吸收稳定操作原则
吸收稳定操作原则

●吸收稳定操作原则吸收—稳定系统的任务是将来自分馏塔顶粗汽油和富气,通过吸收塔和解吸塔分离成干气和脱乙烷汽油,再通过稳定塔将脱乙烷汽油分离成液态烃和稳定汽油。
对于吸收操作,温度越低、压力越高、吸收剂量越大越有利于吸收;对于解吸操作,温度越高,压力越低越有利于解吸。
吸收和解吸操作又相互影响,要从吸收和解吸整体分离效果来考虑控制各自的操作条件。
吸收过度将增加解吸负荷,解吸过度又会增加吸收负荷,吸收或解吸过度后反而会造成分离效果恶化。
因此必须树立吸收—解吸系统整体操作的思想。
对于稳定塔操作,影响分离精度的主要因素是回流比,在塔底重沸器热源充足和塔顶冷凝品负荷允许的情况下,塔顶回流越大,分离效果越好。
但回流过大,将增加塔底重沸器加热负荷和塔盘的气液相负荷,一旦塔盘气、液相负荷超标后,将出现液泛或雾沫夹带,产品分割度变差。
所以稳定塔操作需要根据进料组成、流量的变化,及时调整塔顶回流量,塔顶温度作为液态烃C5含量控制的关键指标,塔底重沸器出口温度作为稳定汽油10%点控制的关键指标。
正常操作●产品质量控制⑴干气中>C3含量的控制①干气冷后温度高;②吸收剂量不足或吸收剂温度高,吸收效果差(干气中C3含量高);③吸收塔温度高或中段回流取热量少,吸收效果差;④稳定深度不够,补充吸收剂用量过大;⑤吸收塔压力过低或波动大;⑥解吸塔温度过高,大量C3、C4组分过度解吸,增加吸收塔的负荷;⑦不凝气排放。
⑵液态烃C2含量的控制a.影响因素①解吸塔底重沸器出口温度低,解吸效果差;②吸收过度导致解吸塔进料中会有大量C2。
⑶液态烃C5含量的控制a.影响因素①稳定塔顶回汉量小或冷却器效果差,造成塔顶温度高;②稳定塔底重沸器出口温度控制过高;③稳定塔压力低或波动大;④进料位置不同,进料口以上的精馏段塔盘娄目不同,影响精馏效果。
⑤回炼轻汽油后塔盘上液相负荷降低,相当于降低了塔顶回流比;⑥粗汽油流量下降或稳定塔进料中液态烃组分含量上升,液态烃C5含量上升。
催化裂化装置吸收稳定单元停工操作法

催化裂化装置吸收稳定单元停工操作法一、吸收稳定单元退油当反应切断进料后,分馏岗位将V22203A、B中轻燃油抽空后,停T22304至T22301的补充吸收油,退油原则尽量将油赶至T22304,各抽出泵抽空后停泵,退油结束。
分馏一中扫线开始前T22304油退完。
轻油由T22301V22302T22302T22304精制单元出装置贫吸收油走付线不经T22303,直接返T22201A,T22303中油压回T22201A,现场注意T22303液位不要压空,严禁干气窜入T22201A。
稳定塔在再沸器出口温度变化不大的情况下,加大稳定轻燃油出装量,在保证塔顶温度不变的情况下尽量加大液化气外送量,V22303无液面时,停P22306AB。
二、吸收稳定单元水顶油1. 分馏未吹扫干净E22310管程,T22304严禁进水,防止突沸。
2. 不合格轻燃油出装置线:新鲜水P22202FV22218管线P22218/2管线P22222不合格轻罐油3. 新鲜水走正常流程进T22301:P22202给水FV22218T22301P22203给水FV222184. T22301一中、二中回流线:一中:二中:P22303LV22302E22303T22301 P22304LV22303E22304T223015. 凝缩油线:T22301P22302FV22302V22302P22301FV22306E22305T22302FV22305V22301注水P22309LV229016. 脱乙烷轻燃油线:T22302P22305FV22307E22307T223047. 稳定塔回流线:P22306给水FV22308T223048. T22301补充吸收剂线:P22307FV22301T22301T223049. 吸收稳定单元撇油。
吸收稳定单元改为三塔循环流程,2小时后,将T22301、V22302抽空,水全部集中在T22302、T22304中,两塔内水位要高,以撇油线在P22307入口见水为准。
吸收稳定操作原则

●吸收稳定操作原则吸收—稳定系统的任务是将来自分馏塔顶粗汽油和富气,通过吸收塔和解吸塔分离成干气和脱乙烷汽油,再通过稳定塔将脱乙烷汽油分离成液态烃和稳定汽油。
对于吸收操作,温度越低、压力越高、吸收剂量越大越有利于吸收;对于解吸操作,温度越高,压力越低越有利于解吸。
吸收和解吸操作又相互影响,要从吸收和解吸整体分离效果来考虑控制各自的操作条件。
吸收过度将增加解吸负荷,解吸过度又会增加吸收负荷,吸收或解吸过度后反而会造成分离效果恶化。
因此必须树立吸收—解吸系统整体操作的思想。
对于稳定塔操作,影响分离精度的主要因素是回流比,在塔底重沸器热源充足和塔顶冷凝品负荷允许的情况下,塔顶回流越大,分离效果越好。
但回流过大,将增加塔底重沸器加热负荷和塔盘的气液相负荷,一旦塔盘气、液相负荷超标后,将出现液泛或雾沫夹带,产品分割度变差。
所以稳定塔操作需要根据进料组成、流量的变化,及时调整塔顶回流量,塔顶温度作为液态烃C5含量控制的关键指标,塔底重沸器出口温度作为稳定汽油10%点控制的关键指标。
正常操作●产品质量控制⑴干气中>C3含量的控制①干气冷后温度高;②吸收剂量不足或吸收剂温度高,吸收效果差(干气中C3含量高);③吸收塔温度高或中段回流取热量少,吸收效果差;④稳定深度不够,补充吸收剂用量过大;⑤吸收塔压力过低或波动大;⑥解吸塔温度过高,大量C3、C4组分过度解吸,增加吸收塔的负荷;⑦不凝气排放。
⑵液态烃C2含量的控制a.影响因素①解吸塔底重沸器出口温度低,解吸效果差;②吸收过度导致解吸塔进料中会有大量C2。
⑶液态烃C5含量的控制a.影响因素①稳定塔顶回汉量小或冷却器效果差,造成塔顶温度高;②稳定塔底重沸器出口温度控制过高;③稳定塔压力低或波动大;④进料位置不同,进料口以上的精馏段塔盘娄目不同,影响精馏效果。
⑤回炼轻汽油后塔盘上液相负荷降低,相当于降低了塔顶回流比;⑥粗汽油流量下降或稳定塔进料中液态烃组分含量上升,液态烃C5含量上升。
最新化工原理实验报告吸收实验要点
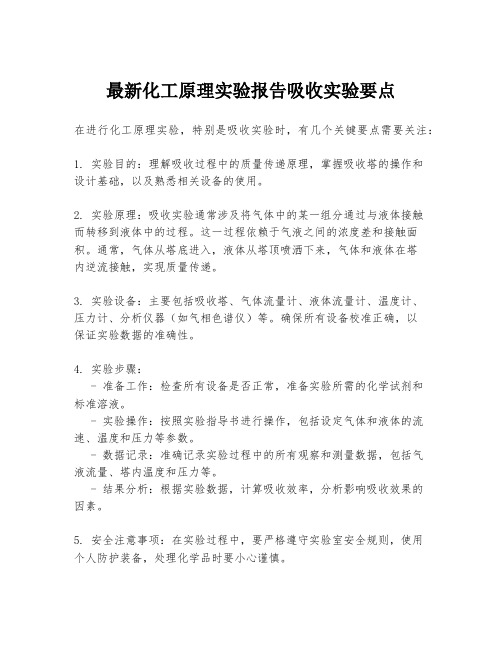
最新化工原理实验报告吸收实验要点在进行化工原理实验,特别是吸收实验时,有几个关键要点需要关注:1. 实验目的:理解吸收过程中的质量传递原理,掌握吸收塔的操作和设计基础,以及熟悉相关设备的使用。
2. 实验原理:吸收实验通常涉及将气体中的某一组分通过与液体接触而转移到液体中的过程。
这一过程依赖于气液之间的浓度差和接触面积。
通常,气体从塔底进入,液体从塔顶喷洒下来,气体和液体在塔内逆流接触,实现质量传递。
3. 实验设备:主要包括吸收塔、气体流量计、液体流量计、温度计、压力计、分析仪器(如气相色谱仪)等。
确保所有设备校准正确,以保证实验数据的准确性。
4. 实验步骤:- 准备工作:检查所有设备是否正常,准备实验所需的化学试剂和标准溶液。
- 实验操作:按照实验指导书进行操作,包括设定气体和液体的流速、温度和压力等参数。
- 数据记录:准确记录实验过程中的所有观察和测量数据,包括气液流量、塔内温度和压力等。
- 结果分析:根据实验数据,计算吸收效率,分析影响吸收效果的因素。
5. 安全注意事项:在实验过程中,要严格遵守实验室安全规则,使用个人防护装备,处理化学品时要小心谨慎。
6. 实验结果分析:通过对收集到的数据进行分析,可以确定吸收塔的效率和操作条件对吸收效果的影响。
此外,还可以通过对比理论值和实验值,来评估实验的准确性和可靠性。
7. 结论:基于实验结果和分析,得出关于吸收过程效率和操作参数对吸收效果影响的结论。
同时,提出可能的改进措施和建议。
8. 参考文献:列出实验报告中引用的所有文献和资料,确保信息来源的准确性和可靠性。
以上是吸收实验的主要内容要点,每个实验报告的具体内容可能会根据实验的具体要求和条件有所不同。
吸收实验原理、要求

填料吸收塔的操作及吸收传质系数的测定一、实验目的(1)了解填料吸收塔的结构和流程;(2)了解吸收剂进口条件的变化对吸收操作结果的影响;(3)掌握吸收总传质系数的测定方法.二、基本原理1.吸收速率方程式吸收传质速率由吸收速率方程式决定:Na = Ky A Δym式中 Ky 为气相总传质系数,mol/m2*h;A 为填料的有效接触面积,m2;Δym 为塔顶、塔底气相平均推动力。
a 为填料的有效比表面积,m2/m3;V 为填料层堆积体积, m3 ;Kya 为气相总容积吸收传质.系数,mol/m3*h。
从上式可看出,吸收过程传质速率主要由两个参数决定:Δym为过程的传质推动力,Kya的倒数1/Kya表征过程的传质阻力。
2.填料吸收塔的操作吸收操作的结果最终表现在出口气体的组成y2上,或组分的回收率η上。
在低浓度气体吸收时,回收率可近似用下式计算:η = (y1 – y2)/y1吸收塔的气体进口条件是由前一工序决定的,一般认为稳定不变。
控制和调节吸收操作结果的操作变量是吸收剂的进口条件:流率 L 、温度 t 和浓度 x2 这三个要素。
由吸收分析可知,改变吸收剂用量是对吸收过程进行调节的最常用方法,当气体流率 G 不变时,增加吸收剂流率,吸收速率η增加,溶质吸收量增加,出口气体的组成y2随着减小,回收率η增大。
当液相阻力较小时,增加液体的流量,总传质系数变化较小或基本不变,溶质吸收量的增加主要是由于传质平均推动力Δym的增大而引起,即此时吸收过程的调节主要靠传质推动力的变化。
但当液相阻力较大时,增加液体的流量,可明显降低传质阻力,总传质系数大幅度增加,而平均推动力却有可能减小(视调节前操作工况的不同而不同),但总的结果使传质速率增大,溶质吸收量增大。
吸收剂入口温度对吸收过程的影响也甚大,也是控制和调节吸收操作的一个重要因素。
降低吸收剂的温度,使气体的溶解度增大,相平衡常数减小。
对于液膜控制的吸收过程,降低操作温度,吸收过程的阻力随之减小,使吸收效果变好,y2降低,但平均推动力Δym或许会有所减小。
安全每日一题
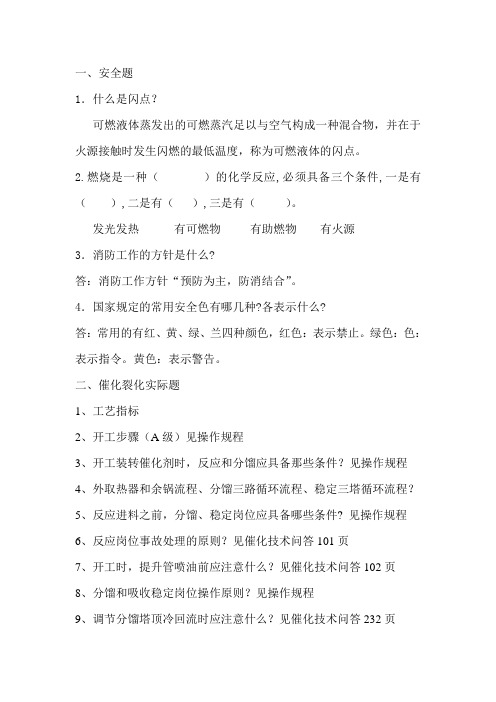
一、安全题
1.什么是闪点?
可燃液体蒸发出的可燃蒸汽足以与空气构成一种混合物,并在于火源接触时发生闪燃的最低温度,称为可燃液体的闪点。
2.燃烧是一种()的化学反应,必须具备三个条件,一是有(),二是有(),三是有()。
发光发热有可燃物有助燃物有火源
3.消防工作的方针是什么?
答:消防工作方针“预防为主,防消结合”。
4.国家规定的常用安全色有哪几种?各表示什么?
答:常用的有红、黄、绿、兰四种颜色,红色:表示禁止。
绿色:色:表示指令。
黄色:表示警告。
二、催化裂化实际题
1、工艺指标
2、开工步骤(A级)见操作规程
3、开工装转催化剂时,反应和分馏应具备那些条件?见操作规程
4、外取热器和余锅流程、分馏三路循环流程、稳定三塔循环流程?
5、反应进料之前,分馏、稳定岗位应具备哪些条件? 见操作规程
6、反应岗位事故处理的原则?见催化技术问答101页
7、开工时,提升管喷油前应注意什么?见催化技术问答102页
8、分馏和吸收稳定岗位操作原则?见操作规程
9、调节分馏塔顶冷回流时应注意什么?见催化技术问答232页
10、冷回流?
11、回流比?。
石油炼制过程

分类习惯上将石油炼制过程不很严格地分为三类过程:(1)一次加工(2)二次加工(3)三次加工。
炼厂总体工艺图如下原油一次加工把原油蒸馏分为几个不同的沸点范围(即馏分)叫一次加工;一次加工装置;常压蒸馏或常减压蒸馏。
是将原油用蒸馏的方法分离成轻重不同馏分的过程,常称为原油蒸馏,它包括原油预处理、常压蒸馏和减压蒸馏。
一次加工产品可以粗略地分为:①轻质馏分油(见轻质油),指沸点在约370℃以下的馏出油,如粗汽油、粗煤油、粗柴油等。
②重质馏分油(见重质油),指沸点在370~540℃左右的重质馏出油,如重柴油、各种润滑油馏分、裂化原料等。
③渣油(又称残油)。
习惯上将原油经常压蒸馏所得的塔底油称为重油(也称常压渣油、半残油、拔头油等)。
原油二次加工(裂化、重整、精制和裂解)二次加工过程:将一次加工得到的馏分再加工成商品油叫二次加工;二次加工装置:催化、加氢裂化、延迟焦化、催化重整、烃基化、加氢精制等。
一次加工过程产物的再加工。
主要是指将重质馏分油和渣油经过各种裂化生产轻质油的过程,包括催化裂化、热裂化、石油焦化、加氢裂化等。
其中石油焦化本质上也是热裂化,但它是一种完全转化的热裂化,产品除轻质油外还有石油焦。
二次加工过程有时还包括催化重整和石油产品精制。
前者是使汽油分子结构发生改变,用于提高汽油辛烷值或制取轻质芳烃(苯、甲苯、二甲苯);后者是对各种汽油、柴油等轻质油品进行精制,或从重质馏分油制取馏分润滑油,或从渣油制取残渣润滑油等。
裂化一是热裂化就是完全依靠加热进行裂化。
主要原料是减压塔生产中得到的含蜡油。
通过热裂化,又可取得汽油、煤油、柴油等轻质油。
但是,热裂化所得到的产品,其质量不够好二是催化裂化就是在裂化时不仅加热而且加入催化剂。
由于催化剂就像人们蒸制馒头时加入酵母一样,能大大加快反应速度,所以,催化裂化比热裂化获得的轻质油多(汽油产率可达60%左右),而且产品的质量也比较好三是加氢催化就是在加入氢气的情况下进行催化裂化。
第三节 稳定单元操作指南

第三节稳定单元操作指南一.吸收稳定单元的主要任务1.将分馏来的粗汽油和气压机来的压缩富气进一步分离为稳定汽油、液化气、干气等产品,并保证产品质量及收率。
2.维护本岗位所属设备,工艺管线,保证安全生产,并及时准确发现本岗位存在问题,做到心中有数,及早处理,杜绝事故发生。
二.吸收稳定单元的操作原则1.生产过程中,要确保系统压力,各塔、容器液面平稳,视稳定汽油、液化气、干气质量变化,调节塔底温度和顶回流量,达到提高汽油收率改善汽油质量,生产合格液化气、燃料气等产品。
2.操作波动时,及时处理,尽量减少对其它岗位的影响,应严格控制各塔和容器不超压、不超温、液位不超高、泵不抽空。
3.控制好各容器液面及压力,注意水包油水界位,防止油水互串入分馏塔,或大量带入稳定系统。
4.切断进料后,尽可能维持本系统压力,尽可能维持三塔循环。
5.处理事故时应尽力利用泵和系统余压将本系统油全部压往罐区,将瓦斯系统放火炬和泄压。
避免瓦斯泄入大气。
6.杜绝一切事故隐患,严防泄漏、着火、爆炸,必要时,吸收稳定系统改三塔循环或紧急停工。
7.操作不正常或发生事故时,需及时处理,严防事故扩大引起超温、超压、火灾、爆炸事故。
8.做好冬季管线及设备的防冻防凝工作。
冬季操作不正常处理时,要考虑防冻问题。
三.吸收稳定单元的操作参数控制1.吸收塔压力控制提高吸收塔操作压力有利于吸收过程的进行。
保证吸收率相同时,提高压力可减少吸收剂用量,降低吸收、脱吸和稳定塔的液相负荷,节省泵功率,脱乙烷汽油可以自压入稳定塔。
提高压力后,气压机的功率要增加,塔底重沸器的热负荷也要相应增加。
通常再吸收塔操作压力由气压机的能力、吸收塔前各个设备的压降和装置的实际情况所决定,一般不作为调节参数,在操作时应注意控制稳塔压,不使其变化。
影响因素1.富气量增大(装置处理量增大,反应深度加大,分馏塔顶后冷效果差)容易引起压力升高;2.进料富气温度变化;3.吸收剂量或富气量的变化影响压力;4.V-1302,T-1301,T-1301二中段集油箱,T-1301一中段集油箱液面超高造成气体憋压;5.气压机工况发生变化;6.干气脱硫压控系统故障、瓦斯管网压力失常;7.吸收塔塔盘工况不佳;8.吸收系统压力控制PC1301失灵或故障;9.T1303操作失常,发生液泛,满液位等导致压降上升。
- 1、下载文档前请自行甄别文档内容的完整性,平台不提供额外的编辑、内容补充、找答案等附加服务。
- 2、"仅部分预览"的文档,不可在线预览部分如存在完整性等问题,可反馈申请退款(可完整预览的文档不适用该条件!)。
- 3、如文档侵犯您的权益,请联系客服反馈,我们会尽快为您处理(人工客服工作时间:9:00-18:30)。
●吸收稳定操作原则
吸收—稳定系统的任务是将来自分馏塔顶粗汽油和富气,通过吸收塔和解吸塔分离成干气和脱乙烷汽油,再通过稳定塔将脱乙烷汽油分离成液态烃和稳定汽油。
对于吸收操作,温度越低、压力越高、吸收剂量越大越有利于吸收;对于解吸操作,温度越高,压力越低越有利于解吸。
吸收和解吸操作又相互影响,要从吸收和解吸整体分离效果来考虑控制各自的操作条件。
吸收过度将增加解吸负荷,解吸过度又会增加吸收负荷,吸收或解吸过度后反而会造成分离效果恶化。
因此必须树立吸收—解吸系统整体操作的思想。
对于稳定塔操作,影响分离精度的主要因素是回流比,在塔底重沸器热源充足和塔顶冷凝品负荷允许的情况下,塔顶回流越大,分离效果越好。
但回流过大,将增加塔底重沸器加热负荷和塔盘的气液相负荷,一旦塔盘气、液相负荷超标后,将出现液泛或雾沫夹带,产品分割度变差。
所以稳定塔操作需要根据进料组成、流量的变化,及时调整塔顶回流量,塔顶温度作为液态烃C5含量控制的关键指标,塔底重沸器出口温度作为稳定汽油10%点控制的关键指标。
正常操作
●产品质量控制
⑴干气中>C3含量的控制
①干气冷后温度高;
②吸收剂量不足或吸收剂温度高,吸收效果差(干气中C3含量高);
③吸收塔温度高或中段回流取热量少,吸收效果差;
④稳定深度不够,补充吸收剂用量过大;
⑤吸收塔压力过低或波动大;
⑥解吸塔温度过高,大量C3、C4组分过度解吸,增加吸收塔的负荷;
⑦不凝气排放。
⑵液态烃C2含量的控制
a.影响因素
①解吸塔底重沸器出口温度低,解吸效果差;
②吸收过度导致解吸塔进料中会有大量C2。
⑶液态烃C5含量的控制
a.影响因素
①稳定塔顶回汉量小或冷却器效果差,造成塔顶温度高;
②稳定塔底重沸器出口温度控制过高;
③稳定塔压力低或波动大;
④进料位置不同,进料口以上的精馏段塔盘娄目不同,影响精馏效果。
⑤回炼轻汽油后塔盘上液相负荷降低,相当于降低了塔顶回流比;
⑥粗汽油流量下降或稳定塔进料中液态烃组分含量上升,液态烃C5含量上升。
⑷汽油10%点的控制
①稳定塔底温度高,10%点高;
②塔顶回流量过大,汽油10%点低;
③塔进料组成的变化,进料中汽油组分含量增加,10%点高。
五、干气、液化气脱硫系统操作:
⑴贫液中的H2S含量
影响因素
①再生温度低;
②溶剂负荷大,出现冲塔;
③再生塔压力过高;
④胺液浓度低、质量差,再生效果差。
液化气中C5含量的控制:
焦化干气C3以上组分含量控制
焦化干气作为燃料,如果含有太多的C3、C4、C5组分,会造成化工原料的浪费。
影响吸收的因素很多,主要有:油气比、操作温度、操作压力、吸收剂和被吸收气体的性质、塔内气液流动状态、塔板数及塔板结构等。
对具体装置来讲,吸收塔的结构等因素都已确定,吸收效果主要靠适宜的操作条件来保证。
主要影响因素:
(1)吸收剂量不足,干气中C3以上组分含量高。
(2)吸收剂的温度高,干气中C3以上组分含量高。
(3)压缩富气冷却后的温度过高,干气中C3以上组分含量高。
(4)再吸收塔操作压力(PIC4206)过低,干气中C3以上组分含量高。
(5)提高吸收剂质量,可显著提高吸收效果,干气中C3以上组分含量低。
(6)吸收剂进料口的位置改变,影响吸收效果,同流量的吸收柴油从25层进料比21 层进料,干气中C3以上组分含量低,但柴油携带量多,影响分离效果。
调节方法:
(1)正常生产中控制一定的油气比,设计油气比为3.2。
(2)再吸收塔顶部温度(TI4291)由吸收剂进料温度来控制,应尽量降低吸收剂的入塔温度。
(3)再吸收塔底部温度(TI4292)由压缩富气进料温度来控制,通过调节A-201和E-201,尽量降低压缩富气冷后温度。
(4)通过调节再吸收塔顶压力提高再吸收塔操作压力
(5)若压缩富气负荷大、进料温度高或吸收剂温度高,吸收剂应改至上进料口。
3.2、再吸收塔顶压力(PIC4206)的控制
提高再吸收塔操作压力有利于再吸收过程的进行,保证吸收率相同时,提高压力可减少吸收剂用量,降低再吸收塔的液相负荷,节省P-201功率,但气压机功耗要增加。
确定再吸收塔压力,由气压机的能力、再吸收塔前各个设备的压降和生产装置的实际情况所决定,正常生产时可通过脱硫塔顶压控阀PIC4207、PIC4206控制系统压力。
主要影响因素:
(1)再吸收塔富气进料量的变化。
(2)进料富气温度的变化。
(3)吸收剂量FIC4223和组份的变化。
(4)脱硫塔C-202液面超高造成再吸收塔憋压。
(5)制氢停止进料。
调节方法:
(1)正常条件下,再吸收塔顶压力由C-202压控阀PIC4207 配和PIC4206自动控制。
(2)调节A-201、E-201控制进料富气温度.
(3)控制C-202液面在40~60%之间。