控 制 的方 向发 展 ,  ̄AC ( da cd Po e s P P A vn e rc s
C n r 1 。 目前 的先进 控制 策略 主要 包括 有 : 自适应 控 制 ,预 测控 制和 鲁 o to )
生产的 灵活 性和 定制 性 。
1工 业 自动化 的产 品与 系统 组成
工 业 自动化 控制 系统 主要 包 括 了计算 机 硬件 、传 动设 各和 通信 网络 , 另 外,还 包 括检测 仪 表。 即:① 计算 机硬 件 ,主要 是指 嵌入 式的 ,还 有工 业 的及工 业控 制 的计算 机等 :② 系统 传动 设备 ,主 要有 电动 机 、伺服 系统 及 调速器 等 ;③ 通信 网络 ,主要 有通 信连 接器 、 网络交 换机 及 网桥等 。 2工 业 自动化 控葺 的现 状 下 面分别 从P C C 和P三 个 方面 介绍 ,见 下 图1 示 。 L 、DS c 所
- 1、下载文档前请自行甄别文档内容的完整性,平台不提供额外的编辑、内容补充、找答案等附加服务。
- 2、"仅部分预览"的文档,不可在线预览部分如存在完整性等问题,可反馈申请退款(可完整预览的文档不适用该条件!)。
- 3、如文档侵犯您的权益,请联系客服反馈,我们会尽快为您处理(人工客服工作时间:9:00-18:30)。
现代工业控制总线的发展趋势前言随着计算机、通信、自动控制、微电子等技术的发展,大量智能控制芯片和智能传感器的不断出现,以及在传感器、通信和计算机领域所取得的巨大成就使人们对系统综合性能尤其是安全性能提出了越来越高的要求:希望能对系统设备的工作状况进行实时监测和控制,并在此基础上实现设备的智能维护。
对企业自动化设备而言,对其工作状况进行远程监测和控制,不仅可方便设备管理者随时了解设备工作状态,设备出现异常时主动报警,便于及时维修,还可拓宽设备服务范围,提高工作性能,延长使用寿命。
这一目标的实现对控制网络在开放性、互连性、分散性等方面提出了更高要求。
一分散控制系统(DCS)当前工业控制计算机的应用范围仍以大系统、分散对象、连续生产过程(如冶金、石化、电力)为主,采用分布式系统结构的分散控制系统仍在发展。
由于开放结构和集成技术的发展,进一步扩展了大型分散控制系统的应用。
1. 应用现状DCS自1975年问世以来,大约有3次比较大的变革,70年代操作站的硬件、操作系统、监视软件都是专用的,由各DCS厂家自己开发并没有动态流程图,通信网络基本上是轮询方式;80年代通信网络较多使用令牌方式;90年代操作站出现了通用系统,90年代末通信网络有的部分遵循TCP/IP协议,有的开始采用以太网。
20多年来,DCS已广泛应用于各工业领域并趋于成熟,成为工业控制系统的主流。
虽以现场总线为基础的FCS发展很快,最终将取代传统DCS,但其发展仍面临一些问题,如统一标准、仪表智能化等。
而传统控制系统的维护和改造还需DCS,因此FCS完全取代传统DCS尚有较长过程。
现DCS的新产品的特点为:系统开放、管控一体化及带有先进控制软件,DCS生产厂家也从事FCS的研发、生产和推广应用。
2. DCS存在的问题(1)1对1结构。
1台仪表,1对传输线,单向传输1个信号。
这种结构造成接线庞杂、工程周期长、安装费用高、维护困难。
(2)可靠性差。
模拟信号传输不仅精确度低,且易受干扰。
为此采用各种措施提高抗干扰性和传输精确度,其结果是增加了成本。
(3)失控状态。
操作员在控制室既不了解现场模拟仪表的工作状况,也不能对其进行参数调整,更不能预测事故,导致操作员对其处于失控状态。
因操作员不能及时发现现场仪表故障,而发生事故已屡见不鲜。
(4)互操作性差。
尽管模拟仪表已统一4~20mA信号标准,可大部分技术参数仍由制造商自定,致使不同品牌仪表无法互换。
因此导致用户依赖制造厂,无法使用性能价格比最优的配套仪表,甚至出现个别制造商垄断市场的局面。
3. DCS在中国因我国传统产业改造和新建工程项目对DCS的急需,80年代从国外引进了几百套DCS来装备石化、冶金、电力等行业。
进入90年代,我国一些新型高科技公司进入DCS领域。
目前在国内生产的DCS不仅具有价格低廉、备品备件方便的优势,而且在技术先进、组态学习容易、技术支持有力等方面都获得用户肯定。
国内DCS生产的最新产品具有系统开放、兼容现场总线、管控一体化和带有先进控制软件,在技术上可初步与国外产品相抗衡。
目前,我国现场控制系统一般仍采用DCS。
4. 发展方向DCS发展至今已相当成熟和实用,毫无疑问,它仍是当前工业自动化系统应用及选型的主流,不会随着现场总线技术的出现而立即退出现场过程控制的舞台。
面对挑战,DCS将沿着以下趋势继续向前发展:(1)向综合方向发展:标准化数据通信链路和通信网络的发展,将各种单(多)回路调节器、PLC、工业PC、NC等工控设备构成大系统,以满足工厂自动化要求,并适应开放式的大趋势。
(2)向智能化方向发展:数据库系统、推理机能等的发展,尤其是知识库系统(KBS)和专家系统(ES)的应用,如自学习控制、远距离诊断、自寻优等,人工智能会在DCS各级实现。
与FF现场总线类似,以微处理器为基础的智能设备如智能I/O、PID控制器、传感器、变送器、执行器、人机接口、PLC相继出现。
(3)DCS工业PC化:由IPC组成DCS已成为一大趋势,PC作为DCS的操作站或节点机已很普遍,PC-PLC、PC-STD、PC-NC等就是PC-DCS先驱,IPC成为DCS 的硬件平台。
(4)DCS专业化:DCS为更适合各相应领域的应用,就要进一步了解相应专业的工艺和应用要求,以逐步形成如核电DCS,变电站DCS、玻璃DCS、水泥DCS 等。
二现场总线控制系统(FCS)现场总线控制系统是继DCS之后的又一种新型工业控制系统,它的出现带来了工业控制领域的一场深刻革命。
现场总线代表一种突破意义的控制思想,改变了原有控制体系结构,使模拟与数字混合的DCS更新换代为全数字现场总线控制系统,真正做到危险分散、控制分散、集中监控和全数字化。
1. 应用现状现场总线发展迅速,现处于群雄并起、百家争鸣的阶段。
目前已开发出40多种现场总线,如Interbus、Bitbus、DeviceNet、Modbus、ARCent、P-Net、FIP、ISP等,其中最有影响力的有5种,分别为FF、Profibus、HART、CAN、LonWorks,如表所示。
FCS全数字化通信使过程控制具有更高可靠性,从传感器、变送器到调节器,均为数字信号,这就使得复杂、精确的信号处理得以实现。
因采用数字总线式通信线路代替DCS 1对1的I/O连线,对于大规模I/O系统,减少了由连线带来的不可靠,同时也降低了布线成本。
此外FCS还具有互操作性、分散性、EIC(电气传动、仪表、计算机)一体化等优点。
在由现场总线构成的FCS中,仪表实际上已成为具有综合功能的智能仪表。
EIC一体化结构恰恰是钢铁工业自动化用得较多而又急需的控制系统结构。
2. 现场总线存在的不足现场总线是一种正在发展中的技术,在许多方面还需改善。
IEC 61158规定了FF、Profibus、WorldFIP等8种现场总线标准,还有一些事实上的标准,如LonWorks和CAN总线等。
现有8种现场总线为国际标准,它们采用的通信协议完全不同,因此要实现这些总线的兼容和互操作十分困难。
许多标准的并存,将导致现场总线技术不易广泛应用。
现场总线还存在着瓶颈问题,表现在:(1)总线切断后,系统有可能产生不可预知的后果;(2)在本安防爆应用中,现有防爆规定限制总线长度和总线上所挂设备数量,同时也限制了现场总线节省线缆优点的发挥;(3)系统组态参数过于复杂,不易掌握,而其设定的好坏对系统性能影响很大。
3. 现场总线在中国以智能化现场仪表为基础的现场总线系统与传统系统相比,其优点不仅在控制方面,更多的是在自诊断、自校正等自动管理方面。
但国内使用的系统规模一般不大,没有把管理自动化和远程诊断功能纳入系统,因此无法发挥FCS降低运行维护费用的优势,所以与传统产业相比,现场总线的优点没有完全体现出来,现在国内还有很多企业对现场总线技术和产品是否成熟可靠持怀疑态度。
现场总线在中国需进一步促进其快速发展,最主要的则是推动企业对现场总线的应用。
我国是发展中国家,还不拥有自主版权的现场总线。
我们应谨慎对待出现在现场总线问题上的争论,它已阻碍了工业自动化领域网络技术的发展和产品的更新换代,我们应抓住网络发展的新机遇,努力发展我国自己的现场总线网络产业。
4. 发展方向现场总线是一种正在发展的技术,在过程控制领域对其要求是:(1)改善实时性,不允许有不确定性;(2)克服本安防爆对总线中节点数和电缆长度的限制,加强现场总线本安概念理论研究;(3)实现可互操作性和信息处理现场化。
今后,对上述3方面还要进行积极研究、不断探索。
实时性和可互操作性是以太网在工业现场应用所要解决的重要问题。
由于Ethernet技术的快速发展,其介入控制已成为事实。
Ethernet的主要特点是:数字式互连网络、可操作性、开放性和高网络功能。
网络功能包括实时性、可靠性等。
而开放性最为重要。
Ethernet是世界上应用最为广泛的计算机通信技术之一,受到广泛技术开发支持,而且已使用多年,具有大量软、硬件资源和开发设计经验。
在以太网上层应用的TCP/IP协议也已开发较成熟;绝大多数PC机均提供以太网接口,操作系统也已配备TCP/IP协议;以太网适配器及其相关产品价格低廉,一块以太网网卡的价格只是Profibus、FF等现场总线网卡的一小部分;而且许多现场总线标准已向上支持以太网,其中主流现场总线FF 于2000年3月宣布用以太网增强H2的方案。
因此,一般认为整合Ethernet和TCP/IP技术的现场总线是今后发展的主流体系和应用热点。
三以太网(Ethernet)开放的以太网是20多年来发展最为成功的网络技术,并导致了一场信息技术的革命。
1. 应用现状工业自动化控制系统网络结构发展越来越分散化,同时系统越来越复杂,内部连接越来越高速化、紧密化,更多的是系统细分成为独立控制孤岛,对驱动器和用户接口需求越来越多。
而无论如何传统PLC技术无法满足该要求,现场总线技术也不能提供相关性能。
只有通过网络技术来解决,而在所有网络技术中,以太网技术是最理想的选择。
目前以太网还只适合于工业控制网络系统的信息层应用。
以太网是Byte级网络,只能部分代替现场总线作用,而将以太网用于现场I/O级,这是目前工控领域研究的热点之一。
2. Ethernet的优势与以往控制网络相比,以太网应用于工业控制具有以下的优势:(1)更高的通信带宽。
以太网是一种成熟、快速的网络协议,数据传输速率为10~100Mb/s。
新一代以太网传输速率更快,可达1Gb/s,能满足不断增长的数据通信需要,成为企业范围的主干网络。
(2)实现现场设备层和企业管理层的无缝连接。
以太网早已成为企业管理网络的首选,将其应用于现场设备控制网络,将实现企业信息网络和控制网络的融合,促进整个企业信息化的集成。
(3)控制系统成本降低。
主要体现在两方面:支持以太网通信的网络设备较低;熟悉以太网网络操作的用户较多,整个系统培训、维护都较容易。
(4)更高稳定性。
光纤网络已成为Internet的主干网络,光纤所具有的良好抗噪声干扰性能使得以太网更适合在实时监控的高噪声设备现场环境。
3. Ethernet在中国的应用目前国内对工业控制网络领域的理论研究主要局限于现场总线网络,部分学者对建立工业以太网控制网络进行了探讨,但仍停留在概念上,未能进入实质性研究阶段,实际应用还不多。
就目前我国网络控制实际情况和发展要求,工业控制系统将普遍以现场总线和DCS相结合作为控制系统的底层和中层,用于工业现场;而将以太网用于控4. 发展方向基于以太网的控制网络所具有的上述优点是目前现场总线技术所无法比拟的。
另外,随着宽带以太网与交换式以太网技术的发展,以太网作为控制网络在控制实时性方面的问题正在逐步得以解决。
虽然以太网采用的是带碰撞检测的载波侦听多路访问协议(CSMA/CD),一般认为该协议不能满足控制系统实时性要求,但100Mb/s以太网已开始广泛应用,千兆以太网产品也已出现;而且以太网交换技术的出现,通过全双工交换技术,可完全避免CSMA/CD中的碰撞;还可方便实现优先级机制,实现网络带宽的最大利用率和最好实现性能。